Top 12 Maintenance Director Skills to Put on Your Resume
In the competitive landscape of facility management, a Maintenance Director needs a well-rounded set of skills to stand out and effectively lead maintenance operations. Crafting a resume that highlights these critical skills is essential for capturing the attention of potential employers and securing a role where strategic oversight and operational efficiency are paramount.
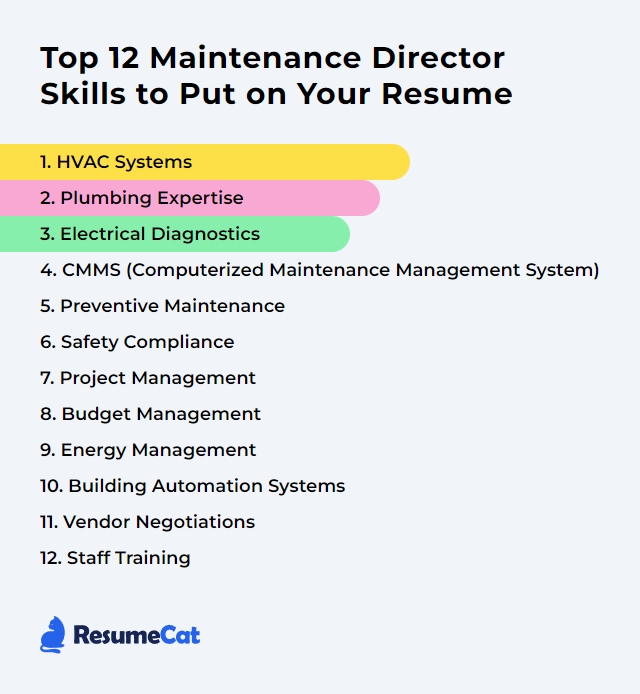
Maintenance Director Skills
- HVAC Systems
- Plumbing Expertise
- Electrical Diagnostics
- CMMS (Computerized Maintenance Management System)
- Preventive Maintenance
- Safety Compliance
- Project Management
- Budget Management
- Energy Management
- Building Automation Systems
- Vendor Negotiations
- Staff Training
1. HVAC Systems
HVAC systems, short for Heating, Ventilation, and Air Conditioning, are integral systems in buildings that regulate indoor temperature, airflow, and air quality to ensure a comfortable and safe environment. For a Maintenance Director, they are critical to manage for operational efficiency, energy conservation, and compliance with health standards.
Why It's Important
HVAC systems are crucial for maintaining indoor air quality, comfort, and safety, ensuring optimal living and working conditions while also managing energy efficiency and reducing operational costs.
How to Improve HVAC Systems Skills
Improving HVAC systems involves a multi-faceted approach focusing on efficiency, performance, and sustainability. Here are concise strategies for a Maintenance Director:
Regular Maintenance: Ensure routine cleaning and inspection of filters, coils, and fans to improve airflow and efficiency. Energy Star provides guidelines on maintenance schedules.
Upgrade Systems: Invest in high-efficiency units which can significantly reduce energy consumption. The Department of Energy offers insights on the latest efficient HVAC technologies.
Smart Controls: Install programmable or smart thermostats to better control temperature and reduce energy waste. Nest and Honeywell provide advanced options.
Air Sealing and Insulation: Improve building envelope to prevent loss of conditioned air, enhancing system efficiency. Building Science Corporation has resources on proper insulation techniques.
Energy Audit: Conduct regular energy audits to identify inefficiencies and areas for improvement. The U.S. Environmental Protection Agency offers guidance on conducting energy audits.
Ductwork Optimization: Ensure ducts are properly sealed and insulated to prevent energy loss. SMACNA provides standards for duct construction and maintenance.
Renewable Energy Integration: Consider integrating solar or geothermal energy to supplement traditional HVAC systems. The National Renewable Energy Laboratory has resources on renewable energy technologies.
Training and Education: Keep staff updated with the latest HVAC technologies and maintenance practices through continuous education. ASHRAE offers courses and certifications for HVAC professionals.
Implementing these strategies will not only improve the performance and efficiency of HVAC systems but also contribute to sustainability and cost savings.
How to Display HVAC Systems Skills on Your Resume
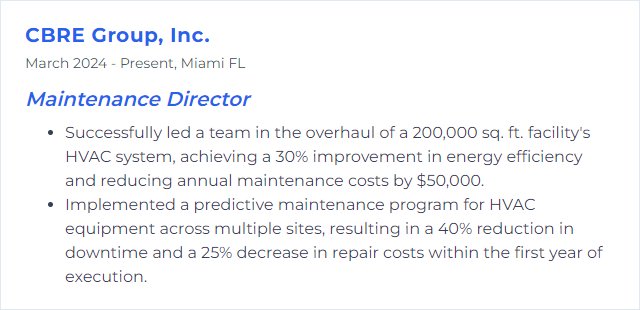
2. Plumbing Expertise
Plumbing expertise refers to the specialized knowledge and skills in installing, maintaining, and repairing plumbing systems, including pipes, fixtures, and water systems, essential for a Maintenance Director to ensure efficient and safe operation of a facility's plumbing infrastructure.
Why It's Important
Plumbing expertise is crucial for a Maintenance Director to ensure the efficient and safe operation of water supply and waste systems, prevent leaks and water damage, and comply with health and building codes, ultimately saving time and reducing costs for facility maintenance.
How to Improve Plumbing Expertise Skills
To improve plumbing expertise as a Maintenance Director, focus on continuous learning, hands-on experience, and leveraging professional networks.
Continuous Learning: Stay updated with the latest plumbing codes, materials, and techniques. Online courses from platforms like Udemy and Coursera can offer structured learning paths.
Hands-On Experience: Practical experience is invaluable. Consider working alongside experienced plumbers or participating in workshops. Organizations like Plumbing-Heating-Cooling Contractors Association (PHCC) provide resources and training opportunities.
Professional Networks: Joining professional networks like LinkedIn and Reddit’s Plumbing Forum can help you connect with experts, share knowledge, and stay informed about industry trends.
By integrating these strategies, you will enhance your plumbing expertise and contribute more effectively to your role as a Maintenance Director.
How to Display Plumbing Expertise Skills on Your Resume
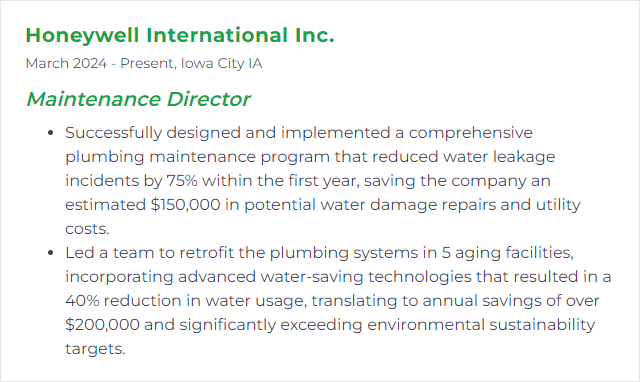
3. Electrical Diagnostics
Electrical diagnostics involve testing and analyzing electrical systems and components to identify faults, inefficiencies, or potential failures, ensuring optimal performance and safety within a facility.
Why It's Important
Electrical diagnostics is essential for ensuring the optimal performance and safety of electrical systems. It helps in identifying problems early, preventing costly repairs, downtime, and potential hazards, thus maintaining operational efficiency and prolonging equipment lifespan.
How to Improve Electrical Diagnostics Skills
Improving electrical diagnostics requires a systematic approach focused on enhancing knowledge, tools, and processes. Here are concise strategies aimed at a Maintenance Director:
Enhance Training: Invest in continuous education for your team. Focus on courses that cover advanced electrical diagnostics techniques. Interplay Learning offers practical, hands-on electrical courses online.
Upgrade Tools: Ensure your team has access to the latest diagnostic tools. Consider tools like advanced multimeters, thermal imagers, and oscilloscopes. Fluke provides a wide range of high-quality diagnostic tools.
Implement a CMMS: A Computerized Maintenance Management System (CMMS) can streamline your maintenance process, making it easier to track, schedule, and analyze electrical maintenance tasks. Fiix Software is a user-friendly CMMS option.
Adopt Predictive Maintenance: Utilize technologies like vibration analysis, infrared thermography, and motor circuit analysis to predict failures before they occur. PdMA offers solutions for motor analysis.
Standardize Procedures: Develop and standardize electrical diagnostic procedures to ensure consistency and efficiency in your maintenance operations. NFPA 70B provides recommended practices for electrical equipment maintenance.
Foster a Safety Culture: Prioritize safety in all electrical diagnostics endeavors. Regularly review and adhere to safety standards such as those from OSHA to minimize risk.
By focusing on these strategies, you can significantly improve the effectiveness of your electrical diagnostics, leading to reduced downtime, enhanced safety, and ultimately, cost savings.
How to Display Electrical Diagnostics Skills on Your Resume
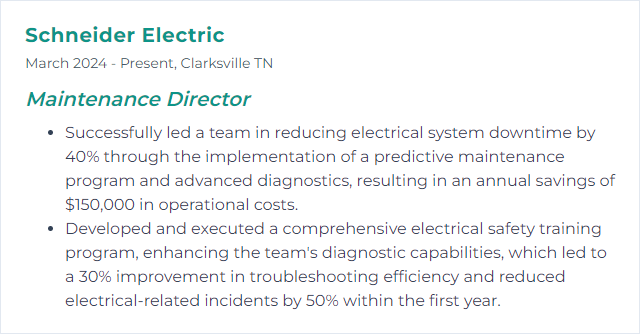
4. CMMS (Computerized Maintenance Management System)
A CMMS (Computerized Maintenance Management System) is a software tool that helps Maintenance Directors streamline and manage all maintenance-related activities, including scheduling, tracking, and reporting on equipment upkeep, work orders, and resources, ensuring operational efficiency and reducing downtime in an organization.
Why It's Important
A CMMS is crucial as it enables a Maintenance Director to streamline operations by automating maintenance scheduling, tracking work orders, managing inventory, and analyzing performance data, leading to increased equipment uptime, cost savings, and enhanced decision-making.
How to Improve CMMS (Computerized Maintenance Management System) Skills
Improving a Computerized Maintenance Management System (CMMS) requires a strategic approach, focusing on system optimization, data accuracy, and user training. Here are key steps for a Maintenance Director to enhance their CMMS:
Conduct a System Audit: Periodically review the CMMS to ensure it meets your current operational needs and identify areas for improvement. Guide to Conducting a CMMS Audit.
Enhance Data Quality: Ensure all asset information, maintenance schedules, and inventory details are up-to-date and accurate. This improves decision-making and system reliability. Data Quality Best Practices.
Integrate with Other Systems: Enhance functionality by integrating your CMMS with other software systems like ERP or IoT devices for real-time data exchange. Benefits of CMMS Integration.
Customize to Fit Needs: Tailor the CMMS features, dashboards, and reports to match your specific maintenance management needs, improving usability and efficiency. Customizing Your CMMS.
Provide Regular Training: Offer ongoing training sessions for all users to ensure they are proficient in using the CMMS and can leverage all its features effectively. Training for CMMS Success.
Implement Preventive Maintenance: Shift from reactive to preventive maintenance strategies within the CMMS to reduce downtimes and extend asset lifespans. Guide to Preventive Maintenance.
Monitor Performance Metrics: Utilize CMMS reporting tools to track maintenance metrics, analyze performance, and identify areas for continuous improvement. Key Performance Indicators for Maintenance.
By focusing on these areas, a Maintenance Director can significantly improve the efficiency and effectiveness of their CMMS, leading to reduced costs, improved asset management, and enhanced operational performance.
How to Display CMMS (Computerized Maintenance Management System) Skills on Your Resume
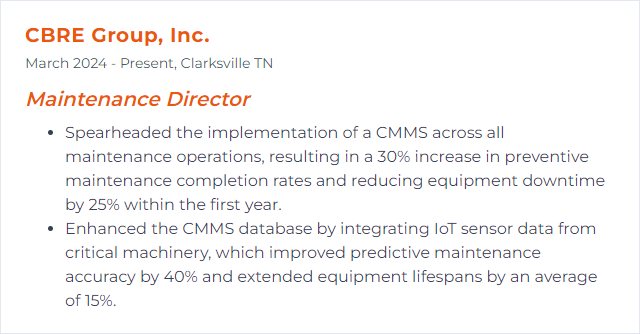
5. Preventive Maintenance
Preventive maintenance is a scheduled maintenance strategy aimed at identifying and mitigating potential equipment failures before they occur to ensure operational efficiency, prolong asset lifespan, and minimize downtime.
Why It's Important
Preventive maintenance is crucial as it minimizes downtime, extends asset life, reduces repair costs, and ensures safety and compliance, ultimately improving operational efficiency and saving the organization money.
How to Improve Preventive Maintenance Skills
Improving Preventive Maintenance (PM) effectively requires a strategic approach focused on optimization, technology integration, and continuous improvement. Here are concise steps for a Maintenance Director to enhance PM:
Assess Current PM Program: Start by thoroughly assessing your current PM activities. Identify gaps, redundancies, and areas for improvement.
Implement a CMMS: Utilize a Computerized Maintenance Management System (CMMS) to streamline scheduling, tracking, and analyzing maintenance tasks. Fiix and UpKeep are popular options.
Adopt Predictive Maintenance Technologies: Incorporate predictive maintenance technologies such as vibration analysis, infrared thermography, and ultrasonic detection to anticipate failures before they occur. Fluke offers a range of tools for this.
Standardize Maintenance Procedures: Develop and standardize maintenance procedures to ensure consistency and efficiency across all operations.
Train and Empower Your Team: Regularly train your maintenance staff on best practices, new technologies, and safety procedures. Encourage a culture of continuous improvement.
Analyze Data and Adjust: Use the data collected from your CMMS and predictive maintenance tools to analyze trends, identify recurring issues, and adjust your PM schedule accordingly.
Engage with Vendors and Experts: Stay informed about the latest in maintenance technologies and practices. Engaging with industry experts and vendors can provide valuable insights and updates.
Review and Revise Regularly: Periodically review the effectiveness of your PM program. Be open to revising your strategies based on performance data and new technologies.
By following these steps and leveraging technology, a Maintenance Director can significantly improve the efficiency and effectiveness of their preventive maintenance program.
How to Display Preventive Maintenance Skills on Your Resume
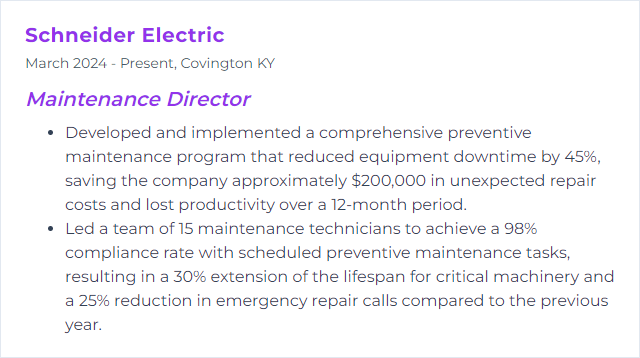
6. Safety Compliance
Safety compliance, in the context of a Maintenance Director, involves ensuring all maintenance activities and operations adhere to established health, safety, and environmental regulations and standards to prevent accidents and injuries.
Why It's Important
Safety compliance is crucial for a Maintenance Director as it ensures the well-being of employees and customers, minimizes legal and financial risks, and maintains the integrity and productivity of operations.
How to Improve Safety Compliance Skills
Improving safety compliance, particularly for a Maintenance Director, involves a multifaceted approach focused on education, enforcement, and continuous improvement. Here are concise strategies to enhance safety compliance:
Conduct Regular Training: Ensure all team members are up-to-date with the latest safety protocols and practices through regular training sessions.
Implement Safety Audits: Regularly audit your facilities and operations to identify and rectify potential hazards.
Engage in Continuous Improvement: Adopt a culture of continuous improvement by encouraging feedback on safety practices from your team and acting on it. Tools like Plan-Do-Check-Act (PDCA) can be instrumental.
Ensure Proper Use of Equipment: Regular checks and maintenance of safety equipment ensure they are always operational. Guidelines from the Equipment Leasing and Finance Association (ELFA) offer insights into managing equipment lifecycle effectively.
Stay Informed on Regulations: Keep abreast of the latest safety regulations and compliance requirements from authoritative sources like OSHA.
Foster a Safety Culture: Encourage a workplace environment where safety is prioritized and valued. Safety Culture offers resources and tools to help build this culture.
By focusing on these areas, a Maintenance Director can significantly improve safety compliance in their operations.
How to Display Safety Compliance Skills on Your Resume
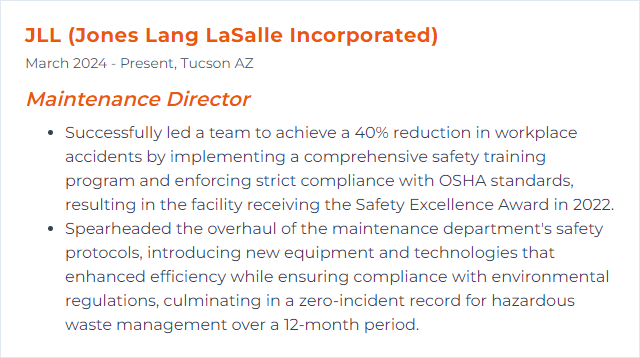
7. Project Management
Project management involves planning, organizing, and overseeing tasks and resources to achieve specific goals within a defined timeline and budget, ensuring that maintenance projects are completed efficiently and effectively.
Why It's Important
Project management is crucial for a Maintenance Director as it ensures efficient organization and execution of maintenance activities, optimizing resource allocation and minimizing downtime, thereby maintaining operational continuity and extending the lifespan of assets.
How to Improve Project Management Skills
Improving project management, especially for a Maintenance Director, involves streamlining processes, enhancing communication, and leveraging technology. Here's a concise guide:
Adopt a Project Management Framework: Implement a structured approach like Agile or Lean to enhance flexibility and efficiency.
Use Project Management Software: Tools like Asana or Trello can help in organizing tasks, tracking progress, and fostering team collaboration.
Prioritize Preventive Maintenance: Shift focus towards preventive maintenance using strategies outlined by Plant Engineering, to reduce downtime and extend asset life.
Enhance Communication: Implement regular check-ins and use platforms like Slack for instant team communication, ensuring everyone is aligned and informed.
Develop Soft Skills: Leadership, problem-solving, and communication are critical. Resources like MindTools offer guidance on improving these skills.
Leverage Data and Analytics: Use data analytics to make informed decisions. Platforms like Power BI can visualize data for better insights into project performance.
Continuous Learning and Improvement: Stay updated with the latest in project management through platforms like Project Management Institute (PMI).
Implementing these strategies can significantly enhance project management capabilities for a Maintenance Director.
How to Display Project Management Skills on Your Resume
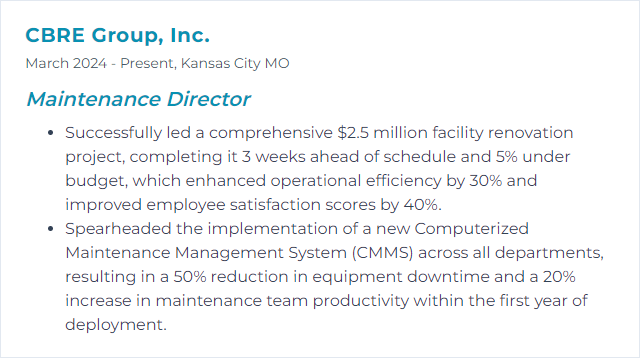
8. Budget Management
Budget management, for a Maintenance Director, involves planning, allocating, and controlling the financial resources allocated for maintenance activities to ensure that all maintenance tasks are completed efficiently and cost-effectively, without exceeding the set financial limits.
Why It's Important
Budget management is crucial for a Maintenance Director as it ensures efficient allocation of resources for preventive and corrective maintenance, minimizes operational costs, and maximizes asset lifespan and performance, directly impacting an organization's profitability and sustainability.
How to Improve Budget Management Skills
Improving budget management, especially for a Maintenance Director, involves strategic planning, monitoring, and optimization of resources. Here are concise steps to enhance budget management:
Set Clear Objectives: Define specific, measurable goals for your maintenance operations. SMART goals framework can be beneficial.
Accurate Budget Forecasting: Use historical data and predictive analysis for more accurate budget forecasting. Tools like QuickBooks can help in creating detailed forecasts.
Prioritize Expenditures: Identify critical maintenance tasks that directly impact operational efficiency and prioritize them in your budget allocation.
Implement a CMMS: A Computerized Maintenance Management System (CMMS) can help in tracking maintenance costs, scheduling preventive maintenance, and managing work orders efficiently.
Regularly Review and Adjust: Continuously monitor budget performance and make necessary adjustments. Use Microsoft Excel or similar tools for tracking and analyzing expenditures.
Optimize Inventory Management: Maintain optimal inventory levels to avoid unnecessary expenses. Inventory management software like PartsBox can automate inventory tracking.
Train Your Team: Ensure your team is well-versed in cost-saving practices and the importance of adhering to the budget. LinkedIn Learning offers courses on budget management and cost reduction.
Engage in Preventive Maintenance: Investing in preventive maintenance can significantly reduce emergency repair costs and downtime. Here’s a guide on Preventive Maintenance best practices.
Negotiate with Vendors: Regularly review and negotiate contracts with suppliers to ensure you're getting the best value for your money.
Leverage Technology: Use technology for better management of resources, scheduling, and energy consumption. Energy management systems, for example, can optimize utility costs.
By following these steps, a Maintenance Director can significantly improve budget management, ensuring that maintenance operations are both efficient and cost-effective.
How to Display Budget Management Skills on Your Resume
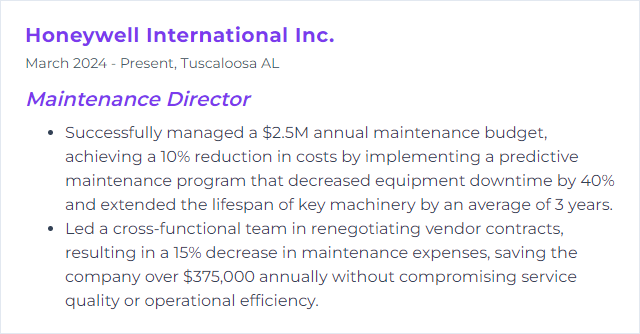
9. Energy Management
Energy management involves overseeing and optimizing energy usage in a facility to reduce costs, improve efficiency, and minimize environmental impact, focusing on the maintenance and operation of systems like HVAC, lighting, and water heating.
Why It's Important
Energy management is crucial for Maintenance Directors because it directly impacts operational efficiency, reduces costs by optimizing energy use, and ensures compliance with environmental regulations, while also enhancing the sustainability and lifespan of facilities.
How to Improve Energy Management Skills
Improving energy management involves a comprehensive approach focusing on optimizing the use of energy across all operations and facilities. For a Maintenance Director, this means:
Assess and Audit: Conduct energy audits to identify where and how energy is being used and wasted. This involves reviewing past energy bills, inspecting equipment, and monitoring energy consumption patterns. Energy Star provides guidelines on conducting energy audits.
Implement Energy-efficient Practices: Introduce energy-efficient practices and technologies. This includes upgrading to LED lighting, optimizing HVAC systems, and installing energy-efficient motors. The Department of Energy offers resources on energy-saving technologies and practices.
Regular Maintenance: Ensure regular maintenance of equipment to keep them running at peak efficiency. This involves cleaning, lubricating, and making adjustments or repairs as needed. The International Facility Management Association provides resources on maintenance best practices.
Employee Training and Engagement: Train staff on energy conservation techniques and encourage their participation in identifying energy-saving opportunities. Resources on employee engagement programs can be found at Energy Star.
Monitor and Optimize: Use energy management systems (EMS) to continuously monitor energy consumption and control energy use in real-time. Information on EMS can be found through the Buildings Performance Institute Europe.
Renewable Energy: Explore opportunities to incorporate renewable energy sources, such as solar or wind, into your energy portfolio. The National Renewable Energy Laboratory offers insights and tools for renewable energy solutions.
Policy and Planning: Develop and enforce energy management policies and procedures. Establish goals and track progress. The International Energy Agency provides guidelines for energy management standards.
Improving energy management is an ongoing process that requires continuous effort and adaptation to new technologies and practices.
How to Display Energy Management Skills on Your Resume
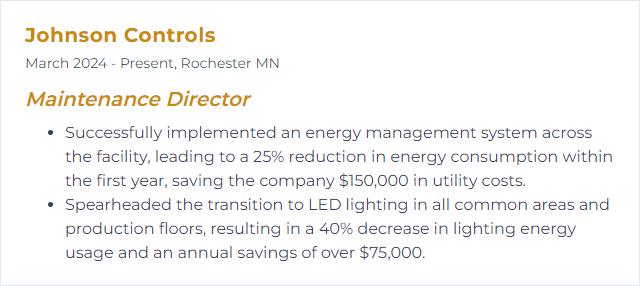
10. Building Automation Systems
Building Automation Systems (BAS) are integrated networks of software and hardware that control a building's environment, including heating, ventilation, air conditioning (HVAC), lighting, and security systems, aimed at improving occupant comfort, efficiently managing energy use, and reducing operational costs. For a Maintenance Director, BAS streamline facility management tasks, enable proactive maintenance strategies, and provide real-time monitoring and data analysis for informed decision-making.
Why It's Important
Building Automation Systems (BAS) are crucial for a Maintenance Director as they enable efficient control and monitoring of the building's mechanical and electrical equipment, such as HVAC, lighting, power systems, and security systems. This results in optimized operation, reduced energy consumption, improved occupant comfort, and proactive maintenance, leading to significant cost savings and enhanced building longevity.
How to Improve Building Automation Systems Skills
To improve Building Automation Systems (BAS) as a Maintenance Director, focus on the following concise strategies:
System Integration: Ensure all components of the BAS, such as HVAC, lighting, and security, are fully integrated for seamless operation and efficiency. Guide to Building Automation Systems.
Regular Updates and Upgrades: Keep the BAS software and hardware updated to leverage the latest features and security patches. Upgrading Building Automation Systems.
Training and Education: Provide ongoing training for staff to ensure they are knowledgeable about system capabilities and best practices. BAS Training Resources.
Preventive Maintenance: Implement a rigorous preventive maintenance schedule to avoid system downtime and extend the life of the BAS components. Preventive Maintenance for BAS.
Energy Monitoring and Management: Use the BAS for continuous energy monitoring to identify inefficiencies and adjust settings for optimal energy use. Energy Management via BAS.
Cybersecurity Measures: Regularly update cybersecurity measures to protect the BAS from external threats and ensure the privacy and security of building operations. Cybersecurity for BAS.
Leverage IoT and AI: Incorporate Internet of Things (IoT) devices and Artificial Intelligence (AI) for predictive maintenance and enhanced operational efficiency. IoT and AI in BAS.
By focusing on these key areas, you can significantly improve the performance and efficiency of Building Automation Systems.
How to Display Building Automation Systems Skills on Your Resume
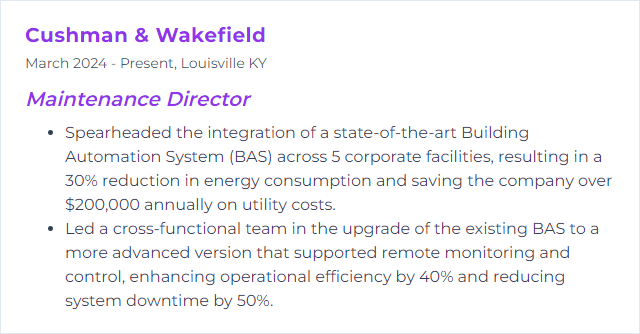
11. Vendor Negotiations
Vendor negotiations for a Maintenance Director involve strategically discussing and agreeing on terms with suppliers to secure the best possible deals on products, services, and contracts essential for maintenance operations, aiming to optimize costs, ensure quality, and guarantee timely delivery.
Why It's Important
Vendor negotiations are crucial for a Maintenance Director to secure quality services and materials at competitive prices, ensuring budget efficiency and optimal facility operations.
How to Improve Vendor Negotiations Skills
Improving vendor negotiations as a Maintenance Director involves strategic planning, communication skills, and understanding your leverage. Here's a concise guide:
Research and Preparation: Understand your needs, the market, and the vendor's position. Harvard Business Review provides insights on negotiation tactics that can be beneficial.
Build Relationships: Establish a good relationship with the vendor for mutual benefits. The Forbes Business Council highlights the importance of strong business relationships.
Effective Communication: Be clear, concise, and assertive in your communication. The MindTools guide on assertiveness offers practical advice.
Leverage Competitiveness: Use competitive bids to your advantage but do so ethically. Investopedia explains competitive bidding processes.
Aim for Win-Win Solutions: Focus on finding solutions that benefit both parties. The Project Management Institute discusses strategies for win-win negotiations.
Understand and Use Leverage: Know your strengths and how to use them effectively in negotiations. The Corporate Finance Institute provides an overview of leverage and its implications.
By applying these strategies, Maintenance Directors can enhance their negotiation skills, leading to better outcomes with vendors.
How to Display Vendor Negotiations Skills on Your Resume
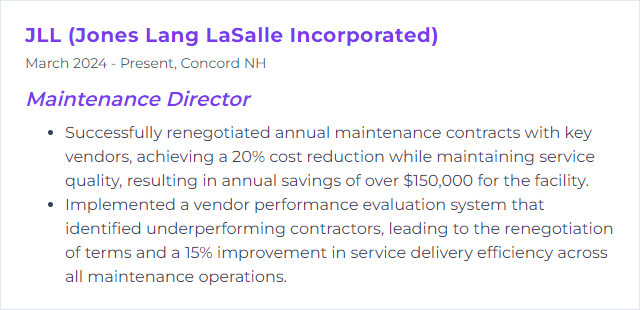
12. Staff Training
Staff training involves educating and equipping employees with the necessary skills, knowledge, and practices required to efficiently perform their duties, specifically tailored for maintenance operations and safety protocols under the guidance of a Maintenance Director.
Why It's Important
Staff training is essential for a Maintenance Director as it ensures the team is skilled and updated on the latest techniques and safety protocols, leading to improved efficiency, reduced downtime, and enhanced compliance with regulations, ultimately contributing to the longevity and reliability of facility operations.
How to Improve Staff Training Skills
Improving staff training, particularly for a Maintenance Director, involves a strategic approach focusing on enhancing skills, knowledge, and safety practices. Here are concise steps for improvement:
Assess Needs: Regularly evaluate the skills and knowledge gaps of your team to tailor training programs effectively. Identify Training Needs.
Blend Learning Methods: Incorporate a mix of learning techniques including hands-on training, online courses, and workshops. This approach caters to different learning styles. Blended Learning Guide.
Utilize Technology: Leverage technology like Learning Management Systems (LMS) for tracking progress and providing accessible resources. Choosing an LMS.
Safety Training: Prioritize safety training to reduce workplace accidents and ensure compliance with regulations. OSHA Training Resources.
Soft Skills Development: Enhance communication, leadership, and problem-solving skills among your maintenance staff. Soft Skills Training.
Feedback and Evaluation: Implement a feedback loop with your team to continuously improve the training process. Feedback Strategies.
Professional Development: Encourage continuous learning and professional development opportunities. Professional Development Strategies.
By adopting these strategies, a Maintenance Director can significantly enhance the effectiveness of staff training, leading to improved performance, safety, and team morale.
How to Display Staff Training Skills on Your Resume
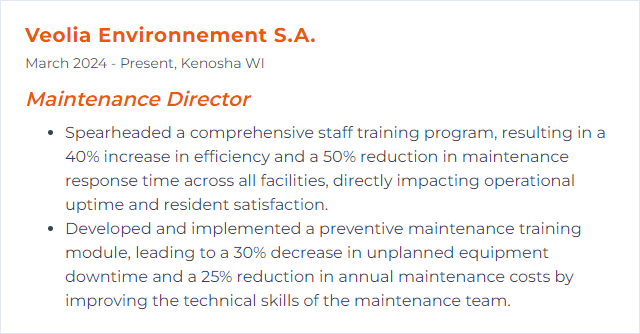