Top 12 Quality Engineer Skills to Put on Your Resume
In today's competitive job market, having a standout resume is crucial for quality engineers seeking to advance their careers. Highlighting a well-rounded set of technical and soft skills on your resume not only showcases your expertise but also positions you as a highly desirable candidate for potential employers.
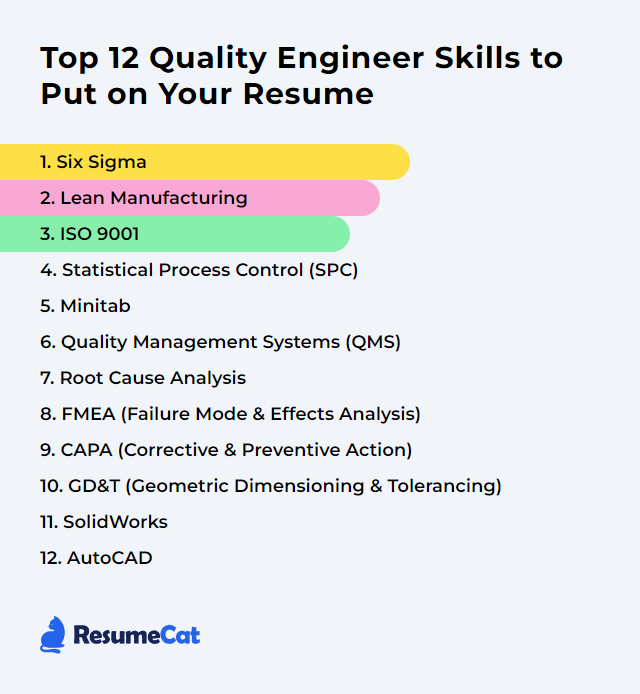
Quality Engineer Skills
- Six Sigma
- Lean Manufacturing
- ISO 9001
- Statistical Process Control (SPC)
- Minitab
- Quality Management Systems (QMS)
- Root Cause Analysis
- FMEA (Failure Mode and Effects Analysis)
- CAPA (Corrective and Preventive Action)
- GD&T (Geometric Dimensioning and Tolerancing)
- SolidWorks
- AutoCAD
1. Six Sigma
Six Sigma is a data-driven methodology and set of tools aimed at process improvement by identifying and removing the causes of defects and minimizing variability in manufacturing and business processes, thereby ensuring quality and efficiency. For a Quality Engineer, it provides a structured approach to problem-solving and quality improvement, focusing on customer satisfaction and cost reduction.
Why It's Important
Six Sigma is important for a Quality Engineer because it provides a rigorous and systematic methodology for process improvement, focusing on reducing variability and defects to enhance product quality and operational efficiency.
How to Improve Six Sigma Skills
Improving Six Sigma practices, especially from a Quality Engineer's perspective, involves continuous learning and application of best practices. Here are concise strategies:
Enhance Statistical Knowledge: Deepen your understanding of statistical tools and analysis techniques essential for Six Sigma projects. Online resources like Khan Academy offer free courses.
Lean Principles Integration: Incorporate Lean manufacturing principles to streamline processes and eliminate waste. The Lean Enterprise Institute provides valuable insights and resources.
Certification and Continuous Education: Attain higher Six Sigma belt certifications and seek continuous education opportunities. ASQ (American Society for Quality) offers various resources and certification programs.
Project Management Skills: Improve project management skills to lead Six Sigma projects effectively. Project Management Institute is a great resource for learning and certification.
Soft Skills Development: Enhance communication, leadership, and problem-solving skills. Courses on platforms like LinkedIn Learning can be very beneficial.
Benchmarking and Networking: Learn from best practices through benchmarking and networking with professionals in the field via platforms like Six Sigma Global Institute.
Utilize Quality Software Tools: Familiarize yourself with the latest quality management software tools. Information on tools can be found through direct research on platforms like Capterra.
Stay Updated with Industry Trends: Follow relevant publications and forums to stay informed about the latest trends and innovations in Quality Engineering and Six Sigma. Quality Magazine is a useful resource.
By focusing on these areas, a Quality Engineer can significantly improve their expertise and contribution to Six Sigma projects.
How to Display Six Sigma Skills on Your Resume
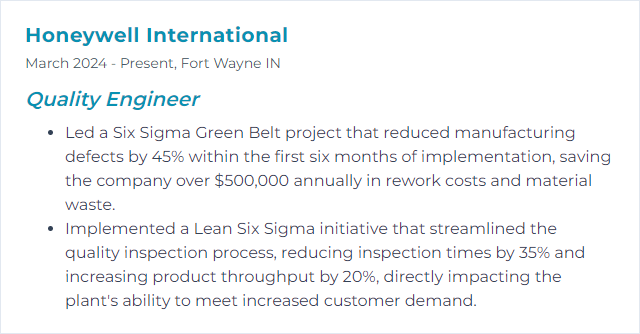
2. Lean Manufacturing
Lean Manufacturing is a systematic approach to minimizing waste within manufacturing systems while maximizing productivity, aimed at enhancing quality and efficiency.
Why It's Important
Lean Manufacturing is important for a Quality Engineer as it emphasizes eliminating waste, optimizing processes, and enhancing product quality, directly contributing to increased efficiency, reduced costs, and higher customer satisfaction.
How to Improve Lean Manufacturing Skills
Improving Lean Manufacturing, especially from a Quality Engineer's perspective, involves focusing on waste reduction, process optimization, and continuous improvement. Here's a concise guide:
Identify Waste: Start by identifying the seven wastes (defects, overproduction, waiting, non-utilized talent, transportation, inventory, motion, and extra-processing). Tools like Value Stream Mapping can help visualize where waste occurs.
Implement 5S: Adopt the 5S methodology (Sort, Set in order, Shine, Standardize, Sustain) to organize and manage the workspace efficiently, which is fundamental for a productive manufacturing environment.
Standardize Processes: Develop and implement standard operating procedures (SOPs) to ensure consistency. PDCA (Plan-Do-Check-Act) cycle can facilitate continuous process evaluation and improvement.
Foster a Culture of Continuous Improvement: Encourage a culture where every employee is looking for ways to improve. Techniques like Kaizen can help in making small, incremental changes that cumulatively lead to significant improvements.
Quality First Approach: Implement Total Quality Management (TQM) principles to ensure that quality is maintained throughout the manufacturing process, rather than just at the end. This involves everyone in the organization in quality improvement.
Use of Lean Tools: Apply lean tools such as Kanban for inventory management, and Poka-Yoke for error-proofing to streamline processes and reduce waste.
Data-Driven Decision Making: Leverage data and analytics for making informed decisions. Tools like Statistical Process Control (SPC) can monitor and control the quality of manufacturing processes.
Supplier Quality Management: Work closely with suppliers to ensure they understand your quality requirements. Techniques like Supplier Quality Management (SQM) can ensure that materials meet specified quality standards before they enter your manufacturing process.
By focusing on these areas, a Quality Engineer can significantly contribute to the enhancement of Lean Manufacturing practices.
How to Display Lean Manufacturing Skills on Your Resume
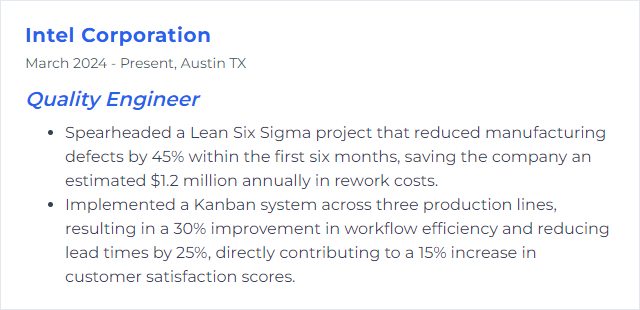
3. ISO 9001
ISO 9001 is an international standard for quality management systems (QMS), providing a framework for companies to ensure they consistently meet customer and regulatory requirements through an effective quality management process. For a Quality Engineer, it serves as a guideline for establishing, implementing, maintaining, and improving a QMS, aimed at enhancing customer satisfaction and continuous improvement.
Why It's Important
ISO 9001 is important because it establishes a framework for consistent quality management practices, ensuring products and services meet customer and regulatory requirements, thereby enhancing customer satisfaction and continuous improvement for a Quality Engineer.
How to Improve ISO 9001 Skills
Improving ISO 9001 in your organization involves a focused approach on continuous improvement, effective management of processes, and the enhancement of customer satisfaction. Here's a concise guide for a Quality Engineer:
Understand the Standard: Ensure you're thoroughly familiar with the ISO 9001 requirements. ISO's official page provides essential resources.
Engage Top Management: Gain commitment from top management for the necessary resources and leadership. Leadership in ISO 9001 offers insights into effective leadership practices.
Employee Training: Train all employees on quality principles and the importance of their role in the QMS. Tools like 9001Academy offer training resources.
Process Approach: Apply a process approach to manage and control how processes are planned and executed. ASQ's process approach explains this in detail.
Risk Management: Implement a systematic approach to risk management. ISO 31000 guidelines can help, and ISO 31000 Guidelines are a useful reference.
Continual Improvement: Use tools like PDCA (Plan-Do-Check-Act) and Six Sigma to drive continual improvement. ASQ's PDCA Cycle provides a good overview.
Customer Focus: Enhance customer satisfaction by understanding and meeting customer requirements. ISO's advice on customer satisfaction is a valuable resource.
Internal Audits: Conduct regular internal audits to ensure compliance and identify areas for improvement. ISO 19011:2018 offers guidelines for auditing management systems.
Management Review Meetings: Hold regular management review meetings to ensure the QMS is effective and aligned with the strategic direction of the organization. Tips for Effective Management Reviews can guide you.
Feedback and Corrective Actions: Implement a feedback mechanism and take corrective actions to address non-conformities and prevent recurrence. ISO 9001 Clause 10 discusses this in detail.
Improving your ISO 9001 implementation is an ongoing journey that requires commitment, continuous learning, and adaptation to new practices and market requirements.
How to Display ISO 9001 Skills on Your Resume
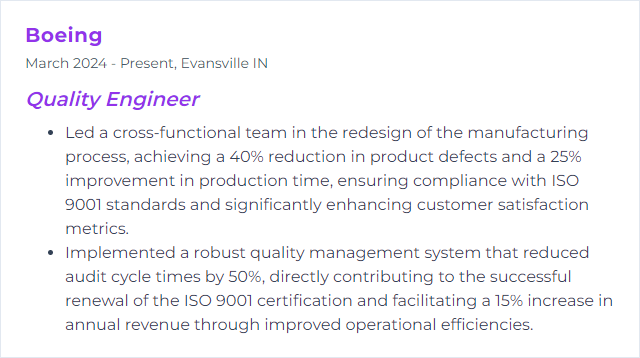
4. Statistical Process Control (SPC)
Statistical Process Control (SPC) is a methodology used by Quality Engineers to monitor, control, and improve process performance by identifying and reducing variability using statistical techniques and data analysis, ensuring product quality meets specified standards.
Why It's Important
Statistical Process Control (SPC) is crucial for a Quality Engineer because it enables the monitoring and controlling of production processes to ensure consistency, reduce variability, maintain product quality, and minimize waste, thereby enhancing customer satisfaction and operational efficiency.
How to Improve Statistical Process Control (SPC) Skills
Improving Statistical Process Control (SPC) as a Quality Engineer involves enhancing the accuracy, reliability, and efficiency of the processes under observation. Here are concise steps to achieve this:
Educate and Train: Ensure all team members understand SPC fundamentals and tools. Online courses from platforms like Coursera or ASQ can be beneficial.
Utilize Software Tools: Adopt advanced SPC software tools for real-time data analysis and monitoring. Explore options like Minitab or SPC Excel Add-in for seamless integration into your processes.
Data Quality: Focus on collecting high-quality, relevant data. This involves verifying measurement systems for accuracy and precision. The MSA (Measurement System Analysis) process can guide this effort.
Implement Control Charts: Use control charts effectively to monitor process stability. Tailor chart selection to your specific process characteristics. The Control Chart Selection Guide can aid in choosing the right chart.
Root Cause Analysis: When variations are detected, promptly perform root cause analysis using tools like Fishbone Diagrams or 5 Whys to identify and address the underlying causes.
Continuous Improvement: Adopt a culture of continuous improvement (Kaizen) by regularly reviewing and optimizing SPC processes. Familiarize yourself with Kaizen principles through resources like the Kaizen Institute.
Benchmark and Collaborate: Benchmark against industry standards and collaborate with peers for insights and best practices. Engage in forums and professional networks like LinkedIn Groups related to quality control and SPC.
By focusing on these areas, you can significantly improve the effectiveness of SPC in your organization, leading to better quality control and process efficiency.
How to Display Statistical Process Control (SPC) Skills on Your Resume
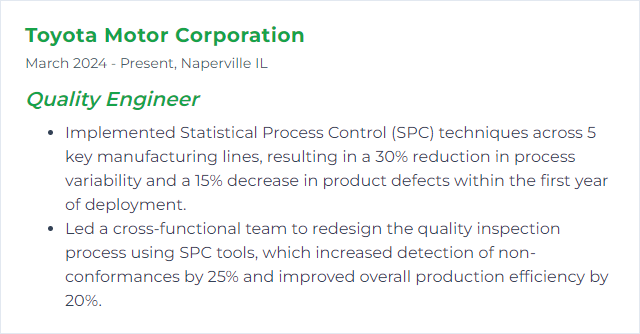
5. Minitab
Minitab is a statistical software package designed for data analysis and quality improvement, widely used by quality engineers for tasks such as process analysis, control charting, hypothesis testing, and design of experiments.
Why It's Important
Minitab is important for a Quality Engineer because it provides powerful statistical analysis, process improvement, and quality control tools, enabling efficient data analysis, problem-solving, and decision-making to enhance product quality and process performance.
How to Improve Minitab Skills
Improving your proficiency with Minitab as a Quality Engineer involves a blend of enhancing your statistical knowledge, understanding Minitab's features in-depth, and applying this understanding to real-world quality projects. Here are concise steps to get started:
Learn the Basics: Familiarize yourself with Minitab's interface and basic statistical tools. Minitab offers a Getting Started guide that's perfect for beginners.
Deep Dive into Quality Tools: Specialize in quality-specific tools such as Control Charts, Capability Analysis, and Design of Experiments (DOE). Minitab's Quality Analysis section provides in-depth tutorials.
Enhance Statistical Knowledge: Strengthen your statistical analysis skills. Khan Academy offers a comprehensive Statistics and Probability course that can elevate your understanding.
Practice with Real Data: Apply your skills on actual quality projects. Experiment with data relevant to your field to gain practical experience.
Join Minitab User Community: Engage with the Minitab user community for insights, tips, and shared experiences. The Minitab Community is a great place to start.
Stay Updated: Minitab frequently updates its software. Keep abreast of these updates and explore new features through the Minitab Blog.
Seek Professional Development: Consider formal training or certification in Minitab. Minitab offers training courses that range from basic to advanced levels.
Utilize Support Resources: For troubleshooting or advanced queries, utilize Minitab's Support section or contact their customer support.
By following these steps and consistently applying your skills to quality engineering projects, you can significantly improve your proficiency with Minitab.
How to Display Minitab Skills on Your Resume
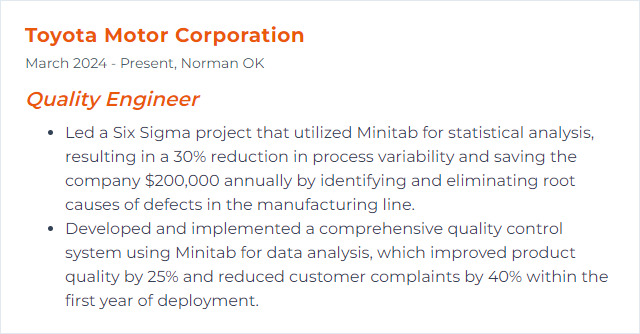
6. Quality Management Systems (QMS)
A Quality Management System (QMS) is a formalized system that documents processes, procedures, and responsibilities for achieving quality policies and objectives. It helps coordinate and direct an organization's activities to meet customer and regulatory requirements and improve its effectiveness and efficiency on a continuous basis. For a Quality Engineer, a QMS provides a structured framework for ensuring product and service quality, compliance with standards, and continuous improvement.
Why It's Important
Quality Management Systems (QMS) are crucial as they provide a structured framework for consistently producing quality products and services, meeting customer expectations, and facilitating continuous improvement, thereby enhancing operational efficiency and competitiveness for a Quality Engineer.
How to Improve Quality Management Systems (QMS) Skills
Improving a Quality Management System (QMS) is a continuous process that involves regular assessment and adjustments to ensure its effectiveness and compliance. Here are concise steps for a Quality Engineer to enhance a QMS:
Regular Audits and Assessments: Conduct internal and external audits regularly to identify areas for improvement. This helps in understanding the current state of your QMS and making necessary adjustments.
Employee Training and Engagement: Ensure all employees are properly trained on the QMS processes relevant to their roles. Engage them in quality objectives and continuous improvement processes to foster a quality culture.
Process Optimization: Continually review and optimize processes within the QMS for efficiency and effectiveness. Utilize lean principles and Six Sigma methodologies to eliminate waste and reduce variability.
Customer Feedback: Incorporate customer feedback into the QMS to align processes with customer expectations and improve customer satisfaction.
Performance Metrics and Continuous Improvement: Establish clear performance metrics and use them to drive continuous improvement. Employ the Plan-Do-Check-Act (PDCA) cycle or similar methodologies to systematically improve QMS processes.
Stay Updated with Standards and Regulations: Keep abreast of the latest ISO standards and industry regulations to ensure your QMS remains compliant and adopts best practices.
Utilize Technology and Software Solutions: Implement QMS software solutions to streamline documentation, process management, and compliance tracking. This can enhance efficiency and traceability within the QMS.
By focusing on these areas, a Quality Engineer can significantly improve the effectiveness of a Quality Management System, ensuring it not only meets but exceeds quality and compliance requirements.
How to Display Quality Management Systems (QMS) Skills on Your Resume
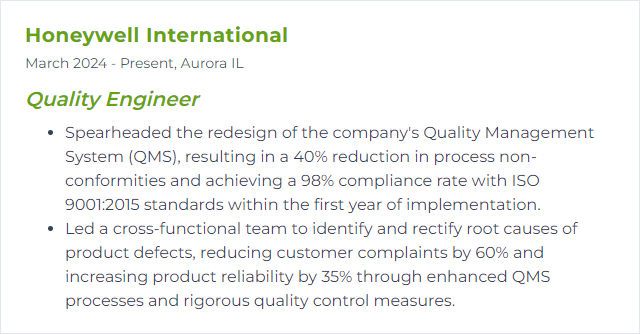
7. Root Cause Analysis
Root Cause Analysis (RCA) is a systematic process used by Quality Engineers to identify the underlying reasons for defects or problems in order to implement effective solutions that prevent recurrence.
Why It's Important
Root Cause Analysis (RCA) is crucial for a Quality Engineer as it helps identify and address the underlying issues causing defects or failures, ensuring the long-term improvement and sustainability of product quality and manufacturing processes.
How to Improve Root Cause Analysis Skills
Improving Root Cause Analysis (RCA) involves a systematic approach to identify the underlying causes of problems to prevent their recurrence. For a Quality Engineer, enhancing RCA skills can be achieved through the following steps:
Define the Problem Clearly: Start with a clear, concise description of the problem, focusing on specific symptoms. ASQ's problem statement guidance offers a good starting point.
Use Structured Methodologies: Employ structured RCA methodologies like the 5 Whys or Fishbone Diagram to systematically explore potential root causes. Familiarize yourself with various tools and select the one most appropriate for the situation.
Collect and Analyze Data: Gather data relevant to the problem. Use Pareto Charts for identifying the most significant factors. Accurate data collection and analysis are crucial for pinpointing the real issues.
Engage the Team: Collaborate with a cross-functional team for diverse perspectives. Tools like Mind Mapping can facilitate brainstorming sessions and help in visualizing the relationships between different factors.
Implement Corrective Actions: After identifying the root causes, develop and implement corrective actions. Plan-Do-Check-Act (PDCA) cycle can be an effective framework for this step.
Verify the Effectiveness: Monitor the implemented solutions to ensure they effectively address the root causes. Use Statistical Process Control (SPC) to track performance and verify improvements.
Document and Share Learnings: Document the entire process and outcomes. Sharing these findings helps prevent recurrence of the problem across the organization.
By following these steps and continually refining your RCA process, you can enhance your effectiveness as a Quality Engineer in identifying and solving problems.
How to Display Root Cause Analysis Skills on Your Resume
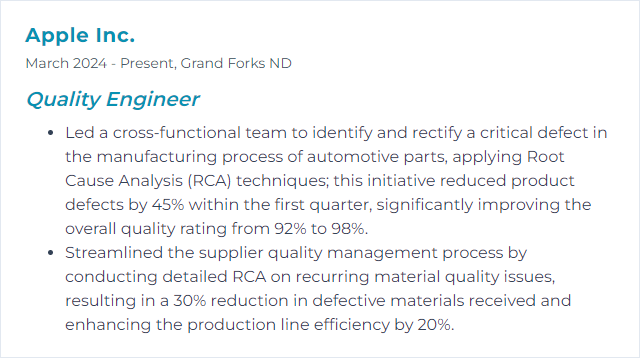
8. FMEA (Failure Mode and Effects Analysis)
FMEA (Failure Mode and Effects Analysis) is a systematic method used by Quality Engineers to identify, assess, and prioritize potential failure modes in a product or process, along with their causes and effects, to prevent failures and improve quality.
Why It's Important
FMEA is important for a Quality Engineer as it systematically identifies potential failures in products or processes, assesses their impact, and prioritizes actions to reduce risk, ensuring reliability and safety while minimizing costs and enhancing customer satisfaction.
How to Improve FMEA (Failure Mode and Effects Analysis) Skills
Improving FMEA involves enhancing the thoroughness, accuracy, and effectiveness of the analysis process. Here are concise steps tailored for a Quality Engineer:
Define the Scope Clearly: Clearly identify the boundaries of the process, product, or system to be analyzed. This ensures all relevant failure modes are considered.
Assemble a Diverse Team: Include members from different departments such as design, manufacturing, and service. Diverse perspectives improve the identification and analysis of potential failures. ASQ’s guide on team roles in FMEA can provide additional insights.
Enhance Data Quality: Use accurate and up-to-date data for the analysis. Historical data, customer feedback, and expert opinions should be incorporated. The IEC 60812 standard provides guidelines on how to systematically use such data.
Prioritize Failure Modes: Utilize the Risk Priority Number (RPN) or other relevant metrics to prioritize failure modes effectively. This helps in focusing on the most critical areas first. AIAG & VDA FMEA Handbook offers a modern approach to prioritizing risks.
Implement Action Plans: Develop and implement action plans to mitigate or eliminate the high-priority failure modes. Ensure actions are specific, measurable, achievable, relevant, and time-bound (SMART).
Review and Update Regularly: FMEA is a living document. Regular reviews and updates should be conducted, especially when there are changes in design, process, materials, or suppliers.
Leverage Software Tools: Use FMEA software tools for efficient data management, analysis, and reporting. These tools can facilitate collaboration, ensure consistency, and save time.
Training and Continuous Improvement: Invest in training for the team on FMEA methodology and tools. Embrace a culture of continuous improvement by learning from past FMEAs and incorporating lessons learned into future analyses. ASQ FMEA Training is a valuable resource for enhancing skills.
Benchmarking and Best Practices: Look for benchmarking opportunities with peers in your industry. Adopting best practices from leading organizations can elevate the quality of your FMEA.
By focusing on these steps, a Quality Engineer can significantly improve the effectiveness of FMEA processes, leading to reduced risks and enhanced product quality.
How to Display FMEA (Failure Mode and Effects Analysis) Skills on Your Resume
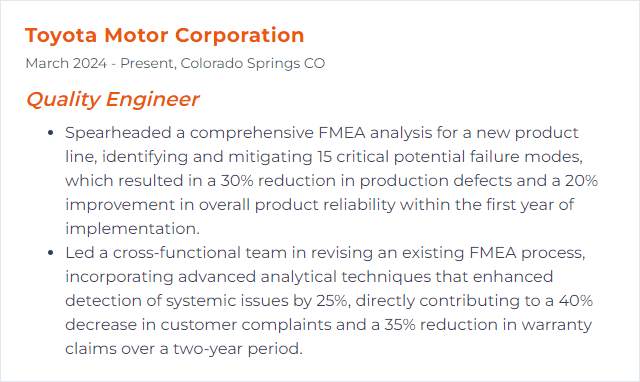
9. CAPA (Corrective and Preventive Action)
CAPA (Corrective and Preventive Action) is a process used in quality management to identify, address, and prevent the recurrence of non-conformities or defects in products or processes. It involves taking corrective actions to fix immediate issues and implementing preventive measures to eliminate the root causes and prevent future occurrences.
Why It's Important
CAPA is crucial for Quality Engineers as it identifies, addresses, and prevents the recurrence of product defects or process inefficiencies, ensuring compliance with quality standards and enhancing customer satisfaction.
How to Improve CAPA (Corrective and Preventive Action) Skills
Improving CAPA involves several focused steps to ensure effectiveness and compliance. Here's a concise guide for a Quality Engineer:
Define the Problem Clearly: Start with a precise definition of the problem. Use tools like 5 Whys to drill down to the root cause.
Root Cause Analysis (RCA): Employ RCA techniques like Fishbone Diagrams or FMEA (Failure Modes and Effects Analysis) to identify underlying causes.
Develop Action Plan: Formulate actions that directly address the root cause. Ensure actions are specific, measurable, achievable, relevant, and time-bound (SMART).
Implementation and Monitoring: Implement corrective and preventive actions. Use project management tools and techniques for effective implementation. Monitor the actions’ effectiveness over time.
Verification of Effectiveness: Verify that the CAPA has resolved the issue without causing additional problems. Techniques like Control Charts can be useful.
Documentation and Review: Document all steps taken and review the CAPA process for potential improvement. Continuous improvement platforms like Kaizen can be integrated into this step.
Training and Communication: Ensure all relevant personnel are trained on the changes. Effective communication tools and strategies are essential.
Leverage Technology: Consider using CAPA management software for tracking and reporting. Various Quality Management Systems (QMS) software are available that include CAPA functionality.
By following these steps, Quality Engineers can enhance their CAPA processes, leading to improved product quality and compliance.
How to Display CAPA (Corrective and Preventive Action) Skills on Your Resume
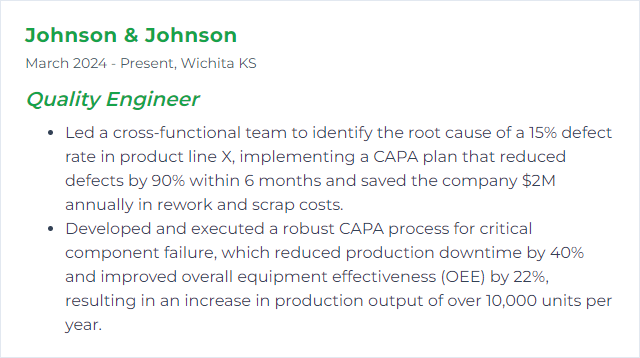
10. GD&T (Geometric Dimensioning and Tolerancing)
Geometric Dimensioning and Tolerancing (GD&T) is a system for defining and communicating engineering tolerances. It uses a symbolic language on engineering drawings and computer-generated three-dimensional solid models for explicitly describing nominal geometry and its allowable variation. GD&T helps in ensuring that parts fit together properly and function as intended, thereby enhancing quality control in manufacturing and engineering projects.
Why It's Important
GD&T is crucial for a Quality Engineer as it ensures precision in manufacturing by clearly defining geometric forms, sizes, and feature relationships on engineering drawings, leading to consistent product quality, reduced waste, and improved interchangeability of parts.
How to Improve GD&T (Geometric Dimensioning and Tolerancing) Skills
Improving your skills in Geometric Dimensioning and Tolerancing (GD&T) as a Quality Engineer involves a combination of theoretical learning, practical application, and continuous improvement. Here's a concise guide:
Understand the Basics: Start with a strong foundation in the principles of GD&T. ASME's GD&T Training offers comprehensive courses.
Practice Regularly: Apply your knowledge in real-world scenarios. Use Engineering Drawing and GD&T exercises from SME to sharpen your skills.
Stay Updated: GD&T standards evolve, so keep abreast of the latest updates. ASME Y14.5 is a crucial resource.
Join Forums and Groups: Engage with communities like Eng-Tips GD&T Forum to exchange knowledge and solve challenges.
Seek Feedback and Mentorship: Collaborate with experienced colleagues or a mentor to review your work and provide guidance.
Utilize Simulation Software: Software like SolidWorks offers GD&T tools that help visualize and test your designs under various conditions.
By following these steps and engaging with each resource, you'll enhance your GD&T proficiency, contributing to improved quality and efficiency in your engineering projects.
How to Display GD&T (Geometric Dimensioning and Tolerancing) Skills on Your Resume
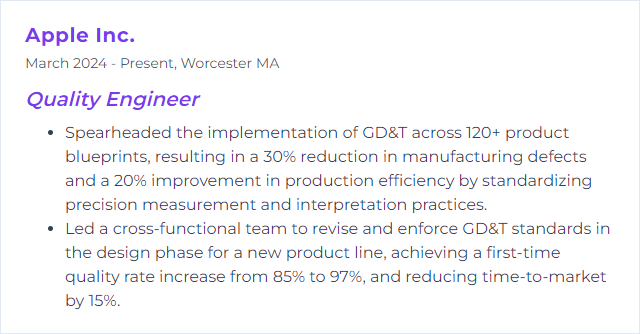
11. SolidWorks
SolidWorks is a computer-aided design (CAD) and computer-aided engineering (CAE) software application used for creating 2D and 3D models. For a Quality Engineer, it facilitates the design, visualization, simulation, and verification of products to ensure quality and precision in manufacturing processes.
Why It's Important
SolidWorks is important for a Quality Engineer because it enables precise 3D modeling and simulation, facilitating the design of high-quality products, the identification and correction of defects before production, and the assurance of adherence to specifications and standards, thereby optimizing product reliability and compliance.
How to Improve SolidWorks Skills
Improving SolidWorks skills, especially for a Quality Engineer, involves a focus on accuracy, efficiency, and leveraging advanced features for quality control and assurance. Here's a concise guide:
Master the Basics: Ensure a solid understanding of SolidWorks fundamentals. Start with the official SolidWorks Tutorials.
Learn Advanced Features: Dive into features like tolerance analysis, GD&T, and advanced assembly techniques to improve design quality. Consider courses from LinkedIn Learning.
Use Simulation Tools: Leverage SolidWorks Simulation to predict performance and identify potential issues early. Check out the Simulation Training page.
Adopt Best Practices for Design and Documentation: Implement design for manufacturability and assembly (DFMA) principles and maintain clear, detailed documentation. The SolidWorks Blog often features useful tips.
Customize SolidWorks for Efficiency: Customize toolbars, menus, and settings for your specific tasks to save time and reduce errors. The CAD Administrator Tools guide can be a good starting point.
Stay Updated: Keep your SolidWorks and related software knowledge current to take advantage of the latest features and improvements. Participate in forums like the SolidWorks Community for insights and updates.
Seek Feedback and Collaborate: Use the SolidWorks eDrawings and other collaboration tools to share your designs with team members for feedback, ensuring quality and efficiency. Explore the Collaborative Business Innovator on the 3DEXPERIENCE platform.
Each step is crucial for a Quality Engineer looking to enhance their SolidWorks proficiency, leading to improved design quality and efficiency.
How to Display SolidWorks Skills on Your Resume
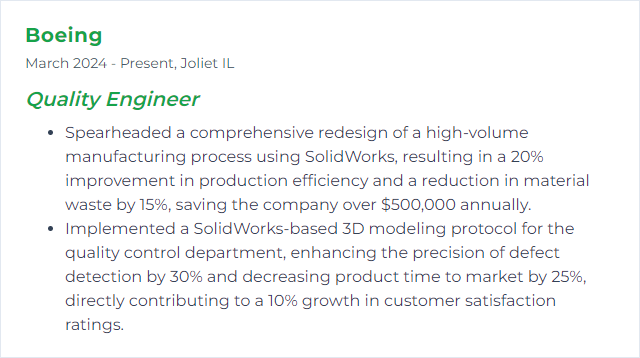
12. AutoCAD
AutoCAD is a computer-aided design (CAD) software used for creating precise 2D and 3D drawings and models, essential for quality engineers in designing, analyzing, and improving product quality and manufacturing processes.
Why It's Important
AutoCAD is important for a Quality Engineer as it enables precise design, specification, and modification of products or processes, ensuring high-quality standards and compliance with industry regulations.
How to Improve AutoCAD Skills
Improving your AutoCAD skills as a Quality Engineer involves focusing on precision, efficiency, and leveraging advanced tools. Here are concise steps to enhance your AutoCAD proficiency:
Master the Basics: Ensure you have a solid understanding of the fundamental commands and tools. Autodesk offers a comprehensive AutoCAD tutorial to get you started.
Customize Your Workspace: Tailor AutoCAD to your specific needs for quality engineering. Autodesk’s guide on customization can streamline your workflow.
Use Templates: Create or adapt templates for repetitive tasks to save time and maintain consistency. This AutoCAD templates tutorial can help.
Learn Advanced Features: Dive into advanced features relevant to quality engineering, such as precision drawing tools and layout management. The AutoCAD advanced tutorial covers these topics.
Automate Tasks with Scripts and Macros: Learn how to automate repetitive tasks to increase efficiency. This guide on scripting offers a good starting point.
Stay Updated: AutoCAD regularly updates its software. Keep abreast of new features and improvements through the AutoCAD blog.
Join Forums and Communities: Engage with other professionals through forums like the AutoCAD Forums for tips, tricks, and networking.
Practice Regularly: Continuous practice is key to mastering AutoCAD. Set aside time regularly to work on AutoCAD projects related to quality engineering.
Seek Feedback: Share your work with peers or mentors to get constructive feedback. This can help identify areas for improvement you might have overlooked.
Enroll in Advanced Courses: Consider enrolling in advanced AutoCAD courses that focus on applications in quality engineering. Platforms like LinkedIn Learning offer courses tailored to various skill levels.
By focusing on these areas, you can significantly improve your AutoCAD skills, contributing to higher quality engineering outcomes.
How to Display AutoCAD Skills on Your Resume
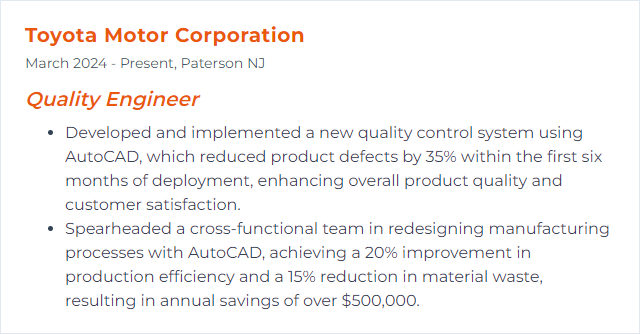