Top 12 Plant Operator Skills to Put on Your Resume
In today's competitive job market, standing out as a plant operator demands showcasing a unique set of skills on your resume that reflects your expertise and readiness for the challenges of the role. Highlighting the top skills not only demonstrates your proficiency in operating machinery and equipment but also your commitment to safety, efficiency, and teamwork, making you a compelling candidate for potential employers.
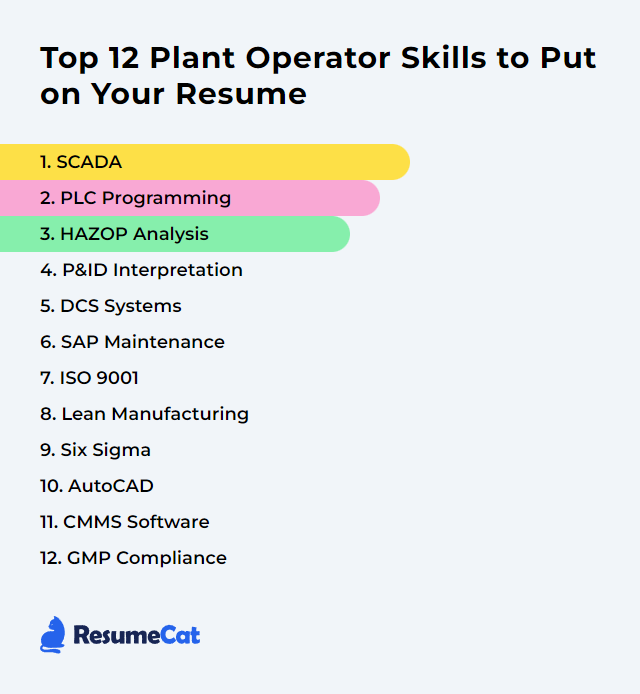
Plant Operator Skills
- SCADA
- PLC Programming
- HAZOP Analysis
- P&ID Interpretation
- DCS Systems
- SAP Maintenance
- ISO 9001
- Lean Manufacturing
- Six Sigma
- AutoCAD
- CMMS Software
- GMP Compliance
1. SCADA
SCADA (Supervisory Control and Data Acquisition) is a system used by plant operators to monitor and control industrial processes remotely, allowing for real-time data collection, process visualization, and control of machinery and processes.
Why It's Important
SCADA (Supervisory Control and Data Acquisition) is crucial for Plant Operators because it enables real-time monitoring and control over plant operations, ensuring efficiency, safety, and minimal downtime.
How to Improve SCADA Skills
Improving SCADA (Supervisory Control and Data Acquisition) systems for plant operators involves enhancing real-time monitoring, control functionality, system security, and data analysis capabilities. Here's a concise guide:
Implement Robust Cybersecurity Measures: Protect your SCADA system from cyber threats by employing firewalls, intrusion detection systems, and regular security audits. The National Institute of Standards and Technology (NIST) offers guidelines for industrial control system security.
Upgrade to High-Performance HMI (Human-Machine Interface): Utilize high-performance HMI principles to design clearer, more intuitive interfaces that improve operator decision-making. ISA (International Society of Automation) provides resources on effective HMI design practices.
Ensure Redundancy and Failover Capabilities: Enhance system reliability by implementing redundancy for critical components and establishing failover mechanisms. This approach minimizes downtime and data loss. Schneider Electric discusses strategies for achieving high availability.
Integrate Advanced Analytics and AI: Leverage data analytics, machine learning, and artificial intelligence to predict maintenance needs, optimize processes, and improve efficiency. Companies like Siemens offer SCADA systems with integrated analytics capabilities.
Conduct Regular Training and Simulations: Regular training sessions and simulation exercises for operators ensure they are proficient with the SCADA system and prepared for emergency scenarios. OSIsoft PI System provides resources for operational intelligence that can support training efforts.
Update and Maintain Regularly: Keep the SCADA software and hardware components up to date with the latest patches and updates to ensure optimal performance and security. Regular maintenance checks can identify and rectify potential issues before they escalate.
By focusing on these areas, plant operators can significantly improve the efficiency, reliability, and security of their SCADA systems, ensuring smoother operations and better decision-making.
How to Display SCADA Skills on Your Resume
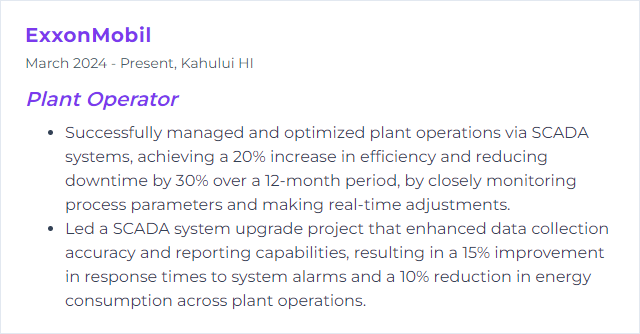
2. PLC Programming
PLC programming involves creating instructions for Programmable Logic Controllers (PLCs) to automate and control machinery and processes in industrial settings, ensuring efficient and safe operations.
Why It's Important
PLC programming is crucial for plant operators because it allows for the automation of machinery and processes, ensuring efficient, precise, and reliable operation of the plant, which minimizes human error and enhances safety and productivity.
How to Improve PLC Programming Skills
Improving PLC programming, especially for a Plant Operator, involves enhancing efficiency, reliability, and safety in automation processes. Here are concise strategies:
Understand Basics Thoroughly: Start with a strong foundation in PLC basics, including logic operations, ladder logic, and programming languages. PLC Academy offers a good starting point.
Learn from Examples: Study and dissect existing PLC programs to understand practical applications and best practices. PLCdev provides ample resources and example projects.
Continual Learning: Stay updated with the latest in PLC technology and programming techniques. Online courses from platforms like Udemy and LinkedIn Learning can be valuable.
Practice Regularly: Apply your knowledge by working on real-world problems or simulated environments. Tools like RSLogix 500 offer a practical platform for practice.
Optimize and Debug: Learn to efficiently troubleshoot and optimize PLC programs to improve performance. Control Engineering has useful tips on troubleshooting.
Safety First: Always prioritize safety in your programming practices. Understanding safety standards is crucial. ISA provides resources on automation safety standards.
Community Engagement: Join forums and groups like PLCTalk for peer support, advice, and sharing knowledge.
Enhancing your PLC programming skills is a continuous process that combines learning, practice, and engagement with the automation community.
How to Display PLC Programming Skills on Your Resume
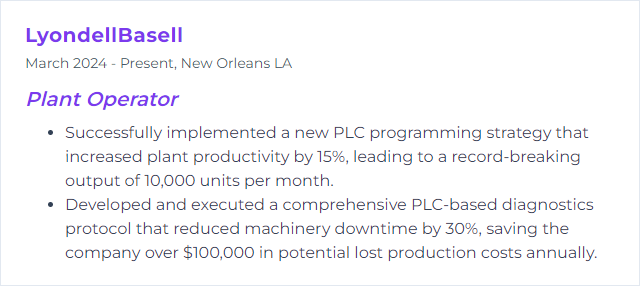
3. HAZOP Analysis
HAZOP (Hazard and Operability Study) is a systematic method used to identify and evaluate risks to personnel or equipment within a plant. It involves analyzing potential deviations from normal operations that could lead to hazards or operational problems. For a plant operator, HAZOP helps in understanding and mitigating risks to ensure safe and efficient plant operations.
Why It's Important
HAZOP (Hazard and Operability) analysis is important for a Plant Operator because it systematically identifies and evaluates potential hazards and operational issues in a plant, ensuring safety, minimizing risks, and optimizing performance.
How to Improve HAZOP Analysis Skills
Improving Hazard and Operability (HAZOP) Analysis involves enhancing the systematic examination of a process or operation to identify potential hazards and operational problems. For a Plant Operator, focusing on the following strategies can significantly enhance HAZOP Analysis:
Preparation: Thoroughly understand the process by reviewing process flow diagrams (PFDs), piping and instrumentation diagrams (P&IDs), and standard operating procedures (SOPs). Chemical Safety Board offers resources on process safety that can be useful.
Training: Ensure that all team members, including operators, are adequately trained in HAZOP methodology. Online courses or workshops provided by institutions like AIChE can be beneficial.
Cross-Functional Teams: Include team members from various disciplines (operations, maintenance, engineering, etc.) to provide diverse perspectives. This IChemE guide offers insights into forming effective HAZOP teams.
Use of Software: Leverage HAZOP software tools for systematic analysis and documentation. Tools like PHAWorks RA Edition from Primatech can improve the efficiency of HAZOP studies.
Regular Reviews: Conduct regular HAZOP reviews to account for changes in operations, processes, or technology. The Center for Chemical Process Safety (CCPS) provides guidelines for effective process safety management.
Action Tracking: Ensure that recommendations from HAZOP studies are tracked and implemented. Software solutions like ActionTrack can help in managing and tracking the actions arising from HAZOP studies.
By focusing on these strategies, Plant Operators can significantly improve the effectiveness of HAZOP Analysis in identifying and mitigating potential hazards in plant operations.
How to Display HAZOP Analysis Skills on Your Resume
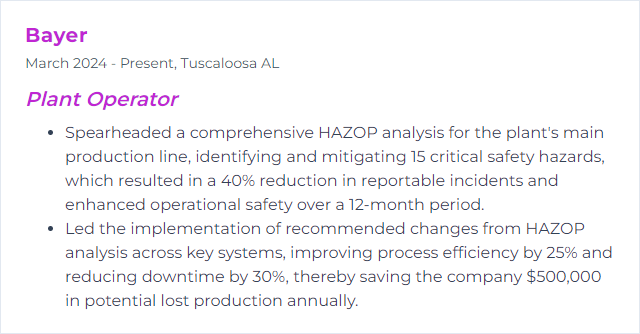
4. P&ID Interpretation
P&ID Interpretation for a Plant Operator involves understanding and reading Process and Instrumentation Diagrams (P&IDs) to visually grasp the process flow, equipment layout, and control schemes of a plant, enabling effective operation, monitoring, and troubleshooting of the facility.
Why It's Important
P&ID interpretation is crucial for a Plant Operator as it ensures accurate understanding of the plant’s process flow and equipment layout, enabling safe, efficient operation and troubleshooting of the facility.
How to Improve P&ID Interpretation Skills
Improving P&ID (Piping and Instrumentation Diagram) interpretation skills for a plant operator involves understanding symbols, lines, and notations commonly used in these diagrams. Here’s a very short and concise guide:
Familiarize with Symbols: Start by learning the basic symbols for equipment, valves, pumps, and instrumentation. Engineering.com offers resources and articles that can help you recognize and understand these symbols.
Understand Line Types: Know the difference between solid, dashed, and dotted lines to distinguish between main process lines, secondary lines, and connections. The ISA (International Society of Automation) provides standards and guidelines that can deepen your understanding.
Study Flow Direction: Practice tracing the flow direction through P&IDs to understand the process flow, which is crucial for operating and troubleshooting plant operations.
Learn Tagging and Labeling: Each component in a P&ID is tagged with a unique identifier. Understanding the tagging system is key for locating equipment and understanding their function within the system.
Use Real Diagrams: Apply your knowledge by practicing with real P&ID diagrams from your workplace. This hands-on approach is invaluable.
Continuous Learning: P&ID interpretation is a skill that improves with experience and continuous learning. Websites like Coursera and edX offer courses related to engineering and plant operations that can enhance your skills further.
By systematically studying each aspect of P&IDs and applying your knowledge in a practical context, you’ll become proficient in interpreting these diagrams, which is crucial for effective plant operation.
How to Display P&ID Interpretation Skills on Your Resume
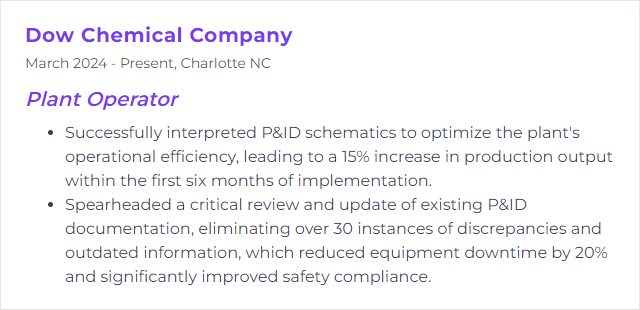
5. DCS Systems
A Distributed Control System (DCS) is a computerized control system used in industrial environments, such as manufacturing plants and refineries, to monitor and control the processes and operations automatically. For a Plant Operator, it serves as the central interface for controlling machinery and processes, ensuring efficiency, stability, and safety.
Why It's Important
DCS (Distributed Control Systems) are crucial for plant operators because they provide centralized control and monitoring of plant operations, enhancing safety, efficiency, and process optimization. This leads to improved productivity and reduced downtime.
How to Improve DCS Systems Skills
Improving Distributed Control Systems (DCS) in a plant setting involves several key steps aimed at enhancing performance, reliability, and user experience for plant operators. Here's a concise guide:
Upgrade Hardware and Software: Regularly update DCS hardware and software to leverage the latest technologies for better efficiency and features. Siemens and Honeywell offer advanced solutions.
Enhance Cybersecurity: Implement robust cybersecurity measures to protect the DCS from external threats. This includes firewalls, intrusion detection systems, and regular security audits. ISA provides standards and guidance.
Optimize Operator Interfaces: Design user-friendly operator interfaces for efficient monitoring and control. This involves intuitive dashboard layouts and ergonomic considerations. Emerson discusses interface optimization.
Implement Advanced Process Control (APC): Use APC techniques to improve process efficiency and stability. This can include model predictive control and fuzzy logic. Rockwell Automation offers APC solutions.
Ensure Regular Training and Support: Provide continuous training and support to operators on the latest DCS features and best practices. This ensures they can fully leverage the system's capabilities. Yokogawa offers comprehensive training programs.
Conduct Performance Analytics: Utilize DCS data analytics tools to monitor system performance and identify areas for improvement. This can help in predictive maintenance and optimization. ABB has analytics tools for this purpose.
By focusing on these areas, plant operators can significantly enhance the efficiency, security, and usability of DCS systems, leading to improved plant performance and safety.
How to Display DCS Systems Skills on Your Resume
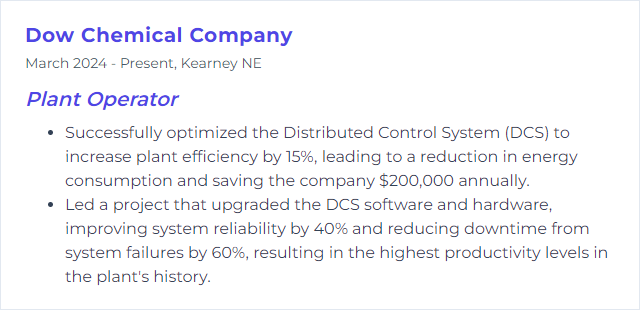
6. SAP Maintenance
SAP Maintenance, in the context of a Plant Operator, refers to the systematic process of scheduling, executing, and recording maintenance tasks and operations within a plant or manufacturing facility using SAP software to ensure machinery and equipment are operating efficiently and reliably.
Why It's Important
SAP Maintenance is crucial for a Plant Operator as it ensures the smooth and efficient operation of plant systems and machinery, minimizes downtime through predictive and preventive maintenance, and optimizes asset life cycles and productivity, thereby safeguarding production continuity and reducing operational costs.
How to Improve SAP Maintenance Skills
Improving SAP Maintenance, especially for a Plant Operator, involves streamlining processes, enhancing system performance, and ensuring data accuracy. Here's a concise guide:
Regular System Audits: Conduct periodic audits to identify inefficiencies or errors in the SAP maintenance system. This helps in optimizing processes and improving data accuracy.
Training and Support: Invest in comprehensive training for staff to ensure they are proficient in using SAP Maintenance modules. SAP's official training and certification programs can be valuable.
Data Quality Management: Implement stringent data entry and validation rules to maintain the integrity of maintenance records. SAP's Master Data Governance can help streamline this process.
Automate Processes: Utilize SAP's automation capabilities to streamline maintenance tasks, such as work order creation, scheduling, and notification. This reduces manual errors and saves time. Explore SAP's Intelligent Robotic Process Automation for options.
Regular System Updates: Ensure your SAP system is always up to date with the latest patches and upgrades. This not only secures the system but also ensures you're leveraging the latest features and efficiencies.
Customize Reports for Decision Making: Customize SAP reports to provide relevant insights for maintenance decision-making. Utilizing SAP's Business Intelligence tools can facilitate this.
Feedback Loop: Establish a feedback mechanism from users to continuously identify areas for improvement and adapt the system accordingly.
Leverage Mobile Solutions: Integrate SAP Maintenance with mobile solutions to enable real-time data entry and access, enhancing flexibility and efficiency. Check SAP's Mobile Services for solutions.
Collaborate with SAP Experts: Engage with SAP consultants or partners for specialized advice on optimizing your maintenance processes. The SAP Partner Finder can help locate experts.
Predictive Maintenance: Implement SAP's predictive maintenance solutions to foresee and address maintenance needs before issues escalate, thereby reducing downtime. SAP's Predictive Maintenance and Service solutions offer insights.
By focusing on these areas, Plant Operators can significantly improve the efficiency and effectiveness of their SAP Maintenance systems.
How to Display SAP Maintenance Skills on Your Resume
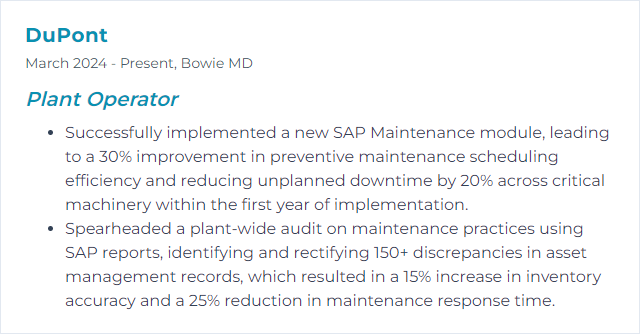
7. ISO 9001
ISO 9001 is an international standard that specifies requirements for a quality management system (QMS). For a Plant Operator, it ensures consistent quality in operations, meeting customer and regulatory requirements, and continuous improvement in processes and efficiency.
Why It's Important
ISO 9001 is important for a Plant Operator as it ensures consistent quality in operations, enhances efficiency, and improves customer satisfaction by standardizing processes and implementing continuous improvement practices.
How to Improve ISO 9001 Skills
Improving ISO 9001 for a Plant Operator involves focusing on enhancing quality management systems, increasing employee engagement, and continuously monitoring and optimizing processes. Here’s how to do it concisely:
Engage Employees: Ensure that all plant operators and staff are fully trained on ISO 9001 standards. Engaging them through training and involvement in quality improvement initiatives fosters a culture of quality. ISO's page on training offers insights on standard-specific training.
Process Optimization: Regularly review and optimize plant operations to increase efficiency and reduce errors. This involves applying Lean principles and Six Sigma methodologies to eliminate waste and reduce variability.
Use of Quality Management Tools: Implement quality management tools such as PDCA (Plan-Do-Check-Act), Root Cause Analysis, and Risk Management frameworks to identify areas for improvement and apply corrective measures efficiently. ASQ’s Quality Resources is a good starting point.
Customer Feedback: Actively seek and incorporate customer feedback to understand their requirements better and improve product quality. This aligns with ISO 9001’s emphasis on customer satisfaction.
Internal Audits: Conduct regular internal audits to ensure compliance with ISO 9001 standards and to identify areas for improvement. ISO 19011:2018 guidelines for auditing management systems can guide you through this.
Management Review: Ensure that top management is involved in the review of the quality management system, focusing on assessing its effectiveness and aligning it with the organization’s strategic direction.
Continuous Improvement: Adopt a culture of continuous improvement through the application of the Kaizen method, focusing on small, incremental changes to improve efficiency and quality.
By focusing on these areas, a Plant Operator can significantly improve their ISO 9001 compliance, leading to enhanced operational efficiency, reduced costs, and higher customer satisfaction.
How to Display ISO 9001 Skills on Your Resume
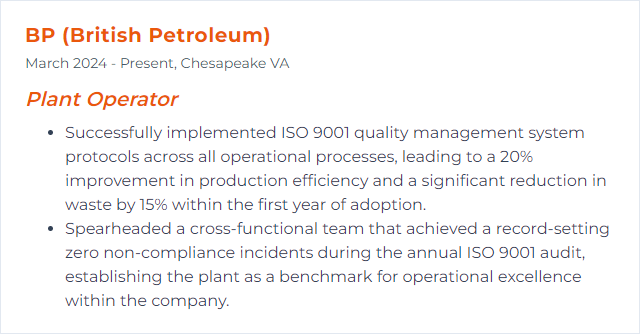
8. Lean Manufacturing
Lean Manufacturing is a systematic approach to minimizing waste within manufacturing systems while maximizing productivity, aimed at improving overall efficiency and effectiveness for plant operators.
Why It's Important
Lean Manufacturing is important for a Plant Operator as it enhances efficiency by reducing waste, improving product quality, shortening production times, and lowering costs, directly contributing to increased profitability and competitiveness.
How to Improve Lean Manufacturing Skills
Improving Lean Manufacturing, especially for a Plant Operator, involves focusing on reducing waste and optimizing processes for efficiency. Here are concise steps with relevant resources:
Value Stream Mapping: Understand and map out all processes to identify value-added and non-value-added steps. Value Stream Mapping Guide.
5S Methodology: Implement the 5S (Sort, Set in order, Shine, Standardize, Sustain) to organize the workplace for efficiency and effectiveness. 5S Explained.
Continuous Improvement (Kaizen): Foster a culture of continuous improvement by encouraging suggestions from all employees and implementing small, incremental changes. Kaizen Guide.
Jidoka (Autonomation): Implement automation with a human touch to stop production when defects are detected, preventing waste. Jidoka Explanation.
Just-In-Time (JIT) Production: Reduce inventory waste by producing just what is needed, when it's needed. Just-In-Time Principles.
Standard Work: Create standard operating procedures for tasks to ensure consistency and efficiency. Standard Work Basics.
Employee Involvement: Engage workers in decision-making and problem-solving to utilize their knowledge and skills fully. Employee Involvement.
Root Cause Analysis: Use tools like the 5 Whys to identify the root cause of problems and prevent recurrence. 5 Whys Technique.
By integrating these lean principles and tools, a Plant Operator can significantly improve manufacturing efficiency, reduce waste, and increase productivity.
How to Display Lean Manufacturing Skills on Your Resume
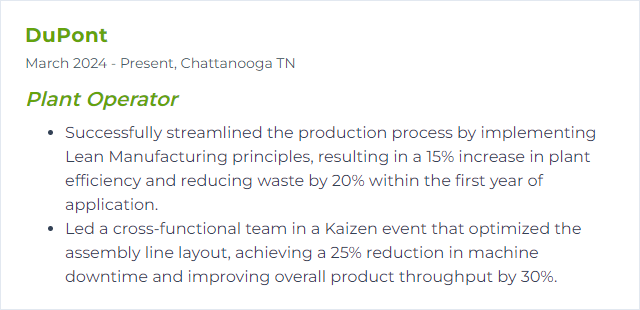
9. Six Sigma
Six Sigma is a data-driven methodology aimed at reducing defects and improving quality in processes, including those in manufacturing and plant operations, by identifying and eliminating causes of errors or variations.
Why It's Important
Six Sigma is important for a Plant Operator because it provides a systematic approach to reducing errors, improving process efficiency, and enhancing productivity, directly contributing to higher quality products and cost savings for the facility.
How to Improve Six Sigma Skills
Improving Six Sigma as a Plant Operator involves focusing on process improvement and variability reduction. Here are concise steps with external resources for further exploration:
Understand the Basics: Familiarize yourself with the Six Sigma principles and methodologies. ASQ's Six Sigma page offers a comprehensive overview.
Identify Key Processes: Pinpoint critical processes that influence product quality and operational efficiency. Use process mapping to visualize these. Lucidchart’s guide on process mapping can help.
Collect and Analyze Data: Use data collection and analysis tools to identify sources of variation and defects. Minitab offers resources tailored for Six Sigma projects.
Implement Lean Principles: Incorporate lean manufacturing techniques to eliminate waste and streamline operations. Lean Enterprise Institute provides insights into lean principles.
Engage in Continuous Learning: Stay informed about the latest in Six Sigma methodologies through continuous education. Six Sigma Online offers courses and certifications.
Apply DMAIC or DMADV: Use these structured Six Sigma methodologies for process improvement (DMAIC) or new process creation (DMADV). iSixSigma provides detailed explanations and guides.
Foster a Culture of Quality: Encourage a team environment focused on quality improvement. Smartsheet’s guide on quality management can offer strategies.
Utilize Technology and Software: Implement Six Sigma software tools for better data analysis and project management. Quality Digest discusses choosing suitable software.
By following these steps and utilizing the provided resources, a Plant Operator can effectively improve Six Sigma processes, leading to enhanced quality, efficiency, and customer satisfaction.
How to Display Six Sigma Skills on Your Resume
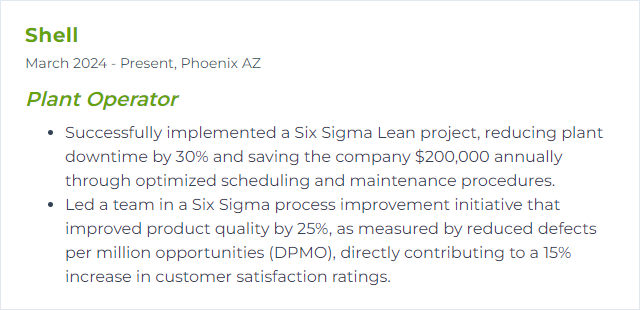
10. AutoCAD
AutoCAD is a computer-aided design (CAD) software used for creating precise 2D and 3D drawings and models, including plant layouts, machinery designs, and process flow diagrams, essential for plant operators in planning, visualizing, and optimizing plant operations.
Why It's Important
AutoCAD is important for a Plant Operator as it enables precise design and layout planning of plant systems, ensuring efficient operation, maintenance, and compliance with safety standards.
How to Improve AutoCAD Skills
To enhance your AutoCAD skills for better performance as a Plant Operator, focus on the following concise strategies:
Learn the Basics Thoroughly: Start with Autodesk's official tutorials to understand fundamental operations, commands, and shortcuts.
Customize Your Workspace: Tailor your AutoCAD interface and toolsets for efficiency in plant operations design. Autodesk provides a guide on customization.
Master 3D Modeling: For plant design, 3D modeling skills are crucial. Improve them through dedicated 3D tutorials.
Utilize AutoCAD Plant 3D: Specifically designed for plant design, AutoCAD Plant 3D offers tools tailored to plant operators' needs.
Learn from Projects and Templates: Explore and learn from existing projects and templates. Autodesk's project manager guide can help manage these resources effectively.
Stay Updated: Keep your skills and software up-to-date. Autodesk's what's new page keeps you informed of the latest features and updates.
Join Forums and Communities: Engage with other professionals in forums such as the Autodesk AutoCAD forums to exchange tips and get advice.
Practice Regularly: Consistent practice is key to improving your proficiency. Set aside regular time for practicing your skills on new projects or through challenges.
By focusing on these areas and leveraging the resources provided, you can significantly improve your AutoCAD skills in the context of plant operations.
How to Display AutoCAD Skills on Your Resume
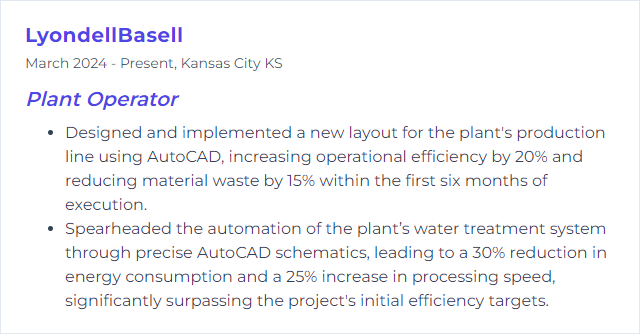
11. CMMS Software
CMMS Software, short for Computerized Maintenance Management System software, is a digital tool used by plant operators to schedule, track, and manage maintenance activities and assets, ensuring optimal equipment performance and minimizing downtime.
Why It's Important
CMMS (Computerized Maintenance Management System) software is important for a Plant Operator because it streamlines maintenance operations, improves asset management, reduces downtime, and enhances decision-making by providing real-time data and insights on equipment health, maintenance schedules, and inventory levels. This leads to increased efficiency, reduced costs, and extended equipment lifespan.
How to Improve CMMS Software Skills
Improving CMMS (Computerized Maintenance Management System) software for a plant operator involves enhancing usability, functionality, and integration capabilities. Here’s a concise guide:
User-Friendly Interface: Simplify the user interface for ease of navigation and operation. This includes clear menus, intuitive design, and mobile compatibility. Nielsen Norman Group offers principles on creating user-friendly interfaces.
Customization and Scalability: Allow customization of features such as dashboards, reports, and alerts to meet specific plant needs. Ensure the software can scale with the growth of the operation. Gartner discusses the importance of software customization.
Integration Capabilities: Enable integration with other systems (e.g., ERP, IoT devices) for seamless data flow and real-time monitoring. IBM provides insights into the benefits of system integration.
Training and Support: Offer comprehensive training materials and responsive customer support to ensure users can maximize the software's potential. TechSmith shares tips on creating effective training materials.
Predictive Maintenance: Incorporate predictive maintenance capabilities using AI and machine learning to forecast equipment failures before they occur. Forbes highlights the importance of predictive maintenance in manufacturing.
Regulatory Compliance: Ensure the software helps in maintaining compliance with industry regulations by keeping records and reports easily accessible and up-to-date. Environmental Protection Agency (EPA) provides resources on environmental compliance.
Feedback Loop: Implement a system for users to easily submit feedback and request features, ensuring the software evolves according to user needs. Harvard Business Review discusses the power of customer feedback.
By focusing on these areas, CMMS software can become more efficient, user-friendly, and effective in supporting plant operators in their maintenance management tasks.
How to Display CMMS Software Skills on Your Resume
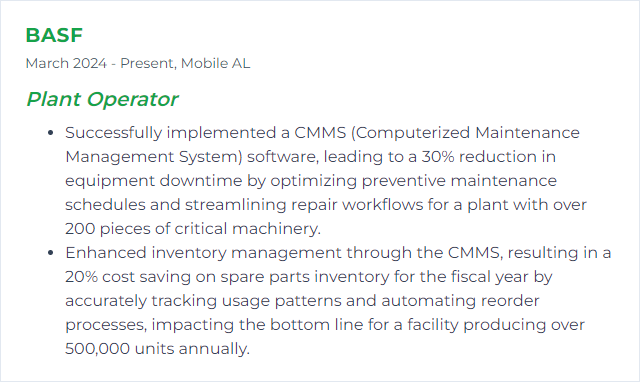
12. GMP Compliance
GMP Compliance, in regard to a Plant Operator, refers to the adherence to Good Manufacturing Practice regulations, ensuring products are consistently produced and controlled according to quality standards. This involves following precise guidelines to minimize risks involved in production that cannot be eliminated through testing the final product.
Why It's Important
GMP (Good Manufacturing Practice) compliance is crucial for plant operators as it ensures the consistent production and quality control of products, minimizes risks related to contamination, mix-ups, and errors, and protects consumer safety and confidence in the product.
How to Improve GMP Compliance Skills
Improving GMP (Good Manufacturing Practice) compliance as a Plant Operator involves several key steps aimed at ensuring that products are consistently produced and controlled according to quality standards. Here's a concise guide:
Understand GMP Regulations: Familiarize yourself with the specific GMP regulations applicable to your sector. Regulatory agencies like the FDA in the U.S. provide extensive resources.
Regular Training: Ensure all staff undergo regular, up-to-date GMP training. This includes understanding the importance of hygiene, documentation, and process adherence.
Maintain Documentation: Keep accurate, detailed records of all processes, changes, and batch records. This is crucial for traceability and audits.
Implement Quality Control Systems: Establish robust quality control measures at every stage of production to detect and correct deviations from set standards.
Regular Audits and Inspections: Conduct regular internal audits to assess compliance and identify areas for improvement. Prepare for external inspections by regulatory bodies.
Continuous Improvement: Adopt a culture of continuous improvement (kaizen). Encourage feedback from staff and act on it to enhance GMP compliance.
Invest in Maintenance: Ensure equipment and facilities are regularly maintained and calibrated to prevent contamination and errors.
For more in-depth guidance, refer to resources provided by regulatory bodies and industry associations:
- ISPE (International Society for Pharmaceutical Engineering)
- ICH (International Council for Harmonisation of Technical Requirements for Pharmaceuticals for Human Use)
By focusing on these areas, a Plant Operator can significantly improve GMP compliance, ensuring that products are safe, effective, and of high quality.
How to Display GMP Compliance Skills on Your Resume
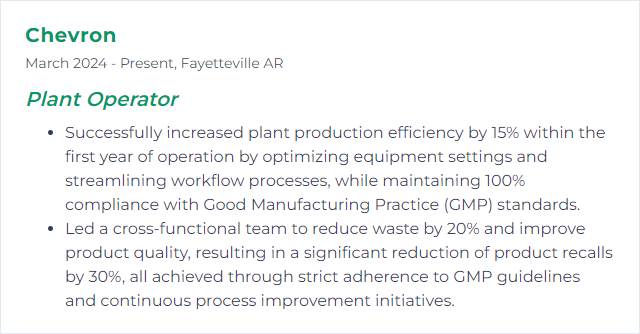