Top 12 HSE Specialist Skills to Put on Your Resume
In the competitive field of Health, Safety, and Environment (HSE), standing out to potential employers requires showcasing a unique set of skills on your resume. This article highlights the top 12 HSE specialist skills that can significantly enhance your job application, making you a more attractive candidate in this critical industry.
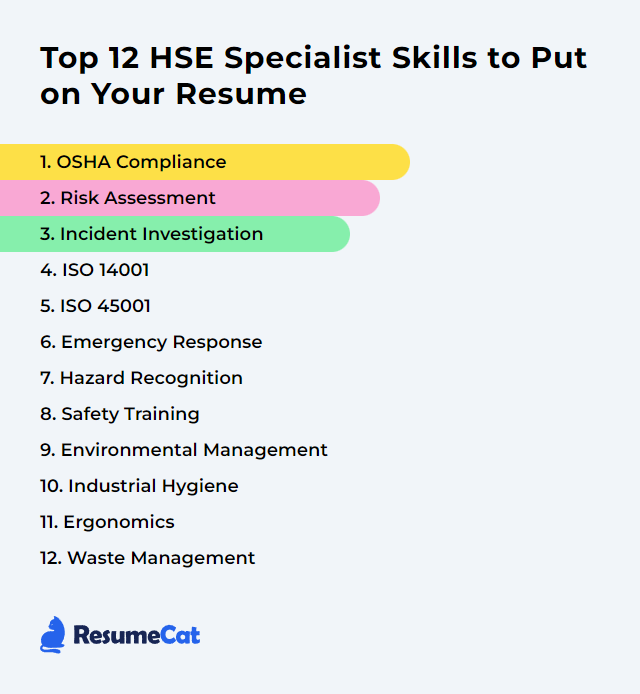
HSE Specialist Skills
- OSHA Compliance
- Risk Assessment
- Incident Investigation
- ISO 14001
- ISO 45001
- Emergency Response
- Hazard Recognition
- Safety Training
- Environmental Management
- Industrial Hygiene
- Ergonomics
- Waste Management
1. OSHA Compliance
OSHA compliance refers to adhering to the standards and regulations established by the Occupational Safety and Health Administration to ensure safe and healthy working conditions. For an HSE (Health, Safety, and Environment) Specialist, it involves implementing and monitoring safety programs, conducting training, and ensuring workplace practices meet OSHA requirements to prevent accidents and occupational illnesses.
Why It's Important
OSHA compliance is crucial for an HSE Specialist because it ensures workplace safety, minimizes the risk of accidents and health hazards, and aligns with legal requirements, thereby protecting both employees and the organization from potential harm and legal consequences.
How to Improve OSHA Compliance Skills
Improving OSHA compliance as an HSE (Health, Safety, and Environment) Specialist involves a proactive approach focusing on thorough training, regular audits, and a strong safety culture. Here’s a concise guide:
Stay Informed: Regularly update your knowledge of OSHA regulations. OSHA’s official website is a primary resource for current standards and guidelines.
Conduct Regular Training: Ensure that all employees receive comprehensive safety training relevant to their roles. OSHA’s Training page offers resources and guidelines for developing effective programs.
Perform Regular Audits and Inspections: Regularly assess your workplace for compliance with OSHA standards. Use OSHA’s inspection guidelines to help identify and correct potential violations.
Develop a Safety Culture: Foster an environment where safety is a shared responsibility. Engage employees in safety discussions and encourage reporting of hazards without fear of retaliation.
Implement a Reporting System: Have an efficient system for reporting injuries, illnesses, and hazards. OSHA’s Recordkeeping rules provide a framework for documenting and reporting workplace incidents.
Seek OSHA Consultation Services: Take advantage of OSHA’s free On-Site Consultation Program for small and medium-sized businesses. This service offers confidential advice and assistance in establishing and improving your workplace safety and health management system.
By integrating these practices, an HSE Specialist can significantly enhance OSHA compliance, reduce workplace injuries and illnesses, and foster a safer work environment.
How to Display OSHA Compliance Skills on Your Resume

2. Risk Assessment
Risk assessment, in the context of an HSE (Health, Safety, and Environment) Specialist, is the systematic process of identifying potential hazards, analyzing and evaluating the risks associated with those hazards, and determining appropriate ways to eliminate or control those risks to protect workers, the public, and the environment.
Why It's Important
Risk assessment is crucial for an HSE (Health, Safety, and Environment) Specialist as it helps identify, evaluate, and prioritize potential hazards in the workplace, enabling the implementation of effective measures to mitigate risks, protect employee well-being, ensure regulatory compliance, and prevent accidents and environmental harm.
How to Improve Risk Assessment Skills
Improving risk assessment, especially for an HSE (Health, Safety, and Environment) Specialist, involves a systematic approach to identifying, analyzing, and managing workplace hazards and risks. Here’s a concise guide:
Stay Updated with Legislation: Keep abreast of the latest health and safety regulations to ensure compliance.
Continuous Training: Engage in continuous professional development to enhance risk assessment skills.
Use Technology: Incorporate risk assessment software to streamline the process.
Engage Stakeholders: Involve employees and other stakeholders in the risk assessment process for comprehensive insights.
Review and Update: Regularly review and update risk assessments to reflect new hazards or changes in the workplace.
By focusing on these areas, an HSE Specialist can significantly improve the effectiveness of risk assessments in their organization.
How to Display Risk Assessment Skills on Your Resume
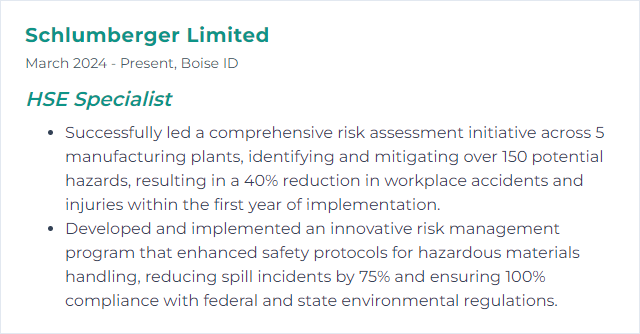
3. Incident Investigation
Incident Investigation, in the context of an HSE (Health, Safety, and Environment) Specialist, is a systematic process aimed at identifying the root causes of workplace incidents, accidents, or near-misses to prevent their recurrence, enhance safety, and ensure compliance with health and safety regulations.
Why It's Important
Incident investigation is crucial for an HSE (Health, Safety, and Environment) Specialist as it enables the identification of root causes and contributing factors of incidents, helping to prevent future occurrences, ensure compliance with safety regulations, and protect the well-being of employees and the environment.
How to Improve Incident Investigation Skills
Improving incident investigation involves a systematic approach to understanding what happened, why it happened, and how similar incidents can be prevented in the future. As an HSE Specialist, you can enhance your incident investigation process by following these concise steps:
Immediate Response and Stabilization: Secure the scene to preserve evidence and ensure safety. Address any immediate hazards.
Plan the Investigation: Assemble a diverse investigation team. Define the scope, objectives, and timeline.
Data Collection: Gather all relevant information. This includes interviewing witnesses, reviewing documents, and collecting physical evidence. OSHA's Incident Investigation guide highlights the importance of thorough data collection.
Analysis: Use root cause analysis tools such as the Five Whys or Fishbone Diagram to identify underlying issues. CCPS - Guidelines for Investigating Chemical Process Incidents provides detailed methodologies.
Report Writing: Develop a clear, concise report that outlines what happened, why it happened, and recommendations for prevention. Ensure the report is understandable to all stakeholders.
Implement Recommendations: Work with relevant departments to put preventative measures in place.
Follow-Up: Monitor the effectiveness of implemented recommendations and adjust as necessary.
Training: Regular training on incident investigation techniques and learnings from past incidents can prevent future occurrences. The National Safety Council offers training resources.
Use of Technology: Leverage incident management software for streamlined reporting, analysis, and tracking of corrective actions.
Foster a Reporting Culture: Encourage a workplace culture where employees feel safe reporting incidents and near misses. This proactive approach can help identify and mitigate risks before they result in incidents.
By systematically applying these steps and continuously seeking to learn and improve, you can enhance the effectiveness of incident investigations within your organization.
How to Display Incident Investigation Skills on Your Resume
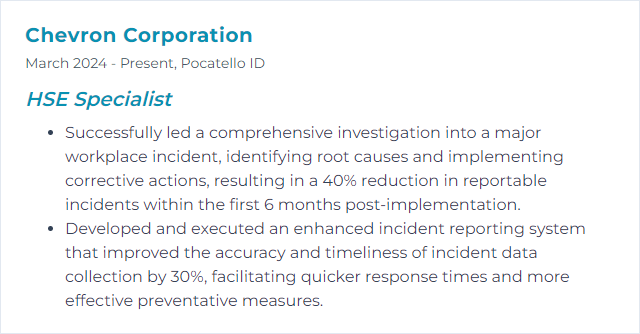
4. ISO 14001
ISO 14001 is an international standard that specifies requirements for an effective environmental management system (EMS), enabling organizations to enhance environmental performance, comply with regulations, and achieve environmental objectives.
Why It's Important
ISO 14001 is important for an HSE Specialist as it sets the international standard for an effective Environmental Management System (EMS), helping organizations improve their environmental performance through more efficient use of resources and reduction of waste, gaining a competitive advantage, and the trust of stakeholders.
How to Improve ISO 14001 Skills
Improving ISO 14001, the Environmental Management System, involves a continuous process of planning, implementing, reviewing, and improving the actions and processes to meet environmental objectives. Here are concise steps for an HSE Specialist:
Gap Analysis: Start by conducting a gap analysis to identify areas for improvement within your current system against ISO 14001 requirements.
Employee Engagement: Increase employee engagement through training and awareness programs, making environmental responsibility a shared goal.
Process Optimization: Optimize processes to reduce waste and increase efficiency. Implementing Lean management techniques can be beneficial.
Performance Monitoring: Use Key Performance Indicators (KPIs) to monitor environmental performance. Regularly review these indicators to identify trends and areas for improvement.
Legal Compliance: Regularly update and comply with relevant environmental legislation and regulations. Use compliance as a minimum standard and strive to exceed it.
Continuous Improvement: Adopt the PDCA (Plan-Do-Check-Act) cycle for continuous improvement of your environmental management system.
Stakeholder Engagement: Engage with stakeholders, including suppliers and customers, to encourage them to adopt environmentally friendly practices. This can lead to improvements in your own system.
External Audits: Regularly undergo external audits from certified bodies to gain an external perspective on your environmental management system's effectiveness.
Technology Utilization: Leverage technology to improve your environmental performance, such as using energy-efficient equipment or adopting a digital EMS.
Management Review: Ensure management is involved in reviewing the EMS to align environmental objectives with business goals, securing necessary resources for improvements.
Improving ISO 14001 is a continual process that demands commitment from all levels of the organization. By following these steps and utilizing the resources provided, an HSE Specialist can effectively enhance their organization's environmental management system.
How to Display ISO 14001 Skills on Your Resume

5. ISO 45001
ISO 45001 is an international standard that specifies requirements for an occupational health and safety (OH&S) management system, enabling organizations to proactively improve its OH&S performance in preventing injury and ill-health.
Why It's Important
ISO 45001 is important because it provides a global standard for occupational health and safety management systems, helping HSE Specialists reduce workplace risks, enhance employee well-being, and improve organizational safety performance.
How to Improve ISO 45001 Skills
Improving ISO 45001, the international standard for occupational health and safety management systems, involves continuous evaluation and enhancement of workplace safety protocols. For an HSE Specialist, key steps include:
- Gap Analysis: Conduct a thorough gap analysis against ISO 45001 requirements to identify areas for improvement.
- Employee Engagement: Foster a culture of safety by involving employees in safety planning and decision-making. Implement worker participation and consultation as recommended by ISO 45001.
- Risk Management: Enhance risk assessment procedures by adopting a proactive approach to identify and mitigate potential hazards before they result in incidents.
- Training and Development: Regularly update and provide training for all employees on the latest health and safety practices, ensuring they are competent and aware of their roles.
- Performance Monitoring: Utilize key performance indicators (KPIs) to track and measure safety performance. Regularly review and analyze data to identify trends and areas for improvement.
- Management Review: Conduct periodic management reviews of the OH&S management system to ensure its continuing suitability, adequacy, and effectiveness.
- Continuous Improvement: Implement a continuous improvement process that integrates feedback from audits, employee suggestions, incident investigations, and management reviews to make ongoing adjustments to health and safety practices.
Improving ISO 45001 compliance is an ongoing process that requires commitment from all levels of an organization, from top management to every employee.
How to Display ISO 45001 Skills on Your Resume
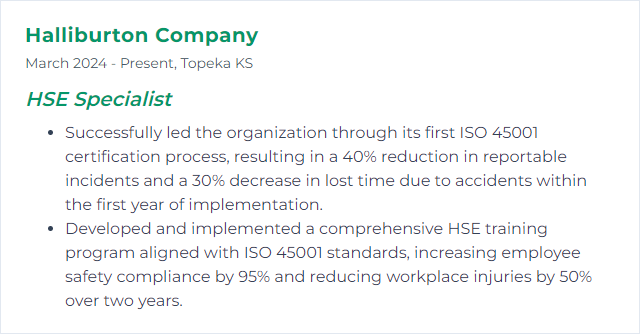
6. Emergency Response
Emergency Response is the organized and immediate action taken to address and manage the aftermath of an emergency situation, aiming to minimize its impact on health, safety, and the environment (HSE).
Why It's Important
Emergency response is crucial for quickly addressing and mitigating hazards, ensuring the safety and health of employees, and minimizing environmental impact, thereby safeguarding both human life and organizational assets.
How to Improve Emergency Response Skills
Improving emergency response involves a multi-faceted approach tailored towards ensuring rapid, efficient, and effective action in case of emergencies. Here are concise strategies for an HSE (Health, Safety, and Environment) Specialist:
Training and Drills: Regularly conduct emergency response drills and training sessions for all employees. This ensures that everyone knows their role and actions to take during an emergency. The Occupational Safety and Health Administration (OSHA) provides resources and guidelines on emergency preparedness training.
Communication Systems: Implement robust and reliable communication systems to quickly disseminate information during emergencies. Tools like mass notification systems can be crucial. The Federal Emergency Management Agency (FEMA) offers insights into developing effective communication plans.
Emergency Response Plan (ERP): Develop and regularly update a comprehensive ERP tailored to specific risks associated with the workplace. The plan should include evacuation procedures, emergency contact numbers, and a continuity plan. Guidance on ERP can be found through the Environmental Protection Agency (EPA).
Equipment and Resources: Ensure the availability and accessibility of emergency response equipment (fire extinguishers, first aid kits, etc.) and resources. Regular checks and maintenance should be conducted to ensure their readiness. The National Fire Protection Association (NFPA) provides standards and codes for emergency equipment.
Collaboration with Local Emergency Services: Establish and maintain a strong relationship with local emergency services (fire department, hospital, etc.). This collaboration can include joint training sessions and sharing of emergency plans. Engaging with the International Association of Emergency Managers (IAEM) can provide insights into effective collaboration techniques.
Review and Feedback: After any drill or actual emergency, conduct a thorough review session to gather feedback and identify areas for improvement. This continuous improvement cycle ensures that the emergency response strategy remains effective and up-to-date.
By focusing on these strategies, an HSE Specialist can significantly improve an organization's emergency response capability, ensuring the safety and well-being of all employees and minimizing the impact of emergencies.
How to Display Emergency Response Skills on Your Resume
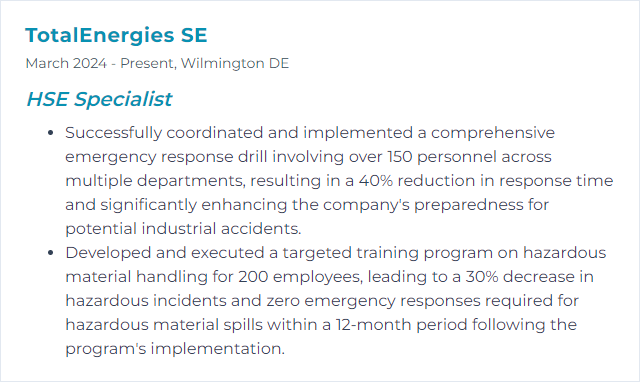
7. Hazard Recognition
Hazard Recognition is the process of identifying potential sources of harm or danger in the workplace, which could lead to accidents, injuries, or health issues, crucial for an HSE (Health, Safety, and Environment) Specialist to prevent incidents and ensure a safe working environment.
Why It's Important
Hazard recognition is crucial for an HSE Specialist as it enables the identification and assessment of potential risks in the workplace, ensuring the implementation of appropriate safety measures and protocols to prevent accidents, injuries, and health issues, ultimately safeguarding employees and the environment.
How to Improve Hazard Recognition Skills
Improving hazard recognition involves a combination of training, practice, and the use of technological tools. Here's a concise guide tailored for an HSE Specialist:
Training: Invest in regular, up-to-date training programs that cover hazard identification, risk assessment, and mitigation strategies. The Occupational Safety and Health Administration (OSHA) offers resources and training guidelines.
Practice: Conduct regular workplace inspections and hazard hunts to practice identifying potential risks. This hands-on approach helps in recognizing less obvious hazards.
Technology: Utilize technology such as safety management software for systematic hazard identification and control. Platforms like SafetyCulture (iAuditor) can streamline this process.
Engagement: Foster a culture of safety by engaging employees in safety discussions, hazard spotting, and feedback loops. Tools like Slack or Microsoft Teams can facilitate communication.
Continuous Learning: Stay informed about industry trends and emerging hazards through professional networks and publications, such as the American Society of Safety Professionals (ASSP).
By integrating these elements, an HSE Specialist can significantly improve hazard recognition in the workplace.
How to Display Hazard Recognition Skills on Your Resume
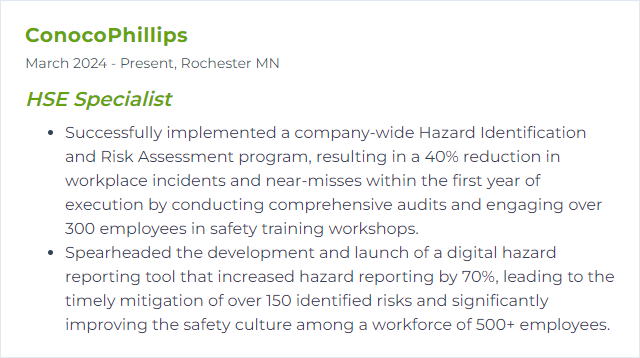
8. Safety Training
Safety training involves educating employees on the necessary procedures, practices, and behaviors to prevent accidents and injuries in the workplace, ensuring a safe and healthy environment. It is a critical component of an HSE (Health, Safety, and Environment) Specialist's role to develop, implement, and monitor these training programs.
Why It's Important
Safety training is crucial because it equips HSE (Health, Safety, and Environment) Specialists with the knowledge and skills needed to identify, assess, and mitigate workplace hazards effectively, ensuring a safe working environment and compliance with legal and regulatory requirements. This training helps in preventing accidents, injuries, and health issues, promoting a culture of safety and well-being among employees.
How to Improve Safety Training Skills
Improving safety training involves a multi-faceted approach focused on engagement, relevance, and continuous improvement. Here are concise recommendations for an HSE (Health, Safety, and Environment) Specialist:
Engage with Interactive Methods: Move beyond traditional lectures by incorporating interactive elements such as virtual reality, simulations, and gamification to enhance learning and retention.
Customize Content: Tailor training material to address the specific risks and scenarios relevant to your workplace. Resources like OSHA’s Training Materials can serve as a starting point for customization.
Leverage Technology: Utilize e-learning platforms and mobile apps for flexible training options that cater to different learning styles and schedules. Explore tools like the NIOSH eNews for updates and ideas.
Promote a Safety Culture: Encourage an environment where safety training is not just a compliance requirement but a core value. Safety culture improvement strategies can guide in fostering this environment.
Assess and Adapt: Regularly evaluate the effectiveness of your training programs through feedback surveys, quizzes, and real-world outcomes. Use findings to make necessary adjustments. Tools like SurveyMonkey can facilitate feedback collection.
Continuous Learning: Offer ongoing learning opportunities and refresher courses to keep safety top-of-mind. Platforms like Coursera and edX provide courses that can supplement ongoing education.
Certify Skills: Where possible, provide certifications or recognitions for completed training. This not only motivates but also formally acknowledges the competency of the workforce. Check Red Cross Training Services for examples.
Leadership Engagement: Ensure that leadership actively participates in and endorses safety training. Their involvement can significantly impact the overall safety culture. Guidance on leadership's role in safety is available through OSHA Leadership.
By focusing on these areas, an HSE Specialist can significantly enhance the effectiveness and impact of safety training within their organization.
How to Display Safety Training Skills on Your Resume
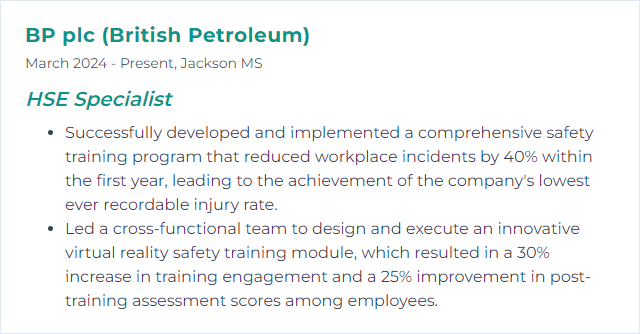
9. Environmental Management
Environmental Management involves planning, implementing, and controlling activities and policies to minimize an organization's environmental impact. It aims to ensure compliance with regulations, prevent pollution, conserve resources, and promote sustainability, crucial for an HSE (Health, Safety, and Environment) Specialist's role in safeguarding both environmental and human health.
Why It's Important
Environmental management is crucial as it helps in safeguarding ecosystems, ensures sustainable resource use, minimizes pollution, and mitigates the impact of human activities on the environment, aligning with the goals of health, safety, and environmental (HSE) specialists to protect human health, workplace safety, and the environment.
How to Improve Environmental Management Skills
Improving Environmental Management, especially from the perspective of a Health, Safety, and Environment (HSE) Specialist, involves a multi-faceted approach focused on compliance, sustainability, and continuous improvement. Here's a very short and concise guide:
Stay Informed: Keep up-to-date with environmental regulations and industry standards to ensure compliance.
Assess Risks: Conduct environmental impact assessments to identify and mitigate potential environmental risks associated with organizational activities.
Implement Management Systems: Adopt recognized environmental management systems (EMS) such as ISO 14001 to streamline processes, reduce waste, and improve sustainability.
Educate and Train: Provide training for employees on environmental policies, practices, and the importance of their role in environmental protection.
Monitor and Report: Regularly monitor environmental performance and report findings to stakeholders. Utilize EMS software for efficient data management and reporting.
Engage Stakeholders: Foster communication with all stakeholders, including employees, community members, and regulatory bodies, to encourage shared environmental responsibility.
Continuous Improvement: Use audits and feedback to continually improve environmental management practices.
By focusing on these areas, an HSE Specialist can effectively enhance their organization’s environmental management efforts, contributing to a safer, more sustainable world.
How to Display Environmental Management Skills on Your Resume
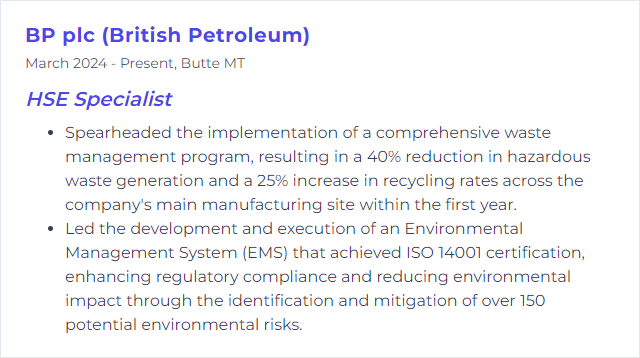
10. Industrial Hygiene
Industrial Hygiene is the discipline focused on anticipating, recognizing, evaluating, and controlling environmental factors or stresses in the workplace that may cause sickness, impaired health, or significant discomfort among workers through the identification and mitigation of physical, chemical, biological, and ergonomic hazards.
Why It's Important
Industrial Hygiene is crucial for an HSE Specialist as it focuses on identifying, assessing, and controlling workplace hazards to prevent occupational diseases and injuries, ensuring the well-being and safety of employees.
How to Improve Industrial Hygiene Skills
Improving Industrial Hygiene involves proactive and systematic approaches to identify, evaluate, and control workplace conditions that may cause workers' injury or illness. As an HSE Specialist, here are concise strategies to enhance Industrial Hygiene:
Conduct Risk Assessments: Regularly assess the workplace for chemical, physical, biological, and ergonomic risks. Tools like NIOSH’s Hierarchy of Controls can guide the implementation of effective control strategies.
Implement Control Measures: Apply engineering controls, administrative controls, and personal protective equipment (PPE) based on the identified risks. The OSHA’s Control Banding page offers insights into simplifying the selection of control measures.
Ensure Proper Ventilation: Good ventilation systems reduce the concentration of airborne contaminants. ASHRAE provides guidelines on ventilation standards that can be adapted to various industrial settings.
Promote Workplace Hygiene Practices: Encourage regular hand washing, clean workspaces, and proper waste disposal. WHO’s guidelines on workplace health offer comprehensive practices that enhance hygiene.
Regular Training and Education: Provide ongoing training on the importance of hygiene, use of PPE, and emergency procedures. OSHA’s Training and Education resources can be utilized to develop effective programs.
Monitor Health and Exposure: Implement a health surveillance program to monitor the effects of exposure to hazardous substances. CDC’s NIOSH offers tools and guidelines for occupational health surveillance.
Continuous Improvement: Use audits, inspections, and feedback to continually assess and improve the Industrial Hygiene program. ISO 45001 provides a framework for an occupational health and safety (OH&S) management system that promotes continuous improvement.
By integrating these strategies, an HSE Specialist can significantly improve Industrial Hygiene in the workplace, ensuring a safer and healthier environment for all employees.
How to Display Industrial Hygiene Skills on Your Resume
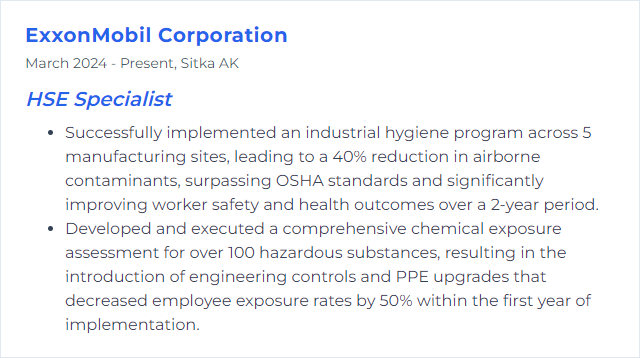
11. Ergonomics
Ergonomics is the science of designing work environments to fit the physical and cognitive abilities of workers, aiming to enhance safety, comfort, and productivity.
Why It's Important
Ergonomics is crucial as it prevents injuries and enhances productivity by designing workspaces, tools, and tasks to fit employees' physical capabilities and limitations, ensuring their health, safety, and efficiency.
How to Improve Ergonomics Skills
Improving ergonomics, particularly from an HSE (Health, Safety, and Environment) Specialist perspective, involves a systematic approach to designing workplaces, tasks, and jobs that fit the individuals' physical capabilities and limitations. Here’s a very short and concise guide:
Conduct Ergonomic Assessments: Regularly evaluate workstations and tasks to identify ergonomic risks such as poor posture, repetitive movements, and manual handling. Tools like the Rapid Upper Limb Assessment (RULA) and the Quick Exposure Check (QEC) can help.
Implement Ergonomic Solutions: Based on assessments, modify workstations, tools, and tasks. This can include adjustable chairs and desks, ergonomic keyboards, and tools designed to reduce strain. The CDC's Ergonomics and Musculoskeletal Disorders page offers solutions.
Promote Proper Work Techniques: Educate employees on proper posture, lifting techniques, and the use of ergonomic equipment. The OSHA Ergonomics page provides guidance and training resources.
Encourage Regular Breaks: Implement schedules that allow short breaks for stretching and resting, reducing muscle fatigue and strain. The Mayo Clinic's Office Stretches offers examples.
Engage Employees: Involve employees in the ergonomic process, encouraging them to report discomfort early and suggest improvements. This collaborative approach ensures solutions are practical and effective.
Review and Iterate: Continuously monitor and review the effectiveness of ergonomic interventions, making adjustments as necessary. This iterative process ensures ongoing improvement and adaptation to new challenges.
By following these steps, an HSE Specialist can significantly reduce the risk of work-related musculoskeletal disorders and enhance overall workplace safety and productivity.
How to Display Ergonomics Skills on Your Resume
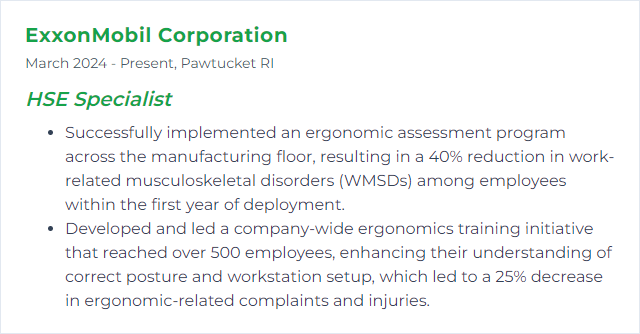
12. Waste Management
Waste Management involves the systematic control of the collection, treatment, and disposal of waste materials, adhering to environmental regulations and ensuring public health and safety.
Why It's Important
Waste Management is crucial for maintaining environmental integrity, protecting public health, and ensuring workplace safety by minimizing pollution, reducing hazards, and promoting sustainable practices.
How to Improve Waste Management Skills
Improving waste management, especially from an HSE (Health, Safety, and Environment) Specialist perspective, involves a multifaceted approach focusing on reducing waste generation, enhancing recycling efforts, and ensuring proper disposal methods. Here’s a concise guide:
Conduct Waste Audits: Regularly assess the types and volumes of waste generated to identify reduction and recycling opportunities. EPA Guidelines provide a framework for managing materials and waste.
Implement 3Rs: Prioritize the principles of Reduce, Reuse, and Recycle to minimize waste. Encouraging these practices can significantly lower waste management costs and environmental impact. WasteWise offers strategies and tools to help organizations apply these principles.
Adopt Eco-friendly Packaging: Shift towards biodegradable, recyclable, or reusable packaging options to reduce waste. The Sustainable Packaging Coalition provides resources and guidelines for sustainable packaging solutions.
Enhance Waste Segregation: Ensure waste is separated at the source to facilitate recycling and proper disposal. This includes hazardous and non-hazardous waste. The WHO Guidelines on safe management of wastes from health-care activities offer comprehensive insights.
Educate and Train Employees: Regular training on waste management practices, including handling hazardous waste, is vital. This not only complies with regulations but also fosters a culture of sustainability. OSHA Training resources can be useful for designing such programs.
Invest in Waste Management Technologies: Adopting technologies for waste collection, sorting, and recycling can enhance efficiency and reduce environmental impact. The International Solid Waste Association provides insights into innovative waste management technologies.
Collaborate with Waste Management Experts: Partnering with professional waste management services can optimize waste handling and disposal. They can offer tailored solutions based on the latest best practices and regulatory compliance. Resource Conservation and Recovery Act (RCRA) Orientation Manual is a valuable resource for understanding regulatory aspects.
By incorporating these strategies, an HSE Specialist can significantly contribute to improved waste management practices within their organization, leading to environmental, economic, and social benefits.
How to Display Waste Management Skills on Your Resume
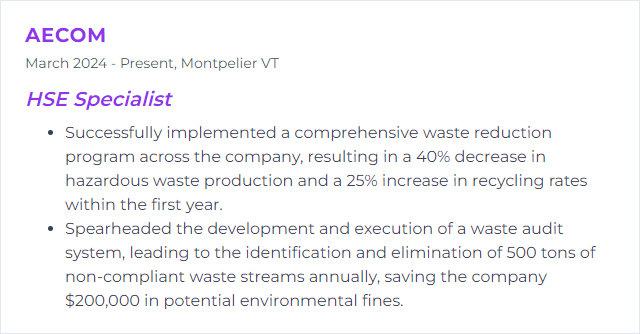