Top 12 Equipment Engineer Skills to Put on Your Resume
In today's competitive job market, standing out as an equipment engineer requires showcasing a blend of technical prowess and soft skills on your resume. Highlighting the top equipment engineer skills effectively communicates to potential employers your capability to innovate, solve complex problems, and contribute to the success of their operations.
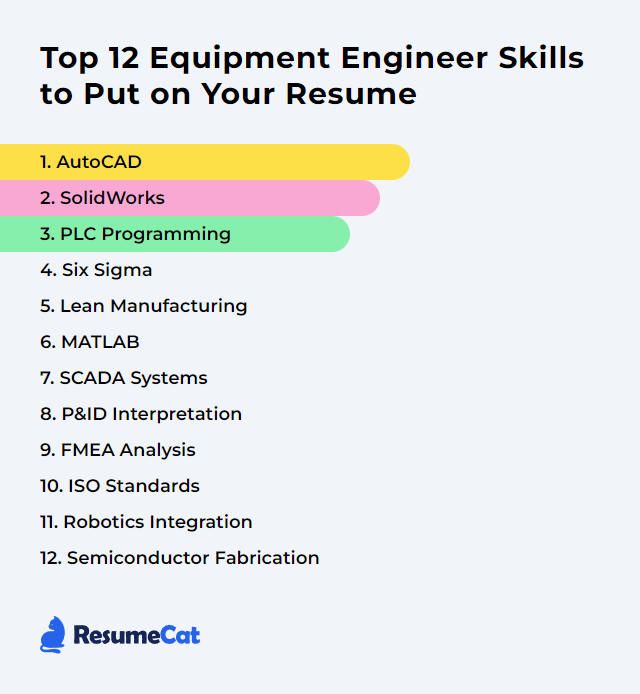
Equipment Engineer Skills
- AutoCAD
- SolidWorks
- PLC Programming
- Six Sigma
- Lean Manufacturing
- MATLAB
- SCADA Systems
- P&ID Interpretation
- FMEA Analysis
- ISO Standards
- Robotics Integration
- Semiconductor Fabrication
1. AutoCAD
AutoCAD is a computer-aided design (CAD) software used by equipment engineers for drafting and designing equipment, machinery components, and systems with precision, allowing for 2D and 3D modeling and documentation.
Why It's Important
AutoCAD is crucial for an Equipment Engineer because it enables precise design, modification, and optimization of equipment and machinery, ensuring accuracy, efficiency, and compatibility with existing systems, ultimately leading to improved performance and reduced production costs.
How to Improve AutoCAD Skills
To improve AutoCAD skills as an Equipment Engineer, focus on the following concise strategies:
Understand the Basics Thoroughly: Start with mastering fundamental concepts and commands. Autodesk's official tutorials provide a solid foundation.
Customize Your Workspace: Tailor your AutoCAD interface and toolsets for equipment engineering tasks. This Customization Guide helps in optimizing your workflow.
Learn 3D Modeling: As an Equipment Engineer, proficiency in 3D modeling is crucial. Explore Autodesk's 3D modeling resources to enhance your designs.
Utilize AutoCAD Libraries and Toolsets: Leverage specialized toolsets and libraries for mechanical design. Autodesk offers a Mechanical Toolset that can significantly speed up engineering tasks.
Practice with Real-World Projects: Apply your skills on actual equipment engineering projects. Engage with communities like Autodesk Forums for insights and feedback.
Stay Updated: AutoCAD frequently updates its software. Stay informed on the latest features and how they can benefit your engineering work. Monitor the AutoCAD Blog for updates and tips.
Training and Certification: Consider official AutoCAD training and certification to validate your skills and knowledge. Check the Certification Page for details on specialized courses for engineers.
By integrating these strategies, you'll enhance your AutoCAD proficiency, contributing to more efficient and innovative equipment design projects.
How to Display AutoCAD Skills on Your Resume
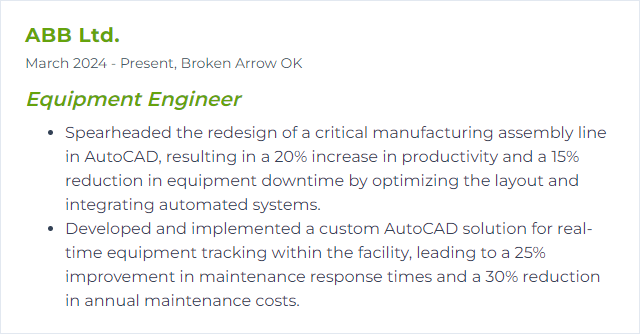
2. SolidWorks
SolidWorks is a computer-aided design (CAD) and engineering software used by equipment engineers to create 3D models, assemblies, and detailed drawings of machinery and equipment.
Why It's Important
SolidWorks is important for an Equipment Engineer because it enables precise 3D modeling and simulation of equipment designs, facilitating efficient development, testing, and optimization of machinery and components, ensuring performance, reliability, and manufacturability.
How to Improve SolidWorks Skills
Improving your SolidWorks skills as an Equipment Engineer involves a combination of practice, learning new techniques, and leveraging advanced features. Here are concise steps to enhance your proficiency:
Tutorials and Online Courses: Begin with SolidWorks tutorials to understand the basics and gradually move to complex concepts.
Practice Regularly: Apply your learning by working on real-world projects or simulations relevant to equipment engineering.
Use SolidWorks Resources: Access the SolidWorks Resource Center for tutorials, tips, and tricks.
Join Forums and Communities: Engage with the SolidWorks Community to exchange knowledge, solve problems, and learn from experienced users.
Certification Programs: Consider obtaining a Certification to validate your skills and learn advanced techniques.
Stay Updated: Keep abreast of new features and updates by regularly checking the SolidWorks Blog.
Optimize SolidWorks Performance: Follow best practices for managing large assemblies and optimizing performance by referring to SolidWorks Support resources.
Customize Your Workflow: Learn to customize SolidWorks to your specific needs for equipment engineering by creating templates, macros, and using the API for automation.
By integrating these strategies, you can significantly improve your SolidWorks skills, making your design process more efficient and productive.
How to Display SolidWorks Skills on Your Resume
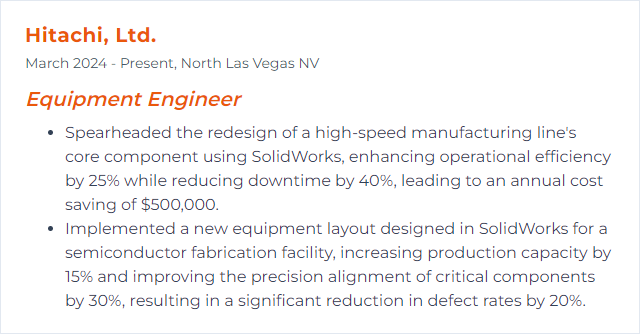
3. PLC Programming
PLC programming involves creating and implementing instructions for Programmable Logic Controllers (PLCs) to automate machinery and industrial processes. As an Equipment Engineer, it enables you to design, develop, and troubleshoot control systems for efficient and reliable equipment operation.
Why It's Important
PLC programming is essential for an Equipment Engineer as it allows for the precise control and automation of machinery, ensuring efficient, reliable, and safe operation of production equipment in industrial environments.
How to Improve PLC Programming Skills
Improving PLC programming as an Equipment Engineer involves enhancing both your technical skills and understanding of the specific machinery or process you are working with. Here are concise steps with relevant resources:
Understand the Basics Thoroughly: Ensure a solid foundation in PLC programming concepts and languages. PLC Academy offers a good starting point.
Learn from Examples: Analyze and dissect existing PLC programs to understand their structure and logic. PLCdev has sample code and project examples.
Stay Updated with Technology: Continuously learn about new PLC technologies and features. Websites like Automation.com provide the latest industry news and technology updates.
Practice Regularly: Apply what you learn by working on real projects or simulations. TheLearningPit offers PLC simulators for practice.
Understand Your Equipment: Deeply understand the machinery or process you are automating. Manufacturer manuals and ISA (International Society of Automation) resources can be invaluable.
Enhance Your Problem-Solving Skills: Work on developing systematic problem-solving techniques. Books like "Structured Text Programming" can offer insights into efficient problem-solving strategies in PLC programming.
Networking and Professional Development: Join forums and groups like PLCTalk for knowledge sharing and professional networking.
Implement Best Practices: Adopt industry best practices for programming, documenting, and testing. Resources like Control Engineering offer articles and guides on best practices.
By focusing on these areas and leveraging the suggested resources, you can significantly improve your PLC programming skills in the context of equipment engineering.
How to Display PLC Programming Skills on Your Resume
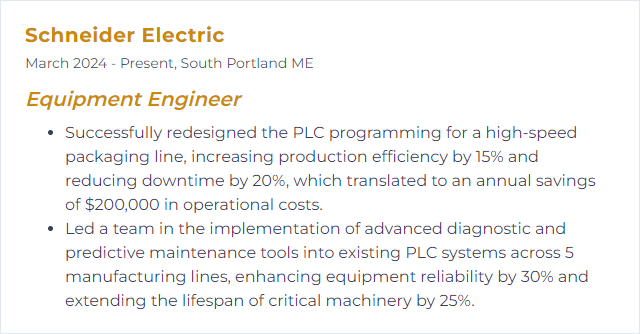
4. Six Sigma
Six Sigma is a data-driven methodology aimed at improving quality by identifying and eliminating defects in processes, including those in equipment engineering, to achieve near-perfect performance.
Why It's Important
Six Sigma is important for an Equipment Engineer because it provides a systematic methodology to reduce defects, improve process efficiency, and ensure the reliability of equipment, leading to higher quality products, reduced downtime, and increased customer satisfaction.
How to Improve Six Sigma Skills
Improving Six Sigma for an Equipment Engineer involves focusing on reducing variability and defects in equipment processes. Here are concise strategies:
Enhance Measurement and Analysis: Implement advanced measurement tools and techniques for precise analysis of equipment performance. Learn more about measurement systems analysis here.
Optimize Equipment Maintenance: Shift towards predictive maintenance using IoT and data analytics to foresee equipment failures. Explore predictive maintenance strategies here.
Streamline Process Improvement: Utilize DMAIC (Define, Measure, Analyze, Improve, Control) methodology specifically tailored for equipment efficiency. A quick guide on DMAIC can be found here.
Enhance Training and Certification: Invest in Six Sigma certification for specialized knowledge on equipment optimization. Information on Six Sigma certification is available here.
Leverage Technology and Automation: Introduce automation and AI to reduce human error and improve process consistency. Insight on automation in Six Sigma is accessible here.
Foster a Culture of Continuous Improvement: Encourage feedback and innovative ideas from the team to continually improve equipment processes. Tips on building this culture are offered here.
By focusing on these areas, an Equipment Engineer can significantly contribute to enhancing Six Sigma initiatives within their organization.
How to Display Six Sigma Skills on Your Resume
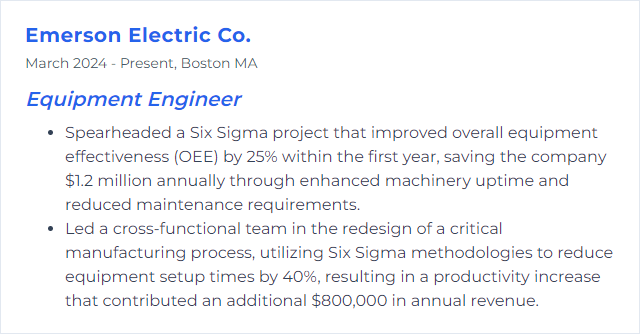
5. Lean Manufacturing
Lean Manufacturing is a systematic approach to reducing waste and improving efficiency in production processes, focusing on maximizing value for the customer by optimizing the use of resources, including equipment, materials, and labor. For an Equipment Engineer, this means designing, selecting, and maintaining machinery and tools that support streamlined operations, minimize downtime, and enhance productivity.
Why It's Important
Lean Manufacturing is crucial for an Equipment Engineer as it streamlines production processes, reduces waste and downtime, optimizes equipment efficiency, and enhances product quality, leading to increased productivity and cost savings.
How to Improve Lean Manufacturing Skills
Improving Lean Manufacturing, particularly from an Equipment Engineer's perspective, involves optimizing processes, reducing waste, and enhancing efficiency. Here are concise strategies:
- Continuous Improvement: Embrace Kaizen, focusing on small, incremental changes to improve efficiency and quality.
- Value Stream Mapping: Identify and eliminate waste in processes through Value Stream Mapping, enhancing flow and reducing cycle times.
- TPM (Total Productive Maintenance): Implement TPM to maximize equipment effectiveness, minimizing downtime and defects.
- 5S Methodology: Apply 5S (Sort, Set in order, Shine, Standardize, Sustain) to organize the workplace, improving efficiency and safety.
- Jidoka (Autonomation): Utilize Jidoka to detect and prevent errors, ensuring equipment stops in the event of anomalies.
By focusing on these areas, an Equipment Engineer can significantly contribute to the efficiency and effectiveness of Lean Manufacturing initiatives.
How to Display Lean Manufacturing Skills on Your Resume
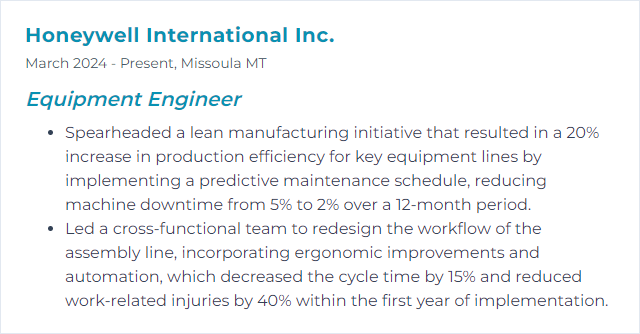
6. MATLAB
MATLAB is a high-level programming language and environment used for numerical computing, data analysis, and algorithm development, particularly useful in engineering for simulating, testing, and analyzing the performance and behavior of equipment and systems.
Why It's Important
MATLAB is important for an Equipment Engineer because it provides powerful tools for numerical analysis, simulation, and visualization, enabling efficient design, testing, and optimization of equipment and systems.
How to Improve MATLAB Skills
To improve MATLAB skills as an Equipment Engineer, focus on:
- Master the Basics: Understand MATLAB syntax, data types, and basic functions. MATLAB's Getting Started guide is a great resource.
- Learn MATLAB for Hardware Interface: Focus on MATLAB's capabilities for interfacing with equipment via Instrument Control Toolbox.
- Explore Data Analysis and Visualization: Utilize MATLAB for analyzing equipment data and visualizing results. The Data Analysis section offers insights.
- Automate Tasks with Scripts: Write scripts to automate routine data processing and equipment control tasks. The MATLAB Scripts documentation provides guidelines.
- Optimize Performance: Learn how to optimize code for performance, crucial for real-time equipment monitoring. MATLAB's Code Optimization guide can help.
- Use MATLAB’s Online Resources: Engage with MATLAB’s online community for code examples, answers, and tutorials.
- Continuous Learning: MATLAB evolves, so keep learning new features and tools relevant to equipment engineering, available through MATLAB's training services.
By focusing on these areas and utilizing MATLAB's extensive resources, you can significantly improve your MATLAB skills in the context of equipment engineering.
How to Display MATLAB Skills on Your Resume
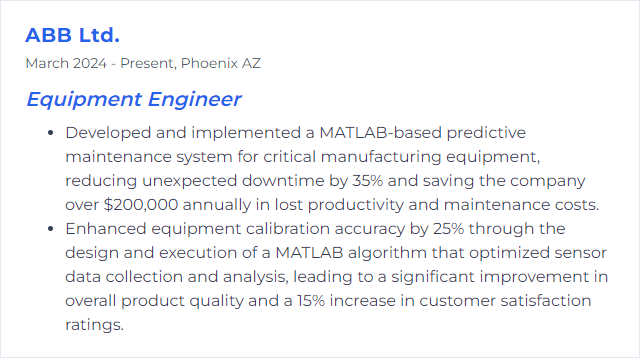
7. SCADA Systems
SCADA systems (Supervisory Control and Data Acquisition) are centralized systems used by equipment engineers to monitor and control industrial processes and machinery. They gather real-time data from sensors on equipment, enabling remote control of devices, optimization of operations, and enhanced troubleshooting capabilities.
Why It's Important
SCADA Systems are crucial for Equipment Engineers because they enable real-time monitoring and control of industrial equipment, ensuring operational efficiency, safety, and reliability.
How to Improve SCADA Systems Skills
Improving SCADA (Supervisory Control and Data Acquisition) systems, especially from an Equipment Engineer's perspective, involves enhancing reliability, security, and efficiency. Here are concise strategies:
Upgrade Security Measures: Implement robust cybersecurity practices to protect against malware and unauthorized access. National Institute of Standards and Technology (NIST) offers guidelines for industrial control system security.
Integrate with IoT: Enhance data collection and monitoring by integrating IoT (Internet of Things) technologies. This can lead to predictive maintenance capabilities. IEEE Xplore provides insights into IoT integration.
Implement Redundancy: Ensure system reliability by implementing redundancy at critical points to avoid single points of failure. ISA (International Society of Automation) offers resources on system design, including redundancy.
Regular Updates and Maintenance: Keep the SCADA software and hardware components updated to the latest standards. This includes patch management and hardware upgrades.
Improve User Interface: Enhance the user interface for better usability and efficiency in monitoring and control tasks. Principles of effective UI design can be found in resources like Nielsen Norman Group.
Data Analytics and AI: Incorporate data analytics and AI for predictive analysis and to optimize operations. Resources on AI in industrial applications can be found at AI Magazine.
Training and Awareness: Regular training for operators and engineers on the latest SCADA technologies and security practices. Training materials and courses can often be found through professional bodies like ISA.
Network Segmentation: Segment SCADA networks from business networks to minimize cybersecurity risks. Guidelines on network segmentation are available through cybersecurity frameworks like NIST.
Real-time Monitoring and Alerts: Implement real-time monitoring systems with instant alerting mechanisms for system anomalies. IEEE Xplore and other technical repositories have research on real-time monitoring systems.
Compliance with Standards: Adhere to international standards like IEC 62443 for industrial communication networks and systems security. Information on standards can be found at IEC.
Improving SCADA systems is an ongoing process that involves staying updated on the latest technologies, security practices, and industry standards.
How to Display SCADA Systems Skills on Your Resume
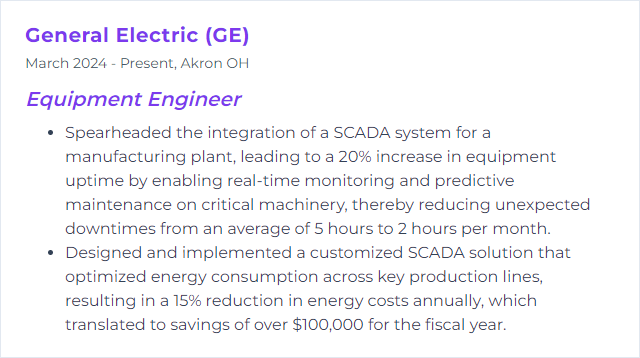
8. P&ID Interpretation
P&ID interpretation for an Equipment Engineer involves analyzing and understanding Piping and Instrumentation Diagrams (P&IDs) to identify the process flow, equipment details, and instrumentation requirements for designing, maintaining, or troubleshooting process systems.
Why It's Important
P&ID (Piping and Instrumentation Diagram) interpretation is crucial for an Equipment Engineer as it ensures accurate understanding and implementation of the process design and operational requirements of machinery and systems, enabling efficient, safe, and compliant engineering solutions.
How to Improve P&ID Interpretation Skills
Improving P&ID (Piping and Instrumentation Diagram) interpretation as an Equipment Engineer involves honing skills in understanding the symbols, conventions, and layout of these diagrams, which are crucial for designing, modifying, and maintaining process systems. Here's a concise guide:
Familiarize with Symbols: Start by learning the standard symbols for equipment, piping, and instrumentation as outlined in ISA-5.1. ISA's guide can serve as a comprehensive resource.
Understand Line Types: Recognize the different line types (solid, dashed, etc.) and their meanings, representing process, utility, or information transfer lines.
Study Process Flow: Trace the process flow from start to finish, understanding how different components interact. Engineering Toolbox provides insights into process flow understanding.
Learn Abbreviations and Tags: Equip yourself to decode the abbreviations and tag numbers used in P&IDs, which identify specific equipment and instruments. This abbreviations list can be a handy reference.
Engage with Real Diagrams: Practice interpreting real P&IDs related to your field. Hands-on experience is invaluable. Websites like P&ID Diagram Basics offer examples and explanations.
Seek Feedback and Clarifications: Discuss your interpretations with experienced engineers or during team meetings to clarify doubts and correct misunderstandings.
Continuous Learning: Stay updated with industry standards and attend workshops or webinars focused on P&ID interpretation. Professional bodies like ASME often host relevant learning events.
By integrating these steps into your professional development, you can significantly enhance your P&ID interpretation skills, leading to better equipment design, safety, and operational efficiency.
How to Display P&ID Interpretation Skills on Your Resume
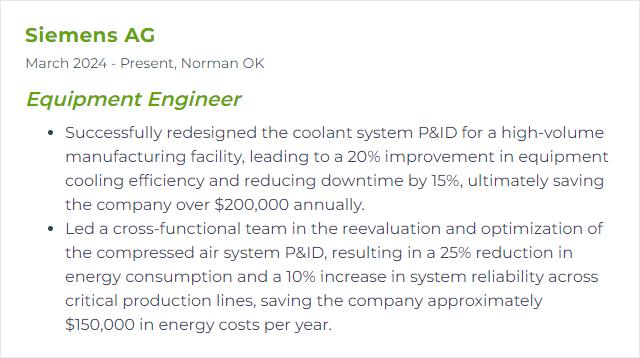
9. FMEA Analysis
FMEA (Failure Modes and Effects Analysis) is a systematic method used by equipment engineers to identify, prioritize, and mitigate potential failures in equipment and processes, aiming to enhance reliability and safety by preventing failures before they occur.
Why It's Important
FMEA (Failure Mode and Effects Analysis) is crucial for an Equipment Engineer because it systematically identifies potential failures in equipment design, manufacturing, or process before they occur. This proactive approach helps prioritize and mitigate risks, ensuring reliability, safety, and cost-effectiveness in equipment operation and maintenance.
How to Improve FMEA Analysis Skills
Improving FMEA (Failure Mode and Effects Analysis) for an Equipment Engineer involves focusing on systematic evaluation, team collaboration, and continuous improvement. Here are concise steps with relevant resources:
Strengthen Team Composition: Involve cross-functional team members with diverse expertise to cover all aspects of potential failures. ASQ's Guide offers insights on team composition.
Enhance Data Quality: Use accurate and up-to-date data for analysis. Incorporate historical data, manufacturer data, and expert opinions. The Reliability Information Analysis Center is a valuable resource for reliability data.
Prioritize Failure Modes: Use the RPN (Risk Priority Number) effectively to prioritize issues, focusing on high-risk areas first. Quality-One provides a detailed explanation of this process.
Implement Robust Detection Methods: Improve the detection strategies for identifying potential failures early. Techniques and tools can be found in IEEE Xplore.
Continuous Learning and Improvement: Learn from each FMEA iteration. Implement lessons learned and best practices. The Engineering Management Institute offers resources for continuous improvement.
Leverage Technology: Use FMEA software tools for better data management and analysis. PFMEA Tool Guide discusses software options.
Training and Education: Invest in FMEA and reliability engineering training for the team. ASME Training & Development offers relevant courses.
By focusing on these areas, Equipment Engineers can significantly improve the effectiveness of their FMEA analysis.
How to Display FMEA Analysis Skills on Your Resume
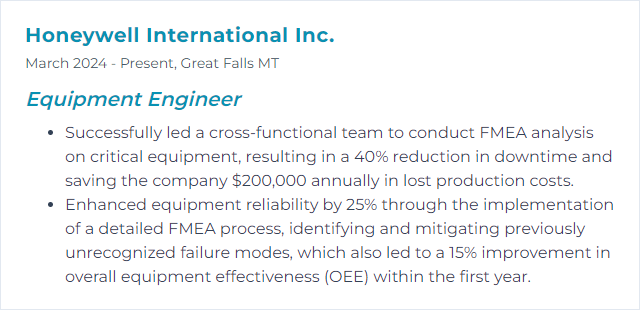
10. ISO Standards
ISO standards are internationally recognized guidelines and specifications designed to ensure quality, safety, efficiency, and interoperability of products, services, and systems. For an Equipment Engineer, they provide a framework for design, manufacturing, testing, and maintenance practices to ensure equipment meets global quality and performance benchmarks.
Why It's Important
ISO Standards are important for an Equipment Engineer because they ensure reliability, safety, and efficiency of equipment through internationally recognized quality and performance benchmarks, facilitating global compatibility and interoperability.
How to Improve ISO Standards Skills
To improve ISO standards as an Equipment Engineer, follow these concise steps:
Understand Current Standards: Begin by thoroughly understanding the existing ISO standards relevant to your field. Review the ISO Catalogue for the latest updates and standards.
Identify Gaps and Opportunities: Assess current processes and equipment against these standards to identify gaps or areas for improvement.
Engage with ISO Committees: Participate in ISO technical committees or working groups related to your expertise. This provides a platform to propose changes or new standards. Find committees through the ISO Committees page.
Collaborate and Network: Collaborate with other professionals and organizations to gather a broad perspective on what improvements can be made. Networking can be facilitated through platforms like LinkedIn or industry-specific forums.
Continuous Learning: Stay informed about new technologies, methodologies, and industry trends. Engage in continuous professional development through courses and certifications from recognized bodies like ASME or IEEE.
Implement and Document: Apply your improvements in your organizational context, documenting the processes and results meticulously. This documentation can support your proposals for ISO standard improvements.
Submit Proposals: Draft and submit proposals for new standards or revisions to existing standards through the proper ISO channels. Guidance on making proposals can be found on the ISO Developing Standards page.
Feedback and Revision: Be open to feedback from the ISO review process and be prepared to revise and resubmit your proposals based on this feedback.
Promote Best Practices: Share your knowledge and the importance of adherence to ISO standards within your organization and the wider engineering community.
Monitor and Evaluate: After the implementation of any new or revised standard, monitor the outcomes and evaluate against the objectives to ensure continuous improvement.
By following these steps, Equipment Engineers can actively contribute to the enhancement of ISO standards, ensuring they remain relevant and effective in improving quality, safety, and efficiency within the industry.
How to Display ISO Standards Skills on Your Resume

11. Robotics Integration
Robotics integration involves the process of planning, designing, and implementing robotic systems into existing industrial environments to enhance automation, efficiency, and productivity, tailored to the specific needs and operational goals of the facility. For an Equipment Engineer, it encompasses selecting the appropriate robots, designing the system layout, ensuring compatibility with existing equipment, and overseeing the installation and programming of robots to perform designated tasks.
Why It's Important
Robotics integration is crucial for an Equipment Engineer as it enhances efficiency, accuracy, and productivity in manufacturing processes, enabling the design and deployment of automated solutions that reduce downtime, minimize errors, and ensure consistent quality, ultimately optimizing operational performance and competitiveness.
How to Improve Robotics Integration Skills
To improve Robotics Integration as an Equipment Engineer, focus on the following key steps:
Understand Requirements: Clearly define the robotic system's goals and requirements. RoboDK's Guide offers insights on specifying robotic system needs.
Select Appropriate Robots: Choose robots that match your application's needs in terms of payload, reach, precision, and speed. ABB's Robot Selector Tool can aid in finding the right robot.
Simulation and 3D Modeling: Use software like RobotStudio for simulation and 3D modeling to visualize and optimize the workflow before physical integration.
Integration with Existing Systems: Ensure seamless integration with existing manufacturing systems. IEEE's guide on industrial network integration provides valuable insights.
Programming and Training: Learn robot programming languages and attend training sessions. Universal Robots Academy offers free online courses.
Safety and Compliance: Adhere to safety standards and regulations. The Robotic Industries Association provides resources on robot safety standards.
Maintenance and Support: Develop a maintenance plan and ensure access to support. Fanuc's Lifecycle Management highlights the importance of ongoing support.
By following these steps and utilizing the provided resources, you can effectively improve robotics integration in your projects.
How to Display Robotics Integration Skills on Your Resume
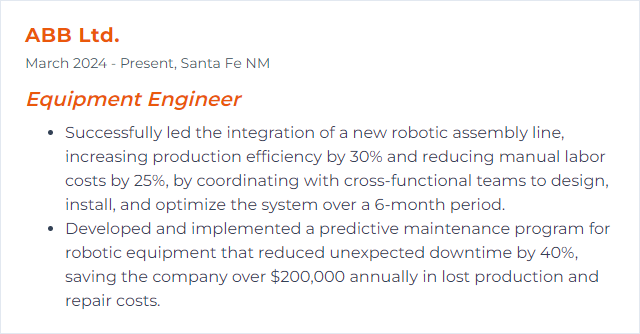
12. Semiconductor Fabrication
Semiconductor fabrication is the process of creating integrated circuits (ICs) on silicon wafers through various manufacturing steps including lithography, doping, etching, and deposition, under highly controlled conditions. For an Equipment Engineer, it involves overseeing, maintaining, and optimizing the complex machinery and systems used in these processes to ensure precision, efficiency, and quality in chip production.
Why It's Important
Semiconductor fabrication is crucial as it involves the complex process of manufacturing semiconductor devices, the foundational components for electronic equipment. For an Equipment Engineer, it is essential because it directly impacts the efficiency, performance, and reliability of the equipment they design, maintain, or improve, enabling advancements in technology and innovation in various industries.
How to Improve Semiconductor Fabrication Skills
Improving semiconductor fabrication, especially from an Equipment Engineer's perspective, involves optimizing processes, equipment maintenance, and adopting cutting-edge technologies. Here's a concise guide:
Process Optimization: Continuously analyze and refine manufacturing processes to enhance yield and efficiency. Utilize process simulation software to predict outcomes and implement changes.
Preventive Maintenance: Implement a rigorous preventive maintenance schedule to minimize downtime and maintain equipment performance at its peak.
Equipment Upgrade: Stay informed about the latest advancements in semiconductor manufacturing equipment. Upgrading to newer, more efficient models can significantly improve fabrication capabilities.
Training and Development: Ensure that all equipment operators are continuously trained on the latest operational techniques and safety protocols. SEMI offers courses and certifications relevant to semiconductor manufacturing.
Collaboration with Suppliers: Work closely with equipment and material suppliers to ensure you're using the best possible resources. This can also help in troubleshooting and optimizing equipment performance.
Adopt Automation and AI: Leverage automation and artificial intelligence to improve process control, predict maintenance needs, and enhance quality control.
By focusing on these areas, an Equipment Engineer can significantly contribute to improving semiconductor fabrication efficiency and yield.
How to Display Semiconductor Fabrication Skills on Your Resume
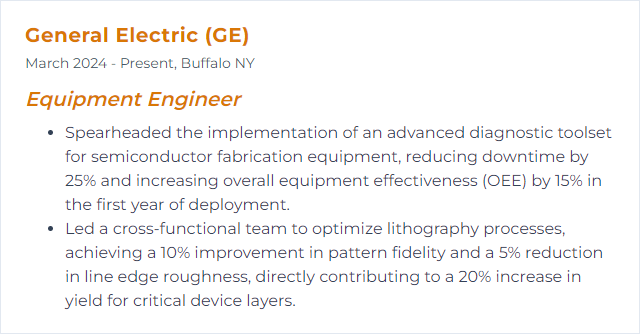