Top 12 Warehouse Clerk Skills to Put on Your Resume
In today's logistics and supply chain industry, warehouse clerks play a pivotal role in ensuring the smooth operation of storage facilities. Highlighting a set of top-notch skills on your resume can significantly elevate your candidacy, showcasing your ability to efficiently manage inventory, execute orders, and contribute to the overall productivity of a warehouse environment.
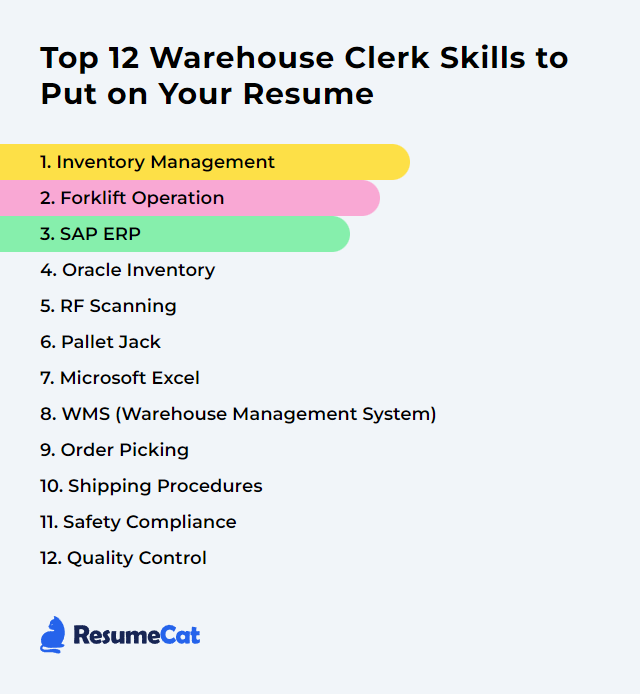
Warehouse Clerk Skills
- Inventory Management
- Forklift Operation
- SAP ERP
- Oracle Inventory
- RF Scanning
- Pallet Jack
- Microsoft Excel
- WMS (Warehouse Management System)
- Order Picking
- Shipping Procedures
- Safety Compliance
- Quality Control
1. Inventory Management
Inventory Management is the process of overseeing and controlling the flow of goods in and out of a warehouse, ensuring accurate stock levels, and organizing the storage of products for efficient retrieval and dispatch.
Why It's Important
Inventory management is crucial for a Warehouse Clerk as it ensures the right quantity of stock is available when needed, reduces excess inventory and storage costs, prevents stockouts and overstock scenarios, and improves order fulfillment accuracy and customer satisfaction.
How to Improve Inventory Management Skills
Improving inventory management, especially from the perspective of a Warehouse Clerk, involves a blend of organization, technology, and strategy. Here are concise tips:
Implement an Inventory Management System: Use software that provides real-time tracking of inventory levels, orders, and deliveries. Shopify and QuickBooks Commerce are popular options.
Regular Audits: Periodically perform physical counts to verify stock levels against your inventory system. This helps in identifying discrepancies early. Square offers tools that can simplify this process.
Optimize Warehouse Layout: Arrange your warehouse efficiently to minimize time spent on picking and packing. Group similar items together and place high-turnover items closer to the shipping area. Camcode provides insights into optimizing warehouse operations.
FIFO Method (First In, First Out): Ensure older stock is sold or used before newer stock. This is crucial for perishable goods. TradeGecko explains FIFO and LIFO methods in detail.
Set Reorder Points: Determine the minimum stock level at which you need to reorder each product. This prevents stockouts and overstocking. Tools like Zoho Inventory can automate this process.
Supplier Relationships: Maintain good relationships with suppliers for better reliability and potentially negotiate better terms. Harvard Business Review offers strategies on negotiating with suppliers.
Use Barcode or RFID Technology: Implement a barcode or RFID system to speed up inventory tracking and reduce errors. Barcodes Inc. provides an introduction to barcode systems.
Continuous Improvement: Always look for ways to refine your inventory management practices based on data analysis and feedback. Kanbanize discusses continuous improvement in inventory management.
By integrating these strategies, Warehouse Clerks can significantly enhance inventory management efficiency and accuracy, leading to overall operational improvements.
How to Display Inventory Management Skills on Your Resume
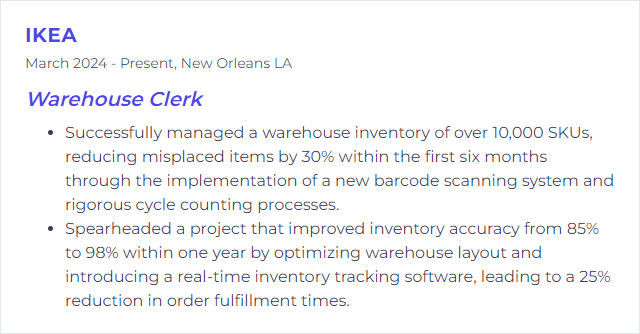
2. Forklift Operation
Forklift operation refers to the use and maneuvering of a forklift, a powered industrial truck, by a warehouse clerk to lift, move, and stack materials and goods within a warehouse setting efficiently and safely.
Why It's Important
Forklift operation is crucial for a Warehouse Clerk as it enables efficient movement, lifting, and placement of heavy goods and materials, significantly improving warehouse operations' speed, safety, and overall productivity.
How to Improve Forklift Operation Skills
Improving forklift operation in a warehouse setting involves enhancing safety, efficiency, and operator skill. Here are concise strategies:
- Training: Ensure all operators undergo comprehensive forklift training, including refreshers, to maintain high skill levels.
- Maintenance: Regularly schedule maintenance for forklifts to prevent breakdowns and ensure operational safety.
- Route Planning: Implement efficient route planning within the warehouse to minimize congestion and travel time.
- Safety Protocols: Enforce strict safety protocols, including speed limits, load capacity adherence, and pedestrian awareness.
- Regular Assessments: Conduct regular skill assessments for operators to identify areas for improvement.
- Use of Technology: Incorporate technology like warehouse management systems (WMS) for better inventory tracking and forklift task allocation.
By focusing on these areas, a Warehouse Clerk can significantly contribute to enhancing forklift operation efficiency and safety within their facility.
How to Display Forklift Operation Skills on Your Resume
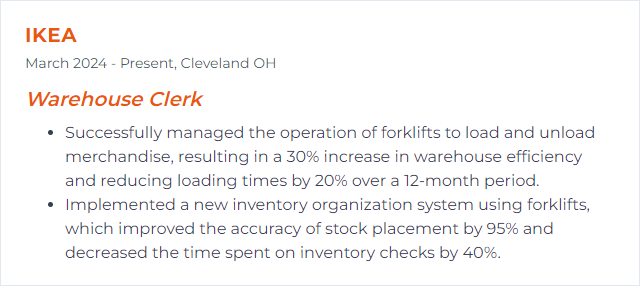
3. SAP ERP
SAP ERP is a comprehensive software system designed to manage and integrate all key business processes, including inventory and supply chain operations, providing real-time visibility and efficiency improvements for warehouse clerks in managing stock levels, orders, and deliveries.
Why It's Important
SAP ERP is important for a Warehouse Clerk as it streamlines inventory management, optimizes warehouse operations, and enhances accuracy in order fulfillment, leading to improved efficiency and productivity.
How to Improve SAP ERP Skills
Improving SAP ERP for a Warehouse Clerk involves enhancing data accuracy, process efficiency, and user experience. Consider the following steps:
Data Accuracy: Implement barcode scanning and RFID technology to ensure real-time inventory tracking and reduce manual data entry errors. SAP Extended Warehouse Management offers solutions for advanced tracking.
Process Efficiency: Utilize SAP's Warehouse Management module to streamline warehouse operations, including receiving, storing, and shipping goods. Automate routine tasks to save time and reduce human error.
User Training and Support: Provide comprehensive training and easy access to support resources to help warehouse clerks quickly adapt to the SAP system. SAP's Training and Certification program can be a valuable resource.
Mobile Solutions: Implement SAP's mobile solutions to allow warehouse clerks to access the ERP system from anywhere in the warehouse, improving productivity and decision-making. SAP Fiori offers user-friendly mobile apps.
Customization and Integration: Tailor the SAP system to meet the specific needs of your warehouse operations and ensure seamless integration with other tools and systems used in your organization. SAP's Integration Suite can facilitate this process.
By focusing on these areas, you can enhance the efficiency and effectiveness of warehouse operations, directly benefiting warehouse clerks and the broader organization.
How to Display SAP ERP Skills on Your Resume
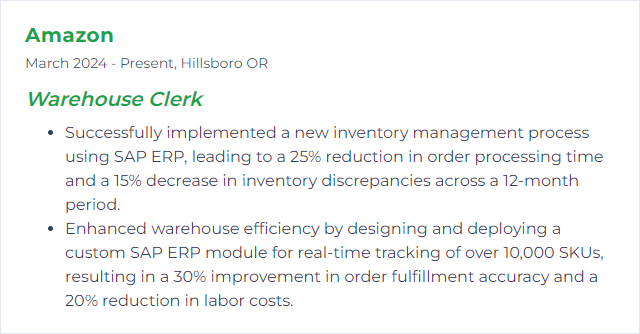
4. Oracle Inventory
Oracle Inventory is a comprehensive system designed to manage and control all inventory-related activities within a warehouse, including tracking stock levels, managing material transactions, and ensuring the accurate and efficient handling of goods, all aimed at optimizing the warehouse clerk's workflow and inventory accuracy.
Why It's Important
Oracle Inventory is important for a Warehouse Clerk as it streamlines inventory management, ensuring accurate tracking, and efficient organization of stock levels, leading to improved order fulfillment and reduced inventory costs.
How to Improve Oracle Inventory Skills
Improving Oracle Inventory for a Warehouse Clerk involves optimizing data accuracy, streamlining processes, and enhancing inventory tracking. Here's a concise guide:
Data Accuracy: Ensure all inventory transactions are accurately recorded in real-time. This includes receipts, issues, transfers, and adjustments. Accurate data entry minimizes discrepancies and improves inventory control.
Streamline Processes: Implement barcode scanning and RFID technologies to automate data capture. This reduces manual entry errors and speeds up transactions. Oracle's Inventory Management offers solutions for automation and process improvement.
Inventory Tracking: Utilize Oracle Inventory's advanced tracking features to monitor stock levels, location, and movement history. Set up alerts for low stock levels or high demand items to prevent stockouts and overstocking.
Training and Support: Ensure all warehouse staff are adequately trained on Oracle Inventory features and best practices. Oracle provides training and certification to help teams use their systems effectively.
Regular Audits: Conduct periodic physical inventory counts and reconcile with Oracle Inventory data to identify discrepancies early. This practice helps in maintaining data integrity and reliability.
Feedback Loop: Create a feedback mechanism where warehouse clerks can report issues or suggest improvements in inventory handling and data management. Continuous improvement is key to optimizing inventory operations.
By focusing on these areas, a Warehouse Clerk can significantly contribute to improving Oracle Inventory's efficiency and accuracy, leading to better inventory management and operational performance.
How to Display Oracle Inventory Skills on Your Resume
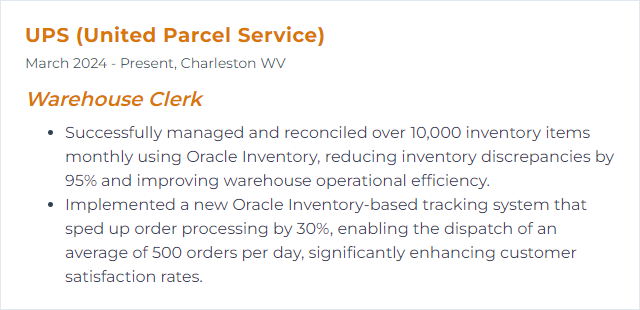
5. RF Scanning
RF Scanning, in the context of a Warehouse Clerk's duties, involves using radio frequency handheld devices to scan barcodes on items. This process efficiently tracks and manages inventory, facilitating accurate picking, packing, and stocking of goods within a warehouse environment.
Why It's Important
RF scanning is important for a Warehouse Clerk because it streamlines inventory management, enhances accuracy in tracking goods, and speeds up the process of receiving, storing, and shipping items, thus improving efficiency and reducing errors.
How to Improve RF Scanning Skills
To improve RF scanning as a Warehouse Clerk:
- Enhance Training: Ensure comprehensive training for staff on using RF scanners efficiently.
- Equipment Maintenance: Regularly maintain and update RF scanning devices to ensure their optimal performance.
- Optimize Layout: Organize warehouse layout to facilitate easy scanning, reducing the distance between items.
- Implement Software Solutions: Use inventory management software that integrates with RF scanning for real-time tracking and management.
- Regular Audits: Conduct regular audits to identify and rectify any inefficiencies in the RF scanning process.
By focusing on these areas, Warehouse Clerks can significantly improve the efficiency and accuracy of RF scanning operations.
How to Display RF Scanning Skills on Your Resume
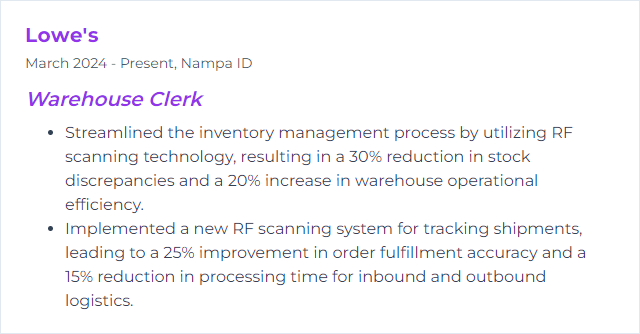
6. Pallet Jack
A pallet jack, also known as a pallet truck, is a manual or powered tool used by warehouse clerks to lift and move pallets within a warehouse.
Why It's Important
A pallet jack is crucial for a Warehouse Clerk as it enables efficient, safe, and easy movement of goods on pallets within the warehouse, significantly enhancing productivity and reducing manual labor efforts.
How to Improve Pallet Jack Skills
To enhance the efficiency and safety of using a pallet jack in a warehouse setting, consider the following concise tips:
Regular Maintenance: Ensure routine checks and maintenance are performed to keep the pallet jack in optimal condition. Focus on wheels, handle, and lifting mechanism. OSHA Maintenance Guidelines.
Proper Training: All operators should receive comprehensive training on safe operation, loading techniques, and navigating the warehouse. National Safety Council Training Resources.
Efficient Storage Layout: Organize warehouse layout to minimize obstructions and optimize pallet jack maneuverability. Effective Warehouse Layout Tips.
Use of Technology: Implement weight indicators or RFID technology to streamline operations and enhance safety. RFID Journal.
Ergonomic Improvements: Consider ergonomic handles or attachments to reduce strain on operators. Ergonomics in Material Handling.
Incorporating these strategies can significantly improve the functionality and safety of pallet jacks in a warehouse environment.
How to Display Pallet Jack Skills on Your Resume
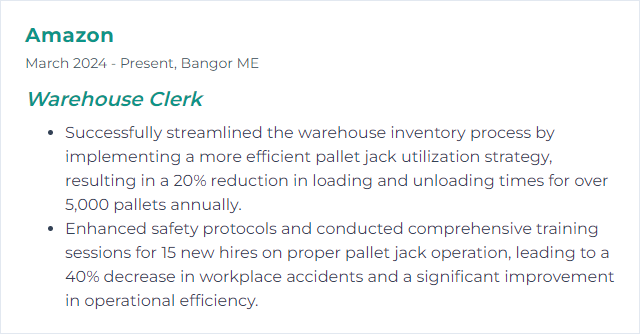
7. Microsoft Excel
Microsoft Excel is a spreadsheet program used for organizing, calculating, and analyzing data, essential for inventory tracking, order processing, and sales reporting tasks in a warehouse environment.
Why It's Important
For a Warehouse Clerk, Microsoft Excel is crucial for efficiently managing inventory, tracking shipments, organizing orders, and analyzing data to optimize warehouse operations.
How to Improve Microsoft Excel Skills
To improve Microsoft Excel skills for a Warehouse Clerk, focus on:
- Mastering Basic Formulas: Start with SUM, AVERAGE, COUNT. Basic Formulas Tutorial.
- Learning Shortcut Keys: Speed up your workflow. Shortcut Keys List.
- Utilizing Data Validation: Ensure data integrity in inventory records. Data Validation Guide.
- Creating Pivot Tables: Analyze large data sets for insights. Pivot Tables Tutorial.
- Implementing VLOOKUP/HLOOKUP: Simplify searches and comparisons. VLOOKUP Guide.
- Exploring Conditional Formatting: Highlight key information automatically. Conditional Formatting Basics.
- Automating Repetitive Tasks with Macros: Save time on routine tasks. Introduction to Macros.
These steps can significantly enhance efficiency and accuracy in warehouse data management tasks.
How to Display Microsoft Excel Skills on Your Resume
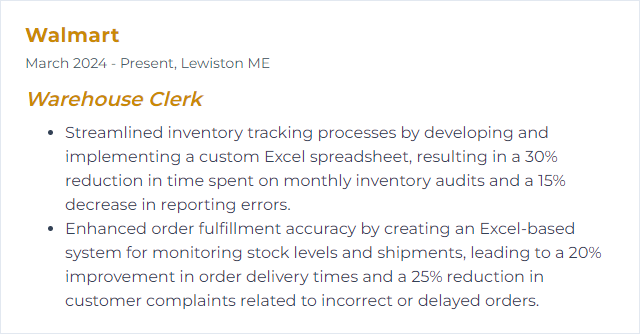
8. WMS (Warehouse Management System)
A Warehouse Management System (WMS) is a software tool designed to optimize and manage the operations within a warehouse, helping Warehouse Clerks track inventory levels, manage orders, and coordinate the storage and movement of goods efficiently.
Why It's Important
WMS is crucial for a Warehouse Clerk as it streamlines inventory management, improves accuracy in order fulfillment, and enhances productivity by automating manual tasks, leading to efficient warehouse operations.
How to Improve WMS (Warehouse Management System) Skills
Improving a Warehouse Management System (WMS) involves several key steps that can enhance efficiency, accuracy, and productivity. For a Warehouse Clerk, focusing on user training, data accuracy, and technology integration is crucial. Here's a concise guide:
Enhance User Training: Ensure all users, especially Warehouse Clerks, are fully trained on the WMS features and best practices. Continuous training programs can help adapt to updates or changes in the system. Training Resources.
Improve Data Accuracy: Emphasize the importance of accurate data entry, as it directly impacts inventory management and order fulfillment. Implement regular audits and validations. Data Management Tips.
Leverage Mobile Technology: Integrate mobile devices equipped with WMS applications to facilitate real-time data access, updates, and communication among warehouse staff. Mobile WMS Solutions.
Automate Processes: Identify repetitive tasks that can be automated (like picking and sorting) to reduce errors and save time. Automation can range from simple software functions to advanced robotics. Warehouse Automation Guide.
Regularly Update WMS Software: Ensure your WMS is up-to-date with the latest features and security patches. Regular updates can improve functionality and efficiency. Communicate with your WMS provider for updates. WMS Providers.
Feedback Mechanism: Implement a feedback system where Warehouse Clerks can report issues, suggest improvements, and share insights on the WMS usage. This feedback is invaluable for continuous improvement. Feedback Strategies.
By focusing on these areas, a Warehouse Clerk can play a significant role in enhancing the effectiveness of a Warehouse Management System.
How to Display WMS (Warehouse Management System) Skills on Your Resume
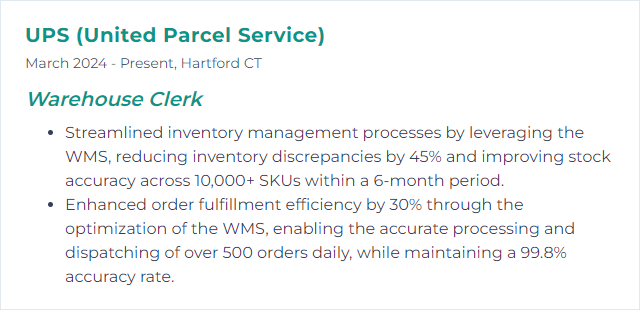
9. Order Picking
Order picking is the process in which a warehouse clerk gathers and collects items from storage to fulfill customer orders.
Why It's Important
Order picking is crucial for a Warehouse Clerk because it directly impacts the accuracy, efficiency, and speed of fulfilling customer orders, ensuring customer satisfaction and optimizing inventory management.
How to Improve Order Picking Skills
Improving order picking in a warehouse setting, particularly for a Warehouse Clerk, can be achieved by streamlining processes and integrating technology. Here are concise strategies:
Implement a Warehouse Management System (WMS): A WMS optimizes order picking by efficiently managing inventory and guiding pickers through the most efficient routes. More on WMS.
Adopt Pick-to-Light Systems: These systems use lights to guide pickers to the correct items, increasing speed and reducing errors. Pick-to-Light explained.
Use Voice Picking Technology: Voice-directed picking frees hands and eyes, allowing for faster and more accurate order picking. Benefits of Voice Picking.
Batch Picking: Group similar orders to minimize travel time. Batch Picking strategies.
Zone Picking: Assign pickers to specific areas to reduce movement and increase expertise in those zones. Understanding Zone Picking.
Cross-Docking: Directly transfer incoming items to outgoing shipments when possible, reducing handling and storage. Cross-Docking insights.
Continuous Improvement: Regularly review processes for inefficiencies and implement changes. Engage with staff for frontline insights. Kaizen in the Warehouse.
By leveraging technology and optimizing picking strategies, warehouses can significantly improve order picking efficiency and accuracy.
How to Display Order Picking Skills on Your Resume
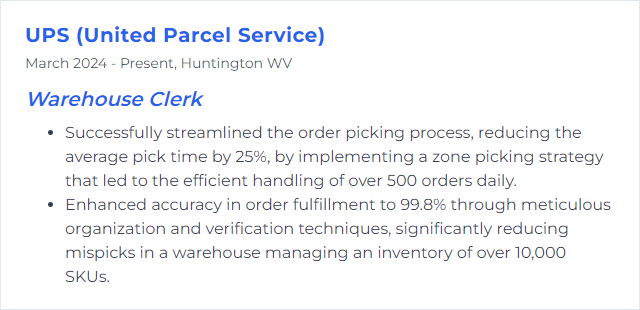
10. Shipping Procedures
Shipping procedures for a Warehouse Clerk involve preparing items for dispatch, ensuring accurate item picking, packing goods securely, processing shipping documents, coordinating with carriers for pickup, and updating inventory and tracking systems to reflect outgoing shipments.
Why It's Important
Shipping procedures are crucial for a Warehouse Clerk because they ensure accurate, timely, and efficient delivery of goods, minimizing errors, delays, and damage, which directly impacts customer satisfaction and inventory management.
How to Improve Shipping Procedures Skills
Improving shipping procedures in a warehouse setting involves enhancing efficiency, accuracy, and speed while maintaining safety. Here's a concise guide for a Warehouse Clerk focusing on key areas:
Streamline Packing Process: Implement standardized packing methods and use appropriate materials to ensure safety and reduce waste. Consider tools like Uline for supplies and equipment.
Inventory Management: Employ an efficient inventory system to track stock levels in real-time, such as Barcodes Inc. for scanners and inventory software, reducing errors and speeding up the shipping process.
Automate Where Possible: Use automation for repetitive tasks like labeling and sorting. Explore options like ShipStation for automated shipping solutions.
Optimize Shipping Routes: Leverage route optimization software to ensure the fastest delivery times. Check Route4Me for optimizing delivery routes.
Regular Training: Keep staff updated on best practices and new technologies with ongoing training. Online platforms like LinkedIn Learning offer courses on logistics and warehousing.
Quality Control Checks: Implement stringent quality control before dispatch to minimize returns and complaints. Incorporate checklists and quality standards into the shipping process.
Customer Communication: Ensure clear and prompt communication with customers regarding their shipping status. Consider CRM tools like Zendesk for managing customer interactions efficiently.
Feedback Loop: Establish a system for receiving feedback from customers and the shipping team to continually refine processes.
By focusing on these areas, a Warehouse Clerk can significantly improve the efficiency and reliability of shipping procedures, contributing to higher customer satisfaction and operational efficiency.
How to Display Shipping Procedures Skills on Your Resume

11. Safety Compliance
Safety compliance for a Warehouse Clerk involves adhering to established health and safety regulations and company policies to prevent accidents, injuries, and ensure a safe working environment.
Why It's Important
Safety compliance is important for a Warehouse Clerk to ensure a safe working environment, prevent accidents and injuries, maintain legal and regulatory adherence, and enhance overall productivity and morale.
How to Improve Safety Compliance Skills
Improving safety compliance for a Warehouse Clerk involves a multi-faceted approach focusing on training, equipment, and environment. Here's a concise guide:
Training: Ensure comprehensive safety training programs are in place, covering all aspects of warehouse work. Regular updates and refresher courses should be mandated.
Personal Protective Equipment (PPE): Provide and enforce the use of appropriate PPE, including safety shoes, helmets, and gloves. Training on proper use is essential.
Ergonomics: Implement ergonomic solutions to reduce strain from repetitive tasks, lifting, or prolonged standing.
Safety Protocols: Develop clear safety protocols for all operations, including handling hazardous materials and operating machinery. Regularly review and update these protocols.
Emergency Preparedness: Conduct regular emergency drills and ensure all employees know the procedures for fires, spills, and other emergencies.
Equipment Maintenance: Maintain a strict schedule for inspecting and servicing equipment, to prevent malfunctions that could lead to accidents.
Incident Reporting: Foster an environment where employees feel comfortable reporting safety concerns and incidents without fear of reprisal. Promptly address and investigate reports to prevent future occurrences.
Continuous Improvement: Regularly assess safety performance and seek feedback from employees to identify areas for improvement.
By adopting these strategies, a Warehouse Clerk can significantly contribute to improving safety compliance in their workplace.
How to Display Safety Compliance Skills on Your Resume
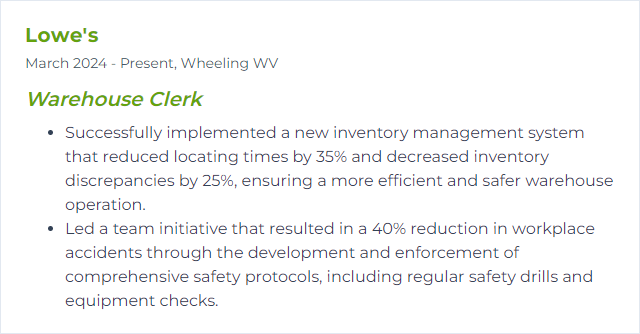
12. Quality Control
Quality Control (QC) for a Warehouse Clerk involves systematically inspecting and verifying the condition and quantity of incoming and outgoing goods to ensure they meet specified standards and requirements.
Why It's Important
Quality control is crucial for a Warehouse Clerk as it ensures that products meet safety and quality standards, minimizes errors and defects, reduces waste and customer complaints, and maintains trust in the company's brand.
How to Improve Quality Control Skills
To improve Quality Control as a Warehouse Clerk, focus on these concise steps:
Standardize Processes: Establish clear, documented procedures for all tasks to ensure consistency. ISO provides international standards that can be a good reference.
Implement Automation: Use technology for tasks like inventory tracking to reduce human error. Solutions like Zebra Technologies offer automation tools suitable for warehouse environments.
Continuous Training: Regularly train staff on quality control standards and new technologies. OSHA offers guidelines and training resources for maintaining safety and quality.
Regular Audits: Conduct frequent quality audits to identify and correct issues promptly. Tools like Intelex can help manage and schedule audits.
Feedback Loop: Establish a system for feedback from staff to continuously improve processes. SurveyMonkey can be used to gather anonymous feedback efficiently.
Supplier Quality Management: Work closely with suppliers to ensure they meet your quality standards. ASQ’s Supplier Quality Management guide offers insights on managing supplier quality.
Use Data Analytics: Leverage data analytics to identify trends and areas for improvement. Tableau is a powerful tool for visualizing warehouse data and insights.
By standardizing processes, embracing automation, investing in training, conducting regular audits, establishing feedback mechanisms, managing supplier quality, and utilizing data analytics, Warehouse Clerks can significantly improve quality control in their operations.
How to Display Quality Control Skills on Your Resume
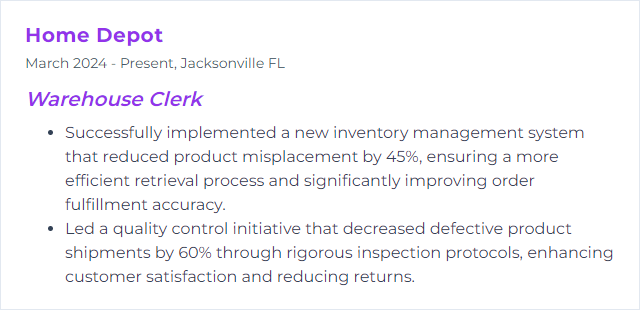