Top 12 Quality Coordinator Skills to Put on Your Resume
A quality coordinator plays a pivotal role in ensuring that products and services meet organizational standards and customer satisfaction. Highlighting a well-rounded set of skills on your resume can significantly enhance your chances of landing this crucial position, demonstrating your capability to maintain high-quality levels across processes.
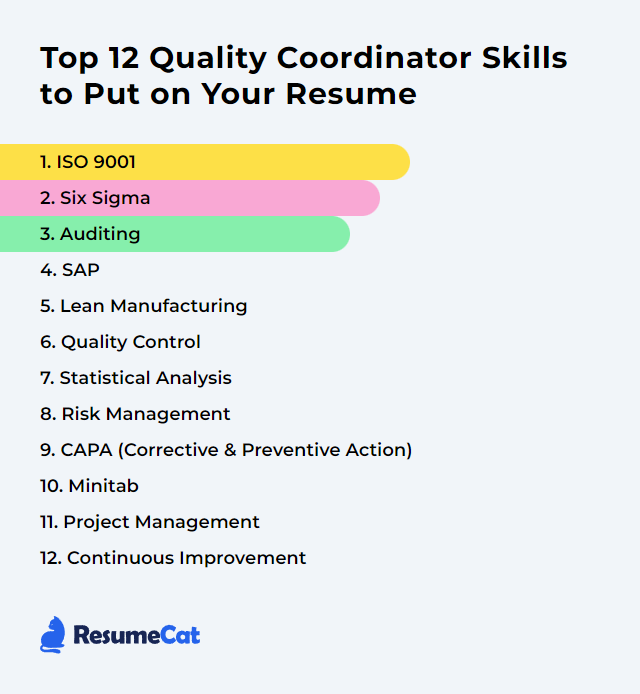
Quality Coordinator Skills
- ISO 9001
- Six Sigma
- Auditing
- SAP
- Lean Manufacturing
- Quality Control
- Statistical Analysis
- Risk Management
- CAPA (Corrective and Preventive Action)
- Minitab
- Project Management
- Continuous Improvement
1. ISO 9001
ISO 9001 is an international standard that specifies requirements for a quality management system (QMS). Organizations use it to demonstrate their ability to consistently provide products and services that meet customer and regulatory requirements, aiming for continual improvement. For a Quality Coordinator, it provides a framework to ensure quality processes are effectively implemented and maintained.
Why It's Important
ISO 9001 is important because it provides a framework for consistent quality management practices, ensuring products and services meet customer requirements and regulatory standards, thereby improving customer satisfaction and operational efficiency. For a Quality Coordinator, it serves as a crucial guideline for monitoring, managing, and improving quality processes across the organization.
How to Improve ISO 9001 Skills
Improving ISO 9001 within your organization, especially from a Quality Coordinator's perspective, involves a focused approach on enhancing the Quality Management System (QMS) for efficiency, effectiveness, and adaptability. Here's a concise guide:
Gap Analysis: Start by conducting a gap analysis to identify where your current QMS does not meet ISO 9001 standards. This will highlight areas for improvement.
Employee Engagement: Engage employees at all levels by providing training on ISO 9001 standards and the importance of their role in the QMS. Promoting a quality culture leads to proactive quality improvement.
Process Optimization: Streamline and optimize your processes to eliminate waste, reduce errors, and improve efficiency. This can be achieved through tools like Six Sigma and Lean management.
Data Analysis: Use data analysis to make informed decisions. Collecting, analyzing, and acting upon quality data helps in identifying trends, preventing nonconformities, and implementing continuous improvement.
Customer Feedback: Implement a robust system for collecting and analyzing customer feedback. This feedback is crucial for understanding customer satisfaction and areas where your product or service can be improved.
Internal Audits: Regular internal audits are essential for assessing the effectiveness of the QMS and identifying areas for improvement. Audits help in preparing for external audits as well.
Management Review: Conduct periodic management reviews of the QMS to ensure its continuing suitability, adequacy, and effectiveness. These reviews should result in actions related to improvements, changes in the QMS, or resource needs.
Continuous Improvement: Adopt a culture of continuous improvement (Kaizen). Encourage innovation and small, incremental changes that lead to higher quality and efficiency over time.
Stay Informed: Keep abreast of the latest developments in ISO 9001 standards and quality management practices. Continuous learning and adaptation are key.
External Resources: Utilize external resources, such as ISO guidance documents, industry best practices, and professional networks, to enhance your understanding and implementation of ISO 9001.
By focusing on these areas, a Quality Coordinator can significantly contribute to the improvement and maintenance of an organization's QMS in line with ISO 9001 standards.
How to Display ISO 9001 Skills on Your Resume
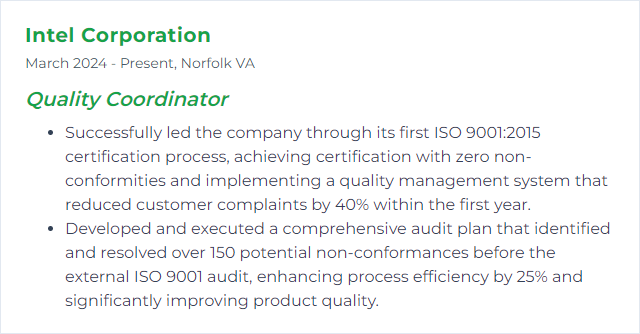
2. Six Sigma
Six Sigma is a data-driven methodology aimed at improving business processes by minimizing defects and variability, ensuring quality control, and enhancing operational efficiency. For a Quality Coordinator, it involves applying statistical tools and techniques to measure, analyze, and optimize organizational processes for quality excellence and customer satisfaction.
Why It's Important
Six Sigma is important for a Quality Coordinator because it provides a data-driven methodology for reducing defects, improving processes, and enhancing quality, thereby increasing customer satisfaction and operational efficiency.
How to Improve Six Sigma Skills
Improving Six Sigma involves continuous learning, applying innovative strategies, and integrating technology. As a Quality Coordinator, focus on these concise strategies:
Educate and Train Continuously: Ensure you and your team are up-to-date with the latest Six Sigma methodologies and tools. Consider online courses from reputable sources like ASQ or Coursera.
Utilize Technology and Software: Leverage Six Sigma software tools for data analysis and project management. Explore options such as Minitab or SigmaXL for statistical analysis.
Implement Six Sigma Across Departments: Extend Six Sigma practices beyond manufacturing to other areas such as HR, marketing, and customer service to enhance overall organizational quality.
Focus on Customer Feedback: Use customer feedback to identify areas for improvement. Tools like SurveyMonkey can be useful for gathering insights.
Adopt Lean Six Sigma Principles: Combine Lean principles with Six Sigma for more efficient processes. Learn more about Lean Six Sigma from resources like iSixSigma.
Regularly Review and Optimize Processes: Schedule regular audits of your processes to ensure they remain efficient and effective. Use findings to make informed adjustments.
Foster a Culture of Continuous Improvement: Encourage a workplace culture where every team member is proactive about identifying inefficiencies and suggesting improvements.
By focusing on these strategies and seeking out reputable sources for ongoing education and tools, you can significantly improve your Six Sigma practices.
How to Display Six Sigma Skills on Your Resume
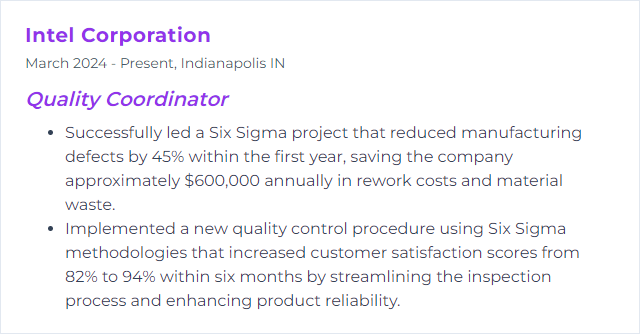
3. Auditing
Auditing, in the context of a Quality Coordinator, is the systematic examination and evaluation of an organization's quality management processes and systems to ensure compliance with established standards, policies, and regulations. This process helps identify areas for improvement and ensures that quality objectives are met consistently.
Why It's Important
Auditing is crucial for a Quality Coordinator as it provides an objective evaluation of an organization's processes and systems, ensuring compliance with regulatory standards, identifying areas for improvement, and enhancing overall quality and efficiency.
How to Improve Auditing Skills
Improving auditing, especially from a Quality Coordinator's perspective, involves a strategic approach focusing on continuous improvement, stakeholder engagement, and leveraging technology. Here’s a concise guide:
Educate and Train: Ensure all team members understand the importance of audits and are trained in both the process and the standards being audited against. ASQ's training resources can be a valuable starting point.
Engage Stakeholders: Involve stakeholders in the audit process to foster a culture of quality and continuous improvement. ISO's guidelines on stakeholder engagement provide a useful framework.
Implement Technology: Use audit management software to streamline the process, ensure compliance, and manage documentation effectively. Intelex and Qualtrax are examples of platforms that can enhance audit efficiency.
Continuous Improvement: Adopt a continuous improvement mindset by regularly reviewing audit processes and outcomes. The Plan-Do-Check-Act cycle provides a structured approach to this.
Follow Best Practices: Stay informed about best practices in auditing by consulting resources like The Institute of Internal Auditors and ISO's auditing standards.
By focusing on these key areas, a Quality Coordinator can significantly improve the auditing process, ensuring it not only meets compliance requirements but also drives quality throughout the organization.
How to Display Auditing Skills on Your Resume
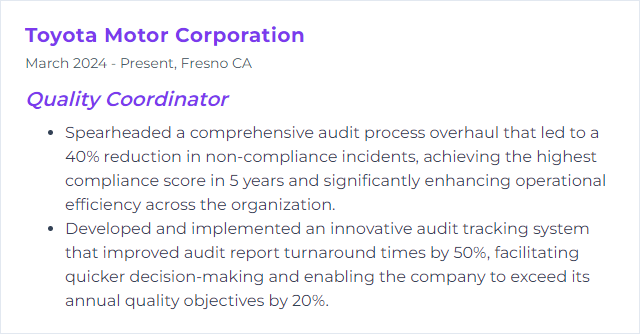
4. SAP
SAP is a comprehensive enterprise resource planning (ERP) software used to manage and integrate various business functions such as finance, supply chain, manufacturing, operations, and quality management. For a Quality Coordinator, SAP provides tools and modules to streamline quality control processes, manage compliance, and ensure product standards are met efficiently.
Why It's Important
SAP is important for a Quality Coordinator because it streamlines and integrates quality management processes, enabling efficient tracking, analysis, and improvement of product quality and compliance across the entire supply chain. This ensures higher product standards and customer satisfaction.
How to Improve SAP Skills
Improving SAP as a Quality Coordinator involves focusing on areas such as process optimization, data integrity, and user training. Here’s a concise guide:
Process Optimization: Streamline SAP processes by leveraging SAP Best Practices. Identify and eliminate redundant steps to enhance efficiency.
Data Integrity: Ensure data accuracy by implementing SAP Master Data Governance. This helps in maintaining consistent and reliable data across the organization.
User Training: Enhance user competency through targeted SAP Training and Certification. This ensures users are well-versed with SAP functionalities, leading to fewer errors and more efficient use of the system.
Customization and Automation: Utilize SAP Fiori for customizing user interfaces for better user experience, and explore SAP's intelligent Robotic Process Automation (RPA) SAP Intelligent RPA for automating repetitive tasks.
Quality Management (QM) Module: Deep dive into the SAP QM module to understand its full capabilities. Tailor the QM module to meet your specific quality control processes. SAP Help Portal on QM provides comprehensive guidance.
Feedback and Continuous Improvement: Implement a feedback loop with end-users to continuously gather insights on problems or areas of improvement. Utilize SAP’s Customer Influence Program to suggest and vote on improvements directly to SAP.
Integration with Other Systems: Ensure SAP is well integrated with other tools and systems used within your organization for seamless data flow and process efficiency. Explore SAP's integration solutions for more insights SAP Integration Suite.
By focusing on these areas, you can significantly improve the efficiency and effectiveness of SAP within your role as a Quality Coordinator.
How to Display SAP Skills on Your Resume
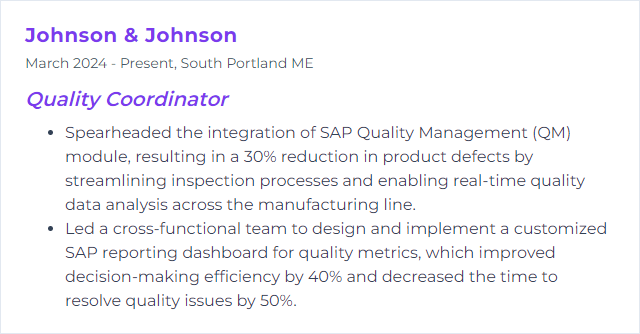
5. Lean Manufacturing
Lean Manufacturing is a systematic approach to minimizing waste within manufacturing systems while maximizing productivity. For a Quality Coordinator, it involves continuously improving processes, ensuring quality products, and enhancing customer satisfaction by streamlining operations and eliminating non-value-added activities.
Why It's Important
Lean Manufacturing is important because it focuses on eliminating waste and inefficiencies, enhancing product quality, and improving customer satisfaction, directly supporting a Quality Coordinator's goals of ensuring high-quality outputs and processes.
How to Improve Lean Manufacturing Skills
Improving Lean Manufacturing involves streamlining processes, eliminating waste, and enhancing efficiency. For a Quality Coordinator, focus on:
Value Stream Mapping: Identify and analyze the flow of materials and information to eliminate non-value-added steps. Learn more about Value Stream Mapping.
5S Methodology: Implement and maintain an organized, clean, and efficient workspace through Sort, Set in order, Shine, Standardize, and Sustain. Explore the 5S System.
Continuous Improvement (Kaizen): Foster a culture of ongoing, incremental improvement in quality, technology, processes, company culture, productivity, safety, and leadership. Kaizen Guide.
Root Cause Analysis: When quality issues arise, identify and address the underlying causes rather than symptoms to prevent recurrence. Root Cause Analysis.
Standard Work: Develop and document the best practices for each task to ensure consistency and efficiency. Regularly review and update these standards. Standard Work Basics.
Employee Engagement and Training: Engage and empower employees with regular training and involvement in problem-solving and improvement initiatives. Building a Lean Culture.
By focusing on these areas, a Quality Coordinator can significantly contribute to the advancement of Lean Manufacturing practices within their organization.
How to Display Lean Manufacturing Skills on Your Resume
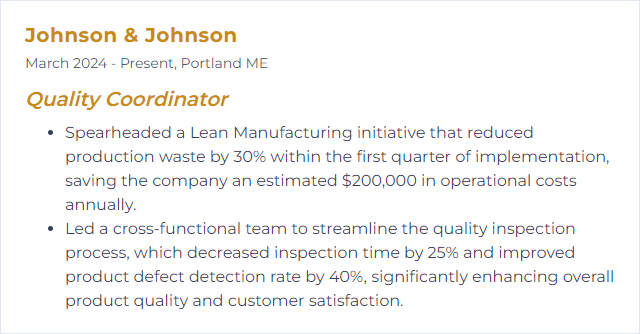
6. Quality Control
Quality Control (QC) is the process of ensuring that products meet specified standards of quality and performance before they reach the customer, involving systematic inspection, testing, and corrective actions as needed. For a Quality Coordinator, it involves coordinating these activities to maintain product quality consistently.
Why It's Important
Quality Control is essential as it ensures products or services meet specific standards and customer expectations, minimizes defects and errors, and enhances customer satisfaction and trust. For a Quality Coordinator, it's crucial for maintaining the company's reputation and competitive edge.
How to Improve Quality Control Skills
Improving quality control involves a strategic approach focused on consistency, training, and continuous improvement. Here are concise steps a Quality Coordinator can take:
Define Quality Standards: Clearly define what quality means for your products or services. Establish specific, measurable standards that align with customer expectations and regulatory requirements.
Implement a Quality Management System (QMS): Adopt a structured QMS like ISO 9001 to manage your processes and quality standards systematically.
Employee Training: Ensure all team members are trained on quality standards and the importance of their role in maintaining them. Continuous education on quality control practices is crucial.
Continuous Monitoring and Auditing: Regularly monitor processes and perform quality audits to identify areas for improvement. Use tools like statistical process control to analyze data effectively.
Feedback Loops: Establish mechanisms for receiving and integrating feedback from customers and employees. This can help in identifying issues early and adjusting processes accordingly.
Root Cause Analysis: When defects occur, employ root cause analysis techniques like the 5 Whys to address the underlying issue, not just the symptoms.
Invest in Quality Control Tools: Utilize modern quality control tools and software to standardize inspections, track defects, and manage documentation.
Foster a Quality Culture: Encourage a culture where quality is everyone's responsibility. Recognize and reward efforts that contribute to quality improvements.
By focusing on these steps, a Quality Coordinator can significantly enhance the quality control processes within their organization.
How to Display Quality Control Skills on Your Resume
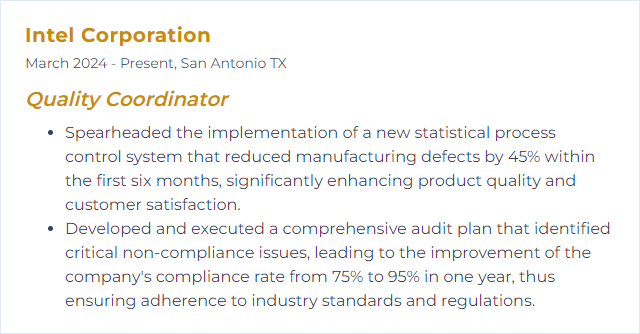
7. Statistical Analysis
Statistical analysis is the process of collecting, examining, summarizing, and interpreting data to identify patterns, trends, and relationships, aiding in decision-making and quality improvement initiatives.
Why It's Important
Statistical analysis is crucial for a Quality Coordinator as it provides evidence-based insights to identify trends, monitor process consistency, and predict future performance, enabling data-driven decisions to enhance product or service quality and customer satisfaction.
How to Improve Statistical Analysis Skills
Improving statistical analysis involves enhancing the accuracy, reliability, and interpretability of data analyses. For a Quality Coordinator, focusing on robust data collection, analysis techniques, and continuous learning are key. Here are concise steps and resources:
Understand the Basics: Ensure a solid understanding of statistical fundamentals. Khan Academy offers comprehensive lessons.
Use the Right Tools: Familiarize yourself with statistical software like R or SPSS for efficient data analysis.
Data Quality Management: Prioritize data integrity by validating and cleaning data regularly. The ASQ provides guidelines on quality management.
Continuous Learning: Stay updated with the latest statistical methods and quality improvement practices through resources like Coursera and edX.
Apply Descriptive and Inferential Statistics: Understand when to use each type to describe data sets or make predictions. Statistics How To is a helpful resource.
Visual Data Analysis: Use visual tools for data exploration and to communicate findings effectively. Tableau offers training on data visualization.
Collaborate and Communicate: Work closely with stakeholders to understand their needs and communicate your findings clearly. MindTools offers communication tips.
Quality Improvement Projects: Apply statistical analysis in quality improvement projects, using methodologies like Six Sigma. The American Society for Quality has extensive resources on Six Sigma.
By focusing on these areas, a Quality Coordinator can significantly improve their statistical analysis capabilities, leading to better decision-making and quality improvement in their organization.
How to Display Statistical Analysis Skills on Your Resume
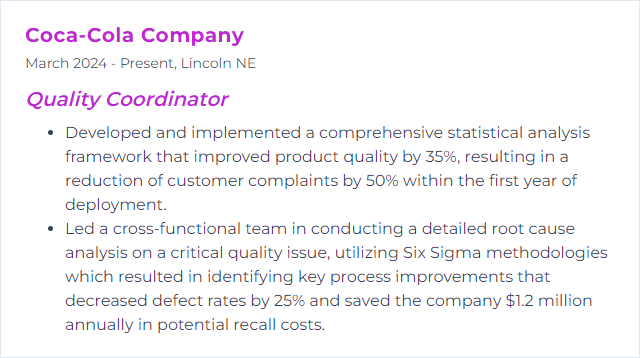
8. Risk Management
Risk management, in the context of a Quality Coordinator, involves identifying, assessing, and prioritizing potential risks to quality objectives, and implementing strategies to minimize, monitor, and control the probability or impact of these risks, ensuring the organization's standards and customer satisfaction are maintained.
Why It's Important
Risk management is vital for a Quality Coordinator as it helps anticipate, identify, and mitigate potential issues that could compromise the quality of products or services, ensuring compliance, customer satisfaction, and continuous improvement.
How to Improve Risk Management Skills
Improving risk management, particularly for a Quality Coordinator, involves a proactive and strategic approach. Here are concise steps to enhance your risk management practices:
Identify Risks: Understand the various types of risks (operational, financial, legal, etc.) that can affect your projects or organization. Tools like SWOT analysis can be helpful.
Assess Risks: Evaluate the likelihood and impact of identified risks using techniques such as risk matrices to prioritize them.
Develop Risk Strategies: Implement strategies to mitigate, transfer, avoid, or accept risks based on their assessment. The ISO 31000 standard provides guidelines on risk management principles and strategies.
Create a Risk Management Plan: Document your risk management processes, strategies, and responsibilities. Tools like Smartsheet offer templates for planning.
Monitor and Review: Regularly review risks and the effectiveness of your risk management strategies. Continuous monitoring is crucial for adapting to new risks and changes in the organization.
Foster a Risk-aware Culture: Encourage open communication about risks and ensure that all team members understand their role in risk management. Training and resources such as Risk Management Online Courses can enhance risk awareness and skills across the organization.
Leverage Technology: Utilize risk management software to streamline risk identification, assessment, and monitoring. Solutions like LogicManager or RiskWatch can be effective.
Compliance and Standards: Always align your risk management practices with relevant industry standards and regulations to ensure compliance.
By systematically implementing these steps and continuously improving your risk management processes, you can significantly enhance your organization's resilience to risks.
How to Display Risk Management Skills on Your Resume
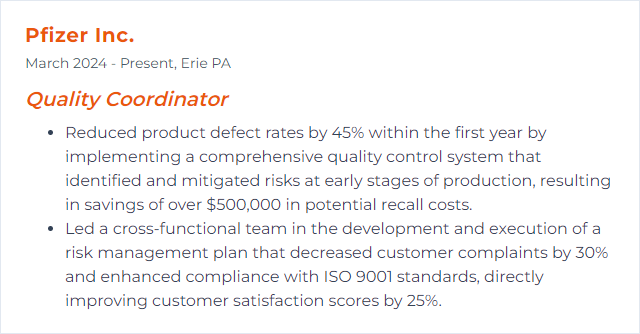
9. CAPA (Corrective and Preventive Action)
CAPA (Corrective and Preventive Action) is a process used by a Quality Coordinator to identify, eliminate, and prevent the recurrence of quality issues. Corrective actions address current problems, while preventive actions aim to eliminate the potential for future issues.
Why It's Important
CAPA is crucial for a Quality Coordinator as it systematically identifies, addresses, and prevents errors or non-conformities, ensuring continuous improvement in quality management and compliance with standards.
How to Improve CAPA (Corrective and Preventive Action) Skills
Improving CAPA involves several strategic steps, aimed at enhancing the effectiveness and efficiency of corrective and preventive actions within an organization. As a Quality Coordinator, focus on the following concise strategies:
Root Cause Analysis: Implement thorough root cause analysis techniques such as the 5 Whys or Fishbone Diagram to accurately identify the underlying reasons for non-conformances.
Risk Management: Integrate risk management principles to prioritize CAPAs based on the potential impact on product quality and patient safety.
Employee Training: Ensure staff are adequately trained in CAPA processes and tools. Continuous training helps maintain a high level of awareness and competence.
Data Analysis: Use data analysis tools to monitor trends and performance indicators, identifying areas for improvement proactively.
Effective Documentation: Maintain clear, concise, and comprehensive CAPA documentation, following guidelines from ISO 13485:2016 for medical devices or relevant standards for your industry.
Cross-Functional Teams: Foster a collaborative approach by involving cross-functional teams in CAPA processes to bring diverse perspectives and expertise.
Review and Follow-Up: Implement a robust CAPA review and follow-up process to ensure actions are effective and prevent recurrence.
Leverage Technology: Utilize CAPA management software to streamline tracking, execution, and reporting of corrective and preventive actions.
By focusing on these key areas, you can significantly improve the CAPA system's responsiveness, effectiveness, and preventive capabilities.
How to Display CAPA (Corrective and Preventive Action) Skills on Your Resume
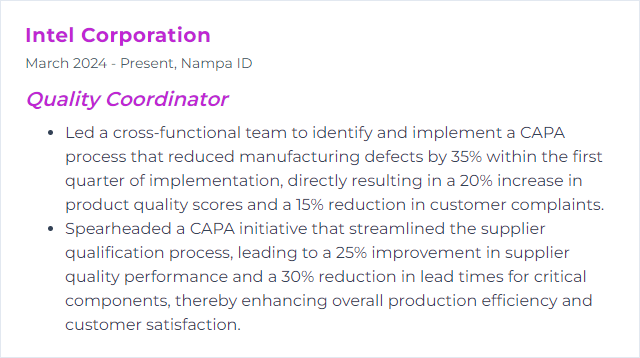
10. Minitab
Minitab is a statistical software package designed for data analysis and improvement in quality management, widely used by Quality Coordinators for process and product optimization through statistical analysis, control chart generation, and defect reduction.
Why It's Important
Minitab is important for a Quality Coordinator because it provides powerful statistical analysis tools that help in identifying trends, solving problems, and making data-driven decisions to improve and maintain quality standards efficiently.
How to Improve Minitab Skills
To improve your proficiency and the effectiveness of Minitab as a Quality Coordinator, follow these concise steps:
Enhance Your Statistical Knowledge: A solid grasp of statistics is crucial for effectively using Minitab. Consider taking online courses or reading books that focus on applied statistics for quality improvement. Khan Academy offers free resources.
Utilize Minitab's Resources: Minitab provides various tutorials, webinars, and case studies that are specifically designed to enhance your understanding and skills.
Practice with Real Data: Apply what you've learned by tackling real-world problems. Use your own quality-related data or access datasets available online to practice.
Join Online Forums and Communities: Engage with other Minitab users by joining forums such as the Minitab Community or relevant LinkedIn groups. This can provide insights into best practices and solutions to common challenges.
Attend Training Programs: Consider enrolling in Minitab-specific training programs, which can range from basic to advanced levels. Minitab offers training courses that are tailored to different user needs.
Stay Updated: Minitab regularly updates its software. Keeping your application up to date ensures you have access to the latest features and tools. Check Minitab’s latest updates regularly.
Feedback Loop: Implement a feedback loop for the processes you analyze with Minitab. This will help in continually refining and improving your quality control strategies based on data-driven insights.
Leverage Support: When facing technical issues or looking for advice on best practices, utilize Minitab's customer support and consulting services to get expert help.
By following these steps and actively seeking out resources and opportunities to learn, you can significantly enhance your effectiveness in using Minitab for quality coordination tasks.
How to Display Minitab Skills on Your Resume
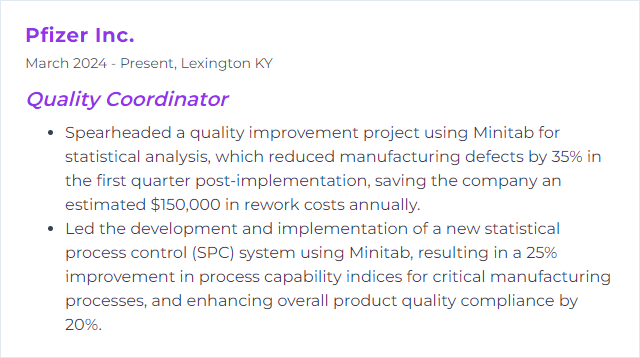
11. Project Management
Project management is the process of planning, executing, and overseeing a project to achieve specific goals within given constraints, such as time, quality, and budget. For a Quality Coordinator, it involves ensuring that project deliverables meet the required standards and specifications.
Why It's Important
Project management is crucial for a Quality Coordinator as it ensures projects are completed efficiently and effectively, meeting quality standards and objectives. It enables systematic planning, execution, and monitoring, ensuring resources are optimally utilized and risks are minimized, leading to consistent quality outcomes and customer satisfaction.
How to Improve Project Management Skills
Improving project management, especially from a Quality Coordinator's perspective, involves focusing on effective planning, continuous monitoring, and adopting best practices for quality assurance. Here are concise steps to enhance project management:
Define Clear Objectives: Establish clear, achievable goals. SMART criteria can guide in setting specific, measurable, attainable, relevant, and time-bound objectives.
Implement a Quality Management System (QMS): Adopt a QMS like ISO 9001, which provides a framework for consistent quality in project delivery.
Effective Communication: Ensure transparent and regular communication among team members. Tools like Slack facilitate seamless communication.
Risk Management: Identify potential risks early and develop mitigation strategies. The Project Management Institute offers insights on effective risk management practices.
Continuous Improvement: Adopt the Plan-Do-Check-Act (PDCA) cycle for continuous improvement in project processes.
Stakeholder Engagement: Maintain active engagement with all stakeholders to align expectations and gather feedback. MindTools provides strategies for effective stakeholder management.
Utilize Project Management Software: Tools like Asana help in tracking project progress, assigning tasks, and managing deadlines efficiently.
Professional Development: Enhance skills and knowledge in project management through certifications like PMP or Prince2.
By focusing on these core areas, a Quality Coordinator can significantly improve project management outcomes, ensuring projects are delivered on time, within budget, and meet the desired quality standards.
How to Display Project Management Skills on Your Resume
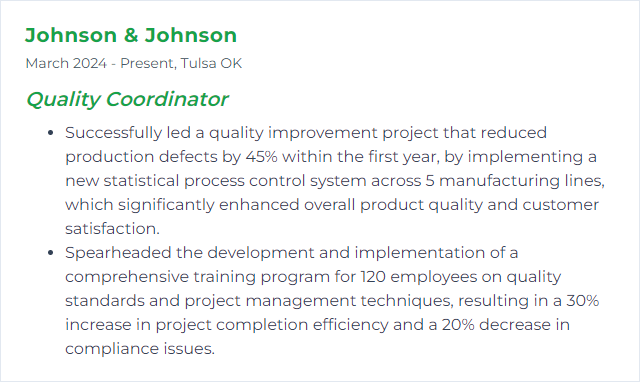
12. Continuous Improvement
Continuous Improvement, in the context of a Quality Coordinator, is an ongoing effort to enhance products, services, or processes through incremental and breakthrough improvements to increase efficiency and quality.
Why It's Important
Continuous improvement is crucial for a Quality Coordinator because it enables the ongoing enhancement of products, processes, and systems, leading to increased efficiency, reduced waste, and higher customer satisfaction. This iterative process fosters a culture of excellence and competitive advantage.
How to Improve Continuous Improvement Skills
Improving Continuous Improvement (CI) necessitates a strategic, focused approach. Here are concise steps for a Quality Coordinator to enhance CI processes:
Educate and Train: Ensure all team members understand CI principles and tools. Invest in training programs to build a knowledgeable workforce.
Implement CI Tools: Utilize CI tools like PDCA (Plan-Do-Check-Act) and Six Sigma methodologies to streamline processes.
Engage Employees: Foster a culture of improvement by involving employees in problem-solving. Tools like IdeaScale can help gather and implement ideas from all levels of the organization.
Set Clear Objectives: Define clear, measurable objectives for improvement initiatives. Use SMART goals to guide your CI efforts.
Monitor and Measure: Regularly review performance using Key Performance Indicators (KPIs). Tools like KPI Library can help identify relevant metrics.
Review and Adapt: Hold regular review meetings to assess progress and adapt strategies as needed. Continuous feedback loops are vital.
Recognize and Reward: Acknowledge and celebrate improvements to motivate continued participation. Recognition platforms can aid in this effort.
By focusing on these strategies, a Quality Coordinator can significantly enhance the effectiveness of Continuous Improvement within their organization.
How to Display Continuous Improvement Skills on Your Resume
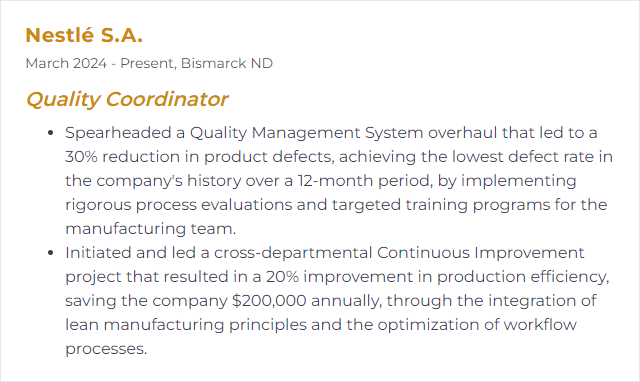