Top 12 Driller Skills to Put on Your Resume
A well-crafted resume highlighting key driller skills can significantly enhance your job prospects in the competitive drilling industry. This article outlines the top 12 skills that employers value, helping you to stand out as a highly capable and versatile candidate in the field of drilling.
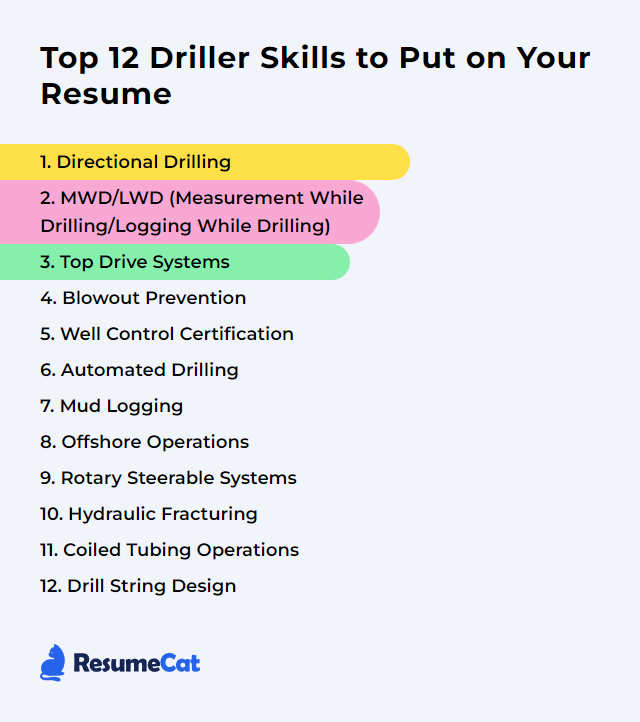
Driller Skills
- Directional Drilling
- MWD/LWD (Measurement While Drilling/Logging While Drilling)
- Top Drive Systems
- Blowout Prevention
- Well Control Certification
- Automated Drilling
- Mud Logging
- Offshore Operations
- Rotary Steerable Systems
- Hydraulic Fracturing
- Coiled Tubing Operations
- Drill String Design
1. Directional Drilling
Directional drilling is a technique used to precisely control the direction and angle of a wellbore to access and produce hydrocarbons from multiple locations from a single vertical well shaft, maximizing resource extraction and minimizing surface impact.
Why It's Important
Directional drilling is important for a driller because it allows for precise targeting of oil and gas reserves, reduces the surface footprint of drilling operations, and enables the drilling of multiple wells from a single location, enhancing efficiency and minimizing environmental impact.
How to Improve Directional Drilling Skills
Improving directional drilling involves enhancing accuracy, efficiency, and safety. For drillers, focusing on the following aspects can lead to significant improvements:
Training and Skills Development: Regularly update drilling teams on the latest directional drilling techniques and technologies. Online resources like IADC offer courses and certifications.
Advanced Planning: Utilize software tools for precise planning of the well path. Services like Schlumberger's Petrel provide detailed simulations and planning capabilities.
Real-Time Monitoring: Implement real-time monitoring systems to make immediate adjustments during drilling. Technologies like Halliburton's Real-Time Solutions can significantly enhance decision-making.
Equipment Maintenance: Ensure regular maintenance and checks of drilling equipment to avoid downtime and accidents. Consulting the equipment manufacturer's guidelines is crucial for proper maintenance.
Utilizing Advanced Tools: Invest in advanced drilling tools and technologies, such as Rotary Steerable Systems (RSS) and Measurement While Drilling (MWD) tools, for higher precision and control. Companies like Baker Hughes offer state-of-the-art drilling tools.
By focusing on these areas, drillers can significantly improve the outcomes of directional drilling operations.
How to Display Directional Drilling Skills on Your Resume
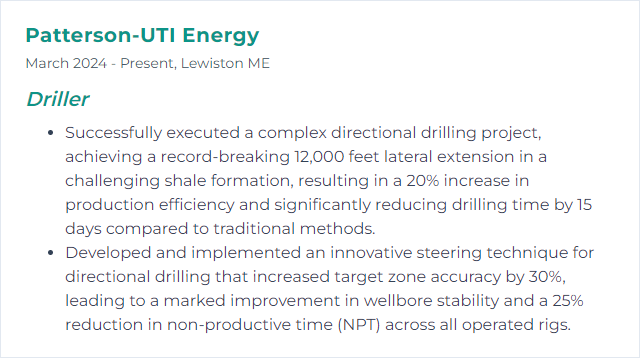
2. MWD/LWD (Measurement While Drilling/Logging While Drilling)
MWD (Measurement While Drilling) and LWD (Logging While Drilling) are real-time technologies used during drilling operations to measure various parameters. MWD focuses on drilling mechanics and trajectory, providing data such as hole depth, direction, and temperature. LWD offers more detailed geological information, like rock properties and formation evaluation. Both systems enhance decision-making, improve drilling efficiency, and reduce risks by enabling adjustments to drilling plans on the fly.
Why It's Important
MWD/LWD is crucial for drillers as it provides real-time data on wellbore conditions and formation properties, enabling accurate drilling, reduced risks, and optimized well placement for safety and efficiency.
How to Improve MWD/LWD (Measurement While Drilling/Logging While Drilling) Skills
Improving MWD/LWD involves enhancing data accuracy, reliability, and real-time decision-making capabilities. As a driller, focus on:
Regular Calibration: Ensure tools are calibrated regularly to maintain accuracy. Schlumberger's guidelines provide insights on maintaining tool integrity.
Advanced Training: Invest in advanced training for your team to interpret MWD/LWD data efficiently. Halliburton offers courses that could be beneficial.
Equipment Upgrades: Use the latest technology with enhanced sensors for better data collection. Information on the latest tech can be found through Baker Hughes' LWD solutions.
Real-time Monitoring: Implement systems for real-time data monitoring and analysis to make immediate adjustments. Weatherford's real-time capabilities offer insights into advanced monitoring techniques.
Collaboration: Work closely with geologists and engineers to integrate drilling data with geological models for better decision-making. The Society of Petroleum Engineers provides resources and case studies on effective collaboration.
By focusing on these areas, drillers can significantly enhance the effectiveness and efficiency of MWD/LWD operations.
How to Display MWD/LWD (Measurement While Drilling/Logging While Drilling) Skills on Your Resume
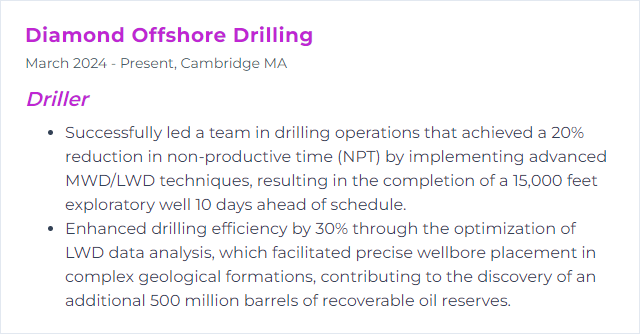
3. Top Drive Systems
Top Drive Systems (TDS) are advanced mechanical systems mounted on drilling rigs to rotate the drill string during the drilling process. Unlike traditional rotary table drilling, a top drive allows the drill to rotate from the top, enhancing drilling efficiency, safety, and enabling the execution of complex drilling operations. It provides drillers with better control over drilling parameters, leading to more accurate and faster drilling.
Why It's Important
Top Drive Systems are crucial for drillers as they enhance drilling efficiency, safety, and accuracy. They allow for continuous drilling by enabling the drill string to be rotated from its top, reducing manual handling and the time required for connecting drill pipes. This leads to faster drilling operations, improved hole quality, and reduced risk of accidents, making them an essential component in modern drilling operations.
How to Improve Top Drive Systems Skills
Improving Top Drive Systems for drillers involves focusing on maintenance, technology upgrades, and operational efficiency. Here’s a concise guide:
Regular Maintenance: Adhere to a strict maintenance schedule to prevent breakdowns and extend the system's life. Inspect and service key components regularly.
Technology Upgrades: Incorporate the latest technological advancements in top drive systems, such as automation and software updates, to enhance performance and safety.
Training: Ensure operators receive ongoing training on the latest operational procedures and safety protocols to maximize efficiency and minimize errors.
Operational Efficiency: Implement best practices for top drive system operation, focusing on optimizing speed and torque settings to improve drilling efficiency while ensuring the system’s longevity.
System Integration: Ensure seamless integration with other drilling rig systems for enhanced performance and monitoring capabilities. Utilizing integrated drilling control systems can lead to more efficient drilling operations.
By focusing on these areas, drillers can significantly improve the performance and reliability of Top Drive Systems.
How to Display Top Drive Systems Skills on Your Resume
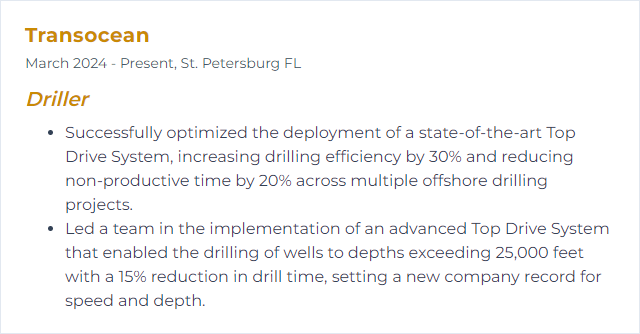
4. Blowout Prevention
Blowout prevention in drilling is a safety mechanism designed to control and prevent the uncontrolled release of underground fluids (such as oil, natural gas, or water) from a well, ensuring operational safety and environmental protection.
Why It's Important
Blowout prevention is crucial for a driller because it safeguards against uncontrolled release of underground fluids (oil, gas, water), preventing potentially catastrophic explosions, environmental disasters, and loss of life.
How to Improve Blowout Prevention Skills
Improving Blowout Prevention (BOP) involves a combination of training, equipment maintenance, and operational best practices tailored for drillers. Here's a concise guide:
Regular Training: Ensure drillers and crew are regularly trained in BOP systems and emergency response protocols. IADC offers courses and certifications.
Routine Maintenance: Conduct routine inspections and maintenance of BOP components to manufacturer specifications. Refer to API for standards and guidelines.
Operational Discipline: Follow strict operational protocols during drilling to minimize risks. Implement a Safety Management System (SMS) that includes BOP checks.
Use of Technology: Incorporate real-time monitoring systems to detect early signs of irregularities. SPE provides resources on the latest technologies and practices.
Effective Communication: Ensure clear and effective communication among the drilling team, especially concerning BOP operations and emergency procedures.
Focusing on these areas will significantly enhance Blowout Prevention capabilities.
How to Display Blowout Prevention Skills on Your Resume
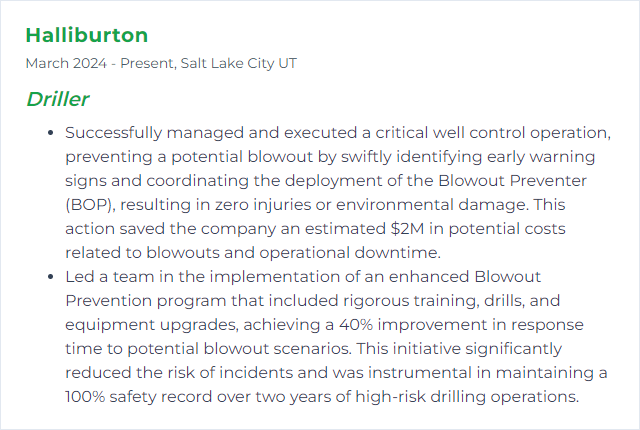
5. Well Control Certification
Well Control Certification for a Driller is a formal recognition that verifies a driller's knowledge and skills in managing and controlling well operations to prevent the uncontrolled release of underground fluids (such as oil, gas, and water), ensuring safe and effective drilling practices.
Why It's Important
Well Control Certification is crucial for Drillers as it ensures they possess the necessary skills and knowledge to prevent and manage well control incidents, safeguarding both personnel and the environment from potentially catastrophic blowouts and spills.
How to Improve Well Control Certification Skills
To improve your Well Control Certification as a Driller, follow these concise steps:
Stay Updated: Keep abreast of the latest IADC (International Association of Drilling Contractors) or IWCF (International Well Control Forum) guidelines and standards.
Continuous Learning: Enroll in refresher courses periodically to keep your knowledge and skills sharp.
Practical Experience: Gain hands-on experience. The more you drill, the better you understand well control principles in real-world scenarios.
Simulation Training: Participate in simulation training programs to enhance decision-making skills in critical situations.
Mentorship: Seek mentorship from experienced drillers and well control experts.
Health and Safety Training: Complete additional health and safety training relevant to drilling operations to broaden your understanding of well control from a safety perspective.
Improving your certification involves a combination of theoretical learning and practical application, underpinned by a commitment to ongoing professional development.
How to Display Well Control Certification Skills on Your Resume
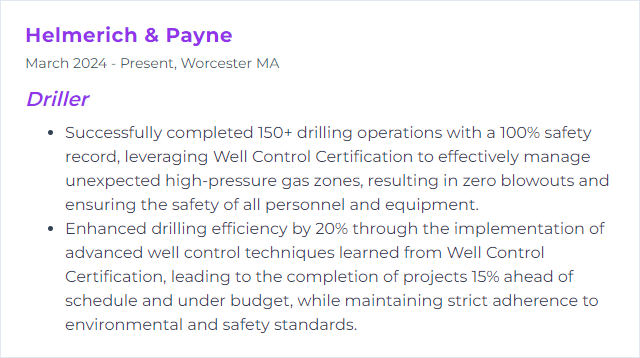
6. Automated Drilling
Automated drilling is a technology-driven process where machinery, controlled by computers and advanced software, performs drilling operations with minimal human intervention, enhancing efficiency, safety, and precision in drilling tasks.
Why It's Important
Automated drilling enhances precision, efficiency, and safety in drilling operations, significantly reducing human error and physical risks for drillers, thereby optimizing resource extraction and operational productivity.
How to Improve Automated Drilling Skills
Improving Automated Drilling involves enhancing precision, efficiency, and safety through technology and best practices. Here’s a concise guide:
Integrate Real-time Monitoring: Employ advanced sensors and IoT (Internet of Things) technology to monitor drilling operations in real-time. This allows for immediate adjustments and optimizations. Society of Petroleum Engineers provides resources on the latest in drilling technology.
Adopt Advanced Control Systems: Utilize AI and machine learning for predictive maintenance and operation optimization. These systems can anticipate issues before they occur, improving efficiency. IEEE Xplore offers research articles on AI applications in drilling.
Implement High-Precision Navigation: Use high-precision GPS and MWD (Measurement While Drilling) technologies to improve the accuracy of drilling paths. This minimizes deviations and maximizes resource extraction. The International Association of Drilling Contractors (IADC) discusses navigation technologies in their publications.
Focus on Safety and Training: Ensure all personnel are trained on automated systems and safety protocols. Utilizing VR (Virtual Reality) for training can prepare teams for various scenarios without real-world risks. Occupational Safety and Health Administration (OSHA) provides guidelines on workplace safety, including in drilling operations.
Regular Maintenance and Upgrades: Keep all automated systems well-maintained and regularly update software to leverage advancements in technology and improve operational efficiency. Society for Maintenance & Reliability Professionals (SMRP) offers insights on maintaining industrial equipment.
By focusing on these areas, drillers can significantly improve the performance and safety of automated drilling operations.
How to Display Automated Drilling Skills on Your Resume
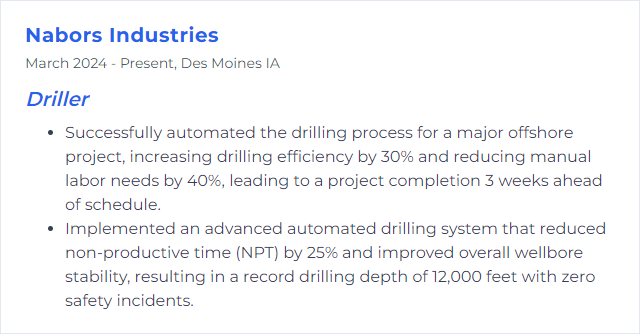
7. Mud Logging
Mud logging is the process of monitoring and analyzing the drilling mud for traces of rock or gas fragments to determine the geological formation and presence of hydrocarbons while drilling for oil or gas, providing critical real-time information on the well status to guide drilling decisions.
Why It's Important
Mud logging is crucial for drillers as it provides real-time monitoring of drilling conditions, identifies potential hazards, and helps optimize drilling efficiency by analyzing rock cuttings and drilling mud for signs of oil or gas presence, pressure changes, and formation characteristics.
How to Improve Mud Logging Skills
To enhance Mud Logging for a Driller:
Implement Real-Time Monitoring: Use advanced sensors and software that provide real-time data on drilling parameters and formation properties. This enables quicker adjustments to drilling operations. Schlumberger offers solutions in this area.
Integrate Data Analysis Tools: Utilize software that integrates and analyzes data from various sources (e.g., LWD, mud logs, MWD) for better decision-making. Halliburton provides such tools.
Enhance Training: Ensure drillers and mud loggers have access to ongoing training on the latest technologies and best practices. IADC offers courses and certifications.
Use Automated Systems: Implement automated drilling systems that adjust drilling parameters in real-time based on mud logging data, optimizing drilling efficiency and safety. NOV has solutions in this field.
Collaborate with Specialists: Work closely with geologists and mud logging specialists for better interpretation of the data and to adjust drilling strategies accordingly. Collaboration platforms like Slack can facilitate this communication.
By focusing on these areas, drillers can significantly improve the efficiency and safety of their operations through enhanced mud logging practices.
How to Display Mud Logging Skills on Your Resume
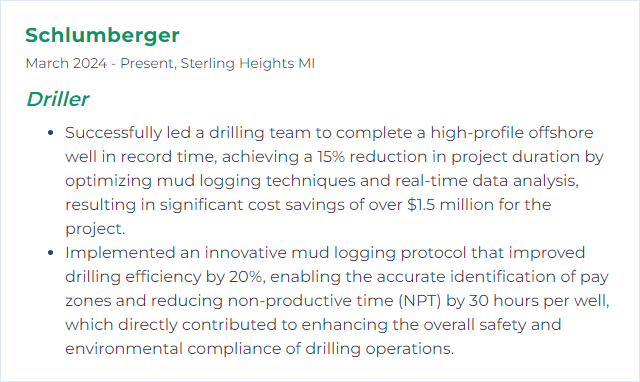
8. Offshore Operations
Offshore operations, in the context of a Driller, refer to the drilling activities conducted on oil rigs or platforms located at sea, away from the mainland, to extract oil or natural gas from beneath the seabed.
Why It's Important
Offshore operations are crucial for drillers as they enable the exploration and extraction of oil and gas reserves located beneath the ocean floor. These operations are vital for meeting global energy demands and contribute significantly to the energy sector's economy.
How to Improve Offshore Operations Skills
Improving offshore operations, particularly from a driller's perspective, involves enhancing safety, efficiency, and environmental sustainability. Here's a concise guide:
Safety Enhancements: Prioritize safety by implementing rigorous training programs and adopting the latest safety technologies. The International Association of Drilling Contractors (IADC) offers resources and guidelines for safety improvements in drilling operations.
Efficiency Improvements: Leverage advanced drilling technologies such as automated drilling systems to increase operational efficiency. The Society of Petroleum Engineers (SPE) provides insights into technological advancements and efficiency strategies.
Environmental Sustainability: Adopt environmentally friendly practices and technologies to minimize the ecological impact of drilling operations. The Environmental Protection Agency (EPA) offers guidelines on environmental practices for offshore oil and gas operations.
Continuous Training and Education: Invest in continuous education and training programs for the workforce to keep them updated with the latest operational, safety, and environmental practices. The Offshore Technology Conference (OTC) is a platform for learning about the latest trends and technologies in offshore operations.
Regular Maintenance and Inspections: Ensure regular maintenance and inspections of equipment to prevent failures and downtime. The American Petroleum Institute (API) sets standards for the oil and natural gas industry, including equipment maintenance and inspection protocols.
By focusing on these areas, offshore drilling operations can be improved significantly, leading to safer, more efficient, and environmentally friendly practices.
How to Display Offshore Operations Skills on Your Resume
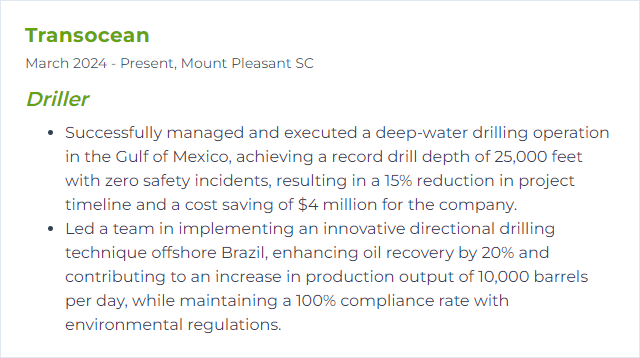
9. Rotary Steerable Systems
Rotary Steerable Systems (RSS) are advanced drilling tools used in the oil and gas industry that enable precise directional control of the drill bit while it rotates continuously from the surface. This technology allows drillers to steer the wellbore in real-time towards specific geological targets without stopping the drilling process, enhancing efficiency and accuracy in well placement.
Why It's Important
Rotary Steerable Systems (RSS) are important for drillers because they allow for precise directional drilling, enabling drillers to navigate complex geological formations, reach targets more efficiently, and optimize well placement, which can significantly enhance production rates and reduce drilling time and costs.
How to Improve Rotary Steerable Systems Skills
To improve Rotary Steerable Systems (RSS) from a driller's perspective, focus on the following key areas:
Training and Competency: Ensure drillers receive comprehensive training on RSS technology, including operational practices and troubleshooting. Familiarity with the system enhances efficiency and reduces downtime.
Real-Time Data Utilization: Leverage real-time data monitoring to make informed decisions on-the-fly, optimizing drilling parameters for improved performance and minimizing tool stress.
Preventive Maintenance: Adhere to a strict preventive maintenance schedule to ensure all RSS components are in optimal condition, reducing the risk of non-productive time.
Collaboration with Service Providers: Work closely with RSS service providers for customized solutions tailored to specific drilling challenges, enabling better performance and tool longevity.
Feedback Loop: Establish a feedback mechanism between the drilling crew and the RSS technical support team to continuously improve tool performance and address any operational issues promptly.
By focusing on these areas, drillers can enhance the efficiency and reliability of Rotary Steerable Systems, leading to improved drilling performance and reduced operational costs.
How to Display Rotary Steerable Systems Skills on Your Resume
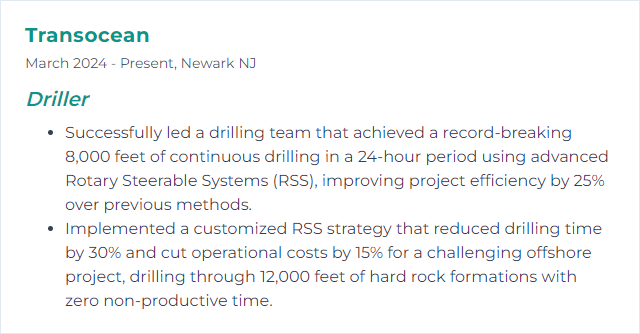
10. Hydraulic Fracturing
Hydraulic fracturing, often referred to as fracking, is a method used to extract oil or natural gas from underground formations. It involves injecting high-pressure fluid into a wellbore to create fractures in the rock formation, allowing oil or gas to flow more freely to the surface. For a driller, it's a technique to enhance well production by improving access to the hydrocarbons trapped in rock.
Why It's Important
Hydraulic fracturing is important for a driller because it enables the extraction of oil and natural gas from rock formations deep underground that were previously inaccessible, significantly increasing well productivity and resource recovery.
How to Improve Hydraulic Fracturing Skills
Improving hydraulic fracturing, especially from a driller's perspective, involves enhancing efficiency, reducing environmental impact, and ensuring the safety and integrity of the process. Here are concise strategies with relevant resources:
Optimize Fracture Design: Utilize advanced modeling software to simulate and optimize fracture designs, considering geological characteristics. Schlumberger offers solutions for optimizing fracture designs.
Use Eco-Friendly Fluids: Shift towards using more environmentally friendly fracturing fluids to reduce environmental impact. Halliburton's CleanSuite technologies focus on reducing environmental footprint.
Implement Real-Time Monitoring: Employ real-time monitoring systems to adjust drilling and fracturing operations on-the-fly for efficiency and safety. Baker Hughes provides real-time operations monitoring solutions.
Enhance Wellbore Integrity: Ensure the integrity of wellbores by using advanced casing and cementing techniques. Weatherford offers comprehensive well integrity solutions.
Water Management: Improve water management practices, including recycling and treatment, to minimize water usage and disposal challenges. Veolia specializes in water treatment solutions for the oil and gas industry.
Adopt Automation and Robotics: Leverage automation and robotics for safer and more efficient fracturing operations. NOV provides automated drilling solutions.
Improving hydraulic fracturing involves a multifaceted approach that combines technology, sustainability, and safety to enhance operational efficiency and reduce environmental impact.
How to Display Hydraulic Fracturing Skills on Your Resume
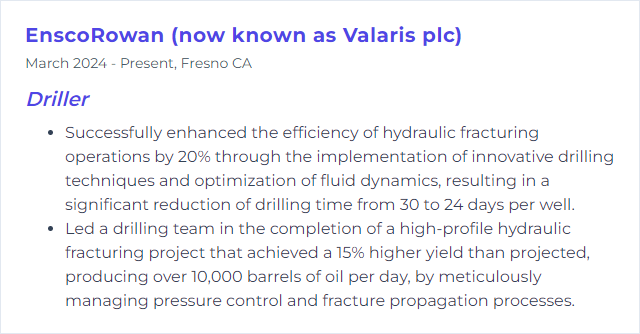
11. Coiled Tubing Operations
Coiled Tubing Operations involve using a long, continuous length of steel or composite tubing which is spooled on a large reel. For drillers, it is primarily used for interventions in oil and gas wells such as for maintenance, drilling, completions, and plugging work, without the need to remove the wellhead or production tubing. This method allows for quicker and more efficient operations compared to conventional drilling or workover rigs.
Why It's Important
Coiled tubing operations are crucial for drillers as they enable efficient well intervention and maintenance without the need to remove the drill pipe, significantly reducing downtime and operational costs. This enhances well productivity and safety during drilling, completion, and repair activities.
How to Improve Coiled Tubing Operations Skills
Improving Coiled Tubing Operations involves enhancing efficiency, safety, and the effectiveness of interventions. Here’s a concise guide:
Pre-Operation Planning: Detailed planning and simulation of operations can significantly reduce risks and downtime. Using software like CoilCADE for job design and modeling improves efficiency.
Real-Time Monitoring: Implement advanced real-time monitoring systems to track operations and make immediate adjustments. Technologies like CoilScan provide diagnostics that help in decision-making.
Equipment Maintenance: Regular maintenance and inspection of coiled tubing units and accessories ensure reliability and safety. Adopt a proactive approach to equipment care to minimize unexpected failures.
Training and Competency: Continuous training programs for operators enhance operational safety and efficiency. Utilize resources from IADC for up-to-date training and certifications.
Adopting New Technologies: Stay updated with the latest advancements in coiled tubing technology, such as the use of CT Tractor for improved reach in horizontal wells, to optimize operations.
Health, Safety, and Environment (HSE): Implement strict HSE protocols to protect personnel and the environment. Guidelines from OSHA can help in establishing a safe working environment.
For drillers, focusing on these aspects can lead to safer, more efficient, and cost-effective coiled tubing operations.
How to Display Coiled Tubing Operations Skills on Your Resume
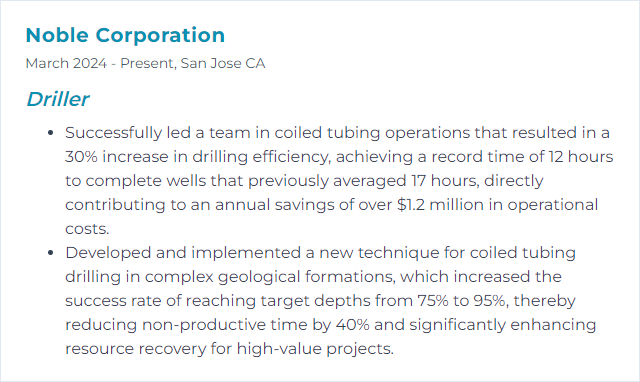
12. Drill String Design
Drill string design refers to the process of selecting and configuring the components of the drill string—the assembly of drill pipe, heavy-weight drill pipe, drill collars, and the bottom hole assembly—tailored to safely and efficiently achieve the drilling objectives, considering factors like well depth, borehole geometry, expected formation pressures, and the drilling environment. This design is crucial for a driller to ensure operational integrity, optimize drilling performance, and minimize the risk of drill string failures.
Why It's Important
Drill string design is crucial for a driller because it ensures optimal performance, safety, and cost-efficiency by selecting the right components and configurations to withstand operational stresses and conditions, thereby preventing failures and non-productive time.
How to Improve Drill String Design Skills
Improving drill string design involves optimizing its components to enhance performance, reduce costs, and mitigate risks during drilling operations. Here's a concise guide:
Material Selection: Choose high-grade materials that offer the best balance between strength and flexibility to withstand operational stresses. API specifications can guide material standards.
Drill Pipe Selection: Select the appropriate drill pipe size, weight, and grade for your specific drilling conditions. Reference the IADC Drilling Manual for guidelines.
Tool Joint Design: Opt for tool joints that match the drill pipe's strength and are suited for the anticipated drilling environment. Custom tool joint designs may be necessary for extreme conditions.
Bottom Hole Assembly (BHA) Design: Design your BHA considering factors like hole size, formation type, and drilling direction. Utilize Schlumberger's guidelines for optimized BHA configurations.
Drill Bit Selection: Choose the right drill bit (PDC, roller cone, etc.) based on the formation characteristics. Halliburton's Drill Bits & Services provides a selection guide.
Stress Analysis: Perform a detailed stress analysis on the drill string to identify weak points and potential failure modes. Software like NOV's IDEAS can be useful.
Torsional Vibration Analysis: Analyze and mitigate torsional vibrations to prevent tool failures. Techniques and tools for analysis can be found on Weatherford's website.
Hydraulic Optimization: Ensure optimal hydraulic performance for effective hole cleaning and bit cooling. Baker Hughes's HYDPRO software offers hydraulic simulation capabilities.
Regular Inspection and Maintenance: Implement a strict inspection and maintenance schedule to identify wear and damage early. Guidelines are available through DS-1 Volume 3 for drill stem inspection.
By considering these aspects and utilizing resources from industry leaders, drillers can significantly improve drill string design for safer and more efficient drilling operations.
How to Display Drill String Design Skills on Your Resume
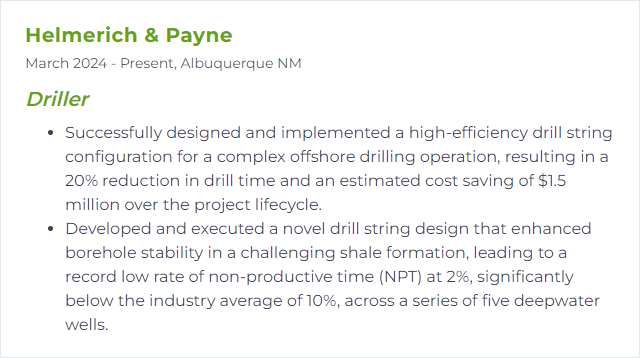