Top 12 Lathe Machinist Skills to Put on Your Resume
In today's competitive job market, standing out as a lathe machinist requires showcasing a blend of technical proficiency, precision, and creativity. Highlighting the top skills on your resume can significantly enhance your attractiveness to potential employers, demonstrating your capability to meet the demands of modern manufacturing environments.
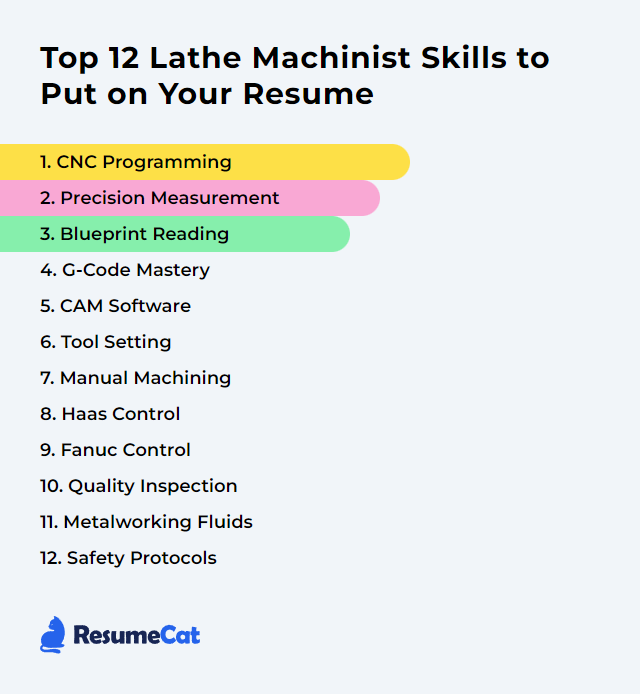
Lathe Machinist Skills
- CNC Programming
- Precision Measurement
- Blueprint Reading
- G-Code Mastery
- CAM Software
- Tool Setting
- Manual Machining
- Haas Control
- Fanuc Control
- Quality Inspection
- Metalworking Fluids
- Safety Protocols
1. CNC Programming
CNC programming for a lathe machinist involves creating computer instructions that guide the CNC lathe machine in shaping metal or other materials by removing excess material. This process transforms raw material into precise cylindrical components according to specific design specifications.
Why It's Important
CNC programming is crucial for a Lathe Machinist as it enables precise control over the lathe operations, ensuring accurate, repeatable, and efficient production of complex parts.
How to Improve CNC Programming Skills
To enhance your CNC programming skills for lathe operations, consider the following concise steps:
Understand the Basics: Solidify your understanding of lathe operations, tools, and materials. MIT's Introduction to CNC Programming is a great starting point.
Master CAD/CAM Software: Invest time in learning CAD/CAM software. Autodesk's Tutorials provide a comprehensive guide to design and programming.
Learn G-Code and M-Code: Familiarize yourself with the G-Code and M-Code commands specific to your machine. CNC Cookbook’s G-Code Tutorial is an excellent resource.
Optimize Tool Paths: Improve efficiency by optimizing tool paths. Mastercam's Dynamic Motion Technology illustrates advanced strategies for reducing machining time and wear.
Implement Efficient Workholding: Explore efficient workholding methods to save time and improve precision. Practical Machinist forums often discuss various techniques and equipment.
Keep Learning: Stay updated with the latest trends and technologies in CNC programming. Regularly visit Modern Machine Shop for news and articles.
By following these steps and continuously practicing, you'll significantly improve your CNC programming skills for lathe operations.
How to Display CNC Programming Skills on Your Resume
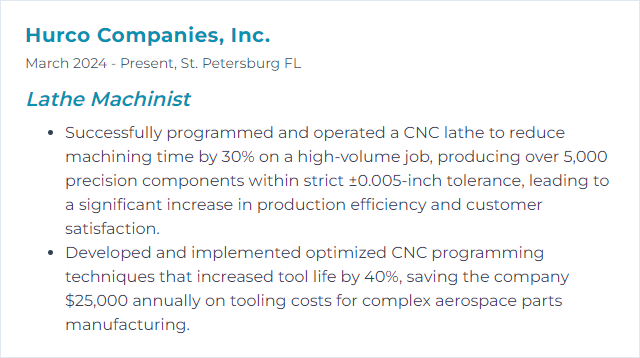
2. Precision Measurement
Precision measurement for a lathe machinist involves using highly accurate tools (such as micrometers, calipers, and dial indicators) to measure the dimensions of machined parts, ensuring they meet the specified tolerances and quality standards.
Why It's Important
Precision measurement is crucial for a lathe machinist to ensure parts are machined to exact specifications, achieving tight tolerances, optimal functionality, and high-quality finishes, thus avoiding waste and ensuring customer satisfaction.
How to Improve Precision Measurement Skills
Improving precision measurement as a lathe machinist involves several key practices:
Calibration: Regularly calibrate measuring instruments to ensure accuracy. NIST guidelines provide a comprehensive approach.
Temperature Control: Maintain a stable temperature in the work environment, as thermal expansion can affect measurements. Mitutoyo offers insights on how temperature impacts measurements.
Proper Tool Selection: Use the correct measuring tools (micrometers, vernier calipers) for the specific measurement. Machinery's Handbook is a valuable resource for tool selection and usage.
Regular Maintenance: Keep both the lathe and measuring tools clean and well-maintained to prevent inaccuracies. Haas Automation provides tips on machine maintenance.
Skill Development: Continuously hone your skills through practice and education. Tooling U-SME offers courses on precision machining techniques.
Incorporating these practices will significantly enhance the precision of measurements in lathe machining operations.
How to Display Precision Measurement Skills on Your Resume
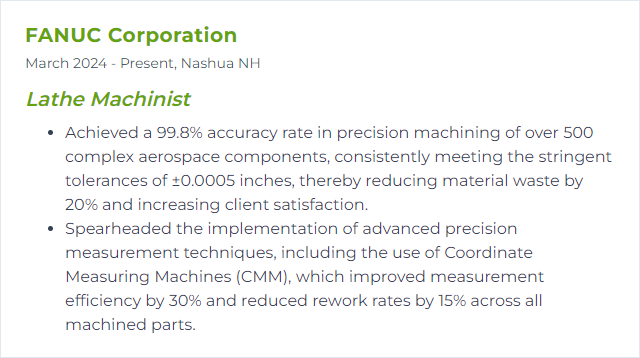
3. Blueprint Reading
Blueprint reading for a lathe machinist involves interpreting detailed technical drawings to understand the specifications and dimensions of parts to be manufactured or machined using a lathe. It includes understanding symbols, tolerances, and measurements crucial for accurately producing components.
Why It's Important
Blueprint reading is crucial for a lathe machinist because it enables accurate interpretation of design specifications and dimensions, ensuring precise machining of components to meet engineering and manufacturing standards.
How to Improve Blueprint Reading Skills
Improving blueprint reading as a lathe machinist involves enhancing your understanding of technical drawings, symbols, and dimensions specific to machining processes. Here are concise steps with relevant resources:
Familiarize with Basic Symbols and Notations: Start by learning the standard symbols and notations used in machining blueprints. Engineering.com offers resources and articles that can help you understand the basics.
Understand Geometric Dimensioning and Tolerancing (GD&T): GD&T provides a clear way to communicate design intent. The American Society of Mechanical Engineers (ASME) offers guidelines and standards.
Practice Reading Blueprints: Regularly practicing with real or sample blueprints can improve your skills. Websites like Practical Machinist often share examples and discussions that can be insightful.
Use Online Courses and Tutorials: Platforms like Udemy and LinkedIn Learning offer courses specifically on blueprint reading and understanding technical drawings.
Join Forums and Groups: Engage with communities on platforms like Reddit’s Machinists subreddit to ask questions, share knowledge, and get feedback on your understanding.
By leveraging these resources and actively practicing, you can significantly improve your blueprint reading skills as a lathe machinist.
How to Display Blueprint Reading Skills on Your Resume
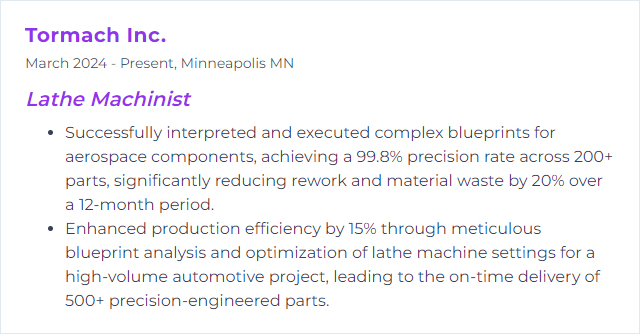
4. G-Code Mastery
G-Code Mastery for a Lathe Machinist refers to the expert-level understanding and application of G-code, the programming language used to control CNC (Computer Numerical Control) lathes. It involves the ability to read, write, and modify G-code to efficiently and accurately produce precision parts on a CNC lathe.
Why It's Important
G-Code mastery is crucial for a Lathe Machinist because it enables precise control over the machining processes, ensuring accuracy, efficiency, and the ability to create complex parts with high precision. It also enhances problem-solving skills for optimizing production and reducing errors.
How to Improve G-Code Mastery Skills
Improving G-code mastery, especially for a lathe machinist, involves a combination of understanding the basics, practicing coding, and continuous learning. Here’s how:
Learn the Basics: Start with understanding the fundamental G-codes and M-codes used in lathe operations. TITANS of CNC Academy offers free courses that cover these basics thoroughly.
Practical Application: Practice writing G-code manually for different operations to solidify your understanding. Websites like CNCCookbook provide excellent resources and examples.
Software Simulation: Use simulation software like Fusion 360 to test your G-code. This helps in understanding the machine’s movements and correcting errors without risking actual machine damage.
Continuous Learning: Stay updated with the latest techniques and codes. Forums like Practical Machinist are great for learning from experienced machinists.
Experimentation: Once comfortable, experiment with optimizing your G-code for efficiency. This could involve reducing run times or tool wear.
Remember, mastery comes with practice and continuous learning. Engage with the community, and don’t hesitate to learn from mistakes.
How to Display G-Code Mastery Skills on Your Resume
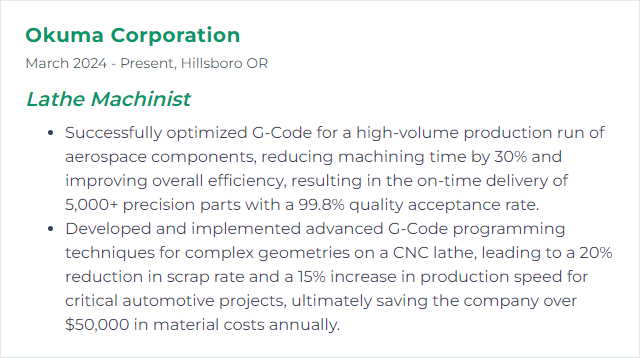
5. CAM Software
CAM (Computer-Aided Manufacturing) software is a tool used by lathe machinists to design parts and create precise programming instructions for CNC (Computer Numerical Control) lathes, automating the machining process to produce parts with high precision.
Why It's Important
CAM software is important for a Lathe Machinist because it automates the process of converting designs into precise machining instructions, significantly enhancing accuracy, efficiency, and productivity in producing complex parts.
How to Improve CAM Software Skills
Improving CAM (Computer-Aided Manufacturing) software for a lathe machinist involves focusing on usability, precision, and integration capabilities. Here are concise strategies to enhance CAM software:
User Interface (UI) Enhancement: Simplify the user interface to enable intuitive navigation and operation. Incorporating drag-and-drop functionality and customizable toolbars can significantly improve efficiency. Autodesk offers insights on UI design for manufacturing software.
Simulation and Verification: Implement advanced simulation tools to visualize the machining process in real-time, reducing errors and material waste. CGTech's VERICUT is a leading example for advanced simulation.
Toolpath Optimization: Integrate smart algorithms that automatically adjust toolpaths for optimal speed, efficiency, and material removal. This reduces machining time and extends tool life. Mastercam's Dynamic Motion technology showcases this capability.
Support for Advanced Tooling: Ensure the software is regularly updated to support the latest tooling technology, such as high-performance end mills and multi-tasking tools. This enhances the machinist's ability to perform complex operations with precision.
Seamless Integration with CAD Software: Enhance the integration with CAD (Computer-Aided Design) software to allow for a smoother workflow from design to manufacturing. This includes support for importing/exporting in various file formats. Siemens provides comprehensive solutions through its NX software.
Customizable Post-Processors: Offer an easy-to-use interface for editing and customizing post-processors to ensure compatibility with various CNC machines. This flexibility allows machinists to adapt quickly to different machines. PostHASTE is an example of a tool offering customizable post-processors.
Training Resources and Community Support: Provide access to extensive training materials, including tutorials, webinars, and forums, to help users maximize the software's capabilities. The Fusion 360 community by Autodesk is a valuable resource for learning and support.
Improving CAM software by focusing on these areas will significantly benefit lathe machinists by making the software more intuitive, efficient, and versatile, ultimately leading to better machining outcomes and higher productivity.
How to Display CAM Software Skills on Your Resume
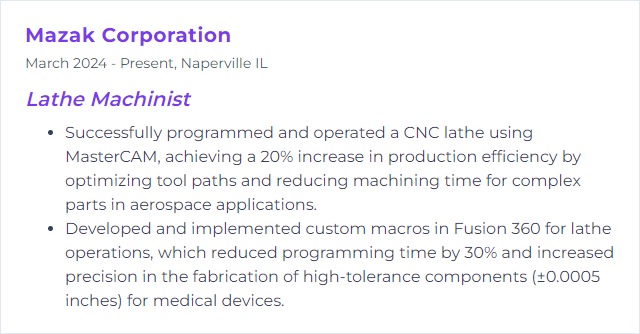
6. Tool Setting
Tool setting in the context of a lathe machinist involves precisely positioning and securing the cutting tools in the lathe machine to ensure accurate machining operations according to the specified dimensions and surface finish of the workpiece.
Why It's Important
Tool setting in lathe operations is crucial for ensuring accuracy, precision, and surface finish quality, as it determines the tool's position relative to the workpiece for optimal cutting conditions, and helps prevent tool wear and damage.
How to Improve Tool Setting Skills
Improving tool setting in lathe machining involves precision and consistency. Here's a concise guide:
Use Presetters: Invest in a high-quality tool presetter to measure tools off the machine for accuracy. Learn more about tool presetters.
Apply Correct Offsets: Ensure you accurately input the tool offset values into the CNC machine. This guide on tool offsets can help.
Regular Calibration: Regularly calibrate your tools and machine to maintain accuracy. This resource highlights the importance of machine maintenance.
Use High-Quality Tools: Invest in high-quality cutting tools for better performance and consistency. Here's why quality matters.
Continuous Learning: Stay updated with the latest techniques and tools in the industry. Websites like Modern Machine Shop offer valuable resources.
By following these steps, you can significantly improve tool setting in lathe machining.
How to Display Tool Setting Skills on Your Resume
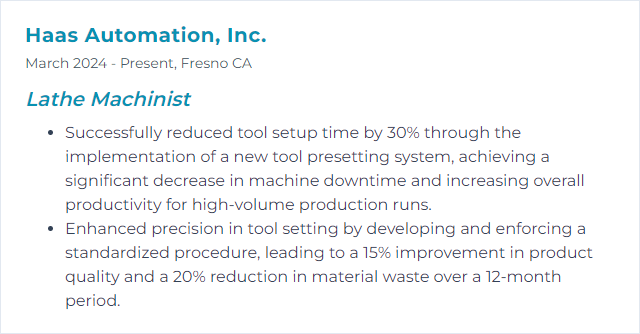
7. Manual Machining
Manual machining, in the context of a lathe machinist, involves the use of hand-operated tools and controls to cut, shape, and finish materials on a lathe, without computer automation.
Why It's Important
Manual machining is crucial for a Lathe Machinist as it provides a deep understanding of fundamental machining principles, enables precise custom work and repairs not feasible with CNC machines, and enhances problem-solving skills necessary for effective machine operation and maintenance.
How to Improve Manual Machining Skills
Improving manual machining, especially for a Lathe Machinist, involves honing skills, understanding materials, and mastering the lathe. Here's a concise guide:
Fundamentals: Start with a strong understanding of machining basics. MIT's Introduction to Machine Tools provides a comprehensive start.
Practice Precision: Precision is key. Practice making precise cuts, and use digital calipers for accurate measurements.
Speeds and Feeds: Learn the right speeds and feeds for different materials. The Machinery's Handbook is an invaluable resource.
Tool Selection and Care: Choose the right tool for the job. Sandvik Coromant's tool selection guide helps in understanding tool materials and geometries.
Workholding Techniques: Master various workholding methods. Practical Machinist forums offer real-world advice and techniques.
Safety: Always prioritize safety. Familiarize yourself with OSHA's Machine Shop Safety guidelines.
Continuous Learning: The field is always evolving. Stay updated with latest techniques through Modern Machine Shop.
Focus on mastering these areas through continuous practice, learning, and by leveraging the wealth of knowledge available from experienced machinists and reputable sources online.
How to Display Manual Machining Skills on Your Resume
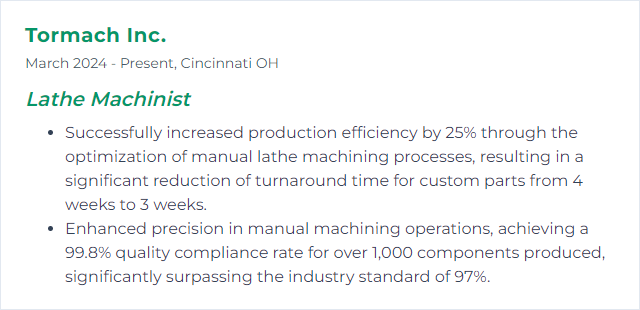
8. Haas Control
Haas Control is a user-friendly computer numerical control (CNC) system designed for operating and programming Haas CNC lathe machines, enabling machinists to efficiently manage and execute machining operations.
Why It's Important
Haas Control is important for a lathe machinist because it provides an intuitive, user-friendly interface for programming and operating the lathe, enhancing precision, efficiency, and productivity in machining tasks.
How to Improve Haas Control Skills
Improving Haas Control for a lathe machinist involves enhancing precision, efficiency, and understanding of the machine's capabilities. Here's a concise guide:
Familiarize with Haas Control Manuals: Deeply understanding the Haas Lathe Operator's Manual is crucial. Haas provides comprehensive manuals online that cover various models and control systems.
Utilize Haas Training Resources: Haas offers online training that can greatly improve your proficiency with their control systems.
Optimize Programming Skills: Improve G-code programming skills through practice and courses. Websites like G-Code Tutor offer tutorials specifically tailored to Haas controls.
Maintenance and Calibration: Regularly check and maintain the lathe for accuracy. Haas provides maintenance procedures that help keep the machine in top condition.
Use Simulation Software: Before executing programs, use simulation software to preview and adjust operations. This helps in minimizing errors and improving efficiency.
Join User Forums: Engage with communities such as CNCZone or the Practical Machinist forums. Sharing experiences and solutions with fellow machinists can provide valuable insights.
Experiment with Advanced Features: Explore and utilize Haas's advanced control features such as Dynamic Work Offsets, Tool Load Monitoring, and High-Speed Machining options to enhance machining processes.
Focusing on these areas will significantly improve your proficiency with Haas Control, leading to better performance and efficiency on a lathe.
How to Display Haas Control Skills on Your Resume
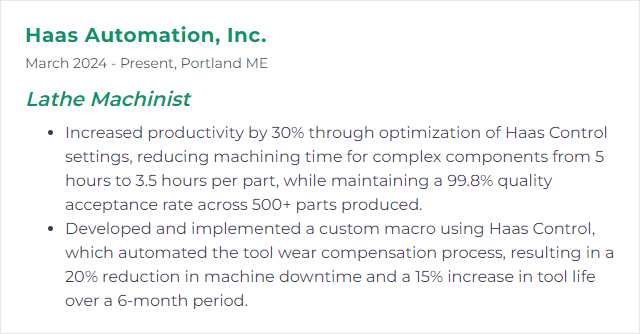
9. Fanuc Control
Fanuc Control is a computer numerical control (CNC) system used in precision machining, offering a user-friendly interface for programming and operating lathes, enabling machinists to efficiently control the cutting and shaping of materials.
Why It's Important
Fanuc Control is crucial for a Lathe Machinist as it provides precise and efficient control over the lathe machine operations, enabling the production of complex parts with high accuracy and repeatability, optimizing productivity and reducing errors in machining processes.
How to Improve Fanuc Control Skills
Improving Fanuc control for a lathe machinist involves optimizing programming, operation, and maintenance. Here are concise strategies:
Understand G-Code and M-Code: Mastery of G-codes (for geometry) and M-codes (for machine functions) enhances programming efficiency. Fanuc G-Code & M-Code List.
Utilize Manuals and Tutorials: Refer to Fanuc manuals and online tutorials to deepen your understanding. Fanuc Manuals.
Custom Macros: Learn to write and use custom macros for repetitive tasks, reducing programming time. Macro Programming.
Maintenance: Regular maintenance ensures optimal performance. Cleanliness, checking alignments, and replacing worn components are critical. Maintenance Tips.
Software Updates: Keep the control software updated to leverage improvements and new features. Fanuc Software Updates.
Optimize Cutting Conditions: Experiment with cutting speeds, feeds, and tool paths for efficiency. Machining Optimization.
Simulation Software: Use simulation software to preview and correct programs, reducing errors and setup time. NC Simulation.
Networking and Sharing: Connect with other machinists and forums to share tips and tricks. CNC Zone.
Practical Training: Engage in hands-on training sessions or workshops to improve operational skills. Fanuc Academy.
Efficient Workflows: Organize your work environment and programming for smoother operations. Lean Manufacturing Principles.
By focusing on these areas, a lathe machinist can significantly enhance the performance and efficiency of Fanuc control systems.
How to Display Fanuc Control Skills on Your Resume

10. Quality Inspection
Quality inspection for a Lathe Machinist involves systematically examining the finished parts produced by the lathe machine to ensure they meet the specified dimensions, tolerances, and surface finish requirements according to the design specifications or standards.
Why It's Important
Quality inspection is crucial for a Lathe Machinist to ensure that machined parts meet precise specifications and quality standards, reducing rework, waste, and ensuring customer satisfaction and safety.
How to Improve Quality Inspection Skills
To improve Quality Inspection as a Lathe Machinist, follow these steps:
Understand Specifications: Familiarize yourself thoroughly with the job specifications and tolerances. ASME provides standards and codes that serve as a fundamental reference.
Regular Calibration: Ensure all measurement tools and equipment are regularly calibrated. NIST offers guidelines for calibration standards.
Use of Precision Instruments: Invest in high-quality micrometers, calipers, and other precision instruments for accurate measurements. Mitutoyo is a reputable supplier of precision measuring tools.
Implement Statistical Process Control (SPC): Utilize SPC techniques to monitor and control the manufacturing process. MoreSteam provides an introduction to SPC.
Continuous Training: Engage in continuous learning and training to stay updated with the latest machining and inspection techniques. Tooling U-SME offers courses tailored for machinists.
First Article Inspection (FAI): Conduct a comprehensive inspection of the first part manufactured to ensure all processes are correctly set up. AS9102 defines FAI requirements.
Feedback and Adjustment: Implement a feedback loop from the quality inspection to the machining process for immediate adjustments and continuous improvement.
Adhering to these steps will significantly enhance the quality inspection process in lathe machining operations.
How to Display Quality Inspection Skills on Your Resume
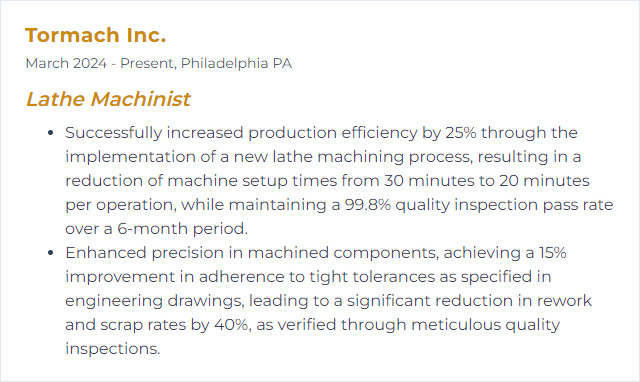
11. Metalworking Fluids
Metalworking fluids are lubricants used in machining processes, such as on a lathe, to cool and lubricate the cutting tool and workpiece, reduce friction and wear, and improve the quality of the workpiece by preventing metal chips from adhering to the tool.
Why It's Important
Metalworking fluids are crucial for a lathe machinist because they lubricate the cutting tool and workpiece, reduce heat and friction, and help remove chips from the cutting area, leading to smoother cuts, longer tool life, and improved workpiece quality.
How to Improve Metalworking Fluids Skills
Improving metalworking fluids (MWFs) for lathe machinists involves enhancing their performance, longevity, and safety. Here are succinct strategies:
Selection: Choose the correct fluid type (e.g., oils, emulsions, synthetics) based on the material being machined and the machining operation. Master Fluid Solutions offers a comprehensive guide to selecting appropriate MWFs.
Maintenance: Regularly monitor and maintain fluid concentration, pH levels, and cleanliness to extend fluid life and prevent corrosion or bacterial growth. The Society of Tribologists and Lubrication Engineers (STLE) provides resources on MWF maintenance.
Filtration: Implement fine filtration systems to remove contaminants and particulates, improving fluid performance and reducing wear on tools and machines. Filtermist specializes in systems for extracting and filtering metalworking fluids.
Coolant Management: Adopt a comprehensive coolant management plan, including proper mixing, delivery, and disposal practices, to enhance efficiency and environmental compliance. Machinery Lubrication offers insights on effective coolant management.
Worker Safety: Ensure safety by using fluids with low toxicity levels, providing adequate ventilation, and using personal protective equipment (PPE) to minimize exposure to MWF mists and aerosols. The Occupational Safety and Health Administration (OSHA) has guidelines on safe handling of MWFs.
By focusing on the right selection, maintenance, filtration, management practices, and safety considerations, lathe machinists can significantly improve the performance and life span of their metalworking fluids.
How to Display Metalworking Fluids Skills on Your Resume
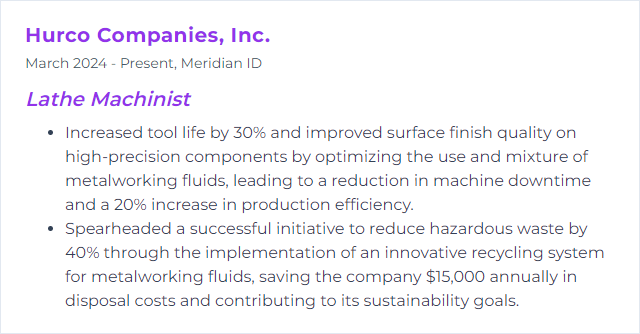
12. Safety Protocols
Safety protocols for a lathe machinist include wearing appropriate personal protective equipment (PPE), ensuring workpieces are securely clamped, using machine guards, keeping the work area clean, and never leaving the machine running unattended.
Why It's Important
Safety protocols are crucial for a Lathe Machinist to prevent accidents, protect against injuries from sharp tools and rotating parts, and ensure safe operation of machinery, thereby maintaining a secure and efficient working environment.
How to Improve Safety Protocols Skills
Improving safety protocols for a Lathe Machinist involves several key steps, focusing on training, equipment maintenance, and the work environment. Here’s a concise guide:
Training: Ensure all machinists undergo comprehensive safety training specific to lathe operations, including the use of personal protective equipment (PPE) and emergency procedures.
Regular Maintenance: Implement a strict maintenance schedule for the lathe to ensure it's in safe working condition, reducing the risk of accidents due to equipment failure.
Use of PPE: Enforce the use of appropriate Personal Protective Equipment, such as safety glasses, gloves, and ear protection, tailored to the hazards present in lathe operations.
Safe Work Practices: Develop and enforce safe work practices, like never leaving the machine running unattended and checking for secure workpiece attachment before beginning lathe operations.
Emergency Preparedness: Ensure clear, easily accessible emergency stops are in place and that all machinists know how to quickly shut down equipment in an emergency.
By focusing on these areas, you can significantly improve safety protocols for lathe machinists, creating a safer working environment.
How to Display Safety Protocols Skills on Your Resume
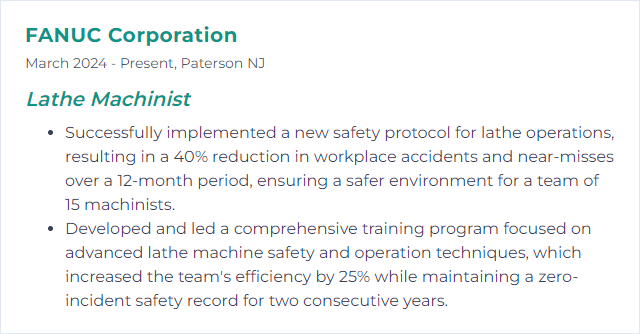