Top 12 Quality Auditor Skills to Put on Your Resume
In the competitive field of quality auditing, showcasing a robust set of skills on your resume can significantly enhance your employability and career prospects. Highlighting your top quality auditor skills is crucial in demonstrating your capability to ensure compliance, enhance efficiency, and drive continuous improvement in any organization.
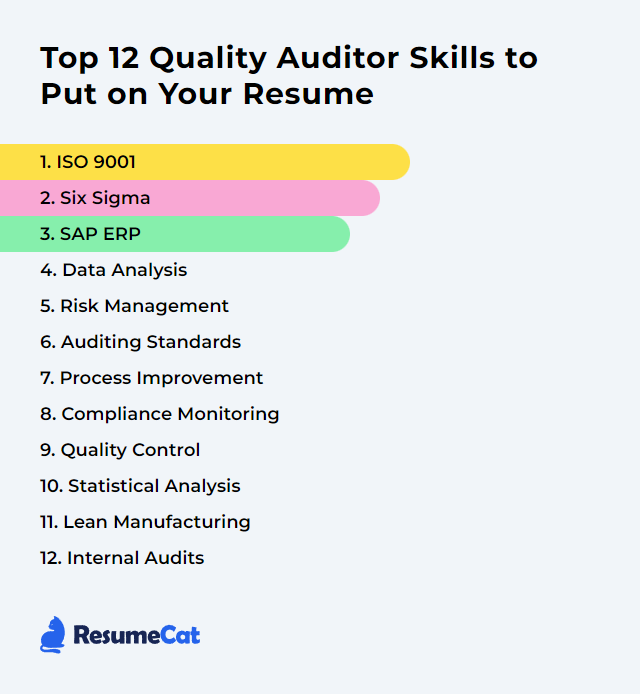
Quality Auditor Skills
- ISO 9001
- Six Sigma
- SAP ERP
- Data Analysis
- Risk Management
- Auditing Standards
- Process Improvement
- Compliance Monitoring
- Quality Control
- Statistical Analysis
- Lean Manufacturing
- Internal Audits
1. ISO 9001
ISO 9001 is an international standard specifying requirements for a quality management system (QMS). It helps organizations ensure they consistently provide products and services that meet customer and regulatory requirements. For a Quality Auditor, it serves as a framework to assess an organization's ability to consistently achieve these standards.
Why It's Important
ISO 9001 is important for a Quality Auditor because it provides a universally recognized framework for a quality management system (QMS), ensuring consistent quality in products and services, enhancing customer satisfaction, and facilitating continuous improvement.
How to Improve ISO 9001 Skills
Improving your ISO 9001 Quality Management System (QMS) involves continuous assessment and enhancement of your processes to better meet customer requirements and enhance satisfaction. As a Quality Auditor, focusing on the following areas can significantly contribute to the effectiveness of the QMS:
Conduct Regular Audits: Regular internal audits help identify non-conformities and areas for improvement. Utilize the findings to drive corrective actions. ISO 19011 provides guidelines for auditing management systems.
Management Review: Ensure that top management periodically reviews the QMS performance, including audit results, customer feedback, and process performance, to make informed decisions and set appropriate directions. ISO 9001 Clause 9.3 details the management review process requirements.
Employee Training and Competence: Continuously evaluate and improve the competence and awareness of employees regarding the QMS. Offer training and development opportunities to fill gaps. ISO 10015 can provide guidance on training and competence management.
Process Optimization: Use process mapping and performance data to identify inefficiencies and areas for optimization. Implement lean methodologies and continuous improvement practices like Six Sigma to enhance process efficiency and effectiveness.
Customer Feedback and Satisfaction: Establish mechanisms for collecting and analyzing customer feedback. Use this information to drive improvements in product quality and customer service. ISO 9001 Clause 9.1.2 focuses on monitoring customer satisfaction.
Risk Management: Implement a proactive approach to identifying and managing risks and opportunities associated with your QMS. ISO 31000 provides guidelines on risk management that can be applied within the QMS framework.
Supplier Management: Develop and maintain strong relationships with suppliers. Conduct supplier audits and evaluations to ensure they meet your quality requirements, contributing to the overall quality of your products and services.
Continual Improvement: Foster a culture of continual improvement within the organization. Encourage innovation and the proactive pursuit of opportunities to enhance the QMS. ISO 9001 Clause 10 outlines the specifics of continual improvement.
By focusing on these areas and leveraging relevant ISO guidelines and best practices, you can significantly improve your ISO 9001 QMS and drive greater value for your customers and stakeholders.
How to Display ISO 9001 Skills on Your Resume
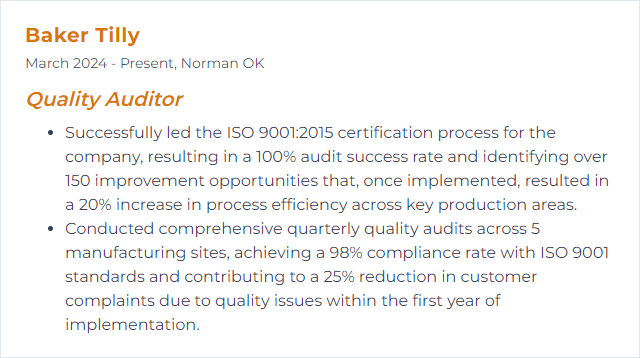
2. Six Sigma
Six Sigma is a data-driven methodology aimed at improving process quality by identifying and eliminating defects, minimizing variability, and reducing waste, thereby ensuring quality control and operational excellence which is critical for a Quality Auditor in ensuring organizational processes meet set standards.
Why It's Important
Six Sigma is important for a Quality Auditor as it provides a systematic and data-driven approach to identifying and eliminating defects, ensuring process improvement, and enhancing product or service quality, thereby facilitating operational excellence and customer satisfaction.
How to Improve Six Sigma Skills
Improving Six Sigma methodologies, especially from a Quality Auditor perspective, involves a continuous cycle of measuring, analyzing, and enhancing business processes to achieve near-perfect products and services. Here are concise steps and resources to guide a Quality Auditor in enhancing Six Sigma practices:
Continuous Education: Stay updated with the latest Six Sigma methodologies, tools, and trends through reputable sources. ASQ (American Society for Quality) and iSixSigma are excellent platforms for resources and training.
Utilize DMAIC Effectively: Ensure the Define, Measure, Analyze, Improve, Control (DMAIC) methodology is applied meticulously for problem-solving. ASQ’s DMAIC Model provides a comprehensive overview.
Leverage Technology: Use statistical analysis software and process mapping tools efficiently to analyze data and processes. Software like Minitab offers specialized tools for Six Sigma practitioners.
Benchmarking: Compare processes against industry best practices to identify areas for improvement. iSixSigma’s Benchmarking section offers insights and methodologies.
Root Cause Analysis: Master root cause analysis techniques to identify the underlying causes of defects or problems. ASQ’s Root Cause Analysis provides tools and techniques.
Soft Skills Development: Enhance communication, leadership, and project management skills to effectively implement Six Sigma projects and engage stakeholders. Project Management Institute (PMI) offers resources on project management skills.
Certification and Training: Obtain or maintain Six Sigma certification levels (Yellow Belt, Green Belt, Black Belt, Master Black Belt) through recognized programs. ASQ Certification is a globally recognized credential.
By focusing on these areas, a Quality Auditor can significantly contribute to the effectiveness and efficiency of Six Sigma methodologies within their organization.
How to Display Six Sigma Skills on Your Resume
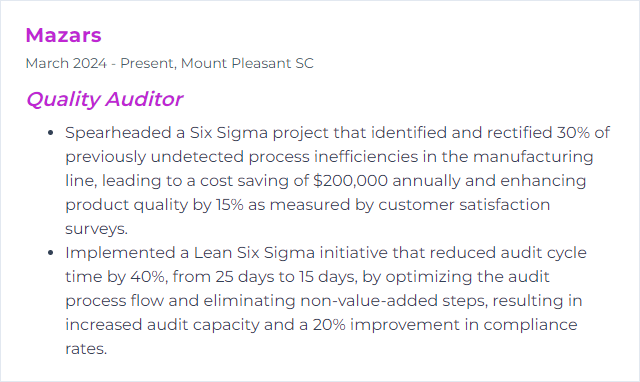
3. SAP ERP
SAP ERP is an enterprise resource planning software developed by SAP SE that integrates core business processes, such as finance, HR, operations, and supply chain, to streamline and improve the efficiency and quality of business operations, providing a centralized platform for data management and process standardization crucial for quality auditors in monitoring compliance and performance metrics.
Why It's Important
SAP ERP is important for a Quality Auditor because it provides a centralized system for managing and tracking all quality-related processes and documentation, ensuring compliance, standardization, and efficiency in quality audits.
How to Improve SAP ERP Skills
Improving SAP ERP, especially from a Quality Auditor's perspective, involves focusing on customization, integration, training, and continuous improvement. Here are concise strategies:
Customization: Tailor SAP ERP to your specific audit requirements to enhance functionality and efficiency. Leverage SAP's customization options to align with your auditing processes.
Integration: Ensure seamless integration with other tools and systems used for quality auditing. This enhances data accuracy and accessibility. SAP offers various integration options that can be leveraged for a cohesive system landscape.
Training: Invest in comprehensive training for the audit team on the latest SAP ERP features and best practices. SAP's Learning Hub provides resources and training modules tailored to different roles and skill levels.
Continuous Improvement: Regularly review and update your SAP ERP system to adapt to new quality standards and auditing requirements. Engage with SAP's User Groups for insights into improvements and updates.
By focusing on these areas, a Quality Auditor can significantly enhance the effectiveness and efficiency of SAP ERP in supporting quality audits.
How to Display SAP ERP Skills on Your Resume
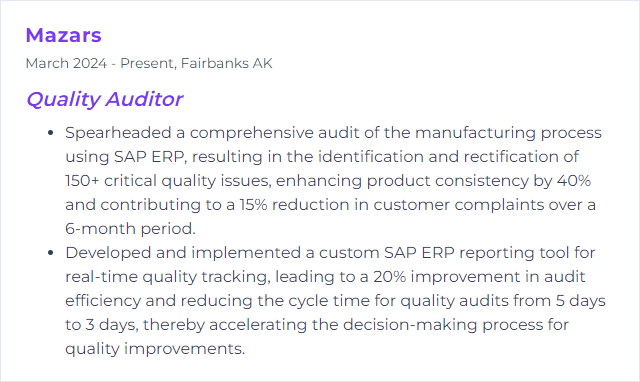
4. Data Analysis
Data analysis, in the context of a Quality Auditor, involves systematically examining data to identify trends, patterns, or anomalies to assess and improve the quality of processes, products, or services.
Why It's Important
Data analysis is crucial for a Quality Auditor as it enables the identification of patterns, trends, and anomalies in quality data. This facilitates informed decision-making, ensuring compliance, enhancing product quality, and driving continuous improvement initiatives.
How to Improve Data Analysis Skills
Improving data analysis, especially for a Quality Auditor, involves honing skills and leveraging tools that enhance accuracy, efficiency, and insightfulness. Here are concise steps:
Enhance Statistical Knowledge: Understand statistical methods and tools relevant to quality auditing. Khan Academy offers comprehensive lessons.
Master Data Analysis Software: Become proficient in software like Excel, Minitab, or R for sophisticated data analysis.
Learn Data Visualization: Master tools like Tableau or Power BI to communicate findings effectively.
Stay Updated: Follow industry trends and updates through platforms like Quality Digest to stay informed about best practices.
Continuous Learning: Enroll in courses from platforms like Coursera or edX to keep your skills sharp and updated.
Implement Quality Management Systems (QMS): Understand frameworks like ISO 9001 and utilize QMS software. Information can be found through ASQ.
Develop Critical Thinking: Practice critical thinking to interpret data accurately and make informed decisions. Resources like CriticalThinking.org can be helpful.
Engage in Peer Review: Engage with colleagues or online communities for peer review of your analysis to gain feedback and insights.
Focusing on these areas will significantly improve the quality and efficiency of data analysis for auditors.
How to Display Data Analysis Skills on Your Resume
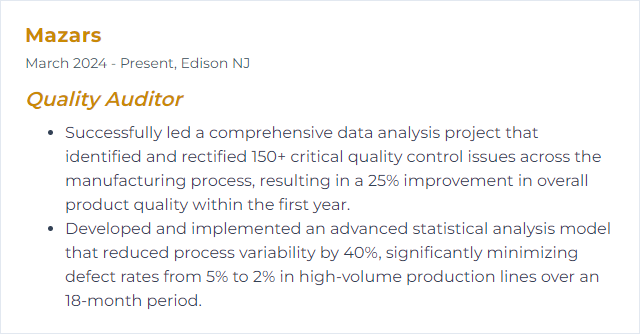
5. Risk Management
Risk management, in the context of a Quality Auditor, involves the systematic process of identifying, assessing, and prioritizing risks to quality, followed by the application of resources to minimize, monitor, and control the probability or impact of these risks.
Why It's Important
Risk Management is crucial for a Quality Auditor as it helps identify, assess, and prioritize potential risks, ensuring the organization's quality standards are met consistently and efficiently, while minimizing errors, enhancing compliance, and protecting its reputation.
How to Improve Risk Management Skills
Improving risk management, particularly from a Quality Auditor's perspective, involves a few key steps that focus on identifying, analyzing, and mitigating risks effectively. Here's a concise guide:
Identify Risks: Start by systematically identifying potential risks that could affect quality outcomes. This can involve reviewing historical data, conducting stakeholder interviews, and using tools like SWOT (Strengths, Weaknesses, Opportunities, Threats) analysis. Learn more about identifying risks.
Assess Risks: Once identified, evaluate the risks based on their likelihood and potential impact. This helps in prioritizing which risks need immediate attention. Techniques like Risk Matrix or FMEA (Failure Modes and Effects Analysis) can be useful. Read about risk assessment methods.
Implement Controls: Develop strategies to mitigate identified risks. This could involve process changes, quality controls, or implementing new policies. It's important to involve key stakeholders in this step to ensure the controls are practical and effective. Explore risk mitigation strategies.
Monitor and Review: Risk management is an ongoing process. Regularly monitor the effectiveness of implemented controls and review the risk management process to identify any new risks or changes in existing risks. Continuous improvement methodologies like PDCA (Plan-Do-Check-Act) can be applied here. Understand the continuous improvement process.
Communication and Documentation: Effective communication and documentation throughout the risk management process are crucial. This ensures transparency, facilitates better decision-making, and assists in compliance and audit trails. Review best practices for documentation and communication.
By following these steps and utilizing the resources linked, Quality Auditors can significantly improve risk management processes within their organizations.
How to Display Risk Management Skills on Your Resume
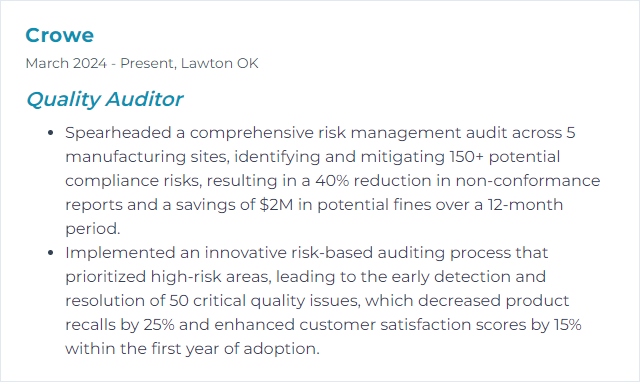
6. Auditing Standards
Auditing Standards are formal guidelines that dictate the procedures and principles auditors should follow during the audit process to ensure audits are performed efficiently, ethically, and consistently, thereby ensuring the quality and reliability of audit outcomes.
Why It's Important
Auditing Standards are crucial for Quality Auditors as they ensure consistency, reliability, and integrity in the auditing process, enabling auditors to effectively assess compliance, identify areas for improvement, and build stakeholder trust in the audit results.
How to Improve Auditing Standards Skills
Improving auditing standards, especially for a Quality Auditor, involves a multi-faceted approach focusing on continuous education, adherence to global standards, technology integration, and stakeholder engagement. Here’s a concise guide:
Continuous Education and Certification: Quality Auditors should pursue ongoing education and certifications to stay abreast of the latest auditing techniques, standards, and regulatory requirements. Organizations such as the American Society for Quality (ASQ) offer various certifications and training programs.
Adherence to Global Standards: Implement and follow internationally recognized auditing standards such as those outlined by the International Organization for Standardization (ISO), specifically ISO 19011, which provides guidelines for auditing management systems.
Technology Integration: Leverage new technologies for data analysis, risk assessment, and audit management. Tools and software that support data analytics can significantly enhance the efficiency and effectiveness of audits. Information on the latest in audit technology can be found through resources like ISACA, which focuses on IT governance.
Stakeholder Engagement: Engage actively with all stakeholders, including those being audited, to ensure transparency and understanding of the auditing process. This approach helps in building trust and cooperation, making the audit more effective.
Ethical Conduct and Independence: Maintain the highest levels of ethics and independence. The Institute of Internal Auditors (IIA) provides a Code of Ethics that serves as a fundamental resource for professionals in the field.
By focusing on these areas, Quality Auditors can significantly improve the standards of their audits, contributing to the overall integrity and effectiveness of quality management systems across industries.
How to Display Auditing Standards Skills on Your Resume
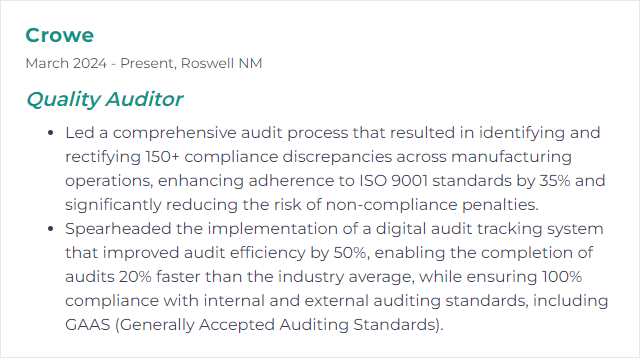
7. Process Improvement
Process Improvement is the systematic approach to enhancing the efficiency, effectiveness, and adaptability of an organization's processes, focusing on meeting or exceeding customer and quality standards, as identified and assessed by a Quality Auditor.
Why It's Important
Process improvement is crucial for a Quality Auditor as it enhances efficiency, reduces errors, and ensures compliance, directly contributing to higher product or service quality and customer satisfaction.
How to Improve Process Improvement Skills
To enhance Process Improvement as a Quality Auditor, focus on these key strategies:
Benchmarking: Compare your processes with those of leading organizations in your industry. Identify gaps and set realistic improvement targets. ASQ offers resources for understanding benchmarking in quality management.
Root Cause Analysis (RCA): Use RCA tools like the 5 Whys or Fishbone Diagram to dig deep into process failures, ensuring solutions address the true underlying issues. MindTools provides a guide on how to apply these techniques.
Continuous Improvement (CI): Adopt a CI mindset, encouraging ongoing small improvements. Familiarize yourself with methodologies like Kaizen for incremental changes. Lean Enterprise Institute has resources on lean thinking and continuous improvement.
Employee Training and Engagement: Ensure all team members are trained in quality principles and engaged in the process improvement journey. Their insights are invaluable. SHRM offers strategies for developing and engaging employees.
Utilize Technology: Leverage quality management software (QMS) for streamlining processes, data analysis, and maintaining documentation. Explore options that fit your organization's size and needs. Capterra lists and compares different QMS solutions.
Audit and Feedback: Regularly audit processes and provide constructive feedback. Use findings to refine and enhance quality improvement efforts. The Chartered Quality Institute has resources and guidelines for quality audits.
By focusing on these strategies and utilizing available resources, you can significantly improve the process improvement initiatives within your organization.
How to Display Process Improvement Skills on Your Resume
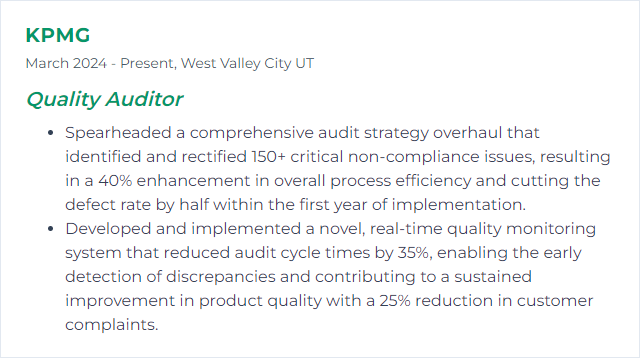
8. Compliance Monitoring
Compliance Monitoring, in the context of a Quality Auditor, refers to the systematic process of assessing and ensuring that organizational activities and outputs adhere to established standards, regulations, and internal policies.
Why It's Important
Compliance monitoring is crucial for a Quality Auditor as it ensures that organizational processes and operations adhere to established standards, regulations, and best practices, mitigating risks and ensuring quality, safety, and integrity.
How to Improve Compliance Monitoring Skills
Improving compliance monitoring, particularly for a Quality Auditor, involves a multifaceted approach focused on enhancing the effectiveness and efficiency of the audit process. Here are concise strategies:
Leverage Technology: Implement audit management software to automate routine tasks, ensuring more time is spent on critical analysis and less on administrative duties.
Risk-Based Auditing: Adopt a risk-based approach to focus resources on areas with the highest risk of non-compliance, ensuring more efficient use of auditing resources.
Continuous Training: Ensure auditors undergo continuous professional development to stay updated on the latest regulatory changes and auditing techniques.
Stakeholder Engagement: Engage regularly with internal and external stakeholders to understand their concerns and perspectives, which can enhance the relevance and focus of the compliance monitoring process.
Data Analytics: Utilize data analytics tools to analyze patterns and trends in compliance data, helping to predict areas of potential non-compliance before they become issues.
Benchmarking: Compare compliance performance against industry standards or peers to identify areas for improvement and adopt best practices. The American Society for Quality (ASQ) offers resources for benchmarking best practices.
By implementing these strategies, Quality Auditors can enhance the efficiency and effectiveness of compliance monitoring, ensuring that they are better equipped to identify and address compliance issues.
How to Display Compliance Monitoring Skills on Your Resume
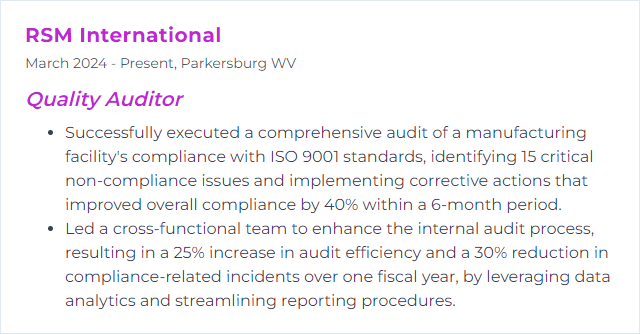
9. Quality Control
Quality Control (QC) is a process through which a business seeks to ensure that product quality is maintained or improved with either reduced or zero errors. For a Quality Auditor, it involves systematically inspecting, testing, and verifying that products and processes meet specified standards and requirements.
Why It's Important
Quality Control is crucial as it ensures products or services meet specific requirements and standards, maintaining customer satisfaction, reducing waste and costs, and enhancing the company's reputation and competitiveness. For a Quality Auditor, it is vital to identify non-conformities and improvement areas to uphold these standards consistently.
How to Improve Quality Control Skills
To improve Quality Control as a Quality Auditor, consider the following concise steps:
Understand Standards: Deeply understand the quality standards and regulations relevant to your industry. ISO and ASQ are key resources for standards and quality information.
Continuous Education: Engage in continuous education through Quality Auditing Courses to stay updated with the latest auditing techniques and quality control processes.
Implement a Quality Management System (QMS): A QMS like ISO 9001 helps establish a structured process for quality control and continuous improvement.
Use Technology: Leverage quality management software tools such as Intelex for efficient tracking, monitoring, and analyzing quality data.
Regular Audits and Feedback: Conduct regular internal and external audits to identify areas for improvement. Tools like AuditBoard can streamline this process. Encourage feedback from stakeholders to gain insights.
Root Cause Analysis (RCA): When issues arise, employ RCA techniques to address the underlying causes, not just symptoms. ASQ’s RCA resources can be a guide.
Benchmarking: Compare practices with leading companies in your industry. Benchmarking tools and resources, such as those offered by APQC, can provide valuable insights.
Focus on Training: Regularly train your team on the latest quality control techniques and tools. Training platforms like Coursera offer relevant courses.
Communication and Collaboration: Foster open communication and collaboration within your team and with external stakeholders to ensure everyone is aligned with quality objectives.
Continuous Improvement: Adopt a Kaizen or continuous improvement mindset, making small, incremental improvements over time. Resources on Kaizen provide strategies and techniques.
By following these steps and utilizing the recommended resources, you can significantly improve quality control processes in your role as a Quality Auditor.
How to Display Quality Control Skills on Your Resume
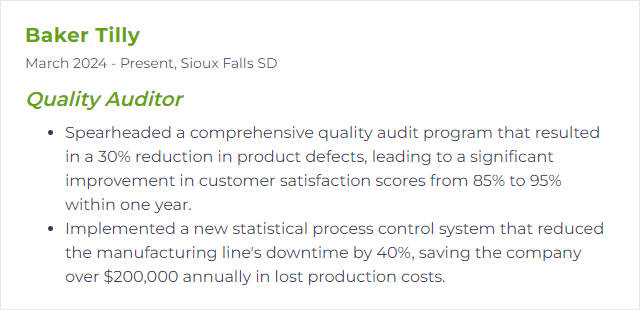
10. Statistical Analysis
Statistical analysis is the process of collecting, examining, interpreting, and presenting numerical data to identify trends, patterns, or insights, enabling a Quality Auditor to make evidence-based decisions and assessments regarding the quality and reliability of products or processes.
Why It's Important
Statistical analysis is crucial for a Quality Auditor as it enables the systematic examination of data to identify trends, variations, and outliers, ensuring the accuracy, reliability, and consistency of processes and products, thereby facilitating informed decision-making and continuous quality improvement.
How to Improve Statistical Analysis Skills
Improving statistical analysis, especially for a Quality Auditor, involves a few precise steps to ensure data accuracy, reliability, and relevance. Here's a very short and concise guide:
Enhance Data Quality: Ensure data collection processes are robust, minimizing errors. This involves validating data sources and using reliable data collection tools. Data Quality
Understand Statistical Methods: Deepen your understanding of statistical methods relevant to quality auditing, such as control charts, regression analysis, and hypothesis testing. Statistical Methods
Use Appropriate Software: Employ statistical analysis software tailored to quality control, like Minitab, SAS, or R, which offer advanced tools for detailed analysis. Minitab
Continuous Learning: Stay updated with the latest trends and advancements in statistical analysis through webinars, courses, and certifications from recognized institutions. Coursera - Statistics with Python
Practical Application: Practice applying statistical methods to real-world scenarios to understand their implications and results better. This involves analyzing case studies or historical data to predict future trends. Case Studies
Peer Review: Regularly engage with peers for review and feedback on your analysis to identify any biases or errors. Peer Review Importance
Ethics and Integrity: Uphold high standards of ethics and integrity in data handling and analysis, ensuring transparency and objectivity. Ethical Guidelines
By focusing on these areas, a Quality Auditor can significantly enhance their statistical analysis skills, leading to better decision-making and quality improvement initiatives.
How to Display Statistical Analysis Skills on Your Resume
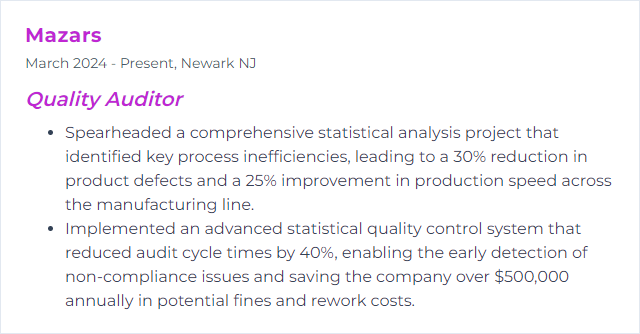
11. Lean Manufacturing
Lean Manufacturing is a systematic approach to minimize waste within a manufacturing system while simultaneously maximizing productivity. For a Quality Auditor, it focuses on enhancing quality and efficiency by evaluating processes, identifying non-value-added activities, and implementing continuous improvement strategies.
Why It's Important
Lean Manufacturing is important because it helps in identifying and eliminating waste in the production process, leading to improved efficiency, higher quality products, and reduced costs, which are critical aspects for a Quality Auditor to ensure the organization's processes are optimized and standards are met.
How to Improve Lean Manufacturing Skills
Improving Lean Manufacturing involves streamlining processes, eliminating waste, and enhancing quality while focusing on customer value. As a Quality Auditor, your role is pivotal in identifying areas for improvement, ensuring adherence to lean principles, and promoting a culture of continuous improvement. Here are concise strategies to enhance Lean Manufacturing:
Continuous Learning and Training: Invest in regular training and workshops for all employees, including lean principles, quality standards, and problem-solving techniques. Lean Enterprise Institute and ASQ (American Society for Quality) offer resources and training materials.
Implement 5S Methodology: Organize and maintain a clean, efficient workplace to reduce waste and improve productivity. The 5S steps are Sort, Set in order, Shine, Standardize, and Sustain. Graphic Products' 5S System Guide provides a detailed overview.
Value Stream Mapping: Analyze and design the flow of materials and information required to bring a product to a customer. Identify and eliminate waste in the process. The Lean Enterprise Institute's guide on Value Stream Mapping can be a useful resource.
Kaizen (Continuous Improvement): Promote a culture of continuous improvement by encouraging employees to identify inefficiencies and suggest improvements. Small, incremental changes can lead to significant benefits. The Kaizen Institute offers insights and case studies.
Root Cause Analysis: When quality issues arise, use tools like the 5 Whys or Fishbone Diagram to investigate and address the underlying causes, rather than just treating symptoms. ASQ's Root Cause Analysis Tools provide a good starting point.
Implement Quality Circles: Encourage the formation of small groups that regularly meet to discuss work-related problems and potential improvements. This fosters teamwork and ownership. ASQ's guide to Quality Circles explains their benefits and implementation.
Utilize Pull Systems and Kanban: Align production with demand to minimize waste and reduce inventory. Kanban boards help visualize work, limit work-in-progress, and ensure smooth workflow. LeanKit's Introduction to Kanban offers a comprehensive overview.
By focusing on these strategies and leveraging available resources, a Quality Auditor can significantly contribute to the improvement of Lean Manufacturing in their organization.
How to Display Lean Manufacturing Skills on Your Resume
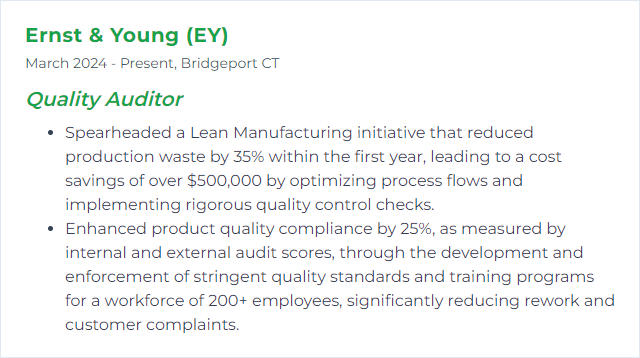
12. Internal Audits
Internal audits are systematic evaluations conducted within an organization by a designated auditor to assess the effectiveness and efficiency of its operations, specifically focusing on quality management systems to ensure compliance with established standards, identify areas for improvement, and facilitate continuous quality enhancement.
Why It's Important
Internal audits are crucial for ensuring that an organization's processes and systems are functioning effectively and efficiently, identifying areas for improvement, and verifying compliance with relevant quality standards, thereby supporting continuous improvement and sustaining quality assurance.
How to Improve Internal Audits Skills
Improving internal audits, especially for a Quality Auditor, involves a continuous process of assessment, feedback, and refinement. Here are concise strategies:
Plan Effectively: Develop a clear, strategic plan that aligns with the organization’s goals. Use ISO 19011:2018 guidelines for structuring your audit program.
Stay Updated: Keep abreast of the latest quality management standards and auditing techniques to ensure relevance and efficiency.
Engage and Train: Ensure all team members are well-trained and understand the importance of audits. The ASQ offers training resources for ongoing learning.
Use Technology: Implement audit management software to streamline processes, improve accuracy, and facilitate data analysis. Tools like AuditBoard can enhance efficiency.
Communicate Effectively: Maintain open lines of communication with all stakeholders. This involves clear, timely, and constructive feedback before, during, and after the audit.
Continuous Improvement: Adopt a Kaizen approach to continuous improvement, using audit findings to drive process enhancements.
Benchmarking: Compare your audit practices and outcomes with those of leading organizations in your sector. Resources like Benchmarking Reports by The IIA can provide valuable insights.
By focusing on these key areas, Quality Auditors can significantly enhance the effectiveness and value of internal audits within their organizations.
How to Display Internal Audits Skills on Your Resume
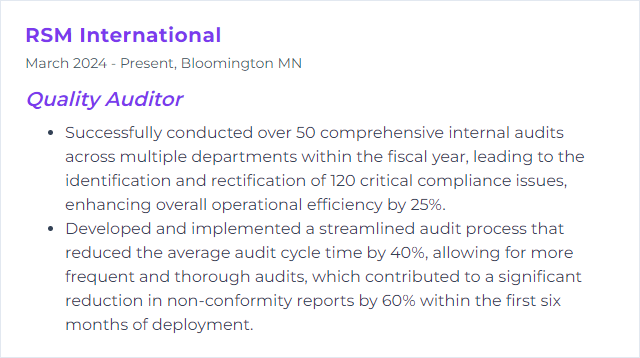