Top 12 Industrial Maintenance Technician Skills to Put on Your Resume
In today's rapidly evolving industrial landscape, a well-crafted resume highlighting key skills is crucial for aspiring industrial maintenance technicians. This article delves into the top 12 skills you need to showcase on your resume, setting you apart in the competitive job market and demonstrating your readiness to tackle the demands of modern industrial maintenance.
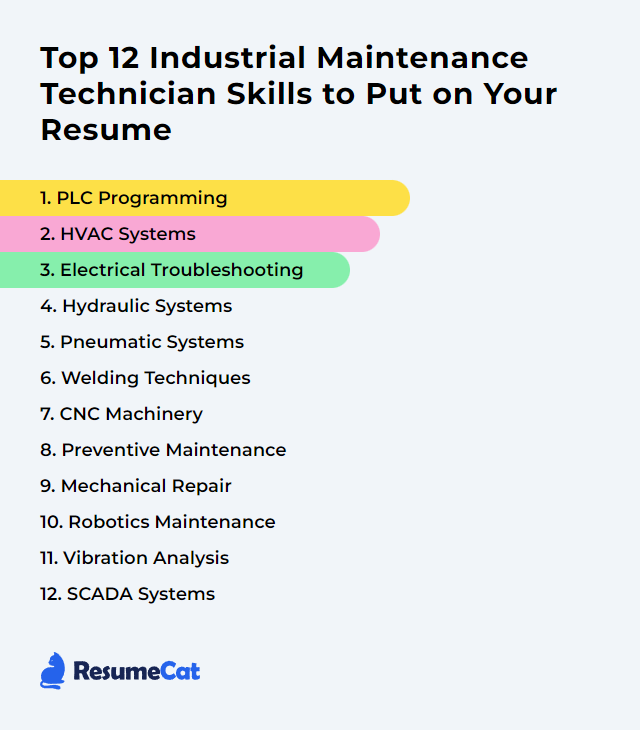
Industrial Maintenance Technician Skills
- PLC Programming
- HVAC Systems
- Electrical Troubleshooting
- Hydraulic Systems
- Pneumatic Systems
- Welding Techniques
- CNC Machinery
- Preventive Maintenance
- Mechanical Repair
- Robotics Maintenance
- Vibration Analysis
- SCADA Systems
1. PLC Programming
PLC Programming involves creating and modifying computer algorithms and instructions to control the operations of industrial machinery and processes through Programmable Logic Controllers (PLCs), essential for automation in manufacturing and production environments.
Why It's Important
PLC programming is crucial for Industrial Maintenance Technicians as it enables the automation, control, and optimization of machinery and processes, ensuring efficient, reliable, and safe industrial operations.
How to Improve PLC Programming Skills
Improving PLC programming skills, especially for an Industrial Maintenance Technician, involves a blend of learning, practice, and staying updated with the latest technologies and standards. Here are concise steps to enhance your PLC programming abilities:
Understand Basics Thoroughly: Start with a solid foundation in electrical principles and PLC basics. PLC Academy offers a good starting point.
Learn Ladder Logic: It's the most common PLC programming language. PLCdev has resources and examples.
Practice with Simulation Software: Tools like Siemens TIA Portal allow you to simulate and test PLC programs without hardware.
Study Real-World Applications: Understanding practical applications can significantly improve your programming. Websites like AutomationDirect offer tutorials and project examples.
Continuous Learning: Technology evolves; keep learning new languages (e.g., Structured Text) and standards. PLCS.net is a great forum for discussion and learning.
Attend Workshops and Webinars: Manufacturers and educational platforms regularly host these to introduce new technologies and best practices. Rockwell Automation often offers valuable webinars.
Get Certified: Earning certifications from recognized bodies can deepen your knowledge and demonstrate your skills. ISA offers certification in automation and control.
By following these steps and engaging with the community, you can significantly improve your PLC programming skills and stay ahead in the field of industrial maintenance.
How to Display PLC Programming Skills on Your Resume
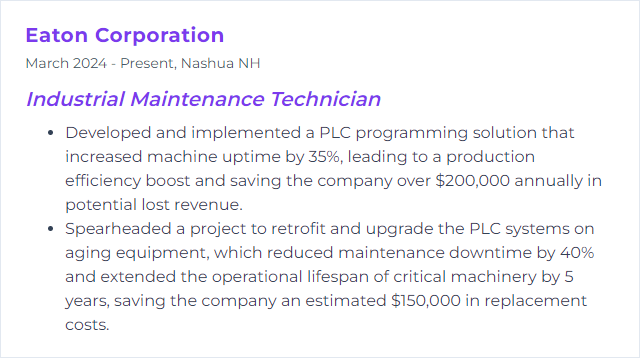
2. HVAC Systems
HVAC systems, standing for Heating, Ventilation, and Air Conditioning, are crucial in maintaining indoor climate control and air quality in industrial settings. They regulate temperature, humidity, and air purity, ensuring a comfortable and safe environment for machinery operation and workforce productivity. An Industrial Maintenance Technician is responsible for the installation, maintenance, and repair of these systems to ensure their efficient and reliable operation.
Why It's Important
HVAC systems are crucial for maintaining optimal temperature and air quality, ensuring both equipment efficiency and a safe, comfortable working environment for personnel, which are key priorities for an Industrial Maintenance Technician.
How to Improve HVAC Systems Skills
Improving HVAC systems, especially from the perspective of an Industrial Maintenance Technician, involves a combination of regular maintenance, system upgrades, and efficiency optimizations. Here are concise strategies:
Regular Maintenance: Conduct routine inspections and cleaning of all components (filters, coils, and fans) to ensure optimal performance. ASHRAE provides guidelines on maintenance schedules and procedures.
System Upgrades: Replace outdated components with high-efficiency models. Consider installing variable frequency drives (VFDs) on fan and pump motors to reduce energy consumption. Energy Star has recommendations on high-efficiency HVAC systems.
Smart Controls: Implement smart thermostats and automation systems for better control over heating, cooling, and ventilation, adjusting in real time to save energy. Department of Energy offers insights into how smart controls can enhance HVAC efficiency.
Airflow Optimization: Ensure ductwork is properly sealed and insulated. Also, adjust dampers to improve airflow and comfort within the facility. The Building Performance Institute provides standards for ductwork and airflow efficiency.
Energy Audit: Conduct or hire a service for an energy audit of your HVAC systems to identify inefficiencies and potential improvements. The U.S. Environmental Protection Agency has resources on conducting energy audits.
Training and Education: Stay updated with the latest HVAC technologies and maintenance techniques through continuous learning and training. HVAC Excellence and NATE offer certification programs that cover the latest in HVAC technology and best practices.
Implementing these strategies will not only improve the performance and efficiency of HVAC systems but also extend their lifespan, ultimately contributing to a more sustainable and cost-effective operation.
How to Display HVAC Systems Skills on Your Resume
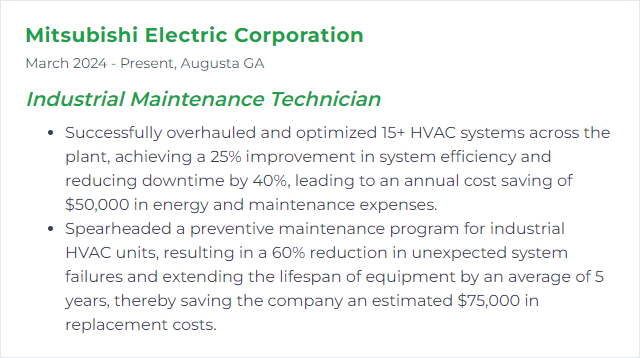
3. Electrical Troubleshooting
Electrical troubleshooting in the context of an Industrial Maintenance Technician involves systematically diagnosing and fixing issues within electrical systems or components in industrial settings, aiming to restore proper operation and ensure safety and efficiency.
Why It's Important
Electrical troubleshooting is crucial for an Industrial Maintenance Technician because it enables quick identification and repair of electrical issues, ensuring machinery operates efficiently, safely, and with minimal downtime, thereby maintaining productivity and preventing costly damage or accidents.
How to Improve Electrical Troubleshooting Skills
Improving electrical troubleshooting skills, especially for an Industrial Maintenance Technician, involves a combination of theoretical knowledge and practical experience. Follow these concise steps:
Understand Electrical Fundamentals: Start with a solid foundation in electrical principles. Websites like All About Circuits offer tutorials on basic to advanced concepts.
Learn from Manuals and Schematics: Familiarize yourself with reading and interpreting electrical schematics and manuals. Resources like Schematics.com can be helpful.
Practice Safety: Always prioritize safety by understanding and following guidelines. OSHA’s Electrical Safety page provides essential safety practices.
Use Diagnostic Tools: Get proficient with multimeters, clamp meters, and oscilloscopes. Fluke offers tutorials and tips on using these tools effectively.
Gain Hands-on Experience: Apply your knowledge through practice. Troubleshooting simulators like Troubleshooters.com offer practical exercises.
Continuous Learning: Technology evolves, so keep updating your skills through courses on platforms like Udemy or Coursera.
Join Forums and Communities: Engage with professionals on platforms like Electrician Talk or Reddit’s r/electricians for advice and tips.
By integrating these resources and strategies, you'll enhance your troubleshooting skills and efficiency as an Industrial Maintenance Technician.
How to Display Electrical Troubleshooting Skills on Your Resume
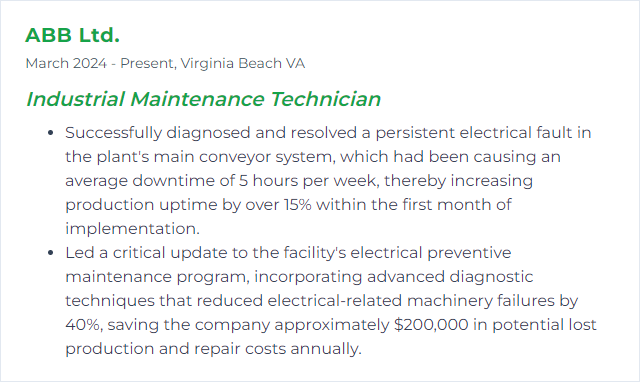
4. Hydraulic Systems
Hydraulic systems use pressurized fluid to generate, control, and transmit power. They are commonly used in industrial machines for lifting, pressing, and moving heavy loads, offering precise control and high force in a compact design. Maintenance technicians typically manage the upkeep, troubleshooting, and repair of these systems to ensure efficient and safe operation.
Why It's Important
Hydraulic systems are crucial for Industrial Maintenance Technicians because they enable the precise control and transmission of power to machinery and equipment, ensuring efficient, reliable, and safe operations in various industrial settings.
How to Improve Hydraulic Systems Skills
Improving hydraulic systems in industrial maintenance involves enhancing efficiency, reliability, and safety. Here are concise strategies:
Regular Maintenance: Schedule routine inspections and maintenance to prevent leaks and component failures. Hydraulics & Pneumatics Guide
Fluid Management: Use high-quality hydraulic fluids and maintain cleanliness to prevent contamination, which is a major cause of hydraulic system failure. Machinery Lubrication on Fluid Management
Heat Management: Implement cooling systems or heat exchangers to maintain optimal operating temperatures and prevent overheating. Mobile Hydraulic Tips on Heat Exchangers
Leak Detection and Repair: Employ leak detection techniques to identify and repair leaks promptly, reducing fluid loss and potential safety hazards. Fluid Power Journal on Leak Detection
System Upgrades: Upgrade older components with modern, more efficient alternatives. This includes using variable speed drives for pumps to reduce energy consumption. Pumps & Systems on VSDs
Training: Ensure that maintenance technicians receive ongoing training on the latest hydraulic technologies and best practices. Hydraulics & Pneumatics Training
Implementing these strategies can significantly improve the performance and lifespan of hydraulic systems in an industrial setting.
How to Display Hydraulic Systems Skills on Your Resume
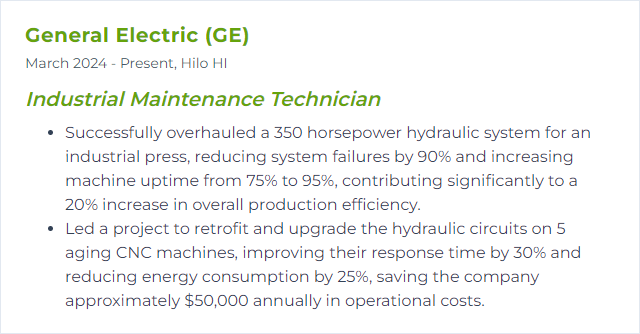
5. Pneumatic Systems
Pneumatic systems are a type of mechanical system that use compressed air to transmit and control energy. In an industrial setting, maintenance technicians use them to operate machinery and tools, such as actuators, valves, and motors, through the controlled release of pressurized air.
Why It's Important
Pneumatic systems are crucial for Industrial Maintenance Technicians because they provide reliable, cost-effective, and safe power transmission for operating various machinery and tools essential for maintenance tasks, enhancing efficiency and productivity in industrial settings.
How to Improve Pneumatic Systems Skills
Improving pneumatic systems in an industrial setting involves enhancing efficiency, reliability, and safety. Here are concise strategies for an Industrial Maintenance Technician:
Regular Maintenance: Schedule routine inspections and maintenance to prevent leaks and component failures. Focus on detecting and fixing leaks, checking filters, and replacing worn parts.
Proper Lubrication: Ensure adequate lubrication of moving parts to reduce wear and tear. Use the manufacturer-recommended lubricants.
Upgrade Components: Consider upgrading to more efficient components such as valves and actuators that offer better performance and energy efficiency. Festo and SMC Corporation are reputable suppliers.
System Monitoring: Implement a pneumatic system monitoring tool to track performance and identify issues early. Parker offers advanced monitoring solutions.
Energy Efficiency: Install an air management system to optimize air use and reduce energy consumption. Atlas Copco provides energy-efficient solutions.
Education and Training: Continuously educate yourself on the latest pneumatic system technologies and best practices. Hydraulics & Pneumatics is a valuable resource for the latest industry news and tips.
By implementing these strategies, you can improve the efficiency, reliability, and safety of pneumatic systems in an industrial environment.
How to Display Pneumatic Systems Skills on Your Resume
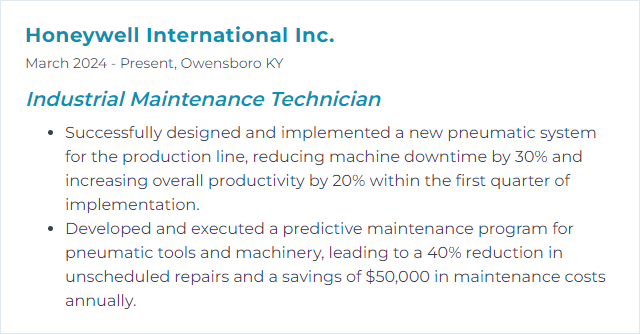
6. Welding Techniques
Welding techniques involve methods of joining metal parts together by melting and fusing them. For an Industrial Maintenance Technician, it's crucial to select the appropriate welding method based on material, application, and strength requirements. Key techniques include Shielded Metal Arc Welding (SMAW), Gas Metal Arc Welding (GMAW/MIG), Gas Tungsten Arc Welding (GTAW/TIG), and Flux-Cored Arc Welding (FCAW). Mastery of these techniques enables effective repair and fabrication of machinery and structural components in an industrial setting.
Why It's Important
Welding techniques are crucial for an Industrial Maintenance Technician because they enable precise, strong, and durable repairs and fabrications essential for maintaining and improving the efficiency and safety of industrial machinery and infrastructure.
How to Improve Welding Techniques Skills
Improving welding techniques, especially for an Industrial Maintenance Technician, involves practice, knowledge update, and the understanding of advanced technologies. Below are concise pointers to enhance welding skills:
Practice Consistently: Regular practice enhances muscle memory and improves hand-eye coordination. Focus on different welding positions and materials.
Learn from Online Resources: Utilize online platforms like Welding Tips and Tricks for tutorials and practical advice.
Understand Welding Procedures: Familiarize yourself with different welding procedures and standards. The American Welding Society (AWS) offers resources and certifications.
Use the Right Equipment: Ensure you have the correct tools and safety gear. Understanding and using the latest welding equipment can significantly improve your technique.
Attend Workshops and Courses: Participate in workshops or courses for hands-on experience. Websites like Lincoln Electric offer training programs.
Seek Feedback and Mentorship: Connect with experienced welders or mentors in your field for feedback and tips. Peer review is invaluable for growth.
Stay Updated: The welding industry continuously evolves. Keep abreast of new technologies and materials by subscribing to industry publications like Welding Journal.
By following these steps and continually seeking to expand your knowledge and skills, you can significantly improve your welding techniques as an Industrial Maintenance Technician.
How to Display Welding Techniques Skills on Your Resume
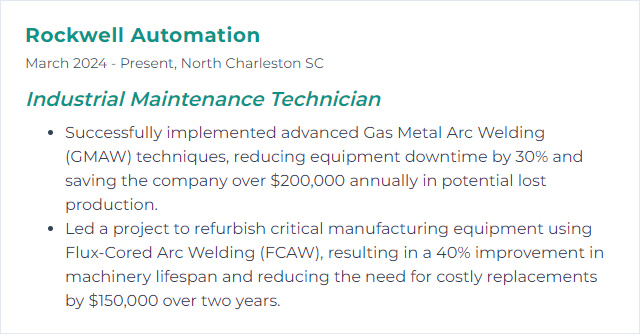
7. CNC Machinery
CNC machinery refers to automated, computer-controlled equipment used in manufacturing to precisely cut, shape, and finish materials. For an Industrial Maintenance Technician, it involves installing, maintaining, and repairing these machines to ensure optimal performance and production efficiency.
Why It's Important
CNC (Computer Numerical Control) machinery is crucial for Industrial Maintenance Technicians as it allows for the precise, consistent, and efficient production of parts and components. This precision ensures high-quality results, reduces waste, and minimizes the need for manual adjustments, enhancing overall operational efficiency and productivity in a manufacturing setting.
How to Improve CNC Machinery Skills
Improving CNC machinery as an Industrial Maintenance Technician involves optimizing performance, enhancing accuracy, and ensuring longevity. Here are concise strategies:
Regular Maintenance: Schedule and perform regular maintenance checks to prevent unexpected breakdowns and ensure smooth operation. Focus on cleaning, lubrication, and checking for wear and tear. Maintenance Tips
Software Updates: Regularly update CNC software to improve efficiency and compatibility with new tools and materials. Software Update Importance
Tool Calibration: Calibrate tools and equipment frequently to ensure precision and reduce errors. Calibration Guide
Training: Invest in ongoing training for operators to keep them updated on the latest CNC technologies and best practices. Training Resources
Energy Efficiency: Optimize machinery for energy efficiency by using energy-efficient motors and adopting practices that reduce power consumption. Energy Efficiency Tips
Upgrade Components: Consider upgrading components such as spindle drives, tool holders, and software to enhance performance and extend machine life. Component Upgrades
Predictive Maintenance: Utilize predictive maintenance tools and technologies to anticipate and address potential issues before they lead to failures. Predictive Maintenance
Implementing these strategies can significantly improve the performance and reliability of CNC machinery in an industrial setting.
How to Display CNC Machinery Skills on Your Resume
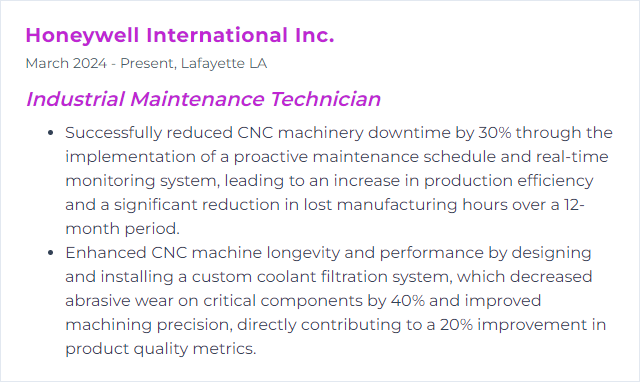
8. Preventive Maintenance
Preventive maintenance is a proactive approach taken by Industrial Maintenance Technicians to regularly inspect, service, and maintain equipment and machinery to prevent unexpected breakdowns and ensure optimal performance.
Why It's Important
Preventive maintenance is crucial for an Industrial Maintenance Technician as it reduces equipment downtime, prevents costly breakdowns, ensures operational safety, and extends the lifespan of machinery, thereby optimizing productivity and minimizing overall maintenance expenses.
How to Improve Preventive Maintenance Skills
Improving preventive maintenance involves a systematic approach to ensure machinery and equipment run efficiently and reliably. Here are key strategies:
Develop a Preventive Maintenance Schedule: Identify all equipment and determine the frequency of maintenance tasks based on manufacturer recommendations and past maintenance data. Fiix Software offers insights on creating an effective schedule.
Implement a Computerized Maintenance Management System (CMMS): Use CMMS software to organize, track, and manage maintenance activities efficiently. UpKeep is a popular option for managing maintenance operations.
Train Your Team: Ensure your technicians are well-trained on the latest maintenance techniques and technologies. TPC Training provides a range of courses for industrial maintenance technicians.
Utilize Condition Monitoring Tools: Employ sensors and devices to continuously monitor equipment conditions, helping to predict failures before they occur. Fluke offers a variety of condition monitoring tools.
Regularly Review and Optimize Maintenance Procedures: Continuously assess the effectiveness of your maintenance strategy and make adjustments as necessary. Industry forums like Plant Services can be valuable resources for best practices and optimization tips.
By following these strategies, you can significantly improve the effectiveness of your preventive maintenance program, leading to reduced downtime, improved safety, and increased equipment lifespan.
How to Display Preventive Maintenance Skills on Your Resume
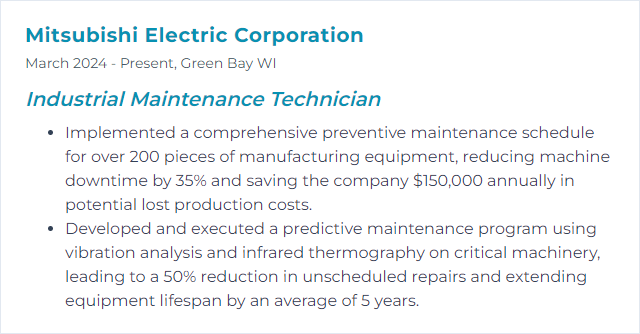
9. Mechanical Repair
Mechanical repair, in the context of an Industrial Maintenance Technician, involves diagnosing, fixing, and maintaining machinery and equipment to ensure optimal functioning and reliability in an industrial setting.
Why It's Important
Mechanical repair is crucial for ensuring the optimal functioning, reliability, and safety of machinery and equipment, minimizing downtime, and extending asset lifespan, which are essential for maintaining productivity and efficiency in an industrial setting.
How to Improve Mechanical Repair Skills
To improve mechanical repair skills as an Industrial Maintenance Technician, focus on the following strategies:
Continuous Learning: Stay updated with the latest industry standards and technologies through online courses and webinars. Platforms like Coursera and edX offer relevant courses.
Hands-On Experience: Gain practical experience through apprenticeships or on-the-job training. Working under the guidance of experienced technicians can provide invaluable insights.
Technical Manuals: Regularly consult machinery and equipment manuals to understand their mechanics deeply.
Networking: Join forums or communities such as Reddit’s r/maintenance or Maintenance.org, to exchange knowledge and troubleshooting tips with peers.
Safety Training: Prioritize safety by completing OSHA training (OSHA Education Center) to understand the best practices and regulations.
Certifications: Obtain certifications such as Certified Maintenance & Reliability Professional (CMRP) from SMRP to validate your skills and knowledge.
Technical Reading: Improve your understanding of mechanical concepts by reading technical books and journals. Websites like Engineering.com provide a wealth of resources.
Problem-Solving Skills: Enhance your problem-solving skills by practicing with real-life scenarios, which can be found in case studies or troubleshooting guides.
By integrating these strategies into your professional development, you can significantly improve your mechanical repair skills and advance your career as an Industrial Maintenance Technician.
How to Display Mechanical Repair Skills on Your Resume
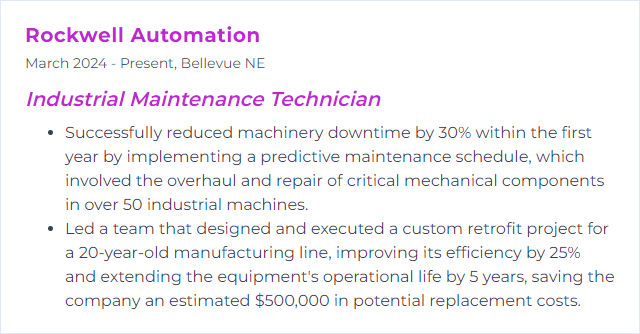
10. Robotics Maintenance
Robotics Maintenance involves the routine inspection, cleaning, calibration, and repair of robotic equipment and systems to ensure their optimal performance and prevent downtime in an industrial setting. This includes troubleshooting mechanical and electrical issues, software updates, and ensuring adherence to safety standards.
Why It's Important
Robotics maintenance is crucial for ensuring consistent productivity, minimizing downtime, and extending the lifespan of robotic systems, thereby safeguarding the investment and maintaining operational efficiency in industrial settings.
How to Improve Robotics Maintenance Skills
Improving robotics maintenance for an Industrial Maintenance Technician involves a combination of best practices, continuous learning, and leveraging the right tools. Here's a concise guide:
Regular Inspections and Preventive Maintenance: Schedule routine inspections and perform preventive maintenance to catch issues before they lead to significant downtime. RobotWorx provides insights on what is involved.
Training and Education: Continuously update your skills and knowledge through courses and certifications. Websites like Tooling U-SME offer specialized courses in robotics and automation.
Utilize Diagnostic Tools and Software: Implement advanced diagnostic tools and software for real-time monitoring and troubleshooting. FANUC offers a maintenance suite designed to minimize downtime.
Follow Manufacturers’ Guidelines: Always adhere to the maintenance guidelines and schedules provided by the robot manufacturers. This ensures the longevity and efficiency of the machinery.
Implement a CMMS (Computerized Maintenance Management System): Use CMMS software to track maintenance activities, manage inventory, and predict future maintenance needs. Fiix is a popular option for maintenance professionals.
By focusing on these areas, Industrial Maintenance Technicians can significantly improve the efficiency and reliability of robotics maintenance in an industrial setting.
How to Display Robotics Maintenance Skills on Your Resume
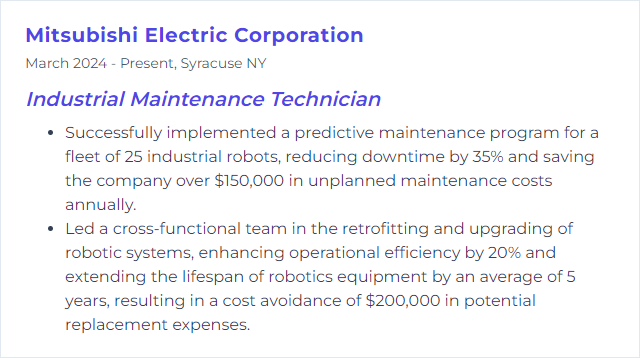
11. Vibration Analysis
Vibration analysis is a technique used in industrial maintenance to detect and diagnose machinery health by measuring and analyzing the frequency and intensity of vibrations emitted by machines during operation, helping predict and prevent equipment failures.
Why It's Important
Vibration analysis is crucial for an Industrial Maintenance Technician because it helps in early detection of machinery faults, ensuring preventive maintenance, reducing downtime, enhancing equipment lifespan, and ensuring safety and efficiency in operations.
How to Improve Vibration Analysis Skills
Improving vibration analysis involves enhancing data collection, analysis skills, and implementing predictive maintenance strategies. Here are concise steps tailored for an Industrial Maintenance Technician:
Educate and Train: Enhance your understanding of vibration analysis principles and equipment. Invest in courses and certifications from recognized institutions like the Vibration Institute.
Use Advanced Tools: Upgrade to high-quality vibration analysis tools that offer better data accuracy and analysis capabilities. Consider tools with advanced features like spectral analysis and integration with predictive maintenance software.
Implement Predictive Maintenance: Shift from reactive to predictive maintenance strategies. Use vibration data to predict equipment failures before they occur.
Data Analysis Skills: Improve your data analysis skills by learning how to interpret vibration data more effectively. Utilize software that can help in diagnosing issues based on vibration patterns.
Regular Monitoring: Establish a routine for regular equipment monitoring. Consistent data collection helps in trend analysis and early detection of potential issues.
Involve in Forums and Groups: Join online forums and groups such as Maintenance.org to stay updated with the latest in vibration analysis techniques and tools.
By focusing on these areas, an Industrial Maintenance Technician can significantly improve their vibration analysis capabilities, leading to better maintenance decision-making and increased equipment reliability.
How to Display Vibration Analysis Skills on Your Resume
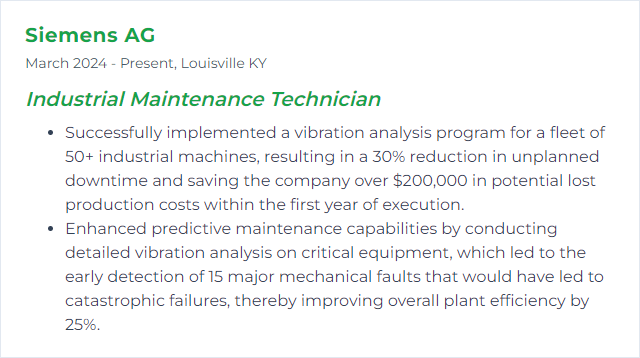
12. SCADA Systems
SCADA (Supervisory Control and Data Acquisition) systems are computer-based systems used by industrial maintenance technicians to monitor, control, and acquire data from industrial processes and equipment across multiple locations. These systems allow for real-time data collection, process control, and equipment monitoring to ensure efficiency, safety, and reliability in industrial operations.
Why It's Important
SCADA Systems are vital for Industrial Maintenance Technicians as they provide real-time monitoring and control over industrial processes and machinery, enabling prompt identification and troubleshooting of operational issues, ensuring efficiency, safety, and minimal downtime in industrial environments.
How to Improve SCADA Systems Skills
Improving SCADA (Supervisory Control and Data Acquisition) systems, particularly from an Industrial Maintenance Technician's perspective, involves a multi-faceted approach focusing on system security, data management, network infrastructure, and ongoing education. Here’s a concise guide:
Enhance Security: Strengthen system security by implementing robust cybersecurity measures. This includes regular software updates, the use of firewalls, and secure authentication protocols. Cybersecurity & Infrastructure Security Agency (CISA) Guidelines offers comprehensive resources on protecting industrial control systems.
Data Management: Optimize data collection and analysis. Employ data analytics tools to predict maintenance needs and improve decision-making. IBM’s guide on data management provides insights on efficiently handling data.
Network Infrastructure: Ensure the SCADA network infrastructure is reliable and scalable. This might involve upgrading network components and using redundant systems to minimize downtime. Cisco’s Industrial Networking solutions can offer a roadmap for robust network setups.
Ongoing Education: Stay updated with the latest SCADA technologies and best practices through continuous learning. Many organizations offer specialized training for SCADA systems. ISA (International Society of Automation) provides various training courses tailored to automation and control professionals.
By focusing on these areas, Industrial Maintenance Technicians can significantly contribute to the efficiency, reliability, and security of SCADA systems.
How to Display SCADA Systems Skills on Your Resume
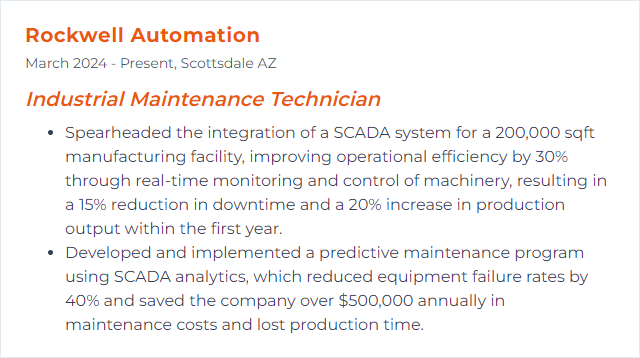