Top 12 PCB Design Engineer Skills to Put on Your Resume
In today's competitive job market, standing out as a PCB Design Engineer requires a resume that showcases a unique blend of technical prowess, creativity, and problem-solving abilities. Highlighting the top skills in your arsenal not only demonstrates your capability to potential employers but also sets the foundation for a successful career in the ever-evolving field of electronics design.
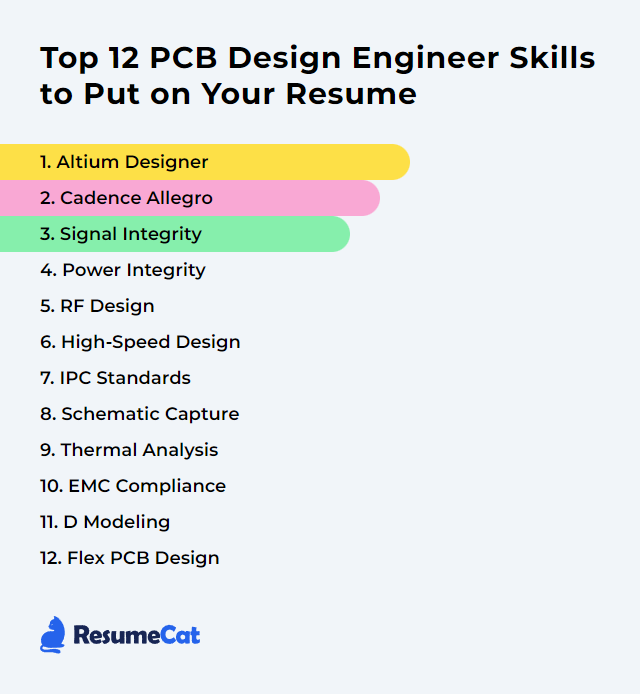
PCB Design Engineer Skills
- Altium Designer
- Cadence Allegro
- Signal Integrity
- Power Integrity
- RF Design
- High-Speed Design
- IPC Standards
- Schematic Capture
- Thermal Analysis
- EMC Compliance
- D Modeling
- Flex PCB Design
1. Altium Designer
Altium Designer is a comprehensive and integrated PCB design software, providing engineers with tools for schematic capture, PCB layout, and 3D visualization of electronic circuits, facilitating the design and development of complex multi-layer printed circuit boards.
Why It's Important
Altium Designer is important for a PCB Design Engineer because it offers an all-in-one solution for PCB design, including schematic capture, PCB layout, and signal integrity analysis, streamlining the design process and enhancing productivity and design quality.
How to Improve Altium Designer Skills
Improving your skills in Altium Designer as a PCB Design Engineer involves both understanding its vast features and staying updated with the latest design techniques. Here are concise tips to enhance your proficiency:
Understand the Basics Thoroughly: Start with Altium's own Getting Started with PCB Design guide to solidify your foundation.
Explore Advanced Features: Dive into advanced features through Altium's Advanced PCB Design Course to leverage the full potential of the software.
Utilize Altium Designer Tutorials: Regularly visit Altium’s Resource Hub for the latest tutorials, webinars, and articles.
Join the Altium Community: Engage with other professionals on the Altium Designer Forum for sharing tips, tricks, and solutions.
Practice Regularly: Nothing beats hands-on practice. Set yourself daily or weekly design challenges to keep your skills sharp.
Stay Updated with Software Updates: Keep your software up-to-date. Check Altium's What’s New section regularly for the latest features and improvements.
Learn from Industry Experts: Follow renowned PCB design experts and their blogs or YouTube channels for insights and advanced techniques.
Optimize Your Workflow: Customize your workspace and learn keyboard shortcuts to improve efficiency. Altium provides a guide on customizing the workspace.
By incorporating these strategies, you'll not only enhance your expertise in Altium Designer but also stay ahead in the rapidly evolving field of PCB design.
How to Display Altium Designer Skills on Your Resume
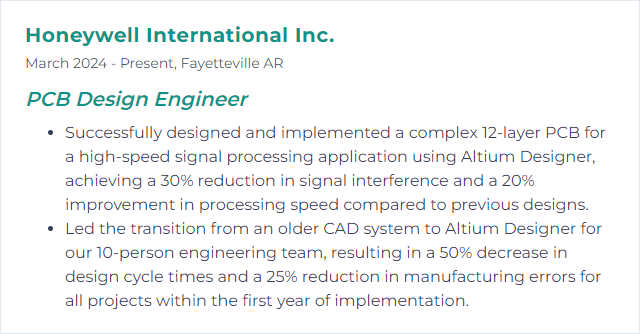
2. Cadence Allegro
Cadence Allegro is a high-performance, comprehensive design and simulation solution used by PCB design engineers for creating complex multilayer printed circuit boards (PCBs). It offers advanced routing, layout, and manufacturing capabilities to streamline the development process from schematic to production.
Why It's Important
Cadence Allegro is important for a PCB Design Engineer because it provides advanced, high-speed PCB design, simulation, and analysis tools, enabling efficient creation and verification of complex, high-performance electronic circuits and systems.
How to Improve Cadence Allegro Skills
Improving your proficiency with Cadence Allegro for PCB design involves several strategies, including learning from tutorials, practicing regularly, customizing your workspace, and leveraging community knowledge. Here's a concise guide:
Official Training and Documentation: Start with Cadence's own resources to understand the foundational aspects and updates.
- Explore Cadence Training Services for official courses.
- Review the Cadence Support for documentation and troubleshooting.
Online Tutorials and Courses: Utilize free and paid tutorials to learn new tricks and techniques.
- LinkedIn Learning offers courses on Cadence Allegro and PCB design principles.
Practice with Real Projects: Apply your skills on actual designs to understand the challenges and solutions in practical scenarios.
- Regular practice helps in familiarizing with tool's interface and shortcuts.
Customize Your Workspace and Tools: Tailor the Allegro environment to suit your workflow for efficiency.
- Learn to create scripts and use Skill language for automation. The Cadence Community is a great place to share and find custom scripts.
Join Forums and Groups: Engage with other PCB designers to exchange knowledge and tips.
- Participate in discussions on platforms like the Cadence Community and Reddit’s r/PrintedCircuitBoard.
Stay Updated with New Features: Cadence frequently updates Allegro with new features and improvements.
- Keep an eye on the What’s New section on the Cadence website.
Keyboard Shortcuts and Efficiency Tips: Learning and using keyboard shortcuts can significantly speed up your design process.
- A list of shortcuts can often be found within the Allegro documentation or through tutorials on sites like YouTube.
By following these strategies and regularly engaging with the Cadence Allegro community, you can improve your skills and efficiency in PCB design.
How to Display Cadence Allegro Skills on Your Resume
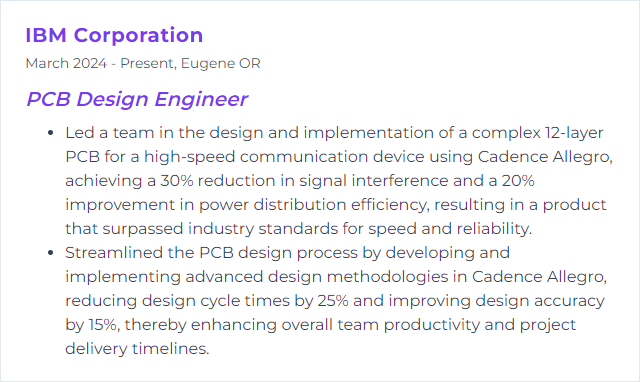
3. Signal Integrity
Signal integrity refers to the quality and performance of electrical signals as they travel through circuits on a printed circuit board (PCB). It is crucial for ensuring reliable and accurate communication between components, by minimizing signal degradation, distortion, and noise. For a PCB Design Engineer, maintaining signal integrity involves careful design practices to uphold signal quality across all operating conditions.
Why It's Important
Signal integrity is crucial for a PCB Design Engineer because it ensures that electrical signals are transmitted without distortion or degradation, maintaining the performance, reliability, and functionality of the electronic device.
How to Improve Signal Integrity Skills
Improving Signal Integrity (SI) in PCB design involves several critical steps focused on minimizing signal degradation and ensuring reliable communication between components. Here's a concise guide:
Proper Routing Techniques: Use differential signaling when possible, maintain consistent impedance, and minimize vias on high-speed signals to reduce reflections and crosstalk. For detailed techniques, see Altium’s Guide on Routing.
Impedance Control: Match the impedance of the PCB traces with the drivers and receivers to minimize reflections. This involves careful selection of trace width and dielectric material. Read more at Cadence's Impedance Control Guide.
Proper Grounding and Power Distribution: Use a solid ground plane and design power distribution networks (PDN) to minimize noise and provide stable power to all components. Texas Instruments provides insights in their Grounding and Power Distribution Guide.
Decoupling Capacitors: Place decoupling capacitors close to power pins of ICs to filter high-frequency noise. For best practices, see Analog Devices’ Decoupling Capacitors Guide.
Signal Integrity Analysis Tools: Utilize software tools for pre-layout and post-layout SI analysis to identify potential issues early. Mentor, a Siemens Business, offers tools and insights at Mentor Signal Integrity Analysis.
Use of Differential Pairs and Length Matching: For high-speed signals, using differential pairs and matching the lengths of critical signal paths can help maintain signal integrity by reducing skew and timing issues. Consult Altium’s Differential Pairs and Length Matching Guide.
Layer Stacking and Material Selection: Optimize the PCB layer stack-up for signal integrity by placing signal layers close to ground planes and selecting materials with suitable dielectric properties. Read more on Layer Stack Management by Altium.
By implementing these strategies, a PCB Design Engineer can significantly improve the signal integrity of their designs, ensuring robust and reliable electronic systems.
How to Display Signal Integrity Skills on Your Resume
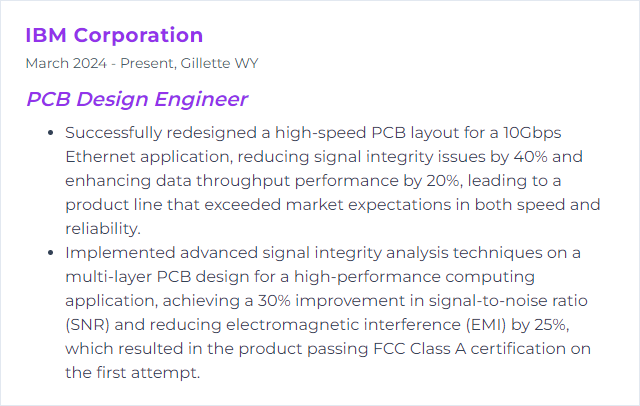
4. Power Integrity
Power Integrity in PCB design refers to ensuring a stable and clean power supply across all components of the circuit board, minimizing noise, voltage drops, and fluctuations that can affect the performance and reliability of the electronic system.
Why It's Important
Power integrity ensures stable and accurate voltage supply throughout a PCB, essential for the reliable performance and functionality of electronic components and systems, preventing signal integrity issues, and ensuring the longevity and reliability of the design.
How to Improve Power Integrity Skills
Improving Power Integrity (PI) in PCB design involves managing the distribution of power across the board to ensure stable and adequate supply to all components. Here are concise steps to improve PI:
Plan Power Distribution Network (PDN): Strategically plan your PDN to minimize impedance and ensure uniform power distribution. Use simulation tools to optimize.
Use Decoupling Capacitors: Place decoupling capacitors close to power pins of ICs to stabilize voltage and reduce noise. Texas Instruments offers insights on effective decoupling.
Manage Power Plane and Ground Plane: Ensure your power and ground planes are closely coupled to reduce inductance. Minimize the distance between them to improve the decoupling effect. Analog Devices provides useful ground plane design techniques.
Optimize Trace Widths and Routing: Calculate and use appropriate trace widths for power traces to minimize voltage drops and avoid overheating. Use direct and short paths for critical power connections. Altium discusses efficient PCB design rules that include power integrity considerations.
Employ Power Integrity Simulation Tools: Use PI simulation software early in the design process to predict and mitigate potential issues. Keysight's Advanced Design System (ADS) and Cadence's Sigrity are examples of tools for analyzing and optimizing PDN performance.
Review and Test: After design and prototyping, thoroughly review and test your PCB for power integrity issues. Use equipment like oscilloscopes to verify the performance matches your design expectations.
By attentively managing your PDN, using decoupling strategies, optimizing physical layout, and employing simulation tools, you can significantly improve power integrity in your PCB designs.
How to Display Power Integrity Skills on Your Resume
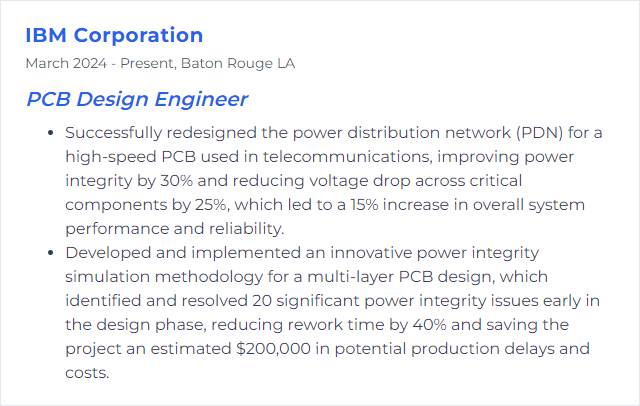
5. RF Design
RF Design refers to the process of planning, creating, and implementing circuits that transmit or receive radio frequencies in the range of about 3 kHz to 300 GHz. For a PCB Design Engineer, it involves the careful layout of PCB tracks, component placement, and impedance matching to ensure optimal performance and minimal interference in wireless communication systems.
Why It's Important
RF (Radio Frequency) design is crucial for a PCB Design Engineer because it ensures reliable communication and signal integrity in devices that operate in the RF spectrum, such as wireless networks, mobile phones, and IoT devices, by addressing challenges like interference, signal loss, and bandwidth limitations.
How to Improve RF Design Skills
Improving RF design in PCB layout involves several key strategies to enhance performance, minimize interference, and ensure signal integrity. Here's a concise guide:
Component Placement: Carefully place RF components to minimize signal path lengths and avoid crossing high-speed digital signals. RF Design Guide
Impedance Matching: Ensure impedance matching across all RF paths to minimize reflections. Use microstrip or stripline transmission lines. Impedance Control
Stackup Design: Optimize PCB stackup for RF signal integrity, using dedicated signal and ground layers to reduce EMI and crosstalk. Stackup Design
Grounding: Implement a solid and continuous ground plane beneath RF traces to reduce noise and improve performance. Effective Grounding
Decoupling and Filtering: Use decoupling capacitors close to RF IC power pins and incorporate filters to suppress harmonics and noise. Decoupling Techniques
Shielding and Isolation: Shield sensitive RF components and maintain adequate isolation between RF and digital sections to prevent interference. RF Isolation Techniques
PCB Material Selection: Choose PCB materials with appropriate dielectric constants and low loss tangents to support RF frequencies. Material Selection
Simulation and Testing: Leverage simulation tools to predict RF performance and conduct thorough testing to validate design under real-world conditions. Simulation Tools
By focusing on these aspects, a PCB design engineer can significantly improve the performance and reliability of RF designs.
How to Display RF Design Skills on Your Resume
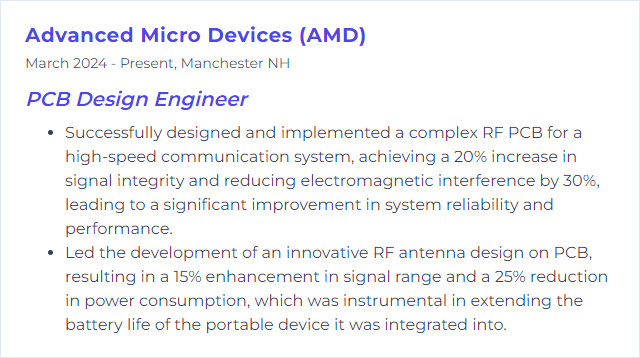
6. High-Speed Design
High-speed design involves the creation and optimization of printed circuit boards (PCBs) to ensure reliable performance and integrity of signals at high frequencies, where phenomena such as reflection, crosstalk, and electromagnetic interference become significant challenges for a PCB Design Engineer.
Why It's Important
High-speed design is crucial for a PCB Design Engineer because it ensures reliable performance and signal integrity in systems operating at high frequencies, reducing noise, interference, and data corruption, thereby optimizing the functionality and speed of electronic devices.
How to Improve High-Speed Design Skills
Improving high-speed design in PCB (Printed Circuit Board) design involves several key strategies to ensure signal integrity, minimize interference, and optimize performance. Here are concise tips:
Control Impedance: Match the impedance of your traces with the source and load impedances to minimize reflections. Use an impedance calculator to help design your traces correctly.
Manage Signal Integrity: Use termination techniques such as series or parallel termination to reduce signal reflections and ringing.
Minimize Crosstalk: Route high-speed signals away from each other and use ground planes between signal layers to shield them. This guide offers detailed strategies.
Optimize Decoupling and Power Distribution: Place decoupling capacitors close to IC power pins. Design a robust power distribution network (PDN) to ensure stable supply across the board. Explore techniques on effective power distribution.
Use Differential Signaling: For very high-speed data transfers, differential pairs can greatly reduce emissions and improve signal integrity. Understanding differential signaling is crucial.
Layout Considerations: Keep high-speed traces short and straight, with minimal vias. Route them over solid ground planes when possible. High-speed layout guidelines provide comprehensive advice.
Consideration of Return Paths: Ensure that the return path for high-speed signals is as direct as possible to reduce loop area and hence, emissions. Designing with return paths in mind can mitigate many high-speed design issues.
Simulation and Testing: Use simulation tools to predict and correct issues related to signal integrity, crosstalk, and EMC before prototyping. Cadence and ANSYS offer solutions for high-speed PCB analysis.
Continuous Learning: Stay updated with the latest trends and technologies in high-speed PCB design. Online resources like All About Circuits and IEEE Xplore are valuable for learning and keeping skills sharp.
By focusing on these areas, PCB design engineers can significantly improve the performance and reliability of high-speed designs.
How to Display High-Speed Design Skills on Your Resume
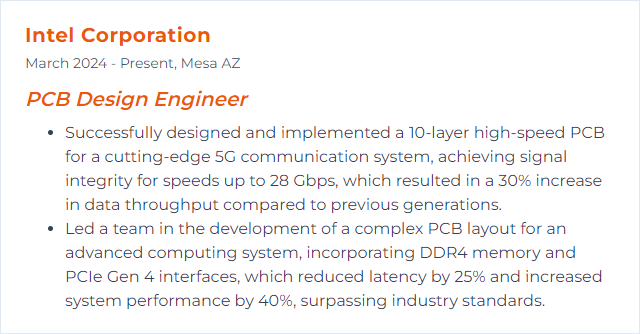
7. IPC Standards
IPC Standards are a series of guidelines developed by the Association Connecting Electronics Industries, aimed at standardizing the assembly and production processes of electronic equipment, including PCB (Printed Circuit Board) design and manufacturing. For a PCB Design Engineer, these standards provide crucial specifications for board layout, material selection, component placement, and soldering to ensure quality, reliability, and consistency in electronic products.
Why It's Important
IPC Standards are crucial for PCB Design Engineers as they provide industry-recognized guidelines that ensure reliability, quality, and consistency in the design and manufacturing of printed circuit boards, facilitating effective communication and interoperability among stakeholders.
How to Improve IPC Standards Skills
Improving IPC Standards as a PCB Design Engineer involves actively participating in IPC standard development, continuous learning, and applying best practices in your designs. Here are concise steps to enhance your adherence and contribution to IPC Standards:
Stay Updated: Regularly visit the IPC website to stay informed about the latest standards and amendments.
IPC Training and Certification: Enroll in IPC certification programs relevant to PCB design, such as IPC-A-600 (Acceptability of Printed Boards) and IPC-6012 (Qualification and Performance Specification for Rigid Printed Boards).
Contribute to IPC Standards Development: Join an IPC standards development committee. Share your experiences and suggestions for improvements through the IPC Committee's page.
Implement Standards in Design: Apply IPC standards rigorously in your PCB designs, focusing on design for manufacturability (DFM) and design for assembly (DFA) principles.
Peer Review and Continuous Improvement: Regularly participate in peer reviews of PCB designs within your organization or IPC community forums to gain insights and feedback for continuous improvement.
Use IPC-Compliant Tools: Ensure that the PCB design software you use complies with IPC standards. Many tools have features or plugins specifically for checking IPC compliance.
Stay Connected with the Community: Join IPC discussion forums and LinkedIn groups related to PCB design to exchange knowledge and stay abreast of evolving standards and technologies.
By actively engaging in these steps, you can contribute to the improvement of IPC standards and enhance the quality and reliability of PCB designs within the industry.
How to Display IPC Standards Skills on Your Resume
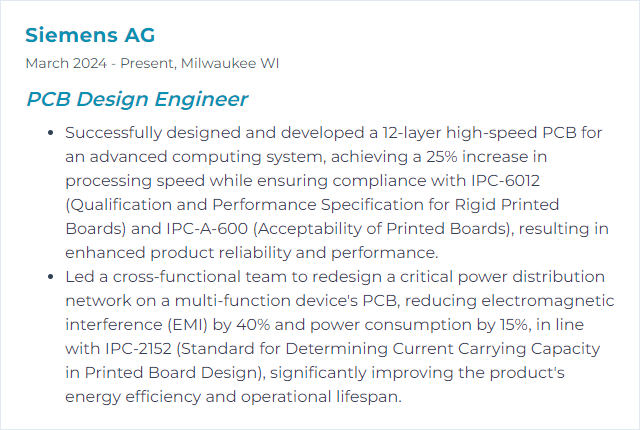
8. Schematic Capture
Schematic capture is the process of creating a detailed diagram (schematic) that represents the electrical connections and components of a circuit, which is a crucial step for PCB (Printed Circuit Board) Design Engineers in designing and laying out PCBs.
Why It's Important
Schematic capture is crucial for a PCB Design Engineer as it provides a detailed blueprint of the electrical circuitry, ensuring accurate communication of design intent, facilitating error checking, and serving as a foundation for PCB layout and fabrication.
How to Improve Schematic Capture Skills
Improving schematic capture involves enhancing accuracy, readability, and efficiency in the design process. Here are concise strategies for a PCB Design Engineer:
Use Hierarchical Design: Break down complex circuits into manageable sub-circuits or blocks. This approach simplifies understanding and editing. Altium’s guide offers insights into hierarchical design benefits.
Standardize Components and Symbols: Create or adhere to a library of standardized symbols and components to ensure consistency and reduce errors. SnapEDA is a good resource for finding standardized parts.
Leverage Design Rule Checks (DRC): Regularly run DRC to catch and correct errors early, enhancing the reliability of your schematic. OrCAD DRC provides robust checking tools.
Utilize Cross-Probing: Employ tools that allow for easy navigation between schematic and PCB layout, facilitating quick identification and correction of issues. Mentor Graphics’ Cross-Probing feature offers an example of efficient navigation.
Incorporate Version Control: Use version control systems to track changes, facilitating collaboration and error tracking. GitHub can be adapted for hardware design version control.
Invest in Training and Continuous Learning: Stay updated with the latest tools and practices in schematic capture and PCB design through online courses and webinars. Coursera and Udemy offer relevant courses.
By implementing these strategies, PCB Design Engineers can significantly improve the quality and efficiency of their schematic capture process.
How to Display Schematic Capture Skills on Your Resume
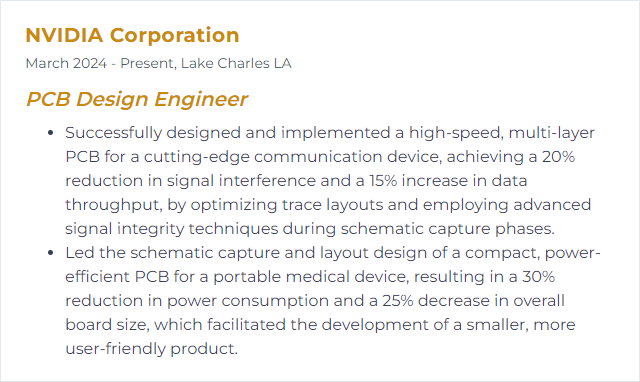
9. Thermal Analysis
Thermal analysis in the context of PCB design involves evaluating how heat is generated, distributed, and dissipated across a printed circuit board during operation. This process helps identify hot spots, ensure components operate within their temperature limits, and guides the design of thermal management solutions to prevent overheating and ensure reliability and longevity of the PCB.
Why It's Important
Thermal analysis is crucial for PCB design engineers because it helps ensure the reliability and performance of electronic components by preventing overheating, which can lead to failure or reduced lifespan. This analysis guides the optimal placement of components, heat sinks, and thermal vias, enhancing the overall system's efficiency and stability.
How to Improve Thermal Analysis Skills
Improving thermal analysis in PCB design involves several strategies aimed at ensuring optimal heat management and maintaining component performance. Here are concise steps along with resources for further exploration:
Material Selection: Choose PCB materials with good thermal conductivity. High thermal conductivity materials help in efficient heat dissipation. Learn More.
Component Placement: Place heat-generating components evenly and in positions that facilitate heat dissipation. Consider the proximity of thermal-sensitive components. Component Placement Guidelines.
Thermal Vias: Implement thermal vias beneath heat-generating components to transfer heat away from them effectively. Thermal Management with Vias.
Heat Sinks and Thermal Pads: Attach heat sinks directly to high-heat components and use thermal pads to improve the thermal interface between components and heat sinks. Heat Sink Selection.
Use of Power Planes: Incorporate power and ground planes in your design to help spread and dissipate heat across the PCB. Power Plane Thermal Management.
Simulation and Analysis Tools: Utilize PCB design software with thermal analysis capabilities to simulate and identify potential hot spots and thermal issues before manufacturing. Thermal Simulation.
Airflow and Cooling Strategies: Design for adequate airflow around the PCB, including the use of fans or convection cooling techniques. Cooling Strategies.
By adopting these strategies, a PCB design engineer can significantly improve the thermal performance of their designs, ensuring reliability and longevity of the electronic components.
How to Display Thermal Analysis Skills on Your Resume
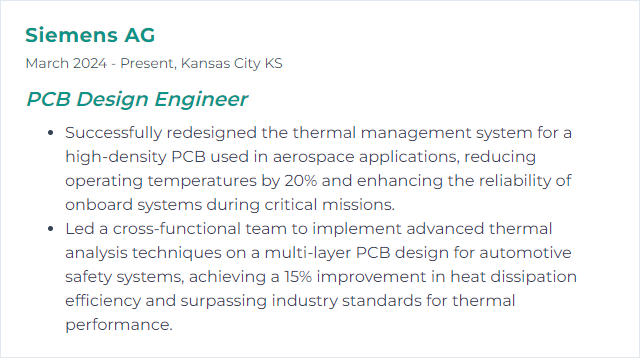
10. EMC Compliance
EMC (Electromagnetic Compatibility) compliance ensures that electronic devices, such as those involving PCB (Printed Circuit Board) designs, do not emit unwanted electromagnetic interference (EMI) that could disrupt the functioning of nearby devices, and are also immune to the EMI from external sources. For a PCB Design Engineer, achieving EMC compliance involves designing circuits and layouts that minimize EMI through careful component placement, routing, and the use of shielding and filtering techniques.
Why It's Important
EMC (Electromagnetic Compatibility) compliance is crucial for a PCB Design Engineer because it ensures that the PCB will operate as intended without causing or being affected by electromagnetic interference (EMI), leading to reliable performance in its intended environment and compliance with global regulatory standards.
How to Improve EMC Compliance Skills
Improving EMC (Electromagnetic Compatibility) compliance in PCB design involves several strategies to minimize electromagnetic interference (EMI) and ensure that the device operates as intended in its electromagnetic environment without causing or suffering undue interference. Here are concise steps a PCB Design Engineer can take:
Grounding: Implement a robust grounding strategy. Use a single-point ground or a ground plane to reduce loop areas and improve EMC performance. Grounding in Mixed-Signal Systems.
Trace Layout: Minimize the length of high-speed traces and route them away from sensitive circuits. Use differential signaling for critical signals. PCB Design Guidelines for Reduced EMI.
Decoupling and Filtering: Place decoupling capacitors close to IC power pins to stabilize power supply voltages. Use filters on I/O lines to prevent high-frequency noise from entering or leaving the PCB. Decoupling Capacitor Design.
Shielding and Guard Traces: Use metal shields over highly sensitive components or circuits. Employ guard traces with vias connected to ground to protect critical signal paths. EMC Design Guide for PCB.
Component Placement and Orientation: Place components to minimize EMI generation and susceptibility. Orient high-speed components in such a way that their fields oppose rather than enhance each other. PCB Layout Design for Low-EMI.
Stackup Design: Use a multilayer PCB stackup with separate layers for power and ground, placing signal layers between them to reduce EMI. PCB Stackup Design Considerations for EMC.
Review and Test: Use EMC simulation tools during the design phase to identify potential issues early. Perform pre-compliance testing to catch and address problems before final compliance testing. EMC Pre-Compliance: Why, What, and How.
By integrating these practices into PCB design workflows, engineers can markedly enhance EMC compliance, reducing the risk of costly redesigns and ensuring smoother certification processes.
How to Display EMC Compliance Skills on Your Resume
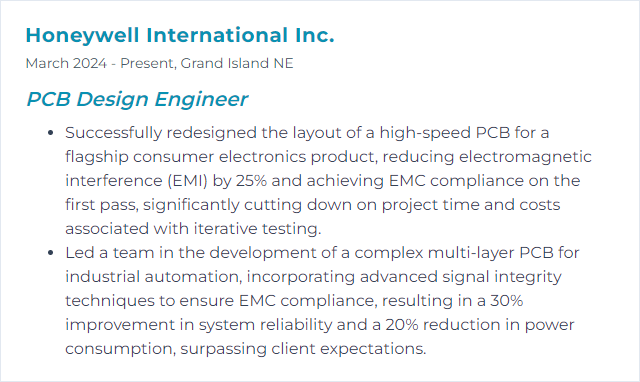
11. D Modeling
3D modeling in the context of a PCB Design Engineer involves creating a digital representation of a printed circuit board and its components in three dimensions. This allows for visualization, analysis, and testing of the PCB design in a simulated real-world environment, facilitating the identification and resolution of potential design and assembly issues before physical prototyping.
Why It's Important
3D modeling is crucial for a PCB Design Engineer as it enables accurate visualization of the PCB in its actual environment, ensures component fit and clearance, facilitates thermal and mechanical stress analysis, and aids in identifying potential manufacturing issues before prototyping, saving time and costs.
How to Improve D Modeling Skills
To improve 3D modeling in PCB design, focus on these key areas:
Understand the Basics: Ensure a solid understanding of PCB design fundamentals and 3D modeling principles. Autodesk offers valuable resources.
Software Proficiency: Master PCB design software. Popular options include Altium Designer and KiCad, both featuring 3D visualization tools.
Component Libraries: Utilize or create detailed 3D component libraries for accurate representation. Check SnapEDA for a vast component library.
Design for Manufacturing (DFM): Apply DFM principles to avoid production issues. Guidelines from IPC are crucial for understanding manufacturing constraints.
Simulation and Analysis: Use simulation tools to predict issues before prototyping. ANSYS provides comprehensive analysis options.
Feedback and Iteration: Incorporate feedback from manufacturing and field tests to refine the model. Continuous learning and adaptation are key.
Stay Updated: Keep up with the latest trends and technologies in PCB design and 3D modeling through forums and publications like EE Times.
By focusing on these areas and leveraging the recommended resources, you can significantly improve your 3D modeling skills in PCB design.
How to Display D Modeling Skills on Your Resume
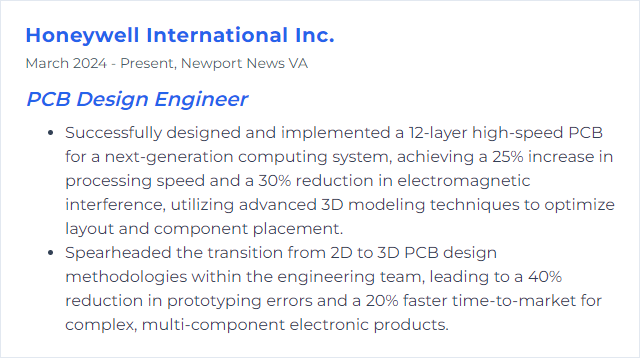
12. Flex PCB Design
Flex PCB Design involves creating flexible printed circuit boards that can bend, twist, and fold, using materials like polyimide or polyester. It requires careful layout planning to accommodate flexing without damaging the circuits, emphasizing trace routing, bend radius, and component placement for durability and reliability in dynamic applications.
Why It's Important
Flex PCB design is crucial for a PCB Design Engineer because it enables the creation of highly adaptable, space-efficient, and lightweight electronic circuits, facilitating innovative and compact product designs, particularly in applications where space and form factor are critical. It allows for enhanced reliability and durability in dynamic environments, reducing mechanical stress on components.
How to Improve Flex PCB Design Skills
Improving Flex PCB design involves several focused strategies to enhance its reliability, functionality, and manufacturability. Here’s a very short and concise guide for a PCB Design Engineer:
Material Selection: Choose the appropriate material considering the application's flexibility requirements and environmental conditions. Common materials include polyimide and polyester. DuPont offers a range of materials suitable for various applications.
Minimize Bend Radius: To enhance durability, minimize the bend radius of the flex circuits. A general rule is to keep the bend radius at least ten times the thickness of the flex PCB. IPC-2223 provides guidelines on bend radius.
Use Hatched Polygons for Ground Planes: Instead of solid copper, use hatched polygons for ground planes to improve flexibility and reduce the risk of cracking. Altium Designer offers features to easily create hatched polygons.
Strengthen Pad and Via Areas: Reinforce pad and via areas with additional coverlay openings or teardrop shapes to reduce stress concentration and prevent pad lifting. Cadence tools can assist in implementing these reinforcements efficiently.
Employ Anchor Stubs: For components that are not intended to flex, use anchor stubs to secure them firmly and reduce mechanical stress. This technique is crucial for components near bending areas.
Optimize Trace Routing: Maintain uniform trace widths and distances where possible, and avoid sharp angles to reduce stress and potential for breakage. The Mentor Graphics suite offers advanced routing tools for complex flex designs.
Implement Rigid-Flex Transitions Carefully: Where flex circuits connect to rigid boards, ensure smooth transitions and adequate support to prevent mechanical stress at the junctions. The IPC-2223 standard provides recommendations for rigid-flex designs.
Testing and Prototyping: Conduct thorough testing, including dynamic flexing tests, and create prototypes to identify and rectify potential issues early in the design phase.
By incorporating these strategies and utilizing the resources linked, PCB Design Engineers can significantly improve the reliability and performance of Flex PCB designs.
How to Display Flex PCB Design Skills on Your Resume
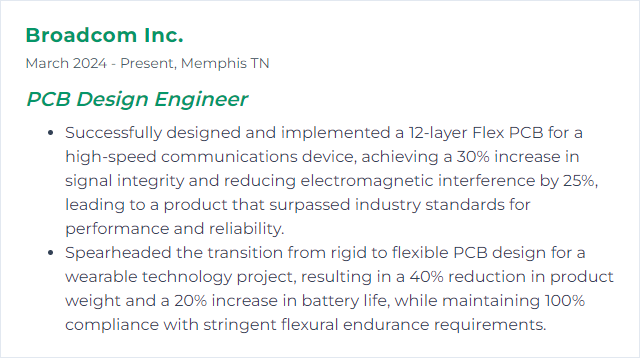