Top 12 Plant Controller Skills to Put on Your Resume
In today's highly competitive job market, standing out as a Plant Controller requires showcasing a unique set of skills on your resume that reflects your expertise in financial management and operational efficiency within manufacturing environments. Highlighting these top skills not only demonstrates your proficiency in managing complex industrial operations but also your ability to drive profitability and strategic growth for your future employer.
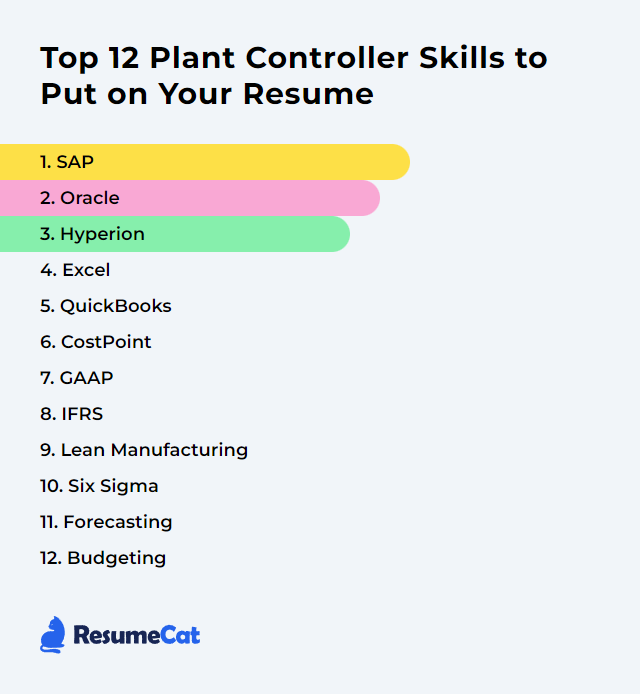
Plant Controller Skills
1. SAP
SAP is an enterprise resource planning (ERP) software that integrates key business functions, enabling a Plant Controller to manage financials, production, inventory, and operations efficiently within a unified system.
Why It's Important
SAP is crucial for a Plant Controller as it provides an integrated platform for real-time financial and operational data management, enabling efficient planning, budgeting, and control over manufacturing costs and processes, thus optimizing plant performance and profitability.
How to Improve SAP Skills
Improving SAP (Systems, Applications, and Products in Data Processing) for a Plant Controller involves optimizing the system for financial reporting, cost control, and operational efficiency. Here are key steps in a very short and concise manner:
Customize Reports: Tailor financial reports to meet specific management requirements. Use SAP's Financial Report Studio for customization.
Automate Processes: Implement SAP's Process Automation to streamline plant controlling operations, reducing manual errors and saving time.
Enhance Data Quality: Utilize SAP Master Data Governance to ensure accuracy and consistency across financial and operational data.
Implement SAP BPC: Use SAP Business Planning and Consolidation (BPC) for more efficient budgeting, forecasting, and financial consolidation processes.
Training and Support: Regularly update skills and knowledge of SAP functionalities through SAP Learning Hub to leverage the full potential of SAP tools.
Integrate Systems: Ensure seamless integration with other systems (e.g., production, HR) for real-time data using SAP Integration Suite.
Continuous Improvement: Regularly review and optimize SAP settings and processes in collaboration with IT and SAP support to align with evolving business needs.
By focusing on these areas, a Plant Controller can significantly improve the efficiency and effectiveness of SAP, enhancing the overall financial and operational control of the plant.
How to Display SAP Skills on Your Resume
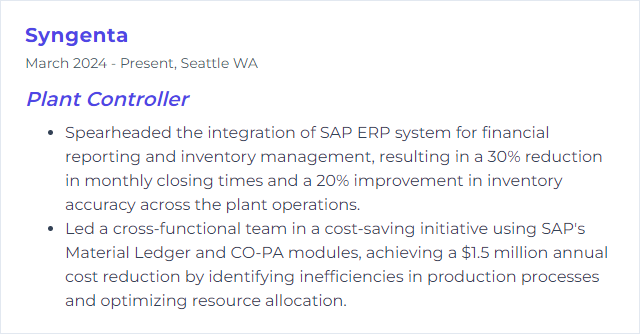
2. Oracle
Oracle, in the context relevant to a Plant Controller, refers to a comprehensive suite of software solutions and cloud services designed for business management, including financials, supply chain, manufacturing, and database management, to enhance operational efficiency and decision-making.
Why It's Important
Oracle is important for a Plant Controller because it provides robust financial management tools that enable precise control over budgets, costs, and operations, ensuring efficient resource allocation and financial integrity in manufacturing processes.
How to Improve Oracle Skills
Improving your Oracle setup for a Plant Controller involves optimizing system performance, data accuracy, and reporting capabilities. Here’s a concise guide:
Upgrade Regularly: Keep your Oracle applications up to date to leverage new features and improvements. Oracle's official documentation provides guidance on the latest updates.
Customize Reports: Use Oracle's reporting tools to create custom reports that meet specific plant management needs. This Oracle Reporting Solutions link provides insights into advanced reporting capabilities.
Implement Automation: Automate repetitive tasks such as data entry and report generation to increase efficiency. Oracle's Process Automation offers solutions for streamlining operations.
Enhance Data Accuracy: Utilize data validation and cleansing tools within Oracle to ensure the accuracy of financial and operational data. Explore Oracle's Data Quality tools for more information.
Invest in Training: Regularly train staff on Oracle updates and best practices to maximize the system's potential. Oracle University offers training and certification programs tailored to different roles and levels of expertise.
Leverage Analytics: Utilize Oracle's analytics and business intelligence tools to gain insights into plant performance and make data-driven decisions. Check out Oracle Analytics for advanced analytics solutions.
Optimize System Performance: Regular system audits and performance tuning can significantly improve Oracle's responsiveness. This guide on Performance Tuning may offer valuable strategies.
Seek Expert Consultation: Consider consulting with Oracle experts or partners for personalized advice on optimizing your system. Oracle's Consulting Services can provide tailored support and solutions.
By focusing on these areas, you can enhance the effectiveness of Oracle for plant controlling, leading to improved decision-making and operational efficiency.
How to Display Oracle Skills on Your Resume
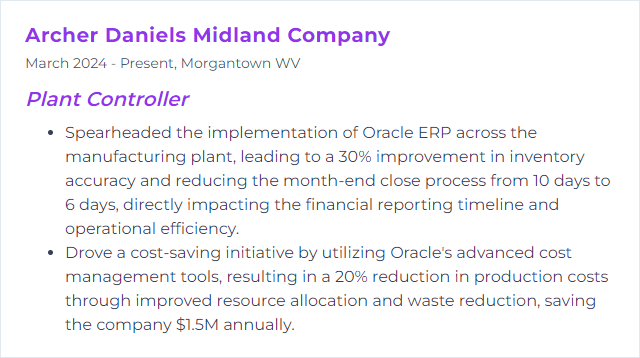
3. Hyperion
Hyperion, in the context of a Plant Controller, refers to a suite of financial software applications developed by Oracle, which includes tools for financial planning, budgeting, forecasting, and consolidation. These applications help in managing and analyzing financial data to optimize plant operations and financial performance.
Why It's Important
Hyperion is important for a Plant Controller as it provides advanced financial consolidation, budgeting, and forecasting capabilities, enabling accurate financial reporting and operational planning to optimize plant performance and profitability.
How to Improve Hyperion Skills
Improving Hyperion for a Plant Controller involves enhancing data accuracy, streamlining reporting processes, and optimizing performance. Here are concise steps to achieve this:
Automate Data Collection: Implement automation tools to reduce manual data entry and improve accuracy. Oracle Data Management offers solutions that can be integrated with Hyperion.
Customize Reports: Tailor financial reports to meet specific plant needs. Use Smart View for ad-hoc analysis and reporting directly within Excel.
Implement Best Practices for Account Reconciliation: Utilize Oracle Account Reconciliation to ensure financial data integrity and streamline the reconciliation process.
Enhance Forecasting Models: Leverage Hyperion Planning to improve budgeting and forecasting accuracy. Incorporate rolling forecasts for more dynamic financial planning.
Optimize System Performance: Regularly monitor and tune the Hyperion environment. Oracle provides performance tuning tips that can help in optimizing the application.
Ensure Data Security: Implement robust security measures to protect financial data. Oracle's Hyperion Security features can help safeguard sensitive information.
Continuous Training: Invest in ongoing training for the financial team to keep up with Hyperion updates and best practices. Oracle offers Hyperion training that can be beneficial.
By focusing on these areas, a Plant Controller can significantly enhance the efficiency and reliability of Hyperion for better financial management and decision-making.
How to Display Hyperion Skills on Your Resume
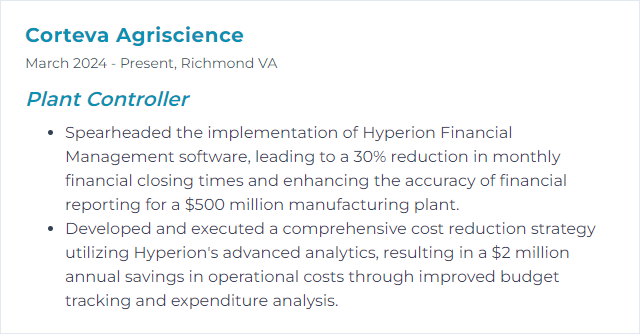
4. Excel
Excel is a spreadsheet software developed by Microsoft, widely used for data analysis, budgeting, financial forecasting, and various other accounting and financial tasks crucial for the role of a Plant Controller.
Why It's Important
Excel is vital for a Plant Controller because it enables efficient financial modeling, budgeting, and analysis, facilitating informed decision-making and operational efficiency in managing plant finances.
How to Improve Excel Skills
To improve Excel skills for a Plant Controller, focus on mastering the following areas:
Advanced Formulas: Understand complex formulas that are crucial for financial analysis and reporting. ExcelJet offers a comprehensive guide.
PivotTables: Enhance your data summarization and analysis skills. Microsoft Support provides tutorials on PivotTables.
Macros and VBA: Automate repetitive tasks to save time. Excel Easy introduces you to Macros and VBA.
Data Visualization: Learn to create impactful charts and graphs. Chandoo has excellent resources for visualization techniques.
Power Query and Power Pivot: For handling and analyzing large data sets efficiently. Microsoft Learn is a valuable resource for Power Query and Power Pivot.
Financial Modeling: Develop models to forecast financial scenarios. Corporate Finance Institute offers insights into best practices.
Excel Shortcuts: Boost your efficiency with keyboard shortcuts. Dezyre provides a list of essential shortcuts.
Improving these areas will significantly enhance your proficiency in Excel, making you more effective in your role as a Plant Controller.
How to Display Excel Skills on Your Resume
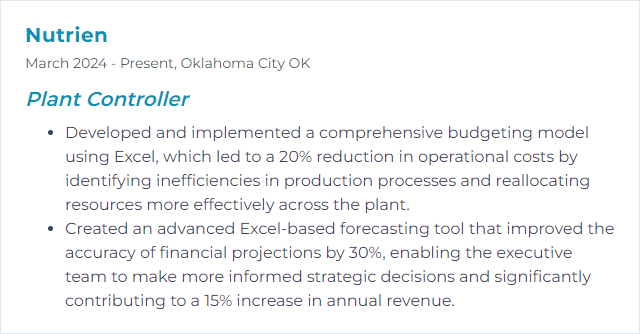
5. QuickBooks
QuickBooks is an accounting software designed for small to medium-sized businesses, offering features for managing invoices, payrolls, expenses, and inventory, which can assist a Plant Controller in financial reporting and budget management.
Why It's Important
QuickBooks is important for a Plant Controller because it streamlines financial management and reporting, providing accurate, real-time visibility into the plant's financial health, enabling more informed and strategic decision-making.
How to Improve QuickBooks Skills
Improving QuickBooks for a Plant Controller involves enhancing its functionality for financial management, reporting, and inventory control. Here are concise steps:
Utilize Custom Reporting: Tailor reports for specific plant management needs, focusing on cost analysis and financial performance. QuickBooks Advanced Reporting can help create detailed financial reports.
Integrate Inventory Management Solutions: Connect QuickBooks with third-party inventory management tools for real-time tracking and valuation. Tools like Fishbowl seamlessly integrate with QuickBooks.
Automate Workflows: Use QuickBooks’ automation features for recurring transactions and financial processes to save time. Learn about automating transactions.
Adopt Cloud-Based Solutions: For improved accessibility and data sharing among team members, consider QuickBooks Online for cloud-based operations. QuickBooks Online offers flexibility and real-time access.
Enhance Security Measures: Implement robust security protocols, including multi-factor authentication and user access controls, to protect financial data. QuickBooks provides security features for safeguarding your information.
Educate and Train Staff: Ensure that all users are proficient in QuickBooks through official training courses and resources. QuickBooks Training offers tutorials and webinars.
Leverage QuickBooks Apps: Explore the QuickBooks App Store for apps designed to enhance functionality in areas like expense tracking, payroll, and more. The QuickBooks App Store has various options.
By focusing on these areas, a Plant Controller can significantly improve the efficiency and effectiveness of QuickBooks for managing the financial aspects of manufacturing processes.
How to Display QuickBooks Skills on Your Resume
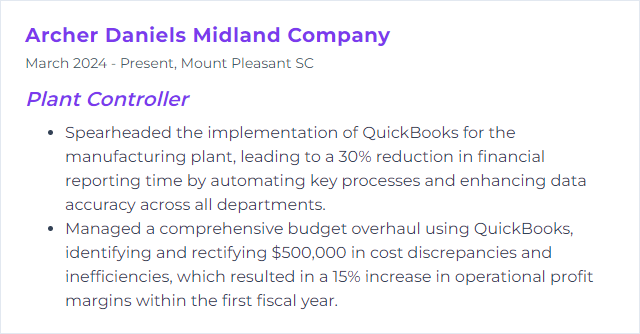
6. CostPoint
CostPoint is an enterprise resource planning (ERP) software designed to manage the financial and project aspects of businesses, including accounting, project management, and HR. For a Plant Controller, it facilitates precise cost tracking, budget management, and financial reporting for effective plant operations and decision-making.
Why It's Important
CostPoint is crucial for a Plant Controller as it provides detailed cost tracking and accounting functionality, enabling precise financial management, budgeting, and cost control for manufacturing operations.
How to Improve CostPoint Skills
Improving CostPoint, especially for a Plant Controller, involves leveraging its features for enhanced financial control and operational efficiency. Here are concise steps:
Automate Processes: Utilize CostPoint's automation capabilities for repetitive tasks like billing, reporting, and budgeting to reduce errors and save time.
Customize Dashboards: Tailor dashboards for real-time visibility into financial metrics relevant to plant operations, ensuring quick decision-making.
Integrate Systems: Ensure seamless data flow by integrating CostPoint with other operational systems (inventory, purchasing, etc.) for a unified view. Deltek Marketplace offers integration tools and partners.
Train Team Members: Regularly train team members on CostPoint’s latest features and best practices to optimize usage and ensure data accuracy.
Leverage Analytics: Use CostPoint’s analytics and reporting tools to analyze financial data, identify trends, and make informed decisions for cost control and efficiency improvements.
Regularly Review and Adjust: Continuously assess and adjust CostPoint settings and processes to align with changing operational needs and financial goals.
By focusing on these areas, a Plant Controller can significantly enhance CostPoint’s effectiveness for better financial oversight and operational performance.
How to Display CostPoint Skills on Your Resume
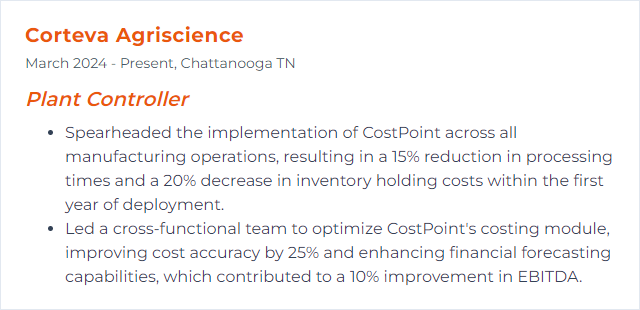
7. GAAP
GAAP (Generally Accepted Accounting Principles) refers to a set of accounting standards and practices that are used to prepare financial statements, ensuring consistency, reliability, and comparability of financial reporting. For a Plant Controller, GAAP guides the accurate reporting of the plant's financial activities, asset valuation, and performance measurement, ensuring compliance with regulatory requirements and facilitating decision-making processes.
Why It's Important
GAAP (Generally Accepted Accounting Principles) provides a standardized framework for financial reporting, ensuring consistency, reliability, and comparability of financial information. For a Plant Controller, GAAP is crucial for accurately reporting the plant's financial performance and position, facilitating informed decision-making and compliance with regulatory requirements.
How to Improve GAAP Skills
Improving GAAP (Generally Accepted Accounting Principles) compliance and application, particularly from a Plant Controller's perspective, involves enhancing financial accuracy, transparency, and adherence to accounting standards. Here are concise steps for improvement:
Continuous Education: Stay updated with FASB (Financial Accounting Standards Board) releases and amendments to GAAP standards to ensure accounting practices are current.
Internal Controls Strengthening: Implement and regularly review internal controls for financial reporting to detect and prevent errors. The COSO Framework provides a comprehensive approach.
Consistent Application: Ensure consistent application of GAAP across all accounting and financial reporting to maintain reliability and comparability of financial statements.
Technology Utilization: Leverage accounting software and ERP systems that are configured to comply with GAAP, enhancing accuracy and efficiency in financial data processing.
External Audit Engagement: Regularly engage with external auditors for unbiased reviews of financial statements and adherence to GAAP. This can provide insights into areas for improvement.
Professional Development: Encourage the finance team to pursue continuous professional development through resources like AICPA (American Institute of Certified Public Accountants) for up-to-date knowledge and skills in GAAP.
Documentation and Policies Review: Regularly review and update accounting policies and procedures documentation to reflect current GAAP standards and ensure they are followed diligently.
By focusing on these areas, a Plant Controller can significantly enhance the accuracy, reliability, and compliance of financial reporting under GAAP.
How to Display GAAP Skills on Your Resume
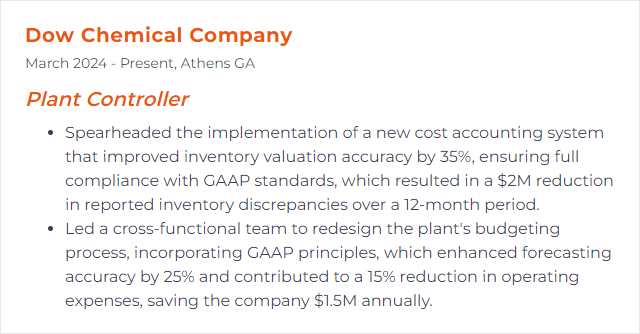
8. IFRS
IFRS (International Financial Reporting Standards) is a set of global accounting standards developed by the International Accounting Standards Board (IASB) that specify how transactions and other accounting events should be reported in financial statements. For a Plant Controller, IFRS provides guidelines for consistently recording and reporting financial data, ensuring transparency, comparability, and compliance in financial statements across international boundaries.
Why It's Important
IFRS (International Financial Reporting Standards) is crucial for a Plant Controller as it ensures financial statements are consistent, transparent, and comparable across international boundaries, facilitating global investment and decision-making.
How to Improve IFRS Skills
Improving IFRS (International Financial Reporting Standards) can enhance transparency, comparability, and efficiency in financial reporting. For a Plant Controller, the focus could be on areas directly impacting manufacturing and operations. Here’s a concise guide:
Enhance Specific Guidance for Manufacturing Costs: Develop clearer guidelines on the capitalization of direct and indirect manufacturing costs to improve consistency across entities. IAS 2 could be refined for better clarity.
Introduce More Detailed Reporting on Asset Lifecycle: Implement more detailed disclosures regarding plant, property, and equipment lifecycle, including maintenance schedules and decommissioning costs, within IAS 16.
Refine Impairment Testing Requirements: Streamline and specify impairment testing processes for non-financial assets, making them more practical for manufacturing settings, referring to IAS 36.
Expand Environmental and Sustainability Reporting: Integrate mandatory environmental and sustainability reporting, considering the growing importance of ESG (Environmental, Social, and Governance) factors, as explored in the IFRS Foundation's work on sustainability reporting.
Facilitate Digital Reporting: Encourage and facilitate the use of XBRL (eXtensible Business Reporting Language) for digital reporting to streamline the process and enhance accessibility. The IFRS Foundation provides resources on digital reporting.
Improvements should aim at balancing the need for detailed, relevant information with the practicalities of reporting for manufacturing operations, ensuring that financial statements remain useful to investors and other stakeholders without imposing undue burdens on entities.
How to Display IFRS Skills on Your Resume
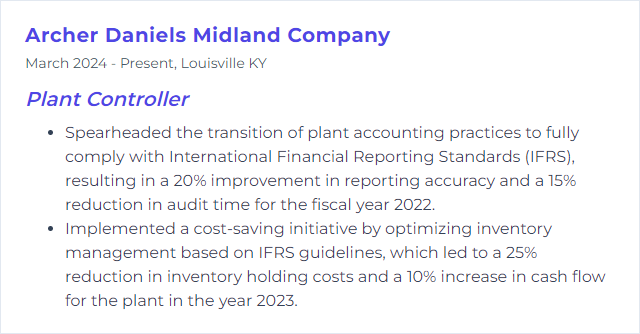
9. Lean Manufacturing
Lean Manufacturing is a systematic approach to minimizing waste within manufacturing systems while simultaneously maximizing productivity. For a Plant Controller, it involves continuous efforts to reduce costs, improve operational efficiency, and optimize inventory management to enhance the plant's financial performance.
Why It's Important
Lean Manufacturing is important because it helps in reducing waste, improving operational efficiency, and enhancing product quality, leading to cost savings, higher profitability, and increased customer satisfaction, all of which are critical for a Plant Controller's goals of optimizing plant performance and financial health.
How to Improve Lean Manufacturing Skills
Improving Lean Manufacturing involves streamlining processes to reduce waste and enhance value to the customer. As a Plant Controller, focus on the following areas:
Value Stream Mapping: Identify and map all steps in your production process to visualize waste and pinpoint areas for improvement. Lean.org provides resources on understanding and implementing value stream mapping.
Continuous Improvement (Kaizen): Foster a culture of continuous improvement by encouraging every employee to suggest ways to reduce waste. This involves regular brainstorming sessions and implementing small, incremental changes. The Kaizen Institute offers insights on embedding Kaizen into your operations.
Just-In-Time (JIT) Production: Aim to reduce inventory levels and increase efficiency by producing just what is needed, when it is needed. This requires tight coordination with suppliers and a flexible workforce. The Toyota Global site shares insights on JIT principles.
Standardized Work: Standardize processes to ensure consistency and efficiency. This involves documenting best practices and training employees to follow them. Resources on standardized work can be found at SME.
5S Methodology: Implement the 5S (Sort, Set in order, Shine, Standardize, Sustain) methodology to organize the workplace in an efficient, ergonomic manner. This leads to a safer, more productive environment. Detailed guidance on 5S can be found at ASQ.
Root Cause Analysis: When problems occur, use tools like the Five Whys or Fishbone Diagram to investigate and address the root cause, preventing recurrence. The ASQ provides resources on conducting root cause analysis.
Implementing these strategies requires commitment and regular review to ensure continuous improvement. Engage your team, provide training, and use metrics to measure progress and success.
How to Display Lean Manufacturing Skills on Your Resume
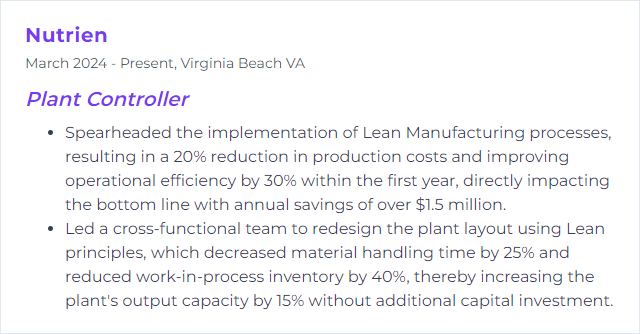
10. Six Sigma
Six Sigma is a data-driven methodology and set of tools aimed at process improvement by reducing variability and defects in manufacturing and business processes, thereby increasing efficiency and quality. For a Plant Controller, it means leveraging Six Sigma to optimize production, reduce waste, and ensure financial performance aligns with operational excellence.
Why It's Important
Six Sigma is important because it provides a systematic approach to reducing errors, improving quality, and optimizing processes, leading to cost reductions and increased efficiency in manufacturing operations, directly supporting a Plant Controller's goal of maximizing financial performance and operational efficiency.
How to Improve Six Sigma Skills
Improving Six Sigma involves continuously enhancing process efficiency and quality by following these concise steps, particularly relevant for a Plant Controller:
- Define clear objectives aligning with business goals to identify problems (ASQ’s Define Phase).
- Measure current performance to establish baselines using accurate data collection methods (iSixSigma on Measurement).
- Analyze data to identify root causes of inefficiencies or defects (ASQ’s Analyze Phase).
- Improve by implementing solutions to address root causes, and ensure those improvements are sustainable (ASQ’s Improve Phase).
- Control the improved processes by monitoring performance and applying corrective measures to prevent regression (ASQ’s Control Phase).
Additionally, emphasize ongoing training and certification for your team (Six Sigma Certification), utilize technological advancements for data analysis, and foster a culture of continuous improvement within your organization.
How to Display Six Sigma Skills on Your Resume
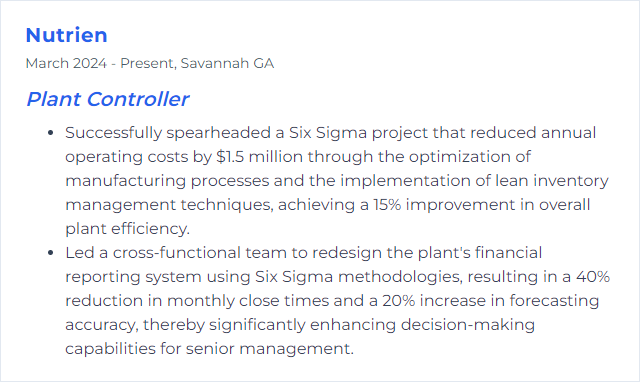
11. Forecasting
Forecasting, in the context of a Plant Controller, involves predicting future financial outcomes and operational needs of the manufacturing plant based on historical data, current trends, and strategic planning. This helps in budgeting, resource allocation, and decision-making to optimize plant performance and profitability.
Why It's Important
Forecasting is crucial for a Plant Controller as it enables effective planning of production schedules, inventory management, and budget allocation, ensuring operational efficiency and cost optimization.
How to Improve Forecasting Skills
Improving forecasting, especially for a Plant Controller, involves a blend of accurate data collection, advanced analytical tools, and continuous refinement. Here are concise steps to enhance forecasting accuracy:
Historical Data Analysis: Begin with a thorough analysis of past performance data to understand trends and seasonality. Utilize Excel for its accessible data analysis tools.
Implement Forecasting Software: Adopt specialized forecasting software like Oracle ERP Cloud for more sophisticated analysis and predictive capabilities.
Collaborative Planning: Engage cross-functional teams to ensure all perspectives are considered. Tools like Anaplan can facilitate this collaborative planning process.
Continuous Improvement: Regularly review forecast accuracy and adjust methodologies as needed. Incorporate feedback loops for ongoing refinement.
External Market Analysis: Stay informed on market trends and incorporate external data sources. Websites like Bloomberg provide valuable market insights.
Education and Training: Keep abreast of the latest forecasting techniques and technologies through platforms like Coursera and edX.
Scenario Planning: Use tools like SAP Analytics Cloud for scenario planning to prepare for various future states.
By following these steps and leveraging the right tools, a Plant Controller can significantly improve forecasting accuracy and reliability.
How to Display Forecasting Skills on Your Resume
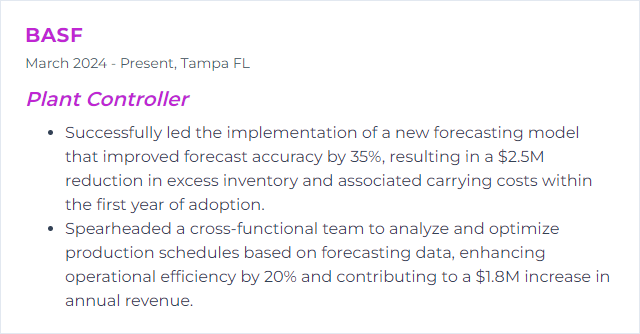
12. Budgeting
Budgeting, in the context of a Plant Controller, involves creating a detailed financial plan that outlines the expected revenues, expenses, and investments necessary for the efficient operation and strategic development of a manufacturing facility over a specific period.
Why It's Important
Budgeting is crucial for a Plant Controller as it provides a financial roadmap for managing operational costs, optimizing resource allocation, and ensuring profitability through efficient financial planning and control.
How to Improve Budgeting Skills
Improving budgeting as a Plant Controller involves strategic planning, accurate forecasting, and continuous monitoring. Here are concise steps:
Develop Accurate Baselines: Start with historical data analysis to understand past performance Financial Modeling Guide.
Implement Rolling Forecasts: Shift from annual budgets to rolling forecasts for more flexibility and accuracy CPA Australia.
Adopt Zero-Based Budgeting (ZBB): Re-evaluate all expenses regularly to ensure they're necessary McKinsey.
Utilize Variance Analysis: Regularly compare actual results against the budget to identify and address discrepancies quickly Investopedia.
Leverage Technology: Use budgeting software for accurate data management and real-time insights Gartner.
Train Your Team: Ensure your team understands budgeting processes and tools for effective implementation Association for Financial Professionals.
Communicate Effectively: Foster open communication with all stakeholders for shared understanding and accountability Harvard Business Review.
By following these steps, a Plant Controller can significantly improve the budgeting process, enhancing the financial health and operational efficiency of the plant.
How to Display Budgeting Skills on Your Resume
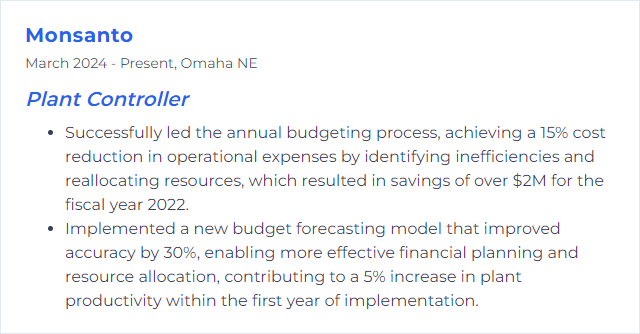