Top 12 Quality Supervisor Skills to Put on Your Resume
Crafting an impressive resume is crucial for landing a position as a Quality Supervisor, and highlighting your top skills is key to standing out. In this guide, we'll explore the top 12 skills that demonstrate your expertise and commitment to ensuring product excellence and operational efficiency, making you an invaluable asset to any team.
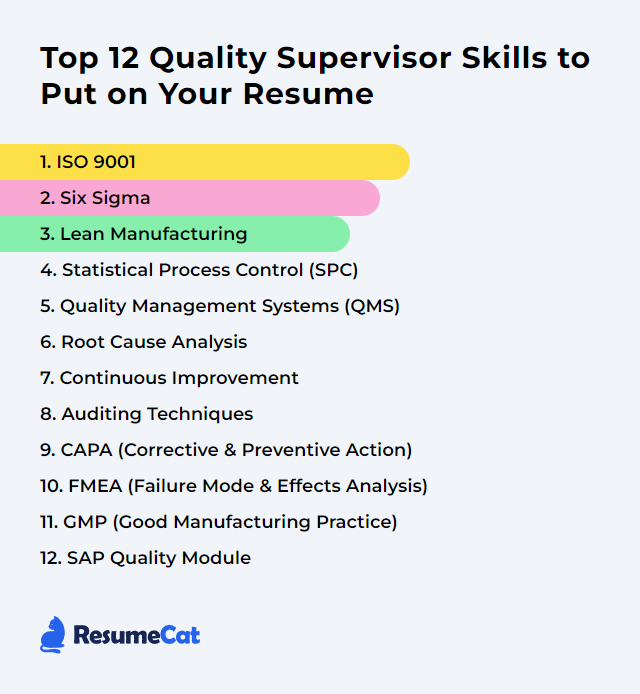
Quality Supervisor Skills
- ISO 9001
- Six Sigma
- Lean Manufacturing
- Statistical Process Control (SPC)
- Quality Management Systems (QMS)
- Root Cause Analysis
- Continuous Improvement
- Auditing Techniques
- CAPA (Corrective and Preventive Action)
- FMEA (Failure Mode and Effects Analysis)
- GMP (Good Manufacturing Practice)
- SAP Quality Module
1. ISO 9001
ISO 9001 is an international standard that specifies requirements for a quality management system (QMS), helping organizations ensure they consistently provide products and services that meet customer and regulatory requirements, aiming for continuous improvement. For a Quality Supervisor, it guides in establishing, implementing, and improving quality processes to enhance customer satisfaction and operational efficiency.
Why It's Important
ISO 9001 is important because it ensures consistent quality in products and services, enhances customer satisfaction, and provides a framework for continuous improvement, directly supporting a Quality Supervisor's goals of maintaining and improving quality standards within an organization.
How to Improve ISO 9001 Skills
Improving ISO 9001 involves a continuous effort to enhance your Quality Management System (QMS). As a Quality Supervisor, focus on these key areas:
Engage Top Management: Ensure top management's commitment to the QMS. Their leadership is crucial for fostering a quality culture throughout the organization. Leadership Commitment.
Employee Involvement: Increase employee involvement by providing training, encouraging feedback, and recognizing their contributions to quality improvements. Employee Involvement.
Process Approach: Streamline processes to enhance efficiency and effectiveness. Utilize process mapping and performance metrics to identify areas for improvement. Process Approach.
Risk Management: Implement a proactive approach to risk management, identifying potential risks and opportunities for improvement. Risk Management.
Customer Focus: Regularly gather and analyze customer feedback to meet and exceed customer expectations. Customer Focus.
Continuous Improvement: Foster a culture of continuous improvement through regular audits, management reviews, and the implementation of corrective actions. Continuous Improvement.
Utilize Technology: Leverage technology to automate and optimize quality management processes. Digital Transformation.
Training and Development: Invest in training and development to enhance the competencies of employees related to quality management. Training and Development.
By focusing on these areas, you can enhance your organization's QMS, driving improvements in quality, efficiency, and customer satisfaction.
How to Display ISO 9001 Skills on Your Resume
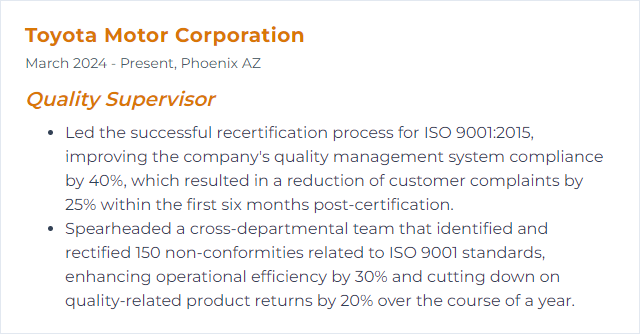
2. Six Sigma
Six Sigma is a data-driven, quality improvement methodology aimed at reducing defects and improving processes to enhance product quality and customer satisfaction.
Why It's Important
Six Sigma is important for a Quality Supervisor as it provides a systematic and data-driven methodology to improve process quality, reduce defects, and increase efficiency, directly contributing to higher customer satisfaction and cost reduction.
How to Improve Six Sigma Skills
Improving Six Sigma as a Quality Supervisor involves a continuous cycle of measuring, analyzing, and refining processes to enhance efficiency and reduce defects. Here’s a very short and concise guide to enhancing your Six Sigma practices:
Educate and Train: Ensure your team and related stakeholders are well-trained in Six Sigma methodologies. Offer or seek regular training sessions to keep everyone updated. ASQ Training Resources
Implement DMAIC Rigorously: Follow the Define, Measure, Analyze, Improve, Control (DMAIC) framework strictly to identify and solve process inefficiencies. iSixSigma DMAIC Overview
Utilize Data Effectively: Make data-driven decisions by collecting and analyzing relevant data meticulously. Embrace statistical tools and software for accuracy. Minitab Statistical Software
Promote a Quality Culture: Foster an organizational culture that values continuous improvement and quality. Encourage open communication and feedback. Lean Enterprise Institute on Culture
Leverage Technology: Adopt the latest technology and tools that can streamline Six Sigma processes, from project management software to advanced analytics tools. Smartsheet for Project Management
Benchmark and Network: Learn from best practices in your industry by benchmarking and networking with other professionals. Attend conferences and join professional forums. ASQ Conferences
Review and Adapt: Regularly review Six Sigma processes and outcomes. Be prepared to adapt strategies based on performance data and changing business environments. Harvard Business Review on Strategy
By focusing on these areas, you can enhance your Six Sigma implementation, driving significant improvements in quality and efficiency.
How to Display Six Sigma Skills on Your Resume
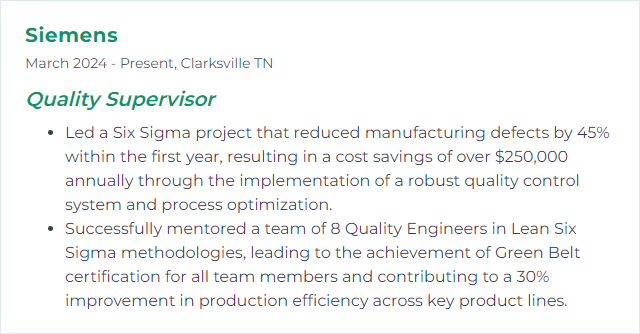
3. Lean Manufacturing
Lean Manufacturing is a systematic approach aimed at minimizing waste within manufacturing systems while simultaneously maximizing productivity. For a Quality Supervisor, it involves focusing on improving product quality, reducing defects, and ensuring efficient processes to enhance customer satisfaction and operational efficiency.
Why It's Important
Lean Manufacturing is important because it aims to reduce waste and inefficiencies, ensuring optimal use of resources. For a Quality Supervisor, it enhances product quality, improves productivity, and ensures consistent delivery of high-quality products to meet customer satisfaction.
How to Improve Lean Manufacturing Skills
Improving Lean Manufacturing, especially from a Quality Supervisor's perspective, involves a focus on continuous improvement, waste reduction, and process optimization. Here are concise strategies:
Implement Continuous Improvement (Kaizen): Encourage and facilitate continuous small improvements in every aspect of the manufacturing process. Kaizen Institute
Adopt 5S Methodology: Ensure a clean, organized, and efficient workspace to improve productivity and quality. Lean Enterprise Institute
Utilize Value Stream Mapping: Identify and eliminate waste in the manufacturing process by analyzing the flow of materials and information. ASQ - Value Stream Mapping
Apply Six Sigma Principles: Use Six Sigma tools to reduce process variations and improve product quality. iSixSigma - Six Sigma Tools
Engage Employees in Problem Solving: Foster a culture where every employee feels responsible for quality and is empowered to identify and solve problems. Lean Manufacturing Tools
Standardize Work Processes: Develop and document best practices to ensure consistency and efficiency in all operations. Lean Production
Focus on Customer Feedback: Regularly gather and analyze customer feedback to align the manufacturing processes with customer requirements. Harvard Business Review - Customer Feedback
Invest in Employee Training: Continuously train employees on Lean principles, quality standards, and new technologies. MIT Sloan - Lean Courses
Implementing these strategies requires a commitment to change and a focus on long-term improvement rather than short-term gains.
How to Display Lean Manufacturing Skills on Your Resume
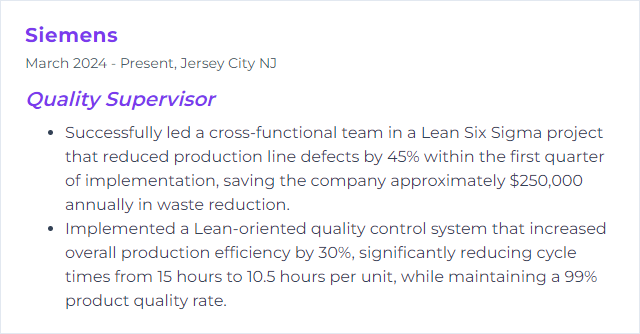
4. Statistical Process Control (SPC)
Statistical Process Control (SPC) is a method used by quality supervisors to monitor and control a process using statistical techniques to ensure it operates at its full potential, producing consistent, conforming products with minimal waste.
Why It's Important
Statistical Process Control (SPC) is crucial for a Quality Supervisor because it provides a data-driven approach to monitoring, controlling, and improving manufacturing processes, ensuring product quality and consistency while minimizing waste and defects.
How to Improve Statistical Process Control (SPC) Skills
Improving Statistical Process Control (SPC) as a Quality Supervisor involves several focused strategies. These include:
Education and Training: Ensure all team members understand SPC principles and tools. Online courses or webinars can be beneficial (ASQ Courses).
Data Accuracy: Implement rigorous data collection methodologies to ensure accuracy and reliability. Use software that minimizes human error.
Real-Time Monitoring: Utilize SPC software that offers real-time monitoring and analysis capabilities, enabling immediate corrective actions (InfinityQS).
Continuous Improvement: Adopt a culture of continuous improvement, using SPC data to identify areas for process enhancements.
Employee Involvement: Engage employees at all levels in SPC activities to foster a sense of ownership and accountability.
Customize SPC Tools: Customize SPC tools and charts to fit the specific needs of your processes and products.
Supplier Quality Management: Extend SPC practices to your suppliers to ensure quality inputs (Supplier Quality Management Strategies).
Regular Audits: Conduct regular SPC system audits to ensure adherence to standards and identify improvement opportunities.
By focusing on these areas, Quality Supervisors can significantly enhance the effectiveness of their SPC initiatives, leading to improved product quality and process efficiency.
How to Display Statistical Process Control (SPC) Skills on Your Resume
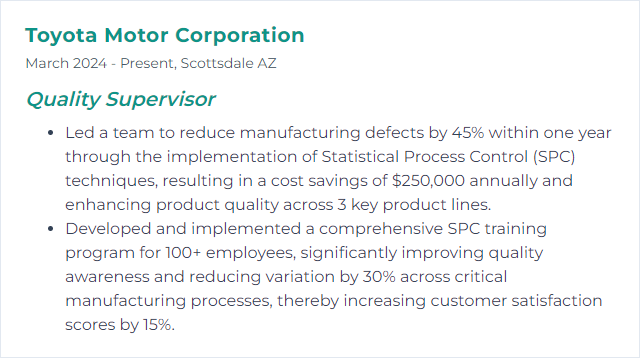
5. Quality Management Systems (QMS)
Quality Management Systems (QMS) are structured frameworks that coordinate and direct an organization's processes, procedures, and responsibilities to meet customer requirements and enhance its effectiveness and efficiency on a continuous basis. For a Quality Supervisor, QMS is a vital tool to ensure product/service quality, compliance, and continuous improvement.
Why It's Important
Quality Management Systems (QMS) are crucial as they provide a structured framework for consistently meeting customer requirements, enhancing satisfaction, and continuously improving operational efficiency, directly impacting a Quality Supervisor's ability to ensure product/service quality and compliance.
How to Improve Quality Management Systems (QMS) Skills
Improving Quality Management Systems (QMS) involves a focused approach on continuous improvement, effective communication, and leveraging technology. Here's a concise guide tailored for a Quality Supervisor:
Assess and Analyze Current QMS: Conduct thorough audits and SWOT analyses to identify areas of improvement. Utilize tools like ISO 9001:2015 for guidance on standards.
Engage and Train Your Team: Ensure your team is well-informed and trained on quality standards and their importance. Resources like ASQ’s Training Courses can be invaluable.
Implement Technology: Adopt QMS software solutions that streamline processes and enhance compliance. Consider platforms like Intelex for integrated management systems.
Continuous Improvement: Embrace methodologies like Kaizen for ongoing improvement. Encourage feedback and innovation within your team.
Effective Communication: Establish clear communication channels and regular meetings to discuss quality objectives and QMS performance. Tools like Slack can facilitate team communication.
Customer Focus: Regularly gather and analyze customer feedback to align your QMS with customer expectations. Tools like SurveyMonkey can help in collecting feedback.
Document Control: Ensure all QMS documentation is up-to-date and accessible. Solutions like DocuWare can help manage documents efficiently.
Regular Audits and Reviews: Schedule regular QMS audits and management reviews to ensure compliance and identify areas for improvement. Guidance on audits can be found through ISO’s Audit Guidelines.
Supplier Management: Ensure your suppliers meet quality standards. Tools like SupplierSelect can assist in managing supplier evaluations.
Set Clear Objectives and KPIs: Define clear, measurable objectives and key performance indicators (KPIs) to track progress. Resources like KPI.org can guide you in setting effective KPIs.
Improving a QMS is an ongoing process that requires commitment, adaptability, and a customer-focused approach. By following these steps, a Quality Supervisor can enhance their QMS, leading to better quality products/services and increased customer satisfaction.
How to Display Quality Management Systems (QMS) Skills on Your Resume
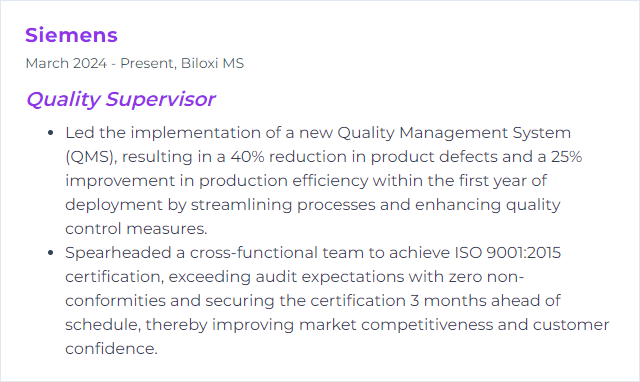
6. Root Cause Analysis
Root Cause Analysis (RCA) is a systematic process used by Quality Supervisors to identify the underlying reasons for defects or problems in a product or process, aiming to implement long-term solutions that prevent recurrence.
Why It's Important
Root Cause Analysis (RCA) is crucial for a Quality Supervisor because it systematically identifies the underlying reasons for problems, allowing for the implementation of effective solutions that prevent recurrence, enhance product quality, and ensure customer satisfaction.
How to Improve Root Cause Analysis Skills
Improving Root Cause Analysis (RCA) involves a systematic approach to identify the underlying problems that lead to issues within an organization. For a Quality Supervisor, enhancing RCA skills can directly impact the quality and efficiency of operations. Here are concise steps to improve RCA:
Define the Problem Clearly: Start by precisely defining the issue, including its symptoms and impact. Use tools like the 5 Whys technique to drill down to the root cause.
Collect Data: Gather comprehensive data related to the problem. This could include production data, process maps, or employee feedback. Tools like Fishbone Diagrams can help organize causes and their effects.
Analyze Data: Utilize analytical tools and techniques to examine the collected data. Techniques like Pareto Analysis can help prioritize issues based on their impact.
Identify Potential Root Causes: Leverage the collected data and analysis to identify potential root causes. Keep an open mind and consider all possibilities.
Verify Root Causes: Test the identified root causes to confirm their validity. This could involve experiments, simulations, or further data analysis.
Implement Corrective Actions: Once the root causes are verified, develop and implement corrective actions to address them. Ensure actions are feasible and sustainable.
Evaluate Effectiveness: After implementation, monitor the situation to ensure the corrective actions have resolved the problem. Use Key Performance Indicators (KPIs) to measure success.
Document and Share Findings: Document the entire RCA process and share the findings with relevant stakeholders. This promotes organizational learning and prevents future occurrences.
For further learning and professional guidance, consider resources and courses offered by reputable organizations such as the American Society for Quality (ASQ) and the Institute of Quality Assurance (IQA).
By following these steps and continuously enhancing your RCA skills, you can significantly improve problem-solving efficacy, leading to higher quality outcomes and operational efficiency.
How to Display Root Cause Analysis Skills on Your Resume
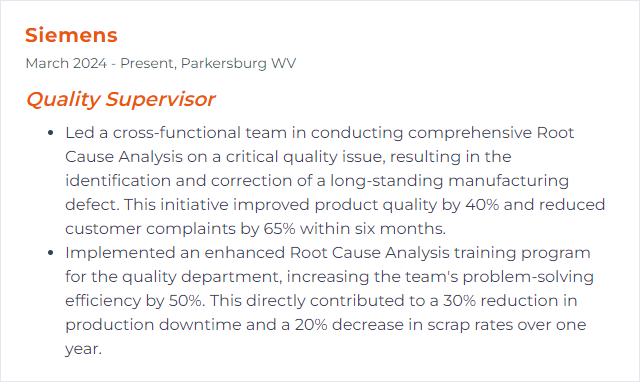
7. Continuous Improvement
Continuous Improvement, in the context of a Quality Supervisor, is an ongoing effort to enhance products, services, or processes through incremental improvements or breakthrough innovations, aiming to elevate quality standards and operational efficiency.
Why It's Important
Continuous improvement is crucial for a Quality Supervisor as it ensures ongoing enhancement of processes, products, and services, leading to increased efficiency, reduced waste, and higher customer satisfaction, ultimately fostering a competitive edge and sustainable success.
How to Improve Continuous Improvement Skills
Improving Continuous Improvement as a Quality Supervisor involves a strategic and engaged approach. Here are concise steps to enhance your continuous improvement processes:
Educate and Train: Continuously educate yourself and your team on lean management and Six Sigma methodologies. Keeping skills up to date is crucial.
Set Clear Objectives: Establish SMART goals (Specific, Measurable, Achievable, Relevant, Time-bound) that align with your company's mission and quality objectives.
Engage Your Team: Promote a culture of continuous improvement by encouraging team involvement. Use techniques like Kaizen to foster team collaboration and engagement.
Implement KPIs: Define and monitor Key Performance Indicators (KPIs) to measure progress and identify areas for improvement.
Utilize Technology: Leverage quality management software to streamline processes, improve data accuracy, and facilitate communication.
Review and Adapt: Regularly review processes and outcomes, using tools like PDCA (Plan-Do-Check-Act) cycles for systematic evaluation and improvement.
Solicit Feedback: Encourage and act on feedback from both customers and employees to uncover insights and opportunities for improvement.
Benchmark and Learn: Compare your processes and performance against industry leaders. Resources like the American Society for Quality (ASQ) can provide valuable benchmarks and learning opportunities.
By strategically applying these steps, you can enhance your continuous improvement efforts, driving quality and efficiency improvements throughout your organization.
How to Display Continuous Improvement Skills on Your Resume
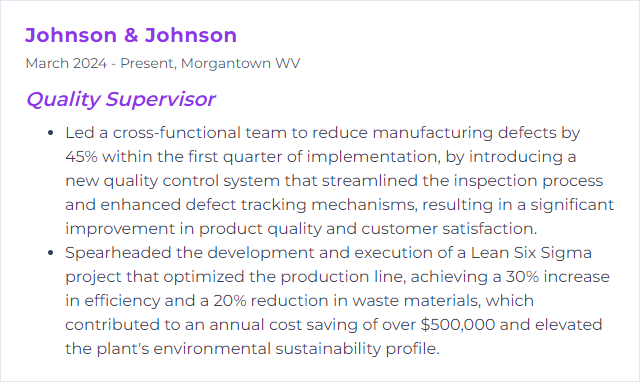
8. Auditing Techniques
Auditing techniques are systematic methods and procedures used by Quality Supervisors to assess and evaluate the effectiveness, compliance, and performance of quality management systems within an organization. These techniques include document reviews, process inspections, interviews, and data analysis to ensure standards and regulations are met.
Why It's Important
Auditing techniques are crucial for a Quality Supervisor because they ensure that the company's processes, products, and systems meet established quality standards, identify areas for improvement, and help maintain compliance with regulatory requirements. This, in turn, enhances customer satisfaction and protects the company's reputation.
How to Improve Auditing Techniques Skills
Improving auditing techniques, especially for a Quality Supervisor, involves a focused approach to enhance accuracy, efficiency, and effectiveness in audit processes. Here’s a concise guide:
Stay Updated with Standards: Regularly review and update your knowledge on the latest ISO standards and industry practices to ensure compliance.
Leverage Technology: Utilize audit management software to streamline audit scheduling, data collection, and report generation for better efficiency.
Enhance Communication Skills: Effective communication is crucial. Training in this area can improve auditor interactions with auditees, making the process smoother and more productive.
Continuous Learning: Engage in professional development courses focused on auditing techniques and quality management to stay ahead of industry trends and methodologies.
Risk-Based Auditing Approach: Implement a risk-based approach to focus efforts on high-risk areas, enhancing the effectiveness of the audits.
Benchmarking and Peer Review: Regularly participate in benchmarking studies and peer reviews to compare auditing practices and learn from best practices within the industry.
By focusing on these areas, a Quality Supervisor can significantly enhance their auditing techniques, contributing to more effective quality management and compliance within their organization.
How to Display Auditing Techniques Skills on Your Resume
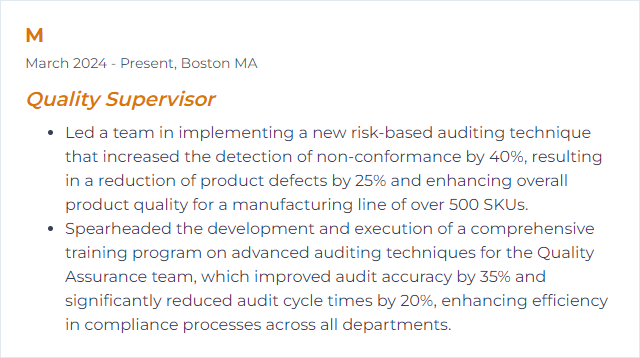
9. CAPA (Corrective and Preventive Action)
CAPA (Corrective and Preventive Action) is a process used by a Quality Supervisor to identify, investigate, and eliminate the causes of detected non-conformities or potential issues in the production or service delivery processes, aiming to prevent their recurrence or occurrence. It involves corrective actions to address current problems and preventive actions to mitigate future risks.
Why It's Important
CAPA is crucial as it identifies and addresses root causes of issues in processes or products, preventing recurrence, ensuring compliance, and maintaining high-quality standards, essential for a Quality Supervisor's goal of continuous improvement and customer satisfaction.
How to Improve CAPA (Corrective and Preventive Action) Skills
Improving CAPA involves a focused, systematic approach ensuring timely and effective resolution of quality issues. Here are concise steps for a Quality Supervisor:
Clearly Define the Problem: Use tools like 5 Whys or Fishbone Diagrams to identify root causes.
Develop an Action Plan: Prioritize actions based on risk and impact. Incorporate SMART goals to ensure each action is specific, measurable, achievable, relevant, and time-bound.
Implement Actions: Assign responsibilities clearly. Use project management tools like Trello or Asana for tracking.
Training and Communication: Train relevant teams on changes. Effective communication tools include Slack for real-time updates.
Monitor and Review: Set up Key Performance Indicators (KPIs) to measure success. Regular reviews help in assessing the effectiveness of the implemented actions.
Document Everything: Use a Document Management System (DMS) for tracking changes, actions, and outcomes for future reference and audits.
Foster a Culture of Continuous Improvement: Encourage feedback and ongoing improvement using platforms like SurveyMonkey for collecting insights.
Implementing these steps systematically can significantly improve the effectiveness of CAPA processes within an organization.
How to Display CAPA (Corrective and Preventive Action) Skills on Your Resume
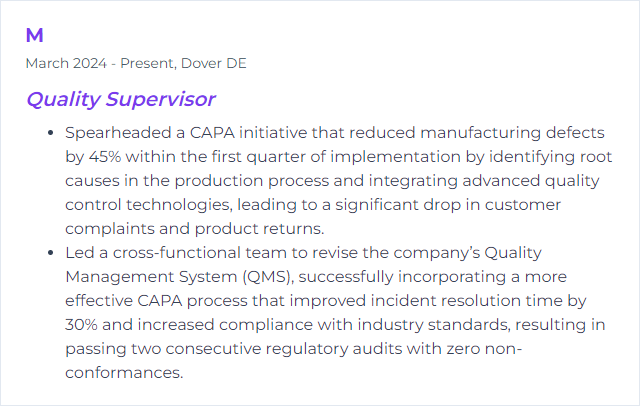
10. FMEA (Failure Mode and Effects Analysis)
FMEA (Failure Mode and Effects Analysis) is a systematic, proactive method for identifying and evaluating potential failure modes and their causes within a product or process, to prioritize and mitigate risks, enhancing reliability and quality.
Why It's Important
FMEA is crucial for a Quality Supervisor because it systematically identifies and evaluates potential failure modes in a product or process, prioritizing risk reduction actions to enhance reliability and safety, thus ensuring high-quality outcomes and customer satisfaction.
How to Improve FMEA (Failure Mode and Effects Analysis) Skills
Improving FMEA involves enhancing its effectiveness and efficiency in identifying and mitigating risks. Here are concise strategies tailored for a Quality Supervisor:
Educate and Train: Ensure all team members are well-trained on FMEA methodology. Use resources like ASQ's FMEA Training to enhance team knowledge.
Cross-Functional Teams: Include members from different departments (design, manufacturing, quality, etc.) to bring diverse perspectives. This collaborative approach can be supported by guidelines from ISO 31000 on risk management.
Prioritize Risks: Use the RPN (Risk Priority Number) to prioritize risks effectively, focusing on high-impact areas first. AIAG & VDA FMEA Handbook offers a standardized approach to calculating and prioritizing RPN.
Leverage Software Tools: Utilize FMEA software tools for better data management and analysis. Tools like IQ-FMEA can streamline the process.
Review and Update Regularly: FMEAs should be living documents. Regular reviews and updates as per ISO 9001:2015 ensure they remain relevant and effective over time.
Benchmark and Learn: Learn from industry best practices and benchmarks. Engaging in forums like Elsmar Cove can provide insights into how others are successfully implementing FMEA.
Integrate with Other Systems: Ensure FMEA is not siloed; integrate it with other quality and risk management systems within the organization. Guidelines on integration can be found in ISO 9001 and ISO 31000.
By focusing on these areas, a Quality Supervisor can significantly improve the effectiveness of FMEA processes in their organization.
How to Display FMEA (Failure Mode and Effects Analysis) Skills on Your Resume
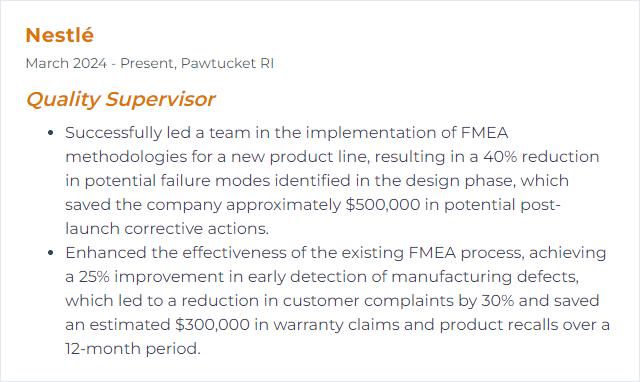
11. GMP (Good Manufacturing Practice)
GMP (Good Manufacturing Practice) is a system for ensuring that products are consistently produced and controlled according to quality standards. It is designed to minimize the risks involved in any pharmaceutical production that cannot be eliminated through testing the final product. For a Quality Supervisor, it involves overseeing the adherence to these standards and protocols to ensure product safety and efficacy.
Why It's Important
GMP ensures products are consistently produced and controlled to quality standards, minimizing risks involved in production that cannot be eliminated through testing the final product. This is crucial for a Quality Supervisor because it provides a framework for meeting regulatory requirements and safeguarding consumer health by ensuring product safety, quality, and efficacy.
How to Improve GMP (Good Manufacturing Practice) Skills
Improving Good Manufacturing Practice (GMP) involves a proactive approach to ensuring products are consistently produced and controlled according to quality standards. Here are key strategies for a Quality Supervisor:
Training and Awareness: Ensure all employees are regularly trained on GMP standards relevant to their roles. Emphasize the importance of compliance and its impact on product quality and safety. FDA Training Courses.
Documentation Improvement: Maintain clear, detailed, and up-to-date documentation for all processes. This includes SOPs, change controls, and batch records. Implement a review system for continuous improvement. WHO Good Documentation Practices.
Regular Audits and Inspections: Conduct internal audits regularly to ensure compliance with GMP standards. Use audit findings to address non-conformities and implement corrective actions promptly. ISO 19011:2018 Guidelines for Auditing.
Quality Control Systems: Strengthen quality control systems by implementing robust testing and validation methodologies. Ensure equipment is calibrated and maintained according to manufacturer specifications. ICH Quality Guidelines.
Vendor Management: Qualify suppliers and vendors through thorough evaluation processes. Regularly assess their compliance with GMP standards to ensure raw materials and components meet required quality specifications. ECA Academy Vendor Qualification.
Continuous Improvement: Foster a culture of continuous improvement through feedback mechanisms, quality circles, and employee engagement in problem-solving. Utilize tools like Six Sigma and PDCA (Plan-Do-Check-Act) for process optimization. ASQ Quality Resources.
By focusing on these areas, a Quality Supervisor can significantly improve GMP compliance, thereby enhancing product quality, safety, and regulatory compliance.
How to Display GMP (Good Manufacturing Practice) Skills on Your Resume
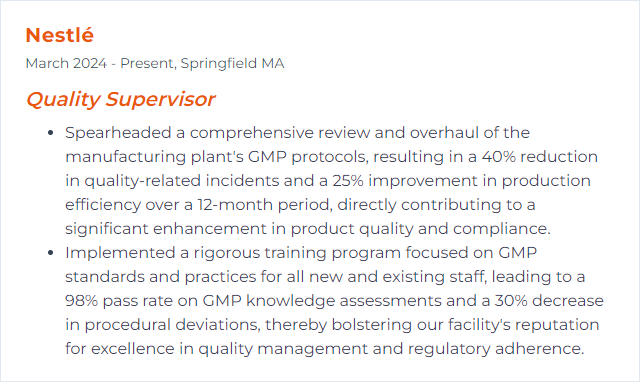
12. SAP Quality Module
The SAP Quality Management (QM) module is a component of the SAP ERP system that focuses on quality assurance and control in manufacturing and logistics. It helps Quality Supervisors oversee all aspects of quality in processes, including planning, inspection, certification, notification, and control, ensuring product compliance and meeting customer requirements efficiently.
Why It's Important
The SAP Quality Module is crucial for a Quality Supervisor as it streamlines quality management processes, ensuring product compliance and consistency. It facilitates efficient defect tracking, quality control, and compliance with industry standards, enhancing product reliability and customer satisfaction.
How to Improve SAP Quality Module Skills
Improving the SAP Quality Management (QM) module involves enhancing its utilization, integrating it with other modules effectively, and leveraging its full potential to streamline quality processes. Here are concise steps for a Quality Supervisor looking to improve the SAP QM module:
Understand SAP QM Capabilities: Begin with a thorough understanding of all features and functionalities within the SAP QM module. SAP's official documentation is a great starting point.
Customize to Fit Your Needs: Tailor the SAP QM module to meet your specific business requirements. This includes customizing inspection methods, quality certificates, and audit management. SAP offers guidance on customization.
Integrate with Other Modules: Ensure seamless integration with other relevant SAP modules like Material Management (MM), Production Planning (PP), and Sales and Distribution (SD) for a holistic approach to quality management. SAP provides insights on module integration points.
Leverage Data Analytics: Utilize SAP's advanced analytics to gain insights into quality performance, identify trends, and make informed decisions. SAP Analytics Cloud (SAC) can enhance your data analysis capabilities.
Train Your Team: Invest in comprehensive training for your team to ensure they are proficient in using SAP QM. SAP offers training and certification programs to upskill your workforce.
Implement Continuous Improvement: Adopt a continuous improvement mindset. Utilize the insights and data gathered from SAP QM to constantly refine and enhance your quality processes.
Stay Updated: Keep abreast of the latest updates and enhancements from SAP for the QM module. Regularly visit the SAP News Center for updates and new features.
Improving the SAP Quality Management module is an ongoing process that involves customization, integration, effective use of analytics, continuous learning, and adapting to new functionalities and updates.
How to Display SAP Quality Module Skills on Your Resume
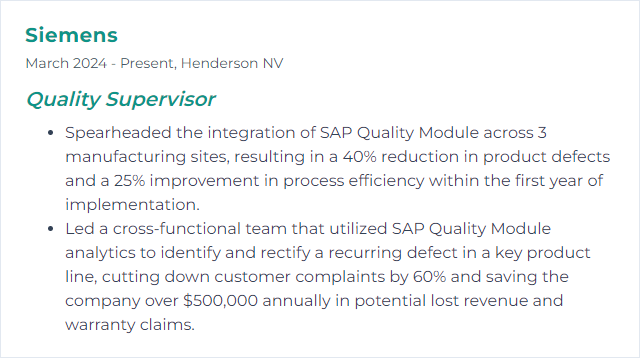