Top 12 Warehouse Operator Skills to Put on Your Resume
In today's competitive job market, standing out as a warehouse operator requires more than just basic knowledge of inventory and equipment handling. Highlighting a comprehensive set of skills on your resume can significantly enhance your attractiveness to employers, showcasing your capability to efficiently manage tasks, lead teams, and ensure operational success in the fast-paced warehouse environment.
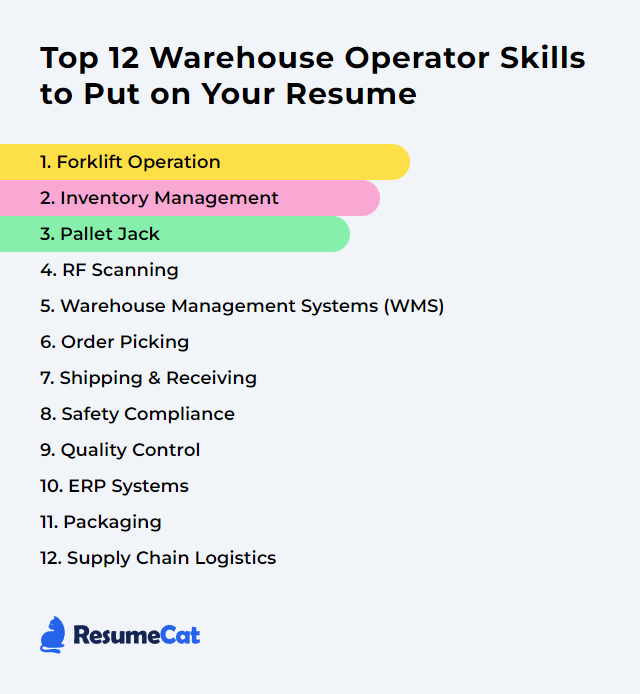
Warehouse Operator Skills
- Forklift Operation
- Inventory Management
- Pallet Jack
- RF Scanning
- Warehouse Management Systems (WMS)
- Order Picking
- Shipping & Receiving
- Safety Compliance
- Quality Control
- ERP Systems
- Packaging
- Supply Chain Logistics
1. Forklift Operation
Forklift operation involves maneuvering a powered industrial truck equipped with a forked platform to lift, transport, and stack goods within a warehouse environment, ensuring efficient material handling and storage.
Why It's Important
Forklift operation is crucial for a Warehouse Operator as it enhances efficiency in material handling, ensures safety in moving heavy loads, and optimizes storage space by allowing for the stacking of goods at various heights.
How to Improve Forklift Operation Skills
Improving forklift operation in a warehouse setting involves enhancing safety, efficiency, and operator skill. Here are concise steps to achieve this:
Training & Certification: Ensure all operators complete OSHA-certified forklift training to understand safety protocols and operation techniques.
Regular Maintenance: Implement a preventive maintenance schedule for forklifts to reduce breakdowns and extend equipment lifespan.
Safety First: Enforce strict adherence to safety protocols, including speed limits, load capacity limits, and wearing seat belts. Utilize resources like NIOSH's forklift safety guide for best practices.
Efficient Layout & Signage: Design the warehouse for easy navigation and minimal obstructions. Use clear signage for forklift operation areas, as outlined by Warehousing's best practices.
Continuous Learning: Encourage ongoing learning and skill development through resources like Forklift Academy for advanced operational techniques.
Use of Technology: Implement technology like telematics systems to monitor forklift usage, maintenance needs, and operator behavior, as discussed by Logistics Management.
By focusing on these areas, a warehouse operator can significantly improve forklift operation, enhancing safety, efficiency, and productivity.
How to Display Forklift Operation Skills on Your Resume
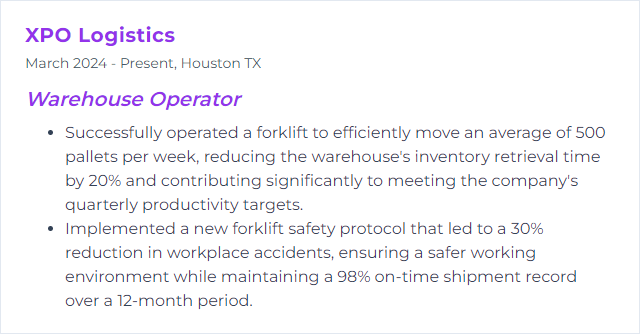
2. Inventory Management
Inventory management for a warehouse operator involves systematically overseeing the ordering, storing, and distributing of goods within a warehouse to ensure optimal stock levels, reduce costs, and meet customer demand efficiently.
Why It's Important
Inventory management is crucial for a Warehouse Operator as it ensures the right stock levels are maintained to meet demand without overstocking, minimizes storage costs, and prevents stockouts, thereby optimizing operations and enhancing customer satisfaction.
How to Improve Inventory Management Skills
Improving inventory management as a Warehouse Operator involves the implementation of strategies and tools designed to optimize stock levels, reduce errors, and ensure efficient operations. Here are concise steps to enhance inventory management:
Implement an Inventory Management System: Use software that integrates with your warehouse operations for real-time tracking and management. Shopify and QuickBooks Commerce offer solutions tailored to various business sizes.
Adopt Barcode or RFID Technology: Simplify tracking and reduce errors by tagging inventory with barcode or RFID systems for quick scanning and updating of stock levels.
Regular Stock Audits: Periodically verify actual stock against system records to identify discrepancies. Tools like Sortly can assist in organizing audits and keeping track of inventory.
Improve Forecasting: Utilize historical sales data and market trends to predict future inventory needs. Software like DemandCaster helps in accurate demand forecasting.
Optimize Warehouse Layout: Ensure efficient space utilization and minimize retrieval time by organizing inventory based on turnover rates and size. SmartDraw offers warehouse layout design tools.
Establish Reorder Points: Set minimum stock levels that trigger automatic reordering to avoid stockouts and overstocking. Inventory management systems often have features to set these points.
Embrace Lean Inventory: Adopt principles of lean inventory to minimize waste and focus on stocking items that add value to your operations. Kanban is a popular methodology for implementing lean principles.
Cross-Train Employees: Ensure staff is versatile and can perform multiple roles within the warehouse to improve efficiency and coverage. LinkedIn Learning offers courses on inventory management and warehouse operations.
By implementing these strategies, Warehouse Operators can significantly improve their inventory management practices, leading to increased efficiency, reduced costs, and higher customer satisfaction.
How to Display Inventory Management Skills on Your Resume
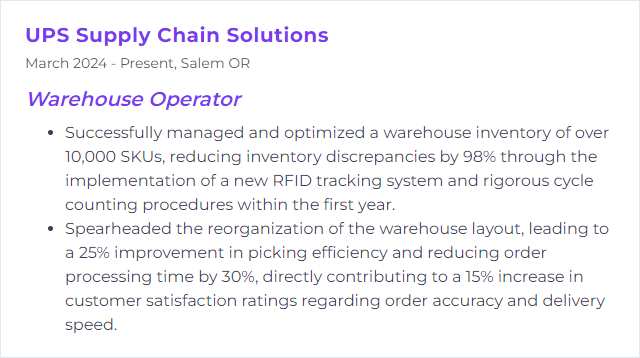
3. Pallet Jack
A pallet jack is a manual or powered tool used by warehouse operators to lift and move pallets, aiding in the transportation of goods within a warehouse environment.
Why It's Important
A pallet jack is crucial for a warehouse operator because it enables efficient movement and handling of heavy goods and pallets, significantly improving productivity and reducing manual labor efforts.
How to Improve Pallet Jack Skills
Improving the efficiency and safety of a pallet jack, essential for warehouse operations, involves regular maintenance, proper usage, and ergonomic enhancements. Here’s a concise guide:
Regular Maintenance: Keep the pallet jack in top condition by regularly checking and maintaining its wheels, bearings, and hydraulic system. OSHA provides guidelines on equipment maintenance to ensure safety and efficiency.
Proper Training: Ensure operators are trained on correct usage to prevent strain and accidents. Training should include lifting techniques and how to navigate tight spaces. The National Safety Council offers resources on workplace safety training.
Ergonomic Handles: Upgrade to ergonomic handles to reduce strain on operators. This small change can significantly increase comfort and control.
Use of Accessories: Employ accessories like skid busters and pallet jack chocks to improve efficiency and safety in the warehouse. Accessories can be found on industry-specific sites like Uline or Global Industrial.
Regular Inspections: Conduct daily inspections to catch and address issues early, minimizing downtime. A checklist can be developed based on manufacturer recommendations and ANSI standards.
Weight Management: Adhere to the pallet jack’s weight limit to prevent overloading, which can lead to equipment failure or operator injury. Information on weight limits and safe operation can typically be found in the user manual or on the manufacturer’s website.
By implementing these strategies, warehouse operators can enhance the performance, safety, and lifespan of their pallet jacks.
How to Display Pallet Jack Skills on Your Resume
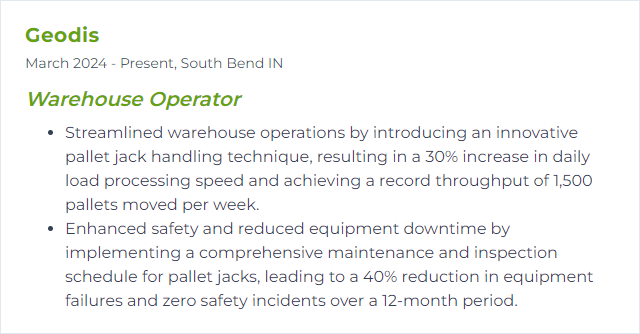
4. RF Scanning
RF Scanning, in the context of a Warehouse Operator, refers to the use of Radio Frequency scanners to track and manage inventory by scanning barcodes on items, enabling real-time updates on stock levels, locations, and movements within the warehouse.
Why It's Important
RF Scanning is crucial for a Warehouse Operator because it enhances inventory accuracy, streamlines picking and packing processes, and reduces errors, ultimately improving efficiency and customer satisfaction.
How to Improve RF Scanning Skills
Improving RF scanning for a warehouse operator involves optimizing both hardware and software components, as well as enhancing user training and ergonomics. Here's a concise guide:
Hardware Upgrade: Ensure RF scanners are up-to-date. Modern scanners offer better range, battery life, and durability. Zebra and Honeywell are reputable brands.
Software Integration: Use warehouse management systems (WMS) that seamlessly integrate with your RF equipment, reducing errors and increasing efficiency. Oracle WMS and SAP EWM are notable examples.
User Training: Regularly train staff on optimal scanning techniques and ergonomics to reduce fatigue and increase productivity. It might be beneficial to create a simple guide or tutorial for new employees.
Ergonomics and Accessibility: Provide equipment such as holsters or mounts to reduce physical strain and improve accessibility. This also helps in keeping the scanners safe and readily available.
Maintenance and Support: Regularly service your RF scanning equipment and ensure that you have prompt technical support to deal with any issues that arise, minimizing downtime.
Feedback System: Implement a feedback loop where workers can report issues or suggest improvements regarding the scanning process. This can uncover valuable insights to enhance efficiency.
By focusing on these areas, a warehouse can significantly improve its RF scanning process, leading to increased accuracy, efficiency, and worker satisfaction.
How to Display RF Scanning Skills on Your Resume
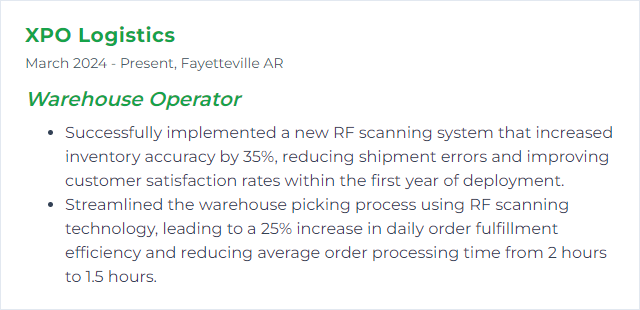
5. Warehouse Management Systems (WMS)
A Warehouse Management System (WMS) is a software solution that assists warehouse operators in managing and optimizing the storage, movement, and processing of goods within a warehouse, ensuring efficient inventory control, order fulfillment, and resource allocation.
Why It's Important
A Warehouse Management System (WMS) is crucial for a Warehouse Operator as it optimizes inventory management, enhances order fulfillment accuracy, improves space utilization, and increases operational efficiency, directly contributing to reduced operational costs and improved customer satisfaction.
How to Improve Warehouse Management Systems (WMS) Skills
Improving Warehouse Management Systems (WMS) requires a strategic approach focused on optimization, integration, and continuous improvement. Here’s a concise guide for Warehouse Operators:
Optimize Inventory Layout: Design the warehouse layout to minimize travel time and improve efficiency. Implement slotting optimization to place items based on their picking frequency. Material Handling Institute offers resources on warehouse optimization techniques.
Integrate Technologies: Enhance your WMS by integrating it with other systems such as ERP (Enterprise Resource Planning) and TMS (Transportation Management Systems) for seamless operations. The Council of Supply Chain Management Professionals (CSCMP) provides insights into effective system integration.
Adopt Automation and Robotics: Incorporate automation technologies like Automated Guided Vehicles (AGVs), conveyor belts, and robotic pickers to reduce manual errors and increase efficiency. Robotics Business Review shares the latest in warehouse automation.
Implement Advanced Picking Strategies: Utilize methods such as batch picking, zone picking, and wave picking to streamline operations. The Warehouse Education and Research Council (WERC) offers best practices on picking strategies.
Leverage Data Analytics: Use data analytics to predict trends, manage inventory levels effectively, and make informed decisions. Gartner publishes research on leveraging data in supply chain management.
Continuous Training and Feedback: Regularly train staff on system updates and encourage feedback for improvements. The Association for Supply Chain Management (ASCM) provides resources on training and development.
Regular System Updates and Maintenance: Work with your WMS provider to ensure your system is always up to date with the latest features and security patches.
By focusing on these areas, Warehouse Operators can significantly improve the efficiency and effectiveness of their Warehouse Management Systems.
How to Display Warehouse Management Systems (WMS) Skills on Your Resume
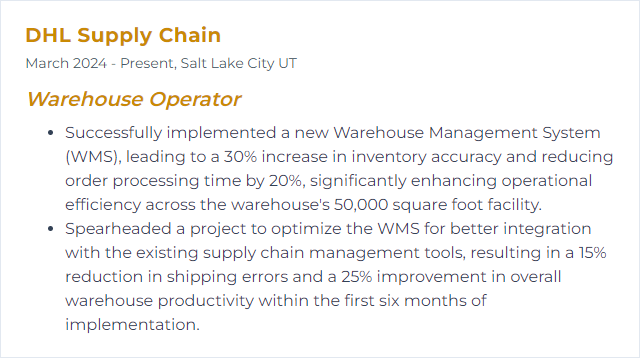
6. Order Picking
Order picking is the process a warehouse operator undertakes to collect and prepare items from a warehouse to fulfill customer orders.
Why It's Important
Order picking is crucial for a warehouse operator because it directly affects customer satisfaction by ensuring accurate and timely delivery of products, thereby also impacting the efficiency of the warehouse operations and inventory management.
How to Improve Order Picking Skills
Improving order picking in a warehouse involves strategic changes to processes and the use of technology to enhance efficiency and accuracy. Here’s a concise guide:
Optimize Layout: Design warehouse layout to minimize travel time between picks. Place high-demand items closer to packing areas. Material Handling and Logistics offers tips on layout optimization.
Implement Batch Picking: Group similar orders to reduce trips. Shopify’s guide explains how this can be streamlined with a Warehouse Management System (WMS).
Use Technology: Adopt a WMS for real-time inventory tracking and order management. RFID and barcode scanning can also reduce errors. Capterra lists software options with reviews.
Adopt Voice Picking: Voice-directed picking can improve accuracy and productivity by allowing hands-free operation. Supply Chain Dive discusses its benefits.
Continual Training: Regularly train staff on new technologies and picking strategies to ensure efficiency. The Balance SMB provides insight into effective training methods.
Measure and Analyze Performance: Use Key Performance Indicators (KPIs) to track picking accuracy, speed, and efficiency. Adjust strategies based on performance data. Logiwa outlines relevant KPIs to monitor.
Implementing these strategies requires a combination of layout optimization, technology adoption, and continuous improvement practices to enhance order picking efficiency in a warehouse setting.
How to Display Order Picking Skills on Your Resume
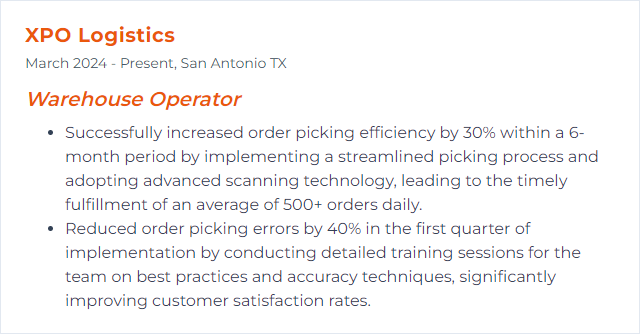
7. Shipping & Receiving
Shipping & Receiving, in the context of a Warehouse Operator, involves the processes of accepting incoming goods, inspecting them for accuracy and damage, storing them appropriately, and then preparing and sending out goods to their next destination.
Why It's Important
Shipping and Receiving are crucial for a Warehouse Operator as they ensure the accurate and timely movement of goods in and out of the warehouse, maintaining inventory levels, and fulfilling customer orders efficiently. This process is essential for operational success, customer satisfaction, and the overall profitability of the business.
How to Improve Shipping & Receiving Skills
Improving Shipping & Receiving in a warehouse involves several key strategies to enhance efficiency, accuracy, and speed. Here's a concise guide:
Implement a Warehouse Management System (WMS): A WMS can significantly streamline operations by automating tasks and providing real-time inventory visibility. Shopify's guide on choosing a WMS is a great place to start.
Optimize Layout and Workflow: Design your warehouse layout to minimize travel time and ensure smooth flow from receiving to shipping. Incorporate principles of lean management. The Lean Way offers insights on employing the 5S system for efficiency.
Standardize Processes: Create standard operating procedures (SOPs) for all tasks to reduce errors and training time. ASQ provides a basic understanding of SOPs and their importance.
Invest in Training: Regularly train staff on best practices, safety, and technology use to improve performance. OSHA offers safety training resources.
Adopt Barcode or RFID Technology: These technologies improve inventory accuracy and speed up receiving and shipping processes. Barcoding, Inc. explains the advantages and applications of barcode and RFID solutions.
Regular Audits and Continuous Improvement: Conduct regular audits of processes and use metrics to identify areas for improvement. Implement a continuous improvement culture. Lean.org dives into continuous improvement strategies.
Foster Vendor Relationships: Work closely with your suppliers and logistics providers to ensure timely deliveries and address issues proactively. Harvard Business Review offers negotiation tips with powerful suppliers.
By focusing on these areas, a Warehouse Operator can significantly enhance the efficiency and reliability of their Shipping & Receiving operations.
How to Display Shipping & Receiving Skills on Your Resume
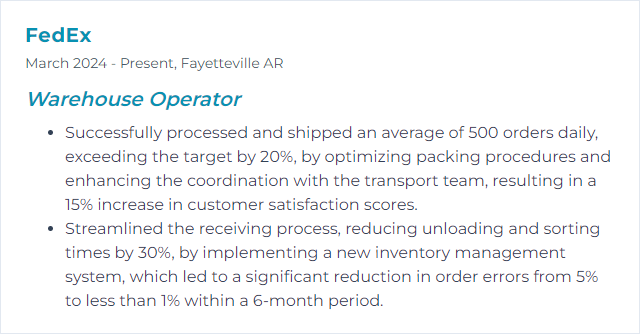
8. Safety Compliance
Safety Compliance for a Warehouse Operator involves adhering to established safety regulations and guidelines to ensure a safe working environment, prevent accidents, and protect the health of employees and visitors.
Why It's Important
Safety compliance is crucial for a warehouse operator to prevent workplace accidents, minimize health risks, and ensure a safe working environment, ultimately reducing legal liabilities and promoting operational efficiency.
How to Improve Safety Compliance Skills
To improve safety compliance as a Warehouse Operator, follow these concise strategies:
Risk Assessment: Regularly conduct risk assessments to identify potential hazards. Implement preventive measures accordingly. OSHA Guidelines on Hazard Identification
Safety Training: Provide ongoing safety training and drills for all employees. Ensure they understand the importance of compliance. NIOSH Training for Warehouse Workers
Maintain Equipment: Regularly inspect and maintain all warehouse equipment to ensure it's in safe working order. Maintenance Checklist
Clear Signage: Install clear safety signage and floor markings throughout the warehouse to guide employees and prevent accidents. Effective Signage Strategies
Emergency Preparedness: Develop and communicate emergency procedures, including evacuation plans and first aid responses. Ready.gov Business Preparedness
Safety Gear: Require and provide appropriate personal protective equipment (PPE) for all staff. OSHA PPE Standards
Engagement and Feedback: Encourage employee engagement by creating channels for reporting hazards and suggesting improvements. Creating a Safety Culture
By implementing these strategies, you can significantly improve safety compliance in your warehouse, ensuring a safer work environment for all employees.
How to Display Safety Compliance Skills on Your Resume
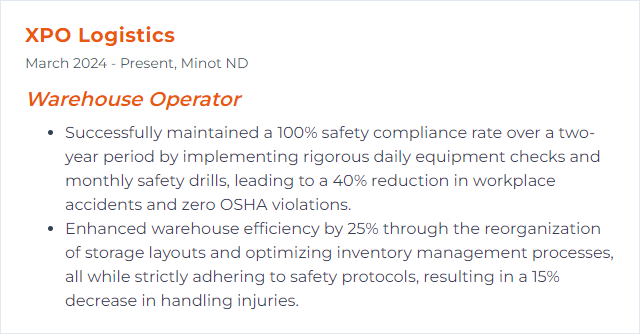
9. Quality Control
Quality Control for a Warehouse Operator involves systematically inspecting and verifying the condition and correctness of incoming and outgoing goods to ensure they meet established standards of quality, safety, and customer specifications.
Why It's Important
Quality Control is crucial for a Warehouse Operator to ensure that inventory is accurate, goods are stored safely, and products meet the required standards before shipment, minimizing errors, returns, and enhancing customer satisfaction.
How to Improve Quality Control Skills
Improving quality control for a Warehouse Operator involves several straightforward steps:
Standardize Processes: Establish clear, standardized procedures for all warehouse operations. The International Organization for Standardization (ISO) provides guidelines that can be adapted to enhance quality control.
Implement a Quality Management System (QMS): Adopt a QMS like ISO 9001, which focuses on meeting customer requirements and enhancing satisfaction through continuous improvement.
Regular Training: Ensure staff are regularly trained on the latest warehouse operations and quality control procedures. The Warehousing Education and Research Council (WERC) offers resources and training for warehouse professionals.
Utilize Technology: Invest in warehouse management systems (WMS) and other technologies that automate and streamline processes, reducing the chance of human error. Information on WMS can be found through Capterra, which provides software reviews and insights.
Continuous Improvement: Adopt lean methodologies and six sigma for continuous improvement of processes. The American Society for Quality (ASQ) offers resources on these methodologies.
Regular Audits and Inspections: Conduct regular internal audits and inspections to identify areas for improvement. Guidelines for effective auditing can be found on ISO’s auditing page.
Feedback Loop: Establish a feedback loop with both employees and customers to gather insights and areas of improvement. This can help in adjusting operations to better meet quality standards.
By focusing on these areas, a Warehouse Operator can significantly improve their quality control measures, leading to more efficient operations and higher customer satisfaction.
How to Display Quality Control Skills on Your Resume
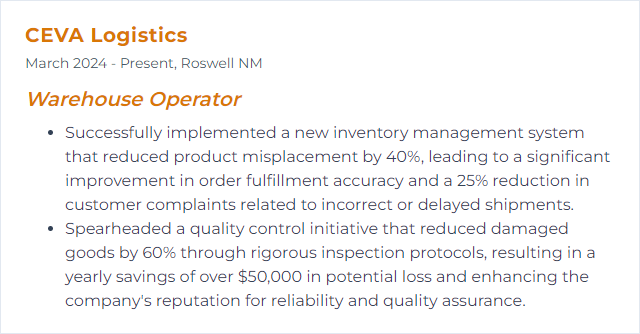
10. ERP Systems
ERP (Enterprise Resource Planning) systems are integrated software platforms used by organizations, including warehouse operators, to manage and automate core business processes such as inventory management, order processing, and supply chain operations, ensuring efficiency and real-time data visibility across all departments.
Why It's Important
ERP systems streamline and integrate core business processes, including inventory management, helping a Warehouse Operator efficiently track and manage stock levels, orders, and deliveries, ensuring timely fulfillment and reducing operational costs.
How to Improve ERP Systems Skills
Improving ERP systems, especially for Warehouse Operators, involves enhancing efficiency, accuracy, and real-time data accessibility. Here’s a concise guide:
Integration with IoT Devices: Connect ERP systems with Internet of Things (IoT) devices for real-time tracking of inventory and equipment. This integration ensures accurate stock levels and operational status updates.
Customization and Scalability: Tailor the ERP system to fit specific warehouse needs and ensure it can scale with business growth. This customization enhances functionality and user adoption.
Implement Mobile Solutions: Use mobile ERP applications to allow warehouse staff to access and input data directly from the warehouse floor, improving accuracy and efficiency. Read more about mobile ERP solutions.
Training and Support: Provide continuous training and support to ensure users are proficient and can troubleshoot minor issues independently. This approach enhances system utilization and efficiency.
Data Analysis and Reporting: Leverage advanced analytics and reporting tools within the ERP system to make informed decisions based on real-time data. Insightful data analysis can optimize warehouse operations and inventory management.
Regular Updates and Maintenance: Keep the ERP system updated with the latest software versions and security patches to maintain performance and protect against vulnerabilities.
By focusing on these areas, Warehouse Operators can significantly improve the efficiency and effectiveness of their ERP systems.
How to Display ERP Systems Skills on Your Resume
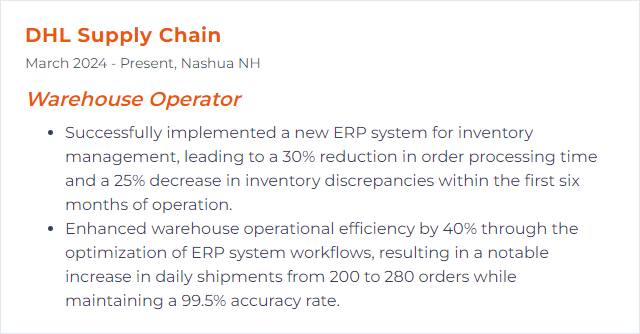
11. Packaging
Packaging in the context of a warehouse operator refers to the process of preparing goods for safe storage and efficient distribution, involving wrapping, boxing, or securing products to ensure they are protected during handling, shipping, and delivery.
Why It's Important
Packaging is crucial for a Warehouse Operator as it ensures product protection during storage and transit, facilitates efficient handling and stacking, and helps in maintaining product integrity, thereby reducing damage and loss.
How to Improve Packaging Skills
Improving packaging in a warehouse setting focuses on enhancing efficiency, sustainability, and product safety. Here are concise strategies:
Optimize Design: Use software like Packaging Design for 3D prototypes to minimize material use and optimize space.
Sustainability: Incorporate eco-friendly materials. Explore alternatives through the Sustainable Packaging Coalition.
Automation: Implement packaging machines for speed and consistency. Packaging Machinery Manufacturers Institute (PMMI) offers insights on automation solutions.
Employee Training: Regularly update staff on best practices through platforms like LinkedIn Learning.
Quality Materials: Use durable materials to reduce damage. Suppliers like Uline provide a wide range of quality packaging materials.
Custom Packaging: Tailor packages to product dimensions for material efficiency and protection. Tools like Packsize offer custom packaging solutions.
Regular Review: Continuously assess and improve packaging processes based on feedback and new technologies.
Focusing on these areas will significantly improve packaging efficiency, sustainability, and product protection in a warehouse environment.
How to Display Packaging Skills on Your Resume
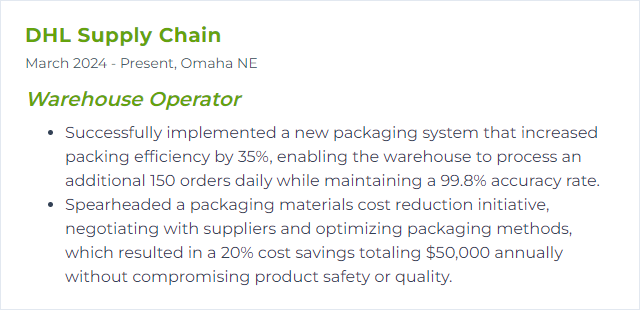
12. Supply Chain Logistics
Supply Chain Logistics, for a Warehouse Operator, involves the efficient management, storage, and movement of goods from their point of origin to the end consumer, ensuring timely delivery and inventory accuracy.
Why It's Important
Supply chain logistics is crucial for a Warehouse Operator as it ensures the efficient and timely movement, storage, and delivery of goods, optimizing space and resources, reducing costs, and ultimately satisfying customer demands effectively.
How to Improve Supply Chain Logistics Skills
Improving supply chain logistics, especially for a warehouse operator, involves optimizing operations to enhance efficiency, reduce costs, and improve service levels. Here are key strategies:
Implement an Efficient Warehouse Management System (WMS): Choose a WMS that integrates seamlessly with your inventory, order management systems, and supply chain partners. Shopify offers insights on selecting a suitable system.
Adopt Lean Inventory Practices: Minimize waste by keeping stock levels closely aligned with demand forecasts. Techniques like Just-In-Time (JIT) can significantly reduce inventory costs. LeanCor provides a detailed explanation.
Optimize Warehouse Layout: Design your warehouse layout to minimize movement and handling. Efficiently organized pick zones and storage areas can substantially increase productivity. The Balance Small Business outlines key considerations.
Leverage Automation and Robotics: Implement automation for repetitive tasks. Robotics can significantly increase picking efficiency and accuracy. Robotics Business Review discusses the impact on the logistics industry.
Enhance Supplier and Partner Collaboration: Foster strong relationships with suppliers and logistics partners. Collaborative planning and shared data can lead to more efficient operations. Supply Chain 24/7 highlights the importance of collaboration.
Regularly Analyze and Optimize Your Supply Chain: Continuously assess performance data to identify bottlenecks and inefficiencies. Use this data to refine your operations. Deloitte offers insights on leveraging analytics for optimization.
Implementing these strategies requires a commitment to continuous improvement and investment in technology. However, the payoff in enhanced efficiency, reduced costs, and improved customer satisfaction can be substantial.
How to Display Supply Chain Logistics Skills on Your Resume
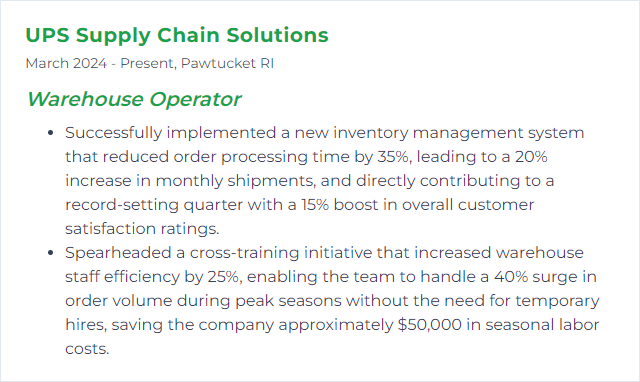