Top 12 Rotating Equipment Engineer Skills to Put on Your Resume
In the dynamic field of rotating equipment engineering, showcasing the right blend of technical knowledge and practical skills on your resume can significantly elevate your marketability. This article delves into the top 12 skills that not only reflect your expertise but also align with industry demands, ensuring you stand out to potential employers.
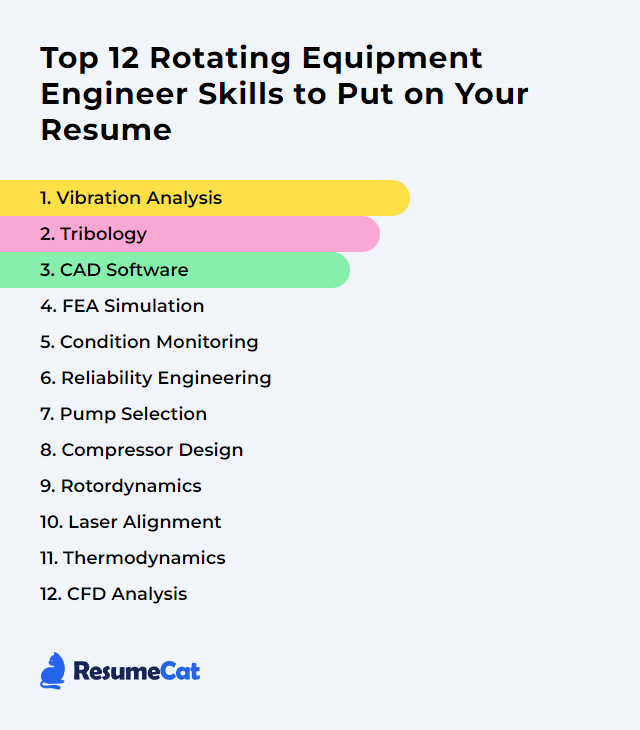
Rotating Equipment Engineer Skills
- Vibration Analysis
- Tribology
- CAD Software
- FEA Simulation
- Condition Monitoring
- Reliability Engineering
- Pump Selection
- Compressor Design
- Rotordynamics
- Laser Alignment
- Thermodynamics
- CFD Analysis
1. Vibration Analysis
Vibration analysis is a technique used by rotating equipment engineers to monitor, analyze, and diagnose the condition of machinery by measuring and examining the frequency, amplitude, and intensity of the vibrations it emits, enabling the detection of issues such as misalignment, imbalance, bearing failures, and other mechanical problems before they lead to costly downtime or catastrophic failure.
Why It's Important
Vibration analysis is crucial for a Rotating Equipment Engineer because it enables the early detection of equipment anomalies and faults, allowing for timely maintenance and repairs. This prevents unexpected failures, enhances equipment reliability, and optimizes operational efficiency.
How to Improve Vibration Analysis Skills
Improving vibration analysis for rotating equipment involves several key steps aimed at enhancing the accuracy and effectiveness of diagnostics and monitoring. As a Rotating Equipment Engineer, you can enhance vibration analysis by:
Educating Yourself: Continuously update your knowledge on vibration analysis techniques and tools. Websites like Vibration Institute offer resources and training.
Utilizing Advanced Tools: Invest in high-quality vibration analysis equipment and software. Companies like Fluke provide state-of-the-art tools for precise measurements.
Implementing Predictive Maintenance: Transition from reactive to predictive maintenance by using data analytics. Platforms like Predictive Maintenance | PdM by IBM offer solutions for leveraging data effectively.
Regular Calibration and Testing: Ensure your vibration analysis equipment is regularly calibrated and tested for accuracy. Guides on calibration can be found at Reliability Direct.
In-depth Analysis: Apply comprehensive analysis techniques, such as FFT (Fast Fourier Transform) and time-waveform analysis, to identify specific equipment faults. Educational resources at Engineering Toolbox can provide further insights into these techniques.
Condition Monitoring Integration: Integrate vibration analysis with other condition monitoring techniques for a holistic view of equipment health. Information on integrated approaches can be explored at Mobius Institute.
Professional Networking: Join professional forums and networks such as Maintenance.org to share insights and learn from peers in the field.
By focusing on these areas, you can significantly improve the effectiveness of vibration analysis in maintaining and optimizing rotating equipment.
How to Display Vibration Analysis Skills on Your Resume
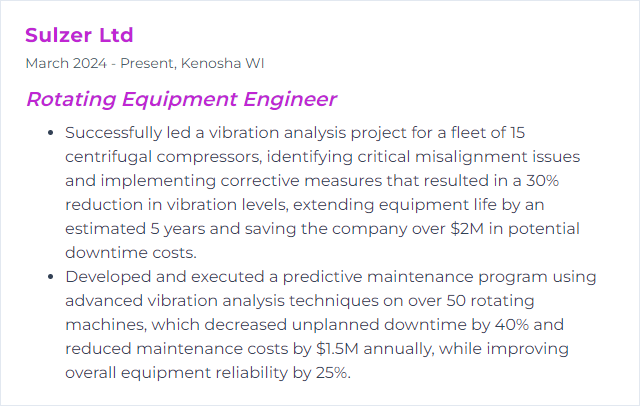
2. Tribology
Tribology is the study of friction, wear, and lubrication between surfaces in relative motion, crucial for designing, maintaining, and improving the efficiency and longevity of rotating equipment in engineering applications.
Why It's Important
Tribology is crucial for a Rotating Equipment Engineer because it studies friction, wear, and lubrication mechanisms, directly impacting the efficiency, reliability, and lifespan of rotating machinery by minimizing energy losses, preventing equipment failure, and optimizing maintenance practices.
How to Improve Tribology Skills
Improving tribology, especially for a Rotating Equipment Engineer, focuses on reducing friction and wear between moving surfaces. Here's a concise guide:
Material Selection: Choose materials with better wear resistance and lower friction coefficients. Consider surface coatings or treatments to enhance material properties. ASM International offers resources on material selection and properties.
Lubrication: Utilize appropriate lubricants to minimize direct contact between surfaces. Select lubricants based on operating conditions and compatibility with materials. The Society of Tribologists and Lubrication Engineers (STLE) provides insights into lubrication best practices.
Surface Engineering: Improve surface finishes and apply coatings to reduce friction and protect against wear. Techniques such as laser texturing or diamond-like carbon (DLC) coatings can significantly enhance performance. Surface Engineering Association offers guidance on surface engineering techniques.
Condition Monitoring: Implement condition monitoring and predictive maintenance to detect early signs of wear or lubrication failure, allowing for timely intervention. Resources on condition monitoring can be found at the International Society of Automation (ISA).
Design Optimization: Optimize component designs to distribute loads more evenly, minimize contact stresses, and improve lubricant flow. Computational tools and resources from American Society of Mechanical Engineers (ASME) can aid in design optimization.
By focusing on these areas, Rotating Equipment Engineers can significantly enhance the tribological performance of machinery, leading to increased efficiency, reduced maintenance costs, and extended equipment lifespan.
How to Display Tribology Skills on Your Resume
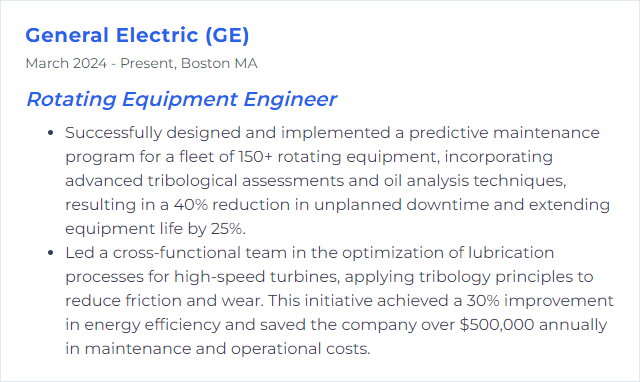
3. CAD Software
CAD software (Computer-Aided Design) is a tool used by rotating equipment engineers to create, modify, analyze, and optimize precision design and drafting of machinery components, ensuring accurate specifications and efficient design workflows.
Why It's Important
CAD software is crucial for Rotating Equipment Engineers as it enables precise design and modeling of complex machinery parts, facilitating accurate analysis, optimization of performance, and streamlined manufacturing processes, ultimately leading to enhanced reliability and efficiency of rotating equipment.
How to Improve CAD Software Skills
Improving CAD software for a Rotating Equipment Engineer involves enhancing features specific to designing, analyzing, and maintaining rotating machinery like turbines, pumps, and compressors. Here are concise improvements:
Integrate Advanced Simulation Capabilities: Incorporate advanced fluid dynamics and stress analysis tools directly into the CAD environment to enable real-time simulation and testing of rotating equipment designs (ANSYS).
Enhanced 3D Visualization: Implement superior 3D visualization tools for intricate rotating parts to allow for better design precision and easier identification of potential issues (SolidWorks).
Customizable Parts Library: Develop a comprehensive, customizable parts library specific to rotating equipment engineering, including bearings, seals, and gears, to speed up the design process (Autodesk Inventor).
Improved Collaboration Tools: Strengthen collaboration features to allow for seamless sharing and editing among team members, regardless of location, including cloud-based sharing and version control (Fusion 360).
Real-Time Performance Analytics: Embed real-time performance analytics to predict equipment behavior under various operating conditions, aiding in the optimization of design for efficiency and reliability (PTC Creo).
User-Friendly Interface: Ensure the interface is intuitive and customizable, allowing engineers to easily navigate through tools and features specific to rotating equipment design.
Comprehensive Training Resources: Offer extensive, up-to-date online tutorials and training resources tailored to rotating equipment engineering to reduce the learning curve and enhance productivity (Solid Edge).
By focusing on these improvements, CAD software can become more tailored to the specific needs of Rotating Equipment Engineers, enhancing their design, analysis, and collaboration capabilities.
How to Display CAD Software Skills on Your Resume
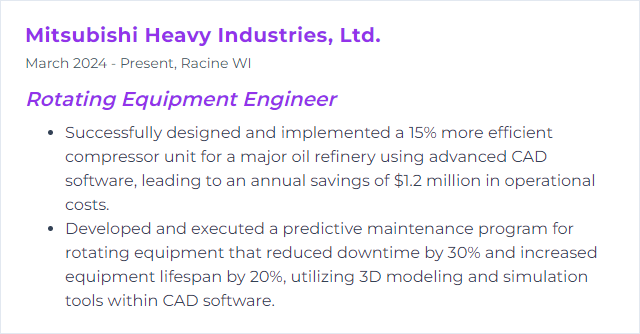
4. FEA Simulation
FEA Simulation (Finite Element Analysis) is a computational tool used by Rotating Equipment Engineers to predict stress, deformation, and vibration in equipment components under various conditions, enhancing design reliability and performance.
Why It's Important
FEA (Finite Element Analysis) simulation is crucial for a Rotating Equipment Engineer as it enables the prediction and assessment of the stress, vibration, and deformation behavior of rotating machinery components under operational conditions, ensuring their reliability, performance optimization, and failure prevention.
How to Improve FEA Simulation Skills
Improving FEA (Finite Element Analysis) simulation, especially for a Rotating Equipment Engineer, involves enhancing model accuracy, computational efficiency, and result interpretation. Here are concise strategies:
Mesh Refinement: Optimize mesh size and quality for critical components to improve accuracy without excessively increasing computational requirements. ANSYS Meshing offers guidance on balancing these aspects.
Material Properties: Ensure accurate input of material properties, including temperature-dependent behavior for metals or viscoelastic properties for polymers. MatWeb is a resource for material properties.
Boundary Conditions and Loadings: Accurately model the operating environment, considering temperature, pressure, and dynamic loads. Special attention to the application of rotational speeds and directions is crucial. SIMSCALE's Documentation provides insights into setting realistic conditions.
Solver Selection: Choose the appropriate solver and algorithms that are best suited for the problem type (e.g., transient dynamics for time-varying loads). COMSOL Multiphysics® offers various solver options for different analyses.
Verification and Validation (V&V): Perform V&V to ensure the model's accuracy. This involves comparing simulation results with analytical solutions or experimental data. NAFEMS is an authority on best practices in V&V.
Sensitivity Analysis: Conduct sensitivity analyses to understand the impact of various parameters on the model’s response, helping to prioritize which aspects of the model to refine. Engineering.com often features articles and case studies on effective sensitivity analysis.
Professional Development: Continuously update skills and knowledge in FEA tools and techniques. Online platforms like Coursera and edX offer courses on FEA and related subjects.
By focusing on these areas, Rotating Equipment Engineers can significantly improve the reliability and accuracy of their FEA simulations.
How to Display FEA Simulation Skills on Your Resume
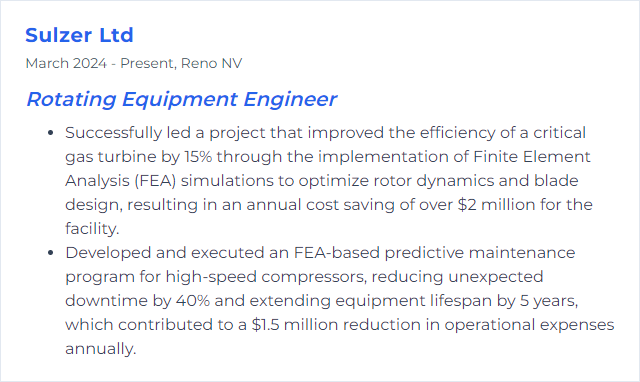
5. Condition Monitoring
Condition Monitoring is the process of continuously or periodically monitoring the performance and health of rotating equipment, such as turbines, pumps, and compressors, to detect signs of deterioration or malfunction early on. It involves collecting and analyzing data from various sensors and instruments to predict equipment failures and schedule maintenance proactively, thereby minimizing downtime and extending equipment lifespan.
Why It's Important
Condition Monitoring is crucial for a Rotating Equipment Engineer as it enables the early detection of equipment anomalies and potential failures, ensuring optimal operation, minimizing downtime, and reducing maintenance costs.
How to Improve Condition Monitoring Skills
To enhance Condition Monitoring for rotating equipment, focus on the following strategies:
Implement Vibration Analysis: Regularly analyze vibration data to detect anomalies in equipment behavior. Tools like Fluke offer comprehensive solutions.
Utilize Oil Analysis: Perform chemical analysis of equipment lubricants to identify wear particles and contaminants. Spectro Scientific is a leader in this area.
Adopt Thermal Imaging: Use thermal cameras to spot overheating issues before they lead to failure. FLIR Systems provides advanced options.
Incorporate Ultrasonic Detection: Detect mechanical and electrical issues through ultrasonic equipment. UE Systems specializes in ultrasonic condition monitoring tools.
Leverage Predictive Maintenance Software: Adopt software solutions that use AI and machine learning to predict equipment failures. IBM Maximo is a recommended option.
Continuous Training: Ensure your team is up-to-date with the latest condition monitoring techniques and tools through ongoing education.
By integrating these strategies, you'll enhance your condition monitoring efforts, leading to reduced downtime and increased equipment lifespan.
How to Display Condition Monitoring Skills on Your Resume

6. Reliability Engineering
Reliability Engineering, in the context of a Rotating Equipment Engineer, involves the systematic application of engineering principles and techniques to ensure that rotating machinery such as turbines, pumps, and compressors operates reliably and efficiently over its expected lifecycle, minimizing downtime and maintenance costs while ensuring safety and compliance with standards.
Why It's Important
Reliability Engineering is critical for a Rotating Equipment Engineer because it ensures the consistent performance and longevity of rotating machinery. By identifying and mitigating potential failures, it minimizes downtime, reduces maintenance costs, and enhances safety and operational efficiency.
How to Improve Reliability Engineering Skills
Improving Reliability Engineering, especially in the context of Rotating Equipment Engineering, involves a multifaceted approach focusing on understanding equipment failure modes, implementing predictive maintenance strategies, and fostering a culture of continuous improvement. Here’s a concise guide:
Understand Failure Modes: Begin with a thorough understanding of the common failure modes for rotating equipment by conducting Failure Mode and Effects Analysis (FMEA). This helps in identifying potential failures and their impacts on operations.
Implement Predictive Maintenance: Utilize Predictive Maintenance (PdM) technologies such as vibration analysis, oil analysis, and thermography to monitor equipment condition and predict failures before they occur.
Root Cause Analysis (RCA): When failures occur, perform Root Cause Analysis to identify the fundamental reasons behind failures, enabling you to prevent recurrence.
Reliability-Centered Maintenance (RCM): Adopt Reliability-Centered Maintenance practices that focus on maintaining system functions based on their criticality and failure modes.
Continuous Training and Education: Ensure ongoing training and education for the team to stay updated with the latest tools, technologies, and best practices in reliability engineering.
Leverage Data Analytics: Use data analytics to analyze historical performance data, which can provide insights for improving equipment reliability and performance.
Foster a Culture of Continuous Improvement: Encourage a workplace culture that emphasizes continuous improvement through regular reviews, feedback, and adjustments to maintenance strategies based on performance data and emerging technologies.
By integrating these strategies, reliability engineers can significantly improve the reliability, efficiency, and lifespan of rotating equipment, ultimately contributing to the overall operational excellence of the organization.
How to Display Reliability Engineering Skills on Your Resume
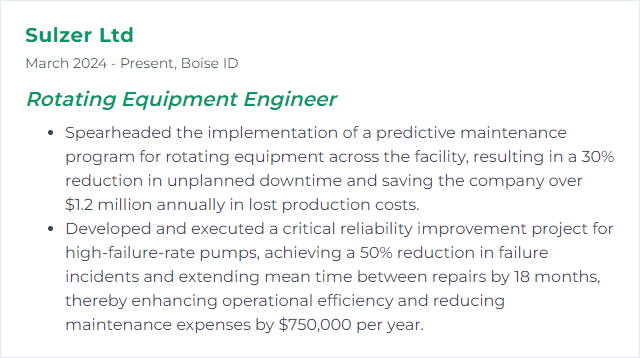
7. Pump Selection
Pump selection involves choosing the most appropriate pump type and size based on the specific requirements of a system, such as fluid properties, flow rate, pressure head, and efficiency, ensuring optimal performance and reliability in line with the application's needs.
Why It's Important
Pump selection is crucial for a Rotating Equipment Engineer to ensure optimal efficiency, reliability, and lifespan of the system by matching the pump's performance characteristics with the specific operational requirements and fluid characteristics.
How to Improve Pump Selection Skills
Improving pump selection involves several critical steps that ensure the chosen pump meets the specific requirements of your system efficiently and reliably. Here are concise guidelines for a Rotating Equipment Engineer:
Understand System Requirements: Clearly define the fluid properties (viscosity, corrosiveness, temperature), flow rate, and head requirements. Hydraulic Institute provides guidelines on assessing system needs.
Pump Type Selection: Choose the appropriate pump type (centrifugal, positive displacement, etc.) based on the fluid characteristics and system design. The PumpScout guide offers insights on selecting the right pump type.
Efficiency Consideration: Select a pump with the best efficiency point (BEP) close to your system's required operating point. The Grundfos Pump Handbook explains the importance of operating near the BEP for energy efficiency.
NPSH Evaluation: Ensure the selected pump has an NPSH available (NPSHa) higher than the NPSH required (NPSHr) to avoid cavitation. Goulds Pumps' Technical Manual includes a section on NPSH and its calculation.
Material Compatibility: Select materials compatible with the fluid to prevent corrosion and wear. The Corrosion Doctors website offers material selection guidance based on fluid properties.
Manufacturer Selection: Choose reputable manufacturers with proven track records and support services. Consulting Pump Industry Analyst can provide insights into leading manufacturers and their offerings.
Lifecycle Cost Analysis: Consider not only the initial cost but also operating, maintenance, and potential downtime costs over the pump's life. The Hydraulic Institute's Pump Life Cycle Costs Guide is a valuable resource for understanding and calculating lifecycle costs.
By following these steps and utilizing the resources provided, a Rotating Equipment Engineer can make informed and optimized pump selection decisions, leading to improved system performance, reliability, and cost-efficiency.
How to Display Pump Selection Skills on Your Resume
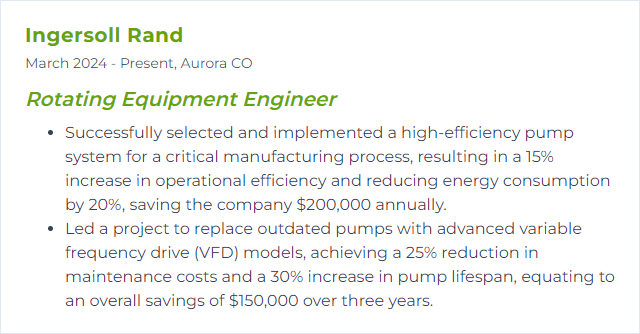
8. Compressor Design
Compressor design, in the context of a Rotating Equipment Engineer, involves specifying the configuration, components, and operating parameters of compressors to efficiently increase the pressure of gases for various industrial applications, ensuring reliability, performance, and compliance with engineering standards and project requirements.
Why It's Important
Compressor design is crucial for Rotating Equipment Engineers because it directly impacts the efficiency, reliability, and operational costs of mechanical systems. Proper design ensures optimal performance, energy conservation, and extended equipment lifespan, thereby reducing downtime and maintenance expenses.
How to Improve Compressor Design Skills
Improving compressor design involves optimizing efficiency, reliability, and performance while minimizing costs and environmental impact. Here are concise strategies for a Rotating Equipment Engineer:
Material Selection: Choose materials with high strength-to-weight ratios and corrosion resistance. Consider advanced composites or alloys for critical components. ASM International Materials
Aerodynamic Optimization: Use computational fluid dynamics (CFD) to model and optimize flow paths, reducing losses and improving efficiency. ANSYS CFD
Thermal Management: Implement effective cooling strategies and heat exchangers to maintain optimal operating temperatures. Heat Exchanger Design Handbook
Vibration Analysis: Employ finite element analysis (FEA) and operational modal analysis to predict and mitigate vibration issues. SOLIDWORKS Simulation
Advanced Manufacturing Techniques: Utilize additive manufacturing for complex geometries and reduced weight. Additive Manufacturing
Control System Integration: Implement smart controls for adaptive performance and predictive maintenance. IEEE Control Systems Society
Sealing and Bearing Technology: Select advanced seals and bearings to reduce leakage and friction losses. SKF Bearings and Seals
Environmental and Safety Standards Compliance: Design to meet the latest environmental regulations and safety standards. ISO Standards for Compressors
Each of these areas requires a balance of theoretical knowledge, practical application, and ongoing research to achieve the best possible compressor design.
How to Display Compressor Design Skills on Your Resume
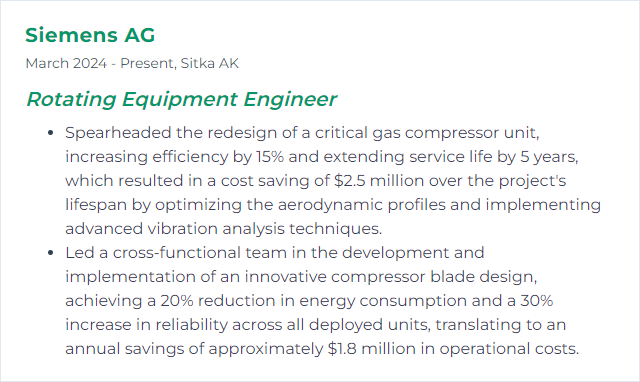
9. Rotordynamics
Rotordynamics is the study of the dynamic behavior of rotating machinery, focusing on predicting and preventing vibrational problems and instabilities within the system. It involves analyzing the forces acting on rotating components (such as shafts, disks, and blades) to ensure their stable operation, critical for a Rotating Equipment Engineer in designing, maintaining, and troubleshooting rotating machinery to avoid failures and extend equipment life.
Why It's Important
Rotordynamics is crucial for ensuring the safety, reliability, and efficiency of rotating machinery by predicting and managing vibrations, ensuring optimal performance, and preventing catastrophic failures.
How to Improve Rotordynamics Skills
To improve Rotordynamics, focus on the following key areas:
Design Optimization: Enhance rotor design by considering factors like shape, material, and mass distribution. Utilize software like ANSYS for simulation and optimization.
Balance Improvement: Achieve better rotor balance by employing precision balancing techniques. Tools like Schenck Balancing Machines can aid in this.
Bearing Selection and Placement: Opt for appropriate bearing types and carefully determine their placement to minimize vibrations. SKF provides a comprehensive bearing selection guide.
Damping Mechanisms: Incorporate damping elements to absorb energy from system vibrations, thereby reducing amplitude. Research on TMDs (Tuned Mass Dampers) for application in rotordynamics.
Regular Maintenance and Monitoring: Implement predictive maintenance strategies and use monitoring tools like VIBXPERT II for early detection of potential issues.
Professional Development: Stay updated with the latest advancements in Rotordynamics by engaging with resources and communities like The Vibration Institute.
Focusing on these areas, while continuously learning and adapting to new technologies, will significantly improve the performance and reliability of rotating equipment.
How to Display Rotordynamics Skills on Your Resume
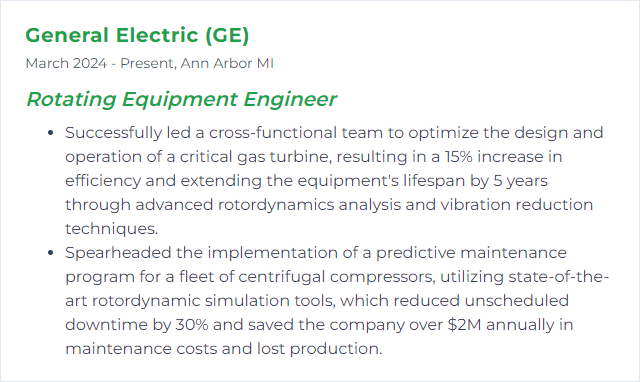
10. Laser Alignment
Laser alignment is a precision method used by rotating equipment engineers to adjust the relative position of rotating machinery components, ensuring their axes are co-linear. This process minimizes wear, vibration, and energy loss, optimizing equipment performance and lifespan.
Why It's Important
Laser alignment is crucial for a Rotating Equipment Engineer because it ensures precision in the alignment of rotating machinery components. This minimizes vibration, reduces wear and tear on parts, extends equipment lifespan, and enhances operational efficiency and reliability.
How to Improve Laser Alignment Skills
Improving laser alignment for rotating equipment involves precise adjustment and calibration to ensure optimal machinery performance. Follow these concise steps:
Preparation: Clean all coupling, shaft, and machinery surfaces. Ensure equipment is in a relaxed state without any residual stress.
Mounting: Attach the laser and receiver units securely on the shafts or coupling hubs following the manufacturer's instructions. Mounting Techniques
Rough Alignment: Manually adjust the machinery to bring it within the rough alignment tolerances. Use a straight edge or a dial indicator for this initial step. Rough Alignment Guide
Measurement: Power on the laser alignment tool and rotate the shafts to take measurements. Ensure to follow the specific procedure provided by the laser alignment tool manufacturer.
Analysis: Analyze the data using the tool's software to understand misalignment issues (horizontal, vertical, angular, or a combination). Understanding Misalignment
Adjustment: Adjust the position of the machines based on the analysis. This may involve shimming or moving the machine horizontally. Shimming and Moving Guide
Verification: After adjustments, perform another measurement to ensure the alignment is within the desired tolerances. Repeat adjustment if necessary.
Documentation: Record all final alignment values and adjustments made for future reference. Importance of Documentation
Maintenance: Regularly check and maintain alignment, especially after machinery service or component replacement.
By following these steps, a Rotating Equipment Engineer can improve laser alignment, leading to reduced vibration, decreased wear, and extended equipment life. Always refer to the equipment manufacturer's guidelines and the laser alignment tool's manual for specific instructions and safety precautions.
How to Display Laser Alignment Skills on Your Resume
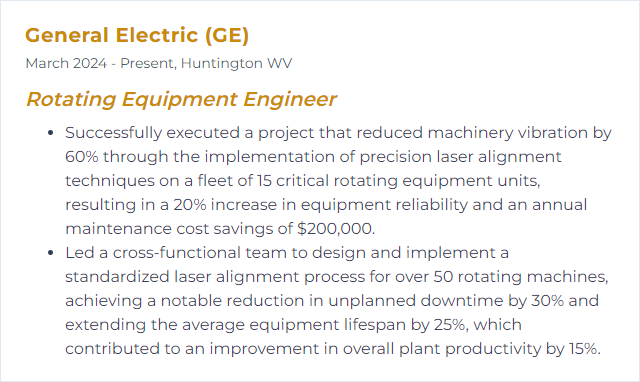
11. Thermodynamics
Thermodynamics is the branch of physics that deals with the relationships between heat and other forms of energy, particularly in how energy is conserved and converted from one form to another. For a Rotating Equipment Engineer, it is fundamental in understanding how energy transformations within machines like turbines, compressors, and engines affect their efficiency, performance, and operational limits.
Why It's Important
Thermodynamics is crucial for a Rotating Equipment Engineer because it provides fundamental principles for understanding energy transformations and efficiency in machinery, enabling the design, analysis, and optimization of rotating equipment such as turbines, compressors, and pumps for maximum performance and energy conservation.
How to Improve Thermodynamics Skills
Improving your understanding of thermodynamics as a Rotating Equipment Engineer involves focusing on the principles that directly affect machinery performance, efficiency, and reliability. Here's a concise guide to enhancing your thermodynamics knowledge:
Grasp the Basics: Ensure a solid understanding of the first and second laws of thermodynamics, as they apply to energy conservation and efficiency in machinery. Khan Academy offers a comprehensive foundation.
Understand Heat Transfer: Master the mechanisms of heat transfer (conduction, convection, and radiation) and their implications on equipment. Engineering Toolbox is a practical resource for engineers.
Study Fluid Mechanics: Since thermodynamics and fluid mechanics are intertwined in rotating equipment, a thorough understanding of fluid behavior enhances your ability to design and analyze systems. MIT OpenCourseWare provides in-depth courses.
Learn from Case Studies: Analyze real-world failures and performance studies of rotating equipment to see thermodynamic principles in action. ScienceDirect offers access to numerous engineering journals and case studies.
Software Tools: Familiarize yourself with simulation software (such as ANSYS or COMSOL Multiphysics) that allows for the modeling of thermodynamic processes in rotating equipment. Tutorials and learning resources are available on their respective ANSYS Learning Hub and COMSOL Learning Center.
Professional Development: Attend workshops, webinars, and courses focused on advanced thermodynamics and rotating equipment engineering. Organizations like ASME offer specialized training and certifications.
Networking and Knowledge Sharing: Engage with professional communities and forums (e.g., Eng-Tips Forums) to exchange knowledge, experiences, and stay updated on industry trends.
By focusing on these steps and leveraging the provided resources, you'll strengthen your thermodynamics foundation and apply this knowledge effectively in your role as a Rotating Equipment Engineer.
How to Display Thermodynamics Skills on Your Resume
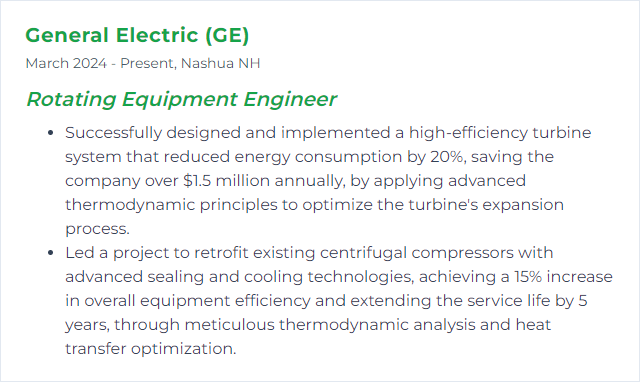
12. CFD Analysis
CFD (Computational Fluid Dynamics) Analysis is a computational tool used by Rotating Equipment Engineers to simulate and study the flow of fluids and gas around and through rotating machinery. It helps in optimizing design, predicting performance, and diagnosing issues by analyzing fluid interactions with the equipment under various operating conditions.
Why It's Important
CFD (Computational Fluid Dynamics) analysis is crucial for a Rotating Equipment Engineer because it enables the prediction and optimization of fluid flow and thermal characteristics in and around rotating machinery, enhancing performance, reliability, and efficiency while reducing wear, energy consumption, and the likelihood of failure.
How to Improve CFD Analysis Skills
Improving CFD (Computational Fluid Dynamics) analysis, especially for a Rotating Equipment Engineer, involves several steps focusing on enhancing accuracy, efficiency, and reliability of simulations. Here’s a concise guide:
Mesh Refinement: Optimize mesh around critical areas (e.g., near blades or rotating parts) to capture flow details accurately. Adaptive mesh refinement techniques can be particularly useful. ANSYS Meshing Guide.
Turbulence Modeling: Choose appropriate turbulence models (e.g., k-ε, k-ω SST) that best represent the flow characteristics of your specific application. Understanding the strengths and limitations of each model is crucial. Turbulence Modeling Resource.
Rotating Frame of Reference: Utilize a rotating frame of reference or sliding mesh technique for dynamic simulations involving moving parts to accurately capture the interaction between the rotating and stationary components. Rotating Frame of Reference Guide.
Boundary Conditions and Physical Models: Ensure that boundary conditions reflect the real-world scenario. Incorporate relevant physical models (e.g., cavitation, multiphase flows) to capture the physics of the problem accurately. Introduction to Boundary Conditions in CFD.
Validation and Verification: Continuously validate and verify your CFD models against experimental data or trusted benchmarks to ensure accuracy and reliability of the simulations. CFD Validation Best Practices.
High-Performance Computing (HPC): Leverage HPC resources to handle complex simulations with higher fidelity within reasonable time frames. This allows for more detailed analyses and faster iteration cycles. Guide to HPC for CFD.
Continual Learning: Stay updated with the latest CFD tools, techniques, and practices through workshops, webinars, and courses. Engage with the community through forums and professional networks. CFD Online is a great resource.
Improving CFD analysis is a continuous process of learning, experimenting, and validating to ensure that simulations accurately represent physical phenomena, thus aiding in the effective design and optimization of rotating equipment.
How to Display CFD Analysis Skills on Your Resume
