Top 12 Welding Engineer Skills to Put on Your Resume
In today's competitive job market, welding engineers must highlight a robust set of technical and soft skills on their resumes to stand out to potential employers. This article explores the top 12 skills that welding engineers should showcase to demonstrate their proficiency and adaptability in the field, ensuring they capture the attention of hiring managers.
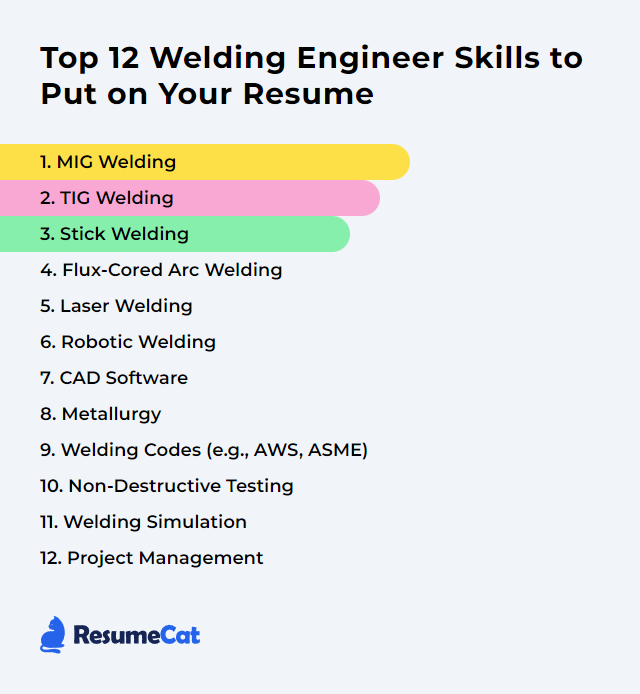
Welding Engineer Skills
- MIG Welding
- TIG Welding
- Stick Welding
- Flux-Cored Arc Welding
- Laser Welding
- Robotic Welding
- CAD Software
- Metallurgy
- Welding Codes (e.g., AWS, ASME)
- Non-Destructive Testing
- Welding Simulation
- Project Management
1. MIG Welding
MIG Welding, or Metal Inert Gas Welding, is a semi-automatic or automatic arc welding process using a continuous, consumable wire electrode and a shielding gas to protect the weld pool from atmospheric contamination.
Why It's Important
MIG welding is crucial for a Welding Engineer due to its versatility in welding various metals, high productivity rates, and ability to produce clean, high-quality welds with minimal post-weld cleanup, optimizing both efficiency and cost-effectiveness in manufacturing and fabrication processes.
How to Improve MIG Welding Skills
Improving MIG welding involves optimizing various parameters and techniques to enhance weld quality, efficiency, and safety. For a Welding Engineer, focusing on the following areas can lead to significant improvements:
Equipment Maintenance: Regularly check and maintain welding equipment, including the gun, wire feeder, and cables, to ensure optimal performance. Lincoln Electric offers a comprehensive maintenance checklist.
Proper Parameter Settings: Adjust voltage, amperage, and wire feed speed according to material thickness and type. MillerWelds provides guidelines on parameter settings.
Use Correct Gas and Material: Select the appropriate shielding gas and welding wire material for the job. Argon and CO2 blends are common, but choices vary based on the application. Hobart Brothers offers insights on material and gas selection.
Optimize Welding Technique: Focus on gun angle, welding direction, and travel speed. Consistency in technique improves overall weld quality. The American Welding Society provides tips on improving MIG welding techniques.
Control Spatter: Reduce spatter to improve weld appearance and reduce cleanup time by fine-tuning parameters and using anti-spatter agents. Welding Answers offers strategies for spatter reduction.
Proper Training and Practice: Continuous education and practice are crucial. Engage in training programs and stay updated with the latest welding technologies and methodologies. The Fabricator emphasizes the importance of good welding techniques and ongoing learning.
By focusing on these areas, a Welding Engineer can significantly improve MIG welding processes, resulting in higher quality welds, increased productivity, and enhanced safety.
How to Display MIG Welding Skills on Your Resume
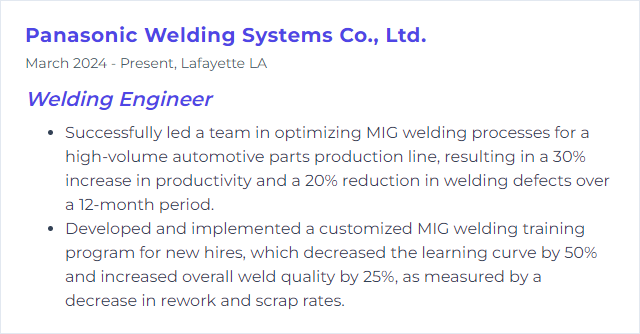
2. TIG Welding
TIG welding, short for Tungsten Inert Gas welding, is a precision arc welding process that uses a non-consumable tungsten electrode to produce the weld. It is characterized by the use of an inert shielding gas, typically argon or helium, to protect the weld area from contamination. This process allows for strong, high-quality welds on a variety of metals, including thin materials and alloys.
Why It's Important
TIG welding is important for a Welding Engineer due to its ability to produce high-quality, precise welds on a variety of metals, including thin materials and alloys. It offers excellent control over the welding process, enabling the creation of strong, clean welds with minimal distortion and no spatter, essential for critical applications in aerospace, automotive, and fabrication industries.
How to Improve TIG Welding Skills
To improve TIG welding, a Welding Engineer can focus on several key areas:
Equipment Check: Ensure the welding machine and accessories (like the torch, gas lens, and tungsten electrode) are appropriate for the job and in good condition. Miller Welds provides a comprehensive guide on equipment selection and maintenance.
Material Preparation: Clean the base materials and tungsten electrode properly to avoid contamination. Use a dedicated stainless steel brush for cleaning and ensure surfaces are free from oils or debris. Hobart Brothers offers tips for effective material preparation.
Shielding Gas Selection: Use the correct type and mixture of shielding gas. Argon is commonly used, but mixtures with helium or hydrogen can be beneficial for specific applications. Lincoln Electric discusses the impact of shielding gas choices.
Welding Technique: Focus on torch angle, welding speed, and filler material feed. Keeping a consistent angle and speed improves weld quality. Practice and refine your technique consistently. Welding Tips and Tricks provides insights into effective TIG welding techniques.
Parameter Optimization: Adjust and optimize welding parameters such as current type (AC/DC), amperage, and pulse settings based on the material and thickness. This American Welding Society (AWS) resource guides on parameter adjustments.
Post-Weld Treatment: Consider post-weld treatments like stress relieving or annealing for certain materials to improve weld strength and reduce residual stresses. TWI Global offers insights into post-weld heat treatment.
By focusing on these areas and continually practicing and adjusting based on results, a Welding Engineer can significantly improve TIG welding quality and efficiency.
How to Display TIG Welding Skills on Your Resume
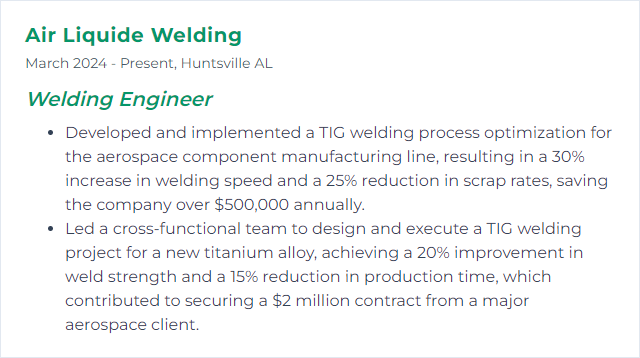
3. Stick Welding
Stick welding, also known as Shielded Metal Arc Welding (SMAW), is a manual arc welding process that uses a consumable electrode coated in flux to lay the weld. This process is versatile and simple, suitable for welding most alloys and joints, and capable of indoor and outdoor operation.
Why It's Important
Stick welding (Shielded Metal Arc Welding - SMAW) is crucial for a Welding Engineer due to its versatility in welding various materials and thicknesses, its efficacy in outdoor and challenging environments, and its simplicity and cost-effectiveness, making it indispensable for repair, construction, and maintenance projects.
How to Improve Stick Welding Skills
To improve stick welding, focus on these key aspects:
Electrode Selection: Choose the right electrode for your workpiece material and welding position. American Welding Society (AWS) provides guidelines on electrode types and applications.
Machine Settings: Adjust the current setting based on electrode size and material thickness. Consult the Lincoln Electric Weld Parameter Guide for specific recommendations.
Technique: Maintain a consistent arc length, usually not more than the electrode diameter. Angle the electrode appropriately; 10-15 degrees in the direction of travel for flat welds. Miller Welds Technique Tips offer practical advice for improving your technique.
Preparation and Cleaning: Ensure surfaces are clean and free of contaminants. Proper joint preparation can significantly impact weld quality. Hobart Institute of Welding Technology provides resources on preparation techniques.
Practice: Consistent practice on scrap material can refine your skills. Experiment with different electrodes, settings, and techniques.
Safety: Always prioritize safety by wearing appropriate personal protective equipment and following safety guidelines from OSHA.
By focusing on these areas, you can significantly improve your stick welding quality and efficiency.
How to Display Stick Welding Skills on Your Resume
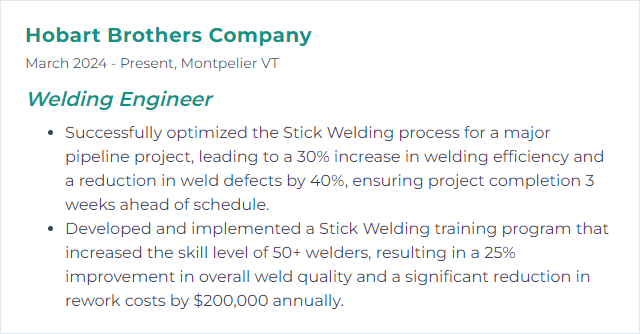
4. Flux-Cored Arc Welding
Flux-Cored Arc Welding (FCAW) is a semi-automatic or automatic arc welding process using a continuously fed consumable tubular electrode filled with a flux. It is used for high-speed welding applications, offering deep penetration and a high deposition rate with the capability of welding in all positions. FCAW can be performed with or without shielding gas, depending on the flux composition.
Why It's Important
Flux-Cored Arc Welding (FCAW) is important for a Welding Engineer because it offers high welding speed, excellent penetration, and versatility in welding various materials, including thick and out-of-position workpieces, while also providing enhanced weld quality through slag protection that reduces porosity and inclusion defects.
How to Improve Flux-Cored Arc Welding Skills
To improve Flux-Cored Arc Welding (FCAW), a Welding Engineer can focus on the following areas:
Material Selection: Choose the appropriate flux-cored wire based on the material being welded and the desired mechanical properties. Lincoln Electric provides a guide on selecting the right wire.
Equipment Optimization: Ensure welding equipment is properly maintained and settings (voltage, amperage, wire feed speed) are optimized for the specific welding task. MillerWelds offers tips on equipment settings and maintenance.
Technique Refinement: Practice and refine welding techniques, such as travel speed, angle, and gun movement. The American Welding Society (AWS) offers educational resources for technique improvement.
Environment Control: Minimize external factors that can affect welding quality, such as wind, moisture, and temperature. Controlling the environment can be crucial for FCAW, especially for outdoor operations.
Quality Assurance: Implement regular testing and inspection protocols to identify and address issues promptly. The Fabricator provides insights into QA practices for FCAW.
Focusing on these areas can lead to significant improvements in FCAW outcomes.
How to Display Flux-Cored Arc Welding Skills on Your Resume
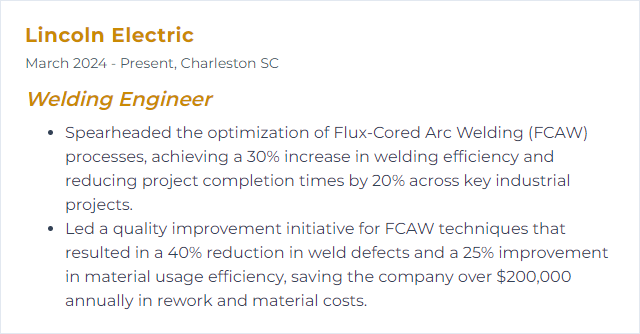
5. Laser Welding
Laser welding is a fusion welding process that uses a highly focused laser beam as the heat source to melt and join materials together. It offers high precision, speed, and minimal heat input, making it suitable for joining thin materials, complex assemblies, and high-strength, temperature-sensitive components.
Why It's Important
Laser welding is crucial for a Welding Engineer due to its high precision, efficiency, and versatility in joining a wide range of materials with minimal heat input, resulting in superior weld quality, reduced distortion, and enhanced productivity in manufacturing processes.
How to Improve Laser Welding Skills
Improving laser welding involves optimizing process parameters, equipment, and material handling to enhance weld quality, efficiency, and application versatility. Here are concise strategies:
Optimize Process Parameters: Adjust laser power, welding speed, and focal position to achieve the desired weld depth and width. Utilize process monitoring to ensure consistent quality.
Material Preparation: Ensure surfaces are clean and properly aligned. Use appropriate joint design to facilitate better weld penetration and strength.
Choose the Right Laser Type: Select between fiber, CO2, or Nd:YAG lasers based on material and application. Each type offers different benefits in terms of wavelength, efficiency, and penetration capabilities.
Employ Advanced Techniques: Techniques like beam shaping and modulation can improve weld quality by controlling heat input and mitigating defects.
Use Filler Material Wisely: For certain applications, adding filler material can improve weld properties. Select a compatible filler and use it judiciously to avoid excessive heat input.
Implement Process Control and Automation: Use advanced sensors and control systems to monitor and adjust the welding process in real-time, improving consistency and reducing defects.
Post-Weld Treatment: Consider post-weld heat treatment or mechanical finishing to improve weld appearance and mechanical properties.
Training and Skill Development: Continuous training for operators on the latest laser welding technologies and best practices is crucial.
By focusing on these areas, welding engineers can significantly improve laser welding operations, leading to better quality, higher efficiency, and expanded application capabilities.
How to Display Laser Welding Skills on Your Resume
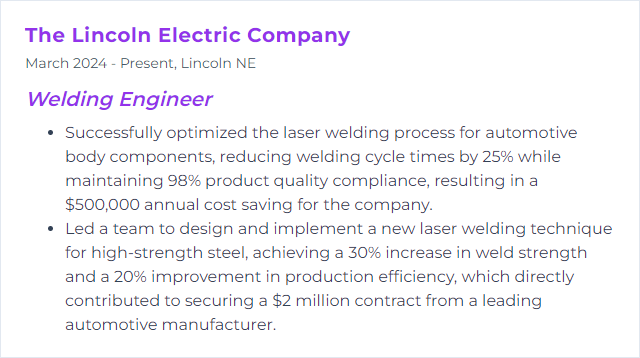
6. Robotic Welding
Robotic welding is an automated process that utilizes programmable robot arms to perform welding tasks, ensuring high precision, repeatability, and efficiency in welding operations. It significantly reduces manual intervention, enhancing productivity and quality in manufacturing environments.
Why It's Important
Robotic welding is crucial for a Welding Engineer as it enhances precision, increases productivity, and ensures consistent quality, while also reducing labor costs and improving workplace safety.
How to Improve Robotic Welding Skills
Improving robotic welding involves enhancing precision, efficiency, and quality while minimizing costs and downtime. Here are key strategies for a Welding Engineer:
Optimize Programming: Utilize advanced software tools for precise programming and simulation to ensure optimal welding paths and parameters. Robotmaster and Octopuz offer solutions tailored to robotic welding.
Regular Maintenance: Implement a strict maintenance schedule to prevent breakdowns and ensure consistent welding quality. Lincoln Electric provides guidelines for maintaining welding equipment.
Quality Control: Employ real-time monitoring and quality control systems to detect and correct defects immediately. Servo-Robot offers advanced laser vision systems for welding inspection and monitoring.
Employee Training: Continuously train operators and technicians on the latest robotic welding technologies and techniques. AWS (American Welding Society) provides certification and training resources.
Material Preparation: Ensure consistent and precise preparation of materials to be welded to reduce variability and improve weld quality.
Invest in Technology Upgrades: Stay abreast of technological advancements in robotic arms, sensors, and welding equipment to enhance capabilities and efficiency.
By focusing on these strategies, a Welding Engineer can significantly improve the performance and outcomes of robotic welding operations.
How to Display Robotic Welding Skills on Your Resume
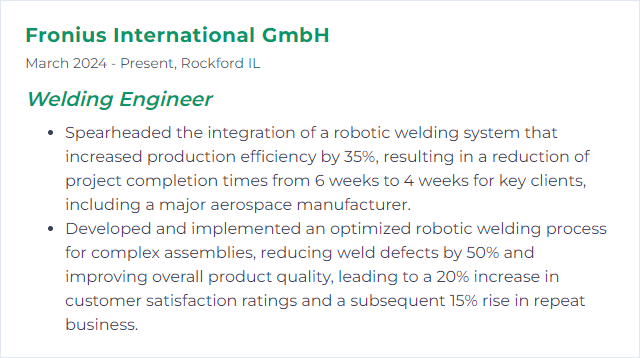
7. CAD Software
CAD software, short for Computer-Aided Design software, is a tool used by welding engineers to create, modify, and analyze precise 2D or 3D designs and models of welding joints and metal fabrications, facilitating accurate planning, simulation, and execution of welding projects.
Why It's Important
CAD software is crucial for a Welding Engineer as it facilitates precise design and simulation of weldments, allowing for optimization of joints, material usage, and welding processes before physical execution, thereby enhancing efficiency, safety, and quality control in fabrication projects.
How to Improve CAD Software Skills
To improve CAD software for a Welding Engineer:
Integrate welding simulation tools: Incorporate simulation tools that predict weld quality, distortion, and stress. Welding Simulation Software by ESI Group offers insights into how welds will perform, which can be integrated into CAD.
Enhance material database: Include a comprehensive and updatable material database specific to welding, including properties of filler materials. MatWeb provides a searchable database of material properties that can be integrated.
Customizable welding symbols and annotations: Implement an extensive library of industry-standard welding symbols and allow for custom annotations for better communication. AWS A2.4:2020 provides standards that can be integrated into the software.
Real-time collaboration tools: Enable real-time collaboration features for teams to work on projects simultaneously. Autodesk BIM 360 is an example of software with collaboration tools that could inspire CAD software improvements.
User-friendly interface: Streamline the interface to make it more intuitive for welding engineers, focusing on workflow efficiency and reducing the learning curve. SketchUp is known for its user-friendly interface, offering lessons for CAD software design.
Mobile compatibility: Ensure the software is compatible with mobile devices for on-the-go access to projects and drawings. Onshape offers full CAD functionality on mobile devices, serving as a model for mobile compatibility.
Compliance and standards integration: Automatically update the software with the latest welding standards and regulations to ensure compliance. ISO and AWS standards can be integrated for reference.
Enhanced visualization and VR support: Integrate advanced visualization tools and VR support to help engineers better visualize the weldment in the context of the entire assembly. Unity provides tools that can be adapted for immersive CAD experiences.
By focusing on these improvements, CAD software can be significantly enhanced to meet the specific needs of welding engineers, leading to more efficient design processes and higher-quality welds.
How to Display CAD Software Skills on Your Resume
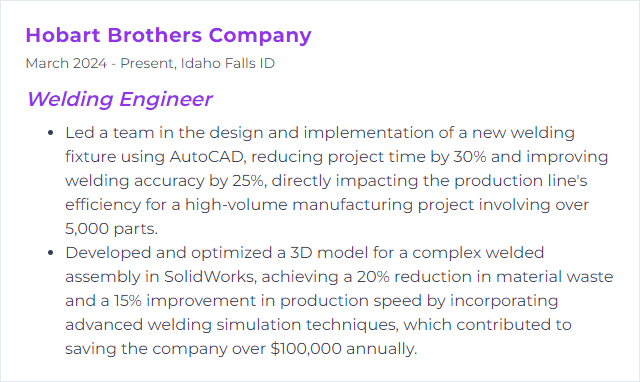
8. Metallurgy
Metallurgy is the science and technology of metals and alloys, focusing on their extraction, characterization, processing, and development for use, including welding applications. It encompasses studying metal properties, behaviors under various conditions, and techniques to join and enhance materials for engineering purposes.
Why It's Important
Metallurgy is crucial for a Welding Engineer because it enables the understanding of metal properties, behaviors, and interactions at different temperatures, ensuring the selection of appropriate materials and welding techniques for strong, reliable, and defect-free joints in constructions and products.
How to Improve Metallurgy Skills
To improve metallurgy as a Welding Engineer, focus on the following strategies:
Stay Updated on Advances: Regularly read industry publications and journals like Materials Science and Technology to keep abreast of the latest developments in materials science and welding technologies.
Material Selection: Optimize material selection by understanding the properties and behaviors of different metals. The ASM International website is a valuable resource for material properties and selection criteria.
Process Optimization: Continuously refine welding processes for efficiency and quality. The American Welding Society (AWS) offers guidelines and standards that can help in optimizing welding techniques and processes.
Post-Weld Treatment: Implement appropriate post-weld heat treatments (PWHT) to enhance the properties of the weldment. Resources like ScienceDirect provide access to studies and articles on effective PWHT practices.
Welding Simulation Software: Utilize advanced simulation software to predict and improve weld quality and performance. Websites like TWI Global offer insights into the latest software tools and methodologies.
Professional Development: Engage in continuous learning and certification programs offered by professional bodies like the AWS to stay current with the evolving field.
By focusing on these areas, a Welding Engineer can significantly improve metallurgy in their projects, ensuring higher quality, efficiency, and innovation in welding practices.
How to Display Metallurgy Skills on Your Resume
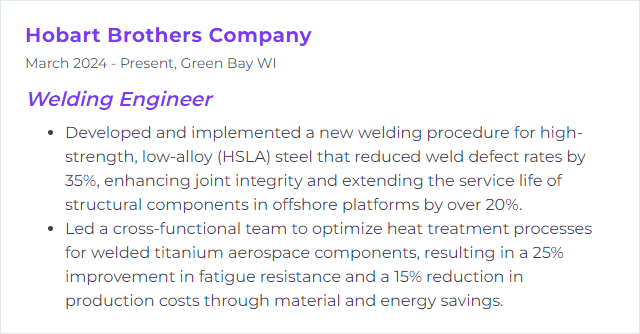
9. Welding Codes (e.g., AWS, ASME)
Welding codes, such as those from the American Welding Society (AWS) and the American Society of Mechanical Engineers (ASME), are standardized guidelines that specify the rules, requirements, and best practices for welding processes and weldments. These codes ensure the quality, safety, and performance of welded structures and components, serving as a critical reference for welding engineers in designing, fabricating, and inspecting welded joints and structures.
Why It's Important
Welding codes, such as AWS (American Welding Society) and ASME (American Society of Mechanical Engineers), are crucial for Welding Engineers because they ensure the safety, reliability, and quality of welding processes and structures. These codes provide standardized guidelines and best practices for welding procedures, materials, and testing, facilitating the production of safe and dependable welded products and constructions.
How to Improve Welding Codes (e.g., AWS, ASME) Skills
Improving welding codes, such as those from the American Welding Society (AWS) and the American Society of Mechanical Engineers (ASME), involves a continuous process of review, feedback, and revision to reflect technological advancements, industry needs, and safety practices. Here's a concise guide for a Welding Engineer:
Stay Informed: Regularly review the latest editions and amendments of AWS and ASME codes. Understanding current guidelines is crucial for identifying areas that need updates or clarifications.
Engage with Professional Bodies: Participate in AWS and ASME committee meetings or forums. These are platforms where professionals discuss code modifications, challenges, and innovations. Your practical insights can drive changes.
Provide Feedback: Both AWS and ASME encourage feedback from industry professionals. Submit proposals or comments on specific code clauses that you believe need improvement based on your experience or new industry trends.
Contribute to Research: Engage in or support welding research that addresses gaps in current codes. Publishing your findings in reputable journals or presenting at conferences can highlight the need for code revisions.
Educate and Train: Offer training sessions or workshops based on the latest codes. This helps in identifying common misunderstandings or areas where the codes may not be clear, which you can then feedback to the code committees.
Collaborate on Standards Development: Join standards development organizations (SDOs) or technical committees related to welding. This direct involvement allows you to contribute to the drafting and revision of codes.
Utilize Digital Platforms: Leverage digital platforms and social media to share knowledge, discuss code improvements, and gather broader community support for proposed changes.
Advocate for International Harmonization: Work towards harmonizing AWS and ASME standards with international standards (e.g., ISO) to facilitate global trade and safety. This involves understanding ISO standards related to welding and proposing changes that align AWS/ASME codes more closely with international practices.
By actively participating in the development and revision process of welding codes, Welding Engineers can help ensure these standards remain relevant, practical, and reflective of the latest technological and safety advancements.
How to Display Welding Codes (e.g., AWS, ASME) Skills on Your Resume
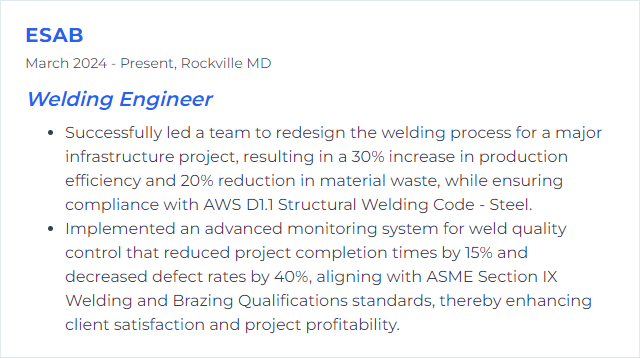
10. Non-Destructive Testing
Non-Destructive Testing (NDT) is a range of analysis techniques used in science and industry to evaluate the properties of a material, component, or system without causing damage. For a Welding Engineer, NDT is crucial for ensuring the integrity and safety of welds without compromising the material's usability, allowing for the detection of defects or discontinuities within the welded joints.
Why It's Important
Non-Destructive Testing (NDT) is crucial for a Welding Engineer as it ensures the integrity and safety of welds without damaging components, enabling early detection of defects, reducing costs, and preventing failures in service.
How to Improve Non-Destructive Testing Skills
Improving Non-Destructive Testing (NDT) techniques for a Welding Engineer involves enhancing accuracy, detection capabilities, and efficiency. Here's a concise guide:
Invest in Advanced Equipment: Utilize the latest NDT technologies such as Phased Array Ultrasonic Testing (PAUT) and Digital Radiography (DR) for better flaw detection and characterization. ASNT's guide on emerging NDT technologies can be a valuable resource.
Regular Training and Certification: Ensure NDT operators are up-to-date with the latest standards and techniques through continuous education and certification. Programs offered by the American Welding Society (AWS) and ASNT are excellent for professional development.
Implement Automation where Possible: Automated NDT methods can increase inspection speed and consistency. Explore options like Automated Ultrasonic Testing (AUT) for weld inspections. The International Institute of Welding (IIW) provides insights into automation in welding and NDT.
Adopt a Multi-technique Approach: No single NDT method is foolproof. Combining techniques (e.g., ultrasonic testing with radiographic testing) can provide more comprehensive inspection results. The Welding Institute (TWI) offers case studies and articles on integrated approaches.
Quality Control and Peer Review: Implement strict quality control protocols and peer reviews of NDT data to ensure accuracy and reliability. Guidelines can be found in AWS and ISO standards.
Leverage Data Analysis Tools: Use software and data analytics to interpret NDT results more effectively, identifying trends and predictive maintenance opportunities. NDT.net is an excellent resource for the latest software and analysis techniques.
By focusing on these areas, a Welding Engineer can significantly improve the effectiveness and efficiency of NDT processes.
How to Display Non-Destructive Testing Skills on Your Resume
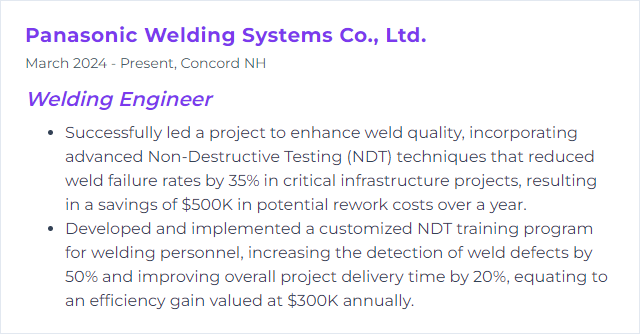
11. Welding Simulation
Welding Simulation is a computational tool used by welding engineers to model and predict the outcomes of welding processes. It encompasses thermal, metallurgical, and mechanical aspects to assess weld quality, distortions, residual stresses, and material properties before actual welding, enabling optimization and troubleshooting of welding procedures.
Why It's Important
Welding simulation is crucial for a Welding Engineer because it enables the prediction and analysis of the thermal, mechanical, and microstructural outcomes of welding processes before actual execution. This aids in optimizing welding parameters, reducing trial and error, minimizing defects, and ensuring structural integrity and performance of the welded components, ultimately saving time and resources.
How to Improve Welding Simulation Skills
Improving welding simulation involves enhancing accuracy, efficiency, and the predictive capability of the simulation models. Here's a very short and concise guide for a Welding Engineer:
Use Advanced Software: Opt for advanced welding simulation software like Simufact Welding or Sysweld that offer detailed models for various welding processes.
Material Characterization: Accurately characterize material properties at high temperatures. Utilize databases such as MatWeb for sourcing material properties.
Mesh Refinement: Implement mesh refinement in areas of high thermal gradients to enhance the accuracy of thermal and mechanical predictions. Software like ANSYS provides advanced meshing tools.
Heat Source Models: Use appropriate heat source models (e.g., Goldak’s double ellipsoid model) that closely mimic the actual welding process. This is crucial for accurate thermal profiles.
Calibration and Validation: Regularly calibrate your simulation model with experimental data. This includes adjusting heat input, thermal boundary conditions, and material properties to match actual weldments.
Incorporate Microstructural Models: For predictions on weld quality and properties, integrate microstructural models. Tools like Thermo-Calc can predict phase transformations.
High-Performance Computing (HPC): Utilize HPC resources to reduce simulation time for complex and large models. Cloud HPC solutions like Rescale can offer scalable computing power.
Continuous Learning: Stay updated with the latest research and advancements in welding simulation by following journals like Science and Technology of Welding and Joining.
By following these steps and leveraging advanced tools, Welding Engineers can significantly improve the outcomes of welding simulations, leading to more accurate, reliable, and efficient fabrication processes.
How to Display Welding Simulation Skills on Your Resume
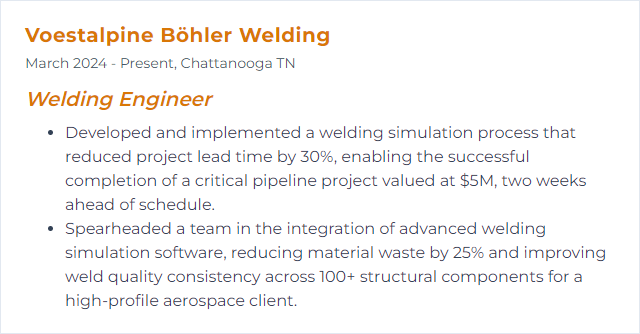
12. Project Management
Project Management, in the context of a Welding Engineer, involves planning, executing, and overseeing welding projects to ensure they are completed on time, within budget, and to the specified quality standards. This includes coordinating team efforts, managing resources, and communicating with stakeholders throughout the project lifecycle.
Why It's Important
Project management is crucial for a Welding Engineer because it ensures that welding projects are completed on time, within budget, and to the required quality standards, while effectively managing resources, coordinating teams, and mitigating risks.
How to Improve Project Management Skills
Improving project management, especially for a Welding Engineer, involves a blend of technical knowledge, organizational skills, and effective communication. Here are concise steps with relevant links:
Enhance Technical Skills: Stay updated with the latest welding technologies and project management software. AWS (American Welding Society) is a great resource for technical advancements in welding.
Adopt Project Management Tools: Utilize tools like Trello or Asana for task organization, scheduling, and team collaboration.
Effective Communication: Establish clear communication channels. Tools like Slack can improve team interaction.
Risk Management: Implement risk assessment strategies. The Project Management Institute offers resources on project risk management.
Continuous Learning: Engage in lifelong learning through courses on platforms like Coursera or edX, focusing on both welding and project management.
Lean Principles: Apply lean manufacturing principles to welding projects for efficiency. The Lean Enterprise Institute has insightful resources.
Quality Management: Ensure quality standards are met by following guidelines from ISO (International Organization for Standardization).
Time Management: Prioritize tasks and set realistic deadlines. Techniques and tools like the Pomodoro Technique can be very helpful.
Team Leadership: Develop leadership skills to motivate and manage your team effectively. Harvard Business Review offers articles and case studies on leadership.
Feedback and Review: Regularly review project progress and solicit feedback from team members and stakeholders. Continuous improvement is key.
Each step involves a strategic approach to managing welding projects more efficiently and effectively, focusing on up-to-date technical knowledge, streamlined project management methodologies, and strong leadership and communication skills.
How to Display Project Management Skills on Your Resume
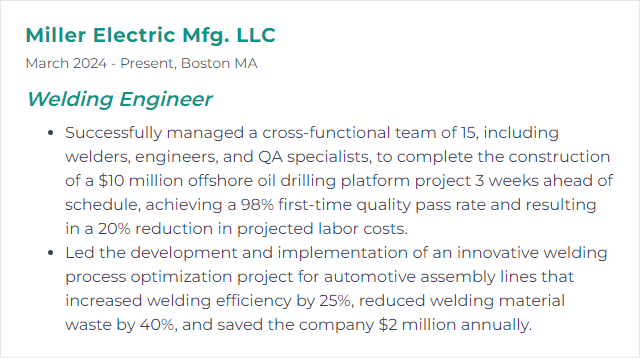