Top 12 Corrosion Engineer Skills to Put on Your Resume
In the highly specialized field of corrosion engineering, showcasing the right set of skills on your resume can significantly elevate your job prospects and set you apart from the competition. This article outlines the top 12 skills that corrosion engineers should highlight to demonstrate their expertise and readiness to tackle the challenges inherent in preserving infrastructure and equipment against corrosive damage.
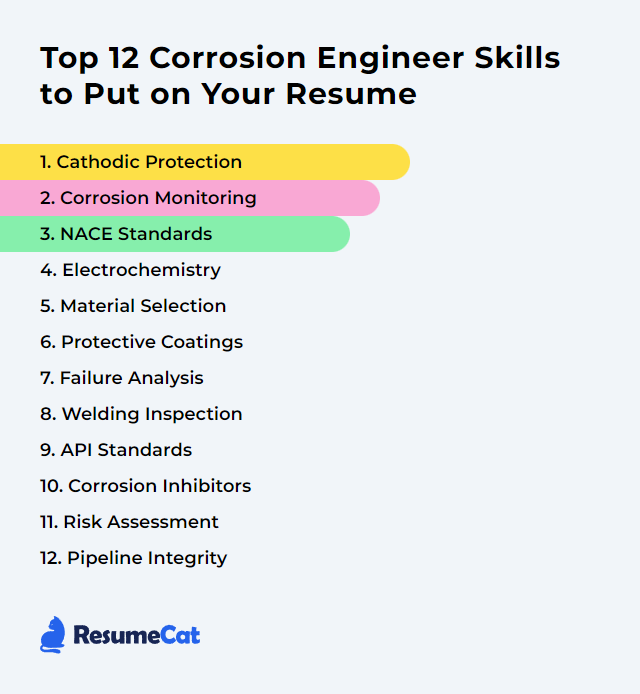
Corrosion Engineer Skills
- Cathodic Protection
- Corrosion Monitoring
- NACE Standards
- Electrochemistry
- Material Selection
- Protective Coatings
- Failure Analysis
- Welding Inspection
- API Standards
- Corrosion Inhibitors
- Risk Assessment
- Pipeline Integrity
1. Cathodic Protection
Cathodic protection is a technique used to control the corrosion of a metal surface by making it the cathode of an electrochemical cell. This is achieved either by attaching a sacrificial anode made of a more easily corroded metal, or by applying a direct electrical current.
Why It's Important
Cathodic protection is essential as it significantly reduces corrosion rates on metal surfaces by making them the cathode of an electrochemical cell, thus extending the lifespan and ensuring the integrity of infrastructure and equipment in corrosive environments.
How to Improve Cathodic Protection Skills
Improving cathodic protection (CP) involves optimizing the protection system to efficiently mitigate corrosion on metal surfaces in conductive environments. Here are concise strategies tailored for a Corrosion Engineer:
Assessment and Monitoring: Regularly assess and monitor the CP system's performance using potential measurements and coupons to ensure it meets the required protection criteria. NACE International provides standards and guidelines for these practices.
Anode Selection and Placement: Choose the appropriate anode material and strategically place anodes to ensure uniform distribution of current. The Corrosion Doctors website offers insights into anode materials and their applications.
Electrical Continuity: Ensure electrical continuity in the structures being protected to allow free flow of protective currents. Techniques and guidelines can be found through ASM International.
Impressed Current CP Systems (ICCP): For structures requiring higher levels of protection, consider using ICCP systems. These systems allow for precise control over the amount of current applied. The Corrosionpedia website offers a good starting point for understanding ICCP.
Regular Maintenance: Conduct regular maintenance of the CP system, including anode replacement, rectifier inspection, and adjustment of protection levels. The Cathodic Protection Co. provides maintenance services and advice.
Advanced Technologies: Incorporate advanced technologies such as remote monitoring and control systems to dynamically adjust protection levels and predict maintenance needs. Information on the latest technologies can be found through NACE International’s CORROSION journal.
Education and Training: Stay updated on the latest CP techniques and technologies by engaging in continuous education and professional development through organizations like NACE International.
By following these strategies and leveraging resources from reputable organizations and industry websites, Corrosion Engineers can significantly improve the effectiveness of cathodic protection systems.
How to Display Cathodic Protection Skills on Your Resume
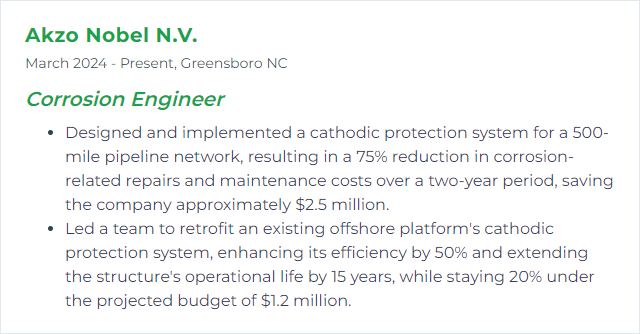
2. Corrosion Monitoring
Corrosion monitoring is the process of systematically tracking and analyzing the rate and extent of corrosion in materials and structures, employing various techniques and instruments to detect, quantify, and predict degradation over time, enabling corrosion engineers to implement preventative and corrective measures to mitigate damage and extend service life.
Why It's Important
Corrosion monitoring is crucial for a Corrosion Engineer as it enables the early detection and evaluation of material degradation, helps in predicting failure, and guides the implementation of cost-effective maintenance and prevention strategies, ensuring safety, reliability, and longevity of assets and infrastructure.
How to Improve Corrosion Monitoring Skills
Improving corrosion monitoring involves a multi-faceted approach focused on enhancing accuracy, reliability, and predictive capabilities. Follow these concise steps for effective improvement:
Utilize Advanced Sensors: Employ modern corrosion rate monitoring sensors like electrical resistance (ER), linear polarization resistance (LPR), and electrochemical noise (ECN) sensors for real-time data. NACE International provides insights into the latest sensor technologies.
Implement Non-destructive Testing (NDT): Use techniques like ultrasonic testing (UT) and radiography to detect and measure corrosion without damaging your assets. ASNT offers resources on NDT methods.
Leverage Predictive Analytics: Incorporate machine learning and AI to analyze historical and real-time data for predictive corrosion management. IBM's Predictive Maintenance explores the application of AI in predictive analytics.
Regular Calibration and Maintenance: Ensure that monitoring equipment is regularly calibrated and maintained to avoid inaccuracies. Guidelines on calibration practices can be found through ASTM International.
Corrosion Coupons and Probes: Use corrosion coupons and probes for direct measurement and monitoring of corrosion rates in your systems. Corrosionpedia offers detailed explanations and resources.
Training and Education: Continuously educate and train staff on the latest corrosion monitoring technologies and practices. NACE International Courses provide a variety of training opportunities for professionals.
By integrating these strategies, corrosion engineers can significantly enhance the effectiveness and efficiency of corrosion monitoring within their operations.
How to Display Corrosion Monitoring Skills on Your Resume
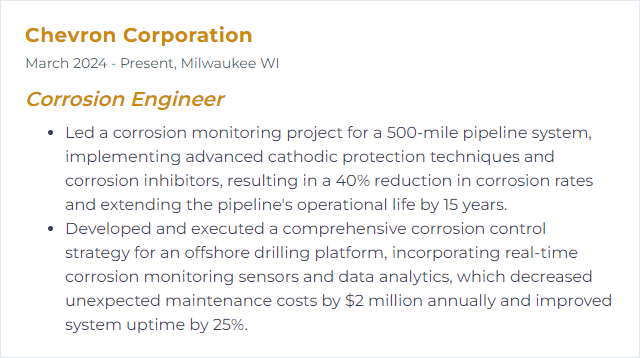
3. NACE Standards
NACE Standards, developed by the National Association of Corrosion Engineers (now part of the Association for Materials Protection and Performance - AMPP), provide guidelines and best practices for preventing and managing corrosion in various industries. For a Corrosion Engineer, these standards serve as crucial references for designing, implementing, and maintaining corrosion control and mitigation strategies to ensure the longevity and reliability of materials, structures, and systems.
Why It's Important
NACE Standards are crucial for a Corrosion Engineer as they provide internationally recognized guidelines and practices for corrosion control, ensuring the safety, reliability, and longevity of materials and structures in various industries.
How to Improve NACE Standards Skills
Improving NACE Standards, now overseen by the Association for Materials Protection and Performance (AMPP) after the NACE International merger with SSPC, can be a critical task for Corrosion Engineers aiming to enhance industry practices and outcomes. Here are concise steps for this process:
Stay Informed and Involved: Regularly review current standards and participate in AMPP community discussions to identify areas of improvement. AMPP website
Identify Gaps or Updates Needed: Focus on technological advancements, new materials, and corrosion mitigation techniques not currently covered or adequately detailed in existing standards.
Gather Supporting Information: Compile research, case studies, and expert opinions to support the proposed changes or new standards. This evidence base is crucial for justifying the need for revision or creation.
Engage with Technical Committees: Most updates or new standards development processes are initiated and carried out by technical committees. Join relevant AMPP technical committees or groups that align with your expertise. AMPP Technical Committees
Draft Proposals: Clearly articulate the rationale, objectives, and scope of the proposed improvements in a formal proposal following AMPP guidelines.
Solicit Feedback: Before official submission, share your proposal with peers for feedback to refine and strengthen your recommendations.
Submit Proposal to AMPP: Follow the official process for submitting standards proposals or revisions as outlined by AMPP. Ensure your submission is complete and meets all required criteria.
Participate in Review and Development Process: Be actively involved in the review process, which may include discussions, revisions, and consensus-building activities.
Promote Education and Training: Once improvements are adopted, contribute to the development of related educational and training materials to facilitate widespread understanding and implementation within the industry.
Monitor and Review: After implementation, continue to monitor the effectiveness of the improvements and suggest further revisions as necessary based on new findings or feedback from application in practice.
Improving NACE Standards is a collaborative and ongoing process that requires active participation and engagement from Corrosion Engineers and other stakeholders in the AMPP community. This ensures that standards remain relevant, comprehensive, and effective in addressing the challenges of corrosion control and material protection.
How to Display NACE Standards Skills on Your Resume
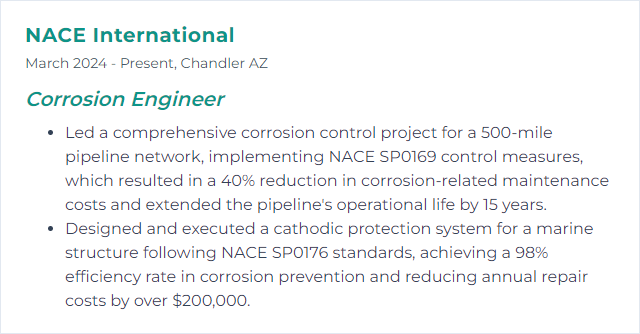
4. Electrochemistry
Electrochemistry is the branch of chemistry that deals with the relationship between electricity and chemical reactions. For a Corrosion Engineer, it specifically focuses on the electrochemical processes that lead to material degradation, such as rusting of metals, and the methods for preventing or controlling such corrosion.
Why It's Important
Electrochemistry is crucial for a Corrosion Engineer because it underpins the mechanisms of corrosion, enabling the prediction, control, and prevention of corrosion processes in metals and alloys, essential for ensuring the longevity and safety of infrastructure and machinery.
How to Improve Electrochemistry Skills
Improving electrochemistry knowledge, especially for a Corrosion Engineer, involves understanding the principles of electrochemical reactions, corrosion mechanisms, and protective strategies. Here's a concise guide:
Strengthen Fundamentals: Grasp the basics of electrochemistry including electrode potentials, Nernst equation, and electrochemical cells. Khan Academy offers concise lessons.
Understand Corrosion Mechanisms: Learn about the different types of corrosion (e.g., galvanic, crevice, pitting) and their electrochemical basis. The NACE International website provides valuable insights.
Corrosion Monitoring and Prevention: Explore techniques for corrosion monitoring, control, and prevention, including cathodic protection, coating technology, and material selection. The Corrosion Doctors portal is a useful resource.
Apply Electrochemical Modeling: Utilize software tools for electrochemical modeling and simulation to predict corrosion behavior and assess protection strategies. COMSOL Multiphysics offers specialized modules.
Continuing Education: Engage in professional development through courses and certifications offered by organizations like NACE International and The Electrochemical Society.
Stay Updated with Research: Keep abreast of the latest research in electrochemistry and corrosion engineering by following journals such as Corrosion Science and Journal of The Electrochemical Society.
Join Professional Forums: Participate in forums and conferences to exchange knowledge with peers. LinkedIn groups dedicated to corrosion engineering and electrochemistry are great for networking.
By combining a solid foundation in electrochemical principles with ongoing education and networking, corrosion engineers can effectively apply their knowledge to mitigate corrosion issues.
How to Display Electrochemistry Skills on Your Resume
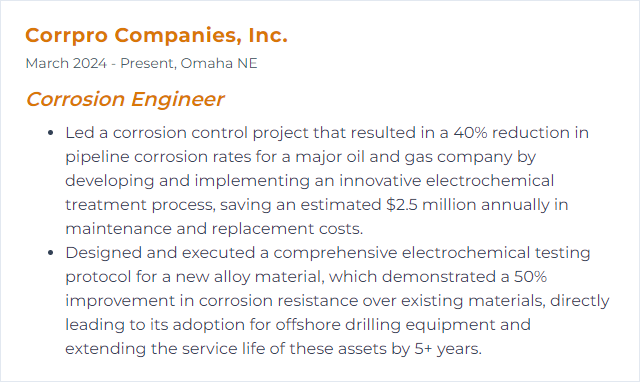
5. Material Selection
Material selection, in the context of a Corrosion Engineer, is the process of choosing materials that are most resistant to corrosion under specific environmental conditions and operational requirements, ensuring longevity, reliability, and cost-effectiveness of equipment and structures.
Why It's Important
Material selection is crucial for a Corrosion Engineer to ensure the longevity, safety, and cost-effectiveness of structures and components by choosing materials that resist corrosion in specific environments, thereby preventing material degradation and failure.
How to Improve Material Selection Skills
Improving material selection, especially in the context of corrosion engineering, involves a systematic approach to ensure long-term durability and cost-effectiveness. Here are concise steps with relevant resources:
Understand the Environment: Knowing the specific corrosive agents (e.g., chemicals, temperature, pressure) your material will be exposed to is crucial. NACE International offers resources on understanding different corrosion environments.
Identify Material Properties: Determine the essential properties needed for your application, such as mechanical strength, corrosion resistance, and thermal stability. The ASM International Materials Database can guide material properties.
Consider Lifecycle Costs: Factor in not just the initial cost but also maintenance, lifespan, and failure risks. The Whole Building Design Guide provides insights into life-cycle cost analysis.
Consult Standards and Guidelines: Use industry standards (e.g., ASTM, ISO) for material selection in corrosive environments. The ASTM International website is a good starting point.
Use Material Selection Software: Utilize specialized software for an in-depth analysis. CES Selector is one example that aids in comparing and selecting materials based on specific criteria.
Collaborate with Suppliers: Engage material suppliers early in the process for insights on the latest materials and technologies.
Test and Validate: Perform corrosion testing (laboratory and field tests) to validate material performance under simulated or actual operating conditions. Corrosion Testing Standards by ASTM provides a comprehensive list of testing methods.
By following these steps and utilizing the resources provided, corrosion engineers can significantly improve material selection for their specific applications.
How to Display Material Selection Skills on Your Resume
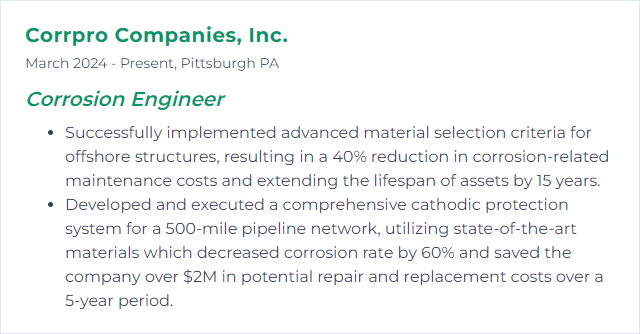
6. Protective Coatings
Protective coatings are specialized barriers applied to surfaces, primarily metals, to prevent or significantly reduce corrosion and degradation caused by environmental exposure, chemicals, or mechanical wear, thus extending the lifespan and maintaining the integrity of the structure or component.
Why It's Important
Protective coatings are crucial for a Corrosion Engineer because they act as a barrier to prevent or slow down the corrosion process, extending the lifespan of materials and structures by safeguarding them against environmental factors such as moisture, chemicals, and salt, thereby ensuring structural integrity and reducing maintenance costs.
How to Improve Protective Coatings Skills
Improving protective coatings for corrosion control involves enhancing their formulation, application, and maintenance strategies. Here are concise strategies for a Corrosion Engineer:
Material Enhancement: Incorporate advanced materials like graphene, nano-coatings, or smart coatings that offer self-healing properties. These materials can significantly increase the durability and effectiveness of coatings (ScienceDirect).
Surface Preparation: Ensure meticulous surface preparation, including cleaning and profiling, to achieve optimal adhesion and coating integrity. This step is critical for the long-term performance of the coating system (SSPC: The Society for Protective Coatings).
Application Technology: Utilize the latest application technologies and techniques, ensuring uniform coverage and thickness. Advanced spraying equipment and robotic applications can enhance the consistency and efficiency of coating applications (Journal of Protective Coatings & Linings).
Environmentally Friendly Alternatives: Develop and use coatings with reduced environmental impact, such as water-based, high-solids, or powder coatings, which also comply with regulatory standards (EPA).
Monitoring and Maintenance: Implement advanced monitoring techniques, like embedded sensors, to track coating performance and detect early signs of degradation. Regular maintenance and inspection schedules should be established to address any issues promptly (NACE International).
Customization: Tailor coatings to specific environmental conditions or service requirements. Understanding the specific challenges, such as chemical exposure or temperature extremes, allows for the development of more effective coating solutions (CoatingsTech Magazine).
By focusing on these strategies, a Corrosion Engineer can significantly improve the performance and lifespan of protective coatings.
How to Display Protective Coatings Skills on Your Resume
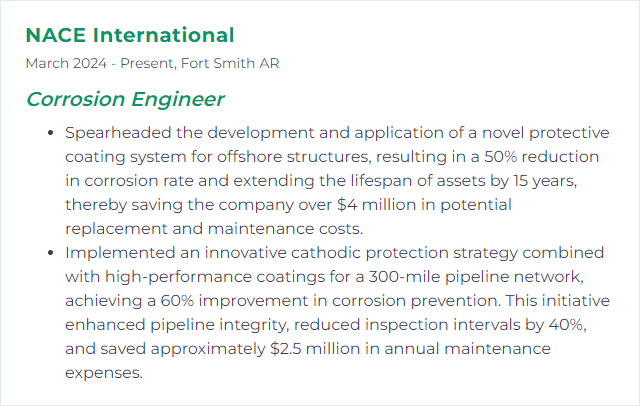
7. Failure Analysis
Failure analysis, in the context of a Corrosion Engineer, is the systematic investigation of materials, components, or structures that have failed due to corrosion, aiming to determine the causes of failure and to prevent future occurrences.
Why It's Important
Failure analysis is crucial for a Corrosion Engineer to identify the root causes of material degradation, prevent future failures, optimize material selection and protective measures, and ensure the safety, reliability, and longevity of structures and components in corrosive environments.
How to Improve Failure Analysis Skills
Improving Failure Analysis as a Corrosion Engineer involves a methodical approach to identifying, understanding, and mitigating corrosion-related failures. Here's a concise guide:
Understand the Basics: Ensure a strong foundation in corrosion principles and mechanisms. The NACE International offers resources and courses on corrosion basics.
Identify the Type of Corrosion: Differentiate between types (e.g., galvanic, pitting, stress corrosion cracking). The Corrosion Doctors website provides insights into various corrosion types.
Gather Comprehensive Data: Collect detailed information about the operating environment, material specifications, and failure history. ASTM's G4-01(2014) Standard Guide offers guidelines for conducting failure analysis.
Use Analytical Tools and Techniques: Employ techniques such as metallography, scanning electron microscopy (SEM), and energy dispersive X-ray spectroscopy (EDS) for microstructural analysis. The Microscopy Society of America provides resources on microscopy techniques.
Mitigation and Prevention Strategies: Develop strategies to prevent future corrosion, including material selection, protective coatings, and cathodic protection. The SSPC: The Society for Protective Coatings offers guidelines on coatings and corrosion protection.
Continual Learning and Certification: Stay updated with the latest technologies and methodologies in corrosion and failure analysis through certifications like the NACE Certified Corrosion Specialist or the ASM International's Certified Materials Professional.
Collaborate and Share Knowledge: Engage with professional communities and forums to share findings and learn from peers. The ASM International Community is a valuable platform for collaboration.
By following these steps, Corrosion Engineers can enhance their failure analysis capabilities, leading to better prevention and mitigation of corrosion-related failures.
How to Display Failure Analysis Skills on Your Resume
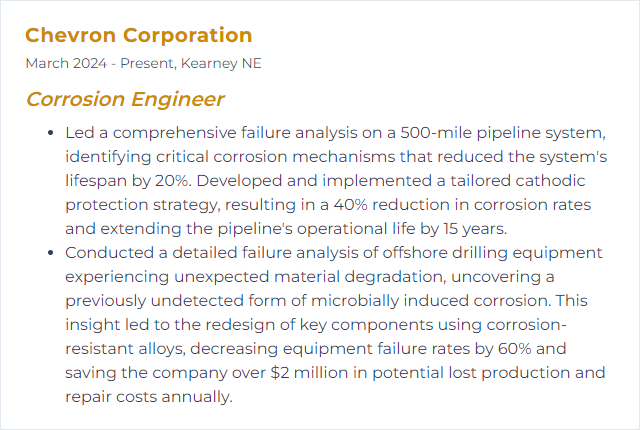
8. Welding Inspection
Welding inspection, in the context of a Corrosion Engineer, is the process of examining welds to ensure they are free from defects and meet the relevant standards for corrosion resistance, integrity, and long-term performance in corrosive environments.
Why It's Important
Welding inspection is crucial for a Corrosion Engineer to ensure the integrity and longevity of welded structures by identifying defects that could lead to premature failure or corrosion, thus preventing potential safety hazards and costly repairs.
How to Improve Welding Inspection Skills
Improving welding inspection, especially from the perspective of a Corrosion Engineer, involves a comprehensive approach that focuses on ensuring the integrity and longevity of welded structures. Here's a concise guide:
Understand Welding Processes: A deep understanding of various welding processes and their susceptibility to corrosion is crucial. Familiarize yourself with AWS Welding Processes.
Enhance Inspection Skills: Invest in advanced training and certification for welding inspection techniques, such as those offered by ASNT or AWS.
Utilize Advanced NDT Techniques: Incorporate advanced Non-Destructive Testing (NDT) methods that are sensitive to corrosion defects, such as Phased Array Ultrasonic Testing (PAUT) and Eddy Current Testing. Find more details at NDT Resource Center.
Apply Corrosion Monitoring Tools: Use corrosion monitoring tools and techniques, such as corrosion coupons and electronic probes, to assess the welded area's susceptibility to corrosion. Explore options at NACE International.
Implement Corrosion Mitigation Strategies: Design and implement corrosion mitigation strategies, such as protective coatings and cathodic protection, in welding specifications. Resources available at SSPC can be very helpful.
Regular Inspection and Maintenance: Establish a schedule for regular inspection and maintenance of welded structures to identify and address corrosion issues promptly. Guidelines can be found within ISO standards available through ISO.
By focusing on these areas, Corrosion Engineers can significantly improve the quality and reliability of welding inspections, leading to safer, longer-lasting structures.
How to Display Welding Inspection Skills on Your Resume
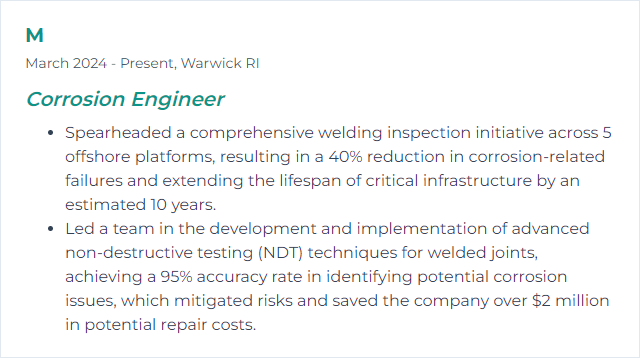
9. API Standards
API Standards are guidelines developed by the American Petroleum Institute that establish recommended practices, technical specifications, and procedures for the design, operation, and maintenance of equipment and facilities in the oil and gas industry, to ensure safety, efficiency, and reliability. For a Corrosion Engineer, these standards include protocols for managing corrosion, material selection, inspection, and mitigation in pipelines, storage tanks, and other infrastructure to prevent failures and extend asset life.
Why It's Important
API (American Petroleum Institute) standards are crucial for corrosion engineers because they provide industry-validated guidelines for designing, maintaining, and operating equipment and facilities safely and efficiently, minimizing corrosion-related failures, ensuring structural integrity, and protecting the environment.
How to Improve API Standards Skills
Improving API standards, particularly from a Corrosion Engineer's perspective, involves a focused approach on enhancing reliability, safety, and efficiency in materials and methods used to prevent, monitor, and manage corrosion. Here’s a concise guide:
Engage in Continuous Learning: Stay updated with the latest advancements in corrosion technology and materials science. Participating in forums like NACE International can provide valuable insights.
Contribute to Research and Development: Actively engage in R&D to discover new materials, coatings, and corrosion protection techniques. Sharing findings in journals such as Corrosion Journal can influence API standards.
Collaborate with Industry Experts: Working alongside experienced professionals through platforms like API (American Petroleum Institute) helps in understanding practical challenges and solutions, which can be standardized for broader implementation.
Participate in API Committees: Direct involvement in API standard development committees ensures that your expertise contributes to shaping effective and practical standards. Check API's page on Participating in the Standards Process for more information.
Implement and Provide Feedback: Apply the latest API standards in your projects and provide constructive feedback based on real-world applications. This continuous feedback loop is essential for the iterative improvement of standards.
Focus on Sustainability and Environment: Ensure that corrosion protection methods are environmentally sustainable. This not only enhances API standards but also aligns with global environmental protection goals.
Utilize Advanced Technology: Leverage technology such as AI and IoT for corrosion monitoring and prediction. Innovations in these areas can significantly influence the development of more effective standards.
By following these steps and actively engaging with the corrosion engineering community, you can contribute significantly to the enhancement of API standards.
How to Display API Standards Skills on Your Resume
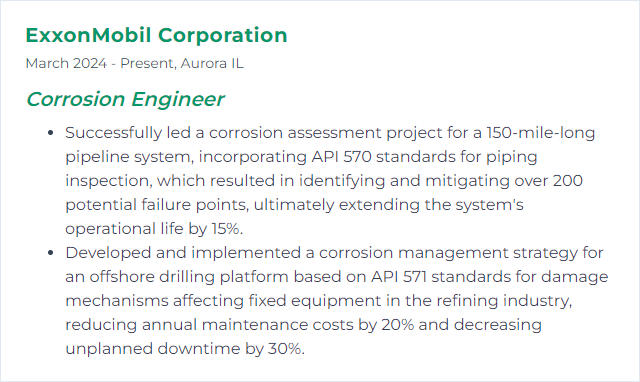
10. Corrosion Inhibitors
Corrosion inhibitors are chemicals added to a medium (such as water, oil, or gas) to significantly decrease the rate of corrosion on metals or alloys within the system. They work by forming a protective film on the surface, altering the corrosive environment, or by scavenging corrosive agents. Their selection and application are critical aspects of corrosion control and management strategies in various industries.
Why It's Important
Corrosion inhibitors are crucial for a Corrosion Engineer because they significantly reduce the rate of metal degradation, extend the lifespan of materials and structures, minimize maintenance costs, and ensure safety and reliability in various industrial applications.
How to Improve Corrosion Inhibitors Skills
Improving corrosion inhibitors involves enhancing their efficiency, specificity, adaptability, and environmental friendliness. Here’s a concise guide:
Selection of Inhibitors: Choose inhibitors based on the metal type, corrosive medium, and operational conditions. Opt for inhibitors with high thermodynamic stability and specific adsorption properties. Corrosion Inhibitors - Principles, Mechanisms and Applications provides insights into selecting appropriate inhibitors.
Synergistic Combinations: Utilize synergistic mixtures of inhibitors to achieve better protection at lower concentrations. Combining organic and inorganic inhibitors can offer enhanced protection. The study on Synergism in Corrosion Inhibition discusses the effectiveness of such combinations.
Environmental Considerations: Develop or select environmentally friendly inhibitors, such as green inhibitors derived from plant extracts, to reduce ecological impact. The article on Green Corrosion Inhibitors provides insights into sustainable options.
Advanced Formulations: Incorporate smart release systems that respond to changes in pH, temperature, or corrosion rate, ensuring targeted delivery of the inhibitor. Research on Smart Coatings for Corrosion Protection offers information on innovative coating technologies.
Monitoring and Optimization: Implement continuous monitoring and feedback loops using corrosion sensors and IoT technology to optimize inhibitor dosage and distribution in real-time. The study Corrosion Monitoring in Industrial Plants Using Nondestructive Testing and Electrochemical Methods highlights modern monitoring techniques.
Research and Development: Stay informed about the latest developments in corrosion science, including novel inhibitor compounds and advanced application methods, by regularly consulting academic journals and industry publications.
By focusing on these strategies, corrosion engineers can enhance the performance of corrosion inhibitors, ensuring long-lasting protection against corrosive damage in a variety of industrial applications.
How to Display Corrosion Inhibitors Skills on Your Resume
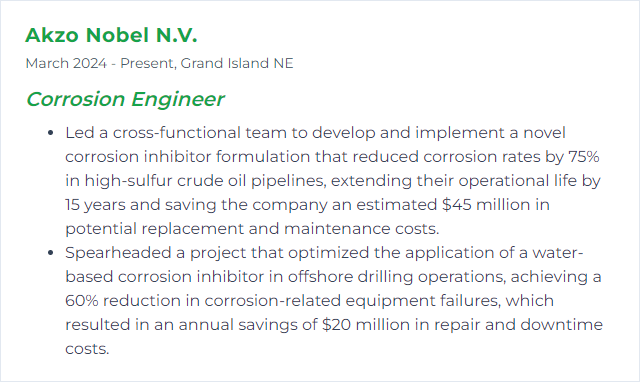
11. Risk Assessment
Risk assessment, in the context of a Corrosion Engineer, is the systematic process of identifying, analyzing, and evaluating the likelihood and potential impact of corrosion-related failures on infrastructure, materials, or equipment, to prioritize mitigation strategies and ensure safety, reliability, and longevity.
Why It's Important
Risk assessment is crucial for a Corrosion Engineer to identify and evaluate potential threats to materials and structures from corrosion, enabling the development of targeted strategies to mitigate these risks, ensure safety, prolong asset life, and optimize maintenance and repair costs.
How to Improve Risk Assessment Skills
Improving risk assessment, especially for a Corrosion Engineer, involves a multifaceted approach focusing on the latest methodologies, technologies, and industry best practices. Here's a concise guide:
Stay Updated with Standards: Regularly consult industry standards related to corrosion control and risk management, such as those from NACE International and API.
Leverage Technology: Utilize advanced corrosion modeling and prediction tools. Software like Cortek offers insights into potential corrosion issues before they escalate.
Risk-Based Inspection (RBI): Implement an RBI approach by integrating it into your maintenance strategies. Tools and frameworks from API RP 580 provide guidelines for establishing an RBI program.
Material Selection and Design: Optimize material selection and component design to mitigate corrosion risks. Resources like ASM International offer extensive material data and design guidelines.
Continual Learning: Engage in continual professional development through platforms like Coursera and edX, which offer courses on corrosion, material science, and risk assessment.
Networking and Collaboration: Join professional networks and forums (e.g., LinkedIn groups related to corrosion engineering) to share knowledge and stay informed on emerging risks and solutions.
Regulatory Compliance: Ensure adherence to local, national, and international regulations related to corrosion control and safety. Government websites and ISO provide relevant legal and regulatory information.
Field Data Analysis: Regularly analyze corrosion data from inspections and monitoring systems to identify trends and potential risk areas. Tools like Tableau can aid in visualizing and interpreting data effectively.
By integrating these steps, Corrosion Engineers can enhance their risk assessment processes, leading to more effective corrosion management and mitigation strategies.
How to Display Risk Assessment Skills on Your Resume
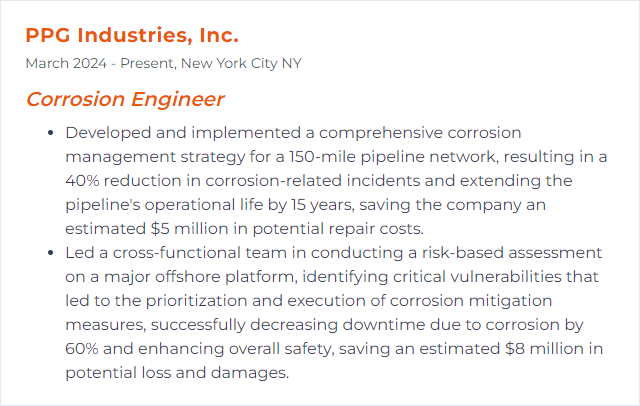
12. Pipeline Integrity
Pipeline integrity, in the context of a Corrosion Engineer, refers to the practice of ensuring a pipeline system's structural soundness and operational reliability by monitoring, preventing, and managing corrosion and other degradation mechanisms to prevent leaks, ruptures, and failures.
Why It's Important
Pipeline integrity is crucial to ensure the safe, reliable, and efficient transportation of fluids without leaks or ruptures, minimizing the risk of environmental harm, operational disruptions, and potential catastrophic failures, thereby safeguarding public safety and protecting assets. For a Corrosion Engineer, maintaining pipeline integrity is essential to prevent material degradation and extend the lifespan of pipeline infrastructure.
How to Improve Pipeline Integrity Skills
Improving pipeline integrity, particularly from a corrosion engineer's perspective, involves a multi-faceted approach focusing on prevention, detection, and remediation of corrosion. Here's a concise guide:
Prevention: Apply protective coatings and cathodic protection to shield pipelines from corrosive environments. Implementing corrosion inhibitors can also be effective. NACE International provides comprehensive resources on materials and protection methods.
Detection: Utilize smart pigging and non-destructive testing (NDT) techniques to detect and assess corrosion. Methods like ultrasonic testing (UT) and magnetic flux leakage (MFL) are commonly used. The American Society for Nondestructive Testing offers insights into NDT techniques.
Monitoring: Continuously monitor pipeline conditions using corrosion monitoring tools, such as electrical resistance probes and linear polarization resistance sensors, to identify corrosive activity early. Corrosionpedia is a useful resource for understanding these technologies.
Data Analysis and Management: Employ corrosion data management systems to analyze data collected from monitoring and inspections, enabling predictive maintenance and timely interventions. Resources like Pipeline & Gas Journal provide insights into the latest technologies and practices.
Regulatory Compliance and Standards: Adhere to industry standards and regulations, such as those from API and ASTM International, to ensure the integrity and safety of pipeline operations.
By integrating these strategies, corrosion engineers can significantly enhance the integrity of pipelines, ensuring their safe and efficient operation.
How to Display Pipeline Integrity Skills on Your Resume
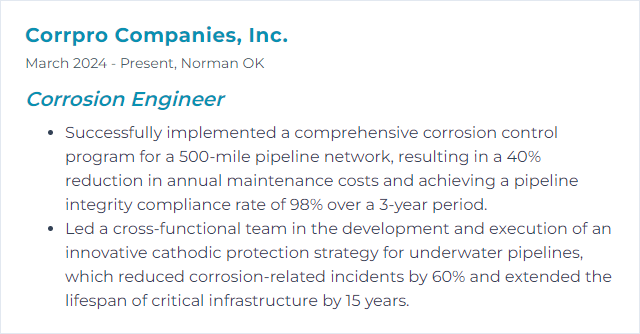