Top 12 Safety Technician Skills to Put on Your Resume
A well-crafted resume highlighting essential Safety Technician skills is crucial for standing out in the competitive job market. Showcasing a blend of technical expertise, analytical abilities, and a keen eye for safety measures can significantly enhance your chances of securing a desirable position in the field.
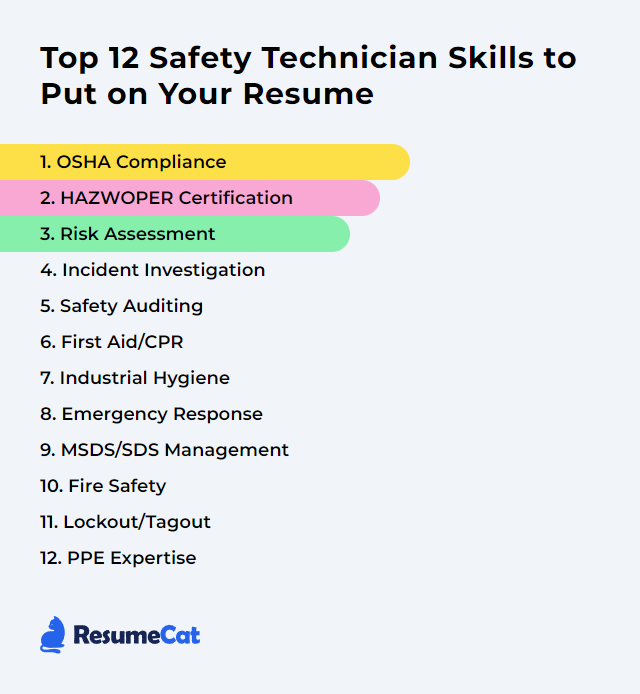
Safety Technician Skills
- OSHA Compliance
- HAZWOPER Certification
- Risk Assessment
- Incident Investigation
- Safety Auditing
- First Aid/CPR
- Industrial Hygiene
- Emergency Response
- MSDS/SDS Management
- Fire Safety
- Lockout/Tagout
- PPE Expertise
1. OSHA Compliance
OSHA compliance for a Safety Technician involves adhering to standards and regulations set by the Occupational Safety and Health Administration to ensure workplace safety and health, prevent accidents and injuries, and protect workers from hazards.
Why It's Important
OSHA compliance is important because it ensures a safe and healthy work environment, reducing the risk of accidents and injuries. For a Safety Technician, it means adhering to established standards to protect workers, avoid legal issues, and maintain operational integrity.
How to Improve OSHA Compliance Skills
Improving OSHA compliance as a Safety Technician involves a multi-faceted approach focusing on education, communication, and proactive management of workplace hazards. Here's a concise guide to enhance compliance:
Stay Informed: Regularly update your knowledge on OSHA standards and regulations. OSHA’s Official Website is an essential resource for the latest information.
Conduct Regular Training: Organize ongoing safety training sessions for employees. Utilize materials from the OSHA Education Center to keep the training up-to-date and relevant.
Perform Frequent Inspections: Regularly inspect the workplace for potential violations and hazards. Utilize OSHA’s Inspection Checklists to guide these inspections.
Implement a Reporting System: Encourage employees to report hazards without fear of retaliation. OSHA’s Whistleblower Protection Program provides guidance on creating a supportive reporting environment.
Develop an Action Plan: Create and maintain an effective action plan for hazard elimination and control. Reference OSHA’s Recommended Practices for Safety and Health Programs for developing a comprehensive safety program.
Engage with OSHA Consultation Services: Use the free consultation service offered by OSHA for small and medium-sized businesses to help recognize and control potential hazards. Find more information on this service here.
By integrating these steps into daily operations, Safety Technicians can significantly improve OSHA compliance, thereby reducing the risk of penalties and enhancing workplace safety.
How to Display OSHA Compliance Skills on Your Resume
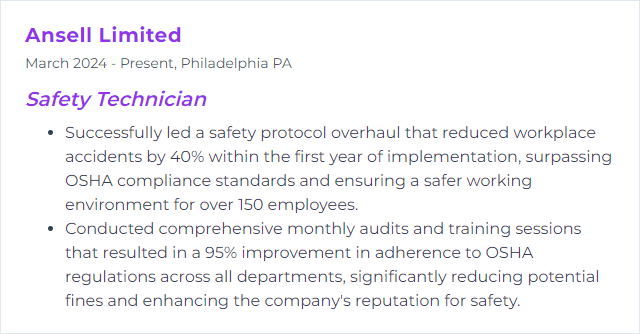
2. HAZWOPER Certification
HAZWOPER certification refers to specialized training mandated by the Occupational Safety and Health Administration (OSHA) for workers, including Safety Technicians, who are involved in hazardous waste operations and emergency response. It ensures they have the knowledge and skills to safely manage and respond to hazardous substances.
Why It's Important
HAZWOPER (Hazardous Waste Operations and Emergency Response) certification is crucial for Safety Technicians as it ensures they have the necessary training to safely manage and respond to hazardous waste operations and emergency situations, protecting themselves, the public, and the environment from hazardous substances.
How to Improve HAZWOPER Certification Skills
Improving HAZWOPER certification for a Safety Technician involves continuous learning and practical experience. Here are concise steps:
Update Knowledge: Regularly review the latest OSHA guidelines and industry practices to stay informed about new safety protocols and technologies.
Advance Training: Enroll in higher-level HAZWOPER courses or specialized training sessions to deepen your expertise. Check resources like the National Environmental Trainers for advanced courses.
Practical Experience: Gain hands-on experience through varied projects. The more diverse your experience, the more skilled you become.
Networking: Join professional organizations such as the American Society of Safety Professionals to connect with peers, share knowledge, and stay informed about industry trends.
Certification Maintenance: Regularly complete the required continuing education units (CEUs) to maintain and renew your certification.
Focus on these areas to enhance your HAZWOPER certification and your effectiveness as a safety technician.
How to Display HAZWOPER Certification Skills on Your Resume
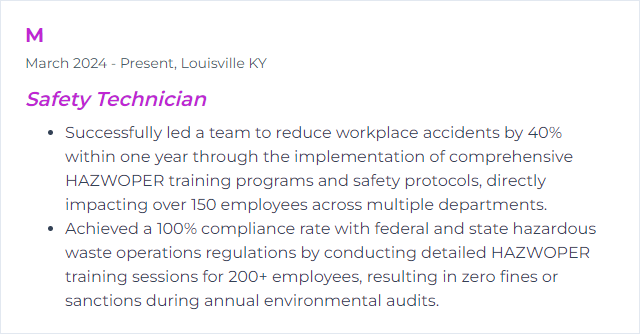
3. Risk Assessment
Risk assessment is the process of identifying, analyzing, and evaluating potential hazards and risks in a workplace to determine their impact on safety and health, and to implement appropriate measures to prevent accidents or injuries.
Why It's Important
Risk assessment is crucial for a Safety Technician as it helps identify potential hazards, evaluate risks, and implement control measures to prevent accidents, ensuring the safety and well-being of workers and compliance with safety regulations.
How to Improve Risk Assessment Skills
Improving risk assessment involves a systematic approach that enables Safety Technicians to identify, analyze, and mitigate risks effectively. Here’s a concise guide:
Stay Informed: Keep abreast of the latest safety standards and regulations by regularly visiting reputable sites like OSHA (Occupational Safety and Health Administration) and ISO (International Organization for Standardization).
Continuous Training: Engage in continuous professional development through platforms like Coursera or edX, which offer courses on risk assessment and safety management.
Utilize Technology: Adopt risk assessment software tools that provide frameworks and templates to streamline the process. Websites like SafetyCulture offer digital checklists and inspection templates.
Risk Identification: Conduct thorough inspections and hazard identification walkthroughs regularly. Tools and guidance can be found on NIOSH (National Institute for Occupational Safety and Health).
Risk Analysis: Apply qualitative and quantitative risk analysis methods to determine the likelihood and consequence of identified risks. Tools like BowtieXP can aid in visual risk analysis.
Mitigation Strategies: Develop and implement risk control measures. The CCPS (Center for Chemical Process Safety) provides resources and guidelines for process safety.
Review and Update: Risk assessments should be dynamic documents. Regularly review and update them to reflect any changes in the work environment, processes, or legislation.
Engage Stakeholders: Ensure communication and consultation with all stakeholders throughout the risk assessment process for collective insight and compliance.
By adopting these steps and leveraging the resources suggested, Safety Technicians can enhance their risk assessment processes, leading to safer work environments.
How to Display Risk Assessment Skills on Your Resume
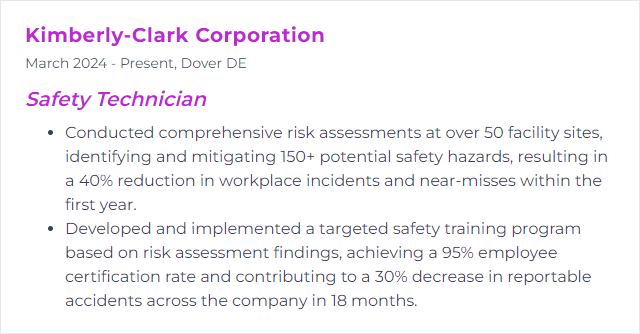
4. Incident Investigation
Incident Investigation, in the context of a Safety Technician, is the systematic process of examining and analyzing incidents that have led, or could lead, to injuries, illnesses, or property damage in the workplace. The goal is to identify root causes and implement measures to prevent future occurrences.
Why It's Important
Incident investigation is crucial for a Safety Technician because it helps identify root causes of accidents or near-misses, prevent future occurrences, ensure compliance with safety regulations, and maintain a safe working environment.
How to Improve Incident Investigation Skills
Improving incident investigation involves a systematic approach to identify root causes and implement effective preventive measures. Here are concise steps tailored for a Safety Technician:
Immediate Response: Secure the scene to preserve evidence. Ensure medical care for the injured and mitigate any immediate hazards. OSHA Quick Card
Plan the Investigation: Assemble an investigation team with diverse knowledge. Define the scope, objectives, and timeline of the investigation. NIOSH Guide
Data Collection: Gather information through interviews, document reviews, and physical evidence. Ensure the process is objective and thorough. CCPS Guidelines
Analysis: Use root cause analysis tools like the 5 Whys or Fishbone Diagram to identify underlying issues. ASSE Foundation
Report Writing: Draft a clear, concise report detailing findings, root causes, and recommended corrective actions. Emphasize facts and avoid blame. CSB Investigation Reports
Implement Changes: Work with management to prioritize and implement corrective actions. Track progress and effectiveness over time. OSHA Safety and Health Programs
Review and Learn: Regularly review investigation processes and outcomes to continuously improve safety practices. AIHA Framework
Consistently applying these steps in incident investigations will enhance the identification of hazards, reduce risks, and promote a safer workplace.
How to Display Incident Investigation Skills on Your Resume
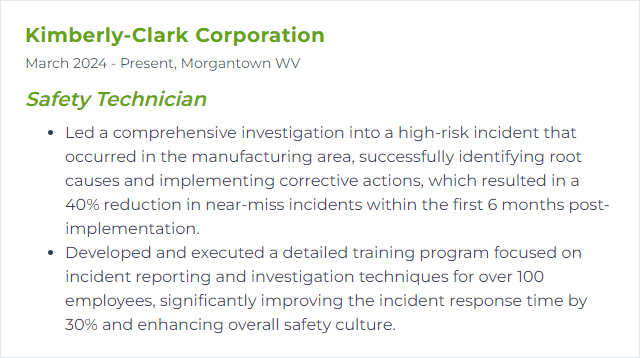
5. Safety Auditing
Safety auditing is the systematic examination of a workplace to assess the efficiency and effectiveness of safety programs, identify hazards, and ensure compliance with relevant safety regulations and standards. It is conducted by safety technicians to improve workplace safety and health outcomes.
Why It's Important
Safety auditing is crucial as it systematically assesses the effectiveness of a company's safety protocols and practices to identify risks, ensure compliance with regulatory standards, and prevent accidents or incidents, thereby protecting employees, assets, and the environment.
How to Improve Safety Auditing Skills
Improving safety auditing involves a multifaceted approach to ensure thoroughness, compliance, and continuous improvement in workplace safety:
Stay Updated: Regularly update your knowledge base with the latest safety standards and regulations from authoritative sources like OSHA or ISO to ensure compliance.
Training: Enhance your skills through professional development courses. Websites like Coursera and Udemy offer courses on safety auditing and related topics.
Use Technology: Adopt safety management software for efficient data collection, analysis, and reporting. Tools like iAuditor by SafetyCulture can streamline audits.
Engage Employees: Encourage a culture of safety by involving employees in the auditing process. This can be achieved through regular safety meetings and feedback sessions.
Continuous Improvement: Implement a continuous improvement process by reviewing audit outcomes, identifying trends, and taking corrective actions. Resources like ASSE provide guidelines for continuous improvement in workplace safety.
Benchmarking: Compare your safety performance against industry standards or peers to identify areas for improvement. Participate in forums and networks, such as The National Safety Council, for insights and benchmarks.
By integrating these strategies, safety technicians can enhance the effectiveness of their safety auditing processes, contributing to a safer work environment.
How to Display Safety Auditing Skills on Your Resume
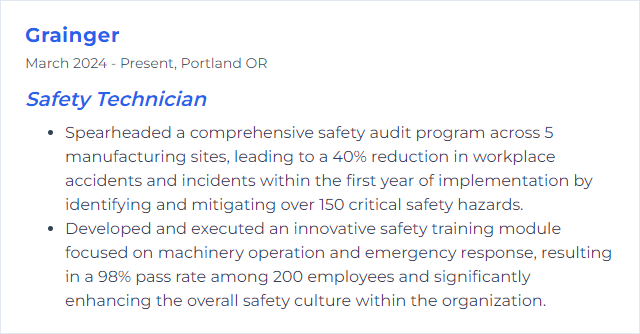
6. First Aid/CPR
First Aid/CPR is a critical skill set involving basic medical techniques and life-saving procedures such as chest compressions and rescue breathing, designed to provide immediate assistance to individuals in emergency situations until professional medical help arrives. For a Safety Technician, it's essential for ensuring workplace safety and responding effectively to accidents or health emergencies.
Why It's Important
First Aid/CPR is crucial for a Safety Technician as it enables them to provide immediate and effective life-saving assistance in emergency situations, helping to prevent further injury, reduce pain, and potentially save lives before professional medical help arrives.
How to Improve First Aid/CPR Skills
Improving your First Aid/CPR skills as a Safety Technician involves continual learning and practice. Here are concise steps to enhance your abilities:
Stay Updated: Regularly review the latest American Red Cross or American Heart Association guidelines to stay informed on the most current First Aid/CPR practices.
Certification Renewal: Ensure your First Aid/CPR certification is always current by enrolling in renewal courses. These often include updates on procedures and techniques.
Practice Regularly: Hands-on practice is crucial. Attend workshops or simulation training sessions to keep your skills sharp. Consider resources like Simulation Learning for practice scenarios.
Learn from Peers: Join forums or communities such as Society for Simulation in Healthcare to exchange knowledge and experiences with other professionals.
Feedback and Evaluation: Seek constructive feedback from certified instructors or colleagues after performing First Aid/CPR, either in real situations or simulations, to understand areas of improvement.
Advanced Training: Consider advanced courses or certifications, such as Advanced Cardiac Life Support (ACLS) or Pediatric Advanced Life Support (PALS), available through the American Heart Association.
Utilize Technology: Engage with apps and online platforms offering First Aid/CPR training modules for continuous learning. Apps like PulsePoint Respond can also keep you informed about emergencies nearby where your skills might be needed.
Stay Physically Fit: Physical readiness is essential for effective First Aid/CPR delivery. Regular exercise and maintaining good health ensure you're prepared for the physical demands of emergency response.
By following these steps and leveraging the resources provided, you can significantly enhance your First Aid/CPR skills as a Safety Technician.
How to Display First Aid/CPR Skills on Your Resume
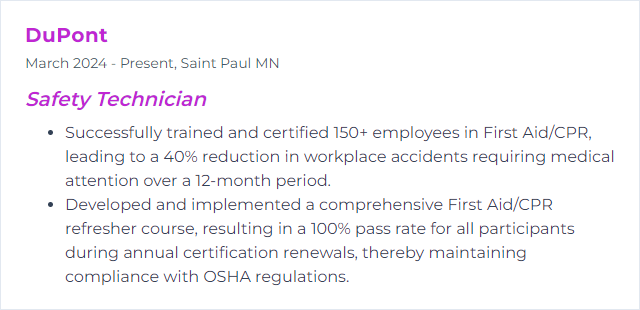
7. Industrial Hygiene
Industrial Hygiene is the science of anticipating, recognizing, evaluating, and controlling workplace conditions that may cause workers' injury or illness. For a Safety Technician, it involves implementing measures to protect the health and safety of workers by identifying hazards, assessing risks, and deploying appropriate controls to minimize exposure to harmful agents or conditions.
Why It's Important
Industrial Hygiene is crucial for a Safety Technician as it focuses on identifying, evaluating, and controlling environmental hazards in the workplace. This ensures the health and safety of workers by preventing occupational diseases and accidents, thereby promoting a safer and more productive work environment.
How to Improve Industrial Hygiene Skills
Improving Industrial Hygiene involves a multi-faceted approach focusing on the anticipation, recognition, evaluation, and control of environmental factors or stresses arising in or from the workplace. Here's a concise guide for a Safety Technician:
Anticipate Hazards: Stay informed about potential industrial hazards by consulting resources like OSHA for updates on regulations and guidance on workplace hazards.
Recognize Hazards: Conduct regular workplace assessments. Tools like NIOSH's Pocket Guide to Chemical Hazards can help identify and understand health hazards.
Evaluate Risks: Use monitoring equipment to measure the magnitude of exposure. AIHA's Exposure Assessment Strategies provides guidance on assessing and managing risks.
Control Hazards: Prioritize control methods starting with elimination, substitution, engineering controls, administrative controls, and personal protective equipment (PPE). The Hierarchy of Controls by NIOSH outlines this strategy effectively.
Educate and Train: Conduct regular training sessions for employees on safety practices and the use of PPE. Resources like OSHA's Training and Education can be instrumental.
Implement a Safety Management System: Adopt frameworks like ISO 45001 for occupational health and safety management.
Continuous Improvement: Regularly review and update safety protocols based on new insights, incidents, and technological advances. Engage in forums and communities, such as Safety+Health Magazine, for the latest in safety practices.
Remember, effective industrial hygiene management requires ongoing effort and adaptation to new challenges and regulations.
How to Display Industrial Hygiene Skills on Your Resume
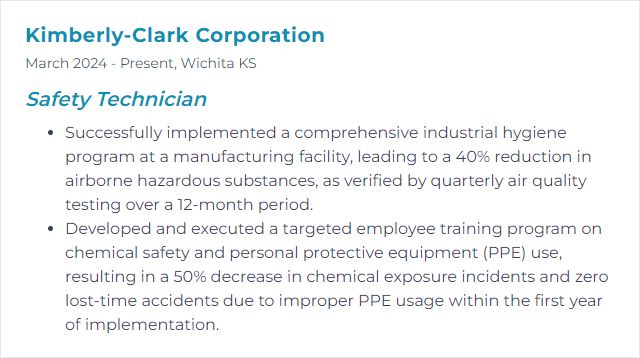
8. Emergency Response
Emergency Response refers to the immediate and coordinated efforts to address and manage unexpected and dangerous situations, focusing on minimizing harm to people, property, and the environment. For a Safety Technician, it involves implementing safety protocols, providing first aid, managing evacuation procedures, and coordinating with emergency services.
Why It's Important
Emergency response is crucial for a Safety Technician as it ensures immediate action to prevent injuries, mitigate hazards, and protect lives and property during unforeseen incidents or accidents.
How to Improve Emergency Response Skills
Improving emergency response involves a multifaceted approach focusing on preparedness, communication, and technology. Here’s a concise guide tailored for a Safety Technician:
Training & Drills: Regularly conduct and participate in emergency response drills to enhance readiness. FEMA provides comprehensive guidelines on organizing these exercises.
Communication Plans: Develop clear communication strategies ensuring all team members know their roles. OSHA’s guidelines on emergency preparedness highlight the importance of effective communication.
Technology Utilization: Leverage technology like emergency notification systems to streamline alerts. The International Association of Emergency Managers offers resources on the latest tech in emergency management.
Continuous Improvement: Regularly review and update emergency plans based on drill feedback and real incident reviews. The Centers for Disease Control and Prevention (CDC) offers resources on improving public health emergency response.
Collaboration with Local Authorities: Establish partnerships with local emergency services to ensure a coordinated response. The National Fire Protection Association (NFPA) provides standards for developing these collaborations.
By focusing on these key areas, a Safety Technician can significantly contribute to enhancing their organization’s emergency response capabilities.
How to Display Emergency Response Skills on Your Resume
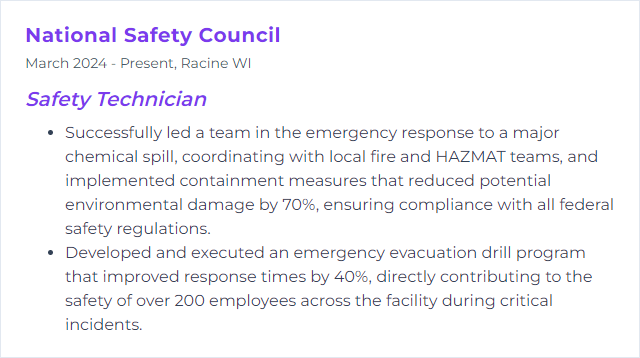
9. MSDS/SDS Management
MSDS/SDS Management involves the organization, storage, and accessibility of Material Safety Data Sheets (MSDS) or Safety Data Sheets (SDS) for all chemicals and hazardous materials within a workplace. As a Safety Technician, this process ensures compliance with safety regulations, facilitates risk assessments, and provides essential information on handling, storage, and emergency measures to maintain workplace safety and health standards.
Why It's Important
MSDS/SDS management is crucial for a Safety Technician as it ensures the safe use, storage, handling, and disposal of chemicals, minimizing health risks and ensuring regulatory compliance.
How to Improve MSDS/SDS Management Skills
Improving Material Safety Data Sheet (MSDS) or Safety Data Sheet (SDS) management involves streamlining the organization, accessibility, and review processes of these critical documents. Here’s a concise guide for a Safety Technician:
Digital Conversion: Convert all paper-based MSDS/SDS to digital formats. This enhances searchability and access. Consider using MSDSonline for digital management solutions.
Centralized Database: Use a centralized, cloud-based system for storing and managing SDSs to ensure they are accessible from any location. Chemical Safety Software offers robust solutions for managing chemical inventories and safety data sheets.
Regular Updates: Establish a schedule for regularly reviewing and updating SDSs to ensure compliance with current regulations. The OSHA Brief on Hazard Communication Standard outlines the necessity of keeping safety data sheets up to date.
Training: Implement ongoing training for employees on how to access and interpret SDS information effectively. SafetySkills offers online training modules on various safety topics, including understanding and using SDSs.
Integration with Inventory: Integrate SDS management with chemical inventory systems to automatically update safety data when new chemicals are procured. Look into EcoOnline for integrated safety and chemical inventory management solutions.
Mobile Accessibility: Ensure that SDSs are accessible via mobile devices to provide immediate access to safety information on the go. SiteHawk offers mobile solutions for quick and easy access to SDSs.
Regulatory Compliance: Keep abreast of regulatory changes and ensure that your SDS management system complies with local, national, and international standards. The EPA’s Chemical Safety and OSHA’s Hazard Communication pages are valuable resources for compliance guidelines.
By implementing these strategies, a Safety Technician can significantly improve the management of MSDS/SDS, thereby enhancing workplace safety and regulatory compliance.
How to Display MSDS/SDS Management Skills on Your Resume
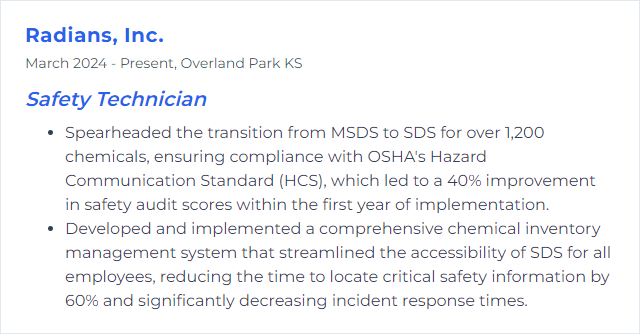
10. Fire Safety
Fire safety refers to the set of practices aimed at reducing the destruction caused by fire, including preventive measures to avoid the outbreak of fires, ensuring the safe evacuation of individuals, and implementing strategies for fighting fires effectively to minimize damage and injuries. For a Safety Technician, it involves assessing fire hazards, implementing fire prevention policies, ensuring compliance with fire safety regulations, and training staff in emergency response procedures.
Why It's Important
Fire safety is crucial to prevent loss of life, injury, and damage to property and the environment, ensuring a safe workplace and compliance with legal and regulatory obligations.
How to Improve Fire Safety Skills
Improving fire safety involves a multi-faceted approach focusing on prevention, detection, and response. Here's a concise guide for Safety Technicians:
Conduct Regular Risk Assessments: Identify potential fire hazards and address them promptly. OSHA provides guidelines for workplace fire safety assessments.
Implement Fire Safety Policies: Develop and enforce strict fire safety policies, including smoking regulations and control of flammable materials. NFPA offers comprehensive codes and standards.
Install and Maintain Fire Detection Systems: Ensure the installation of adequate fire alarms and smoke detectors. Regular maintenance is crucial. NFPA 72 details fire alarm and signaling code.
Provide Fire Extinguishers: Position appropriate types of fire extinguishers throughout the premises and ensure they are easily accessible. Regular checks and maintenance are necessary. OSHA's Extinguisher Requirements give clear directives.
Offer Regular Training and Drills: Conduct fire safety training sessions and evacuation drills for all employees. FEMA’s Fire Safety Outreach materials can be used for effective training.
Ensure Clear Escape Routes: Regularly inspect escape routes and exits to ensure they are clear and well-marked. OSHA’s Means of Egress provides specifics on requirements.
Develop an Emergency Response Plan: Create and communicate a comprehensive fire emergency response plan. Ready.gov has resources for planning.
Regular Electrical System Inspections: Faulty wiring and overloaded circuits are common fire hazards. Regular inspections by qualified electricians can prevent these. NEC provides standards for electrical safety.
Control and Store Flammable Materials Safely: Follow guidelines for the storage and handling of flammable materials. OSHA’s Flammable Liquids standard outlines best practices.
Encourage a Culture of Safety: Foster an environment where employees feel responsible for maintaining fire safety. Encouraging reporting of hazards without fear of reprisal can be effective.
By following these steps and staying informed about the latest in fire safety through authoritative sources, Safety Technicians can significantly improve fire safety in their workplaces.
How to Display Fire Safety Skills on Your Resume
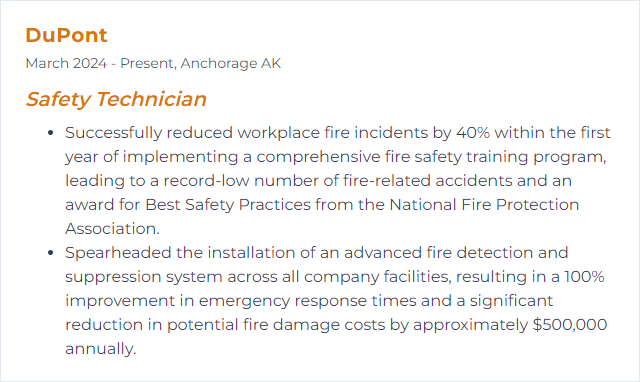
11. Lockout/Tagout
Lockout/Tagout (LOTO) is a safety procedure used to ensure that dangerous machines are properly shut off and are not able to be started up again prior to the completion of maintenance or servicing work. It involves placing a lock and/or tag on the energy isolating device of a machine to prevent the release of hazardous energy and to protect workers from injury.
Why It's Important
Lockout/Tagout (LOTO) is crucial for ensuring the safety of workers by preventing the accidental startup or release of hazardous energy during maintenance or servicing of equipment, thereby reducing the risk of injuries or fatalities.
How to Improve Lockout/Tagout Skills
To improve Lockout/Tagout (LOTO) as a Safety Technician, follow these concise strategies:
Regular Training: Ensure all employees undergo comprehensive LOTO training regularly, focusing on procedures specific to your facility's equipment.
Clear Procedures: Develop and maintain clear, equipment-specific LOTO procedures, easily accessible to all employees.
Routine Audits: Conduct regular audits of LOTO practices to identify and rectify non-compliance or procedural weaknesses.
LOTO Stations: Install well-stocked LOTO stations at strategic locations to ensure easy access to necessary equipment.
Feedback Mechanism: Implement a system for employees to report issues or suggest improvements regarding LOTO procedures without fear of reprisal.
By focusing on these strategies, you can significantly enhance the effectiveness and compliance of your LOTO program.
How to Display Lockout/Tagout Skills on Your Resume
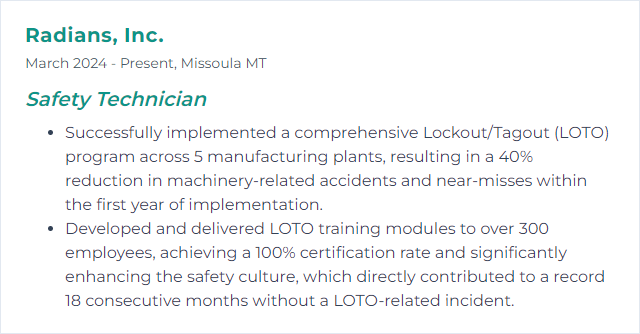
12. PPE Expertise
PPE Expertise, in the context of a Safety Technician, refers to specialized knowledge and skills in selecting, using, and maintaining Personal Protective Equipment to ensure worker safety and compliance with health and safety regulations.
Why It's Important
PPE expertise is crucial for a Safety Technician as it ensures the correct selection, use, and maintenance of Personal Protective Equipment, protecting workers from hazards and minimizing the risk of workplace injuries and illnesses.
How to Improve PPE Expertise Skills
Improving PPE (Personal Protective Equipment) expertise, especially for a Safety Technician, involves continuous learning and practical experience. Here are concise steps with inline linking to enhance your knowledge and skills in PPE:
Stay Updated with Regulations: Familiarize yourself with the latest OSHA standards for PPE to ensure compliance and safety.
Certification and Training: Consider obtaining certifications such as Certified Safety Professional (CSP) or Certified Industrial Hygienist (CIH) that cover PPE topics extensively.
Manufacturer Training: Participate in training sessions offered by PPE manufacturers. Many have online resources, such as 3M’s Safety Training.
Attend Workshops and Seminars: Look for PPE workshops and seminars provided by industry associations like American Society of Safety Professionals (ASSP).
Hands-On Experience: Gain practical experience by actively participating in workplace safety assessments and PPE selection processes.
Networking: Join professional networks or online forums such as Safety Community to exchange knowledge and experiences with peers.
Read Widely: Stay informed with the latest trends and research in PPE by subscribing to relevant journals like Journal of Occupational and Environmental Hygiene.
By following these steps and actively engaging in continuous learning opportunities, a Safety Technician can significantly improve their PPE expertise.
How to Display PPE Expertise Skills on Your Resume
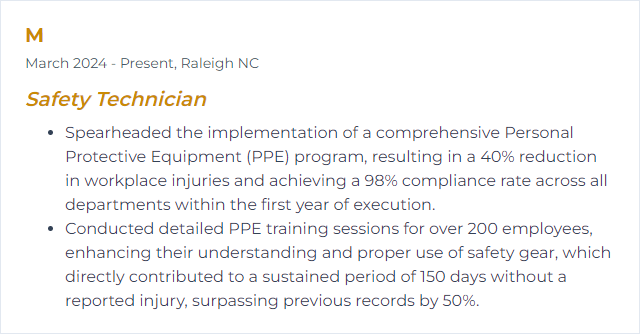