Top 12 Distribution Supervisor Skills to Put on Your Resume
A compelling resume for a Distribution Supervisor position should showcase a blend of technical knowledge and leadership acumen, highlighting the unique skills that make you an invaluable asset to any logistics operation. Tailoring your resume to reflect these top skills can significantly elevate your candidacy, setting you apart in a competitive job market.
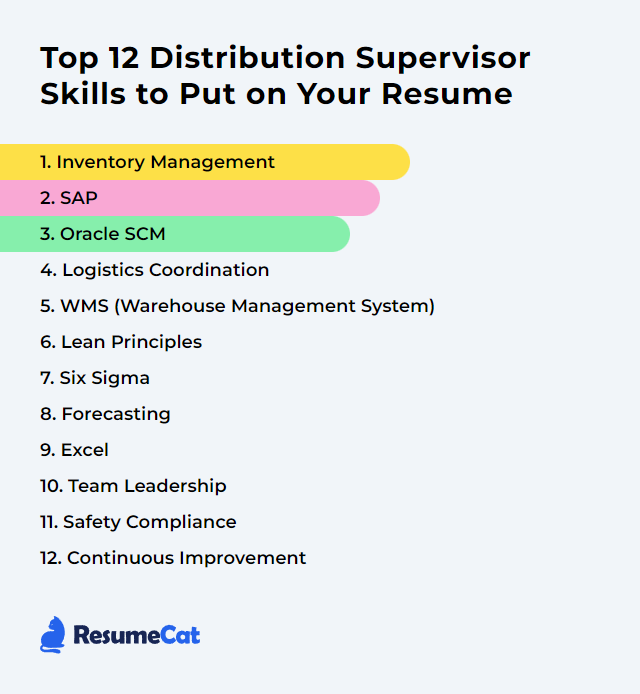
Distribution Supervisor Skills
- Inventory Management
- SAP
- Oracle SCM
- Logistics Coordination
- WMS (Warehouse Management System)
- Lean Principles
- Six Sigma
- Forecasting
- Excel
- Team Leadership
- Safety Compliance
- Continuous Improvement
1. Inventory Management
Inventory management involves overseeing and controlling the ordering, storage, and distribution of a company's stock to ensure availability while minimizing costs and maximizing efficiency. For a Distribution Supervisor, it means coordinating these processes to ensure timely and accurate delivery of goods.
Why It's Important
Inventory management is crucial for a Distribution Supervisor as it ensures the right quantity of products is available for distribution at the right time, optimizing storage costs, reducing waste, and enhancing customer satisfaction through timely deliveries.
How to Improve Inventory Management Skills
Improving inventory management, especially for a Distribution Supervisor, involves a combination of strategy, technology, and efficient processes. Here are key steps in a very short and concise format:
Implement an Inventory Management System: Use software that provides real-time tracking of stock levels, orders, sales, and deliveries. Shopify's Guide to Inventory Management Systems offers a comprehensive look at options.
Adopt Lean Inventory Practices: Keep stock at optimal levels to meet demand without overstocking. The 5S System (Sort, Set in order, Shine, Standardize, Sustain) can help organize inventory efficiently.
Improve Forecasting: Use historical data, market trends, and sales forecasts to predict inventory needs more accurately. Harvard Business Review’s article on improving forecasting provides insights into strategic alignment and forecasting.
Enhance Supplier Relationships: Work closely with suppliers to ensure timely deliveries and understand supply chain constraints. The Institute for Supply Management offers resources on supplier relationship management.
Regular Audits and Cycle Counts: Conduct regular checks to ensure inventory accuracy. QuickBooks’ guide on cycle counting explains how this process can be more efficient than traditional physical inventory counts.
Train Your Team: Ensure your team understands the importance of inventory accuracy and how to manage it effectively. APICS provides training and certifications in supply chain management.
Utilize Demand Planning Tools: Tools that analyze sales trends to better predict future inventory needs can optimize stock levels. Gartner’s research on supply chain planning highlights the importance of integrating demand planning tools.
Implementing these strategies can significantly improve inventory management in a distribution setting, enhancing efficiency, reducing costs, and improving customer satisfaction.
How to Display Inventory Management Skills on Your Resume
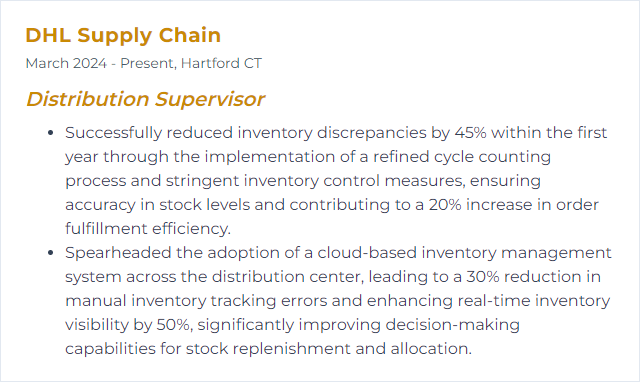
2. SAP
SAP is an enterprise resource planning (ERP) software that integrates key business functions, including distribution, inventory, and supply chain management, helping Distribution Supervisors streamline operations, improve efficiency, and ensure timely delivery of goods.
Why It's Important
SAP is crucial for a Distribution Supervisor as it integrates core business processes, enabling efficient inventory management, streamlined order processing, and accurate demand forecasting, thus ensuring timely and cost-effective distribution operations.
How to Improve SAP Skills
Improving SAP (Systems, Applications, and Products in Data Processing) for a Distribution Supervisor involves optimizing system configuration, enhancing user skills, and integrating advanced technologies. Here’s a concise guide:
System Configuration: Customize SAP to align with distribution processes, ensuring efficient inventory management and logistics. Refer to SAP's official Configuration Guide.
Training: Enhance user competency through SAP training modules specific to distribution tasks. SAP offers various training courses.
Automation: Implement SAP’s Advanced Planning and Optimization (APO) and Extended Warehouse Management (EWM) to automate supply chain processes. Check SAP EWM.
Integration: Use SAP Integration Suite to connect SAP with other business applications for seamless data flow. Learn more at SAP Integration Suite.
Analytics: Utilize SAP Business Warehouse and SAP Analytics Cloud for real-time reporting and analytics for informed decision-making. Explore SAP Analytics Cloud.
Feedback Loop: Establish a feedback mechanism with end-users to continuously identify areas for improvement and update the SAP system accordingly.
SAP Fiori: Adopt SAP Fiori for a more intuitive user experience, enhancing productivity. Visit SAP Fiori.
For further reading, consider SAP's official documentation and community forums for tips and best practices tailored to distribution supervisors.
How to Display SAP Skills on Your Resume
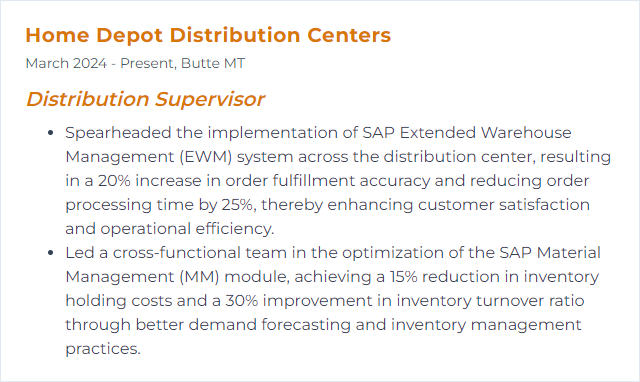
3. Oracle SCM
Oracle SCM (Supply Chain Management) is a comprehensive suite of applications designed to automate and streamline an organization's supply chain processes, from procurement to manufacturing, and distribution. For a Distribution Supervisor, it offers tools to efficiently manage warehouse operations, inventory levels, and distribution strategies, ensuring timely delivery of goods while minimizing costs.
Why It's Important
Oracle SCM (Supply Chain Management) is crucial for a Distribution Supervisor because it streamlines and optimizes the distribution process, ensuring efficient inventory management, timely delivery, and cost reduction, thereby enhancing overall operational efficiency and customer satisfaction.
How to Improve Oracle SCM Skills
To improve Oracle SCM (Supply Chain Management) as a Distribution Supervisor, focus on these key areas:
Educate and Train Your Team: Ensure that your team is well-versed in Oracle SCM functionalities. Oracle offers various training options which can streamline operations.
Leverage Automation and Analytics: Utilize Oracle SCM’s automation and analytics features to optimize inventory management and demand forecasting.
Implement Best Practices for Inventory Management: Adopt best practices for inventory management within Oracle SCM to reduce costs and improve efficiency. Oracle provides guidance on inventory management.
Enhance Collaboration with Suppliers: Utilize Oracle SCM's collaboration tools to improve communication and efficiency with suppliers. The suite offers supplier collaboration for better integration.
Stay Updated with Oracle SCM Updates: Regularly update your system and stay informed about new features or enhancements in Oracle SCM. Oracle’s Cloud Readiness documentation is a valuable resource.
Customize Oracle SCM to Fit Your Needs: Tailor Oracle SCM to better meet your specific distribution needs. Explore Oracle’s configuration options for more information.
Seek Feedback and Continuously Improve: Regularly solicit feedback from your team on the Oracle SCM system and look for continuous improvement opportunities.
By focusing on these areas, you can significantly improve Oracle SCM efficiency and effectiveness in your role as a Distribution Supervisor.
How to Display Oracle SCM Skills on Your Resume
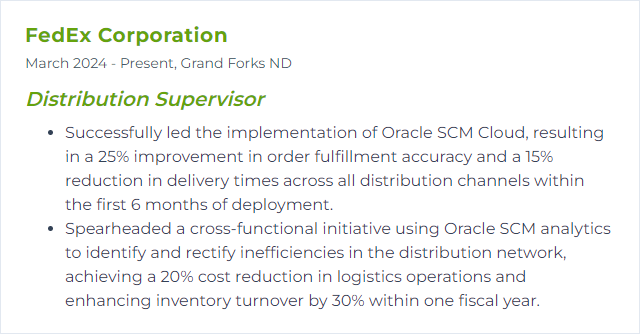
4. Logistics Coordination
Logistics Coordination, in the context of a Distribution Supervisor, involves overseeing and managing the movement, storage, and delivery of goods. This includes planning, implementing, and monitoring the efficient, cost-effective flow of products from origin to destination to ensure timely delivery and inventory accuracy.
Why It's Important
Logistics coordination is crucial for a Distribution Supervisor as it ensures the efficient and timely movement of goods, optimizes resource use, reduces costs, and enhances customer satisfaction by delivering products accurately and promptly.
How to Improve Logistics Coordination Skills
Improving logistics coordination, particularly for a Distribution Supervisor, involves enhancing communication, implementing technology, and optimizing processes. Here are concise strategies:
Enhance Communication: Establish clear communication channels between all stakeholders, including suppliers, transporters, and customers. Tools like Slack or Microsoft Teams can facilitate real-time updates and collaboration.
Implement Technology: Adopt logistics management software (Logi-Sys) or transportation management systems (TMS) to streamline operations, from tracking shipments to inventory management.
Optimize Routing and Scheduling: Use route optimization software (Route4Me) to ensure efficient delivery schedules, reducing fuel costs and improving delivery times.
Continuous Training: Regularly train staff on new technologies and best practices in logistics coordination. Platforms like LinkedIn Learning offer courses tailored to logistics and supply chain management.
Data Analysis and Feedback: Utilize data analytics tools (Tableau) to assess performance metrics and identify areas for improvement. Implement a feedback loop with customers and suppliers to adjust strategies accordingly.
By focusing on these areas, a Distribution Supervisor can significantly improve logistics coordination, leading to more efficient operations, cost savings, and enhanced customer satisfaction.
How to Display Logistics Coordination Skills on Your Resume
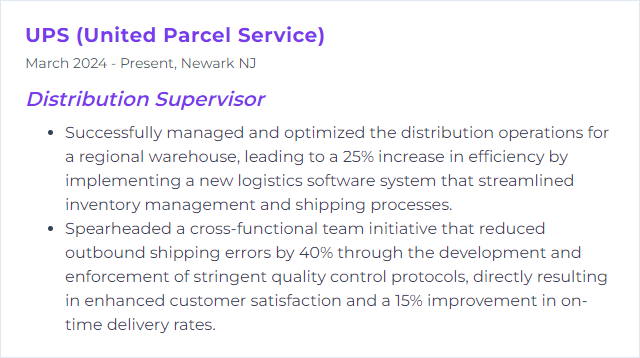
5. WMS (Warehouse Management System)
A Warehouse Management System (WMS) is a software solution that optimizes and controls warehouse operations, from inventory management to order fulfillment, specifically designed to support the efficiency and productivity of distribution supervisors and their teams.
Why It's Important
A Warehouse Management System (WMS) is crucial for a Distribution Supervisor as it streamlines operations by optimizing inventory management, enhancing order fulfillment accuracy, and improving labor allocation, thereby boosting overall efficiency and reducing operational costs.
How to Improve WMS (Warehouse Management System) Skills
Improving a Warehouse Management System (WMS) involves several key strategies focused on enhancing efficiency, accuracy, and productivity in warehouse operations. Here are concise recommendations for a Distribution Supervisor:
Implement Real-Time Data Tracking: Enhance your WMS with real-time tracking of inventory and orders. This improves decision-making and operational efficiency. Consider RFID or IoT-based systems for real-time updates. Zebra Technologies offers solutions in this area.
Integrate with Other Systems: Ensure your WMS is integrated with other business systems (ERP, CRM, etc.) for seamless data flow and improved accuracy. SAP Extended Warehouse Management is known for its integration capabilities.
Optimize Warehouse Layout: Use your WMS data to optimize the warehouse layout, ensuring efficient use of space and minimizing travel time for picking operations. Lucas Systems provides tools and strategies for warehouse optimization.
Adopt Automation and Robotics: Integrate automation tools and robotics to reduce manual tasks, speeding up operations and reducing errors. Companies like Fetch Robotics offer warehouse automation solutions.
Continuous Training and Feedback: Offer ongoing training for staff on WMS functionalities and encourage feedback for continuous improvement. Platforms like Udemy have courses on WMS best practices.
Regular System Updates and Maintenance: Keep your WMS software up to date with the latest features and security patches. Regular maintenance ensures optimal performance and minimizes downtime.
Implement Advanced Picking Strategies: Use your WMS to implement advanced picking strategies like wave, batch, or zone picking to increase efficiency. Manhattan Associates offers solutions that support various picking methodologies.
Analyze and Act on Data: Regularly review WMS-generated data and analytics to identify trends, bottlenecks, and opportunities for improvement. Tools like Tableau can help visualize and analyze WMS data.
By focusing on these strategies, a Distribution Supervisor can significantly improve the functionality and efficiency of their Warehouse Management System, leading to a more productive and error-free operation.
How to Display WMS (Warehouse Management System) Skills on Your Resume
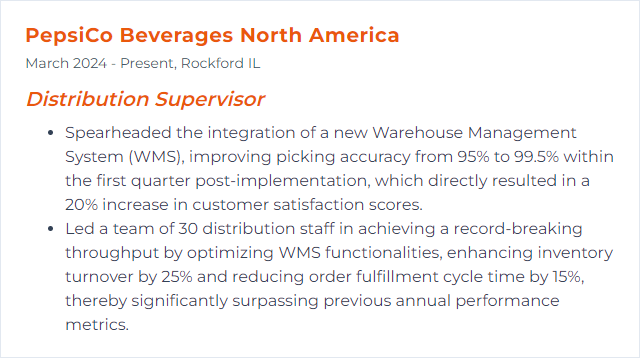
6. Lean Principles
Lean principles focus on maximizing value for the customer while minimizing waste. For a Distribution Supervisor, this means streamlining operations to ensure efficient product flow, reducing excess inventory, minimizing errors, and enhancing overall service quality with the goal of delivering products faster, more reliably, and at a lower cost.
Why It's Important
Lean Principles are important for a Distribution Supervisor because they streamline operations by eliminating waste, improving efficiency, and enhancing customer satisfaction, leading to reduced costs and increased profitability.
How to Improve Lean Principles Skills
To improve Lean Principles as a Distribution Supervisor, follow these concise strategies:
Identify Value: Understand your customers' needs to ensure that your distribution processes align with their value expectations. Lean Enterprise Institute offers insights on identifying value from the customer's perspective.
Map the Value Stream: Identify and map all the steps in your distribution process, eliminating any step that does not add value. The Lean Manufacturing Tools website provides a guide to value stream mapping.
Create Flow: Ensure that your distribution operations are streamlined to allow for a smooth flow of products. The American Society for Quality (ASQ) provides resources on creating flow within lean operations.
Establish Pull: Implement pull systems to replace traditional push strategies in inventory management, ensuring products are replenished based on customer demand. Learn more at Planet Lean.
Pursue Perfection: Continuously seek ways to improve and optimize distribution processes. The Gemba Academy offers resources on continuous improvement.
By focusing on these strategies, you can enhance efficiency, reduce waste, and improve customer satisfaction in your distribution operations.
How to Display Lean Principles Skills on Your Resume
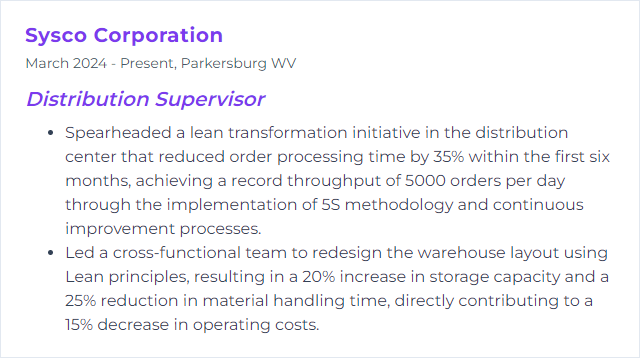
7. Six Sigma
Six Sigma is a data-driven methodology aimed at reducing defects and improving processes, quality, and efficiency in operations, including distribution, by identifying and eliminating variability and inefficiencies.
Why It's Important
Six Sigma is important for a Distribution Supervisor because it provides a structured, data-driven approach to reducing errors, improving process efficiency, and enhancing product quality, leading to increased customer satisfaction and lower operational costs.
How to Improve Six Sigma Skills
Improving Six Sigma, particularly from the standpoint of a Distribution Supervisor, involves focusing on streamlining processes, reducing waste, and enhancing quality control. Here are concise steps with relevant external resources:
Understand the Basics: Gain a solid understanding of Six Sigma principles. ASQ’s Six Sigma Resources is a great starting point.
Define Objectives: Clearly define your improvement objectives in the context of distribution. Focus on areas like reducing shipping errors, improving package handling, or speeding up delivery times.
Measure Performance: Use metrics relevant to distribution such as order accuracy, delivery time, and damage rates. Tools like Lean Six Sigma Measurement System Analysis can help.
Analyze Data: Employ Six Sigma’s DMAIC (Define, Measure, Analyze, Improve, Control) framework to analyze performance data. Utilize statistical analysis tools. iSixSigma offers resources on various Six Sigma tools and methods.
Implement Improvements: Based on analysis, implement process improvements. This may involve reorganizing workflows, adopting new technologies, or enhancing employee training programs.
Control and Monitor: Establish control measures to maintain improvements. Regularly monitor performance against established KPIs to ensure sustained improvement.
Engage Your Team: Six Sigma is a team effort. Engage your distribution team in the process through training and involvement in improvement projects. Six Sigma Online Certification & Training can be a resource for team training.
Leverage Technology: Use technology solutions like Warehouse Management Systems (WMS) to automate and optimize distribution processes. Research available options that align with your Six Sigma goals.
By following these steps and utilizing the provided resources, a Distribution Supervisor can effectively improve their operations through Six Sigma methodologies.
How to Display Six Sigma Skills on Your Resume
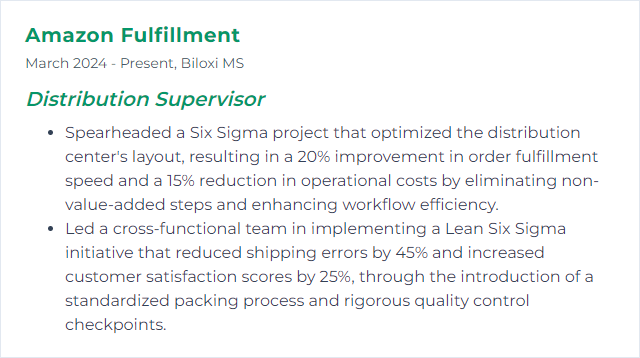
8. Forecasting
Forecasting, for a Distribution Supervisor, involves predicting future inventory needs and product demand to ensure efficient distribution operations, minimize costs, and meet customer expectations.
Why It's Important
Forecasting is crucial for a Distribution Supervisor as it aids in anticipating demand, ensuring optimal inventory levels, and scheduling efficient delivery routes, leading to improved customer satisfaction and cost reduction.
How to Improve Forecasting Skills
Improving forecasting, especially from the perspective of a Distribution Supervisor, involves a combination of data analysis, technology utilization, and collaboration. Here are concise steps:
Leverage Historical Data: Analyze past sales and distribution data to identify patterns and trends. Tools like Excel or more advanced software (IBM Planning Analytics) can facilitate this analysis.
Implement Forecasting Software: Utilize specialized forecasting software (Demand Planning Software) that uses algorithms and artificial intelligence to predict future demand more accurately.
Collaborate Across Departments: Work closely with sales, marketing, and production teams to gather insights that impact demand forecasts. Collaboration platforms (Microsoft Teams) can improve communication and information sharing.
Monitor External Factors: Stay informed about market trends, economic indicators, and other external factors that could influence demand. Use resources like MarketWatch for up-to-date information.
Adjust and Optimize Regularly: Regularly review and adjust forecasts based on actual sales outcomes and changing circumstances. Forecasting is an iterative process that benefits from continuous refinement.
Educate Your Team: Ensure your team understands the principles of effective forecasting and how to use the tools at their disposal. Online courses from platforms like Coursera or Udemy can be valuable.
By following these steps and leveraging the right tools and strategies, a Distribution Supervisor can significantly improve forecasting accuracy and efficiency.
How to Display Forecasting Skills on Your Resume
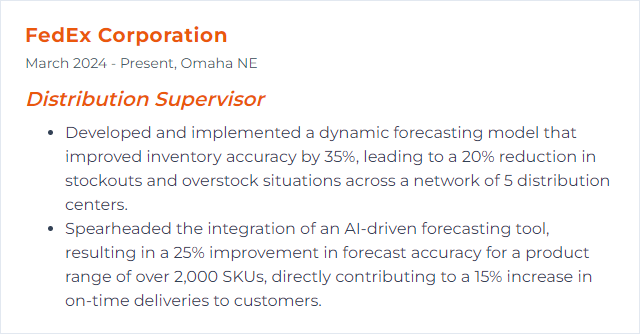
9. Excel
Excel is a spreadsheet program used for data analysis, reporting, and inventory management, essential for a Distribution Supervisor to efficiently monitor distribution processes, track shipments, and manage stock levels.
Why It's Important
Excel is crucial for a Distribution Supervisor because it enables efficient data management, facilitates inventory tracking, scheduling, and forecasting, and aids in analyzing performance metrics to optimize distribution processes.
How to Improve Excel Skills
To improve Excel skills as a Distribution Supervisor, focus on mastering specific functionalities that streamline logistics, inventory management, and scheduling tasks. Here's a concise guide:
Learn Advanced Formulas: Enhance your ability to analyze logistical data. Focus on functions like
VLOOKUP
,INDEX
,MATCH
, andSUMIFS
.Master PivotTables: Aggregate, analyze, and present large sets of data efficiently.
Utilize Conditional Formatting: Highlight key data points, such as inventory levels or delivery times, to easily identify outliers or trends.
- Conditional Formatting
Implement Macros: Automate repetitive tasks, saving time on routine reports and analysis.
- Getting Started with Macros
Explore Data Visualization Tools: Use charts and graphs to make data-driven decisions and presentations more impactful.
- Charts and Graphs
Leverage Excel Add-ins and Tools: Explore tools like Power Query for data importation and transformation, and Power Pivot for advanced data modeling.
- Power Query
- Power Pivot
By focusing on these areas, a Distribution Supervisor can significantly enhance their efficiency and analytical capabilities in Excel.
How to Display Excel Skills on Your Resume
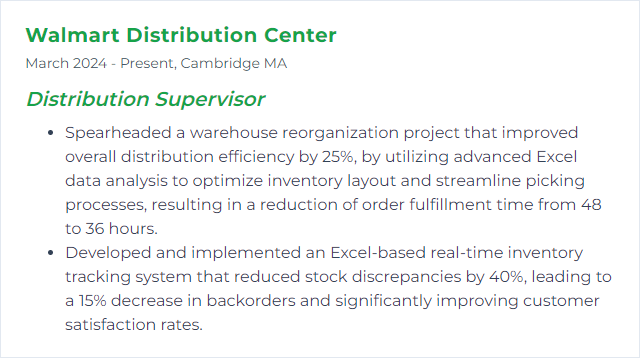
10. Team Leadership
Team leadership, in the context of a Distribution Supervisor, involves guiding and coordinating a group of employees to efficiently manage the flow of goods, ensuring accurate and timely distribution while fostering a positive and productive work environment.
Why It's Important
Team leadership is crucial for a Distribution Supervisor as it ensures efficient coordination and management of logistics, enhances productivity through motivated and guided team efforts, and fosters a positive and proactive work environment, leading to timely and accurate distribution operations.
How to Improve Team Leadership Skills
Improving team leadership, especially for a Distribution Supervisor, involves enhancing communication, fostering teamwork, and developing strategic planning skills. Here are concise strategies:
Enhance Communication Skills: Improve how you convey expectations and feedback. MindTools offers resources on effective communication techniques.
Foster Teamwork: Encourage collaboration among team members. The Table Group provides insights on building cohesive teams.
Develop Strategic Planning Skills: Learn to anticipate challenges and devise effective solutions. Harvard Business Review has articles and case studies on strategic planning.
Lead by Example: Demonstrate the work ethic, attitude, and behavior you expect from your team. Forbes discusses the importance of authenticity in leadership.
Continuous Learning: Stay updated with the latest industry trends and leadership strategies. Coursera offers courses on leadership and management.
Employee Development: Invest in training and development opportunities for your team. LinkedIn Learning provides a wide range of courses that can enhance your team's skills.
By focusing on these areas, a Distribution Supervisor can significantly improve their team leadership skills, leading to a more productive and motivated team.
How to Display Team Leadership Skills on Your Resume
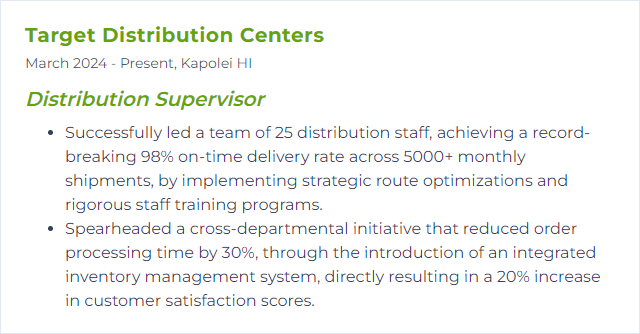
11. Safety Compliance
Safety compliance, in the context of a Distribution Supervisor, refers to adhering to established safety regulations and standards to ensure a secure working environment within distribution and warehousing operations. This includes implementing and monitoring safety policies, training employees on safety practices, and ensuring all equipment and processes meet legal and industry safety requirements.
Why It's Important
Safety compliance is crucial for a Distribution Supervisor because it ensures the well-being of employees, minimizes risks of accidents and injuries, adheres to legal regulations, and maintains productivity and efficiency in the distribution process.
How to Improve Safety Compliance Skills
Improving safety compliance as a Distribution Supervisor involves a proactive approach focusing on consistent training, clear communication, and regular assessments. Here's how to do it:
Training: Ensure all employees undergo regular safety training specific to their roles. This should include updates on new regulations and refresher courses.
Communication: Maintain open lines of communication through meetings and safety bulletins, enabling employees to report hazards without fear of retaliation.
Assessment and Feedback: Conduct regular safety audits to identify and rectify potential hazards. Incorporate employee feedback into safety strategies to ensure their effectiveness.
Policies and Procedures: Develop and enforce clear safety policies and procedures, making sure they are accessible to all employees.
Safety Equipment: Provide the necessary personal protective equipment (PPE) and ensure its proper use and maintenance.
Emergency Preparedness: Regularly update and practice emergency response plans to ensure everyone knows their role during an incident.
Recognition and Rewards: Implement a recognition system for employees who consistently adhere to safety protocols, encouraging a culture of safety.
By focusing on these key areas, a Distribution Supervisor can significantly improve safety compliance within their operations, leading to a safer work environment for everyone involved.
How to Display Safety Compliance Skills on Your Resume
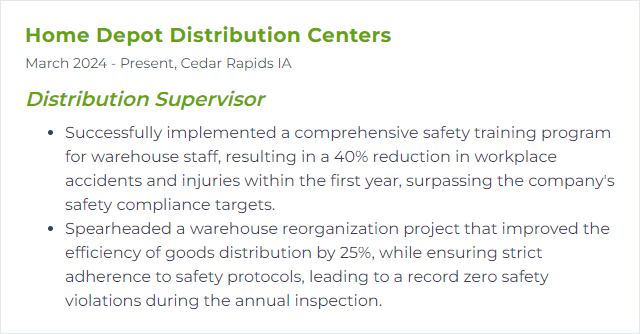
12. Continuous Improvement
Continuous Improvement is a systematic, ongoing effort to enhance processes, systems, or services, aiming at increasing efficiency, reducing waste, and improving quality, directly impacting productivity and performance in distribution operations.
Why It's Important
Continuous Improvement is crucial for a Distribution Supervisor because it streamlines operations, boosts efficiency, reduces costs, and enhances customer satisfaction, ensuring the distribution process remains competitive and adaptable to changing market demands.
How to Improve Continuous Improvement Skills
To improve Continuous Improvement for a Distribution Supervisor, focus on these key strategies:
Identify Areas for Improvement: Regularly analyze operational data and processes to identify inefficiencies. Tools like a Pareto Chart can help prioritize the most significant areas for improvement.
Engage Your Team: Foster a culture of continuous improvement by involving your team in problem-solving. Techniques such as Kaizen encourage employee participation in identifying and implementing improvements.
Implement Lean Principles: Adopt Lean Management principles to eliminate waste and optimize processes, enhancing productivity and reducing costs.
Use Technology: Leverage technology like Warehouse Management Systems (WMS) and data analytics tools to streamline operations and gain insights for improvements. Explore platforms like Fishbowl Inventory for inventory management solutions.
Continuous Learning: Invest in training and development. Encourage your team to stay updated with the latest distribution and logistics practices through platforms like LinkedIn Learning.
Monitor and Adjust: Implement a robust system for tracking the impact of changes. Use Key Performance Indicators (KPIs) to measure success and be prepared to adjust strategies as necessary.
By focusing on these strategies, a Distribution Supervisor can drive significant improvements in their operations, fostering a culture of continuous enhancement and efficiency.
How to Display Continuous Improvement Skills on Your Resume
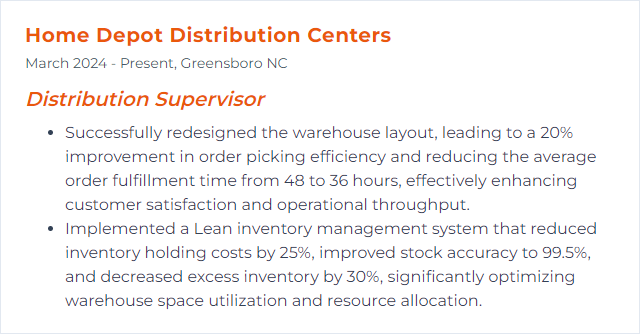