Top 12 Corrosion Technician Skills to Put on Your Resume
In the highly specialized field of corrosion control, showcasing a robust set of skills on your resume can significantly elevate your marketability to potential employers. This article outlines the top 12 skills that corrosion technicians should highlight to demonstrate their expertise and readiness to tackle the challenges of preserving infrastructure and equipment from the detrimental effects of corrosion.
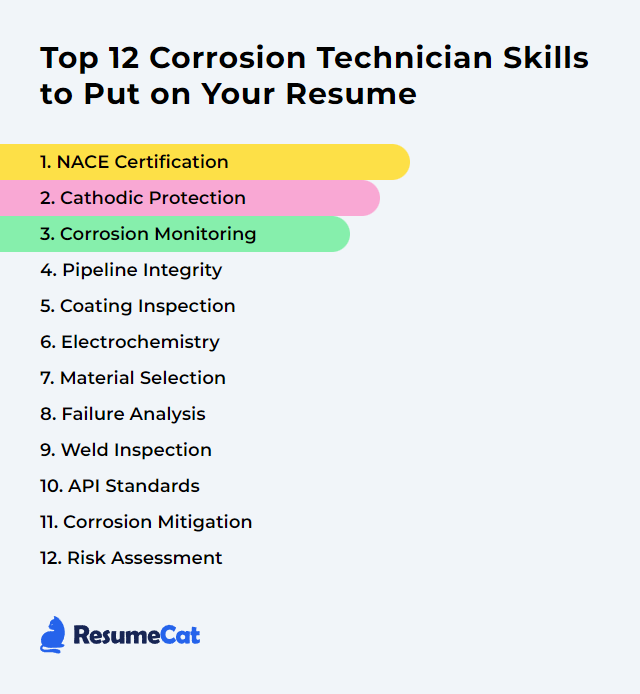
Corrosion Technician Skills
- NACE Certification
- Cathodic Protection
- Corrosion Monitoring
- Pipeline Integrity
- Coating Inspection
- Electrochemistry
- Material Selection
- Failure Analysis
- Weld Inspection
- API Standards
- Corrosion Mitigation
- Risk Assessment
1. NACE Certification
NACE certification, for a Corrosion Technician, is a professional credential awarded by the NACE International Institute, recognizing expertise in the prevention, inspection, and mitigation of corrosion on various structures and materials.
Why It's Important
NACE Certification is important for a Corrosion Technician as it validates their expertise and knowledge in corrosion control, ensuring adherence to industry standards and enhancing their credibility and job prospects in the field.
How to Improve NACE Certification Skills
Improving your NACE Certification as a Corrosion Technician involves a variety of steps focused on education, experience, and continuous learning. Here’s a concise guide:
Gain Practical Experience: Hands-on experience in corrosion control is crucial. Work on projects that allow you to apply theoretical knowledge in real-world scenarios.
Continuing Education: Enroll in advanced courses and workshops to stay updated with the latest technologies and methods in corrosion management. NACE (now part of AMPP) offers specialized courses that can be found on their official website.
Networking: Join professional groups and forums related to corrosion technology. Networking with professionals can provide insights and opportunities not found in textbooks. Consider joining AMPP’s community.
Certification Upgrades: Aim for higher-level certifications as you gain experience. Review the prerequisites and prepare for the next level of certification through AMPP’s Certification Guide.
Attend Seminars and Conferences: Stay informed about the latest research and technologies in the field of corrosion control by attending seminars and conferences. Check out the events section on the AMPP website.
Read and Contribute to Industry Literature: Stay informed with the latest studies and articles in corrosion technology. Journals and magazines from AMPP can be a good source. Also, consider contributing to share your knowledge and insights.
Practice Ethical Standards: Uphold the highest professional and ethical standards as outlined by AMPP. This enhances your reputation and credibility in the field.
By following these steps, you can enhance your skills and knowledge, making you a more competent and qualified Corrosion Technician with improved NACE Certification credentials.
How to Display NACE Certification Skills on Your Resume
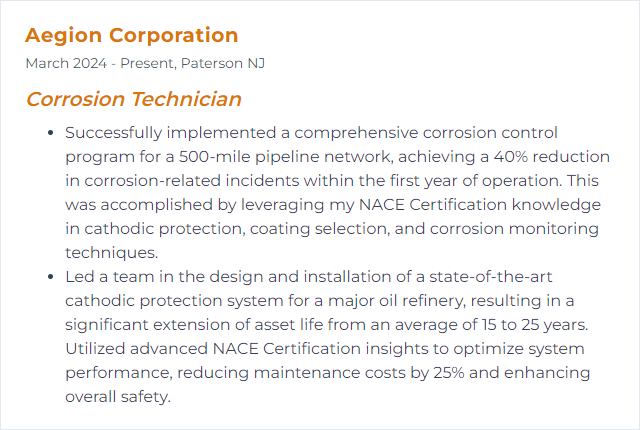
2. Cathodic Protection
Cathodic protection is a method used to prevent metal corrosion by making the metal to be protected the cathode of an electrochemical cell, either by attaching a more easily corroded "sacrificial anode" or by applying an external direct current.
Why It's Important
Cathodic protection is crucial for preventing corrosion in metal structures by transforming them into cathodes, thus extending their lifespan and ensuring structural integrity, crucial for maintaining safety and reducing maintenance costs.
How to Improve Cathodic Protection Skills
Improving cathodic protection involves optimizing system design and maintenance to effectively control corrosion on metal structures. Here’s a concise guide for a Corrosion Technician:
Assessment and Monitoring: Regularly assess the structure's potential and current flow using appropriate instrumentation. Monitoring ensures the cathodic protection system is functioning within desired parameters. NACE International offers guidelines and standards for these assessments.
Anode Selection and Placement: Choose the correct type of anode (galvanic or impressed current) based on the environment and application. Proper placement ensures even distribution of protective currents. Corrosionpedia provides insights on anode types and their applications.
Electrical Continuity: Ensure good electrical continuity within the protected structure to allow uniform distribution of cathodic protection. This might involve adding bonding connections between isolated metal parts.
Regular Inspections and Maintenance: Conduct regular inspections of the anode, reference electrodes, and the protected structure. Replace anodes as needed and adjust power sources to maintain optimal protection levels. The Corrosion Doctors website offers practical maintenance tips.
Utilize Cathodic Protection Modeling Software: Use software tools for designing and optimizing CP systems. These tools can simulate potential distribution and effectiveness, helping in making informed decisions on system adjustments. MATCOR and other companies offer such technological solutions.
Education and Training: Stay informed about the latest technologies, standards, and practices in cathodic protection. Organizations like NACE International and The Institute of Corrosion offer courses and certifications for corrosion technicians.
Implementing these strategies requires a deep understanding of cathodic protection principles and a commitment to ongoing education and system improvement.
How to Display Cathodic Protection Skills on Your Resume
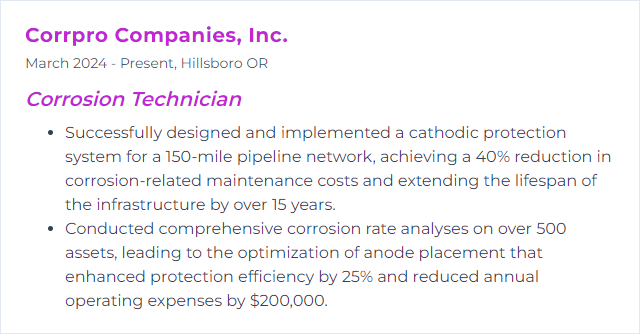
3. Corrosion Monitoring
Corrosion monitoring is the process of systematically tracking and measuring the rate at which materials, typically metals, degrade within their operating environments. For a Corrosion Technician, it involves using various techniques and tools to detect, analyze, and document corrosion levels to prevent failures, ensure safety, and optimize maintenance and replacement schedules.
Why It's Important
Corrosion monitoring is crucial for a Corrosion Technician as it enables the early detection of corrosion, helping to prevent structural failures, ensure safety, minimize economic losses, and guide the implementation of effective corrosion control measures.
How to Improve Corrosion Monitoring Skills
Improving corrosion monitoring involves adopting a comprehensive strategy that integrates advanced technologies, regular assessments, and data analysis to efficiently predict and mitigate corrosion risks. Here's a concise guide for a Corrosion Technician:
Utilize Advanced Sensors: Deploy smart sensors that can provide real-time data on corrosion rates, environmental conditions, and metal thickness.
Implement Non-destructive Testing (NDT): Use NDT methods like ultrasonic testing and radiography for in-situ corrosion assessment without damaging the equipment.
Digital Monitoring Tools: Leverage digital corrosion monitoring tools for continuous surveillance and analysis of corrosion data.
Regular Visual Inspections: Conduct frequent inspections and document findings. Utilize drones for accessing hard-to-reach areas.
Corrosion Inhibitors: Explore and apply corrosion inhibitors tailored to the specific environment and material.
Data Analysis and Predictive Modeling: Employ software for predictive modeling based on historical and real-time data to foresee corrosion trends and prevent failures.
Training and Education: Stay updated with the latest in corrosion monitoring techniques through continuous training and certification.
Collaborative Approach: Work closely with engineers, maintenance teams, and material scientists for an integrated approach to corrosion management.
By enhancing skills and integrating technology, a Corrosion Technician can significantly improve the effectiveness of corrosion monitoring strategies.
How to Display Corrosion Monitoring Skills on Your Resume
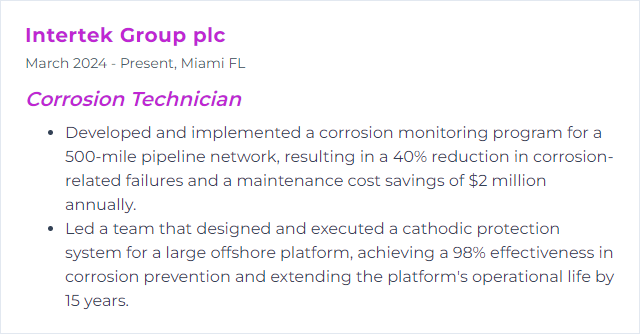
4. Pipeline Integrity
Pipeline integrity refers to the comprehensive management process implemented by corrosion technicians and other professionals to ensure pipelines are designed, operated, and maintained safely and effectively, minimizing risks such as leaks, ruptures, or failures due to corrosion, material defects, or external forces.
Why It's Important
Pipeline integrity is crucial for ensuring safe and efficient transport of materials, preventing leaks and catastrophic failures, which can lead to environmental damage, financial losses, and safety hazards. For a Corrosion Technician, maintaining pipeline integrity is key to mitigating corrosion risks and prolonging the pipeline's lifespan, thus safeguarding both public safety and operational continuity.
How to Improve Pipeline Integrity Skills
Improving pipeline integrity, especially from the perspective of a Corrosion Technician, involves a focused approach on monitoring, prevention, and maintenance strategies aimed at combating corrosion. Here's a concise guide:
Regular Inspections and Monitoring: Implement routine inspections using tools like Pipeline Inspection Gauges (PIGs) and Cathodic Protection Systems, to detect early signs of corrosion and ensure the effectiveness of cathodic protection measures.
Cathodic Protection Implementation: Utilize Cathodic Protection, a method to control the corrosion of a metal surface by making it the cathode of an electrochemical cell. It's vital for mitigating corrosion on metal surfaces.
Coating and Linings Application: Apply protective coatings and linings to the pipeline exterior and interior. This serves as a barrier against corrosive agents.
Environmental Control: Understand and control the environmental factors contributing to corrosion. This includes moisture control, temperature regulation, and minimizing exposure to corrosive substances.
Data Analysis and Risk Assessment: Regularly analyze the collected data from inspections and monitoring to assess the risk and prioritize maintenance. Software tools and integrity management programs can aid in this process.
Education and Training: Stay updated with the latest in corrosion prevention technologies and strategies through continuous education and training.
Implementing these strategies effectively can significantly enhance the integrity of pipelines, ensuring their safe and efficient operation.
How to Display Pipeline Integrity Skills on Your Resume
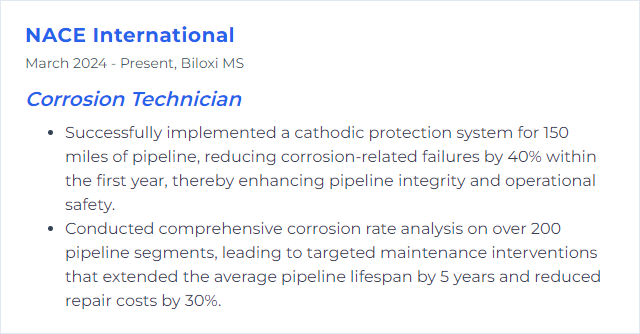
5. Coating Inspection
Coating inspection, in the context of a Corrosion Technician, involves the examination and evaluation of protective coatings applied to metal surfaces to prevent corrosion. This process includes assessing the coating's application quality, adherence, thickness, and integrity to ensure long-term protection against environmental factors that cause corrosion.
Why It's Important
Coating inspection is crucial for a Corrosion Technician to ensure the integrity and longevity of protective coatings on metal surfaces, preventing corrosion, thereby minimizing maintenance costs, and ensuring safety and structural reliability.
How to Improve Coating Inspection Skills
Improving coating inspection as a Corrosion Technician involves a combination of enhancing your technical knowledge, applying advanced inspection tools, and adhering to industry standards. Here’s a concise guide:
Educate Yourself: Continuously update your knowledge on the latest coating technologies and inspection techniques. Online courses and webinars can be valuable resources. The NACE International website is a great place to start, offering a range of educational resources.
Utilize Advanced Inspection Tools: Invest in and learn how to effectively use advanced inspection tools such as digital dry-film thickness gauges, adhesion testers, and holiday detectors. Understanding the proper use of these tools can significantly improve inspection accuracy. For a comprehensive guide on tools, the SSPC (The Society for Protective Coatings) provides insightful guidelines and standards.
Follow Industry Standards: Adherence to standards set by organizations like NACE and SSPC ensures that inspections meet the highest quality benchmarks. Familiarize yourself with standards like SSPC-PA 2 for coating thickness measurement and NACE No. 2/SSPC-SP 10 for surface cleanliness.
Hands-on Practice: Practical experience is invaluable. Participate in workshops and hands-on training sessions whenever possible. Both NACE and SSPC offer certification programs that include practical components.
Stay Informed on Environmental and Safety Regulations: Coating inspection doesn’t only involve evaluating the quality of the work but also ensuring that it complies with environmental and safety regulations. EPA and OSHA websites are crucial resources for keeping up with these regulations.
Join Professional Networks: Engaging with professional communities can provide insights into best practices and innovative approaches. LinkedIn groups and forums dedicated to corrosion and coating professionals are good places to start.
By focusing on education, utilizing the right tools, adhering to standards, gaining hands-on experience, complying with regulations, and networking with peers, you can significantly improve your coating inspection processes.
How to Display Coating Inspection Skills on Your Resume
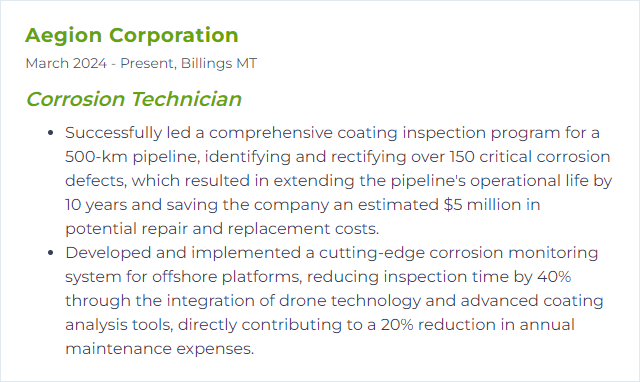
6. Electrochemistry
Electrochemistry is the branch of chemistry that studies chemical reactions which take place at the interface of an electrode, usually a solid metal or a semiconductor, and an ionic conductor, the electrolyte. These reactions involve electric charges moving between the electrode and the electrolyte. For a Corrosion Technician, electrochemistry is crucial as it helps understand and prevent corrosion processes, which are electrochemical in nature, where metals are oxidized and deteriorate in their environment.
Why It's Important
Electrochemistry is vital for a Corrosion Technician because it provides the foundational principles for understanding, predicting, and controlling corrosion processes, which are electrochemical in nature. This knowledge is crucial for the design of effective corrosion prevention and mitigation strategies.
How to Improve Electrochemistry Skills
Improving your skills in electrochemistry as a Corrosion Technician involves a combination of theoretical knowledge and practical application. Here's a concise guide:
Strengthen Fundamental Knowledge: Ensure a strong understanding of basic electrochemistry principles. The Electrochemical Society offers resources and publications for deepening your theoretical knowledge.
Practical Application: Apply your knowledge in real-world scenarios. Hands-on experience with corrosion monitoring, prevention, and protection techniques is critical. The NACE International (now part of SSPC: The Society for Protective Coatings) provides training, certifications, and resources specifically for corrosion professionals.
Stay Updated: Electrochemistry and corrosion technology are evolving fields. Subscribe to journals such as Corrosion Journal and participate in workshops and conferences to stay informed about the latest research, tools, and techniques.
Networking and Collaboration: Engage with the community through forums and professional networks. Sharing experiences and solutions with peers can provide new insights and approaches. LinkedIn groups and specific forums on The Corrosion Network can be valuable.
Software Proficiency: Familiarize yourself with corrosion analysis and prediction software. Tools like COMSOL Multiphysics® (COMSOL) for simulation and modeling can enhance your ability to predict and mitigate corrosion issues.
Safety and Environmental Compliance: Understand the environmental impact of corrosion and the importance of safety in handling materials and chemicals. Resources from Environmental Protection Agency (EPA) and Occupational Safety and Health Administration (OSHA) provide guidelines and standards.
By focusing on these areas, you can significantly improve your expertise in electrochemistry and corrosion management.
How to Display Electrochemistry Skills on Your Resume
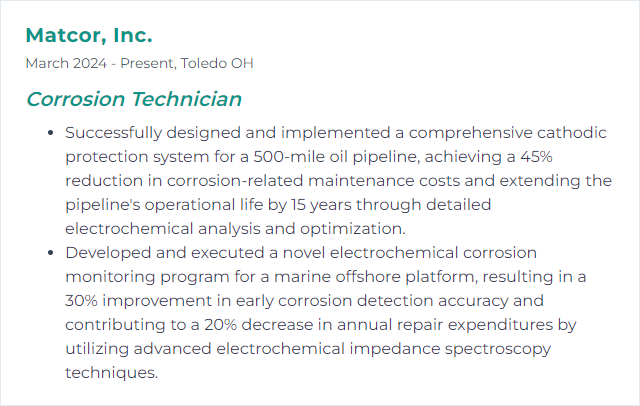
7. Material Selection
Material selection is the process of choosing materials that best suit the specific requirements of a project or application, with a focus on resistance to corrosion, durability, cost, and performance, to ensure longevity and reliability of the equipment or structure under various environmental conditions.
Why It's Important
Material selection is crucial for a Corrosion Technician because the right materials can significantly reduce or prevent corrosion, ensuring the longevity, safety, and reliability of equipment and structures, thereby minimizing maintenance costs and downtime.
How to Improve Material Selection Skills
Improving material selection, especially in the context of corrosion management, involves a multi-faceted approach that integrates understanding material properties, environmental factors, and application requirements. Here are concise steps for a Corrosion Technician to enhance material selection:
Understand the Environment: Recognize the corrosive elements (chemicals, temperature, pressure) the material will be exposed to. The NACE International provides resources on understanding different corrosive environments.
Material Properties: Familiarize with the chemical, mechanical, and physical properties of various materials. Use the ASM International Materials Database to compare material properties.
Corrosion Resistance: Select materials with inherent resistance to corrosion in the specific environment they will be used. The Corrosion Doctors website offers insights into materials' corrosion resistance.
Protective Coatings: Consider materials that can be effectively coated or treated to enhance their corrosion resistance. The SSPC: The Society for Protective Coatings provides guidelines on protective coatings.
Design Considerations: Opt for materials that fit the design requirements, including shape, weight, and ease of fabrication. The American Institute of Steel Construction (AISC) offers resources on design considerations for steel structures.
Cost-Effectiveness: Balance between the initial material cost and the lifespan of the material in the corrosive environment. Tools like Total Cost of Ownership (TCO) calculators can help in making cost-effective decisions.
Standards and Regulations: Ensure materials comply with international and local standards and regulations relevant to the application and environment. The ASTM International standards are a key resource.
Consultation and Collaboration: Engage with material scientists, engineers, and industry experts for insights. Professional platforms like LinkedIn can facilitate networking and knowledge exchange.
By incorporating these steps, a Corrosion Technician can make informed and effective material selection decisions to mitigate corrosion and enhance the longevity and safety of structures and components.
How to Display Material Selection Skills on Your Resume
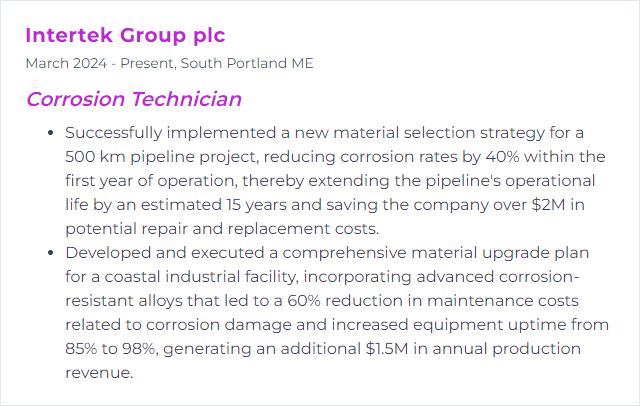
8. Failure Analysis
Failure analysis, in the context of a Corrosion Technician, is the systematic investigation of a material or component failure due to corrosion, aiming to identify the causes and recommend preventive measures.
Why It's Important
Failure analysis is crucial for a Corrosion Technician because it identifies the root causes of material degradation, enabling the development of effective prevention strategies to ensure the integrity and longevity of infrastructure and equipment.
How to Improve Failure Analysis Skills
Improving failure analysis, especially for a Corrosion Technician, involves systematic approaches to identify, understand, and mitigate material degradation. Here's a concise guide:
Understand the Basics: Grasp fundamental corrosion mechanisms and types (NACE International).
Data Collection: Gather comprehensive data on the failed component, including its material, operating environment, and history of use.
Visual Inspection: Perform thorough visual inspections and document findings (ASM International).
Non-Destructive Testing (NDT): Utilize NDT methods like ultrasonic testing or radiography to assess internal damage without further harming the component (American Society for Nondestructive Testing).
Sample Analysis: Analyze samples using techniques like Scanning Electron Microscopy (SEM) or Energy Dispersive X-ray (EDX) for microstructural and chemical insights (Microscopy Society of America).
Root Cause Analysis (RCA): Apply RCA techniques to trace the fundamental reasons behind the failure, considering all possible factors.
Report and Recommend: Compile findings into a comprehensive report detailing the failure analysis process, conclusions, and recommendations for prevention.
Continual Learning: Stay updated with the latest in corrosion science and failure analysis techniques through professional development and training (NACE International Courses).
By following these steps, Corrosion Technicians can enhance their failure analysis capabilities, leading to more accurate diagnoses and effective prevention strategies.
How to Display Failure Analysis Skills on Your Resume
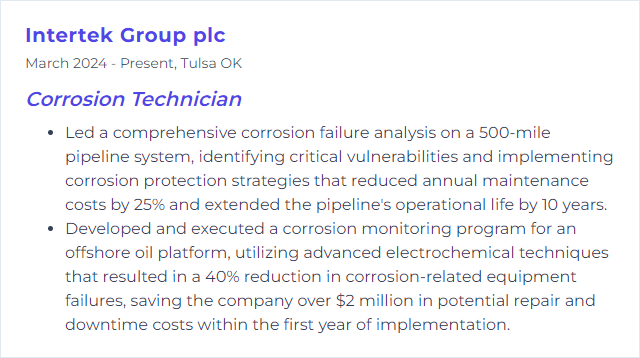
9. Weld Inspection
Weld inspection is the process of examining the quality and integrity of welds to ensure they meet specified standards and are free from defects that could lead to corrosion or failure. For a Corrosion Technician, it involves assessing weld areas for signs of corrosion, material degradation, or improper welding techniques that could compromise the structure's longevity and safety.
Why It's Important
Weld inspection is crucial for a Corrosion Technician to ensure the integrity and longevity of welded structures by identifying potential defects that can lead to corrosion, thereby preventing structural failures and ensuring safety and reliability.
How to Improve Weld Inspection Skills
Improving weld inspection, especially from a Corrosion Technician's perspective, involves a blend of enhanced techniques, continuous learning, and the application of advanced tools. Here are some concise tips for improvement:
Enhance Visual Inspection Skills: Begin with mastering visual inspection techniques, as it's the most fundamental aspect of weld inspection. Understanding weld profiles, color changes, and surface irregularities can provide initial insights into potential corrosion issues. AWS Visual Inspection Workshop offers a good starting point.
Utilize Non-Destructive Testing (NDT) Methods: Incorporate advanced NDT methods such as Ultrasonic Testing (UT), Magnetic Particle Testing (MT), and Radiographic Testing (RT) for deeper insights. These techniques can help in identifying subsurface flaws and inclusions that are not visible to the naked eye. ASNT provides resources and certifications in these areas.
Apply Corrosion Mapping Tools: Use corrosion mapping tools and techniques to accurately measure and monitor corrosion and material thickness over time. This can help in predicting potential weld failures. Ultrasound technology is often used for this purpose. Olympus-IMS has resources and equipment for corrosion monitoring.
Keep Updated with Codes and Standards: Stay informed about the latest industry standards and codes related to welding and corrosion, such as those from API and NACE, now part of SSPC: The Society for Protective Coatings.
Participate in Continuous Learning: Engage in continuous learning through workshops, seminars, and online courses focused on welding inspection and corrosion. Platforms like Coursera and edX offer courses relevant to this field.
Implement Corrosion Control Measures: Understand and apply corrosion control measures in welding, such as selecting appropriate welding materials, using corrosion-resistant weld metals, and applying protective coatings. Knowledge of cathodic protection can also be beneficial. NACE Resources provide extensive information on corrosion control.
By focusing on these areas, a Corrosion Technician can significantly improve their weld inspection capabilities, leading to better maintenance, longer material life, and overall safety improvements.
How to Display Weld Inspection Skills on Your Resume
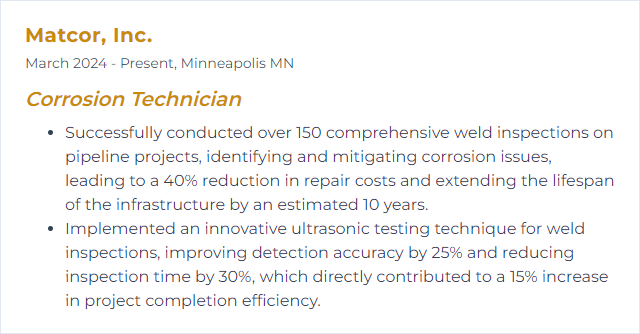
10. API Standards
API standards for a Corrosion Technician refer to guidelines and best practices developed by the American Petroleum Institute for designing, maintaining, and inspecting equipment and infrastructure to prevent corrosion in the oil and gas industry.
Why It's Important
API standards are crucial for Corrosion Technicians because they provide consistent, reliable methods for monitoring, preventing, and managing corrosion in pipelines and equipment. This ensures safety, operational efficiency, and compliance with regulatory requirements.
How to Improve API Standards Skills
Improving API (American Petroleum Institute) standards, particularly from the perspective of a Corrosion Technician, involves a few key steps focused on enhancing the reliability, safety, and effectiveness of corrosion control methods. Here's a concise guide:
Continuous Learning and Adaptation: Stay updated with the latest corrosion control technologies and methods. Engage in continuous education through resources like NACE International and API's own courses and certifications.
Active Participation in Standards Development: Join API committees or working groups to contribute to the development or revision of standards. Your practical experience can provide valuable insights for improvement. Information on participation can be found on the API Standards Committees page.
Implementing Best Practices: Ensure that the latest API standards and recommended practices for corrosion control are being correctly implemented in your operations. Regularly review practices against standards such as API 571 (Damage Mechanisms Affecting Fixed Equipment in the Refining Industry) and API 580 (Risk-Based Inspection).
Feedback and Case Studies: Document and share feedback or case studies on the application of API standards in corrosion control. This real-world evidence can be invaluable for refining and updating standards. Submit findings or suggestions through the API website.
Collaboration with Industry Peers: Foster collaborations with peers through forums, conferences, and workshops to discuss challenges, share solutions, and disseminate knowledge on API standards. Engaging in platforms like LinkedIn groups related to API standards or corrosion technology can be beneficial.
Adoption of New Technologies: Explore and integrate new technologies like advanced non-destructive testing methods or corrosion monitoring tools. Staying at the forefront of technological advancements can drive improvements in standards.
Safety and Environmental Compliance: Ensure that all practices not only meet API standards but also adhere to environmental regulations and safety protocols. This holistic approach can lead to the development of more comprehensive and responsible standards.
By focusing on these areas, Corrosion Technicians can play a pivotal role in enhancing API standards, ensuring they remain relevant, practical, and effective in addressing the evolving challenges of corrosion control.
How to Display API Standards Skills on Your Resume
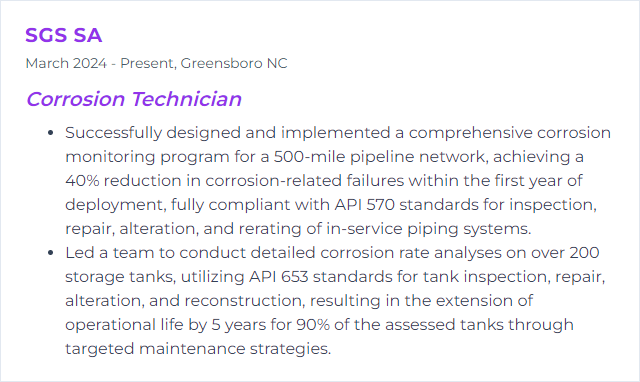
11. Corrosion Mitigation
Corrosion mitigation refers to the processes and strategies a Corrosion Technician implements to prevent, reduce, or control corrosion damage in materials and structures, ensuring their longevity and functionality.
Why It's Important
Corrosion mitigation is crucial as it extends the lifespan of materials and structures, prevents failures and leaks that could pose safety hazards, and reduces maintenance costs, ensuring the reliability and integrity of assets under a corrosion technician's care.
How to Improve Corrosion Mitigation Skills
Improving corrosion mitigation involves a multifaceted approach that combines selecting appropriate materials, applying protective coatings, employing cathodic protection, and regular monitoring and maintenance.
Material Selection: Choose materials that naturally resist corrosion in the specific environment they will be exposed to. Stainless steel, for example, offers resistance in many corrosive environments.
Protective Coatings: Apply protective coatings like paints, plating, or powder coatings to act as a barrier between the material and corrosive agents.
Cathodic Protection: Implement cathodic protection systems, such as sacrificial anodes or impressed current systems, to mitigate corrosion on metal surfaces.
Corrosion Inhibitors: Use corrosion inhibitors, chemicals that, when added in small concentrations, decrease the corrosion rate of a material.
Regular Monitoring and Maintenance: Conduct regular inspections and employ corrosion monitoring techniques like electrical resistance, linear polarization resistance, and ultrasonic thickness measurements to identify and address issues early.
Environment Control: Reduce exposure to corrosive environments where possible, such as controlling humidity or limiting contact with chemicals.
By implementing these strategies, a Corrosion Technician can significantly enhance corrosion mitigation efforts, prolonging the lifespan of materials and structures in corrosive environments.
How to Display Corrosion Mitigation Skills on Your Resume
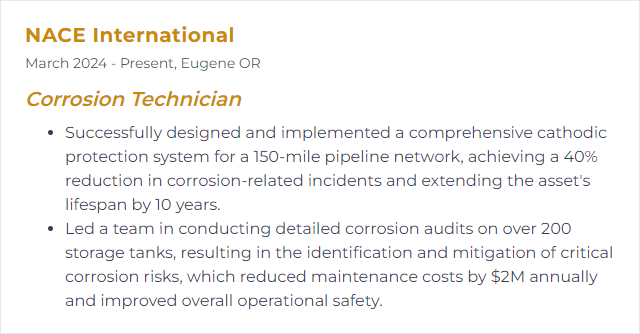
12. Risk Assessment
Risk assessment, in the context of a Corrosion Technician, involves evaluating the potential hazards and vulnerabilities of materials or structures to corrosion, determining the likelihood and consequences of corrosion damage, and identifying the necessary preventive measures to mitigate risks and ensure integrity and safety.
Why It's Important
Risk assessment is crucial for a Corrosion Technician as it helps identify and evaluate potential risks to infrastructure or equipment due to corrosion, enabling the implementation of preventative measures, ensuring safety, reducing repair costs, and prolonging asset lifespan.
How to Improve Risk Assessment Skills
Improving risk assessment, especially for a Corrosion Technician, involves a blend of updated technical knowledge, practical experience, and leveraging advanced tools and methodologies. Here’s a concise guide:
Update Knowledge Base: Stay informed about the latest in corrosion science and technology. Understand materials, environments, and their interactions. NACE International offers resources and training for professionals.
Use Advanced Tools: Leverage modern assessment tools like corrosion mapping and predictive maintenance software. Tools like Cortec’s Corrosion Management Software can help in predicting and preventing corrosion risks.
Implement Risk-Based Inspection (RBI): Adopt an RBI approach to focus on areas with the highest risk. Guidelines from API 580 and 581 provide a structured framework for conducting risk assessments.
Engage in Continuous Learning: Keep abreast of new methodologies and standards in risk assessment through professional development courses. ASME offers courses and certifications that could be beneficial.
Practical Experience: Hands-on experience is invaluable. Engage in fieldwork, understand different corrosion mechanisms in practice, and learn from seasoned professionals about effective assessment strategies.
Collaborate and Network: Share knowledge and learn from peers by engaging with professional communities and forums. Platforms like LinkedIn’s Corrosion Professionals Group can be a valuable resource for exchanging insights and staying updated on industry trends.
By integrating these strategies, a Corrosion Technician can significantly enhance their risk assessment capabilities, contributing to safer and more efficient operations.
How to Display Risk Assessment Skills on Your Resume
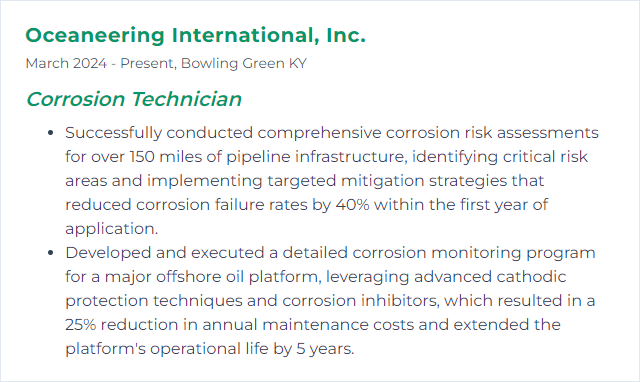