Top 12 Quality Systems Manager Skills to Put on Your Resume
To excel as a Quality Systems Manager, incorporating a blend of technical expertise and soft skills into your resume is essential. Highlighting these skills showcases your ability to oversee quality systems effectively, ensuring products meet both customer expectations and regulatory standards.
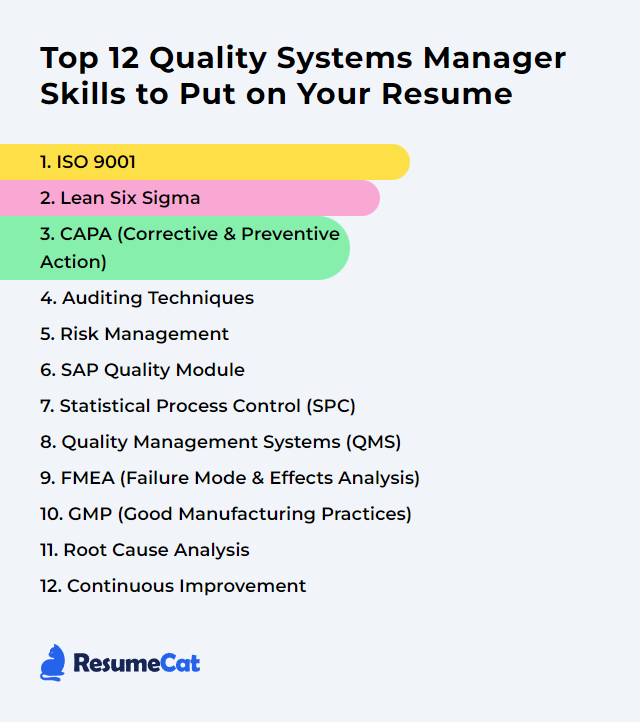
Quality Systems Manager Skills
- ISO 9001
- Lean Six Sigma
- CAPA (Corrective and Preventive Action)
- Auditing Techniques
- Risk Management
- SAP Quality Module
- Statistical Process Control (SPC)
- Quality Management Systems (QMS)
- FMEA (Failure Mode and Effects Analysis)
- GMP (Good Manufacturing Practices)
- Root Cause Analysis
- Continuous Improvement
1. ISO 9001
ISO 9001 is an international standard for quality management systems (QMS), outlining criteria to ensure consistency in providing products and services that meet customer and regulatory requirements, thereby enhancing customer satisfaction. It focuses on continuous improvement and risk-based thinking. For a Quality Systems Manager, it serves as a framework to guide and improve the organization's processes and operational efficiency.
Why It's Important
ISO 9001 is important because it provides a structured framework for quality management, ensuring consistent product and service quality, enhancing customer satisfaction, and facilitating continuous improvement, which are crucial for a Quality Systems Manager to uphold and oversee organizational standards.
How to Improve ISO 9001 Skills
Improving ISO 9001 in your organization involves a focused approach on continuous improvement, employee involvement, process optimization, and customer satisfaction. Here’s a concise guide for a Quality Systems Manager:
Conduct a Gap Analysis: Identify areas that require improvement or are not in compliance with ISO 9001 standards. ASQ’s guide on gap analysis can be a good starting point.
Engage Employees: Foster a culture of quality by involving employees in the improvement process. Training and communication are key. The ISO’s page on training can provide insights into effective strategies.
Optimize Processes: Use process mapping and lean methodologies to streamline processes for efficiency and effectiveness. Refer to Lean Enterprise Institute for lean resources.
Implement a Continuous Improvement Process: Adopt methodologies like Plan-Do-Check-Act (PDCA) for ongoing improvement. The ISO 9001 Checklist offers practical advice on implementing PDCA within the ISO framework.
Enhance Customer Satisfaction: Regularly collect and analyze customer feedback to improve products and services. The ISO’s guidelines on enhancing customer satisfaction can guide you in establishing effective feedback mechanisms.
Conduct Internal Audits: Regular internal audits help identify non-conformities and opportunities for improvement. ISO’s auditing page provides insights into conducting effective audits.
Review and Improve the Quality Management System (QMS): Regular management reviews of the QMS ensure it remains effective and aligns with organizational goals. ISO 9000 Store offers guidance on management review processes.
Utilize Quality Management Tools: Tools like Six Sigma, Kaizen, and 5S can help in analyzing and improving processes. The American Society for Quality (ASQ) offers resources on various quality tools.
By systematically implementing these steps and leveraging the provided resources, you can improve your organization’s ISO 9001 quality management system, leading to enhanced quality, efficiency, and customer satisfaction.
How to Display ISO 9001 Skills on Your Resume
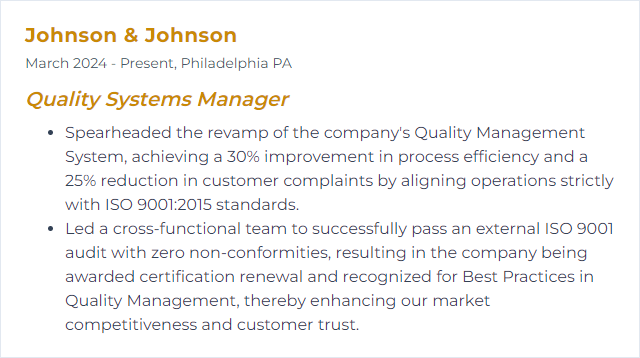
2. Lean Six Sigma
Lean Six Sigma is a methodology that combines the waste reduction principles of Lean with the process improvement and variation reduction focus of Six Sigma to enhance organizational efficiency, quality, and productivity. For a Quality Systems Manager, it serves as a strategic approach to optimizing processes, reducing defects, and ensuring high-quality outputs across the organization.
Why It's Important
Lean Six Sigma is important for a Quality Systems Manager because it provides a proven methodology for reducing waste, improving efficiency, and enhancing the quality of products or services, directly contributing to customer satisfaction and the organization's bottom line.
How to Improve Lean Six Sigma Skills
Improving Lean Six Sigma within an organization, especially from a Quality Systems Manager perspective, involves a focus on continuous improvement, team collaboration, and data-driven decision-making. Here are concise strategies:
Enhance Training: Ensure all team members receive comprehensive Lean Six Sigma training tailored to their roles. This builds a solid foundation of knowledge and skills.
Implement Kaizen: Adopt Kaizen or continuous improvement practices to encourage small, incremental changes that cumulatively lead to significant improvements.
Utilize DMAIC: Emphasize the DMAIC methodology (Define, Measure, Analyze, Improve, Control) for problem-solving and process improvement projects, ensuring a structured approach.
Focus on Customer Value: Align projects with customer needs and expectations, using tools like Voice of the Customer (VOC) to prioritize improvements that enhance customer satisfaction.
Foster a Culture of Collaboration: Encourage cross-functional teamwork and open communication to leverage diverse insights and expertise. This can lead to more innovative solutions and buy-in from stakeholders.
Leverage Technology: Implement Lean Six Sigma software tools that facilitate project management, data analysis, and process mapping to streamline projects and enhance accuracy.
Monitor and Adapt: Regularly review process metrics and project outcomes to identify areas for further improvement. Be open to adapting strategies based on performance data and feedback.
For Quality Systems Managers, integrating these strategies into their Lean Six Sigma initiatives can lead to enhanced process efficiencies, reduced waste, and improved product quality, ultimately driving organizational success.
How to Display Lean Six Sigma Skills on Your Resume
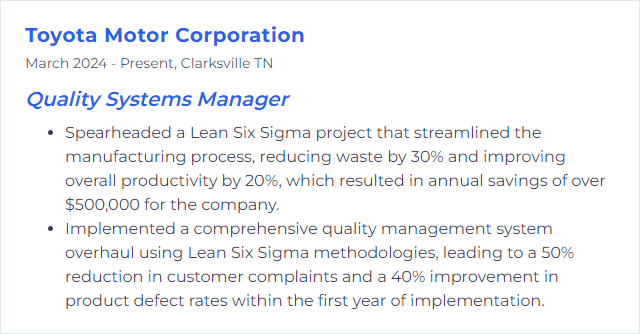
3. CAPA (Corrective and Preventive Action)
CAPA (Corrective and Preventive Action) is a process used within quality management systems to identify and address root causes of non-conformities or defects, aiming to correct them and prevent their recurrence, thereby ensuring continuous improvement in product quality and compliance.
Why It's Important
CAPA is crucial because it systematically identifies, addresses, and prevents the recurrence of quality issues, ensuring product safety and compliance while enhancing customer satisfaction and operational efficiency.
How to Improve CAPA (Corrective and Preventive Action) Skills
Improving CAPA involves a strategic approach focused on identifying root causes, implementing timely solutions, and fostering a culture of quality. Here's a concise guide for a Quality Systems Manager:
Root Cause Analysis: Employ robust techniques like the 5 Whys or Fishbone Diagram to accurately pinpoint the root causes of issues. ASQ Root Cause Analysis
Risk Management: Integrate risk assessment tools like FMEA (Failure Mode and Effects Analysis) to evaluate and prioritize risks, guiding effective preventive actions. ISO 14971
Employee Training: Ensure all team members are trained on CAPA procedures and the importance of quality compliance. Quality Training
Data Analysis: Utilize data analytics to monitor quality indicators and trends, enabling proactive identification of potential issues. Quality Data Analysis
Timeliness and Effectiveness: Set clear timelines for CAPA resolution and regularly review the effectiveness of implemented actions. CAPA Timeliness
Documentation: Maintain comprehensive documentation of CAPA processes, from identification through resolution, ensuring traceability and compliance. ISO 13485
Continuous Improvement: Adopt a culture of continuous improvement through regular CAPA review meetings and leveraging lessons learned for systemic improvements. Continuous Improvement
By systematically addressing these areas, a Quality Systems Manager can enhance the CAPA process, leading to improved product quality and compliance.
How to Display CAPA (Corrective and Preventive Action) Skills on Your Resume
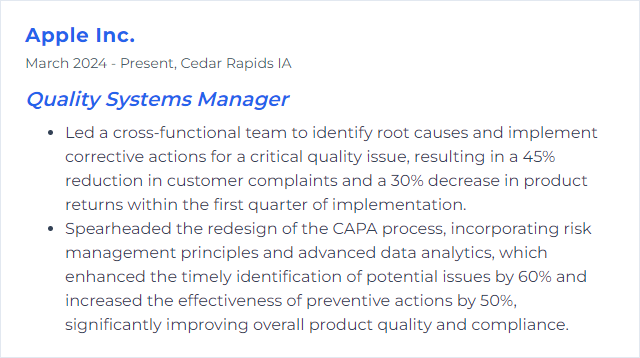
4. Auditing Techniques
Auditing techniques are systematic processes and procedures used by Quality Systems Managers to assess the effectiveness, compliance, and efficiency of an organization's quality management system against defined standards or regulations. These techniques include document reviews, interviews, observations, and sampling to ensure quality objectives are being met and to identify areas for improvement.
Why It's Important
Auditing techniques are crucial for a Quality Systems Manager because they provide a systematic approach to evaluate and improve the effectiveness of quality management systems. This ensures compliance with standards, identifies areas for improvement, and enhances customer satisfaction by maintaining high-quality products and services.
How to Improve Auditing Techniques Skills
Improving auditing techniques involves a continuous process of learning, adaptation, and application of best practices. A Quality Systems Manager can enhance their auditing skills and methodologies by:
Staying Educated: Continuously update your knowledge on the latest standards and regulations relevant to your industry. Websites like ASQ offer resources and training for quality professionals.
Leveraging Technology: Use digital tools and software for audit management and data analysis to increase efficiency and accuracy. Explore options on Capterra for audit software reviews.
Practicing Risk-Based Thinking: Focus on areas with the highest risk to allocate your auditing resources more effectively. The ISO website provides insights into risk-based thinking as per ISO standards.
Enhancing Communication Skills: Effective communication is key during audits. Short courses on platforms like LinkedIn Learning can help improve these skills.
Gathering and Using Feedback: After each audit, gather feedback from the auditees and use it to improve future audits. Continuous improvement forums and platforms like Quality Magazine can offer insights into best practices.
Benchmarking and Networking: Join professional networks or forums, such as The Chartered Quality Institute, to share experiences and learn from peers.
By focusing on these areas, a Quality Systems Manager can significantly enhance their auditing techniques, contributing to more effective quality control and assurance processes.
How to Display Auditing Techniques Skills on Your Resume
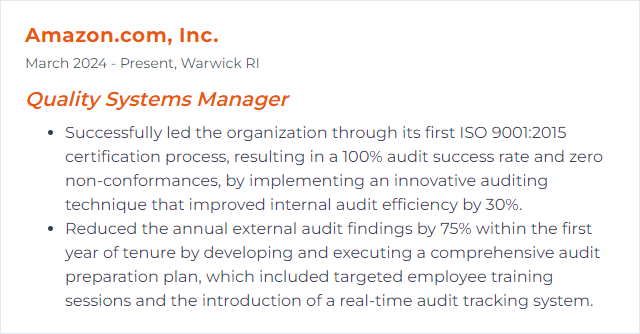
5. Risk Management
Risk management involves identifying, assessing, and prioritizing risks followed by coordinated efforts to minimize, monitor, and control the probability or impact of unfortunate events in an organization's processes and operations, aiming to ensure quality, safety, and compliance.
Why It's Important
Risk management is crucial for a Quality Systems Manager because it helps to identify, assess, and mitigate potential issues that could compromise the quality, compliance, and performance of products or services, ensuring customer satisfaction and regulatory adherence while minimizing costs and protecting the organization's reputation.
How to Improve Risk Management Skills
Improving risk management, especially from the perspective of a Quality Systems Manager, involves a multi-faceted approach focusing on identifying, assessing, and mitigating risks in processes or products. Here's a concise guide:
Risk Identification: Begin by systematically identifying potential risks using tools like SWOT (Strengths, Weaknesses, Opportunities, Threats) analysis or Failure Mode and Effects Analysis (FMEA). ASQ provides a detailed guide on FMEA.
Risk Assessment: Evaluate the identified risks in terms of their severity, occurrence, and detection levels. This helps in prioritizing the risks to manage. The ISO 31000 standard offers a framework for risk assessment and management.
Risk Mitigation: Develop strategies to mitigate the high-priority risks. This could involve redesigning processes, implementing new safety measures, or enhancing quality control procedures. Training and communication are key components in this step.
Continuous Monitoring: Risk management is an ongoing process. Regularly review and update your risk management strategies to adapt to new risks or changes in existing risks. Tools like the Plan-Do-Check-Act (PDCA) cycle can facilitate continuous improvement.
Documentation and Communication: Keep detailed records of all risk management activities and communicate these efforts across the organization to ensure alignment and compliance. The ISO 9001:2015 standard emphasizes the importance of documentation and communication in quality management systems.
Leverage Technology: Consider using risk management software to streamline the process. This can improve accuracy in risk assessment and ensure that risk mitigation efforts are tracked and documented effectively.
By focusing on these key areas, a Quality Systems Manager can significantly improve the risk management process within their organization, ensuring that products and services meet or exceed quality standards while minimizing potential risks.
How to Display Risk Management Skills on Your Resume
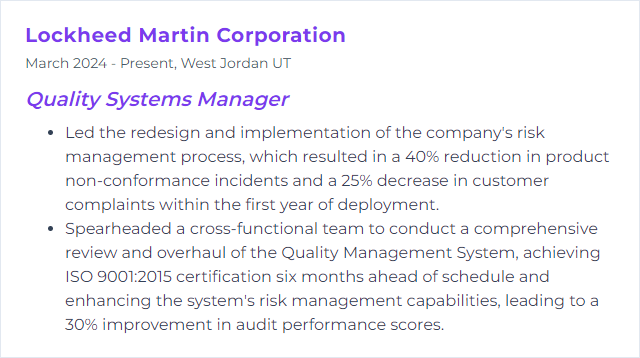
6. SAP Quality Module
The SAP Quality Module, part of SAP's ERP system, is designed for Quality Systems Managers to oversee and manage the quality control processes within an organization. It enables the planning, execution, and tracking of quality testing activities, inspection outcomes, and compliance with regulatory standards, aiming to ensure product excellence and customer satisfaction.
Why It's Important
The SAP Quality Module is crucial for a Quality Systems Manager as it enables systematic monitoring and management of quality in manufacturing processes, ensures compliance with regulatory standards, and facilitates continuous improvement, thereby enhancing product quality and customer satisfaction.
How to Improve SAP Quality Module Skills
Improving the SAP Quality Module involves a strategic approach focusing on customization, integration, training, and continuous improvement. Here’s a concise guide:
Customization: Tailor the SAP Quality Module to fit your specific business processes and quality standards. Utilize SAP’s customization tools to adjust workflows, forms, and reports to meet your unique requirements. SAP Customization Guide.
Integration: Ensure seamless integration with other SAP modules (like Material Management, Production Planning) and external systems (ERP, CRM) for a holistic approach to quality management. This improves data accuracy and decision-making. SAP Integration Guide.
Training: Invest in comprehensive training for your team. This includes not only how to use the SAP Quality Module but also understanding its role in the broader quality management system. SAP offers official training and certification programs. SAP Training and Certification.
Continuous Improvement: Utilize the data and reports generated by the SAP Quality Module to identify areas for improvement. Implement a continuous improvement process (like PDCA - Plan, Do, Check, Act) to enhance quality processes systematically. ASQ Continuous Improvement.
Stay Updated: Keep your SAP Quality Module and related processes up-to-date with the latest SAP releases and quality management trends. Participate in SAP user groups and forums for insights and updates. SAP User Groups.
Leverage SAP Support and Resources: Utilize SAP support and resources for troubleshooting and enhancing module performance. SAP’s support portal offers access to knowledge articles, documentation, and direct assistance. SAP Support Portal.
By focusing on these areas, a Quality Systems Manager can significantly improve the effectiveness and efficiency of the SAP Quality Module, leading to better quality control, compliance, and overall operational excellence.
How to Display SAP Quality Module Skills on Your Resume
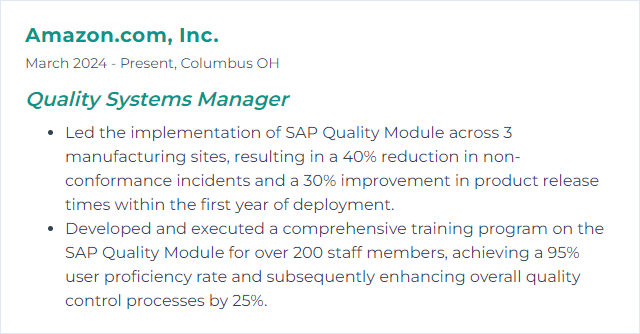
7. Statistical Process Control (SPC)
Statistical Process Control (SPC) is a method used to monitor, control, and ensure the stability of manufacturing processes through statistical analysis, aiming to detect and prevent quality problems by identifying process variations early. It involves using control charts and other tools to analyze process data, enabling Quality Systems Managers to make informed decisions to maintain process consistency and product quality.
Why It's Important
Statistical Process Control (SPC) is crucial for a Quality Systems Manager as it enables the monitoring and control of process variations, ensuring product consistency, quality, and continuous improvement, while reducing waste and costs.
How to Improve Statistical Process Control (SPC) Skills
Improving Statistical Process Control (SPC) involves a series of steps focusing on enhancing data quality, process understanding, and employee engagement. Here's a very short and concise guide tailored for a Quality Systems Manager:
Educate and Train Staff: Ensure all team members understand SPC principles and tools. Offer continuous training sessions. ASQ's training resources can be a good start.
Standardize Data Collection: Implement standardized methods for data collection to ensure accuracy and reliability. NIST's Guidelines on SPC software can help in selecting tools for better data management.
Implement Real-time Monitoring: Use SPC software that allows for real-time monitoring of processes to quickly identify and address issues. SPC Software Comparison by Capterra offers options.
Engage in Continuous Improvement: Adopt a continuous improvement mindset. Use SPC data to identify areas for process improvement. The Deming Institute provides resources on continuous improvement philosophies.
Encourage Employee Involvement: Engage employees in the SPC process by encouraging them to contribute ideas for improvement and participate in problem-solving. Harvard Business Review's article on employee suggestions highlights its importance.
Regularly Review SPC Processes: Periodically review and update your SPC processes to adapt to new challenges or changes in the production environment. ISO 9001 standards can guide the review process.
By focusing on these areas, a Quality Systems Manager can significantly improve the effectiveness of SPC in their organization, leading to higher quality products, improved customer satisfaction, and reduced costs.
How to Display Statistical Process Control (SPC) Skills on Your Resume
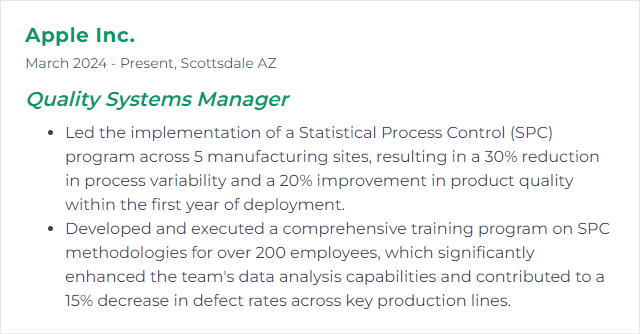
8. Quality Management Systems (QMS)
Quality Management Systems (QMS) are a set of policies, processes, and procedures required for planning and execution in the core business area of an organization. They help ensure that a company can consistently meet customer and regulatory requirements and improve its effectiveness and efficiency on a continuous basis. For a Quality Systems Manager, a QMS provides the framework for monitoring and improving product quality and business processes.
Why It's Important
Quality Management Systems (QMS) are crucial as they provide a structured framework for consistently meeting customer requirements, enhancing satisfaction, and facilitating continuous improvement, ensuring the organization's products and services are of the highest quality. This supports a Quality Systems Manager in effectively monitoring, managing, and improving quality across all operations.
How to Improve Quality Management Systems (QMS) Skills
Improving a Quality Management System (QMS) involves a continuous process of evaluation, feedback, and enhancement to meet and exceed customer expectations and comply with regulatory requirements. Here are concise steps aimed at Quality Systems Managers:
Conduct Gap Analysis: Begin by comparing your current QMS against industry standards (like ISO 9001) to identify areas for improvement. ASQ’s guide offers insights into standards and gap analysis.
Engage Stakeholders: Ensure the involvement of all stakeholders in the QMS improvement process for valuable feedback and buy-in. ISO’s page on quality management principles emphasizes the importance of customer focus and engagement of people.
Implement a Continuous Improvement Process: Adopt methodologies like Plan-Do-Check-Act (PDCA) for systematic improvements. The EPA’s PDCA resource provides a framework for this approach.
Enhance Employee Training: Regularly train employees on quality standards, new technologies, and processes to improve their performance. OSHA’s Training Guidelines offer comprehensive strategies for effective training programs.
Leverage Technology: Utilize QMS software for better document control, process mapping, and data analysis. Capterra’s QMS Software guide helps in selecting the right tool for your organization.
Monitor and Measure Performance: Use Key Performance Indicators (KPIs) to track the effectiveness of your QMS. The Balanced Scorecard Institute provides a strategic approach to setting and monitoring KPIs.
Conduct Internal Audits: Regular audits help identify non-conformities and areas for improvement. ISO’s auditing guidelines can serve as a reference for conducting effective audits.
Review and Improve: Hold regular management review meetings to assess the QMS performance and make necessary adjustments. ISO’s tips on management review can guide you through this process.
By following these steps and leveraging the resources provided, Quality Systems Managers can significantly enhance their organization's Quality Management System, driving continuous improvement and ensuring customer satisfaction.
How to Display Quality Management Systems (QMS) Skills on Your Resume
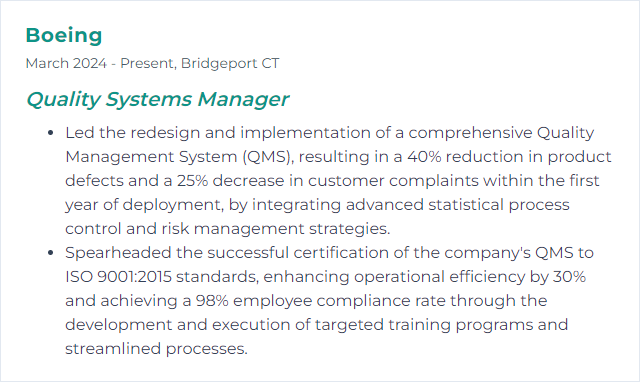
9. FMEA (Failure Mode and Effects Analysis)
FMEA (Failure Mode and Effects Analysis) is a systematic method used to identify, evaluate, and prioritize potential failures in a product, process, or system to mitigate and prevent identified risks, ensuring reliability and quality improvement from a Quality Systems Manager perspective.
Why It's Important
FMEA is important because it proactively identifies potential failures in products or processes, assesses their impact, and prioritizes actions to mitigate risks, ensuring product quality and reliability, and enhancing customer satisfaction.
How to Improve FMEA (Failure Mode and Effects Analysis) Skills
Improving FMEA involves enhancing its effectiveness and efficiency in identifying and addressing potential failures. Here are concise strategies:
Cross-functional Teamwork: Involve a diverse team from various departments (design, manufacturing, quality, customer service) to ensure all potential failure modes are considered. ASQ
Training: Provide comprehensive training on FMEA methodology and tools for the team members to enhance their understanding and efficiency. AIAG Training
Historical Data Analysis: Utilize historical data and lessons learned from past FMEAs to identify common failure modes and their effects, improving the focus and efficiency of the analysis. NI
Software Tools: Adopt specialized FMEA software to streamline the process, facilitate collaboration, and ensure consistency across analyses. FMEA Software
Risk Prioritization: Focus on high-risk items identified by the FMEA for immediate action, using the Risk Priority Number (RPN) to prioritize effectively. Quality-One
Review and Update Regularly: Periodically review and update FMEAs to incorporate changes in design, process, regulations, and feedback from customers and suppliers. SAE International
Integration with Other Quality Tools: Integrate FMEA with other quality management tools (like Control Plans and SPC) for a comprehensive approach to quality improvement. ASQ Integration
By implementing these strategies, a Quality Systems Manager can significantly improve the effectiveness of FMEAs within their organization.
How to Display FMEA (Failure Mode and Effects Analysis) Skills on Your Resume
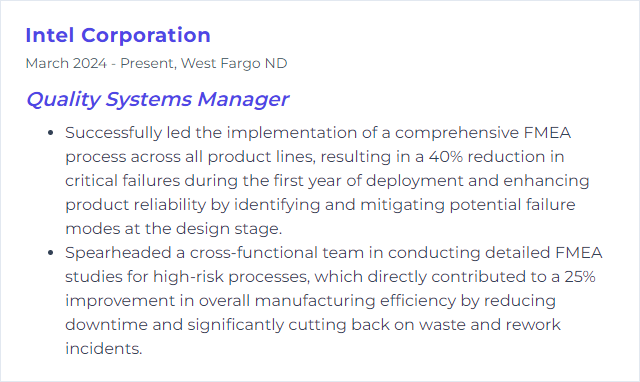
10. GMP (Good Manufacturing Practices)
GMP (Good Manufacturing Practices) refers to a system of guidelines that ensure products are consistently produced and controlled according to quality standards. It covers all aspects of production, from raw materials to finished products, aiming to minimize risks inherent in pharmaceutical and food production that cannot be eliminated through testing the final product. For a Quality Systems Manager, GMP represents the foundation for ensuring product safety, efficacy, and quality, through systematic control and documentation of manufacturing processes and environment.
Why It's Important
GMP ensures products are consistently produced and controlled according to quality standards. It minimizes risks involved in production that cannot be eliminated through testing the final product, safeguarding consumer health and maintaining your company's reputation and legal compliance.
How to Improve GMP (Good Manufacturing Practices) Skills
Improving Good Manufacturing Practices (GMP) involves several key steps focused on compliance, training, and continuous improvement. Here's a concise guide:
Compliance with Regulations: Stay updated with the latest GMP regulations from regulatory bodies like the FDA. Ensure your practices align with these standards.
Employee Training: Regularly train employees on GMP principles, emphasizing the importance of quality and safety. Use engaging training methods to enhance understanding.
Documentation: Maintain detailed and accurate documentation for all processes. This includes SOPs, change controls, and quality checks. Utilize document management systems for better organization and accessibility.
Quality Control and Assurance: Implement robust quality control (QC) and quality assurance (QA) programs. Regularly review and test products and processes to ensure they meet the required standards. ISO 9001 can provide a framework for quality management systems.
Internal Audits: Conduct internal audits regularly to identify areas for improvement. Use the findings to implement corrective actions and prevent recurrence.
Feedback Loops: Establish mechanisms to gather feedback from employees, customers, and audits. Use this feedback to continuously improve GMP practices.
Invest in Technology: Leverage technology to enhance traceability, improve efficiency, and reduce errors. Consider systems like ERP for integrated management of core business processes.
Supplier Management: Ensure your suppliers adhere to GMP standards. Conduct supplier audits and establish quality agreements to maintain a high-quality supply chain.
By focusing on these areas, a Quality Systems Manager can significantly improve GMP within their manufacturing operations. Continuous improvement and adherence to regulatory standards are key to maintaining high quality and safety in manufacturing.
How to Display GMP (Good Manufacturing Practices) Skills on Your Resume
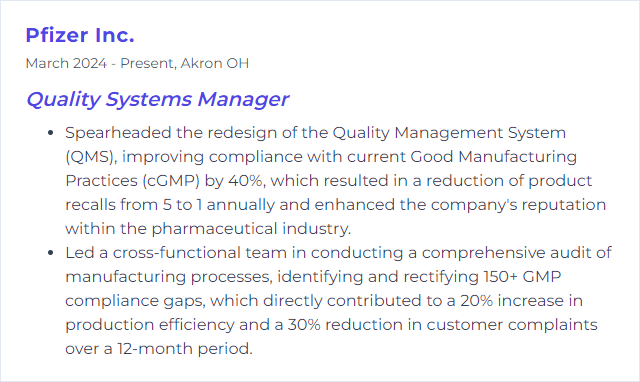
11. Root Cause Analysis
Root Cause Analysis (RCA) is a systematic process used by Quality Systems Managers to identify the underlying reasons for a problem or defect in order to implement solutions that prevent recurrence, ensuring quality and efficiency in operations.
Why It's Important
Root Cause Analysis (RCA) is crucial for a Quality Systems Manager because it enables the identification and resolution of the fundamental issues causing defects or failures, preventing their recurrence, and ensuring the continuous improvement of quality and operational efficiency within the organization.
How to Improve Root Cause Analysis Skills
Improving Root Cause Analysis (RCA) involves enhancing the precision, efficiency, and effectiveness of identifying and addressing the fundamental reasons for problems within an organization's processes or products. Here’s a concise guide tailored for a Quality Systems Manager:
Enhance Team Skills: Train your team in RCA methodologies such as the 5 Whys, Fishbone Diagram, and FMEA (Failure Mode and Effects Analysis). Engage them in RCA training offered by recognized quality organizations like ASQ (American Society for Quality).
Leverage Data Analytics: Utilize data analytics tools to gather and analyze data related to defects or failures. Tools like Minitab can assist in identifying patterns and root causes more efficiently.
Implement Cross-functional Teams: Foster collaboration among departments by forming cross-functional teams. This brings diverse perspectives and expertise to the RCA process, enhancing the identification and resolution of root causes.
Standardize RCA Processes: Develop and standardize RCA procedures to ensure consistency and completeness in how root causes are identified and addressed. The ISO 9001 Quality Management System can serve as a guideline for standardization.
Use RCA Software Tools: Adopt RCA software tools that facilitate a systematic approach to identifying, analyzing, and solving problems. Tools like Cause Mapping can simplify complex issues into more manageable components.
Monitor and Follow-up: Establish a system for monitoring the implementation of corrective actions and their effectiveness over time. Continuous follow-up ensures that the root cause has been adequately addressed and prevents recurrence.
Foster a Culture of Continuous Improvement: Encourage an organizational culture that views mistakes as learning opportunities. Tools like Kaizen can promote continuous improvement and proactive root cause analysis.
Review and Learn: Regularly review the outcomes of RCA processes to learn from successes and failures. This ongoing review process can lead to improvements in how future RCAs are conducted.
Improving RCA within an organization is a continuous process that requires commitment, the right tools, and a culture that values quality and continuous improvement.
How to Display Root Cause Analysis Skills on Your Resume
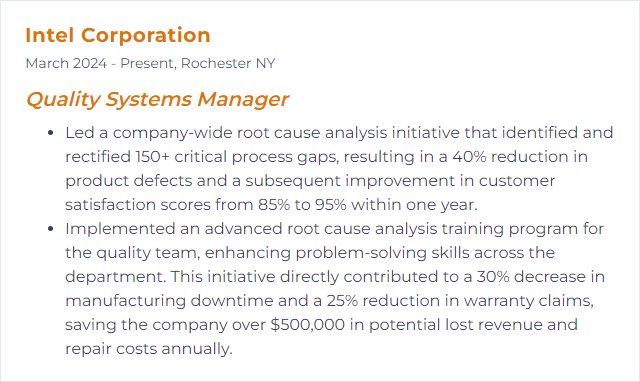
12. Continuous Improvement
Continuous improvement, in the context of a Quality Systems Manager, refers to the ongoing effort to enhance products, services, or processes through incremental and breakthrough improvements, aiming to boost quality, efficiency, and customer satisfaction.
Why It's Important
Continuous Improvement is crucial for a Quality Systems Manager as it ensures ongoing enhancement of processes, products, and services, leading to increased efficiency, reduced waste, and higher customer satisfaction, thereby maintaining competitive advantage and compliance with quality standards.
How to Improve Continuous Improvement Skills
To improve Continuous Improvement as a Quality Systems Manager, focus on the following strategies:
Engage Your Team: Foster a culture of continuous improvement by encouraging team participation and feedback. Empower employees to identify areas for improvement and suggest solutions. Harvard Business Review discusses strategies for engaging your team.
Implement Lean Six Sigma: Use Lean Six Sigma methodologies to identify and eliminate waste and defects. This approach combines lean manufacturing/lean enterprise and Six Sigma to improve quality and efficiency. The American Society for Quality (ASQ) provides resources on implementing these practices.
Adopt Agile Practices: Agile methodologies can enhance your continuous improvement process by promoting adaptability and quick responses to change. Scrum.org offers insights into adopting agile practices.
Utilize Technology: Invest in quality management software that enables tracking, management, and analysis of quality metrics. This technology can streamline processes and provide actionable insights. Capterra lists various quality management software options.
Continuous Learning and Training: Provide ongoing training and development opportunities for your team. Staying informed on the latest quality management trends and techniques is crucial. Coursera and edX offer courses on quality management.
Set Clear, Measurable Goals: Establish specific, measurable, achievable, relevant, and time-bound (SMART) goals for your continuous improvement efforts. This clarity helps in tracking progress and identifying areas for further improvement. MindTools explains how to set SMART goals.
By focusing on these strategies and leveraging the resources provided, you can significantly enhance your continuous improvement process and drive greater efficiencies and quality within your organization.
How to Display Continuous Improvement Skills on Your Resume
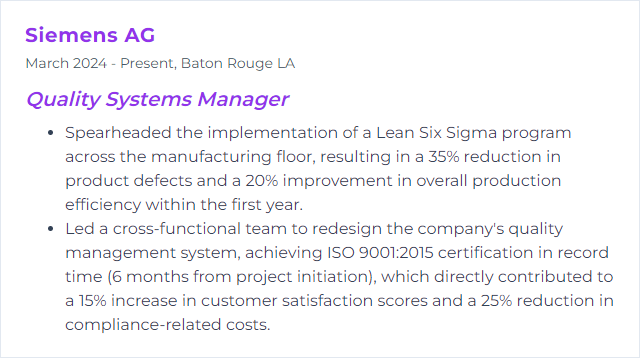