Top 12 Industrial Electrician Skills to Put on Your Resume
In today's competitive job market, standing out as an industrial electrician requires more than just technical proficiency. Highlighting a robust set of skills on your resume can demonstrate your versatility and readiness to tackle complex industrial challenges, making you a top candidate for employers.
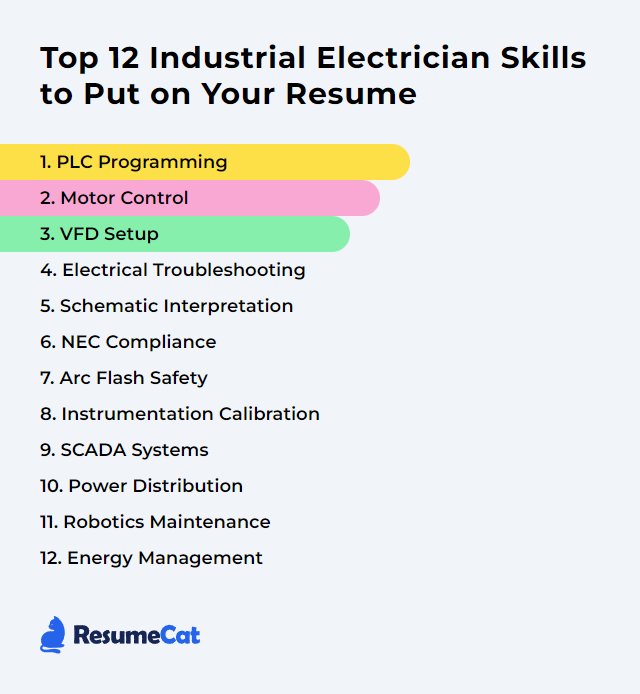
Industrial Electrician Skills
- PLC Programming
- Motor Control
- VFD Setup
- Electrical Troubleshooting
- Schematic Interpretation
- NEC Compliance
- Arc Flash Safety
- Instrumentation Calibration
- SCADA Systems
- Power Distribution
- Robotics Maintenance
- Energy Management
1. PLC Programming
PLC programming involves creating and modifying computer code to control the operation of industrial machinery and processes via Programmable Logic Controllers (PLCs). It allows electricians to automate equipment, ensuring efficient and precise control over manufacturing or operational tasks.
Why It's Important
PLC programming is crucial for an Industrial Electrician as it enables the automation, control, and monitoring of industrial machinery and processes, ensuring efficiency, safety, and reliability in manufacturing and production environments.
How to Improve PLC Programming Skills
Improving PLC programming skills, especially for an industrial electrician, involves continuous learning and practice. Here's a concise guide:
Understand the Basics: Ensure you have a solid foundation in PLC basics, including understanding ladder logic, function blocks, and structured text. PLC Academy offers a comprehensive starting point.
Practice Regularly: Hands-on experience is crucial. Use simulation software like PLCLogix to practice without needing physical hardware.
Learn from Real Projects: Study existing programs and reverse-engineer them to understand their structure and logic. Websites like PLCtalk can be a valuable resource for real-world examples and discussions.
Stay Updated: The field of PLC programming is always evolving. Follow industry news and updates through platforms like Automation.com.
Certifications and Courses: Consider taking courses or earning certifications from recognized bodies such as Siemens or Rockwell Automation.
Join Forums and Groups: Engage with online communities on sites like PLCS.net to exchange knowledge, tips, and get answers to your queries.
Apply Best Practices: Learn and apply industry best practices in your programming. This includes proper documentation, using consistent naming conventions, and modular programming.
By following these steps and leveraging the resources mentioned, you can significantly improve your PLC programming skills as an industrial electrician.
How to Display PLC Programming Skills on Your Resume
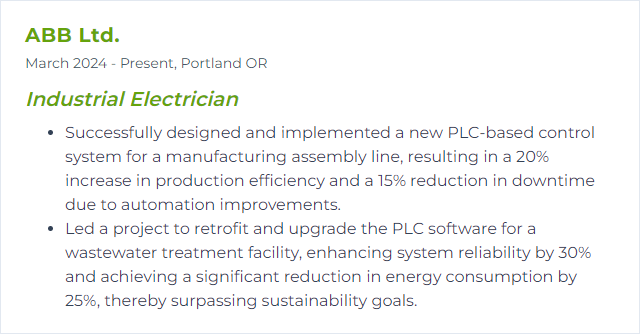
2. Motor Control
Motor control refers to the process of regulating or managing the performance of an electric motor in an industrial setting. It involves starting, stopping, controlling speed, direction, and protecting against overloads or faults.
Why It's Important
Motor control is crucial for an industrial electrician because it enables precise management of machine operations, improving efficiency, safety, and reliability in industrial settings.
How to Improve Motor Control Skills
Improving motor control, especially in an industrial setting, involves enhancing both the efficiency and safety of motor operation. As an industrial electrician, focusing on the following areas can lead to significant improvements:
Understand Motor Basics: Begin with a solid understanding of motor principles, types, and operations. ABB's motor guide is an excellent resource.
Learn Control Techniques: Familiarize yourself with various motor control techniques such as Direct On Line (DOL), Star-Delta, and Variable Frequency Drives (VFDs). Schneider Electric provides insights on VFDs and soft starters.
Implement Regular Maintenance: Proper maintenance prevents failures and extends motor life. IEEE's guide on motor maintenance outlines best practices.
Use Proper Protective Devices: Ensure motors are equipped with the right protective devices to prevent damage. Littelfuse's motor protection guide discusses various options.
Upgrade Your Skills: Continuously improve your knowledge and skills through courses and certifications. PLC Programming and motor control courses on platforms like Udemy and Coursera can be valuable.
Stay Updated: Keep up with the latest technologies and practices in motor control by reading industry publications and joining professional forums.
By focusing on these areas, you can significantly improve motor control in your industrial environment, enhancing both performance and safety.
How to Display Motor Control Skills on Your Resume
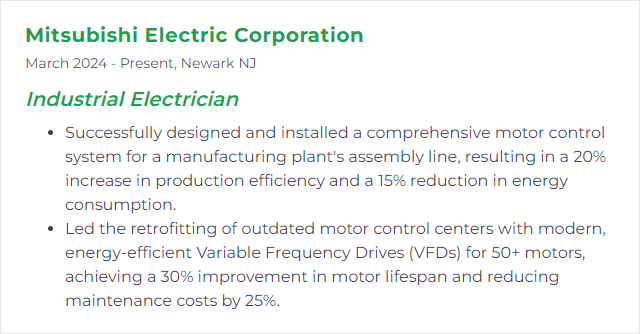
3. VFD Setup
A VFD Setup involves configuring a Variable Frequency Drive to control the speed, torque, and direction of an electric motor in industrial applications, optimizing performance, energy efficiency, and process control.
Why It's Important
A VFD (Variable Frequency Drive) setup is crucial in industrial settings as it allows for precise control of motor speed, improves energy efficiency, and extends the life of mechanical equipment, leading to significant cost savings and operational efficiency for an industrial electrician's tasks.
How to Improve VFD Setup Skills
Improving a Variable Frequency Drive (VFD) setup in an industrial setting involves optimizing performance, ensuring safety, and enhancing efficiency. Here’s a very short and concise guide:
Correct Sizing: Choose a VFD with the appropriate power rating for the motor. This ensures efficiency and longevity. ABB's guide provides insights on sizing VFDs correctly.
Proper Installation: Follow manufacturer guidelines for installation, including input and output wiring, grounding, and environmental considerations (temperature, humidity). Schneider Electric's installation tips can be very helpful.
Parameter Configuration: Configure VFD parameters according to the motor and application requirements. This includes setting the correct motor parameters, acceleration/deceleration times, and limits on current and voltage. Siemens offers a comprehensive parameter manual for their drives.
EMI and RFI Mitigation: Use shielded cables, proper grounding, and install EMI filters if necessary to reduce electromagnetic and radio frequency interference. Rockwell Automation discusses techniques for reducing EMI.
Preventive Maintenance: Regularly inspect and maintain the VFD and associated equipment. Check for dirt accumulation, terminal tightness, and signs of wear. Eaton’s preventive maintenance guide can be a good resource.
Thermal Management: Ensure adequate cooling for the VFD. This may involve checking the cooling fan, heat sink, and the ambient temperature of the installation location. Yaskawa's thermal management tips provide valuable insights.
Use of Dynamic Braking: In applications with high inertia loads, consider using dynamic braking to safely and efficiently bring the load to a stop. Mitsubishi Electric explains dynamic braking in their VFDs.
By adhering to these guidelines, an industrial electrician can significantly improve the performance and reliability of a VFD setup.
How to Display VFD Setup Skills on Your Resume
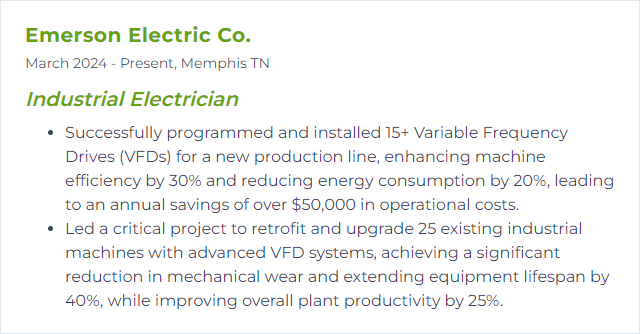
4. Electrical Troubleshooting
Electrical troubleshooting in the context of an industrial electrician involves systematically diagnosing and identifying issues within electrical systems or circuits to find and correct faults, ensuring the efficient operation of industrial machinery and equipment.
Why It's Important
Electrical troubleshooting is crucial for an industrial electrician because it ensures the safe, efficient, and continuous operation of industrial systems and machinery, prevents downtime, and minimizes the risk of electrical hazards and costly repairs.
How to Improve Electrical Troubleshooting Skills
To improve electrical troubleshooting as an Industrial Electrician, follow these concise steps:
Understand Schematics: Master reading and interpreting electrical schematics and wiring diagrams. Resources like All About Circuits provide foundational knowledge.
Use the Right Tools: Equip yourself with essential tools like a multimeter, clamp meter, and insulation resistance tester. Fluke offers a range of high-quality troubleshooting tools.
Safety First: Always adhere to safety protocols. OSHA’s Electrical Safety guidelines are crucial for preventing accidents.
Hands-On Practice: Apply your skills in real-world scenarios. Online platforms like PLC Academy offer practical exercises and simulations.
Continuous Learning: Keep updating your knowledge. Websites like Electrician Talk host forums for sharing experiences and advice.
By focusing on these areas, you can significantly enhance your electrical troubleshooting skills in an industrial setting.
How to Display Electrical Troubleshooting Skills on Your Resume
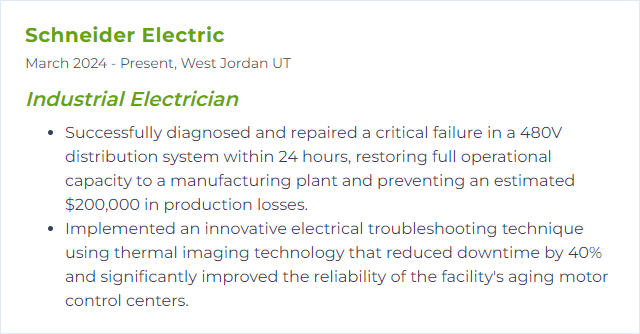
5. Schematic Interpretation
Schematic interpretation involves understanding and analyzing electrical diagrams or schematics to identify the components, connections, and functionality of electrical systems, essential for troubleshooting, installation, and maintenance tasks performed by an industrial electrician.
Why It's Important
Schematic interpretation is crucial for an industrial electrician because it enables the accurate installation, troubleshooting, and maintenance of complex electrical systems, ensuring safety and operational efficiency in industrial environments.
How to Improve Schematic Interpretation Skills
Improving schematic interpretation skills, especially for an industrial electrician, involves enhancing your understanding of electrical diagrams and symbols, practicing reading various schematics, and staying updated with industry standards. Here's a concise guide:
Understand Basic Symbols: Start with mastering the basic symbols used in electrical schematics. This guide from Electrical Engineering Portal provides a comprehensive list of symbols.
Learn Schematic Structures: Different industries might use various schematic styles. Familiarize yourself with the structures commonly used in your field. AutomationDirect offers a useful introduction.
Practice Regularly: Practice reading different schematics. Try to redraw them from memory or explain their functions. Websites like All About Circuits offer plenty of resources for practice.
Use Simulation Software: Engage with simulation software like LTspice to create and analyze circuits, helping reinforce your understanding of how schematics translate to real-world applications.
Stay Updated: Electrical standards and symbols evolve. Regularly consult resources like the National Electrical Code (NEC) and join forums such as Mike Holt’s Forum to stay informed on the latest changes and interpretations.
Remember, improving your schematic interpretation is a continuous process that requires consistent effort and curiosity.
How to Display Schematic Interpretation Skills on Your Resume
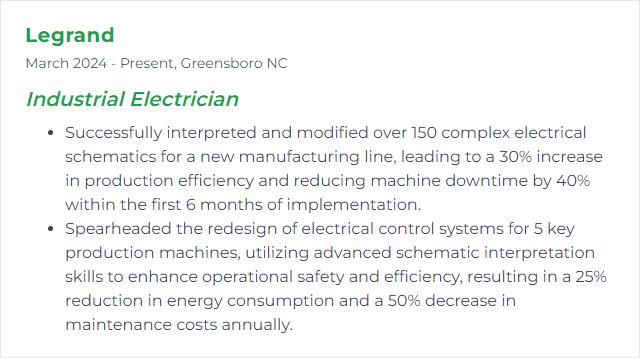
6. NEC Compliance
NEC Compliance refers to adherence to the National Electrical Code, a set of standards designed to ensure safe electrical installations and practices in the United States, specifically applicable to the work of industrial electricians in the design, installation, and maintenance of electrical systems.
Why It's Important
NEC compliance is crucial for an industrial electrician because it ensures electrical systems are installed safely and correctly, reducing the risk of electrical fires, shocks, and other hazards, thus protecting workers, equipment, and facilities.
How to Improve NEC Compliance Skills
Improving NEC (National Electrical Code) compliance as an industrial electrician involves staying updated on code changes, thorough planning, and continuous learning. Here are concise steps to enhance NEC compliance:
Stay Informed: Regularly review the NEC updates to stay current with the latest standards.
Continuing Education: Enroll in continuing education courses focused on NEC to deepen your understanding and application of the code.
Use NEC Resources: Utilize NEC handbooks and guides for a comprehensive understanding of code requirements and practical applications.
Field Practice: Apply NEC rules diligently in every project. Regularly review your work for compliance and learn from any mistakes to prevent future issues.
Collaborate and Network: Engage with fellow electricians and professionals through forums like Mike Holt's Forum to share knowledge, tips, and experiences related to NEC compliance.
Inspection Readiness: Always prepare and maintain documentation and projects to be inspection-ready, ensuring compliance with NEC standards.
Adhering to these steps will significantly enhance your NEC compliance as an industrial electrician.
How to Display NEC Compliance Skills on Your Resume
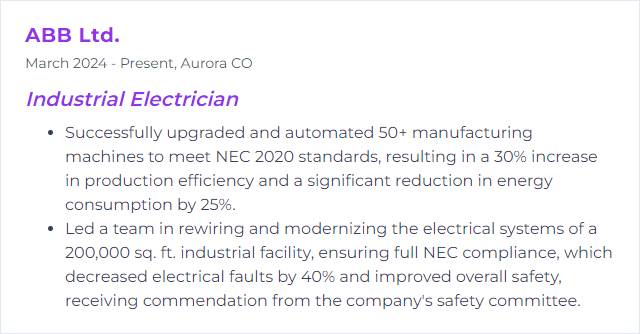
7. Arc Flash Safety
Arc flash safety refers to the practices, equipment, and regulations designed to protect industrial electricians from arc flash hazards—a sudden, explosive release of electrical energy that occurs during a fault in electrical equipment, capable of causing severe burns, blindness, and even death. This includes the use of personal protective equipment (PPE), adherence to safety standards like NFPA 70E, and proper training to prevent and mitigate risks associated with arc flash incidents.
Why It's Important
Arc flash safety is crucial for industrial electricians because it prevents severe burns, blindness, hearing loss, and fatal injuries caused by explosive energy releases during electrical faults, ensuring their safety and well-being while working with high voltage systems.
How to Improve Arc Flash Safety Skills
Improving Arc Flash Safety for an industrial electrician involves a multi-faceted approach focusing on risk assessment, preventive measures, and adherence to safety standards. Here is a concise guide:
Risk Assessment: Conduct regular arc flash risk assessments to identify potential hazards and determine the necessary level of personal protective equipment (PPE).
Labeling: Ensure all electrical equipment is properly labeled with arc flash warning labels, indicating the arc flash boundary and required PPE.
Training: Provide comprehensive training for all electricians on arc flash hazards, safety procedures, and the correct use of PPE.
Use of PPE: Ensure electricians always wear appropriate PPE, including flame-resistant clothing, gloves, face shields, and other gear based on the identified risk level.
Safe Work Practices: Implement and enforce safe work practices, such as establishing an electrically safe work condition by de-energizing and grounding circuits before work begins, as recommended by NFPA 70E.
Tools and Equipment: Use insulated tools and equipment to reduce the risk of arc flash when working on or near live parts.
Maintenance: Regularly maintain electrical systems and equipment to ensure they are in good condition, reducing the risk of faults that can cause arc flashes.
By following these guidelines, an industrial electrician can significantly improve arc flash safety in their work environment.
How to Display Arc Flash Safety Skills on Your Resume
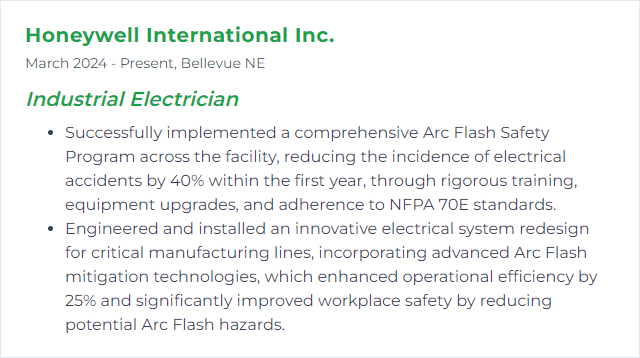
8. Instrumentation Calibration
Instrumentation calibration is the process of configuring and adjusting instruments in an industrial setting to ensure they provide accurate and precise measurements, essential for maintaining optimal performance and safety in electrical systems and machinery operations.
Why It's Important
Instrumentation calibration is crucial for ensuring accurate and reliable measurements, essential for maintaining process control, safety, and regulatory compliance in industrial settings.
How to Improve Instrumentation Calibration Skills
Improving instrumentation calibration in an industrial setting involves precise steps to ensure accuracy and reliability of instruments. Follow these concise guidelines:
Understand Instrument Specifications: Before calibration, thoroughly understand the instrument's specifications and requirements. This ensures you calibrate within the correct parameters.
Use Certified Standards: Always use certified reference materials or standards for calibration. These should be traceable to national or international standards.
Regular Calibration Schedule: Implement a regular calibration schedule based on the manufacturer’s recommendations and instrument usage to maintain accuracy over time.
Proper Calibration Techniques: Use the correct calibration techniques as specified by the instrument manufacturer or industry standards. This might involve comparison with a known standard, zero adjustments, and span adjustments.
Calibration Environment: Ensure the calibration environment is suitable. Environmental conditions such as temperature and humidity should be stable and within specified limits.
Record Keeping: Maintain detailed calibration records for each instrument. This should include date, time, technician, methods used, and calibration results.
Training: Ensure that personnel involved in calibration are properly trained. This includes understanding calibration procedures, instrument handling, and interpretation of results.
Review and Adjust Calibration Frequency: Regularly review calibration data to adjust calibration frequency. Instruments that consistently show little to no drift may require less frequent calibration, whereas those with significant drift may need more.
Use of Calibration Software: Consider using calibration management software to automate calibration schedules, record-keeping, and to ensure compliance with industry standards.
Improving instrumentation calibration is a continuous process that requires attention to detail, adherence to standards, and a commitment to quality.
How to Display Instrumentation Calibration Skills on Your Resume
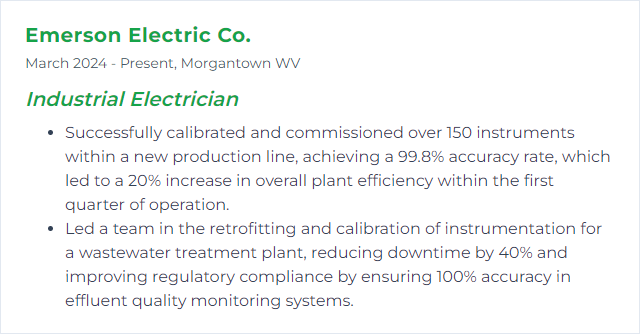
9. SCADA Systems
SCADA (Supervisory Control and Data Acquisition) systems are computer-based systems used by industrial electricians to monitor and control industrial, infrastructure, or facility-based processes, allowing for real-time data collection, control, and analysis to ensure efficiency and reliability in operations.
Why It's Important
SCADA systems are crucial for industrial electricians as they provide real-time monitoring and control of electrical systems, enhancing efficiency, reliability, and safety in industrial operations.
How to Improve SCADA Systems Skills
Improving SCADA (Supervisory Control and Data Acquisition) systems involves several key strategies, particularly from an industrial electrician's perspective. Here's a concise guide:
Enhance Security: Implement advanced cybersecurity measures to protect against unauthorized access and attacks. Regularly update software and hardware components to patch vulnerabilities. The National Institute of Standards and Technology (NIST) offers guidelines for improving industrial control systems security.
Upgrade Hardware: Ensure all hardware components are up-to-date and capable of handling increased loads. This may include upgrading PLCs (Programmable Logic Controllers), RTUs (Remote Terminal Units), and communication infrastructure. Rockwell Automation provides a range of modern industrial control products.
Implement Redundancy: Design systems with redundancy to improve reliability and availability. This involves having backup systems in place to take over in case of a primary system failure. Schneider Electric offers solutions for building redundancy in industrial settings.
Optimize Network Infrastructure: Ensure the network infrastructure is optimized for speed and reliability. This includes proper segmentation, use of industrial-grade switches, and secure wireless communication where necessary. Cisco provides comprehensive industrial networking solutions.
Regular Training and Updates: Continuously train staff on the latest technologies and best practices in SCADA systems management. This ensures that the team can efficiently operate and troubleshoot the system. ISA (International Society of Automation) offers training courses for professionals.
Data Management and Analysis: Implement advanced data analytics tools to make informed decisions based on real-time data. This can help in predictive maintenance, energy management, and improving overall efficiency. Siemens offers SCADA systems with integrated data analytics capabilities.
Regular Maintenance and Audits: Conduct regular maintenance checks and system audits to ensure everything is functioning as expected. This helps in identifying and rectifying issues before they escalate. ABB provides comprehensive maintenance services for SCADA systems.
By focusing on these areas, industrial electricians can significantly enhance the performance, reliability, and security of SCADA systems, ensuring they meet the demands of modern industrial operations.
How to Display SCADA Systems Skills on Your Resume
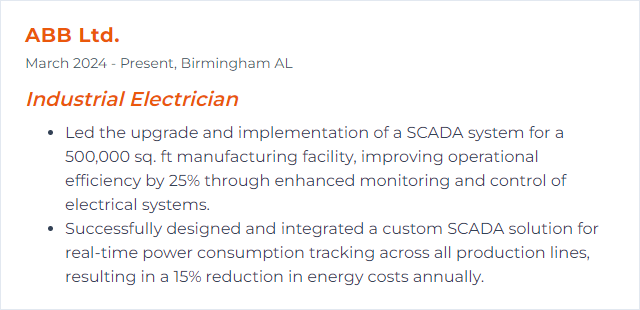
10. Power Distribution
Power distribution in an industrial setting involves the process of distributing electrical power from a centralized source to various machinery, equipment, and areas within a facility, ensuring safe, efficient, and reliable electricity supply to meet operational needs.
Why It's Important
Power distribution is crucial for ensuring a reliable, efficient, and safe supply of electricity to different machinery and equipment in an industrial setting, enabling optimal operation, minimizing downtime, and safeguarding against electrical hazards.
How to Improve Power Distribution Skills
Improving power distribution in an industrial setting involves several key strategies aimed at enhancing efficiency, reliability, and safety. As an industrial electrician, focusing on these areas can lead to significant improvements:
Conduct a thorough assessment of the existing power distribution system to identify inefficiencies and areas for improvement. This includes evaluating the age, condition, and capacity of equipment.
Implement a regular maintenance schedule for all components of the power distribution system, including transformers, switchgear, and distribution panels, to prevent failures and extend equipment life. Electrical Preventive Maintenance (EPM).
Upgrade outdated equipment with modern, energy-efficient alternatives that can handle current and future load requirements more effectively. This may involve replacing old transformers, switchgear, and cables with more efficient models. Energy Efficient Equipment Upgrades.
Enhance power quality by installing power factor correction devices and harmonic filters to reduce losses and improve the efficiency of the power distribution system. Poor power quality can lead to inefficiencies and equipment damage. Power Quality Improvement.
Integrate renewable energy sources (such as solar or wind) into the power distribution system to reduce dependency on non-renewable energy sources and lower energy costs. Integrating Renewable Energy.
Implement smart grid technology to allow for real-time monitoring and control of the power distribution system, improving response times to outages and optimizing energy use. Smart Grids and Industrial Automation.
Ensure proper grounding and bonding of all equipment to improve safety and reduce the risk of electrical shock and equipment damage. Grounding and Bonding.
Educate and train staff on the latest best practices, safety standards, and energy management strategies to ensure they can identify issues and implement improvements effectively. Workplace Electrical Safety.
By focusing on these strategies, an industrial electrician can significantly improve the power distribution system's efficiency, reliability, and safety.
How to Display Power Distribution Skills on Your Resume
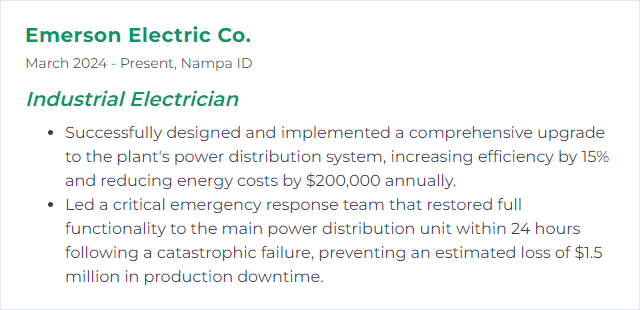
11. Robotics Maintenance
Robotics maintenance involves the upkeep, repair, and regular servicing of industrial robots to ensure their optimal performance and reduce downtime in manufacturing processes. This includes tasks such as software updates, mechanical adjustments, and troubleshooting for an industrial electrician.
Why It's Important
Robotics maintenance is crucial for ensuring consistent production efficiency, minimizing costly downtime, and extending the lifespan of robotic systems, thereby safeguarding investments and maintaining safety standards in industrial environments.
How to Improve Robotics Maintenance Skills
Improving robotics maintenance, especially for an industrial electrician, involves a blend of preventive maintenance, regular training, and the use of modern tools and technologies. Here are concise strategies:
Preventive Maintenance: Schedule regular inspections and maintenance tasks to prevent equipment failures. Rockwell Automation offers insights on predictive maintenance technologies.
Training and Education: Stay updated with the latest robotics technologies and maintenance techniques. Platforms like LinkedIn Learning provide courses on robotics and automation.
Use of Diagnostic Tools: Incorporate advanced diagnostic tools and software for timely identification of issues. Fluke offers a range of electrical diagnostic tools suitable for industrial applications.
Implement a CMMS: A Computerized Maintenance Management System (CMMS) like Fiix can help manage maintenance schedules, inventory, and work orders efficiently.
Safety and Compliance: Always adhere to safety standards and regulations. OSHA’s Guidelines for Robotics Safety in the Workplace provide essential safety measures.
Collaboration with Manufacturers: Work closely with robot manufacturers for support and access to original parts and service manuals. This can also include attending workshops or webinars they offer.
By focusing on these areas, an industrial electrician can significantly improve the efficiency and reliability of robotics maintenance in an industrial setting.
How to Display Robotics Maintenance Skills on Your Resume
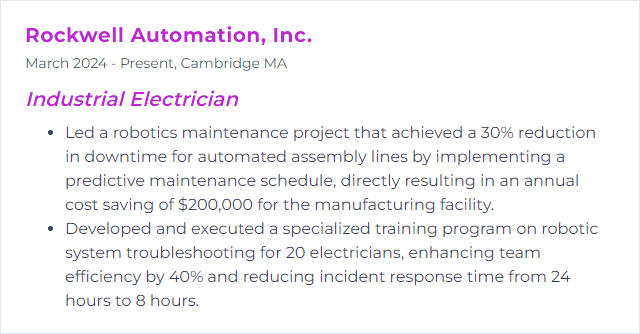
12. Energy Management
Energy Management involves monitoring, controlling, and conserving energy in a facility or system, aiming to improve efficiency, reduce costs, and minimize environmental impact. For an Industrial Electrician, it entails optimizing electrical systems, machinery, and processes to use energy more effectively.
Why It's Important
Energy management is crucial for an industrial electrician because it helps in optimizing energy use, reducing operational costs, ensuring equipment longevity, and minimizing environmental impact, thus ensuring sustainable and efficient industrial operations.
How to Improve Energy Management Skills
Improving energy management as an industrial electrician involves optimizing electrical systems for efficiency, monitoring energy usage, and implementing sustainable practices. Here are concise steps:
Conduct Energy Audits: Regularly assess electrical systems to identify inefficiencies and potential areas for improvement. Energy.gov provides guidelines on conducting energy assessments.
Implement Energy-Efficient Technologies: Upgrade to energy-efficient lighting, motors, and HVAC systems. The Database for State Incentives for Renewables & Efficiency (DSIRE) offers information on incentives for such technologies.
Use Energy Management Systems (EMS): Install EMS to monitor, control, and optimize the performance of electrical systems. Siemens offers comprehensive solutions for building automation and control.
Adopt Renewable Energy Sources: Integrate solar panels or wind turbines into your energy supply. EnergySage is a useful resource for exploring solar options and obtaining quotes.
Educate and Train Staff: Ensure all team members are aware of energy-saving practices and procedures. The Industrial Efficiency Technology Database provides valuable information on technologies and training.
Monitor and Optimize Power Quality: Use power quality analyzers to detect and rectify issues such as voltage sags, transients, and harmonics. Fluke offers a range of tools for power quality analysis.
Implement Preventive Maintenance: Regular maintenance of electrical equipment can prevent inefficiencies and failures. The National Electrical Manufacturers Association (NEMA) provides standards and guides for maintenance practices.
By systematically applying these strategies, an industrial electrician can significantly contribute to improving energy management within their facility.
How to Display Energy Management Skills on Your Resume
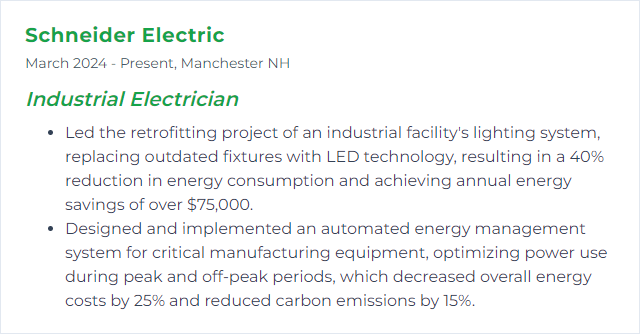