Top 12 Directional Driller Skills to Put on Your Resume
In the highly specialized field of directional drilling, showcasing a robust set of skills on your resume can significantly elevate your marketability to potential employers. This article outlines the top 12 directional driller skills essential for demonstrating your expertise and precision in navigating complex underground drilling projects, setting you apart in the competitive job landscape.
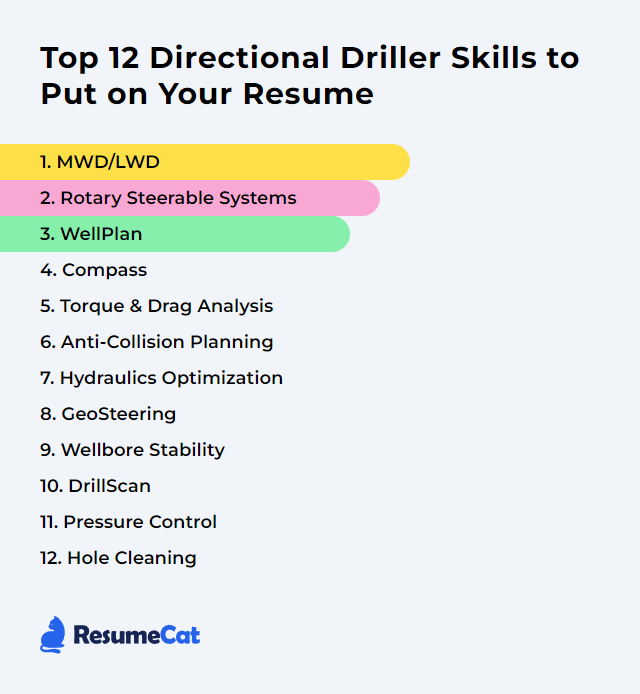
Directional Driller Skills
- MWD/LWD
- Rotary Steerable Systems
- WellPlan
- Compass
- Torque & Drag Analysis
- Anti-Collision Planning
- Hydraulics Optimization
- GeoSteering
- Wellbore Stability
- DrillScan
- Pressure Control
- Hole Cleaning
1. MWD/LWD
MWD (Measurement While Drilling) and LWD (Logging While Drilling) are technologies used in directional drilling to provide real-time data on the wellbore position (MWD) and formation properties (LWD) to the surface, enabling precise steering of the drill bit to optimize well placement and production.
Why It's Important
MWD/LWD (Measurement While Drilling/Logging While Drilling) is crucial for a Directional Driller because it provides real-time downhole data on parameters such as direction, inclination, tool face, and formation properties. This information enables precise steering of the drill bit to optimize well placement, improve drilling efficiency, and mitigate risks associated with drilling operations.
How to Improve MWD/LWD Skills
Improving Measurement-While-Drilling (MWD) and Logging-While-Drilling (LWD) systems is crucial for directional drillers to enhance accuracy, efficiency, and decision-making during drilling operations. Here’s a very short and concise guide:
Enhance Data Quality: Implement real-time data quality monitoring tools to ensure high-quality measurements. Use advanced algorithms to filter noise from the signal for clearer data interpretation.
Upgrade Hardware: Invest in the latest MWD/LWD tools with improved sensor technology for higher resolution data and better durability under extreme conditions (Schlumberger).
Increase Communication Speed: Utilize high-speed telemetry systems, like electromagnetic or mud pulse telemetry, to increase data transmission rates, allowing for quicker decision-making (Halliburton).
Integrate Software Solutions: Use advanced drilling software for real-time data analysis and visualization. Software solutions can provide predictive modeling and simulations to optimize drilling parameters (Baker Hughes).
Regular Training: Ensure the drilling team, especially the directional drillers, undergo regular training on the latest MWD/LWD technologies and best practices for data interpretation and decision-making.
Collaborative Decision Making: Foster a collaborative environment where data from MWD/LWD systems is integrated with geological and reservoir data for comprehensive decision-making.
Preventive Maintenance: Adopt a rigorous maintenance schedule for MWD/LWD tools to prevent downhole failures and non-productive time.
By focusing on these areas, directional drillers can significantly improve the performance and reliability of MWD/LWD operations, leading to more efficient and cost-effective drilling projects.
How to Display MWD/LWD Skills on Your Resume
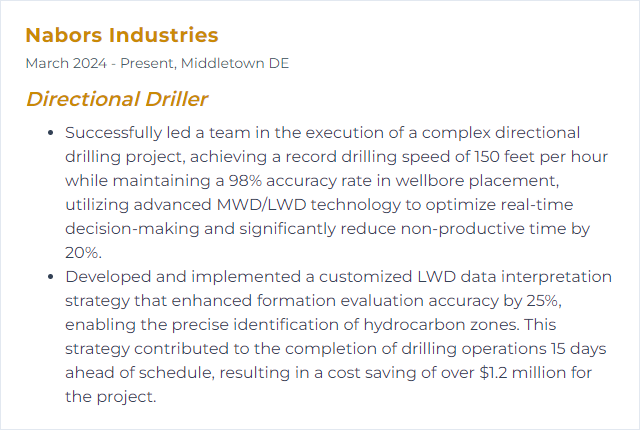
2. Rotary Steerable Systems
Rotary Steerable Systems (RSS) are advanced drilling tools used by directional drillers to accurately control the direction of the drill bit while drilling continuously, allowing for precise wellbore placement without the need to stop and reorient the drill string, enhancing drilling efficiency and accuracy.
Why It's Important
Rotary Steerable Systems (RSS) are crucial for directional drillers because they significantly enhance drilling efficiency and accuracy. They allow for continuous and precise directional control while drilling, minimizing the need for corrective actions and reducing drilling time. This leads to more accurate wellbore placement, improved well productivity, and reduced operational costs.
How to Improve Rotary Steerable Systems Skills
Improving Rotary Steerable Systems (RSS) for Directional Drillers involves focusing on precision, efficiency, and equipment reliability. Here's a concise guide:
Enhanced Training: Ensure drillers undergo continuous training on the latest RSS technologies and operational best practices. Schlumberger and Halliburton offer advanced training and resources.
Real-Time Data Analysis: Utilize real-time monitoring and data analysis tools for immediate adjustments and optimization. NOV provides solutions for real-time decision-making.
Equipment Maintenance: Regular and rigorous maintenance schedules to prevent downtime and ensure system reliability. Baker Hughes emphasizes the importance of maintenance for RSS performance.
Software Upgrades: Keep software updated for the latest advancements in trajectory planning and drilling efficiency. Weatherford offers software solutions tailored for RSS.
Collaboration with Manufacturers: Work closely with RSS manufacturers for customized solutions, feedback loops, and to stay ahead of technological advancements.
By focusing on these areas, Directional Drillers can significantly improve the performance and outcomes of their Rotary Steerable Systems.
How to Display Rotary Steerable Systems Skills on Your Resume
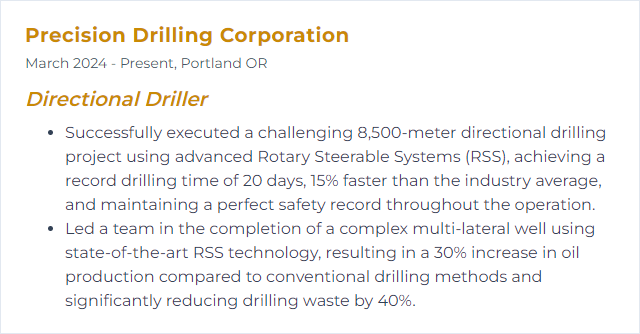
3. WellPlan
WellPlan is a software tool designed for planning and optimizing the trajectory of wells in directional drilling operations, assisting Directional Drillers in ensuring accurate and efficient drilling paths.
Why It's Important
WellPlan is important for a Directional Driller as it provides detailed drilling plans and trajectory predictions, ensuring accurate, efficient, and safe drilling operations while minimizing risks and optimizing resource use.
How to Improve WellPlan Skills
Improving WellPlan for a Directional Driller involves enhancing accuracy, efficiency, and adaptability in the drilling process. Here's a concise guide:
Update Software Regularly: Ensure you're using the latest version of WellPlan to leverage new features and improvements. Schlumberger Software Updates
Integrate Real-Time Data: Incorporate real-time drilling data for dynamic adjustments. Tools like NOV's NOVOS can provide valuable insights.
Utilize Advanced Simulation Tools: Use advanced simulation tools to anticipate challenges and plan contingencies. DrillScan's advanced drilling software can be particularly useful.
Enhance Communication: Improve communication channels between the rig and the planning team for better coordination and decision-making. IHS Markit provides platforms for efficient data exchange.
Invest in Training: Regular training sessions for the team on the latest features and best practices in WellPlan and directional drilling. Schlumberger Training Services offer courses that could be beneficial.
Implement Data Analytics: Use data analytics to analyze past drilling operations and identify areas for improvement. Baker Hughes's analytics solutions could be of assistance.
Adopt Best Practices: Adopt industry best practices for well planning and execution. Resources like SPE (Society of Petroleum Engineers) provide valuable research and case studies.
Feedback Loop: Create a feedback loop from operations back to the planning phase to continuously improve the planning process.
By focusing on these areas, a directional driller can significantly enhance the effectiveness and efficiency of WellPlan.
How to Display WellPlan Skills on Your Resume
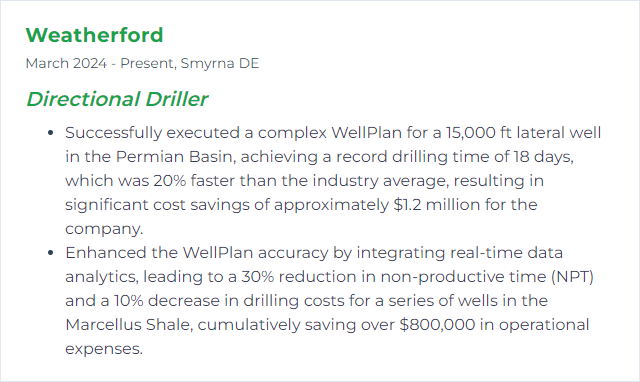
4. Compass
In the context of a Directional Driller, a compass is an instrument used to determine the drill bit's orientation and direction underground, ensuring accurate drilling along the predetermined path.
Why It's Important
For a Directional Driller, a compass is essential for determining the accurate orientation of the drilling equipment, ensuring the drill bit progresses in the correct direction to reach the targeted oil or gas reservoir efficiently and safely.
How to Improve Compass Skills
To improve a compass for a Directional Driller, follow these concise steps:
Calibration: Regularly calibrate your compass to ensure accuracy. Use known reference points or a professional calibration service.
Magnetic Interference: Minimize magnetic interference by keeping the compass away from metallic objects and electrical equipment.
Maintenance: Regularly clean the compass and check for damage to ensure smooth needle movement and reliable readings.
Digital Tools: Complement the compass with digital tools like GNSS receivers for enhanced precision in directional drilling operations.
Education: Continuously educate yourself on magnetic declination changes and how to adjust your compass readings accordingly.
Quality Equipment: Invest in a high-quality, drilling-specific compass that offers enhanced durability and precision for professional use.
By following these steps, you can improve compass accuracy and reliability for directional drilling applications.
How to Display Compass Skills on Your Resume
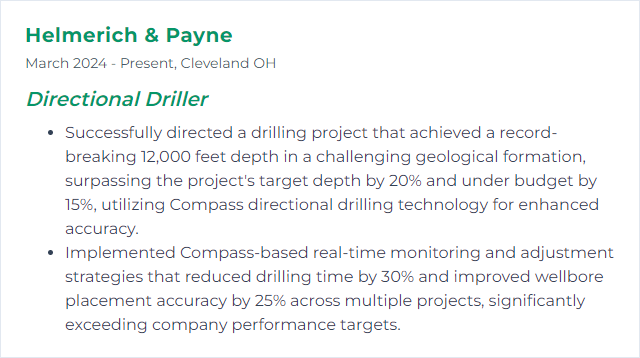
5. Torque & Drag Analysis
Torque & Drag Analysis is a computational evaluation used by directional drillers to predict and manage the forces of torque (twisting force) and drag (frictional force) encountered by the drill string and bottom hole assembly during wellbore drilling operations. This analysis helps in optimizing drilling parameters, preventing equipment damage, and ensuring efficient and safe drilling practices.
Why It's Important
Torque and Drag Analysis is crucial for a Directional Driller as it helps in predicting and managing the forces acting on the drill string during operations. This ensures optimal drilling efficiency, prevents equipment damage, and minimizes the risk of stuck pipe incidents, thus saving time and cost while enhancing safety.
How to Improve Torque & Drag Analysis Skills
Improving Torque & Drag Analysis for a Directional Driller involves a few key steps aimed at optimizing drilling performance and minimizing risks. Here’s a concise guide:
Use Accurate Wellbore Profiles: Ensure the wellbore trajectory data is precise. This involves updating the planned vs. actual well path continuously.
Update Drilling Parameters: Regularly update drilling parameters in your analysis software to reflect current operations. This includes weight on bit (WOB), rotational speed (RPM), and mud properties.
Implement Real-time Monitoring: Utilize real-time monitoring tools to track torque and drag in real-time, allowing for immediate adjustments. Schlumberger provides technologies for real-time data acquisition.
Apply Correct Friction Factors: Accurately apply friction factors based on the latest wellbore conditions and mud types. This can involve lab tests or data from similar wells.
Use Advanced Software Tools: Employ advanced T&D analysis software with capabilities for modeling complex well paths and conditions. Landmark Solutions - Halliburton offers advanced drilling software for comprehensive analysis.
Conduct Pre-Drill Analysis: Perform detailed pre-drill torque and drag analysis to anticipate challenges and plan mitigation strategies.
Training and Experience: Ensure the drilling team, especially the directional drillers, are trained in interpreting torque and drag data and understanding its implications on drilling operations.
By focusing on these areas, a Directional Driller can significantly improve the accuracy and effectiveness of Torque & Drag Analysis, leading to safer and more efficient drilling operations.
How to Display Torque & Drag Analysis Skills on Your Resume
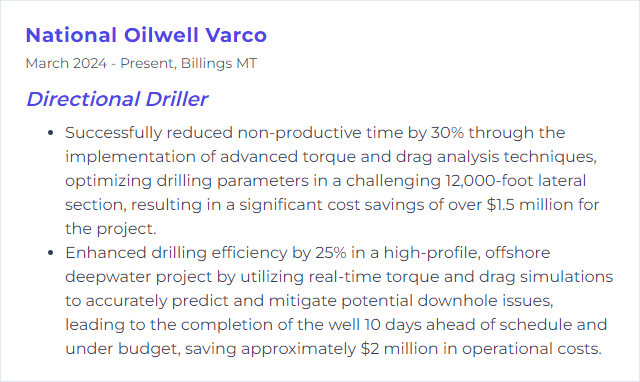
6. Anti-Collision Planning
Anti-Collision Planning in the context of a Directional Driller involves designing and executing drilling paths that avoid interference with existing wellbores to prevent collisions, ensuring safety and integrity of the operation.
Why It's Important
Anti-collision planning is crucial for a Directional Driller to ensure the safety and integrity of drilling operations by preventing the drill bit from inadvertently colliding with existing infrastructure, such as other wells. This minimizes the risk of costly damages, environmental hazards, and potential loss of the wellbore.
How to Improve Anti-Collision Planning Skills
Improving Anti-Collision Planning for a Directional Driller involves several key steps aimed at enhancing safety and efficiency during drilling operations. Here's a concise guide:
Comprehensive Data Analysis: Use real-time and historic drilling data to analyze potential collision threats. Software like Halliburton's Landmark aids in visualizing well paths and identifying risks.
Advanced Software Tools: Implement advanced drilling software that offers predictive modeling for collision risks. Schlumberger's Petrel and DrillScan’s well planning solutions provide sophisticated simulations and anti-collision algorithms.
Real-Time Monitoring: Utilize real-time monitoring systems to track the wellbore position accurately. Systems like NOV's eVolve optimize drilling operations and enhance safety protocols.
Regular Training: Ensure all personnel, especially directional drillers, undergo regular training on the latest anti-collision techniques and technologies. Organizations like IADC offer courses and resources.
Pre-Drill Planning: Engage in thorough pre-drill planning, including detailed risk assessments and contingency planning. Tools like Baker Hughes's CIRCA well planning software can assist in this phase.
Collaboration and Communication: Foster a collaborative environment where information is freely shared among team members. Effective communication ensures that all potential risks are identified and mitigated promptly.
By integrating these strategies, directional drillers can significantly improve anti-collision planning, ensuring safer and more efficient drilling operations.
How to Display Anti-Collision Planning Skills on Your Resume
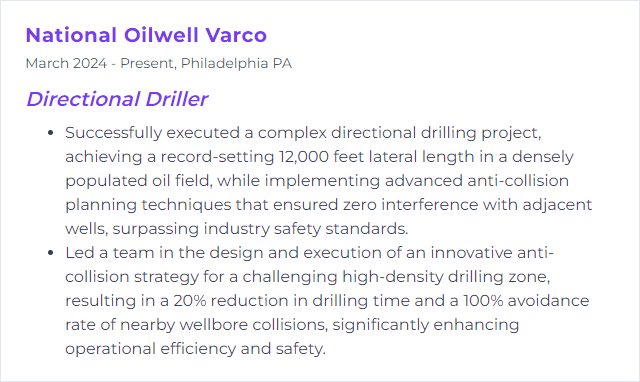
7. Hydraulics Optimization
Hydraulics optimization in the context of directional drilling involves fine-tuning the flow rate and pressure of drilling fluids to maximize drilling efficiency, ensure the stability of the wellbore, and optimize the removal of drill cuttings, while minimizing wear on the drill bit and the risk of formation damage. This process is crucial for maintaining optimal drilling performance and minimizing operational costs.
Why It's Important
Hydraulics optimization is crucial for a Directional Driller because it ensures efficient drilling by optimizing mud flow rates and pressures, which minimizes drill bit wear, prevents downhole problems, and enhances the rate of penetration. This results in cost-effective drilling operations and improved well productivity.
How to Improve Hydraulics Optimization Skills
To improve hydraulics optimization in directional drilling, focus on these key strategies:
Optimize Mud Properties: Adjust the viscosity and density of the drilling fluid to enhance flow and cuttings removal. Utilizing advanced mud additives can also improve performance. Schlumberger Mud Solutions
Nozzle Selection: Choose the correct nozzle size and configuration for your drill bit to ensure optimal hydraulic horsepower at the bit and efficient cuttings evacuation. Baker Hughes Drill Bit Nozzles
Flow Rate Management: Optimize the pump flow rate to balance cuttings removal with preventing formation damage and maintaining borehole stability. Halliburton Drilling Fluids
Equipment Configuration: Use software and predictive models to simulate and configure your drilling assembly for optimal hydraulics. This includes adjusting pipe sizes, lengths, and pump pressures. NOV Downhole Tools
Real-time Monitoring: Implement real-time monitoring systems to track drilling fluid properties, flow rates, and pressures to make immediate adjustments for optimal performance. Weatherford Drilling Services
By focusing on these areas, a directional driller can significantly improve hydraulics optimization.
How to Display Hydraulics Optimization Skills on Your Resume
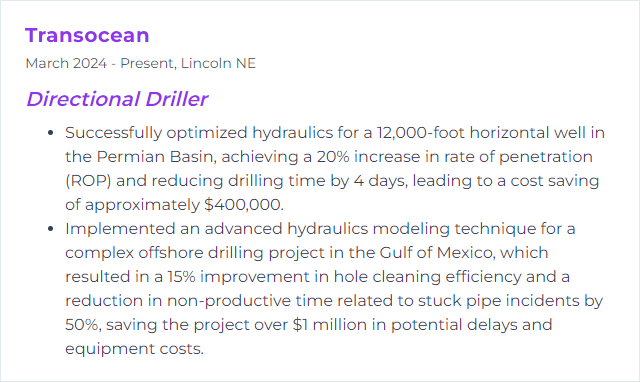
8. GeoSteering
GeoSteering is the real-time process of adjusting the direction of a drill bit to follow a predetermined geological boundary or target layer, optimizing well placement for maximum productivity. For a Directional Driller, it involves interpreting geological and drilling data to make immediate decisions on the drill path to stay within the desired formation.
Why It's Important
GeoSteering is crucial for a Directional Driller because it allows for real-time adjustments in the drilling direction to accurately target and stay within the most productive zones of the reservoir, optimizing hydrocarbon recovery and minimizing drilling costs and risks.
How to Improve GeoSteering Skills
Improving GeoSteering, especially from the perspective of a Directional Driller, involves enhancing real-time data interpretation, communication, and drilling techniques to precisely navigate the drill bit through the target geological formations. Here are concise strategies:
Enhance Real-time Data Acquisition: Utilize advanced Logging While Drilling (LWD) tools to obtain high-quality geological and petrophysical data in real-time.
Integrate Data Visualization Tools: Adopt 3D visualization software to interpret data effectively, allowing for immediate adjustments to drilling paths.
Improve Communication: Establish a robust communication system between the rig site and geosteering experts to enable swift decision-making.
Continuous Learning and Training: Engage in ongoing training programs focused on the latest geosteering techniques and technologies.
Adopt Predictive Analytics: Use predictive modeling tools to foresee drilling challenges and optimize drill paths ahead of time.
Implementing these strategies can significantly improve geosteering outcomes, enhancing well placement accuracy and overall drilling efficiency.
How to Display GeoSteering Skills on Your Resume
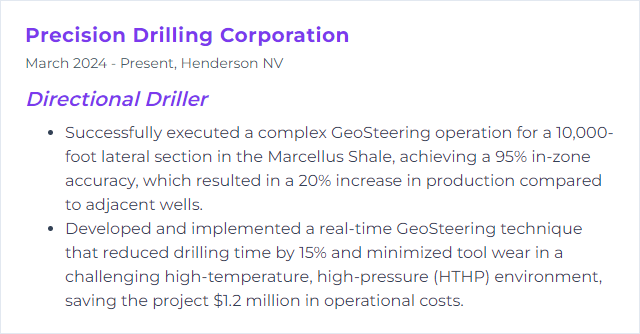
9. Wellbore Stability
Wellbore stability refers to the condition where the walls of a drilled wellbore maintain their structural integrity and do not collapse, fracture, or undergo excessive deformation. For a Directional Driller, maintaining wellbore stability is critical to ensure safe, efficient, and cost-effective drilling operations, especially when navigating complex geological formations at various angles.
Why It's Important
Wellbore stability is crucial for a Directional Driller to ensure safe and efficient drilling operations, minimize non-productive time, and avoid incidents like wellbore collapses or stuck drill strings, which can significantly increase costs and operational risks.
How to Improve Wellbore Stability Skills
To improve wellbore stability for a Directional Driller, consider the following concise strategies:
Understand Geomechanics: Study the in-situ stresses and rock mechanical properties. Tools like Schlumberger's geomechanics services can provide insights.
Optimize Mud Weight: Use pore pressure and fracture gradient data to select a mud weight that minimizes the risk of wellbore collapse or fracturing. The IADC Mud Weight Window provides guidelines.
Use Appropriate Drilling Fluids: Select drilling fluids (mud systems) that enhance wellbore stability, like inhibitive mud systems for shale formations.
Employ Borehole Strengthening Techniques: Techniques such as wellbore plugging and proper drilling practices can reduce the risk of wellbore instability. Baker Hughes' solutions offer various options.
Monitor Real-Time Data: Use LWD (Logging While Drilling) and MWD (Measurement While Drilling) technologies to monitor well conditions and adjust operations as needed.
Plan the Well Path Carefully: A well-planned trajectory that accounts for stress orientations and magnitudes can help minimize wellbore instability. Software like Halliburton's Landmark aids in efficient planning.
By integrating these strategies, a Directional Driller can enhance wellbore stability, reducing non-productive time and minimizing risks associated with wellbore collapse, stuck pipe, and loss of circulation.
How to Display Wellbore Stability Skills on Your Resume
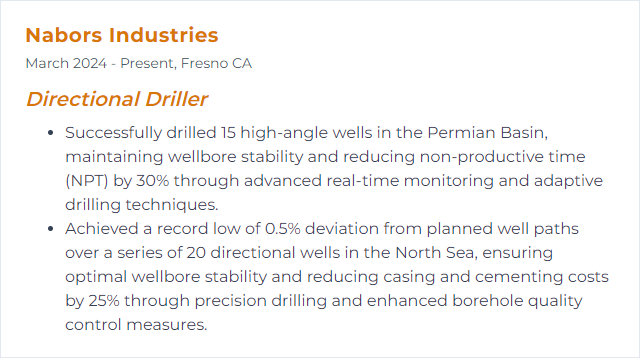
10. DrillScan
DrillScan is a software solution and service provider that offers advanced drilling engineering software, expertise, and technologies to improve the efficiency and safety of drilling operations, particularly for directional drillers. It aids in planning, optimizing, and executing directional and horizontal wells by analyzing and predicting drilling mechanics and well trajectory.
Why It's Important
DrillScan is important for a Directional Driller because it provides advanced drilling software and expertise that enhance the planning, execution, and analysis of directional drilling operations, thereby improving accuracy, efficiency, and safety.
How to Improve DrillScan Skills
Improving DrillScan for a Directional Driller involves enhancing its capabilities in drilling optimization, wellbore placement, and real-time decision-making. Here’s a short guide:
Update Software Regularly: Ensure your DrillScan software is always up to date. New updates often include bug fixes, new features, and improvements in data analysis and modeling capabilities. DrillScan’s official website should have the latest software updates and release notes.
Integrate Real-Time Data: Enhance decision-making by integrating real-time drilling data. This allows for immediate adjustments in drilling operations, optimizing wellbore placement and minimizing risks. NOV and Schlumberger offer solutions for real-time data integration.
Advanced Training: Participate in advanced DrillScan training courses to fully understand its capabilities and latest features. Knowledge in advanced features like predictive modeling and stress analysis can significantly improve drilling operations. DrillScan’s training offers specialized courses for directional drillers.
Use Advanced Analytics: Leverage DrillScan’s advanced analytics and simulation tools to predict downhole conditions and optimize drilling parameters. This can lead to improved rates of penetration and reduced non-productive time.
Collaborate and Share Insights: Collaboration platforms like Drillers.com allow directional drillers to share insights, challenges, and solutions. Engaging with the community can provide new strategies and tips for maximizing DrillScan’s potential.
By regularly updating software, integrating real-time data, undergoing advanced training, utilizing analytics, and collaborating with peers, directional drillers can significantly improve their efficiency and effectiveness in using DrillScan.
How to Display DrillScan Skills on Your Resume
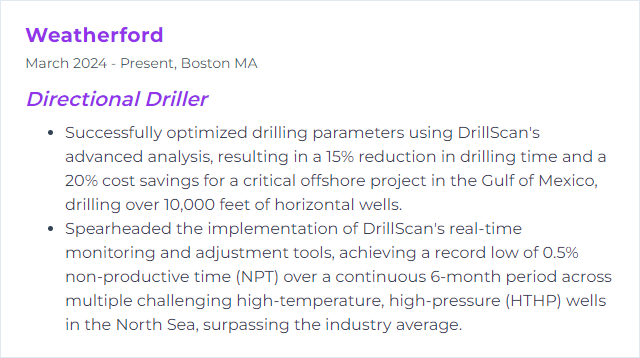
11. Pressure Control
Pressure control in the context of a Directional Driller involves managing the hydraulic pressures within the wellbore to ensure safe and effective drilling operations. This includes controlling the mud pressure to prevent blowouts and maintaining the integrity of the well.
Why It's Important
Pressure control is crucial for a Directional Driller to ensure safe and efficient drilling operations, maintain wellbore stability, prevent blowouts by managing the balance between mud weight and formation pressures, and optimize drilling performance by adjusting to varying geological conditions.
How to Improve Pressure Control Skills
Improving pressure control in directional drilling involves precision, real-time monitoring, and adjusting techniques to maintain optimal downhole pressure conditions. Here are concise steps to enhance pressure control:
Utilize Real-Time Monitoring Systems: Implement advanced real-time monitoring systems to track downhole conditions continuously. This allows for immediate adjustments in drilling parameters to maintain desired pressure levels.
Apply Managed Pressure Drilling (MPD) Techniques: Adopt Managed Pressure Drilling (MPD) methodologies. MPD provides more precise control over the annular pressure profile, enabling safer and more efficient drilling through challenging formations.
Enhance Mud System Management: Ensure the drilling fluid or mud system is optimized for the specific drilling conditions. Use mud system management tools and techniques to adjust the mud weight and properties, balancing the formation pressure effectively.
Implement Advanced Drilling Software: Leverage advanced drilling software that can predict and simulate downhole conditions. This software assists in planning and executing drilling operations with enhanced pressure control.
Continuous Training: Ensure the drilling team, especially the directional drillers, undergo continuous training on the latest pressure control techniques and technologies. This includes industry-standard training on pressure control and well control certifications.
Regular Equipment Maintenance: Perform regular maintenance and checks on all pressure control equipment, including Blowout Preventers (BOPs), to ensure they are functioning correctly. This equipment maintenance is crucial for preventing uncontrolled pressure releases.
By integrating these strategies, directional drillers can significantly improve pressure control, leading to safer and more efficient drilling operations.
How to Display Pressure Control Skills on Your Resume
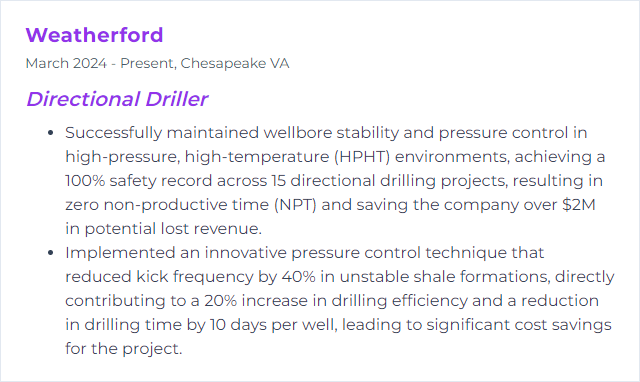
12. Hole Cleaning
Hole cleaning, in the context of directional drilling, refers to the process of removing cuttings, debris, and sediment from the borehole to prevent blockages and ensure efficient drilling operations. This is critical for maintaining the desired trajectory and minimizing drilling problems.
Why It's Important
Hole cleaning is crucial for a Directional Driller as it ensures efficient removal of cuttings from the wellbore, prevents stuck pipe incidents, maintains wellbore stability, and optimizes drilling performance by reducing torque and drag, contributing to a safer and more cost-effective drilling operation.
How to Improve Hole Cleaning Skills
Improving hole cleaning in directional drilling involves optimizing drilling parameters and equipment to ensure efficient removal of cuttings from the wellbore. Focus on:
Optimize Drilling Fluid Properties: Ensure the drilling mud has appropriate rheological properties (viscosity and gel strength) to suspend and transport cuttings. M-I SWACO offers detailed insights into fluid optimization.
Use Proper Hole Cleaning Tools: Employ tools like rotating control devices and agitators to enhance cuttings transport. National Oilwell Varco provides various equipment options.
Optimize Drill Pipe Rotation and Flow Rate: Adjust the drill pipe rotation speed and mud flow rate to improve cuttings suspension and transport. Schlumberger discusses techniques and equipment for optimizing these parameters.
Monitor Cuttings and Mud Properties: Regularly analyze cuttings and mud properties to adjust drilling parameters as needed. The use of real-time monitoring systems can be crucial (Halliburton).
Implement Proper Wellbore Geometry: Design the wellbore trajectory to minimize areas where cuttings can accumulate, using software and planning tools from companies like Baker Hughes.
Improving hole cleaning is a dynamic process requiring continuous monitoring and adjustment of drilling parameters and practices.
How to Display Hole Cleaning Skills on Your Resume
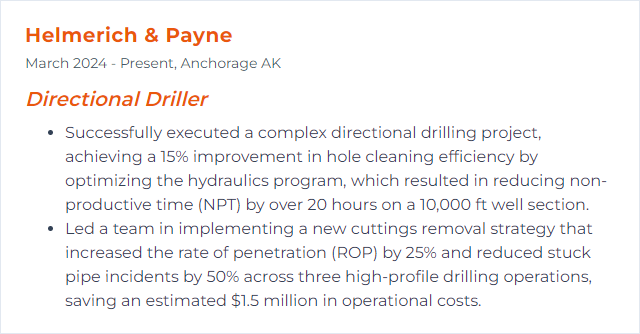