Top 12 Safety Manager Skills to Put on Your Resume
In today's competitive job market, standing out as a safety manager requires showcasing a unique set of skills that demonstrate your ability to maintain a safe and compliant working environment. This article delves into the top 12 skills that, when featured on your resume, can significantly enhance your appeal to potential employers by highlighting your expertise in promoting safety and health standards effectively.
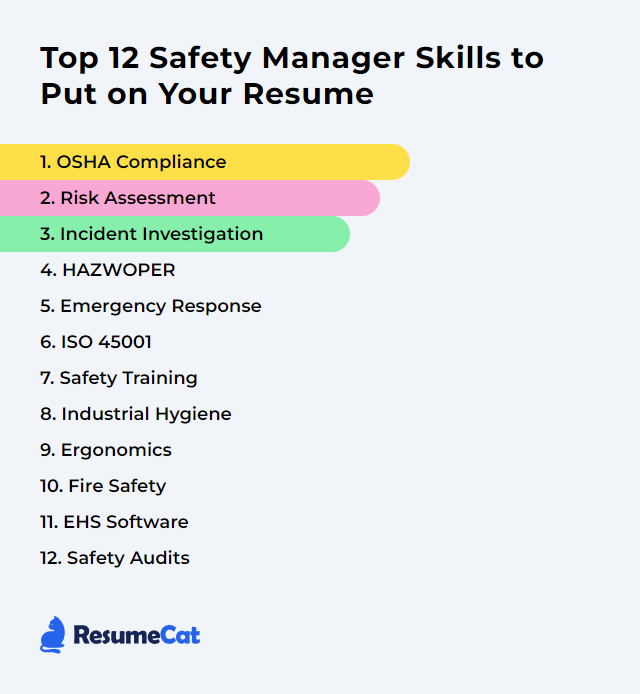
Safety Manager Skills
- OSHA Compliance
- Risk Assessment
- Incident Investigation
- HAZWOPER
- Emergency Response
- ISO 45001
- Safety Training
- Industrial Hygiene
- Ergonomics
- Fire Safety
- EHS Software
- Safety Audits
1. OSHA Compliance
OSHA Compliance for a Safety Manager involves ensuring that workplace practices, policies, and environments meet the standards set by the Occupational Safety and Health Administration (OSHA) to protect employees' health and safety.
Why It's Important
OSHA compliance is crucial for a Safety Manager because it ensures a safe and healthy workplace by adhering to standardized safety regulations, thereby minimizing the risk of accidents, legal liabilities, and potential fines. It also helps in maintaining a positive reputation and boosting employee morale and productivity.
How to Improve OSHA Compliance Skills
Improving OSHA compliance involves several key steps that Safety Managers can take to ensure their organization adheres to the Occupational Safety and Health Administration's regulations. Here’s a brief guide:
Stay Informed: Regularly review OSHA standards and updates relevant to your industry. OSHA’s Law and Regulations page is a great starting point.
Conduct Regular Audits: Perform regular safety audits to identify potential hazards and non-compliance issues. Use OSHA’s Recommended Practices for Safety and Health Programs as a guide.
Employee Training: Ensure all employees receive comprehensive safety training, as per OSHA’s Training Requirements. Tailor this training to both general safety and specific hazards of your workplace.
Implement a Safety Program: Develop and enforce a safety program that includes employee participation, hazard identification, and prevention. Refer to OSHA’s Safety and Health Programs recommendations.
Maintain Records: Keep accurate records of work-related injuries and illnesses as required by OSHA’s Recordkeeping rules.
Open Communication: Encourage an open line of communication where employees can report hazards or safety concerns without fear of retaliation.
Respond Promptly: Quickly address any identified hazards or violations to prevent accidents and potential fines.
Leverage OSHA Resources: Utilize OSHA’s compliance assistance resources, which include consultation services, training, and educational tools specifically designed to help maintain compliance.
Adhering to these steps can significantly improve OSHA compliance, ensuring a safer workplace and minimizing the risk of costly violations.
How to Display OSHA Compliance Skills on Your Resume
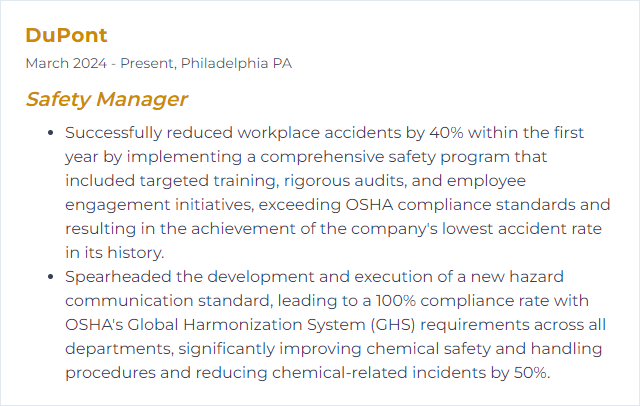
2. Risk Assessment
Risk assessment is the process of identifying, analyzing, and evaluating potential hazards in a workplace to determine their impact on worker safety and health, and implementing measures to mitigate or eliminate those risks.
Why It's Important
Risk assessment is crucial for a Safety Manager as it enables the identification and evaluation of potential hazards, allowing for the implementation of preventive measures to mitigate risks, ensuring the safety and well-being of employees, and compliance with legal and regulatory requirements.
How to Improve Risk Assessment Skills
Improving risk assessment involves a continuous process of identifying, analyzing, and managing potential risks in a workplace. As a Safety Manager, you can enhance this process by following a few concise steps:
Stay Informed: Keep updated with the latest safety standards and regulations. Websites like OSHA (Occupational Safety and Health Administration) provide a wealth of resources.
Engage Employees: Involve employees in risk assessments to gain insight into potential hazards. This can improve the identification and management of risks.
Use Technology: Implement risk assessment software tools to streamline the process. Check out options like SafetyCulture (iAuditor).
Continuous Learning: Attend workshops, webinars, and training sessions to stay ahead. Organizations like ASSE (American Society of Safety Professionals) offer various learning resources.
Review and Update: Regularly review and update risk assessments to reflect any changes in the workplace or industry best practices.
By adopting these strategies, you can significantly improve risk assessment processes, contributing to a safer work environment.
How to Display Risk Assessment Skills on Your Resume
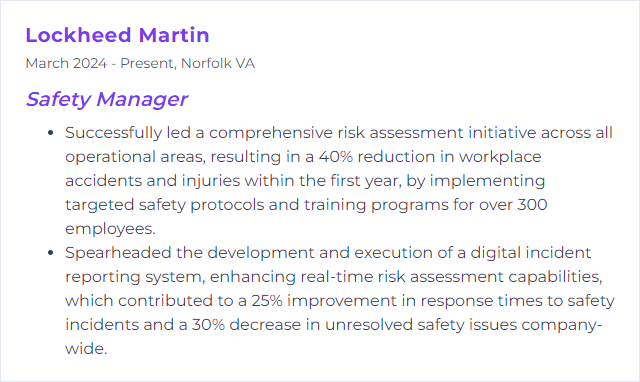
3. Incident Investigation
Incident Investigation is the systematic examination of an adverse event to determine its causes, with the goal of preventing recurrence and enhancing safety.
Why It's Important
Incident investigation is crucial for a Safety Manager because it helps identify the root causes of incidents, prevent future occurrences, enhance safety protocols, and ensure regulatory compliance, ultimately safeguarding the well-being of employees and the organization.
How to Improve Incident Investigation Skills
Improving incident investigation involves a multi-faceted approach aimed at enhancing the thoroughness, accuracy, and effectiveness of the investigative process. Here’s a very short and concise guide for a Safety Manager:
Training and Competence: Ensure all investigators are well-trained and competent. Offer regular training sessions on investigative techniques, root cause analysis, and legal requirements. OSHA's Incident Investigation guide provides a good starting point.
Use of Technology: Leverage technology such as incident management software for systematic data collection, analysis, and reporting. Tools like iAuditor by SafetyCulture can streamline the process.
Structured Methodology: Adopt and standardize a structured methodology for incident investigation such as the "5 Whys" or "Fishbone Diagram". The CDC's Root Cause Analysis page provides insights into implementing these techniques.
Stakeholder Involvement: Involve various stakeholders, including employees, in the investigation process to gain multiple perspectives. Engaging employees can also be found in the TapRooT® system, which emphasizes team investigation.
Timely Response: Ensure that investigations are initiated promptly after an incident to gather accurate evidence and witness statements. This aspect is underlined in the NIOSH Incident Investigation guide.
Comprehensive Documentation: Maintain thorough documentation for each step of the investigation process, which is crucial for legal compliance and continuous improvement. The AIHA provides resources on effective documentation practices.
Follow-up and Feedback: Implement the corrective actions identified during the investigation and monitor their effectiveness. Provide feedback to all relevant parties about the outcomes of the investigation to promote a culture of continuous improvement.
By focusing on these areas, a Safety Manager can significantly enhance the effectiveness of incident investigations, leading to safer work environments and compliance with regulatory requirements.
How to Display Incident Investigation Skills on Your Resume
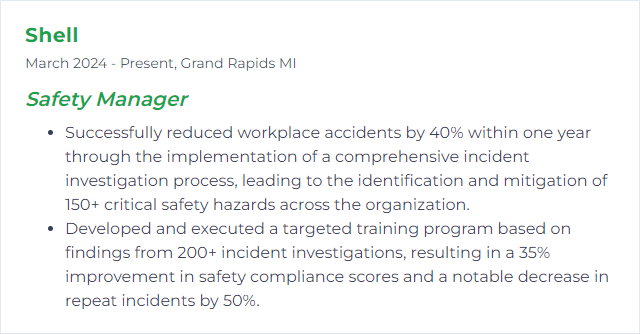
4. HAZWOPER
HAZWOPER (Hazardous Waste Operations and Emergency Response) is a set of guidelines mandated by OSHA (Occupational Safety and Health Administration) designed to ensure the safety and health of workers involved in operations dealing with hazardous substances, including cleanup, treatment, storage, and emergency response situations. As a Safety Manager, it involves ensuring proper training, safety procedures, and protective measures are in place for employees handling hazardous materials.
Why It's Important
HAZWOPER (Hazardous Waste Operations and Emergency Response) is crucial for a Safety Manager because it ensures the safety and health of workers handling hazardous substances, minimizes risks of accidents and exposures, and complies with regulatory requirements, protecting both employees and the environment.
How to Improve HAZWOPER Skills
Improving HAZWOPER (Hazardous Waste Operations and Emergency Response) involves continuous training, proper equipment maintenance, and regular safety audits. Here's a concise guide for a Safety Manager:
Enhance Training Programs: Ensure that all employees undergo comprehensive HAZWOPER training and regular refresher courses. Tailor training to the specific hazards and operations of your site. OSHA Training Requirements provide a detailed guide.
Conduct Regular Drills: Organize frequent emergency response drills to practice and reinforce the correct procedures during an actual hazardous waste incident. This improves response times and efficiency.
Maintain and Upgrade Equipment: Regularly inspect, maintain, and when necessary, upgrade personal protective equipment (PPE) and other safety gear to ensure they are in optimal condition. NIOSH Personal Protective Equipment offers insights into proper equipment selection and maintenance.
Implement Safety Audits: Conduct periodic safety audits to identify and mitigate potential hazards in the workplace. Use findings to improve safety protocols and training programs.
Foster a Safety Culture: Promote a culture of safety within the organization by encouraging open communication about hazards and safety concerns. Engage employees in safety meetings and decision-making processes.
Stay Updated with Regulations: Keep abreast of the latest HAZWOPER regulations and standards by frequently visiting OSHA’s Hazardous Waste page and incorporating any changes into your safety protocols.
Leverage Technology: Utilize technology for better training methods, like virtual reality simulations, and for monitoring hazardous conditions in real-time.
By focusing on these areas, a Safety Manager can significantly improve the effectiveness of their organization's HAZWOPER program, ensuring a safer workplace for all employees.
How to Display HAZWOPER Skills on Your Resume
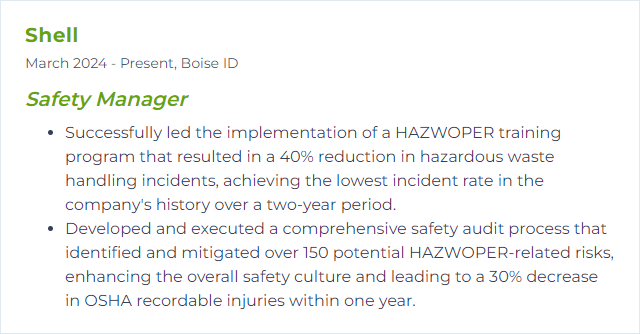
5. Emergency Response
Emergency Response refers to the strategic and immediate actions taken by an organization, under the guidance of a Safety Manager, to address and manage unexpected and potentially harmful incidents, ensuring the safety and well-being of all personnel and minimizing damage to property and the environment.
Why It's Important
Emergency Response is crucial for swiftly addressing incidents, minimizing harm to individuals, property, and the environment, ensuring regulatory compliance, and maintaining organizational continuity and reputation.
How to Improve Emergency Response Skills
Improving emergency response involves strategic planning, training, and collaboration. As a Safety Manager, focus on these steps:
Assess Risks: Identify potential emergencies specific to your organization (FEMA Risk Assessment).
Develop an Emergency Plan: Create a comprehensive plan addressing identified risks, including evacuation routes and meeting points (OSHA eTool).
Training and Drills: Regularly train employees on the emergency plan and conduct drills to ensure readiness (Red Cross Training Services).
Communication Systems: Implement effective communication tools and protocols for emergencies (FCC Emergency Communications).
Collaborate with Local Authorities: Work with local emergency services to align your plans and understand community resources (Ready.gov Community Preparedness).
Review and Improve: Regularly review and update your emergency response plan based on drill feedback and changes in the organization or external environment (CDC Emergency Preparedness and Response).
By focusing on these key areas, you can significantly improve your emergency response capabilities.
How to Display Emergency Response Skills on Your Resume
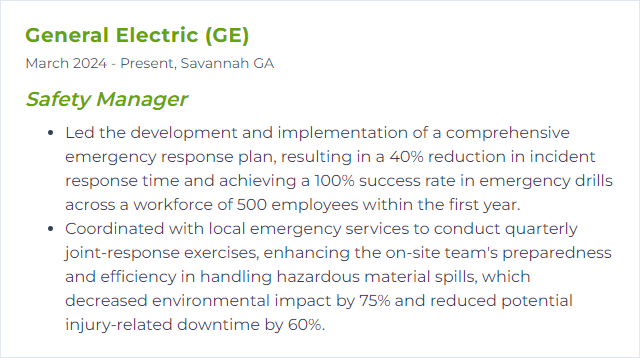
6. ISO 45001
ISO 45001 is an international standard for occupational health and safety management systems, aimed at improving employee safety, reducing workplace risks, and creating better, safer working conditions. For a Safety Manager, it provides a framework to increase safety, reduce workplace risks, and enhance health and well-being at work, ensuring compliance with legislation.
Why It's Important
ISO 45001 is crucial for a Safety Manager as it provides a global standard for occupational health and safety management, helping to reduce workplace risks, enhance employee safety, and improve organizational health and safety performance.
How to Improve ISO 45001 Skills
Improving ISO 45001, the international standard for occupational health and safety (OH&S) management systems, requires a continuous commitment to enhancing workplace safety and health practices. Here’s a concise guide for a Safety Manager:
Perform Gap Analysis: Regularly assess your current OH&S management system against ISO 45001 requirements to identify areas for improvement. BSI’s Gap Analysis Tool can facilitate this process.
Engage Leadership and Workers: Ensure active participation from management and workers in safety initiatives to foster a strong safety culture. The ISO 45001 Guidance Document offers strategies for worker engagement.
Continuous Training and Awareness: Regularly conduct training sessions to keep all employees informed about their roles in maintaining and improving the OH&S management system. Online resources like OSHAcademy provide free training materials.
Implement a Robust Incident Investigation Process: Investigate incidents thoroughly to identify root causes and prevent recurrence. The CCOHS guide outlines effective investigation techniques.
Monitor and Measure Performance: Use Key Performance Indicators (KPIs) to track the effectiveness of your OH&S management system. Safeopedia provides insights into leading and lagging indicators.
Audit and Review: Conduct regular internal and external audits to ensure compliance with ISO 45001 standards. ISO’s auditing guidance can help streamline this process.
Continual Improvement: Implement corrective actions based on audit findings, incident investigations, and performance data to continuously improve the OH&S management system. The Plan-Do-Check-Act (PDCA) cycle is a fundamental concept in ISO 45001 for driving continual improvement.
By following these steps and leveraging the resources provided, a Safety Manager can significantly improve their organization's ISO 45001 management system, leading to a safer and healthier workplace.
How to Display ISO 45001 Skills on Your Resume
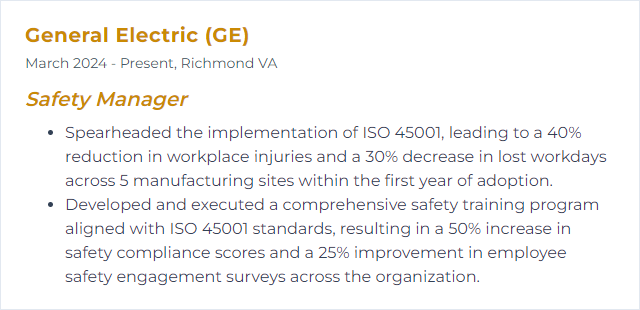
7. Safety Training
Safety training involves educating employees on the proper procedures, practices, and behaviors to minimize workplace risks and ensure a safe working environment. It covers hazard recognition, equipment use, emergency response, and regulatory compliance. For a Safety Manager, it's about designing, implementing, and overseeing these training programs to protect employees and meet organizational safety goals.
Why It's Important
Safety training is crucial as it equips employees with the knowledge and skills to perform their duties safely, minimizing the risk of accidents and injuries. For a Safety Manager, it ensures regulatory compliance, reduces potential liability, and fosters a culture of safety within the organization, ultimately protecting both employees and the company.
How to Improve Safety Training Skills
Improving safety training involves a strategic approach focusing on engagement, relevance, and continuous improvement. Here are concise strategies a Safety Manager can implement:
Assess and Identify Needs: Conduct a comprehensive risk assessment to tailor training to specific workplace hazards. OSHA's recommendations can guide this process.
Interactive Training: Incorporate interactive elements such as simulations, VR, and hands-on exercises to enhance engagement. Tools like SafetySkills offer interactive online safety training courses.
Utilize Technology: Leverage e-learning platforms for flexibility and accessibility. Platforms like Coursera and Udemy offer courses on various safety topics.
Feedback and Improvement: Regularly collect feedback from participants to continuously improve training effectiveness. Engage with platforms like SurveyMonkey for easy feedback collection.
Continuous Learning: Promote a culture of continuous learning by providing access to ongoing educational resources and updates. Resources like National Safety Council offer continuous learning opportunities.
Certification and Recognition: Implement a certification or recognition program to incentivize participation and completion. Information on certification can be found through Board of Certified Safety Professionals.
By focusing on these strategies, a Safety Manager can significantly enhance the effectiveness of safety training within their organization.
How to Display Safety Training Skills on Your Resume
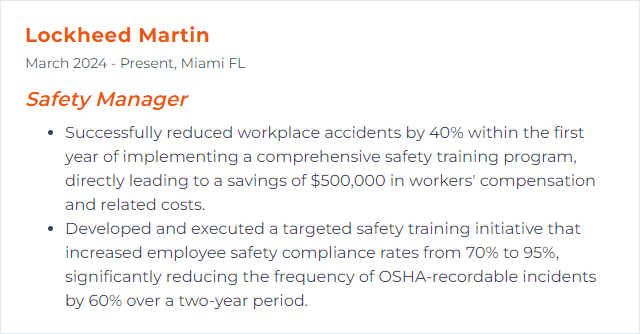
8. Industrial Hygiene
Industrial Hygiene is the science of anticipating, recognizing, evaluating, and controlling workplace conditions that may cause workers' injury or illness. For a Safety Manager, it involves implementing measures to mitigate occupational hazards and ensuring a safe and healthy work environment.
Why It's Important
Industrial Hygiene is crucial for a Safety Manager as it focuses on identifying, evaluating, and controlling workplace hazards, thereby safeguarding the health and well-being of employees, reducing the risk of occupational illnesses and injuries, and ensuring compliance with health and safety regulations.
How to Improve Industrial Hygiene Skills
Improving Industrial Hygiene involves several key steps focused on identifying, evaluating, and controlling environmental factors or stresses arising in or from the workplace that may cause sickness, impaired health, or significant discomfort among workers. As a Safety Manager, you can enhance Industrial Hygiene by:
Conducting Risk Assessments: Regularly assess the workplace for physical, chemical, biological, and ergonomic risks. OSHA's guidance on estimating the level of risk can be a helpful starting point.
Implementing Control Measures: Based on the risk assessments, implement appropriate control measures following the hierarchy of controls. This includes elimination, substitution, engineering controls, administrative controls, and personal protective equipment (PPE). NIOSH offers a detailed explanation of this hierarchy.
Training and Education: Ensure workers receive training on the risks they are exposed to and how to protect themselves. Training should include proper use of PPE, hygiene practices, and emergency procedures. OSHA's Training Requirements provide a comprehensive resource.
Monitoring and Surveillance: Regularly monitor the workplace environment and workers' health to identify new hazards and assess the effectiveness of control measures. Tools and guidelines from AIHA (American Industrial Hygiene Association) can assist in setting up effective monitoring systems.
Review and Continuous Improvement: Continuously review and update the industrial hygiene program to reflect changes in processes, technologies, and regulatory requirements. Engaging with ISO Standards, such as ISO 45001 for occupational health and safety, can provide a structured framework for continuous improvement.
By systematically applying these steps and leveraging resources from authoritative bodies like OSHA, NIOSH, AIHA, and ISO, a Safety Manager can significantly improve Industrial Hygiene practices within their organization.
How to Display Industrial Hygiene Skills on Your Resume
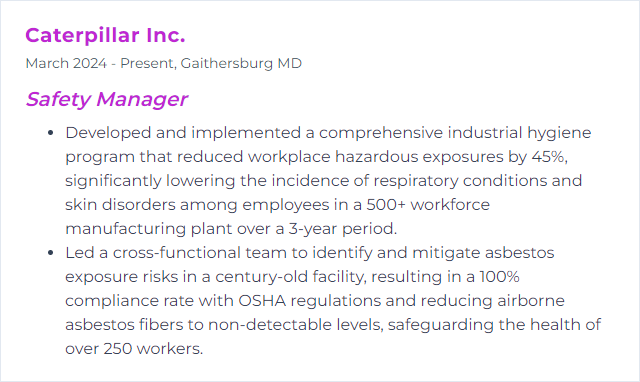
9. Ergonomics
Ergonomics is the science of designing workplaces, products, and systems to fit the people who use them, aiming to enhance safety, comfort, and efficiency, thereby reducing the risk of injuries and improving productivity.
Why It's Important
Ergonomics is crucial for ensuring a safe, efficient, and comfortable work environment, reducing the risk of injuries and enhancing productivity by optimizing the design of workspaces, tools, and tasks to fit the physical needs of employees.
How to Improve Ergonomics Skills
Improving ergonomics, especially from a Safety Manager's perspective, involves assessing workplace ergonomics, educating employees, and implementing ergonomic solutions. Here's a concise guide:
Conduct Ergonomic Assessments: Use tools like the Rapid Upper Limb Assessment (RULA) to identify ergonomic risks in work tasks.
Ergonomic Training: Provide training sessions on ergonomic principles and practices. The Occupational Safety and Health Administration (OSHA) offers resources and guidelines for ergonomic training.
Implement Ergonomic Solutions: Adjust workstations, equipment, and task designs based on ergonomic principles. The Cornell University Ergonomics Web (CUErgo) offers practical solutions and tips.
Encourage Microbreaks: Promote short, frequent breaks to reduce muscle fatigue. Guidance can be found through Mayo Clinic’s suggestions on work-break balance.
Monitor and Adjust: Regularly review and adjust ergonomic practices based on employee feedback and new ergonomic research findings.
By taking these steps, Safety Managers can significantly reduce workplace injuries, improve employee comfort, and enhance productivity.
How to Display Ergonomics Skills on Your Resume
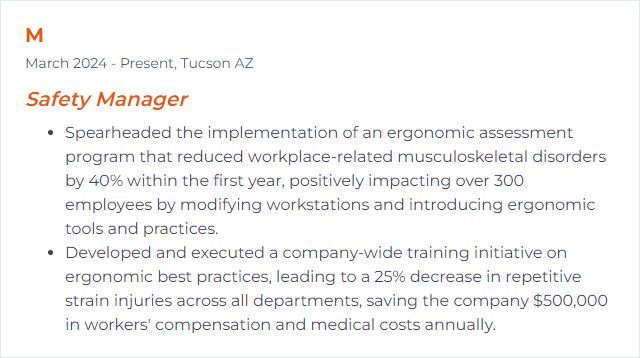
10. Fire Safety
Fire safety involves implementing practices and measures to prevent, manage, and mitigate the risks and impacts of fire, ensuring the protection of people, property, and the environment. It encompasses fire prevention strategies, emergency response planning, and compliance with relevant safety regulations and standards.
Why It's Important
Fire safety is crucial to protect lives, prevent injuries, minimize property damage, ensure business continuity, and comply with legal requirements, thereby safeguarding both human and financial resources.
How to Improve Fire Safety Skills
To improve fire safety, a Safety Manager should:
- Assess Risks: Conduct regular fire risk assessments to identify potential hazards and implement measures to mitigate them.
- Educate and Train: Provide comprehensive fire safety training for all employees on emergency procedures, use of fire extinguishers, and evacuation routes.
- Maintain Equipment: Ensure regular inspection and maintenance of fire detection systems, alarms, extinguishers, and sprinklers as detailed by the National Fire Protection Association (NFPA).
- Implement Fire Drills: Organize periodic fire drills to ensure everyone knows how to exit the building safely during an emergency.
- Ensure Clear Exit Routes: Keep all exit routes and doors clear of obstructions and well-marked, as recommended by OSHA guidelines.
- Comply with Regulations: Stay updated with local and national fire safety regulations to ensure compliance and reduce liability risks.
By focusing on these key areas, Safety Managers can significantly improve fire safety in any organization.
How to Display Fire Safety Skills on Your Resume

11. EHS Software
EHS Software is a digital platform that enables Safety Managers to streamline and manage their organization's Environment, Health, and Safety (EHS) programs, ensuring compliance with regulations, minimizing risks, and enhancing workplace safety.
Why It's Important
EHS (Environmental, Health, and Safety) software is crucial for a Safety Manager as it streamlines compliance management, mitigates risks by identifying hazards, enhances incident response times, and improves overall workplace safety and health standards, ensuring a safer and legally compliant work environment.
How to Improve EHS Software Skills
Improving EHS (Environmental, Health, and Safety) software involves enhancing its usability, functionality, and integration capabilities to better serve the needs of Safety Managers. Here are concise strategies:
User-Friendly Interface: Design an intuitive and easy-to-navigate interface. Usability is crucial for ensuring that Safety Managers can efficiently access and utilize the software’s features. Nielsen Norman Group offers insights on usability principles.
Customization and Scalability: Allow customization options for different company sizes and needs, ensuring the software grows with the organization. Gartner delves into customization best practices.
Comprehensive Reporting Tools: Incorporate advanced reporting features for accurate tracking and analysis of safety data. OSHA’s guide on recordkeeping provides a framework for what data might be crucial.
Integration Capabilities: Ensure the software can seamlessly integrate with other systems (HR, Operations) for a unified management approach. Forbes Technology Council shares valuable integration tips.
Mobile Accessibility: Develop a mobile application or optimize for mobile use, allowing Safety Managers to access the software on-the-go. TechCrunch discusses the importance of mobile-first strategies.
Real-Time Alerts and Notifications: Implement real-time alerts for immediate notification of safety incidents or risks. MIT Technology Review underscores the value of real-time alerts in crisis management.
Training and Support: Provide comprehensive training materials and responsive customer support to ensure users can effectively utilize the software. Training Magazine highlights methods for measuring training effectiveness.
Regulatory Compliance: Regularly update the software to comply with the latest EHS regulations and standards. Environmental Protection Agency (EPA) and Occupational Safety and Health Administration (OSHA) are key resources for U.S. regulations.
Feedback Mechanism: Incorporate a feedback system for users to suggest improvements, ensuring the software evolves based on user needs. Harvard Business Review discusses effective employee feedback methods.
By focusing on these strategies, Safety Managers can significantly enhance the effectiveness and user satisfaction of EHS software, leading to better safety outcomes and compliance.
How to Display EHS Software Skills on Your Resume
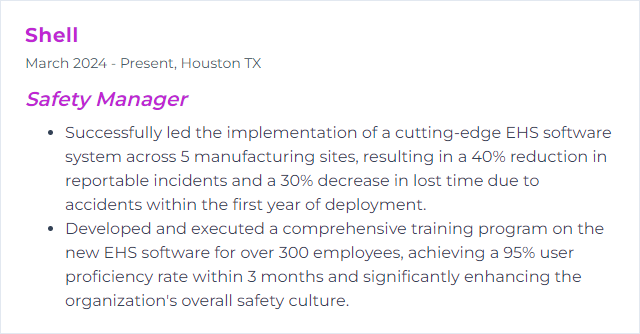
12. Safety Audits
Safety audits are systematic assessments conducted by or for safety managers to evaluate and improve the effectiveness of health and safety programs, ensuring compliance with regulations, identifying risks, and preventing incidents in the workplace.
Why It's Important
Safety audits are critical as they proactively identify potential hazards, ensure compliance with safety regulations, and mitigate risks, thereby protecting employees, avoiding legal liabilities, and maintaining operational integrity for the organization.
How to Improve Safety Audits Skills
Improving safety audits involves a comprehensive approach focusing on preparation, execution, and follow-up. Here are concise steps a Safety Manager can take to enhance the process:
Pre-audit Preparation: Clearly define the audit's scope and objectives. Engage employees and inform them about the audit process to foster a culture of transparency and cooperation. Utilize checklists tailored to your organization's specific needs and regulatory requirements. OSHA’s Safety and Health Program Management Guidelines provide a good starting point for what areas to cover.
During the Audit: Employ a mix of observation, interviews, and document reviews to assess compliance with safety protocols. Use technology, such as digital checklists or mobile apps, for efficient data collection and analysis. For example, the iAuditor by SafetyCulture app offers customizable safety audit checklists.
Post-audit Follow-up: Develop a clear action plan to address identified issues, prioritizing them based on risk. Engage with employees to discuss findings and gather feedback on proposed improvements. Implement corrective actions and schedule regular follow-up audits to ensure compliance and continuous improvement.
Continuous Improvement: Foster a culture of continuous improvement by regularly reviewing and updating safety protocols and training programs. Stay informed on industry best practices and regulatory changes. Resources like the National Safety Council provide updates and guidelines for workplace safety.
Training and Education: Continuously educate and train employees on safety practices and the importance of compliance. Utilize resources such as OSHA’s Training and Education to keep up with the latest training programs and requirements.
By focusing on thorough preparation, detailed execution, and diligent follow-up, Safety Managers can significantly enhance the effectiveness of safety audits, leading to a safer and more compliant workplace.
How to Display Safety Audits Skills on Your Resume
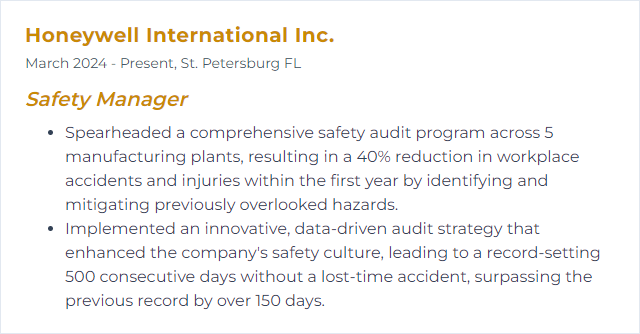