Top 12 Distribution Center Supervisor Skills to Put on Your Resume
In the fast-paced world of logistics and supply chain management, having a resume that stands out is crucial for distribution center supervisors. Highlighting a top-tier list of skills on your resume not only showcases your ability to efficiently manage operations and lead teams but also positions you as a prime candidate in a competitive job market.
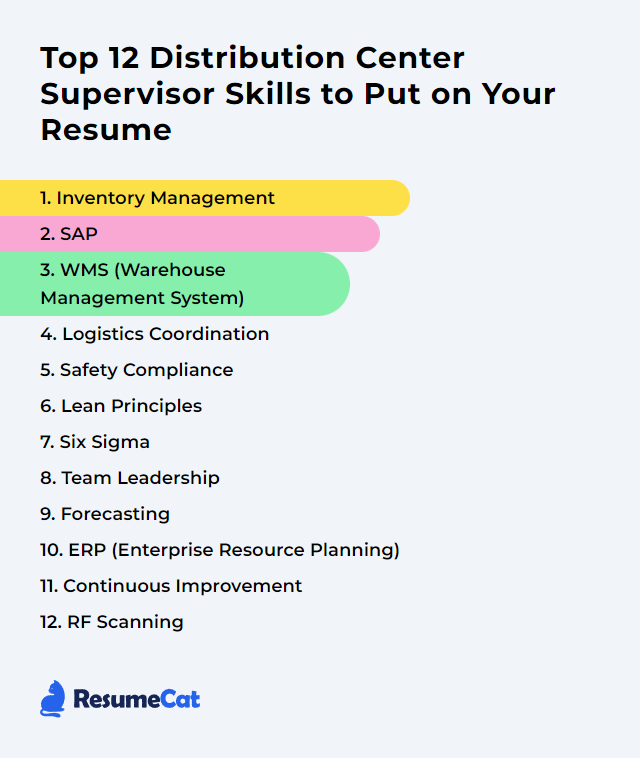
Distribution Center Supervisor Skills
- Inventory Management
- SAP
- WMS (Warehouse Management System)
- Logistics Coordination
- Safety Compliance
- Lean Principles
- Six Sigma
- Team Leadership
- Forecasting
- ERP (Enterprise Resource Planning)
- Continuous Improvement
- RF Scanning
1. Inventory Management
Inventory management involves overseeing and controlling the ordering, storage, and distribution of goods within a distribution center to ensure the right quantities are available to meet customer demand, minimize costs, and optimize storage space and logistics.
Why It's Important
Inventory management is crucial for a Distribution Center Supervisor as it ensures the optimal balance of stock levels to meet customer demand without overstocking, minimizing costs and maximizing efficiency in order fulfillment.
How to Improve Inventory Management Skills
Improving inventory management, especially for a Distribution Center Supervisor, involves implementing strategic practices to optimize efficiency, reduce costs, and ensure product availability. Here are concise tips:
Adopt Lean Inventory Practices: Reduce waste by keeping stock levels closely aligned with demand. Learn More.
Implement an Inventory Management System: Use technology to track inventory in real-time, improving accuracy and decision-making. Explore Options.
Regular Audits: Conduct regular physical counts and compare them against inventory records to identify discrepancies early. Audit Guide.
Supplier Collaboration: Work closely with suppliers to improve order accuracy, lead times, and to create a responsive supply chain. Collaboration Tips.
Forecasting: Use historical data and market trends to forecast demand more accurately, minimizing overstock and stockouts. Forecasting Basics.
Continuous Improvement: Regularly review inventory processes and KPIs to identify areas for improvement. Improvement Strategies.
Employee Training: Ensure all staff are trained in inventory management best practices and system use. Training Importance.
By focusing on these areas, a Distribution Center Supervisor can significantly improve inventory management, leading to increased efficiency, reduced costs, and better customer satisfaction.
How to Display Inventory Management Skills on Your Resume
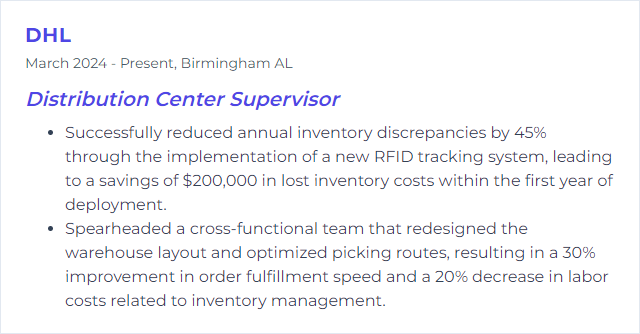
2. SAP
SAP is an enterprise resource planning (ERP) software that integrates various business processes, including inventory management, order processing, and logistics, to streamline operations in a distribution center, aiding supervisors in efficient resource planning and decision-making.
Why It's Important
SAP is crucial for a Distribution Center Supervisor because it streamlines inventory management, optimizes supply chain processes, and enhances decision-making through real-time data insights, ensuring efficient operations and customer satisfaction.
How to Improve SAP Skills
Improving SAP for a Distribution Center Supervisor involves optimizing system processes, enhancing user knowledge, and leveraging advanced SAP functionalities. Here are brief, actionable steps:
Automate Processes: Automate repetitive tasks like order processing and inventory management using SAP's Integrated Business Planning.
Enhance Data Accuracy: Implement SAP Extended Warehouse Management for real-time inventory tracking and improved data accuracy.
Customize Reports: Utilize SAP Business Intelligence to generate custom reports tailored to specific distribution center needs.
Train Staff: Regularly conduct training sessions for all SAP users to improve efficiency. SAP offers training and certification courses that could be very beneficial.
Monitor KPIs: Use SAP's analytics tools to monitor Key Performance Indicators (KPIs) and identify areas for improvement.
Implement Best Practices: Adopt SAP’s best practices for warehouse management to enhance overall operational efficiency.
Feedback Loop: Create a feedback loop with your team to collect insights and issues encountered with SAP, allowing for continuous system improvement.
By focusing on these areas, Distribution Center Supervisors can significantly improve SAP's effectiveness and efficiency in their operations.
How to Display SAP Skills on Your Resume
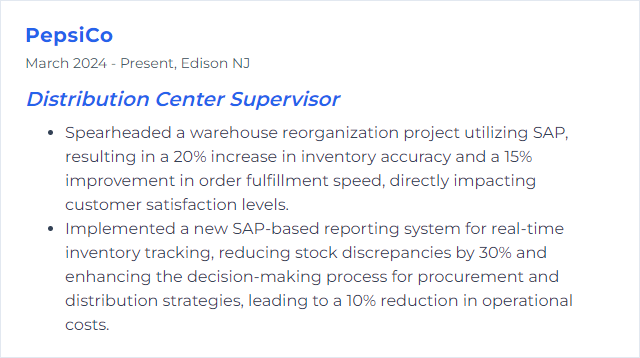
3. WMS (Warehouse Management System)
A Warehouse Management System (WMS) is a software solution designed to optimize and manage the operations within a warehouse or distribution center, ensuring efficient inventory control, storage, picking, packing, and shipping processes.
Why It's Important
A Warehouse Management System (WMS) is crucial for a Distribution Center Supervisor because it optimizes warehouse operations by automating inventory management, enhancing order accuracy, improving space utilization, and increasing efficiency in picking and shipping processes. This results in reduced operational costs and improved customer satisfaction.
How to Improve WMS (Warehouse Management System) Skills
Improving a Warehouse Management System (WMS) involves several steps focused on optimizing efficiency, accuracy, and productivity in a distribution center. As a Distribution Center Supervisor, here are concise strategies:
Data Analysis and Continuous Improvement: Regularly review system data to identify bottlenecks and inefficiencies. Utilize WMS analytics for actionable insights.
Integration with Other Systems: Ensure your WMS is fully integrated with other business systems (ERP, CRM, etc.) for seamless data flow. Learn more about the benefits of system integration.
Training and User Support: Continuously train staff on the WMS functionalities. Implement a structured training program to enhance user competence.
Adopt Automation: Incorporate automation tools and robotics where feasible to reduce manual errors and improve efficiency. Explore WMS and automation integration.
Customization and Scalability: Customize the WMS to fit specific operational needs and ensure it can scale with business growth. Guide to WMS customization.
Regular System Updates and Maintenance: Keep the WMS up-to-date with the latest software versions and security patches. Understand the importance of WMS updates.
Feedback Loop: Establish a feedback loop with users to continuously gather insights and improve the system. Implementing a feedback mechanism can enhance system usability and effectiveness.
By focusing on these areas, you can significantly improve the performance and efficiency of your Warehouse Management System.
How to Display WMS (Warehouse Management System) Skills on Your Resume
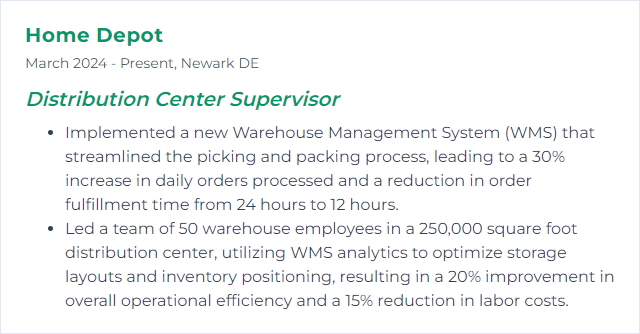
4. Logistics Coordination
Logistics coordination involves managing and overseeing the movement, distribution, and storage of goods in and out of a distribution center to ensure efficient and timely delivery, optimal inventory levels, and resource allocation. It includes planning, implementing, and controlling procedures for effective transportation and storage of goods while coordinating with various stakeholders to meet customer demands and organizational goals.
Why It's Important
Logistics coordination is crucial for a Distribution Center Supervisor because it ensures the efficient and timely movement of goods, optimizes inventory management, minimizes costs, and enhances customer satisfaction by delivering the right products at the right time.
How to Improve Logistics Coordination Skills
Improving logistics coordination, especially for a Distribution Center Supervisor, involves enhancing efficiency, communication, and adaptability in operations. Here are key strategies:
Implement a Robust Warehouse Management System (WMS): Streamline inventory tracking, order processing, and shipping. SelectHub offers insights into top WMS solutions.
Optimize Inventory Management: Adopt Just-In-Time (JIT) inventory practices to reduce storage costs and improve order fulfillment speed.
Enhance Communication: Use tools like Slack for real-time communication between teams and Trello for task management, ensuring everyone is on the same page.
Leverage Data Analytics: Use data analytics tools to forecast demand, optimize routes, and reduce transportation costs. Tableau is a powerful analytics platform.
Focus on Continuous Improvement: Adopt the Kaizen methodology for continuous operational improvements, encouraging feedback and suggestions from all team members.
Build Strong Relationships with Suppliers and Carriers: This can lead to better rates and reliability. Regularly review and negotiate contracts to ensure competitive service levels.
Train Your Team: Ensure your team is well-trained on the latest logistics software and best practices. LinkedIn Learning offers courses in logistics and supply chain management.
Adopt Lean Logistics Principles: Minimize waste in your operations. LeanCor provides insights and services for implementing lean principles in logistics.
By focusing on these areas, a Distribution Center Supervisor can significantly improve logistics coordination, leading to more efficient operations, reduced costs, and higher customer satisfaction.
How to Display Logistics Coordination Skills on Your Resume
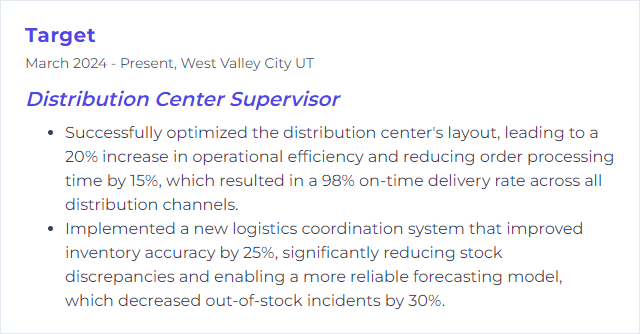
5. Safety Compliance
Safety compliance in the context of a Distribution Center Supervisor involves ensuring that all operations and activities within the distribution center adhere to relevant safety regulations and standards, aiming to protect employees, property, and the environment from accidents and hazards.
Why It's Important
Safety compliance is crucial for a Distribution Center Supervisor because it ensures the well-being of employees, minimizes the risk of accidents and injuries, and protects the company from legal issues and financial losses.
How to Improve Safety Compliance Skills
Improving safety compliance in a distribution center environment involves a multifaceted approach focusing on training, communication, monitoring, and continuous improvement. Here's a concise guide for a Distribution Center Supervisor:
Conduct Regular Training: Ensure all employees undergo regular safety training programs that are relevant to their roles. This includes both onboarding training for new hires and refresher courses for existing staff.
Implement a Safety Communication Strategy: Develop and maintain clear communication channels for discussing safety issues. Use toolbox talks and safety boards to share information and updates.
Perform Regular Safety Audits: Conduct safety audits regularly to identify and rectify potential hazards in the distribution center. This should involve a thorough inspection of equipment, workspaces, and practices.
Encourage Reporting of Safety Concerns: Create an environment where employees feel comfortable reporting safety concerns without fear of retaliation. Implement an anonymous reporting system if necessary.
Act on Feedback and Incidents: Quickly act on the feedback received from safety audits and incident reports. Implement corrective measures and follow up to ensure they are effective.
Stay Updated with Regulations: Keep abreast of latest safety regulations and ensure your distribution center complies with them. This might involve regular training or updates to procedures and equipment.
Utilize Safety Management Tools: Consider using safety management software or systems to streamline reporting, tracking, and addressing safety issues.
Remember, fostering a culture of safety requires commitment at all levels of the organization, continuous education, and the willingness to invest in safety improvements.
How to Display Safety Compliance Skills on Your Resume
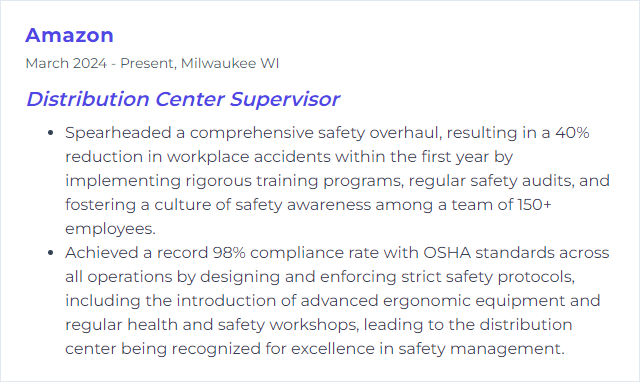
6. Lean Principles
Lean Principles focus on maximizing value for customers while minimizing waste. For a Distribution Center Supervisor, this means streamlining processes to ensure efficient flow of goods, reducing unnecessary inventory, and improving overall operational efficiency to deliver products faster and at a lower cost.
Why It's Important
Lean Principles are important for a Distribution Center Supervisor because they streamline operations, reduce waste, enhance productivity, and improve overall efficiency, leading to faster, more reliable service and lower operational costs.
How to Improve Lean Principles Skills
To improve Lean Principles in the context of a Distribution Center Supervisor, focus on:
Identify Value: Understand customer needs to ensure that your distribution center provides value efficiently. Lean Enterprise Institute offers insights on identifying value from the customer's perspective.
Map the Value Stream: Document and analyze processes to identify non-value-added steps. Tools like Value Stream Mapping from Lean.org can help visualize and streamline processes.
Create Flow: Reorganize work to ensure smooth process flow, minimizing delays and bottlenecks. This Lean Flow Guide provides practical steps.
Establish Pull: Implement pull systems to reduce inventory and improve responsiveness. The Kanban System is an effective tool for visual management and pull system implementation.
Pursue Perfection: Continuously seek to improve all processes, involving team members in problem-solving. Resources like Gemba Academy offer continuous learning in Lean principles.
Implementing these principles requires ongoing commitment and engagement with your team. Encouraging open communication and fostering a culture of continuous improvement are key to sustaining Lean practices in a distribution center environment.
How to Display Lean Principles Skills on Your Resume
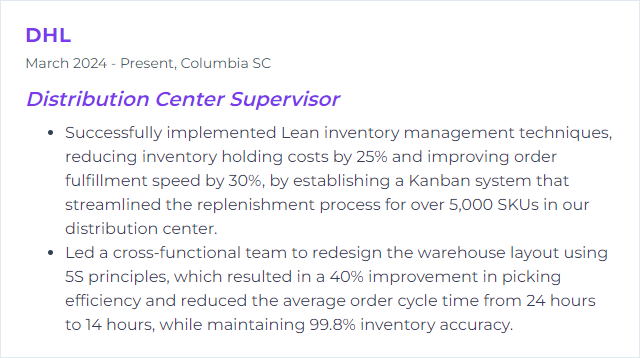
7. Six Sigma
Six Sigma is a data-driven approach and methodology for eliminating defects and improving processes, focusing on quality control and efficiency, particularly relevant for enhancing operations and customer satisfaction in a distribution center environment.
Why It's Important
Six Sigma is important for a Distribution Center Supervisor because it provides a systematic approach to reduce errors, improve process efficiency, and enhance customer satisfaction through data-driven decision-making and continuous improvement.
How to Improve Six Sigma Skills
Improving Six Sigma in the context of a Distribution Center Supervisor involves streamlining processes, reducing waste, and enhancing quality to near perfection. Here are concise strategies:
Define Objectives Clearly: Identify specific goals such as reducing shipment errors or improving packing time. Define Phase Tools.
Measure Current Performance: Use data to establish current performance baselines. Tools like control charts can be helpful. Measure Phase Tools.
Analyze Data: Identify root causes of inefficiencies through tools like Fishbone diagrams. Analyze Phase Tools.
Improve Processes: Implement solutions such as reorganizing workstations or optimizing inventory layout. Lean Six Sigma methodologies can be particularly useful here. Improve Phase Tools.
Control and Sustain: Develop standard operating procedures (SOPs) and training to maintain improvements. Regular audits and KPI monitoring are vital. Control Phase Tools.
Employee Involvement: Engage your team in the Six Sigma process through training and involvement in improvement projects. Employee Involvement.
Continuous Education: Stay informed on the latest trends and technologies in distribution and Six Sigma through continuous learning. ASQ Resources.
By focusing on these strategies, a Distribution Center Supervisor can significantly improve operations through the application of Six Sigma methodologies.
How to Display Six Sigma Skills on Your Resume
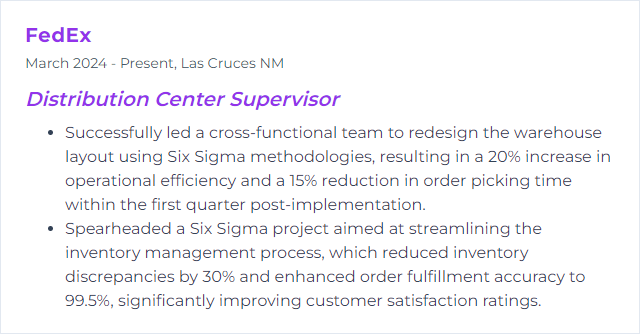
8. Team Leadership
Team leadership in the context of a Distribution Center Supervisor involves guiding and coordinating a group of employees to ensure efficient operations, meeting performance goals, and fostering a collaborative and positive work environment. This role requires effective communication, problem-solving skills, and the ability to motivate and support team members to achieve specific distribution objectives.
Why It's Important
Team leadership is crucial for a Distribution Center Supervisor because it ensures efficient coordination, motivates employees for peak performance, enhances problem-solving, and maintains operational flow, directly impacting timely and accurate product distribution.
How to Improve Team Leadership Skills
Improving team leadership, especially for a Distribution Center Supervisor, involves enhancing communication, fostering a positive work culture, and developing effective management strategies. Here are concise tips for improvement:
Enhance Communication: Clearly communicate goals, expectations, and feedback. Harvard Business Review offers insights on giving effective team feedback.
Lead by Example: Demonstrate the work ethic, attitude, and behavior you expect from your team. Forbes discusses authentic leadership.
Empower Your Team: Delegate tasks to build trust and develop your team’s skills. The American Management Association provides a step-by-step guide to delegation.
Encourage Team Collaboration: Promote a collaborative environment where team members feel valued and engaged. Inc. Magazine shares secrets to building effective teams.
Foster a Positive Work Culture: Cultivate a supportive and inclusive culture. Gallup explains the importance of the right work culture over mere employee satisfaction.
Continuous Learning and Improvement: Invest in training and development for both yourself and your team. LinkedIn Learning offers courses on leadership and management.
Adapt and Be Flexible: Stay open to new ideas and be ready to adjust strategies as necessary. McKinsey & Company discusses leadership in times of crisis.
Use Technology Wisely: Implement tools and systems that enhance efficiency and communication. Capterra lists warehouse management software that can streamline operations.
By focusing on these areas, a Distribution Center Supervisor can significantly improve their team leadership skills, leading to a more efficient, motivated, and cohesive team.
How to Display Team Leadership Skills on Your Resume
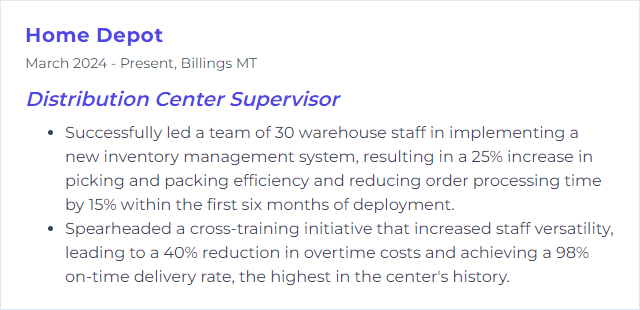
9. Forecasting
Forecasting, in the context of a Distribution Center Supervisor, involves predicting future inventory needs, customer demand, and supply chain challenges to ensure efficient operations and meet customer expectations.
Why It's Important
Forecasting is crucial for a Distribution Center Supervisor as it enables efficient inventory management, ensures timely order fulfillment, minimizes stockouts and overstock, optimizes staffing levels, and enhances overall operational efficiency and customer satisfaction.
How to Improve Forecasting Skills
Improving forecasting, especially for a Distribution Center Supervisor, involves a blend of data analysis, technology adoption, and collaboration. Here are concise strategies:
Leverage Historical Data: Analyze past sales and inventory levels to identify patterns. Tools like Excel can be basic but effective for trend analysis.
Implement Forecasting Software: Invest in specialized forecasting software that uses AI and machine learning for more accurate predictions.
Collaborate with Stakeholders: Work closely with sales, marketing, and procurement to understand market trends and customer needs. This collaboration can be facilitated through platforms like Slack for communication.
Monitor External Factors: Stay informed on industry trends, economic indicators, and seasonal impacts by utilizing resources like the U.S. Bureau of Economic Analysis.
Continuous Improvement: Regularly review forecasting accuracy and adjust processes accordingly. Implement a feedback loop within systems like Asana for task and project management.
By combining data-driven approaches with effective communication and the right technology, Distribution Center Supervisors can significantly improve their forecasting accuracy.
How to Display Forecasting Skills on Your Resume
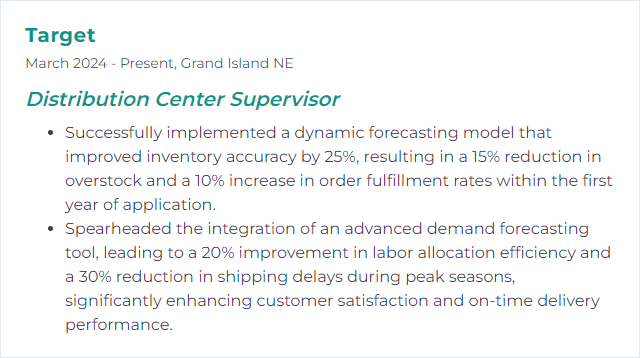
10. ERP (Enterprise Resource Planning)
ERP (Enterprise Resource Planning) is a software system that integrates and manages all core business processes, such as inventory management, order processing, and shipping, in real-time, enabling a Distribution Center Supervisor to optimize operations and improve efficiency.
Why It's Important
ERP systems are crucial for Distribution Center Supervisors as they streamline inventory management, optimize supply chain operations, and ensure timely order fulfillment by integrating processes and data across departments, leading to increased efficiency and reduced operational costs.
How to Improve ERP (Enterprise Resource Planning) Skills
Improving ERP systems, especially for a Distribution Center Supervisor, involves optimizing processes, enhancing data accuracy, and ensuring system agility. Here's a concise guide:
Process Optimization: Streamline workflows by identifying and eliminating bottlenecks. Use ERP analytics to pinpoint inefficiencies.
Data Accuracy: Implement real-time data capture methods (like RFID or barcode scanning) to ensure inventory and transaction accuracy.
Training: Continuously train staff on ERP functionalities to improve user competency and data integrity. APICS offers resources for operational excellence.
Integration: Ensure your ERP integrates seamlessly with other business systems (e.g., CRM, SCM) for a unified data ecosystem. Gartner provides insights on technology integration.
Customization: Tailor the ERP system to fit your specific distribution center needs, focusing on modules that enhance inventory management and order processing.
Feedback Loop: Establish a feedback loop with end-users to continuously gather insights and improve ERP system usability and effectiveness.
Technology Upgrades: Stay updated with ERP software upgrades and emerging technologies that can enhance system performance and capabilities.
By focusing on these areas, a Distribution Center Supervisor can significantly improve the efficiency and effectiveness of their ERP system, leading to optimized operations and better decision-making.
How to Display ERP (Enterprise Resource Planning) Skills on Your Resume

11. Continuous Improvement
Continuous Improvement is an ongoing effort to enhance processes, systems, and performance in a Distribution Center, aiming for increased efficiency, reduced waste, and improved productivity and quality.
Why It's Important
Continuous improvement is crucial for a Distribution Center Supervisor because it enhances efficiency, reduces costs, ensures adaptability to market changes, and improves customer satisfaction through streamlined processes and consistent quality enhancement.
How to Improve Continuous Improvement Skills
To improve Continuous Improvement as a Distribution Center Supervisor, follow these concise steps:
Identify Areas for Improvement: Regularly analyze operations to identify inefficiencies or areas that could benefit from streamlining. Tools like SWOT analysis can be useful.
Implement Lean Principles: Adopt Lean Management techniques to eliminate waste and improve efficiency in processes.
Empower Your Team: Engage your team in the improvement process by encouraging suggestions and feedback. Implement a structured approach like Kaizen for continuous, incremental improvements.
Use Technology: Leverage technology for better inventory management and data analysis. Tools like Warehouse Management Systems (WMS) can optimize distribution center operations.
Measure and Adjust: Establish key performance indicators (KPIs) to measure progress. Use tools like Six Sigma to quantify how far a process deviates from perfection and pinpoint areas for adjustment.
Invest in Training: Continuously train your team on best practices and new technologies. Resources like APICS offer courses and certifications in supply chain management.
Foster a Culture of Continuous Improvement: Create an environment where improvement is part of the daily routine. Encourage open communication and recognize contributions to foster a positive culture. Harvard Business Review’s article on creating a culture of continuous improvement offers additional insights.
By focusing on these areas, you can enhance continuous improvement efforts in your distribution center, leading to more efficient, effective operations.
How to Display Continuous Improvement Skills on Your Resume
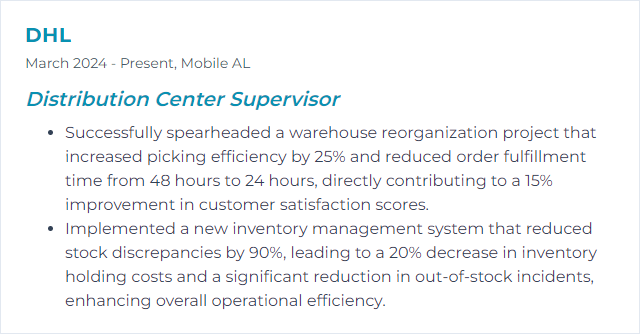
12. RF Scanning
RF Scanning in a Distribution Center context refers to the use of Radio Frequency technology to capture and transmit data about inventory and shipments. This process involves handheld scanners that read barcodes or RFID tags on products, allowing for real-time tracking, efficient inventory management, and accurate order fulfillment.
Why It's Important
RF scanning is crucial for a Distribution Center Supervisor because it enhances inventory accuracy, streamlines order picking processes, improves efficiency, and reduces errors, leading to better overall warehouse management and customer satisfaction.
How to Improve RF Scanning Skills
Improving RF scanning in a Distribution Center involves several key steps. Here's a concise guide:
Training: Ensure all staff are properly trained on using RF scanners. This includes handling, scanning techniques, and troubleshooting. RFID Journal offers resources and case studies on effective training methods.
Software Updates: Regularly update the RF scanner software to ensure compatibility and efficiency. Manufacturers often provide updates and support; check their official websites for the latest software versions.
Equipment Maintenance: Conduct regular maintenance checks on RF scanners to ensure they are in good working condition. This helps in reducing downtime and improving scanning accuracy. Refer to the maintenance guidelines provided by your equipment manufacturer.
Optimize Wi-Fi Connectivity: Ensure your distribution center has strong and stable Wi-Fi coverage as RF scanners rely on this for real-time data transmission. Cisco offers best practices for optimizing Wi-Fi infrastructure.
Feedback Mechanism: Implement a feedback mechanism for users to report issues or suggest improvements regarding the RF scanning process. This can lead to valuable insights for enhancing efficiency. SurveyMonkey provides tools for creating quick surveys for feedback collection.
Use of Accessories: Equip RF scanners with necessary accessories like protective covers, lanyards, or holsters to reduce the risk of damage and improve ease of use. Many accessories can be found on Amazon and specialized retailers.
By focusing on these areas, a Distribution Center Supervisor can significantly improve the efficiency and accuracy of RF scanning operations.
How to Display RF Scanning Skills on Your Resume
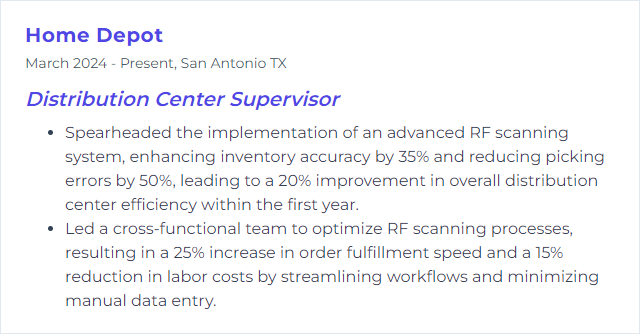