Top 12 Welding Inspector Skills to Put on Your Resume
In the competitive field of welding inspection, showcasing a robust set of skills on your resume can make you stand out to potential employers. Understanding and highlighting the top skills that demonstrate your expertise and efficiency in inspecting welds is crucial for advancing your career in this technical profession.

Welding Inspector Skills
- Ultrasonic Testing
- Radiographic Testing
- Magnetic Particle Inspection
- Dye Penetrant Inspection
- AWS Certification
- ASME Standards
- Visual Inspection Techniques
- Welding Metallurgy
- ISO 9001
- NDT Techniques
- Welding Codes
- Quality Assurance Procedures
1. Ultrasonic Testing
Ultrasonic Testing (UT) is a non-destructive testing technique used by welding inspectors to detect internal flaws, measure material thickness, and evaluate weld integrity by using high-frequency sound waves.
Why It's Important
Ultrasonic Testing (UT) is crucial for a Welding Inspector as it enables the non-destructive evaluation of weld quality and integrity, detecting internal flaws like cracks or voids, ensuring safety and compliance without damaging the components.
How to Improve Ultrasonic Testing Skills
To improve Ultrasonic Testing (UT) as a Welding Inspector, focus on the following steps:
- Enhance Knowledge and Skills: Continuously update your knowledge about ultrasonic testing methods, equipment, and advancements. ASNT offers resources and courses that could be beneficial.
- Use Advanced Equipment: Invest in and utilize state-of-the-art UT equipment for better accuracy and detection capability. Explore the latest offerings from manufacturers like Olympus for industry-standard tools.
- Calibration and Validation: Regularly calibrate your UT equipment to ensure accuracy. Refer to guidelines from NDT Resource Center for calibration procedures.
- Practice and Experience: Gain hands-on experience through practice and working on diverse projects. Practical exposure is key to recognizing and interpreting signals accurately.
- Peer Review and Collaboration: Engage with peers for review and discussion of findings. Platforms like LinkedIn Groups can connect you with professionals for knowledge sharing.
- Stay Updated with Standards: Familiarize yourself with the latest standards and regulations from bodies like AWS (American Welding Society) to ensure compliance and best practices.
By focusing on these areas, you'll enhance your proficiency and accuracy in ultrasonic testing within the welding inspection field.
How to Display Ultrasonic Testing Skills on Your Resume
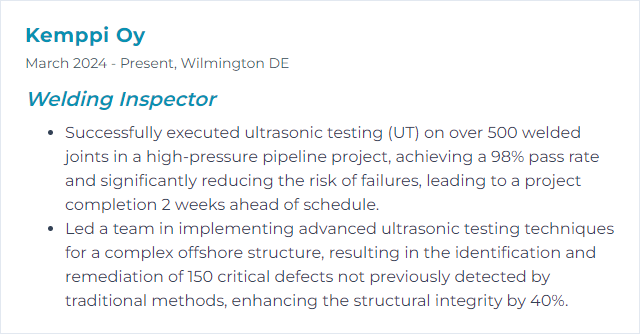
2. Radiographic Testing
Radiographic Testing (RT) is a non-destructive examination technique used by Welding Inspectors to inspect the internal structure of welds. It involves using X-rays or gamma rays to create images of the weld that reveal defects such as cracks, porosity, and inclusions without damaging the component.
Why It's Important
Radiographic Testing (RT) is crucial for a Welding Inspector because it provides a non-destructive means to internally inspect welds for defects such as cracks, porosity, and improper fusion, ensuring the structural integrity and safety of the welded component.
How to Improve Radiographic Testing Skills
Improving Radiographic Testing (RT) for a Welding Inspector involves enhancing image quality, interpretation accuracy, and ensuring safety standards. Here are concise steps:
Understand Standards and Codes: Familiarize with relevant standards (e.g., ASME, ASTM) to ensure compliance in RT procedures.
Optimize Exposure Conditions: Adjust factors like source-to-object distance and exposure time to improve image quality. Refer to ISO 17636 for guidance.
Use High-Quality Equipment: Employ high-resolution detectors and up-to-date X-ray or gamma-ray sources. Regular maintenance and calibration are crucial.
Enhance Image Processing: Apply digital image enhancement techniques if using digital radiography, focusing on contrast and edge definition improvements.
Continuous Learning: Stay updated with the latest RT technologies and interpretation techniques through resources like the American Welding Society (AWS).
Safety First: Always adhere to radiation safety practices as outlined by International Radiation Protection Association (IRPA) to protect yourself and others.
Remember, practice and continuous education are key to mastering radiographic testing in welding inspection.
How to Display Radiographic Testing Skills on Your Resume
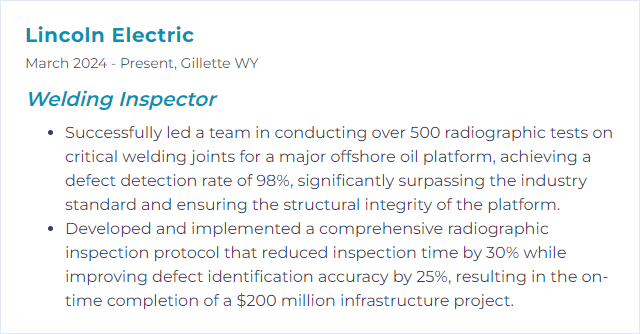
3. Magnetic Particle Inspection
Magnetic Particle Inspection (MPI) is a non-destructive testing method used by welding inspectors to detect surface and near-surface discontinuities in ferromagnetic materials. It involves magnetizing the part, applying magnetic particles, and observing for particle accumulations that indicate flaws like cracks or voids.
Why It's Important
Magnetic Particle Inspection (MPI) is crucial for a Welding Inspector because it allows for the quick and effective detection of surface and near-surface discontinuities or flaws (such as cracks) in ferromagnetic materials, ensuring the integrity and safety of welded components.
How to Improve Magnetic Particle Inspection Skills
To improve Magnetic Particle Inspection (MPI) as a Welding Inspector, focus on the following key areas:
Preparation: Ensure the surface is clean and accessible. Surface preparation is critical for detecting surface and near-surface discontinuities. ASM International provides resources on material surface preparation.
Equipment Check: Regularly verify the equipment's functionality, including the magnetizing force and UV lights. The American Society for Nondestructive Testing (ASNT) offers guidelines on equipment maintenance and calibration.
Technique Selection: Choose the appropriate technique (wet fluorescent, dry powder, etc.) based on the material and the type of defects expected. The Welding Institute (TWI) offers insights into selecting the most effective MPI technique.
Proper Application: Apply the magnetic particles evenly and ensure the magnetization direction is correct for revealing the defects. Guidance can be found through NDT Resource Center.
Interpretation Skills: Enhance defect recognition and interpretation skills through continuous education and practice. Resources for training and certification are available at ASNT.
Documentation: Accurately report findings, including the location and size of the defects, to allow for proper evaluation and action.
By focusing on these areas, you can significantly improve the effectiveness of Magnetic Particle Inspection in welding inspections.
How to Display Magnetic Particle Inspection Skills on Your Resume
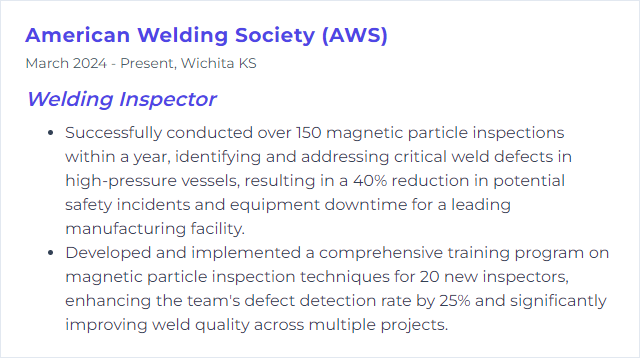
4. Dye Penetrant Inspection
Dye Penetrant Inspection (DPI) is a non-destructive testing method used by welding inspectors to detect surface-breaking defects in non-porous materials. It involves applying a visible or fluorescent dye to the surface, allowing it to penetrate into defects, and then developing the surface to visualize any imperfections caught by the dye.
Why It's Important
Dye Penetrant Inspection is important for a Welding Inspector as it allows for the detection of surface-breaking defects in non-porous materials, ensuring the integrity and safety of welds without damaging the component being tested.
How to Improve Dye Penetrant Inspection Skills
Improving Dye Penetrant Inspection (DPI) involves several key steps tailored to enhance the efficiency and accuracy of the process, especially from the perspective of a Welding Inspector:
Pre-Cleaning: Ensure the surface is thoroughly cleaned to remove any contaminants that might obscure defects. Use appropriate cleaning methods like solvent cleaning, ensuring the surface is dry before applying the penetrant. ASM International provides detailed guidance on surface preparation.
Proper Application: Apply the penetrant correctly, ensuring full coverage without over-application, which might lead to false readings. Follow the manufacturer's instructions for application time to allow penetrant to seep into flaws properly.
Adequate Dwell Time: Adhere to the recommended dwell time, which allows the penetrant to penetrate defects fully. This time varies based on the penetrant type and the material being inspected. NDT Resource Center offers insights on optimizing dwell times.
Thorough Removal: Remove excess penetrant meticulously, using the method recommended by the penetrant manufacturer, to avoid washing out penetrant from defects or leaving residues that could interfere with developing and inspection.
Proper Developer Application: Apply developer evenly and allow it to draw penetrant out of defects for clear visibility. The choice between dry or non-aqueous wet developer depends on the inspection requirements and the surface being tested.
Adequate Inspection Conditions: Perform the inspection under suitable lighting conditions (white light for visible dye penetrants and UV light for fluorescent penetrants) and from various angles to ensure no defects are missed. The American Welding Society (AWS) provides standards for lighting conditions.
Continuous Training: Regularly update training and certification for inspectors to keep abreast of the latest DPI techniques and standards. This includes understanding the limitations of DPI and when to employ supplementary NDT methods.
Record Keeping and Reporting: Maintain detailed records of inspections, including photographs of defects, to improve traceability and inform future inspections.
By focusing on these areas, a Welding Inspector can significantly enhance the effectiveness of Dye Penetrant Inspection processes.
How to Display Dye Penetrant Inspection Skills on Your Resume
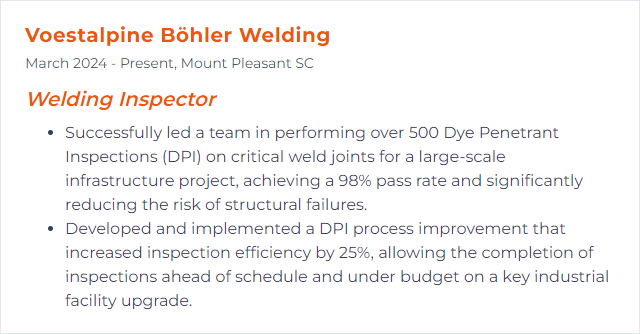
5. AWS Certification
AWS Certification, in the context of a Welding Inspector, refers to a professional credential provided by the American Welding Society that validates an individual's expertise and knowledge in welding inspection, ensuring adherence to industry standards and safety protocols.
Why It's Important
AWS Certification, in the context of a Welding Inspector, validates expertise and adherence to recognized welding standards, ensuring quality, safety, and compliance in welding processes and projects. It enhances professional credibility and marketability in the welding industry.
How to Improve AWS Certification Skills
To improve your AWS Certification as a Welding Inspector, focus on the following concise steps:
Understand the Body of Knowledge: Review the AWS CWI Body of Knowledge to ensure you understand all topics covered in the certification exam.
Hands-On Experience: Gain practical experience in welding inspection. Working under the guidance of a current CWI can provide invaluable insights.
AWS CWI Preparatory Courses: Consider enrolling in AWS CWI Preparatory Courses for focused study and understanding of critical concepts.
Study Guides and Practice Exams: Utilize the official AWS study guides and practice exams. Regularly testing your knowledge can highlight areas needing improvement.
Join AWS Sections or Chapters: Connect with local AWS sections or chapters for networking with other professionals, which can provide support and advice.
Stay Updated: Keep up with the latest in welding technologies, standards, and AWS guidelines by regularly visiting the AWS website and reading relevant publications.
Health and Safety Knowledge: Ensure you're up to date with health and safety practices in welding, as this is crucial for a Welding Inspector.
Remember, persistence, practical experience, and continuous learning are key to improving your AWS Certification status as a Welding Inspector.
How to Display AWS Certification Skills on Your Resume
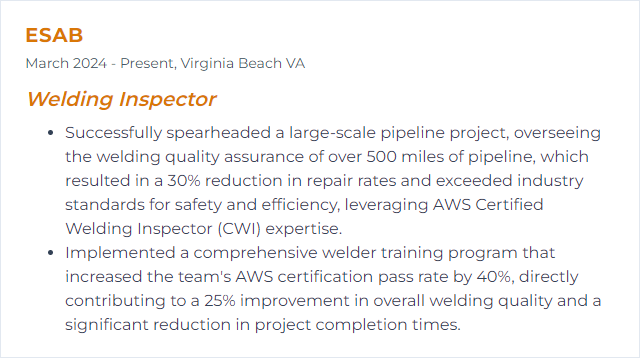
6. ASME Standards
ASME Standards, in the context of a Welding Inspector, refer to a set of guidelines and norms established by the American Society of Mechanical Engineers that outline the best practices, procedures, and safety requirements for welding processes and fabrication to ensure the quality and structural integrity of welded components and structures.
Why It's Important
ASME standards are crucial for welding inspectors as they provide universally recognized guidelines ensuring the safety, reliability, and quality of welding processes and welded structures, thereby minimizing the risk of failures and accidents.
How to Improve ASME Standards Skills
Improving ASME (American Society of Mechanical Engineers) standards, particularly from the perspective of a Welding Inspector, involves a continuous process of review, feedback, and adaptation to the latest technologies, materials, and best practices. Here are concise steps to enhance ASME standards:
Stay Informed: Regularly update your knowledge on the latest welding technologies, materials, and methods. ASME provides resources and updates on their official website.
Engage with ASME: Participate in ASME committees or forums. Your practical insights as a Welding Inspector can highlight areas for improvement or clarification in existing standards. Learn how to get involved through the ASME Volunteer Page.
Continuous Education: Enroll in ASME training courses that focus on new standards and technologies in welding. This not only broadens your understanding but also equips you to identify gaps in current standards. Explore available courses on the ASME Learning & Development Page.
Feedback and Proposals: Provide constructive feedback on standards based on your field experience. ASME encourages the submission of proposals for revisions or new standards through their Public Review Documents page.
Collaborate with Industry Peers: Interaction with other professionals through conferences, workshops, or online forums can spark initiatives to refine or develop standards. These collaborative efforts can lead to the submission of joint proposals to ASME for consideration.
Adopt and Advocate Best Practices: Apply ASME standards diligently in your work and advocate for their adoption by your peers and organization. Demonstrating the benefits of these standards in practice can encourage their broader acceptance and highlight areas for improvement.
Utilize ASME Resources: ASME offers numerous resources, including publications, newsletters, and technical journals, which can provide insights into emerging trends and standards development. Regularly consulting these resources can inform your understanding and feedback on standards. Access these through the ASME Publications page.
By actively engaging in these steps, a Welding Inspector can significantly contribute to the evolution and improvement of ASME standards, ensuring they remain relevant, practical, and effective in addressing the challenges and opportunities of modern welding practices.
How to Display ASME Standards Skills on Your Resume
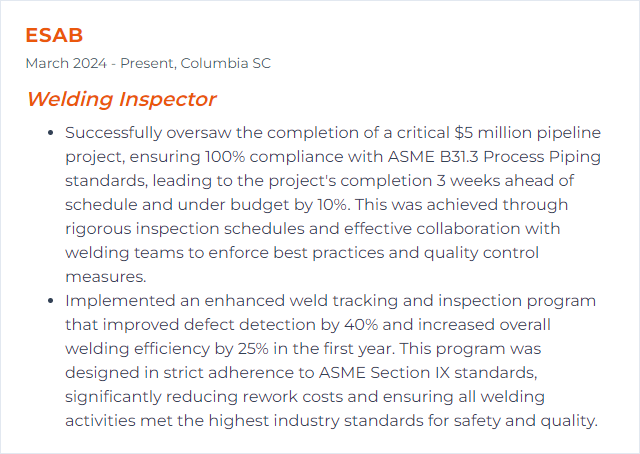
7. Visual Inspection Techniques
Visual Inspection Techniques in the context of a Welding Inspector involve the use of the naked eye and auxiliary aids (like magnifying glasses or gauges) to examine welds for defects, discontinuities, and compliance with specified standards regarding size, shape, and cleanliness, without damaging the weld. This method is crucial for ensuring the quality and safety of the welding work.
Why It's Important
Visual Inspection Techniques are crucial for a Welding Inspector as they enable the early detection of surface defects and irregularities in welds, ensuring the structural integrity and compliance with safety standards. This non-destructive method is cost-effective, requires minimal equipment, and allows for immediate assessment, enhancing the quality and reliability of the welding work.
How to Improve Visual Inspection Techniques Skills
Improving visual inspection techniques, especially for a welding inspector, involves enhancing skills, tools, and methodologies to accurately assess welds. Here are concise strategies:
Enhance Knowledge: Stay updated with the latest welding standards and codes. American Welding Society (AWS) offers resources and certifications.
Use of Tools: Employ advanced inspection tools such as magnifying glasses or boroscopes for better visibility. Understand their proper use through resources like ASNT.
Lighting and Position: Ensure optimal lighting and viewing angles. OSHA provides guidelines on workplace lighting for inspections.
Surface Preparation: Clean and prepare surfaces thoroughly before inspection to reveal subtle defects. Techniques can be learned through NACE International.
Documentation: Develop a systematic approach to documentation for consistency and completeness. ISO standards can guide documentation practices.
Continuous Training: Engage in continuous learning and hands-on training to refine inspection skills. AWS Education offers courses tailored to welding inspection.
Peer Review: Regularly participate in peer reviews and collaborative inspections to gain insights and alternative perspectives.
By focusing on these areas, welding inspectors can significantly improve their visual inspection techniques, leading to more accurate and reliable inspections.
How to Display Visual Inspection Techniques Skills on Your Resume
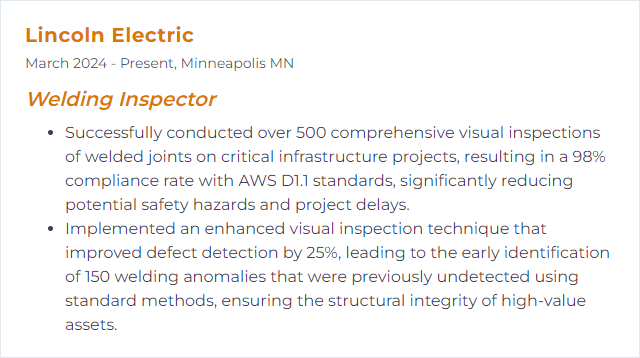
8. Welding Metallurgy
Welding metallurgy is the study of the structural and compositional changes that occur in metals and their alloys during welding processes. It encompasses the understanding of how welding heat and mechanical treatments influence the microstructure, properties, and performance of welded joints. For a Welding Inspector, this knowledge is crucial for assessing weld quality, predicting the behavior of welded materials under various conditions, and ensuring that welding operations meet specified standards and safety requirements.
Why It's Important
Welding Metallurgy is important for a Welding Inspector because it encompasses the study of how welding processes affect the microstructure and properties of metals, ensuring the integrity and performance of welded structures by preventing defects, ensuring proper material selection, and applying appropriate welding techniques.
How to Improve Welding Metallurgy Skills
Improving welding metallurgy, especially from a Welding Inspector's perspective, involves understanding the properties of metals being welded, the welding process, and how to control the factors affecting the weld quality. Here's a concise guide:
Understand Base Metals: Know the chemical and mechanical properties of base metals to predict how they will react under heat from welding. ASM International provides resources on material properties.
Control Heat Input: Heat input affects the metallurgical properties of the weld. Use welding procedures that control the maximum and minimum heat input. The American Welding Society (AWS) offers guidelines on welding procedures and parameters.
Preheat and Interpass Temperature: Proper control of preheat and interpass temperatures can reduce residual stresses and prevent undesirable metallurgical changes. TWI Global has insights on best practices.
Choose the Right Filler Material: The compatibility of filler material with base metals is critical. Ensure the chosen filler metal matches or exceeds the mechanical properties of the base metals. The Lincoln Electric website provides filler metal selection guides.
Post-Weld Heat Treatment (PWHT): PWHT can relieve stresses and temper the weld, improving its metallurgical properties. Refer to the ASM Heat Treating Society for more on heat treatment processes.
Understand Welding Defects and Testing Methods: Be familiar with common welding defects and their causes. Use non-destructive testing (NDT) methods to assess weld quality and integrity. The American Society for Nondestructive Testing (ASNT) offers resources on NDT techniques.
Continuous Education: Welding technology and metallurgy are constantly evolving. Participate in workshops, webinars, and courses offered by professional bodies like AWS.
By focusing on these areas, a Welding Inspector can significantly contribute to improving the metallurgical quality of welds.
How to Display Welding Metallurgy Skills on Your Resume
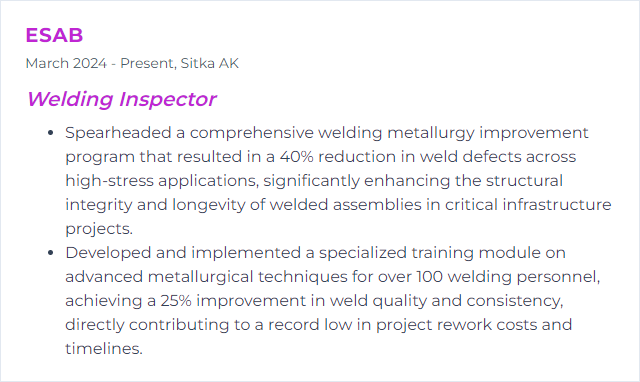
9. ISO 9001
ISO 9001 is a global standard for quality management systems. For a Welding Inspector, it outlines requirements to ensure consistent quality in welding processes, including planning, operation, monitoring, and continuous improvement, ensuring high-quality welds that meet customer and regulatory requirements.
Why It's Important
ISO 9001 is important for a Welding Inspector because it ensures standardized quality management practices are in place, guaranteeing consistent quality and performance in welding processes and outputs.
How to Improve ISO 9001 Skills
Improving ISO 9001, especially from a Welding Inspector's perspective, involves a focused approach on quality management principles and specific welding quality standards. Here’s a concise guide:
Understand and Apply ISO 9001 Fundamentals: Deepen your understanding of ISO 9001 principles, focusing on customer focus, leadership, engagement of people, process approach, improvement, evidence-based decision making, and relationship management. ISO 9001 Fundamentals.
Enhance Welding Quality Management: Align welding processes with ISO 3834 (Quality requirements for fusion welding of metallic materials) to ensure comprehensive quality management in welding operations. This standard complements ISO 9001 by addressing welding-specific quality requirements. ISO 3834 Guidelines.
Continuous Improvement: Implement a continuous improvement strategy, using tools such as PDCA (Plan-Do-Check-Act) to systematically improve welding processes and quality. Emphasize on reducing welding defects and improving weld quality. PDCA Cycle.
Training and Competence: Ensure all welding personnel, including inspectors, welders, and supervisors, are adequately trained and certified. Consider certifications such as CWI (Certified Welding Inspector) from AWS (American Welding Society) to enhance expertise and credibility. AWS Certification.
Welding Inspection and Testing: Regularly perform rigorous welding inspections and testing according to relevant standards (e.g., AWS D1.1, ASME Section IX). Use both destructive and non-destructive testing methods to ensure weld quality and compliance. AWS D1.1.
Documentation and Records: Maintain comprehensive documentation and records of all welding activities, inspections, and corrective actions. This ensures traceability, accountability, and facilitates continuous improvement. ISO 9001 Documentation.
Customer Feedback and Satisfaction: Actively seek and incorporate customer feedback to improve welding quality and service. Implement mechanisms to measure and enhance customer satisfaction.
By focusing on these areas, a Welding Inspector can significantly contribute to enhancing the quality management system under ISO 9001, ensuring high-quality welding operations that meet or exceed customer and regulatory requirements.
How to Display ISO 9001 Skills on Your Resume
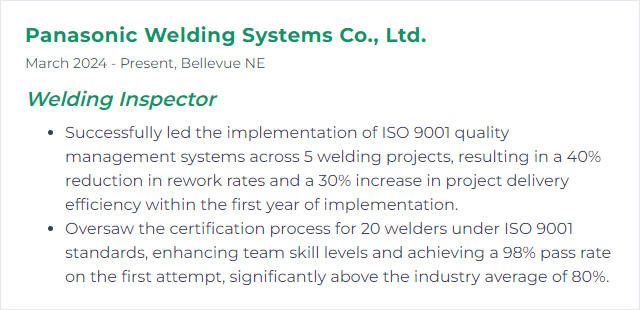
10. NDT Techniques
NDT (Non-Destructive Testing) techniques refer to a range of inspection methods used by welding inspectors to evaluate the properties, integrity, and composition of materials or welds without causing damage. These methods include ultrasonic testing, radiographic testing, magnetic particle testing, and dye penetrant testing among others. They are crucial for ensuring the safety and quality of welds in various industries.
Why It's Important
NDT (Non-Destructive Testing) techniques are crucial for a Welding Inspector as they enable the detection of defects, discontinuities, and inconsistencies in welded joints without damaging the components. This ensures the structural integrity, safety, and compliance of the welding work with standards and specifications, while also allowing for timely corrective actions.
How to Improve NDT Techniques Skills
Improving Non-Destructive Testing (NDT) techniques, especially for a Welding Inspector, involves staying updated with the latest technological advancements, adhering to best practices, and continuously enhancing skills through education. Here's a brief guide:
Continuous Learning: Engage in ongoing education through courses and certifications from reputable organizations. American Welding Society (AWS) and The American Society for Nondestructive Testing (ASNT) offer various resources and certification programs.
Adopt Advanced Technologies: Incorporate advanced NDT technologies such as Phased Array Ultrasonic Testing (PAUT) and Time-of-Flight Diffraction (TOFD) for more detailed inspections. Learn more about advanced NDT methods through Olympus IMS.
Utilize Software Tools: Implement software tools for better data management and analysis, enhancing the accuracy of your NDT results. Explore options like NDT Office, an efficient software for managing NDT operations.
Standard Compliance: Ensure compliance with international standards such as those from ISO (International Organization for Standardization) and ASTM International. Familiarize yourself with the standards relevant to welding and NDT.
Practical Experience: Gain hands-on experience with various NDT methods and materials. Practical exposure is invaluable for understanding real-world challenges and nuances.
Networking and Professional Groups: Join professional networks and forums such as LinkedIn groups for NDT professionals or The Welding Institute (TWI) to share knowledge, stay informed about industry trends, and connect with experts.
Safety Training: Prioritize safety by staying informed about the latest safety protocols and training. Organizations like OSHA (Occupational Safety and Health Administration) provide guidelines and resources.
By focusing on these areas, a Welding Inspector can significantly improve their NDT techniques, ensuring more accurate, reliable, and efficient inspection processes.
How to Display NDT Techniques Skills on Your Resume
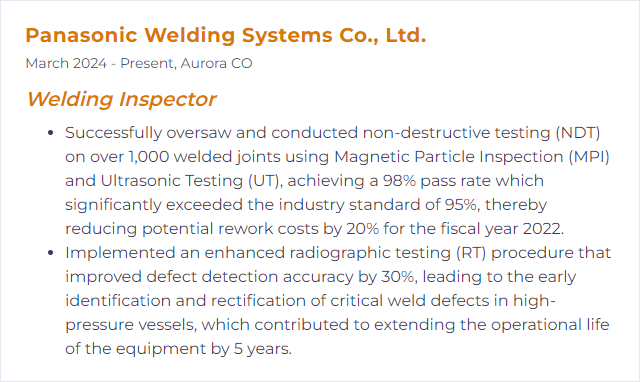
11. Welding Codes
Welding codes are standardized guidelines and requirements that govern welding practices and procedures to ensure the quality, safety, and reliability of welded structures and components. For a Welding Inspector, these codes serve as the criteria for inspecting, testing, and certifying welds in various industries and applications.
Why It's Important
Welding codes are crucial because they establish standardized requirements and best practices for welding processes, ensuring the safety, reliability, and quality of welded structures and components. For a Welding Inspector, these codes serve as essential guidelines for inspecting and evaluating the quality of welds against recognized industry standards, helping to prevent failures and ensure compliance with regulatory and contractual obligations.
How to Improve Welding Codes Skills
Improving welding codes involves a continuous process of review, feedback, and updates to ensure they reflect the latest technologies, materials, and safety practices. As a Welding Inspector, contributing to the enhancement of welding codes can be achieved through the following steps:
Stay Informed: Regularly update your knowledge by engaging with professional bodies and standards organizations. Resources like the American Welding Society (AWS) and ASME (The American Society of Mechanical Engineers) offer valuable insights and updates on welding standards.
Field Experience Feedback: Document and share your observations and experiences related to the practical application of welding codes. Highlight areas for improvement based on real-world scenarios.
Participate in Committees: Join technical committees or standards development groups within organizations like AWS. This direct involvement allows you to contribute your expertise to the revision process. Information on participation can be found on the respective websites of standard organizations.
Continuing Education: Engage in continuous learning through courses and certifications offered by recognized institutions. This not only enriches your expertise but also keeps you abreast of emerging technologies and methodologies that could impact welding codes.
Public Commenting: Utilize the public review and commenting periods offered by standards organizations to provide constructive feedback on proposed changes to welding codes.
Collaborate with Peers: Engage in discussions with fellow welding inspectors and professionals through forums and conferences. Sharing knowledge and challenges can uncover common areas that need addressing in welding codes.
Advocate for Research and Innovation: Encourage investment in welding research and the adoption of innovative practices. Innovations need to be reflected in updated codes to ensure they remain relevant and effective.
By actively engaging in these steps, Welding Inspectors can play a crucial role in improving welding codes, ensuring they remain up-to-date and relevant to the evolving field of welding technology and practices.
How to Display Welding Codes Skills on Your Resume
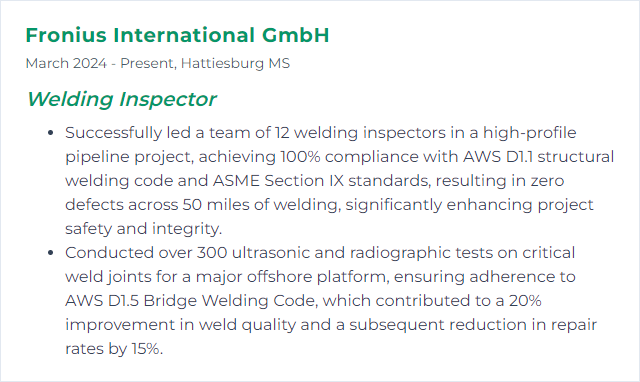
12. Quality Assurance Procedures
Quality Assurance Procedures for a Welding Inspector involve systematic processes designed to ensure that welding activities meet specified quality standards. These include reviewing welding specifications, inspecting materials and equipment, monitoring welding processes, verifying welder qualifications, and conducting final inspections to ensure compliance with relevant codes and specifications, aiming for zero defects and adherence to safety regulations.
Why It's Important
Quality Assurance Procedures are crucial for a Welding Inspector to ensure that welding works meet specified standards and codes, guaranteeing the structural integrity, safety, and longevity of the welded components or structures.
How to Improve Quality Assurance Procedures Skills
Improving Quality Assurance (QA) procedures, especially for a Welding Inspector, involves several key steps aimed at enhancing the precision, efficiency, and effectiveness of welding inspections. Here's a concise guide:
Update and Standardize Documentation: Ensure that all QA documents, including welding procedure specifications (WPS) and procedure qualification records (PQR), are current and comply with relevant standards. AWS and ASME are primary sources for standards and guidelines.
Implement Regular Training: Invest in ongoing education and certification for inspectors. The American Welding Society (AWS) offers various certifications, including Certified Welding Inspector (CWI), that ensure inspectors are up-to-date with the latest welding technologies and QA methodologies.
Adopt Advanced Inspection Technologies: Utilize advanced non-destructive testing (NDT) methods such as ultrasonic testing (UT) and radiographic testing (RT) for more accurate inspections. Resources for learning about NDT methods include the American Society for Nondestructive Testing (ASNT).
Enhance Communication and Collaboration: Foster strong communication between the QA team, welders, and other stakeholders. This can be facilitated through regular meetings and the use of collaborative platforms for sharing QA findings and feedback.
Conduct Regular Audits: Perform internal and external audits of the QA process to identify areas for improvement. The International Organization for Standardization (ISO) provides guidelines for quality management systems that can be adapted for welding inspection.
Implement Continuous Improvement: Adopt a culture of continuous improvement by regularly reviewing and updating QA procedures based on audit findings, technological advancements, and feedback from the QA team and stakeholders.
By focusing on these areas, a Welding Inspector can significantly improve Quality Assurance procedures, leading to higher quality welds, reduced rework, and enhanced overall project outcomes.
How to Display Quality Assurance Procedures Skills on Your Resume
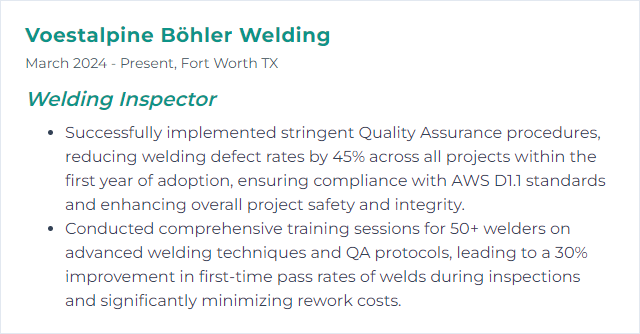