Top 12 Quality Assurance Inspector Skills to Put on Your Resume
In today's competitive job market, standing out as a Quality Assurance Inspector requires showcasing a blend of technical proficiency, keen attention to detail, and excellent communication skills on your resume. Highlighting your top skills effectively can make the difference in catching the eye of hiring managers and securing your position in the field.
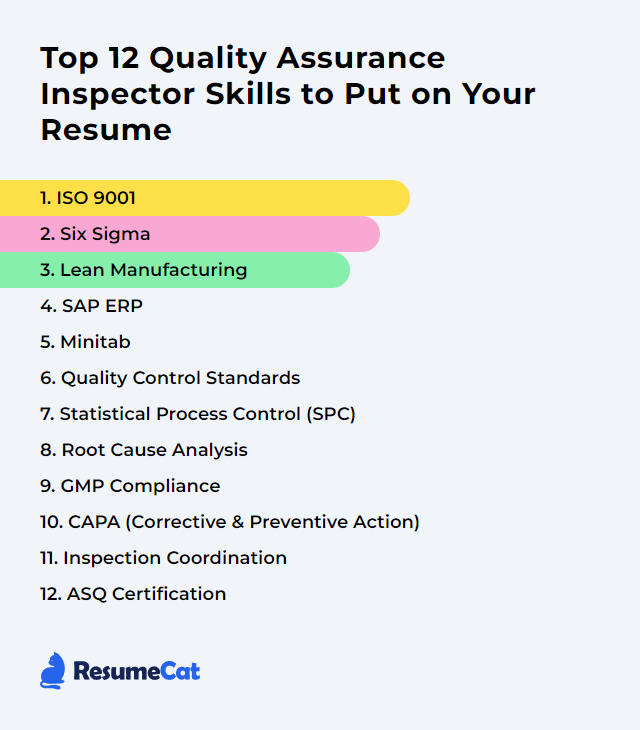
Quality Assurance Inspector Skills
- ISO 9001
- Six Sigma
- Lean Manufacturing
- SAP ERP
- Minitab
- Quality Control Standards
- Statistical Process Control (SPC)
- Root Cause Analysis
- GMP Compliance
- CAPA (Corrective and Preventive Action)
- Inspection Coordination
- ASQ Certification
1. ISO 9001
ISO 9001 is an international standard that specifies requirements for a quality management system (QMS). It helps organizations ensure they consistently provide products and services that meet customer and regulatory requirements. For a Quality Assurance Inspector, it provides a framework and criteria for monitoring and improving product quality and performance.
Why It's Important
ISO 9001 is important because it provides a framework for consistent quality management practices, ensuring products and services meet customer and regulatory requirements, thereby enhancing customer satisfaction and continuous improvement. For a Quality Assurance Inspector, it outlines the standards for quality checks, documentation, and process improvement, ensuring their work aligns with international quality standards.
How to Improve ISO 9001 Skills
Improving ISO 9001 involves a focus on continuous improvement, customer satisfaction, and process optimization. Here’s a concise guide tailored for a Quality Assurance Inspector:
Understand the Standard: Deeply understand the requirements of ISO 9001. Continuous education on updates and best practices is crucial. The ISO website provides resources and updates.
Engage in Training: Participate in ISO 9001 training programs to stay updated on best practices and auditing techniques. Online resources like ASQ offer valuable courses.
Implement a Process Approach: Focus on the efficiency and improvement of processes. Documenting, reviewing, and optimizing processes are key. ISO’s process approach guide provides insights.
Promote a Culture of Quality: Encourage a company-wide commitment to quality. Engage teams through meetings and training to foster a quality-centric mindset.
Conduct Regular Audits: Perform regular internal audits to identify non-conformities and areas for improvement. Use findings to implement corrective actions. The ISO 19011 guidelines can assist in conducting effective audits.
Use Quality Tools: Utilize quality tools (e.g., Six Sigma, PDCA) for problem-solving and process improvement. Resources like ASQ’s Quality Tools can be very helpful.
Focus on Customer Feedback: Collect, analyze, and act on customer feedback to improve product quality and customer satisfaction. Implementing a feedback loop is essential for continuous improvement.
Monitor and Measure Performance: Establish Key Performance Indicators (KPIs) to monitor quality objectives and processes. Regular review meetings to assess KPIs help in identifying improvement areas.
Continuously Improve: Adopt the PDCA (Plan-Do-Check-Act) cycle for continuous improvement of the quality management system (QMS). This iterative process is fundamental to ISO 9001’s philosophy.
Stay Informed on Regulatory Changes: Keep abreast of changes in quality management standards and regulations. Websites like Quality Digest can provide valuable updates and insights.
By focusing on these areas, a Quality Assurance Inspector can significantly contribute to the improvement and maintenance of an organization’s ISO 9001 QMS.
How to Display ISO 9001 Skills on Your Resume
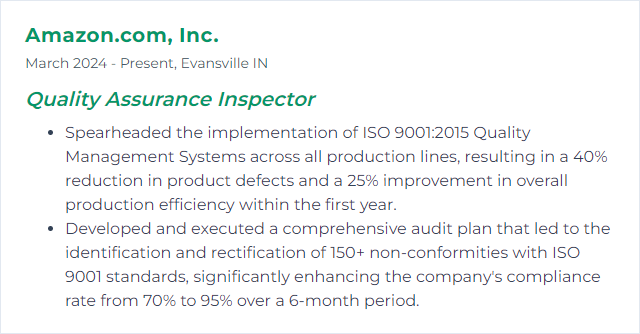
2. Six Sigma
Six Sigma is a data-driven methodology and set of techniques aimed at improving business processes by minimizing defects and variability to enhance quality and efficiency, highly relevant for Quality Assurance Inspectors in monitoring and ensuring product or service excellence.
Why It's Important
Six Sigma is important because it provides a systematic methodology to reduce defects and improve quality, ensuring products meet or exceed customer satisfaction. For a Quality Assurance Inspector, it enhances precision in identifying and eliminating errors, fostering consistent quality control and operational efficiency.
How to Improve Six Sigma Skills
Improving Six Sigma as a Quality Assurance Inspector involves enhancing your knowledge and application of the methodology to streamline processes, reduce errors, and ensure high-quality outputs. Here are concise steps with inline linking for further exploration:
Educate Yourself Further: Deepen your understanding of Six Sigma principles and tools. Online courses from ASQ or Coursera can be a good start.
Apply DMAIC Rigorously: Ensure you're applying the Define, Measure, Analyze, Improve, Control (DMAIC) framework effectively in every project. iSixSigma offers detailed insights into each phase.
Utilize Quality Tools: Master and utilize Six Sigma tools like Fishbone Diagrams, FMEA, and Control Charts effectively. The American Society for Quality (ASQ) provides resources and tools for quality improvement.
Engage in Continuous Learning: Stay updated with the latest trends and techniques in Six Sigma and quality improvement. Subscribing to Quality Magazine can be insightful.
Get Certified: Consider advancing your skills through Six Sigma Green Belt or Black Belt certification, which can provide a structured path for improvement. Information on certification can be found at ASQ’s Certification page.
Implement Quality Improvement Projects: Apply your skills in real-world projects and document the results. This hands-on experience is invaluable.
Network with Professionals: Joining forums and groups, such as those found on LinkedIn, can provide insights and advice from experienced professionals.
By following these steps and leveraging the resources provided, you can significantly enhance your effectiveness as a Quality Assurance Inspector within the Six Sigma framework.
How to Display Six Sigma Skills on Your Resume
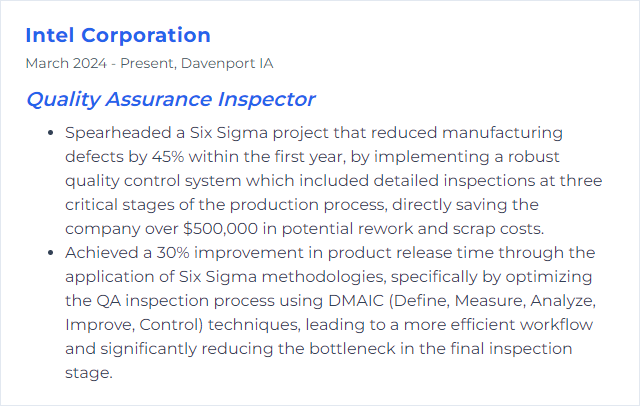
3. Lean Manufacturing
Lean Manufacturing is a systematic approach to minimize waste within manufacturing systems while maximizing productivity, aimed at improving overall product quality and efficiency relevant to a Quality Assurance Inspector's role in ensuring products meet set standards with minimal defects and waste.
Why It's Important
Lean Manufacturing is important for a Quality Assurance Inspector as it emphasizes reducing waste, improving process efficiency, and ensuring product quality, thereby enabling more consistent and reliable inspection processes and outcomes.
How to Improve Lean Manufacturing Skills
Improving Lean Manufacturing, particularly from a Quality Assurance Inspector's perspective, involves focusing on waste reduction, continuous improvement, and quality control at every stage. Here are concise strategies to enhance Lean Manufacturing:
Implement Continuous Improvement (Kaizen): Foster a culture of continuous improvement by encouraging feedback and suggestions from all employees. This involves regular training and workshops. Learn more about Kaizen.
Adopt the 5S System: Ensure a clean, organized, and efficient workspace to improve productivity and quality. The 5S principles are Sort, Set in order, Shine, Standardize, and Sustain. Details on 5S System.
Use Six Sigma Techniques: Implement Six Sigma methodologies to reduce defects and waste, thereby improving quality and efficiency. DMAIC (Define, Measure, Analyze, Improve, Control) is a core tool. Six Sigma Explained.
Apply Poka-Yoke (Error Proofing): Incorporate error-proofing methods to prevent and solve quality issues at the source, reducing rework and ensuring product quality. Introduction to Poka-Yoke.
Build Quality into the Process: Shift from detecting defects to preventing them by integrating quality control into each phase of the manufacturing process. Quality at Source.
Utilize Value Stream Mapping: Identify and eliminate non-value-adding activities in your processes to streamline production, reduce costs, and improve quality. Value Stream Mapping Guide.
Engage in Root Cause Analysis: When defects occur, use tools like the 5 Whys or Fishbone Diagram to identify and address the underlying causes, rather than just treating symptoms. Root Cause Analysis Techniques.
For Quality Assurance Inspectors, actively participating in these strategies ensures that Lean Manufacturing efforts are aligned with quality goals, fostering an environment of excellence and continuous improvement.
How to Display Lean Manufacturing Skills on Your Resume
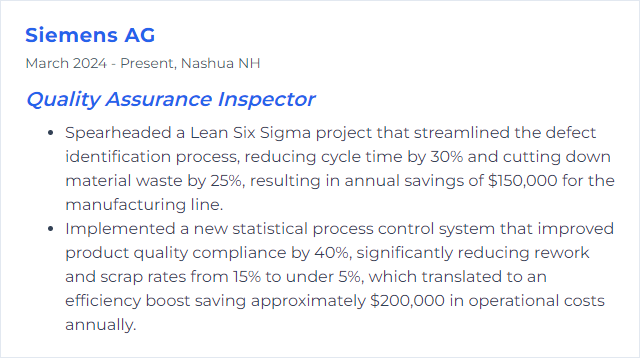
4. SAP ERP
SAP ERP is an enterprise resource planning software developed by SAP SE that integrates and automates core business processes, such as finance, HR, and supply chain management, to improve efficiency and data accuracy across an organization. For a Quality Assurance Inspector, it provides tools and data analytics to monitor and ensure product quality standards, manage compliance, and streamline quality control processes.
Why It's Important
SAP ERP is important for a Quality Assurance Inspector because it enables streamlined data management, process integration, and real-time visibility into quality control measures, ensuring consistent product and service quality adherence to standards.
How to Improve SAP ERP Skills
Improving SAP ERP for a Quality Assurance Inspector involves enhancing data accuracy, process automation, and reporting capabilities. Here are concise steps to achieve this:
Implement Data Validation: Ensure data entered into SAP ERP is accurate and consistent. Use input validation rules to prevent errors. SAP Documentation on Input Validation.
Automate Quality Checks: Utilize SAP's Quality Management (QM) module to automate inspections and quality checks. This reduces manual effort and increases efficiency. SAP QM Overview.
Customize Reports: Tailor reports in SAP to meet the specific needs of Quality Assurance Inspectors. Use SAP's reporting tools to create detailed and actionable reports. SAP Reporting and Analysis.
Integrate with Other Systems: Ensure SAP ERP integrates seamlessly with other systems (e.g., CRM, SCM) for a holistic view of quality across the supply chain. SAP Integration Suite.
Train Users: Provide continuous training and support to Quality Assurance Inspectors on using SAP ERP effectively. SAP Training and Certification.
By focusing on these areas, SAP ERP can be optimized to better support the roles and responsibilities of Quality Assurance Inspectors.
How to Display SAP ERP Skills on Your Resume
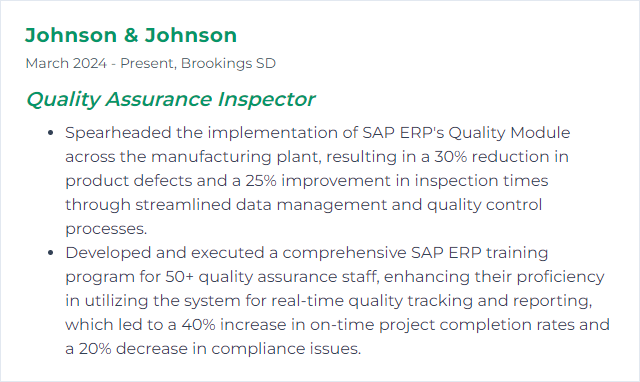
5. Minitab
Minitab is a statistical software package designed for data analysis and quality improvement, widely used by Quality Assurance Inspectors to monitor and enhance product quality through statistical methods and tools.
Why It's Important
Minitab is important for a Quality Assurance Inspector because it provides powerful statistical tools to analyze quality data, identify trends, pinpoint root causes of issues, and ensure process improvements, leading to enhanced product quality and customer satisfaction.
How to Improve Minitab Skills
Improving your efficiency and effectiveness in Minitab as a Quality Assurance Inspector involves focusing on key areas such as enhancing data analysis skills, automating repetitive tasks, and staying updated with the latest features. Here’s a concise guide to help you:
Master Statistical Tools: Deepen your understanding of statistical tools crucial for quality assurance, including control charts, capability analysis, and hypothesis testing. Minitab offers tutorials and case studies that are directly applicable to quality assurance tasks.
Utilize Minitab Assistant: Leverage the Minitab Assistant feature which guides you through analysis and helps in interpreting results accurately. This tool is especially useful for those who are not statistical experts.
Automate with Macros: For repetitive tasks, learn to create and use macros in Minitab. Macros can automate your analysis processes, saving time and reducing errors. Minitab’s support offers guidance on creating and using macros.
Stay Updated: Regularly update your software version to access the latest features and improvements. Check the Minitab blog and What’s New section for updates and tips.
Training and Education: Consider enrolling in Minitab training courses or webinars to enhance your skills further. Minitab offers a range of training options suited for different levels of expertise.
By focusing on these areas, you can significantly improve your proficiency in Minitab, leading to more effective and efficient quality assurance processes.
How to Display Minitab Skills on Your Resume
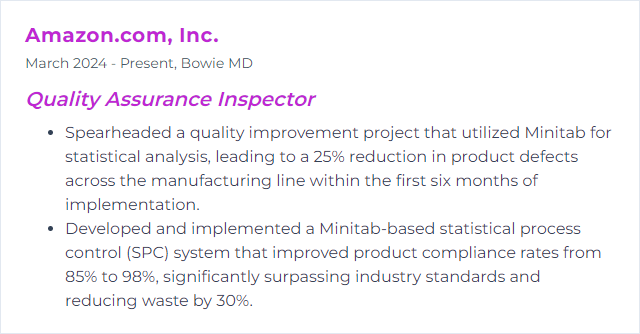
6. Quality Control Standards
Quality Control Standards are a set of criteria and guidelines established to ensure products or services meet specific requirements and maintain a desired level of excellence. For a Quality Assurance Inspector, these standards guide the inspection, testing, and evaluation processes to ensure consistent quality and reliability in the final output.
Why It's Important
Quality Control Standards are crucial as they ensure products meet specific requirements for consistency, safety, and customer satisfaction, enabling Quality Assurance Inspectors to detect defects and non-compliance, thereby maintaining high quality and preventing costly errors and recalls.
How to Improve Quality Control Standards Skills
Improving Quality Control Standards involves a multifaceted approach that emphasizes training, process optimization, and continuous improvement. Here's a concise guide for a Quality Assurance Inspector:
Enhance Training Programs: Invest in comprehensive training for all employees focusing on quality standards, inspection techniques, and the importance of quality control. ASQ's Training Courses offer a variety of options.
Standardize Processes: Develop and implement clear, standardized processes for all stages of production. This ensures consistency and makes it easier to identify areas for improvement. The ISO 9001 standards provide a framework for quality management systems.
Utilize Technology: Adopt advanced quality control technologies such as automated inspection systems and quality management software to enhance accuracy and efficiency. Explore solutions at Capterra.
Continuous Improvement: Implement a continuous improvement process, such as Kaizen, to systematically analyze and improve quality control processes over time. The Kaizen Institute offers insights and methodologies.
Engage in Audits and Feedback Loops: Regularly perform internal and external audits to assess compliance with quality standards. Use feedback from these audits to make informed improvements. Guidance on conducting effective audits can be found through ISO's Auditing Practices Group.
Collaborate with Suppliers: Work closely with suppliers to ensure that materials and components meet your quality standards. Supplier quality management resources are available at ASQ.
By focusing on these areas, Quality Assurance Inspectors can significantly improve quality control standards and contribute to the overall success and reliability of their products.
How to Display Quality Control Standards Skills on Your Resume
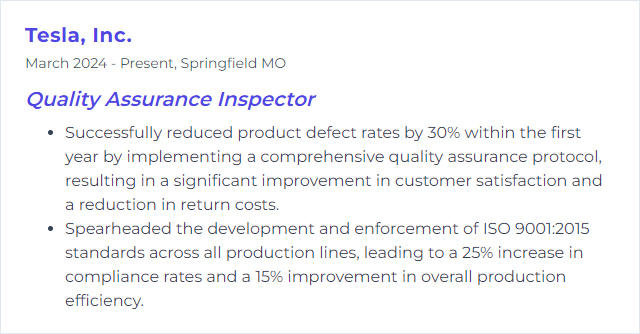
7. Statistical Process Control (SPC)
Statistical Process Control (SPC) is a method used in quality assurance that employs statistical techniques to monitor and control a process, ensuring that it operates at its full potential to produce conforming product with minimal waste. For a Quality Assurance Inspector, SPC involves analyzing process data through control charts and other tools to detect and address variations in the process before they lead to non-conformance, thereby maintaining product quality and consistency.
Why It's Important
Statistical Process Control (SPC) is crucial for a Quality Assurance Inspector because it enables the monitoring and control of process variability, ensuring product consistency and quality, reducing waste, and improving production efficiency.
How to Improve Statistical Process Control (SPC) Skills
Improving Statistical Process Control (SPC) involves enhancing data collection, analysis, and process optimization methods to ensure quality control and continuous improvement. Here's a concise guide for a Quality Assurance Inspector:
Enhance Data Collection: Use reliable and accurate measurement tools. Ensure data is collected consistently and systematically. ASQ offers insights on data collection and analysis tools.
Educate and Train: Invest in SPC training for team members to understand its importance and application. NIST provides resources on SPC concepts.
Implement Real-Time Monitoring: Utilize software that allows for real-time monitoring of processes. This enables immediate detection and correction of variations. Consider tools like Minitab for statistical analysis.
Analyze and Act on Data: Use SPC charts to identify trends, variations, and process capabilities. Focus on root cause analysis to systematically eliminate sources of variation. The PQ Systems website offers practical advice on using SPC charts effectively.
Continuous Improvement: Adopt a culture of continuous improvement by regularly reviewing process performance and implementing kaizen (continuous improvement) principles. The Lean Enterprise Institute provides resources on continuous improvement strategies.
By focusing on these steps, a Quality Assurance Inspector can significantly improve the effectiveness of SPC, leading to higher quality products and processes.
How to Display Statistical Process Control (SPC) Skills on Your Resume
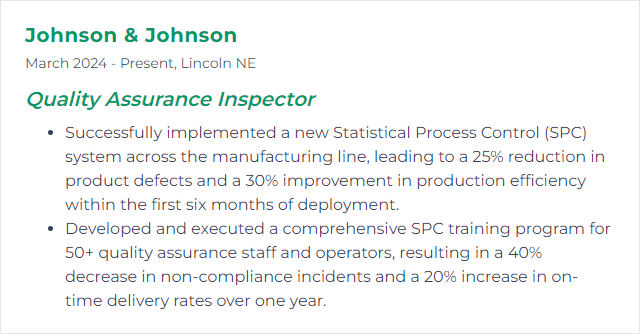
8. Root Cause Analysis
Root Cause Analysis (RCA) is a systematic process for identifying the underlying causes of problems or incidents to prevent their recurrence, particularly used in quality assurance to ensure product and process integrity.
Why It's Important
Root Cause Analysis (RCA) is crucial for a Quality Assurance Inspector because it enables the identification and resolution of the underlying issues causing defects or problems, ensuring the prevention of future occurrences and maintaining high-quality standards in products or processes.
How to Improve Root Cause Analysis Skills
Improving Root Cause Analysis (RCA) in the context of a Quality Assurance Inspector involves a structured approach to identify the underlying causes of problems to prevent their recurrence. Here are concise steps with resources for further exploration:
Define the Problem Clearly: Start by accurately defining the problem. Use tools like the 5 Whys or Fishbone Diagram to get a clear understanding of the issue. ASQ's Problem-Solving Tools
Gather Data: Collect data related to the problem's occurrences, including times, conditions, and other relevant information. This step may involve reviewing production logs, quality control reports, and customer feedback. CDC’s Data Collection Methods
Analyze Data: Use statistical tools and analysis methods to identify patterns or anomalies. Pareto Charts and Scatter Diagrams can be useful here. MindTools' Pareto Analysis
Identify Root Causes: Apply RCA methods like the 5 Whys or Cause and Effect Analysis to drill down to the root causes. iSixSigma's 5 Whys
Develop Action Plan: Once the root causes are identified, develop an action plan to address them. This should include corrective actions to fix the issue and preventive measures to avoid recurrence. Smartsheet's Action Plan Template
Implement and Monitor: Implement the action plan and monitor the situation to ensure the problem is resolved and does not recur. Continuous monitoring and follow-up are crucial. ProjectManager's Guide to Monitoring and Controlling
Review and Adjust: Regularly review the effectiveness of the action plan and make necessary adjustments. Continuous improvement should be the goal. ASQ's Continuous Improvement
Documentation and Training: Document the findings, actions taken, and lessons learned. Train relevant staff on the changes implemented to prevent future occurrences. TechSmith's Guide on Creating Effective Training Videos
By following these steps and utilizing the linked resources, a Quality Assurance Inspector can enhance their Root Cause Analysis process, leading to improved problem-solving and quality control outcomes.
How to Display Root Cause Analysis Skills on Your Resume
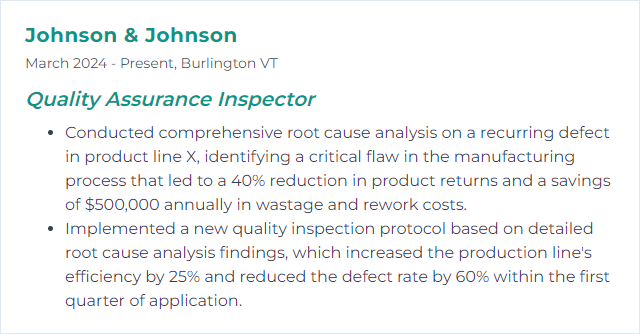
9. GMP Compliance
GMP Compliance refers to adherence to Good Manufacturing Practice regulations, ensuring products are consistently produced and controlled according to quality standards. For a Quality Assurance Inspector, it involves inspecting manufacturing processes, verifying compliance with regulatory standards, and ensuring products meet quality and safety requirements.
Why It's Important
GMP (Good Manufacturing Practice) compliance is crucial for a Quality Assurance Inspector because it ensures that products are consistently produced and controlled according to quality standards. This minimizes risks involved in pharmaceutical and food production that cannot be eliminated through testing the final product.
How to Improve GMP Compliance Skills
Improving GMP (Good Manufacturing Practice) compliance involves a multifaceted approach focusing on continuous training, thorough documentation, regular audits, and a culture of quality. Here’s a concise guide for a Quality Assurance Inspector:
Continuous Training: Ensure all staff, especially those on the production floor, are regularly trained and updated on GMP standards and their roles in compliance. FDA's Training Resources offer guidelines and courses.
Thorough Documentation: Maintain meticulous records of all processes, changes, and quality checks. Documentation should be clear, up-to-date, and readily accessible. The ICH Guideline Q7 provides insights into good documentation practices.
Regular Audits: Conduct internal audits frequently to identify and rectify non-compliance issues. Use findings to improve procedures and training. ISO 19011 Guidelines for auditing management systems can be a valuable resource.
Culture of Quality: Foster a quality-centric culture where every employee feels responsible for maintaining GMP standards. Encourage reporting of non-compliance without fear of repercussions.
Engage with Regulatory Bodies: Stay updated with guidelines from regulatory bodies like the FDA (FDA GMP Requirements) and EMA (EMA GMP Guidelines) to ensure your practices are aligned with the latest standards.
Utilize Technology: Implement quality management systems (QMS) to streamline documentation, training, and audits. Technology can also help in tracking compliance and identifying areas for improvement.
By focusing on these areas, a Quality Assurance Inspector can significantly contribute to enhancing GMP compliance within their organization.
How to Display GMP Compliance Skills on Your Resume
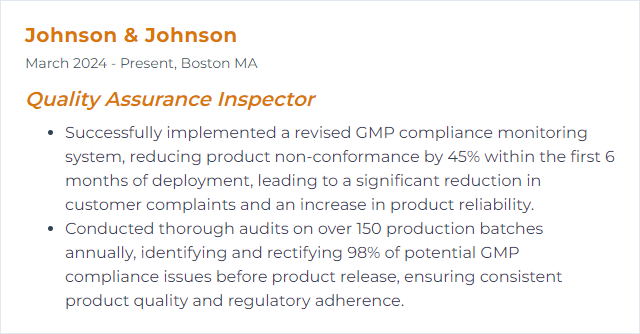
10. CAPA (Corrective and Preventive Action)
CAPA (Corrective and Preventive Action) is a quality management process used by a Quality Assurance Inspector to identify, address, and eliminate the root causes of identified issues or non-conformities to prevent their recurrence (corrective action) and to anticipate and prevent potential issues before they occur (preventive action).
Why It's Important
CAPA is crucial for a Quality Assurance Inspector because it helps identify, correct, and prevent defects or issues in products and processes, ensuring product quality, safety, and compliance with standards, thereby maintaining customer satisfaction and regulatory adherence.
How to Improve CAPA (Corrective and Preventive Action) Skills
Improving CAPA processes involves a structured approach focusing on accurately identifying issues, implementing effective solutions, and preventing recurrence. For a Quality Assurance Inspector, the following steps can significantly enhance CAPA effectiveness:
Identify the Root Cause: Use tools like 5 Whys or Fishbone Diagrams to drill down to the underlying cause of the problem, not just addressing symptoms.
Evaluate the Impact: Assess the scope and impact of the issue on product quality, compliance, and customer satisfaction to prioritize actions.
Develop an Action Plan: Create a detailed action plan including corrective (address current issue) and preventive (avoid recurrence) measures. Ensure actions are specific, measurable, achievable, relevant, and time-bound (SMART).
Implement Changes: Execute the action plan effectively. This may involve training, process changes, or equipment modifications.
Monitor and Verify: Use Quality Control tools to monitor the outcomes of the implemented actions. Verify their effectiveness over time to ensure the problem is resolved and does not recur.
Document and Communicate: Keep detailed records of the CAPA process and share lessons learned across the organization to prevent similar issues.
Review and Update: Regularly review the CAPA process itself for continuous improvement opportunities.
For a comprehensive understanding and improvement of CAPA processes, refer to the FDA's CAPA Guidance and the ISO 13485:2016 standards on quality management systems for medical devices, which provide industry-specific insights.
How to Display CAPA (Corrective and Preventive Action) Skills on Your Resume
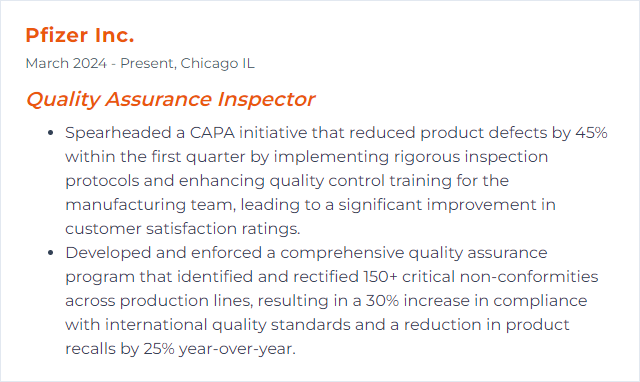
11. Inspection Coordination
Inspection Coordination, in the context of a Quality Assurance Inspector, involves organizing, scheduling, and overseeing inspections to ensure that products, services, or processes meet established quality standards. It includes coordinating with relevant departments, managing inspection activities, and ensuring compliance with quality specifications and regulatory requirements.
Why It's Important
Inspection Coordination is crucial for a Quality Assurance Inspector as it ensures that all inspections are systematically organized and conducted efficiently, guaranteeing that products or services meet the required quality standards and compliance is maintained, thereby minimizing defects and enhancing customer satisfaction.
How to Improve Inspection Coordination Skills
Improving Inspection Coordination as a Quality Assurance Inspector involves streamlining communication, adopting efficient scheduling practices, leveraging technology, and fostering a culture of continuous improvement. Here’s a concise guide:
Streamline Communication: Utilize communication tools like Slack for real-time collaboration and Trello for task management. Establish clear lines of communication between all stakeholders.
Efficient Scheduling: Adopt scheduling software such as Calendly to organize inspections and avoid conflicts, ensuring all parties are available.
Leverage Technology: Use inspection software like iAuditor by SafetyCulture to standardize inspection processes, collect data in real-time, and generate instant reports.
Continuous Improvement: Implement a feedback loop with teams to identify bottlenecks and areas for improvement. Tools like SurveyMonkey can facilitate gathering insights.
Training and Development: Regularly update training materials and sessions to ensure all inspectors are knowledgeable about the latest standards and practices. Online platforms like Coursera offer relevant courses.
By focusing on these key areas, Quality Assurance Inspectors can significantly enhance the efficiency and effectiveness of inspection coordination.
How to Display Inspection Coordination Skills on Your Resume
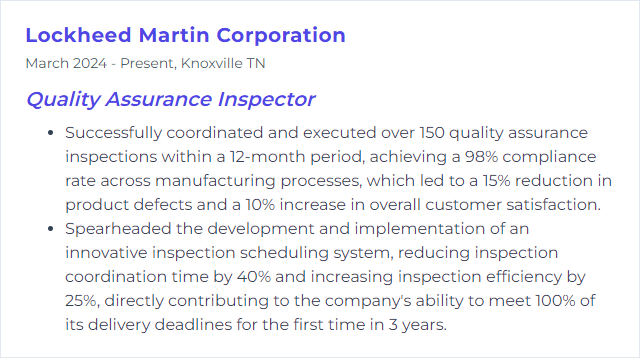
12. ASQ Certification
ASQ Certification refers to credentials granted by the American Society for Quality to individuals who demonstrate understanding and proficiency in specific areas of quality assurance through passing an exam, thereby recognizing their expertise and competence in quality control practices, standards, and principles relevant to roles such as a Quality Assurance Inspector.
Why It's Important
ASQ Certification is important for a Quality Assurance Inspector because it validates their expertise in quality principles and practices, demonstrates their commitment to the quality profession, and enhances their credibility and career prospects.
How to Improve ASQ Certification Skills
To improve your ASQ Certification as a Quality Assurance Inspector, focus on the following steps:
Understand the Body of Knowledge (BoK): Begin by thoroughly reviewing the specific BoK for your certification. ASQ provides detailed BoK for each certification on their official website.
Gain Practical Experience: Practical experience in quality assurance is crucial. Ensure you meet the experience requirements detailed by ASQ for your certification level.
Study and Training: Invest in study materials and training courses. ASQ offers various learning resources including books, courses, and webinars tailored to different certifications.
Join a Study Group: Collaborating with peers can enhance your understanding. ASQ forums and local ASQ sections can be a good place to find study groups.
Practice with Sample Exams: Regularly practicing with sample exams can help familiarize you with the exam format and identify areas needing improvement. ASQ provides sample exams for this purpose.
Stay Updated: Quality standards and practices evolve, so stay informed about the latest trends and updates in your field. Engaging with professional communities and reading relevant publications can help.
Apply for the Exam: Once prepared, apply for your certification exam through the ASQ website.
Continuous Improvement: After obtaining your certification, focus on continuous professional development to maintain and enhance your skills.
By following these steps and leveraging the resources provided by ASQ, you can significantly improve your ASQ Certification as a Quality Assurance Inspector.
How to Display ASQ Certification Skills on Your Resume
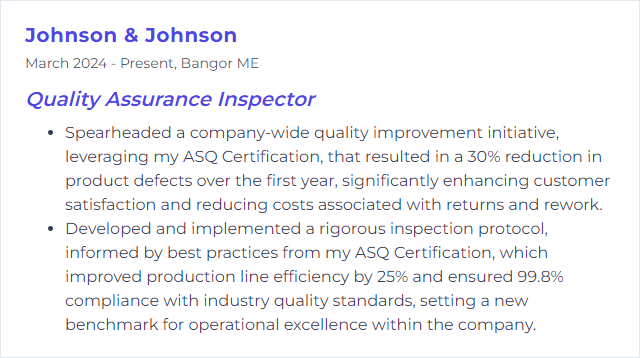