Top 12 Maintenance Manager Skills to Put on Your Resume
In today’s competitive job market, standing out as a maintenance manager requires a well-crafted resume that highlights your unique set of skills. This article will guide you through the top 12 skills essential for maintenance managers, ensuring your resume catches the eye of potential employers and showcases your capabilities effectively.
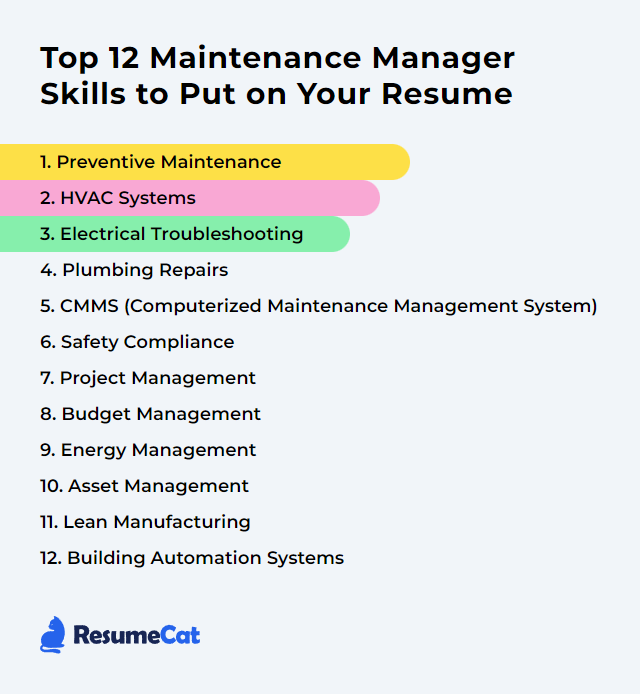
Maintenance Manager Skills
- Preventive Maintenance
- HVAC Systems
- Electrical Troubleshooting
- Plumbing Repairs
- CMMS (Computerized Maintenance Management System)
- Safety Compliance
- Project Management
- Budget Management
- Energy Management
- Asset Management
- Lean Manufacturing
- Building Automation Systems
1. Preventive Maintenance
Preventive maintenance is a scheduled and routine maintenance approach aimed at preventing equipment failures and prolonging asset life by performing regular maintenance tasks, inspections, and replacements at predetermined intervals or based on prescribed criteria, thereby ensuring operational efficiency and reducing the likelihood of unscheduled downtime.
Why It's Important
Preventive maintenance is crucial as it minimizes equipment downtime, extends asset life, reduces repair costs, and ensures operational efficiency and safety, thereby optimizing overall performance and profitability.
How to Improve Preventive Maintenance Skills
To enhance Preventive Maintenance, follow these concise steps:
Assessment: Start by evaluating your current maintenance operations to identify gaps and areas for improvement. Tools like a SWOT analysis can be beneficial.
Plan Development: Create a comprehensive preventive maintenance plan that includes schedules, procedures, and responsibilities. This plan should be based on manufacturers' recommendations and operational experience. Resources like Fiix can help in planning and scheduling.
Training: Ensure your team is well-trained on the latest maintenance techniques and technologies. Platforms like LinkedIn Learning offer courses on various maintenance-related topics.
Technology Utilization: Implement maintenance management software to automate scheduling, tracking, and reporting of maintenance activities. UpKeep and Maintenance Connection are popular options.
Data Analysis: Regularly review maintenance data to identify trends and predict potential failures before they occur. Tools like IBM Maximo provide analytics capabilities for predictive maintenance.
Continuous Improvement: Adopt a culture of continuous improvement by regularly reviewing and updating your preventive maintenance process based on feedback and new insights. The Plan-Do-Check-Act cycle is a valuable methodology for this.
Stakeholder Engagement: Engage with all stakeholders, including maintenance staff, operators, and management, to ensure their input and buy-in for the preventive maintenance program.
By following these steps and leveraging the recommended resources, you can significantly improve your preventive maintenance operations.
How to Display Preventive Maintenance Skills on Your Resume
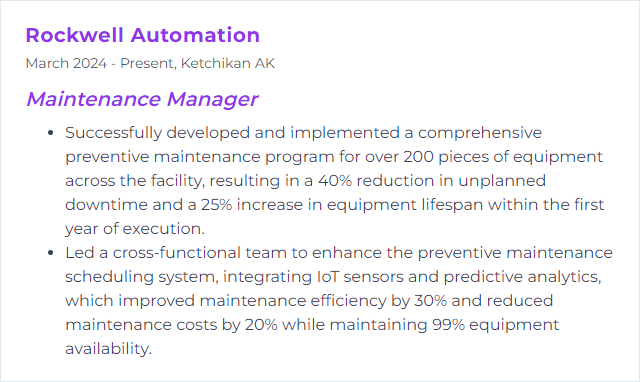
2. HVAC Systems
HVAC systems, or Heating, Ventilation, and Air Conditioning systems, are integral to maintaining indoor air quality, comfort, and temperature control in buildings. For a Maintenance Manager, they involve overseeing the installation, routine care, repair, and optimization of these systems to ensure they operate efficiently and reliably.
Why It's Important
HVAC systems are crucial for maintaining optimal indoor air quality, temperature, and humidity levels, ensuring a comfortable, healthy, and productive environment. They also play a significant role in protecting infrastructure and equipment from damage due to moisture and temperature extremes. For a Maintenance Manager, efficient HVAC operation is vital for reducing energy consumption, minimizing repair costs, and extending the lifespan of the system and associated equipment.
How to Improve HVAC Systems Skills
Improving HVAC systems involves a strategic approach focusing on maintenance, efficiency, and upgrades. As a Maintenance Manager, consider the following concise strategies:
Regular Maintenance: Schedule routine inspections and maintenance to ensure the HVAC system runs efficiently. This includes cleaning filters, checking ducts, and servicing components. (ASHRAE)
Upgrade Filters: Use high-efficiency filters to improve air quality and system performance. (EPA's Guide on Indoor Air Quality)
Seal and Insulate Ducts: Improve system efficiency by sealing leaks and insulating ducts to prevent energy loss. (Energy Star Duct Sealing)
Smart Thermostats: Install smart thermostats for better temperature management and energy savings. (Department of Energy on Programmable Thermostats)
Energy-Efficient Upgrades: Consider upgrading to ENERGY STAR® rated HVAC equipment to enhance efficiency and performance. (ENERGY STAR HVAC)
Ventilation Improvements: Enhance ventilation to control humidity and improve indoor air quality. (ASHRAE Ventilation for Acceptable Indoor Air Quality)
Training for Staff: Ensure your maintenance team is well-trained on the latest HVAC technologies and maintenance practices. (HVAC Excellence)
Implementing these strategies will lead to a more efficient, reliable, and cost-effective HVAC system.
How to Display HVAC Systems Skills on Your Resume
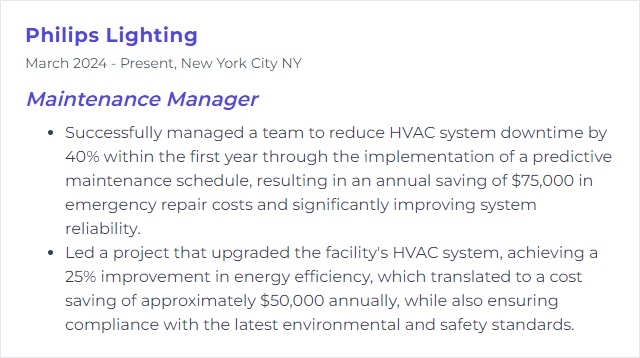
3. Electrical Troubleshooting
Electrical troubleshooting is the systematic process of diagnosing and identifying issues within an electrical system or circuit to find and correct faults, ensuring the system operates efficiently and safely. For a Maintenance Manager, it involves overseeing the application of this process to maintain operational uptime and safety standards.
Why It's Important
Electrical troubleshooting is crucial for a Maintenance Manager as it ensures the safety, efficiency, and reliability of electrical systems, minimizes downtime, and prevents costly equipment failures, contributing to the overall productivity and operational continuity of the facility.
How to Improve Electrical Troubleshooting Skills
Improving electrical troubleshooting skills, particularly for a Maintenance Manager, involves a combination of knowledge enhancement, practical experience, and leveraging the right tools and resources. Here’s a concise guide:
Educate Continuously: Stay updated with the latest electrical codes, standards, and technologies. Online platforms like Coursera and edX offer courses on electrical engineering and maintenance.
Understand Schematics: Master the ability to read and understand electrical schematics and diagrams. Resources like All About Circuits provide valuable insights.
Hands-on Practice: Practical experience is irreplaceable. Use simulators like Troubleshooting - Electrical Circuits for safe, realistic troubleshooting practice.
Use Diagnostic Tools: Familiarize yourself with advanced diagnostic tools. Learn their applications through tutorials on platforms like YouTube.
Implement a Systematic Approach: Adopt a step-by-step approach to troubleshooting, which includes identifying the problem, understanding the system, theorizing potential causes, testing theories, and taking action.
Safety First: Always prioritize safety by following guidelines from authoritative sources such as OSHA.
Leverage Technical Support: Don't hesitate to use manufacturer support and forums for specific equipment issues.
Feedback and Review: After resolving an issue, review the process to identify improvements for future troubleshooting.
By integrating continuous learning, practical application, and leveraging the right tools, you can significantly improve electrical troubleshooting skills in a maintenance environment.
How to Display Electrical Troubleshooting Skills on Your Resume
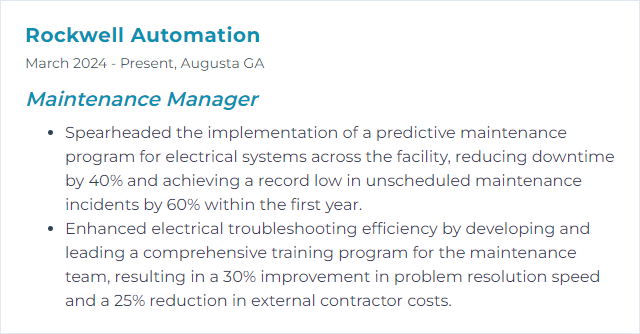
4. Plumbing Repairs
Plumbing repairs involve fixing leaks, unclogging pipes, replacing damaged parts, and maintaining the water supply and waste systems to ensure proper functionality within a facility.
Why It's Important
Plumbing repairs are crucial for maintaining the integrity of a building's infrastructure, ensuring water efficiency, preventing property damage, and safeguarding occupant health by addressing leaks, blockages, and potential contamination risks promptly.
How to Improve Plumbing Repairs Skills
Improving plumbing repairs, especially from a Maintenance Manager's perspective, involves a combination of adopting best practices, leveraging technology, and ensuring your team has the right skills and tools. Here are concise strategies:
Educate Your Team: Continuously train your maintenance staff on the latest plumbing repair techniques and technologies. Online platforms like Coursera and Udemy offer courses that cover a wide range of plumbing topics.
Use Quality Tools and Materials: Invest in high-quality plumbing tools and materials that can withstand regular use and improve repair efficiency. Tools and materials reviews can be found on Home Depot or Lowe's websites.
Implement Preventive Maintenance Software: Adopt preventive maintenance software like Fiix or UpKeep to schedule regular inspections and maintenance, reducing emergency repairs.
Adhere to Codes and Standards: Ensure all repairs comply with local building codes and standards. Reference materials and guidelines are available through the International Plumbing Code (IPC) and American Society of Plumbing Engineers (ASPE).
Encourage Clear Communication: Use project management tools like Trello or Slack to facilitate clear communication among your team, ensuring everyone is informed about repair statuses and schedules.
Regularly Review and Optimize Processes: Continuously assess and refine your plumbing repair processes for efficiency and effectiveness. Feedback tools like SurveyMonkey can help gather insights from your team and clients.
By focusing on these areas, Maintenance Managers can significantly improve the quality and efficiency of plumbing repairs.
How to Display Plumbing Repairs Skills on Your Resume
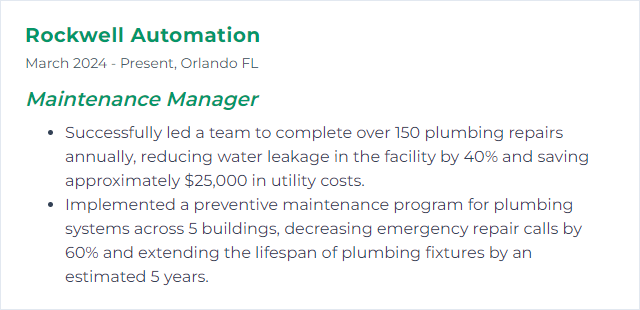
5. CMMS (Computerized Maintenance Management System)
A Computerized Maintenance Management System (CMMS) is a software tool that helps maintenance managers oversee, schedule, and track maintenance activities, manage work orders, maintain historical records of asset repairs, and ensure compliance with regulatory standards, thus enhancing operational efficiency and reducing downtime.
Why It's Important
A CMMS is crucial for a Maintenance Manager as it streamlines maintenance operations, enhances asset lifecycle, ensures compliance, and improves decision-making through real-time data analytics, significantly boosting efficiency and reducing downtime.
How to Improve CMMS (Computerized Maintenance Management System) Skills
Improving a CMMS (Computerized Maintenance Management System) involves streamlining processes, enhancing data accuracy, and ensuring the system is fully utilized to support maintenance operations efficiently. Here are concise strategies for a Maintenance Manager to consider:
Regular Training: Ensure all users undergo regular training to stay updated on features and best practices, enhancing system utilization.
Data Integrity: Focus on maintaining high data quality by regularly reviewing and cleaning data to ensure accurate reporting and decision-making.
Integration: Integrate your CMMS with other business systems (e.g., ERP, IoT devices) for seamless data flow and enhanced functionality. More on integration benefits can be found here.
Customization: Tailor the CMMS to meet your specific operational needs, which can include custom fields, reports, and dashboards. This customization guide provides insights: CMMS Customization.
Performance Monitoring: Implement KPIs (Key Performance Indicators) to monitor system and maintenance performance, facilitating continuous improvement. Explore effective KPIs here.
Feedback Loop: Establish a feedback mechanism for users to suggest improvements, helping to identify pain points and areas for enhancement.
Mobile Accessibility: Ensure the CMMS is accessible via mobile devices to support real-time data entry and access, enhancing efficiency. Insight on mobile CMMS benefits is available here.
By focusing on these areas, a Maintenance Manager can significantly improve the efficiency and effectiveness of their CMMS, driving better maintenance outcomes and operational efficiency.
How to Display CMMS (Computerized Maintenance Management System) Skills on Your Resume
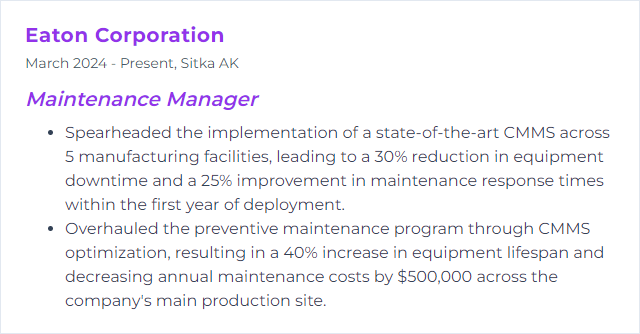
6. Safety Compliance
Safety Compliance, in the context of a Maintenance Manager, refers to ensuring that all maintenance activities and operations adhere to established safety standards and regulations to prevent accidents and ensure the well-being of employees and the environment.
Why It's Important
Safety compliance is crucial for a Maintenance Manager to prevent workplace accidents, ensure legal adherence, reduce liability risks, and maintain a safe, productive environment for all employees.
How to Improve Safety Compliance Skills
Improving safety compliance, especially for a Maintenance Manager, involves a multi-faceted approach focusing on training, regular audits, clear communication, and continuous improvement. Here's a concise guide:
Regular Training: Ensure all team members undergo regular safety training sessions, focusing on both general practices and specific procedures related to their tasks.
Safety Audits: Conduct regular safety audits to identify potential hazards and non-compliance issues, then implement corrective actions promptly.
Clear Communication: Establish clear communication channels for reporting safety concerns or incidents. Use visual aids and signs to remind staff of key safety protocols.
Personal Protective Equipment (PPE): Ensure all staff have access to and understand the importance of using the appropriate PPE for their tasks.
Maintenance Safety Procedures: Develop and enforce strict safety procedures for all maintenance tasks. Regularly review and update these procedures as necessary.
Emergency Preparedness: Regularly review and practice emergency response plans with your team, ensuring everyone knows their role during an emergency.
Feedback and Continuous Improvement: Encourage feedback from staff regarding safety practices and use this to drive continuous improvement. Implement a safety management system that allows for regular review and enhancement of safety practices.
By integrating these strategies, a Maintenance Manager can significantly improve safety compliance within their team or organization, creating a safer work environment for everyone involved.
How to Display Safety Compliance Skills on Your Resume
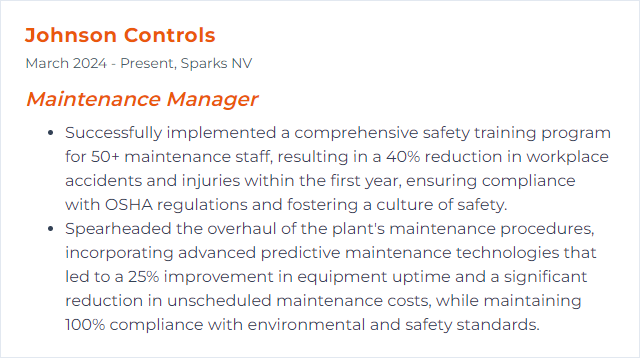
7. Project Management
Project management, in the context of a Maintenance Manager, involves planning, executing, and overseeing maintenance projects to ensure they are completed on time, within budget, and to the required quality standards while minimizing downtime and ensuring asset longevity.
Why It's Important
Project management is crucial for a Maintenance Manager because it ensures efficient organization and execution of maintenance tasks, minimizes downtime, optimizes resource use, and maintains equipment reliability, leading to reduced costs and enhanced operational effectiveness.
How to Improve Project Management Skills
Improving project management, especially for a Maintenance Manager, involves several focused strategies. Here are concise steps to enhance efficiency and effectiveness:
Prioritize Planning: Spend significant time planning before initiating any project. Utilize tools like Gantt charts for scheduling and visualizing project timelines.
Implement Software Tools: Adopt project management software like Asana or Trello to streamline task allocation, communication, and progress tracking.
Regular Training: Engage in continuous learning through PMI certifications to stay updated on best practices and methodologies.
Effective Communication: Foster open communication channels within teams and with stakeholders for timely updates and feedback. Tools like Slack can facilitate instant messaging and collaboration.
Risk Management: Develop a proactive approach to identifying and mitigating risks. Utilize risk management frameworks to prepare and respond to potential setbacks.
Quality Control: Implement quality management systems like Six Sigma or ISO 9001 to ensure that maintenance standards are consistently met or exceeded.
Performance Metrics: Use Key Performance Indicators (KPIs) to measure project success and areas for improvement.
Stakeholder Engagement: Keep stakeholders informed and involved throughout the project lifecycle. Tools like Basecamp can help in centralizing communication and documentation.
Adapt and Flex: Be ready to adapt your plan based on project feedback and changing conditions. Agility is key to dealing with unforeseen challenges.
Post-Project Review: Conduct lessons learned sessions after project completion to gather insights and improve future projects.
Focusing on these areas will help any Maintenance Manager improve their project management capabilities.
How to Display Project Management Skills on Your Resume
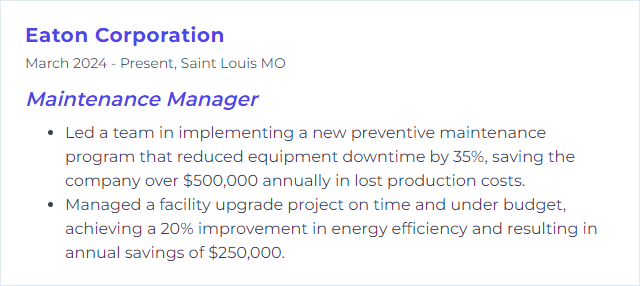
8. Budget Management
Budget management for a Maintenance Manager involves planning, allocating, tracking, and controlling costs within an allocated budget to ensure the maintenance department operates efficiently and effectively, without overspending, while achieving its maintenance goals and objectives.
Why It's Important
Budget management is crucial for a Maintenance Manager to ensure efficient allocation of resources, minimize operational costs, and maintain optimal asset performance, ultimately supporting the organization's financial health and operational continuity.
How to Improve Budget Management Skills
Improving budget management, especially for a Maintenance Manager, involves strategic planning, monitoring, and adjustment. Here are concise steps to enhance budget management:
Understand Your Expenses: Break down your maintenance costs into fixed and variable expenses. This clarity helps in better allocation. Camcode offers insights on cost reduction for maintenance managers.
Prioritize Maintenance Tasks: Use a prioritization system for maintenance tasks to allocate your budget efficiently. Focus on preventive maintenance to reduce unexpected costs. Fiix Software provides guidance on managing maintenance budgets.
Implement a CMMS: A Computerized Maintenance Management System (CMMS) helps in tracking maintenance costs, predicting future expenses, and improving budget allocation. UpKeep offers a robust CMMS solution.
Review and Adjust Regularly: Continuously monitor your budget performance and make necessary adjustments. Regular reviews help in identifying overspending and reallocating resources effectively.
Invest in Training: Investing in your team's training can improve efficiency and reduce costly mistakes. Reliable Plant shares insights on the importance of training in maintenance.
Negotiate with Vendors: Build strong relationships with vendors and negotiate for better rates or bulk discounts. This can significantly reduce your maintenance costs.
Leverage Technology: Utilize technology for predictive maintenance and energy management to save costs in the long run. Energy Star provides resources on energy saving for buildings.
By following these steps and leveraging the resources provided, a Maintenance Manager can significantly improve budget management.
How to Display Budget Management Skills on Your Resume
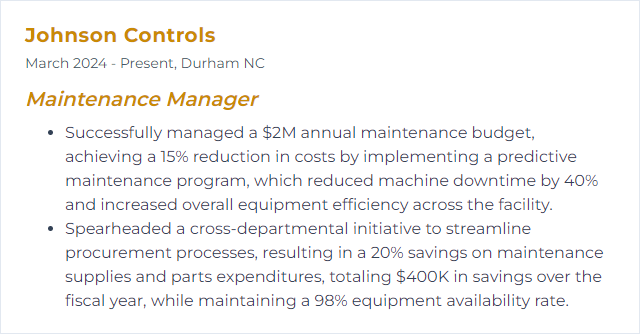
9. Energy Management
Energy Management involves monitoring, controlling, and conserving energy within a facility or organization, focusing on optimizing energy use, reducing costs, and ensuring sustainable operations, which is vital for a Maintenance Manager to maintain efficient and cost-effective facility operations.
Why It's Important
Energy management is crucial for a Maintenance Manager as it helps optimize energy use, reduce operational costs, increase system efficiency, and promote sustainability, ensuring a more profitable and environmentally responsible operation.
How to Improve Energy Management Skills
Improving energy management involves a comprehensive strategy focusing on optimizing the use and efficiency of energy resources. As a Maintenance Manager, you can enhance energy management by:
Conducting Energy Audits: Regularly assess energy use and identify areas for improvement. Energy Star provides guidelines for industrial facilities.
Implementing Preventive Maintenance: Ensure all equipment is running efficiently through routine inspections and maintenance. The U.S. Department of Energy’s Federal Energy Management Program offers a guide on best practices.
Upgrading to Energy-Efficient Equipment: Replace outdated systems with energy-efficient alternatives. The Database of State Incentives for Renewables & Efficiency® (DSIRE) is a comprehensive source of information on incentives and policies that support renewables and energy efficiency in the United States.
Optimizing HVAC Systems: Regular maintenance and upgrades to heating, ventilation, and air conditioning (HVAC) systems can significantly reduce energy consumption. ASHRAE provides standards and guidelines.
Training Staff on Energy Conservation: Educate employees on energy-saving practices and encourage their participation. The Industrial Assessment Centers (IACs) offer training and resources.
Monitoring and Reporting: Use energy management systems (EMS) to track energy consumption and savings. ENERGY STAR Portfolio Manager is a tool for measuring and tracking energy and water consumption, as well as greenhouse gas emissions.
By implementing these strategies, you can significantly improve your facility's energy management.
How to Display Energy Management Skills on Your Resume
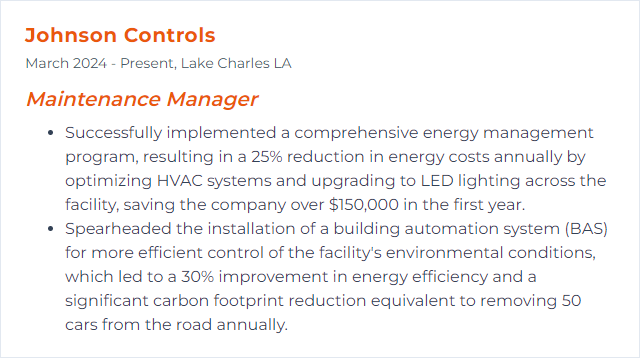
10. Asset Management
Asset Management, in the context of a Maintenance Manager, is the systematic process of developing, operating, maintaining, upgrading, and disposing of assets cost-effectively while ensuring they are in optimal condition to support business objectives.
Why It's Important
Asset management is crucial for a Maintenance Manager as it ensures optimal performance and longevity of assets, reduces downtime and repair costs, and enhances decision-making regarding maintenance, replacement, and investment strategies, ultimately supporting organizational efficiency and profitability.
How to Improve Asset Management Skills
Improving Asset Management as a Maintenance Manager involves strategic planning, efficient execution, and continuous improvement to ensure the longevity and reliability of assets. Here are concise steps to enhance Asset Management:
Implement a Comprehensive Asset Register: Create a detailed list of all assets, including their specifications, location, and condition. This register serves as the foundation for effective asset management. Learn more about asset registers.
Adopt Predictive Maintenance: Shift from reactive to predictive maintenance strategies using IoT sensors and data analytics to predict equipment failures before they occur. Introduction to Predictive Maintenance.
Utilize CMMS/EAM Software: Implement Computerized Maintenance Management Systems (CMMS) or Enterprise Asset Management (EAM) software to streamline maintenance operations, schedule preventive maintenance, and manage work orders efficiently. Benefits of CMMS.
Regular Training for Staff: Ensure that maintenance staff are regularly trained on the latest technologies and best practices in asset management and maintenance. Importance of Training.
Perform Regular Audits and Reviews: Conduct periodic audits of the asset management processes to identify areas for improvement and ensure compliance with industry standards. Guide to Asset Management Audits.
Establish KPIs and Metrics: Define clear Key Performance Indicators (KPIs) and metrics to measure the effectiveness of asset management strategies and make data-driven decisions. Asset Management KPIs.
Engage in Continuous Improvement: Adopt a culture of continuous improvement by regularly reviewing and updating asset management practices based on feedback, audit results, and performance metrics. Continuous Improvement in Maintenance.
By focusing on these key areas, Maintenance Managers can significantly improve the efficiency, reliability, and longevity of their organization's assets.
How to Display Asset Management Skills on Your Resume
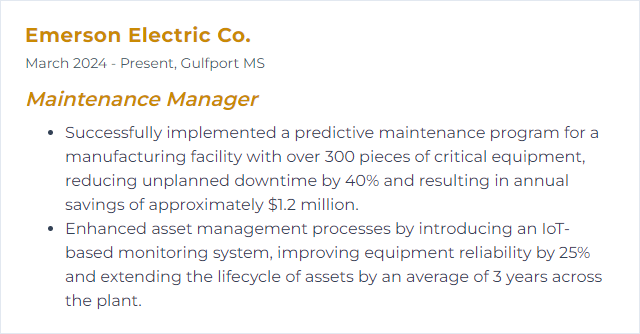
11. Lean Manufacturing
Lean Manufacturing is a systematic approach to eliminating waste and optimizing processes in production to improve efficiency, quality, and productivity, directly impacting maintenance by streamlining equipment upkeep and reducing downtime.
Why It's Important
Lean Manufacturing is important for a Maintenance Manager because it focuses on reducing waste and improving operational efficiency, leading to more reliable equipment, fewer breakdowns, and lower maintenance costs, ultimately enhancing productivity and profitability.
How to Improve Lean Manufacturing Skills
Improving Lean Manufacturing, especially from a Maintenance Manager's perspective, involves optimizing processes, reducing waste, and ensuring equipment reliability. Here are concise strategies:
Implement Total Productive Maintenance (TPM): Focus on proactive and preventive maintenance to maximize the operational efficiency of equipment. Learn more about TPM.
Adopt 5S Methodology: Streamline workspace organization (Sort, Set in order, Shine, Standardize, Sustain) to improve efficiency and safety. Explore 5S Methodology.
Use Root Cause Analysis (RCA): When failures occur, employ RCA to prevent future incidents by addressing the core problem. Understand RCA techniques.
Leverage Predictive Maintenance: Utilize data and technology (like IoT sensors) to predict when maintenance should be performed to prevent unexpected equipment failures. Discover Predictive Maintenance.
Continuously Train Maintenance Team: Ensure your team is knowledgeable about lean principles and the latest maintenance strategies. Check out training resources.
Engage in Cross-functional Collaboration: Work closely with other departments (e.g., production, quality) to identify improvement opportunities and align goals. Read about collaboration in Lean.
By focusing on these areas, a Maintenance Manager can significantly contribute to a leaner, more efficient manufacturing environment.
How to Display Lean Manufacturing Skills on Your Resume
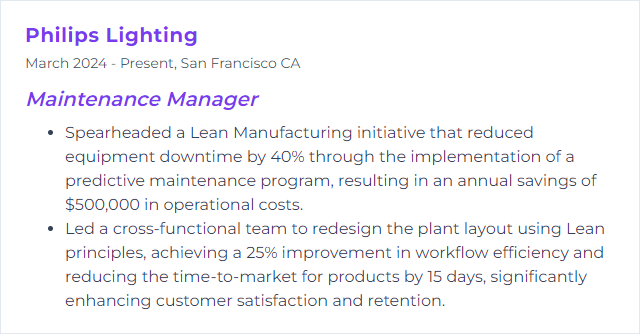
12. Building Automation Systems
Building Automation Systems (BAS) are integrated networks of software and hardware that control and monitor various building services such as lighting, HVAC (heating, ventilation, and air conditioning), security, and fire systems. For a Maintenance Manager, BAS streamline operations, enhance energy efficiency, and reduce manual intervention by automating routine tasks and providing real-time data and alerts for proactive maintenance.
Why It's Important
Building Automation Systems (BAS) are important for Maintenance Managers because they streamline building operations, enhance energy efficiency, reduce operational costs, and improve overall system reliability and lifespan, ensuring optimal performance and comfort with minimal manual intervention.
How to Improve Building Automation Systems Skills
Improving Building Automation Systems (BAS) involves optimizing efficiency, enhancing control, and ensuring system reliability. Here are concise strategies tailored for a Maintenance Manager:
System Integration: Ensure your BAS interfaces seamlessly with all building systems (HVAC, lighting, security) for centralized control. ControlTrends offers insights on integration techniques.
Software Updates: Regularly update your BAS software to leverage the latest features and security patches. AutomatedBuildings.com provides updates on new software releases.
Energy Management: Utilize your BAS for energy monitoring and management to identify savings opportunities. The U.S. Department of Energy’s Building Technologies Office offers resources on energy-efficient practices.
Preventive Maintenance: Implement a preventive maintenance schedule for your BAS components to reduce downtime and extend system life. FacilitiesNet provides guidelines on preventive maintenance strategies.
Training: Ensure staff are trained on the BAS operations and updates to maximize system potential. The Building Automation Systems Training Program offers courses tailored for facility managers.
Data Analysis: Utilize BAS data analytics to make informed decisions on building operations and improvements. International Society of Automation offers resources on utilizing automation data effectively.
By focusing on these areas, you can enhance the efficiency and reliability of your Building Automation Systems, ensuring a comfortable, safe, and cost-effective environment.
How to Display Building Automation Systems Skills on Your Resume
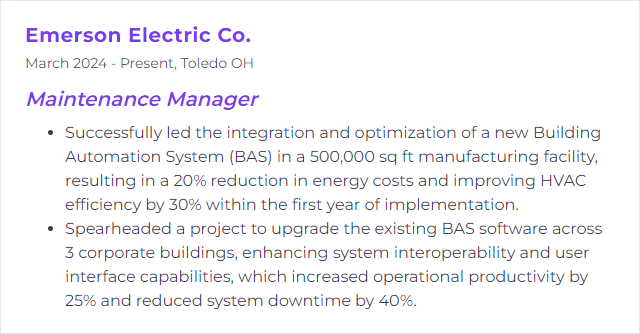