Top 12 Quality Inspector Skills to Put on Your Resume
In today's competitive job market, standing out as a quality inspector requires showcasing a unique set of skills on your resume. Mastering and highlighting these top skills can significantly enhance your appeal to employers, demonstrating your capability to ensure the highest standards of quality in products and processes.
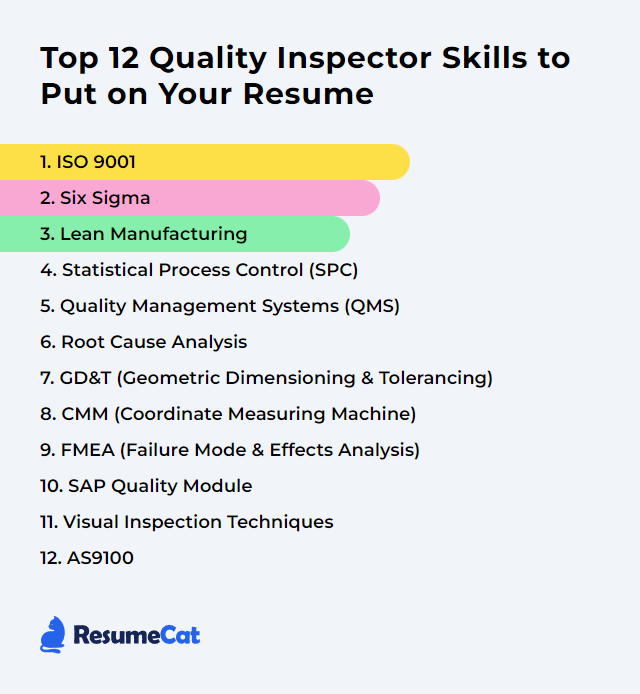
Quality Inspector Skills
- ISO 9001
- Six Sigma
- Lean Manufacturing
- Statistical Process Control (SPC)
- Quality Management Systems (QMS)
- Root Cause Analysis
- GD&T (Geometric Dimensioning and Tolerancing)
- CMM (Coordinate Measuring Machine)
- FMEA (Failure Mode and Effects Analysis)
- SAP Quality Module
- Visual Inspection Techniques
- AS9100
1. ISO 9001
ISO 9001 is an international standard that specifies requirements for a quality management system (QMS). For a Quality Inspector, it guides the principles and practices for ensuring product and service quality meet customer and regulatory requirements through effective process control, improvement, and customer satisfaction monitoring.
Why It's Important
ISO 9001 is important because it ensures consistent quality in products and services, meeting customer expectations and regulatory requirements, thereby enhancing customer satisfaction and continuous improvement in processes, pivotal for a Quality Inspector's role in maintaining and verifying quality standards.
How to Improve ISO 9001 Skills
Improving ISO 9001, particularly from the perspective of a Quality Inspector, involves focusing on continuous improvement, effective documentation, and stakeholder engagement. Here's a concise guide:
Conduct Regular Audits: Regularly perform internal audits to ensure compliance and identify areas for improvement. Use these findings to enhance processes and quality management systems. ISO 19011 provides guidelines for auditing management systems.
Engage with Stakeholders: Engage with customers, suppliers, and employees to gather feedback on quality and processes. This feedback is crucial for making informed improvements. ISO 9001:2015 Clause 9 emphasizes the importance of performance evaluation.
Implement Corrective Actions: Quickly address any non-conformities or issues identified during audits or through feedback. Document these actions thoroughly to prevent recurrence. ISO 9001:2015 Clause 10 focuses on improvement, including corrective actions.
Continuous Training: Ensure ongoing training and competency development for all employees, particularly those involved in quality control and inspection. This enhances their ability to identify and address quality issues.
Leverage Quality Management Tools: Utilize quality management tools such as Six Sigma, Kaizen, and 5S to streamline processes and reduce waste, thereby improving quality and efficiency.
Maintain Comprehensive Documentation: Keep detailed records of processes, changes, and quality control activities. This helps in tracking improvements and proves compliance during external audits.
By focusing on these areas, a Quality Inspector can significantly contribute to improving an organization's ISO 9001 compliance and overall quality management system.
How to Display ISO 9001 Skills on Your Resume
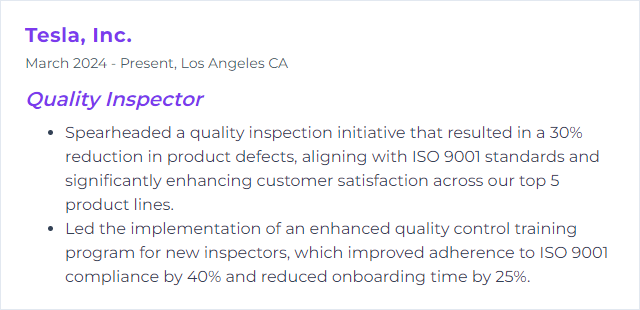
2. Six Sigma
Six Sigma is a data-driven approach and methodology for eliminating defects, aiming to improve quality and efficiency in processes by minimizing variability. For a Quality Inspector, it involves using statistical tools to measure, analyze, and enhance a company's operational performance, ensuring products or services meet stringent quality standards.
Why It's Important
Six Sigma is important for a Quality Inspector because it provides a systematic and data-driven methodology to reduce defects, improve processes, and ensure quality consistency, directly enhancing product reliability and customer satisfaction.
How to Improve Six Sigma Skills
To improve Six Sigma as a Quality Inspector, focus on:
Enhance Your Knowledge: Deepen your understanding of Six Sigma methodologies by pursuing higher certifications like Green Belt or Black Belt. These programs build expertise in identifying defects, process improvement, and data analysis.
Apply DMAIC Rigorously: Emphasize the DMAIC (Define, Measure, Analyze, Improve, Control) model in your quality inspection processes. This structured approach helps in systematically improving and optimizing processes.
Use Quality Tools Effectively: Familiarize yourself with and utilize Six Sigma tools such as Fishbone Diagrams, Control Charts, and FMEA (Failure Modes and Effects Analysis). These tools aid in identifying, analyzing, and mitigating quality issues.
Lean Integration: Integrate Lean principles with Six Sigma. Combining lean manufacturing techniques with Six Sigma can expedite waste reduction and streamline processes, enhancing overall efficiency.
Continuous Learning and Application: Stay informed about the latest trends and tools in quality management by visiting leading quality resources like ASQ (American Society for Quality) and iSixSigma. Apply new learnings and methodologies to your work to continuously improve your competence and performance as a Quality Inspector.
By focusing on these areas, a Quality Inspector can significantly contribute to and improve Six Sigma processes within their organization.
How to Display Six Sigma Skills on Your Resume
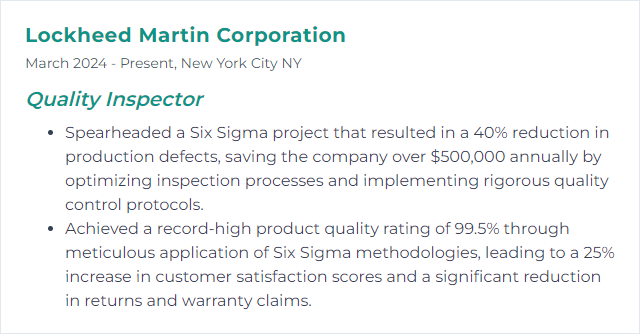
3. Lean Manufacturing
Lean Manufacturing is a systematic approach to minimizing waste within manufacturing systems while maximizing productivity, aimed at achieving higher quality products with fewer defects, as relevant to a Quality Inspector's focus on ensuring product quality and process efficiency.
Why It's Important
Lean Manufacturing is important because it focuses on reducing waste and improving efficiency, directly impacting product quality by minimizing defects and ensuring consistent, high-quality outputs. For a Quality Inspector, it streamlines inspection processes and enhances the overall quality of products.
How to Improve Lean Manufacturing Skills
Improving Lean Manufacturing, especially from a Quality Inspector's perspective, involves focusing on waste reduction, continuous improvement, and quality enhancement. Here are concise steps:
- Implement Continuous Improvement: Engage in Kaizen activities to constantly seek ways to improve processes and eliminate waste.
- Adopt a Zero-Defects Mentality: Emphasize the importance of quality in every aspect of production. Tools like Poka-Yoke can help prevent errors before they occur.
- Enhance Process Efficiency: Utilize Value Stream Mapping to identify and eliminate waste in production processes, focusing on adding value to the customer.
- Foster a Culture of Quality: Train and empower all team members to take responsibility for quality, promoting an environment where quality improvement is everyone's job. Quality Culture resources can guide in shaping such an environment.
- Utilize Quality Inspection Tools Effectively: Make use of advanced inspection tools and techniques such as Statistical Process Control (SPC) to monitor processes and ensure they remain within specified limits.
- Engage in Root Cause Analysis: When defects occur, use techniques like The 5 Whys to identify the underlying cause and implement corrective actions to prevent recurrence.
By focusing on these areas, a Quality Inspector can significantly contribute to the improvement of Lean Manufacturing practices within their organization.
How to Display Lean Manufacturing Skills on Your Resume
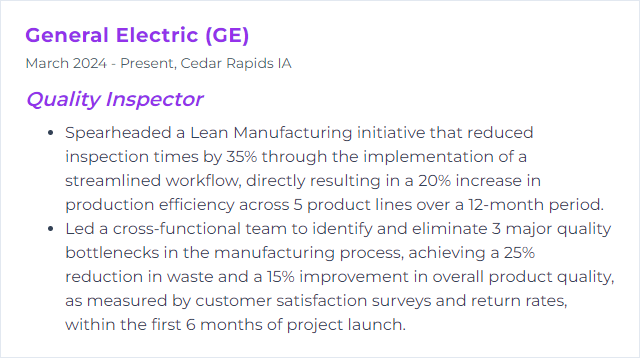
4. Statistical Process Control (SPC)
Statistical Process Control (SPC) is a method used by quality inspectors to monitor and control a process using statistical techniques to ensure it operates at its fullest potential, minimizing variability and defects.
Why It's Important
Statistical Process Control (SPC) is crucial for a Quality Inspector because it enables the monitoring and control of production processes to ensure they operate at their intended level of performance, thus minimizing variability, reducing defects, and enhancing product quality consistently.
How to Improve Statistical Process Control (SPC) Skills
Improving Statistical Process Control (SPC) involves several key steps. Here's a concise guide tailored for a Quality Inspector:
Education and Training: Ensure comprehensive understanding and skills in SPC techniques. ASQ’s SPC training offers a good start.
Data Collection: Implement rigorous and accurate data collection methods, focusing on consistency. NIST’s Guidelines can help refine this process.
Software Tools: Leverage SPC software for more efficient data analysis and visualization. Consider tools like Minitab or SPC for Excel for ease of use and robust analysis capabilities.
Process Monitoring: Regularly monitor processes using control charts. For guidelines on effective control chart implementation, ASQ’s resources are invaluable.
Continuous Improvement: Adopt a Kaizen or continuous improvement approach to SPC, making incremental improvements based on data-driven insights. Learn more about Kaizen.
Communication and Collaboration: Foster open communication and collaboration between departments to ensure SPC findings are effectively implemented. This guide from Harvard Business Review highlights the importance of team dynamics.
Review and Adapt: Regularly review SPC processes and adapt to changes in production or technology. Staying updated with the latest in SPC can be achieved through resources like Quality Magazine.
Remember, the effectiveness of SPC hinges on the commitment to quality at all levels of the organization and the continuous application of the SPC principles.
How to Display Statistical Process Control (SPC) Skills on Your Resume
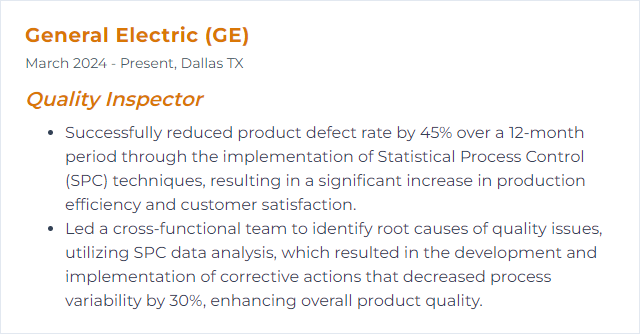
5. Quality Management Systems (QMS)
A Quality Management System (QMS) is a structured framework of policies, processes, and procedures required for planning and execution in the core business areas of an organization, aiming to consistently meet customer and regulatory requirements and enhance customer satisfaction. For a Quality Inspector, a QMS guides the inspection criteria, methods, and documentation to ensure products or services meet the established quality standards.
Why It's Important
Quality Management Systems (QMS) are crucial because they ensure that products and services consistently meet customer requirements and improve their quality and reliability, thus enhancing customer satisfaction. For a Quality Inspector, QMS provides structured processes and clear criteria for inspecting, monitoring, and improving quality, ensuring compliance with standards and regulations, and facilitating continuous improvement in quality control efforts.
How to Improve Quality Management Systems (QMS) Skills
Improving Quality Management Systems (QMS) involves a continuous process of evaluation and enhancement to meet and exceed customer expectations. For a Quality Inspector, focusing on the following steps can be crucial:
Understand and Apply QMS Standards: Familiarize yourself with global standards like ISO 9001, which outlines the criteria for a QMS. Understanding these standards can help ensure the processes you inspect meet international quality benchmarks.
Engage in Continuous Training: Stay updated with the latest quality inspection techniques and QMS processes through ongoing professional development. This can include workshops, webinars, and certification courses.
Implement a Robust Audit Process: Regularly conduct audits of the QMS to identify areas for improvement. Audits can help uncover inefficiencies and non-conformances in the system.
Leverage Technology: Utilize QMS software solutions to streamline quality inspections, manage documentation efficiently, and monitor quality metrics in real-time.
Foster a Culture of Quality: Advocate for a culture of continuous improvement within the organization. Encourage feedback from all stakeholders and implement a system where quality goals are aligned with organizational objectives.
Focus on Customer Feedback: Systematically collect and analyze customer feedback to understand their needs and expectations better. Use this information to drive improvements in the QMS.
Benchmarking and Best Practices: Regularly compare your QMS with those of industry leaders. Adopting industry best practices can help in enhancing the effectiveness of your QMS.
By following these steps, a Quality Inspector can significantly contribute to the improvement of Quality Management Systems, ensuring that the organization not only meets but exceeds the quality standards expected by customers and regulatory bodies.
How to Display Quality Management Systems (QMS) Skills on Your Resume
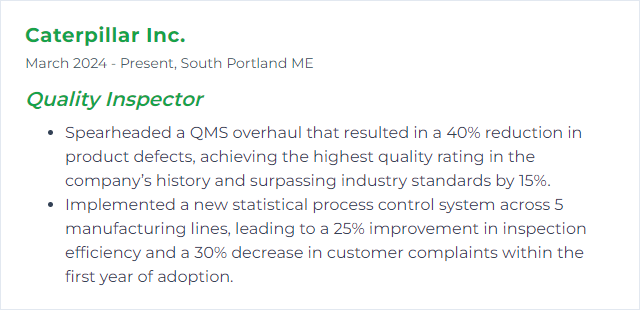
6. Root Cause Analysis
Root Cause Analysis (RCA) is a systematic process used by Quality Inspectors to identify the underlying reasons for defects or problems in products or processes, aiming to implement solutions that prevent recurrence.
Why It's Important
Root Cause Analysis is essential for a Quality Inspector because it helps identify the underlying cause of defects or problems, ensuring the implementation of effective solutions to prevent recurrence, thereby maintaining product quality and enhancing customer satisfaction.
How to Improve Root Cause Analysis Skills
Improving Root Cause Analysis (RCA) for a Quality Inspector involves a systematic approach to identify the underlying causes of problems to prevent their recurrence. Here’s a concise guide:
Define the Problem Clearly: Start with a clear, concise description of the issue, focusing on specific symptoms.
Collect Data: Gather all relevant data about the problem, including when and where it occurs, its severity, and any patterns.
Identify Possible Causes: Use brainstorming or tools like the 5 Whys technique or Fishbone Diagram to list potential causes.
Analyze Causes: Investigate the listed causes to determine their validity by looking for evidence that links them directly to the problem.
Identify Root Cause(s): Through analysis, pinpoint the primary cause(s) that, if resolved, would prevent recurrence.
Develop Action Plan: Create a strategy to address the root cause(s), including corrective actions and responsible parties.
Implement and Monitor: Apply the corrective actions and monitor the situation to ensure the problem is resolved.
Review and Adjust: Assess the effectiveness of the intervention. If the problem persists, revisit the analysis to identify any missed or new causes.
For further enhancement in RCA skills, consider exploring resources and training offered by reputable organizations:
ASQ’s Root Cause Analysis: Offers training and certification for quality professionals.
Root Cause Analysis Tools and Techniques: Provides a detailed overview of various RCA tools and methodologies.
Remember, effective RCA is iterative. If initial solutions don't resolve the problem, revisit your analysis to explore other potential causes.
How to Display Root Cause Analysis Skills on Your Resume
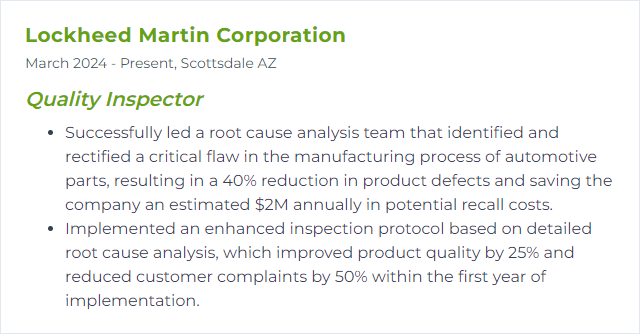
7. GD&T (Geometric Dimensioning and Tolerancing)
GD&T (Geometric Dimensioning and Tolerancing) is a system for defining and communicating engineering tolerances. It uses symbolic language on engineering drawings and computer-generated three-dimensional solid models for explicitly describing nominal geometry and its allowable variation. For a Quality Inspector, GD&T provides a clear and precise way to check parts and assemblies for adherence to design intentions, ensuring that components fit together properly and function as intended with the desired quality.
Why It's Important
GD&T is crucial for a Quality Inspector because it ensures parts meet precise geometric specifications and tolerances, facilitating consistent, accurate, and interoperable manufacturing and quality control across diverse components and assemblies.
How to Improve GD&T (Geometric Dimensioning and Tolerancing) Skills
Improving GD&T skills, especially for a Quality Inspector, involves a combination of theoretical learning, practical application, and continuous improvement. Here’s a concise guide:
Understand the Basics: Start with a solid foundation in the principles of GD&T. ASME Y14.5 is the primary standard for GD&T in the United States. ASME's website offers resources and the standard itself for study.
Online Courses and Certifications: Engage in online courses that offer structured learning paths. Websites like Udemy and Coursera offer courses on GD&T fundamentals and advanced topics. Look for courses that offer practical examples and quizzes.
Hands-On Practice: Apply what you learn in real-world scenarios or through simulation software. Practice interpreting and creating drawings with GD&T specifications. This hands-on experience is crucial.
Join Forums and Groups: Engage with professional communities online. LinkedIn groups and forums like Eng-Tips can be valuable for asking questions, sharing experiences, and staying updated on industry trends.
Read Books and Articles: Supplement your learning with books and industry publications. "Geometric Dimensioning and Tolerancing" by David A. Madsen is a recommended read. Also, regularly visit Quality Magazine for articles and case studies related to GD&T and quality inspection.
Feedback and Mentorship: Seek feedback on your work from more experienced colleagues or a mentor. They can provide insight and tips that only come from years of experience.
Continual Learning: GD&T standards and best practices evolve. Stay informed on the latest updates to standards like ASME Y14.5 through ASME and participate in refresher courses or workshops as needed.
By following these steps and consistently applying yourself, you can significantly improve your GD&T skills as a Quality Inspector.
How to Display GD&T (Geometric Dimensioning and Tolerancing) Skills on Your Resume
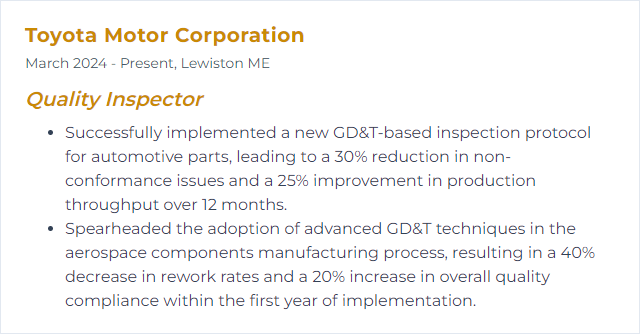
8. CMM (Coordinate Measuring Machine)
A Coordinate Measuring Machine (CMM) is a device used in manufacturing and assembly processes to inspect the dimensions and geometry of physical objects. It precisely measures the coordinates of points on an object's surface using a probe, helping Quality Inspectors ensure that parts meet specified tolerances and quality standards.
Why It's Important
A Coordinate Measuring Machine (CMM) is critical for a Quality Inspector because it enables precise measurement of an object's geometry to ensure parts meet specified tolerances and quality standards, thus ensuring product reliability and consistency.
How to Improve CMM (Coordinate Measuring Machine) Skills
Improving the performance and accuracy of a Coordinate Measuring Machine (CMM) involves several key steps. For a Quality Inspector, focusing on calibration, maintenance, software updates, operator training, and environmental control is crucial. Here’s a concise guide:
Regular Calibration: Ensure your CMM is calibrated regularly against known standards to maintain accuracy. NIST provides guidelines and standards for calibration.
Routine Maintenance: Perform routine maintenance checks and cleanings as per the manufacturer's recommendations to prevent mechanical wear and tear. Mitutoyo offers maintenance tips for CMMs.
Software Updates: Keep the CMM software updated to leverage the latest features and improve measurement efficiency. Hexagon MI often releases software updates and improvements.
Operator Training: Ensure operators are well-trained in CMM usage, measurement techniques, and software functionalities. ZEISS Academy provides comprehensive training programs.
Environmental Control: Maintain a stable environment (temperature, humidity, vibration) where the CMM operates, as environmental fluctuations can affect measurements. Renishaw discusses environmental considerations in detail.
Implementing these steps can significantly enhance the performance and reliability of your CMM operations.
How to Display CMM (Coordinate Measuring Machine) Skills on Your Resume
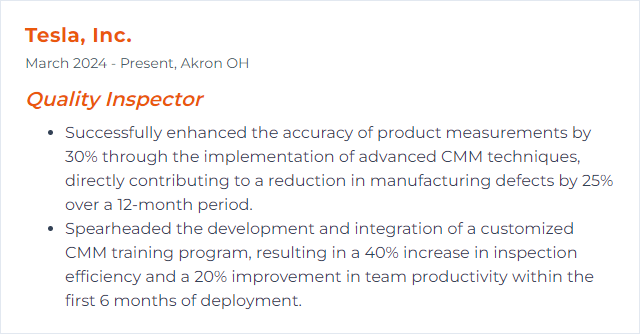
9. FMEA (Failure Mode and Effects Analysis)
FMEA (Failure Mode and Effects Analysis) is a systematic method used to identify and evaluate potential failures in a product or process, assess their impact, and prioritize actions to mitigate or eliminate risks, ensuring quality and reliability.
Why It's Important
FMEA (Failure Mode and Effects Analysis) is crucial for a Quality Inspector because it proactively identifies potential failures in products or processes and their likely effects, enabling the prioritization of corrective actions to mitigate risks, enhance reliability, and ensure product quality and safety.
How to Improve FMEA (Failure Mode and Effects Analysis) Skills
Improving Failure Mode and Effects Analysis (FMEA) involves several key steps focused on enhancing the accuracy, comprehensiveness, and effectiveness of the analysis. Here's a concise guide tailored for a Quality Inspector:
Cross-Functional Teamwork: Assemble a diverse team with members from different departments (design, manufacturing, quality, etc.) to gain varied perspectives on potential failure modes. ASQ's guide on FMEA teamwork emphasizes the importance of collaborative analysis.
Thorough Risk Assessment: Utilize the Risk Priority Number (RPN) effectively by accurately identifying and assessing the severity, occurrence, and detection of each potential failure mode. AIAG & VDA FMEA Handbook provides a standardized approach for risk assessment.
Dynamic Documentation: Keep FMEA documents dynamic by regularly updating them with new findings, changes in the manufacturing process, or updates in standards. This ensures the FMEA remains relevant and effective. The ISO 9001 Checklist mentions the importance of maintaining documented information.
Leverage Software Tools: Utilize FMEA software tools for more efficient data management, analysis, and reporting. These tools can also facilitate easier collaboration among team members. ReliaSoft XFMEA is an example of such a tool that streamlines the FMEA process.
Training and Education: Continuously educate and train the FMEA team on best practices, new methodologies, and updates to relevant standards. The ASQ FMEA Training is a resource for deepening team expertise in FMEA.
Integration with Other Quality Tools: Integrate FMEA with other quality management tools like Control Plans and Statistical Process Control (SPC) for a more holistic approach to quality management. Integrating FMEA with Other Quality Processes provides insights into how FMEA can work in tandem with other tools.
By focusing on these areas, a Quality Inspector can significantly enhance the effectiveness of FMEA in identifying and mitigating risks in the manufacturing process.
How to Display FMEA (Failure Mode and Effects Analysis) Skills on Your Resume
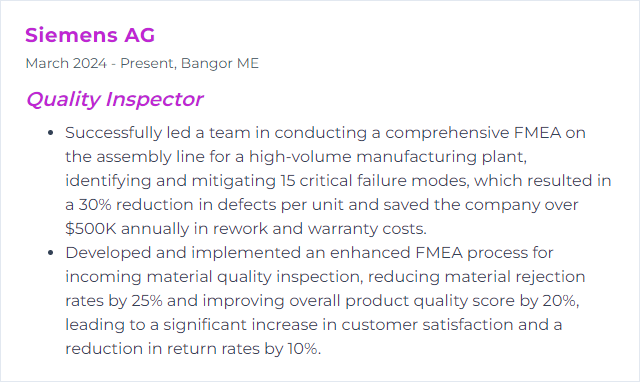
10. SAP Quality Module
The SAP Quality Module, also known as SAP QM (Quality Management), is a component of the SAP ERP system that supports the various aspects of quality management. For a Quality Inspector, it provides functionalities to plan, execute, and record quality inspections of materials and products, manage defects, and ensure compliance with quality standards. It helps in maintaining high-quality products and processes through integrated quality control and quality assurance processes.
Why It's Important
The SAP Quality Management (QM) module is crucial for a Quality Inspector as it streamlines and automates the process of quality control and assurance, from planning through inspection to certification. It ensures compliance, reduces defects, and enhances product quality by integrating with manufacturing and procurement processes.
How to Improve SAP Quality Module Skills
Improving the SAP Quality Module, especially for a Quality Inspector, involves focusing on several key areas to enhance efficiency, accuracy, and usability. Here are concise steps with relevant resources:
Enhance Data Quality: Implement data validation checks and standardize data entry procedures to improve the accuracy of quality data. SAP Master Data Governance can help in maintaining high-quality master data across the enterprise.
Automate Processes: Utilize SAP's automation features to streamline repetitive tasks such as inspection lot creation and result recording. This not only saves time but also reduces human errors. Explore SAP Intelligent Robotic Process Automation for opportunities to automate within the quality module.
Integrate with Other Modules: Ensure the Quality Module is seamlessly integrated with other SAP modules like Material Management (MM) and Production Planning (PP) for a holistic approach to quality across the supply chain. SAP's Integration Suite can facilitate this.
Enhance Reporting and Analytics: Leverage SAP Analytics Cloud to create comprehensive dashboards and reports for real-time quality monitoring and decision-making. This allows Quality Inspectors to identify trends and issues promptly. Check out SAP Analytics Cloud for more on advanced analytics capabilities.
Continuous Training and Support: Ensure that Quality Inspectors have ongoing access to training and resources to keep up with new features and best practices within the SAP Quality Module. SAP's Training and Certification can be a valuable resource for this.
Feedback Loop for Continuous Improvement: Establish a feedback loop with Quality Inspectors to gather insights on usability and functionality issues, which can then be addressed in future improvements or customizations.
By focusing on these areas, you can significantly enhance the effectiveness of the SAP Quality Module for Quality Inspectors, leading to improved quality control processes and outcomes.
How to Display SAP Quality Module Skills on Your Resume
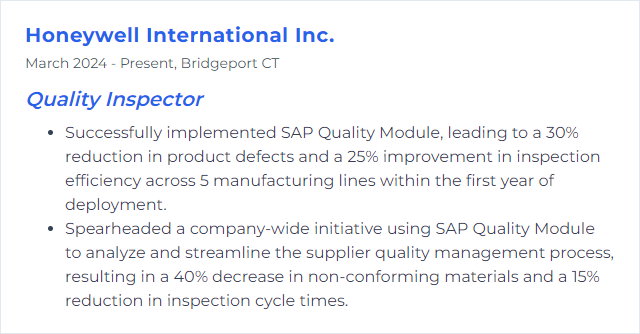
11. Visual Inspection Techniques
Visual Inspection Techniques involve the use of the human eye, possibly enhanced with various tools (like magnifying glasses or lamps), to evaluate the quality and integrity of materials, components, and assemblies. It checks for defects, damages, or deviations from the specified standards, focusing on surface issues and alignment without dismantling the item. This method is fundamental for a Quality Inspector to ensure products meet quality and safety criteria.
Why It's Important
Visual Inspection Techniques are crucial for Quality Inspectors as they enable the early detection of defects, ensuring products meet quality standards and specifications, thereby preventing costly rework and maintaining customer satisfaction through the delivery of defect-free products.
How to Improve Visual Inspection Techniques Skills
Improving Visual Inspection Techniques for a Quality Inspector involves enhancing accuracy, efficiency, and consistency in identifying defects. Here are concise strategies:
Enhance Lighting and Environment: Proper lighting and a controlled environment minimize shadows and reflections, improving defect visibility. OSHA provides guidelines on optimal lighting conditions.
Use Appropriate Inspection Tools: Employ magnifying glasses, microscopes, or digital imaging for detailed inspection. Tools should be chosen based on the inspection requirements. ASQ offers insights on tool selection.
Standardize Inspection Processes: Develop and follow standardized inspection checklists or procedures to ensure consistency. The ISO 9001 standards can guide creating effective quality management systems.
Implement Training and Certification: Regular training and certification ensure inspectors are up-to-date with the latest inspection techniques and standards. ASQ Certifications offer various options for professional development.
Adopt Automated Inspection Systems: Where applicable, integrate automated visual inspection systems to augment human inspectors, reducing fatigue and improving detection rates. Machine Vision Systems offer examples of technologies that can be adopted.
Continuous Feedback and Improvement: Encourage feedback from inspectors about the inspection process and implement a continuous improvement cycle based on this feedback. Plan-Do-Check-Act (PDCA) is a methodical cycle for achieving continuous improvement.
Implementing these strategies can significantly enhance the effectiveness of visual inspection techniques for Quality Inspectors.
How to Display Visual Inspection Techniques Skills on Your Resume
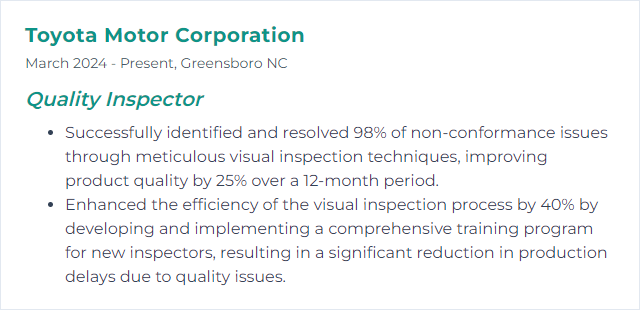
12. AS9100
AS9100 is a widely adopted and standardized quality management system for the aerospace industry. It encompasses the requirements of ISO 9001 along with additional aerospace-specific quality and safety standards. For a Quality Inspector, it means adhering to rigorous inspection protocols, documentation practices, and quality standards to ensure products and services meet the stringent requirements of the aerospace sector.
Why It's Important
AS9100 is important for a Quality Inspector because it provides a standardized, high-quality framework for ensuring safety, reliability, and compliance within the aerospace industry, directly impacting the quality and integrity of products and services.
How to Improve AS9100 Skills
Improving AS9100 as a Quality Inspector involves enhancing the quality management system (QMS) in the aerospace sector. Here are concise steps with external resources for further exploration:
Understand AS9100 Requirements: Thoroughly understand the specific requirements of AS9100D. Familiarize yourself with the standard's structure and key areas relevant to quality inspection. AS9100D Overview.
Engage in Continuous Training: Stay updated with the latest quality inspection techniques and AS9100 revisions through regular training. ASQ Training Resources.
Implement a Robust Inspection Plan: Develop and maintain a comprehensive inspection plan that aligns with AS9100 requirements, focusing on critical areas identified in the standard. Creating an Inspection Plan.
Utilize Corrective and Preventive Actions (CAPA): Actively identify non-conformities and inefficiencies. Use CAPA to address these issues, preventing recurrence and promoting continuous improvement. CAPA Guidelines.
Promote a Culture of Quality: Encourage a workplace environment where every employee is engaged in quality improvement and understands their role in the QMS. Building a Culture of Quality.
Conduct Regular Audits: Perform internal audits to ensure compliance with AS9100 standards and identify areas for improvement. Guide to Internal Quality Audits.
Leverage Quality Metrics and KPIs: Track performance using specific metrics and key performance indicators (KPIs) to measure the effectiveness of the QMS and identify improvement opportunities. KPIs for Quality Management.
Foster Supplier Quality Management: Ensure that suppliers comply with AS9100 standards, integrating supplier quality within the organization's QMS. Supplier Management Best Practices.
Engage in Continuous Improvement: Adopt a mindset of continuous improvement, using tools like Six Sigma and Lean to enhance processes continually. Continuous Improvement in AS9100.
By focusing on these areas, a Quality Inspector can significantly contribute to the improvement of their organization's QMS under AS9100 standards.
How to Display AS9100 Skills on Your Resume
