Top 12 Maintenance Planner Skills to Put on Your Resume
A well-crafted resume highlighting your maintenance planner skills can set you apart in the job market, demonstrating your ability to ensure operational efficiency and reduce downtime. Possessing a blend of technical knowledge, organizational capabilities, and strategic planning abilities is crucial for anyone looking to excel in this role and catch the eye of potential employers.
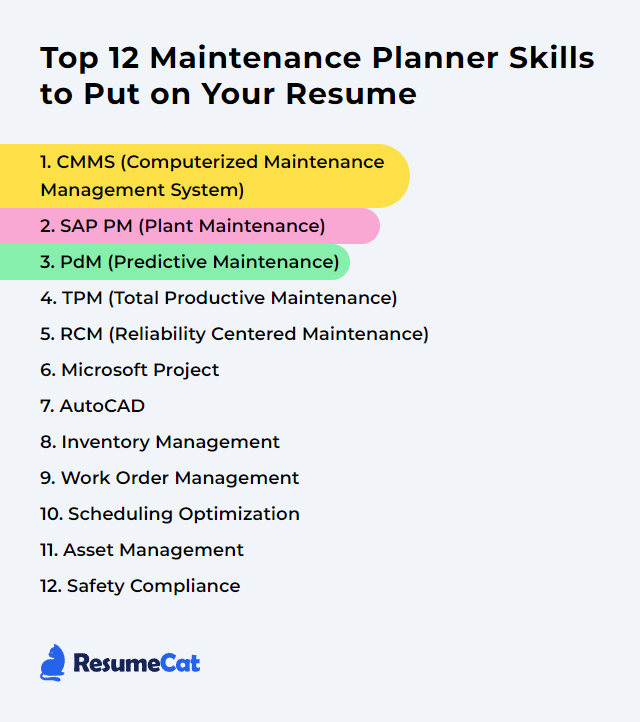
Maintenance Planner Skills
- CMMS (Computerized Maintenance Management System)
- SAP PM (Plant Maintenance)
- PdM (Predictive Maintenance)
- TPM (Total Productive Maintenance)
- RCM (Reliability Centered Maintenance)
- Microsoft Project
- AutoCAD
- Inventory Management
- Work Order Management
- Scheduling Optimization
- Asset Management
- Safety Compliance
1. CMMS (Computerized Maintenance Management System)
A Computerized Maintenance Management System (CMMS) is a digital tool that helps maintenance planners schedule, track, and manage maintenance activities and resources, ensuring efficient operation and prolongation of asset life.
Why It's Important
A CMMS is crucial for a Maintenance Planner because it streamlines scheduling, tracks maintenance tasks, and organizes asset information, thereby enhancing efficiency, minimizing downtime, and reducing maintenance costs.
How to Improve CMMS (Computerized Maintenance Management System) Skills
Improving a Computerized Maintenance Management System (CMMS) for a Maintenance Planner involves several key steps focused on maximizing efficiency, ensuring data accuracy, and enhancing system functionality. Here are concise strategies:
Data Integrity: Ensure all asset and maintenance data entered into the CMMS is accurate and up-to-date. This foundational step enhances decision-making and planning efficiency. CMMS Data Accuracy Tips
Training: Provide comprehensive training for all CMMS users to maximize the system's utility and ensure it's used to its full potential. Maintenance Training Best Practices
Customization: Tailor the CMMS to fit the specific needs of your maintenance operations, including custom reports, dashboards, and workflow automation. Customizing Your CMMS
Integration: Integrate the CMMS with other business systems (e.g., ERP, SCM) for seamless data flow and consolidated analytics. CMMS Integration Guide
Regular Audits and Updates: Conduct regular audits of CMMS data and processes and keep the software updated to leverage new features and improvements. CMMS Audit and Update Practices
Feedback Loop: Establish a continuous feedback loop with users to identify pain points and opportunities for system enhancements. Implementing Feedback Loops
Preventive Maintenance Optimization: Use CMMS data analytics to optimize preventive maintenance schedules, reducing downtime and extending asset life. Preventive Maintenance Optimization
Adhering to these strategies can significantly enhance the effectiveness of a CMMS, leading to improved maintenance planning, reduced operational costs, and increased equipment uptime.
How to Display CMMS (Computerized Maintenance Management System) Skills on Your Resume
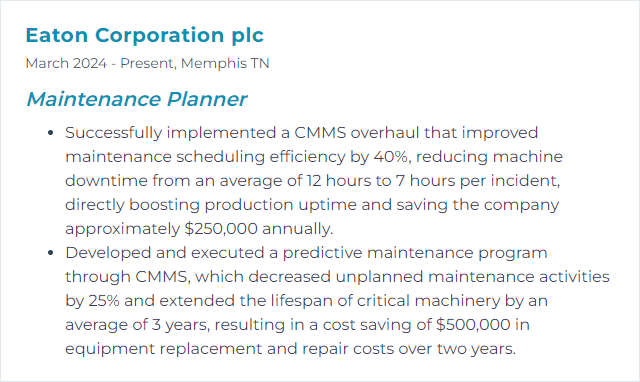
2. SAP PM (Plant Maintenance)
SAP PM (Plant Maintenance) is a module within the SAP ERP system designed to support the planning, processing, and execution of maintenance activities and tasks. It enables maintenance planners to schedule preventive maintenance, manage repair activities, and ensure optimal asset performance and reliability.
Why It's Important
SAP PM (Plant Maintenance) is crucial for a Maintenance Planner as it streamlines and automates maintenance processes, ensuring timely and efficient planning, execution, and monitoring of maintenance activities. This maximizes asset uptime and reliability, optimizes resource allocation, and enhances overall operational efficiency.
How to Improve SAP PM (Plant Maintenance) Skills
Improving SAP PM (Plant Maintenance) for a Maintenance Planner involves a strategic approach focused on optimizing system use, enhancing maintenance planning, and leveraging SAP's capabilities for efficient asset management. Here are key steps to achieve this:
Enhance Data Quality: Ensure all equipment and functional locations are accurately captured in SAP. Clean and structured data is crucial for effective maintenance planning and analysis.
Utilize Maintenance Strategies: Develop and apply preventive maintenance strategies based on the criticality and usage of assets. This includes setting appropriate maintenance plans and task lists in SAP.
Leverage SAP Work Centers: Optimize work center configurations to reflect real organizational structures and capacities for accurate planning and scheduling.
Implement Mobile Solutions: Adopt SAP Mobile Solutions for real-time data access and updates by maintenance personnel in the field, enhancing the efficiency of maintenance tasks.
Continuous Training: Regularly train maintenance planners on SAP PM functionalities, updates, and best practices. Ensuring they are proficient in using SAP Learning Hub can significantly improve maintenance planning efficiency.
Use SAP PM Reports: Utilize SAP PM reporting tools to analyze maintenance performance and asset health. This data can guide decision-making and improvements in maintenance strategies.
Integration with Other Modules: Ensure SAP PM is well integrated with other SAP modules like MM (Material Management) for seamless procurement and inventory management, and CO (Controlling) for accurate cost tracking. This integration ensures a holistic approach to maintenance management.
Feedback Loop: Establish a feedback loop with the maintenance team to continuously identify challenges and opportunities for improvement within SAP PM. This hands-on feedback is crucial for ongoing optimization.
By focusing on these areas, Maintenance Planners can significantly enhance the effectiveness of SAP PM in their organizations, leading to improved asset reliability, cost efficiency, and overall maintenance performance.
How to Display SAP PM (Plant Maintenance) Skills on Your Resume
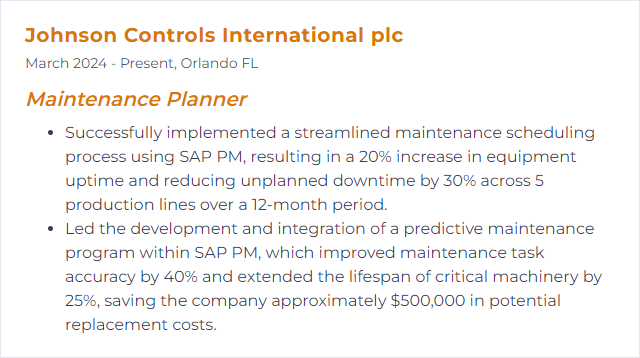
3. PdM (Predictive Maintenance)
Predictive Maintenance (PdM) is a proactive maintenance strategy that uses data analysis and monitoring tools to predict and prevent equipment failures before they occur, optimizing maintenance planning and reducing downtime.
Why It's Important
Predictive Maintenance (PdM) is important because it helps a Maintenance Planner anticipate equipment failures before they occur, allowing for timely, cost-efficient repairs and minimizing unexpected downtime, thus optimizing maintenance schedules and improving overall operational efficiency.
How to Improve PdM (Predictive Maintenance) Skills
Improving Predictive Maintenance (PdM) involves several strategic steps focused on enhancing the efficiency and effectiveness of maintenance operations. Here's a very short and concise guide aimed at a Maintenance Planner:
Data Quality and Collection: Ensure accurate and comprehensive data collection from equipment. Use advanced sensors and IoT devices for real-time monitoring. IBM's guide on the importance of data in PdM provides insights into leveraging data for maintenance.
Analysis Tools: Invest in advanced analytics and AI tools for data interpretation. These tools can predict potential failures more accurately. SAS’s perspective on predictive maintenance highlights the significance of analytical tools in PdM.
Training and Skills Development: Continuously train staff on the latest PdM technologies and techniques. SMRP (Society for Maintenance & Reliability Professionals) offers resources and certifications for maintenance professionals.
Integrate Systems: Ensure your CMMS (Computerized Maintenance Management System) is integrated with PdM tools for seamless operation. Fiix Software’s insights on integration explain the benefits of this approach.
Review and Optimize: Regularly review PdM strategies and performance. Adjust based on feedback and technological advancements. Plant Services provides case studies and articles on optimizing maintenance strategies.
Implementing these strategies requires a balance of technological investment, skill development, and strategic planning to significantly improve PdM outcomes.
How to Display PdM (Predictive Maintenance) Skills on Your Resume
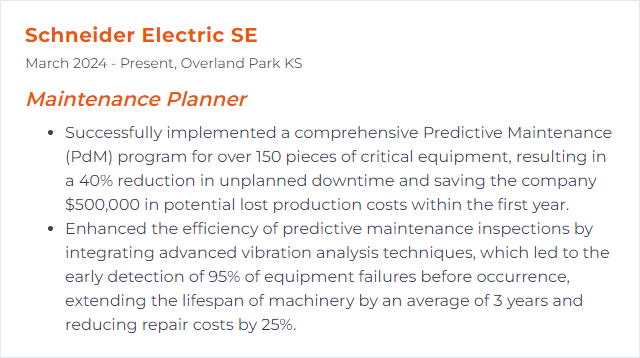
4. TPM (Total Productive Maintenance)
Total Productive Maintenance (TPM) is a proactive maintenance strategy aimed at maximizing equipment effectiveness and minimizing downtime by involving all employees in preventive and predictive maintenance activities. For a Maintenance Planner, TPM emphasizes planning and scheduling regular maintenance tasks, improving equipment reliability, and reducing maintenance costs through efficient use of resources and improved workplace organization.
Why It's Important
TPM (Total Productive Maintenance) is important for a Maintenance Planner because it enhances equipment reliability, reduces downtime, and optimizes maintenance resources, leading to increased production efficiency and cost savings.
How to Improve TPM (Total Productive Maintenance) Skills
Improving Total Productive Maintenance (TPM) involves a strategic approach aimed at increasing equipment effectiveness and fostering a culture of continuous improvement. Here's a concise guide tailored for a Maintenance Planner:
Implement a Comprehensive Maintenance Plan: Develop and refine maintenance schedules based on equipment usage and performance data. This plan should include preventive, predictive, and corrective maintenance actions. Maintenance Planning and Scheduling Handbook provides insights into creating effective maintenance strategies.
Engage Operators in Routine Maintenance: Train operators to perform basic maintenance tasks and spot potential issues. This empowers them to take immediate action and reduces downtime. The Lean Production Toolkit offers resources on integrating lean principles like this into your operations.
Utilize Technology for Data Analysis: Adopt maintenance management software to track equipment performance, maintenance history, and identify trends. This data can be used to predict failures and optimize maintenance schedules. Fiix Software is an example of a platform that facilitates such analytics.
Focus on Continuous Training: Ensure all maintenance staff are continuously trained on the latest maintenance techniques and technologies. This includes training on the TPM methodology itself. Reliabilityweb.com offers resources and training on maintenance strategies and reliability.
Implement Root Cause Analysis (RCA): When failures occur, conduct a thorough root cause analysis to prevent recurrence. This involves systematically identifying and addressing the underlying causes of failures. ASQ's Root Cause Analysis provides a framework for conducting effective RCA.
Promote a Culture of Continuous Improvement: Encourage suggestions from all employees on how to improve maintenance processes and equipment reliability. Implementing a system to capture and evaluate these suggestions can lead to significant improvements. The Kaizen Institute offers guidance on fostering a culture of continuous improvement.
By focusing on these strategies, a Maintenance Planner can significantly enhance the effectiveness of TPM within their organization, leading to reduced downtime, increased equipment lifespan, and improved overall efficiency.
How to Display TPM (Total Productive Maintenance) Skills on Your Resume
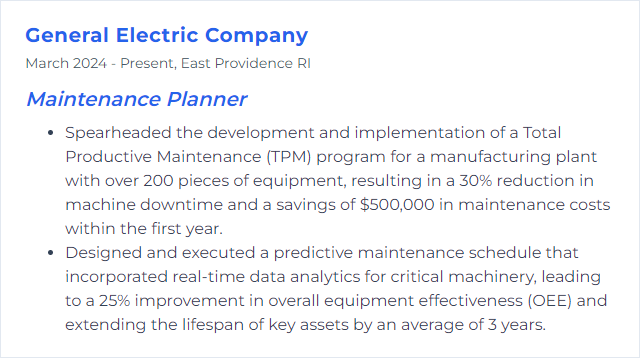
5. RCM (Reliability Centered Maintenance)
Reliability Centered Maintenance (RCM) is a maintenance strategy focused on identifying and prioritizing maintenance tasks based on the criticality and reliability of equipment, with the goal of ensuring optimal performance and minimizing downtime, specifically tailored to support the responsibilities and decision-making processes of a Maintenance Planner.
Why It's Important
RCM (Reliability Centered Maintenance) is important because it ensures the most effective maintenance strategies are applied to each asset, enhancing equipment reliability and performance, while optimizing maintenance costs and minimizing downtime. For a Maintenance Planner, it provides a structured framework to prioritize maintenance tasks based on criticality and risk, ensuring efficient resource allocation and scheduling, ultimately supporting operational efficiency and safety.
How to Improve RCM (Reliability Centered Maintenance) Skills
Improving Reliability Centered Maintenance (RCM) involves a strategic approach that focuses on optimizing maintenance tasks to enhance system reliability and performance. For a Maintenance Planner, the following steps can be crucial:
Understand System Functions: Deeply understand the equipment and system functions to identify critical components. RCM Guide provides an introduction to understanding system functionalities in the context of RCM.
Failure Modes Analysis: Perform a thorough Failure Modes and Effects Analysis (FMEA) to identify all possible failure modes and their consequences. The FMEA Info Centre offers resources on conducting effective FMEA.
Prioritize Maintenance Tasks: Based on the FMEA, prioritize maintenance tasks focusing on critical components that affect reliability the most. The Maintenance Policy and Procedures Manual outlines how to set priorities in maintenance planning.
Optimize Maintenance Strategies: Select the most effective maintenance strategies (predictive, preventive, corrective) for each component based on its failure mode and impact. The Plant Services Guide discusses optimizing maintenance strategies.
Implement and Monitor: Implement the chosen strategies and continuously monitor their effectiveness through Key Performance Indicators (KPIs). The SMRP Best Practices provides a framework for monitoring maintenance effectiveness.
Continuous Improvement: Use data collected from monitoring to continuously improve the RCM process, incorporating feedback and new findings. The Reliability Excellence offers insights into continuous improvement in maintenance.
For a Maintenance Planner, focusing on these steps and leveraging available resources can significantly improve the effectiveness of an RCM program.
How to Display RCM (Reliability Centered Maintenance) Skills on Your Resume
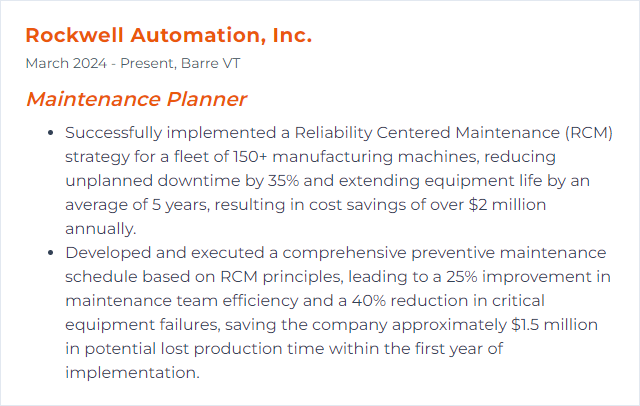
6. Microsoft Project
Microsoft Project is a project management software designed for managing, tracking, and organizing projects, tasks, and resources. For a Maintenance Planner, it facilitates scheduling maintenance activities, allocating resources, and monitoring progress to ensure timely completion of maintenance projects.
Why It's Important
Microsoft Project is important for a Maintenance Planner because it provides powerful tools for scheduling, resource management, and tracking progress, enabling efficient planning, execution, and monitoring of maintenance activities.
How to Improve Microsoft Project Skills
To improve Microsoft Project for a Maintenance Planner, consider the following concise strategies:
Customize Views: Tailor views to highlight key maintenance schedules and critical paths. Customize Project views.
Integrate with Maintenance Software: Use add-ins or API to integrate with specialized maintenance management software for real-time updates. Explore Microsoft Power Automate for automation between applications.
Use Templates: Create or adapt project templates specific to maintenance planning activities. Download templates or customize your own.
Leverage Reports: Generate and customize reports specific to maintenance planning needs for insightful analytics. Create and customize reports.
By customizing views, integrating with specialized software, utilizing templates, and leveraging detailed reporting, a Maintenance Planner can significantly enhance the functionality and efficiency of Microsoft Project.
How to Display Microsoft Project Skills on Your Resume
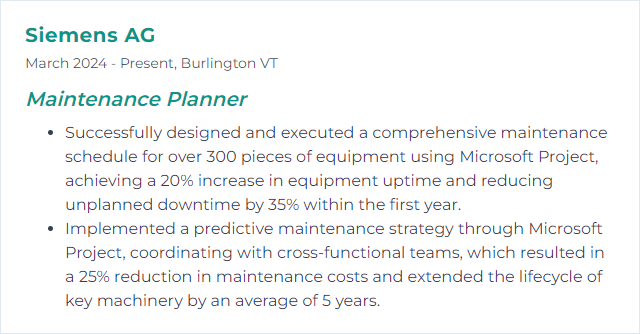
7. AutoCAD
AutoCAD is a computer-aided design (CAD) software used for creating precise 2D and 3D drawings and models, widely used in various fields including maintenance planning for designing equipment layouts, maintenance space planning, and creating detailed parts schematics.
Why It's Important
AutoCAD is important for a Maintenance Planner as it enables precise planning and visualization of maintenance activities, helps in designing and modifying equipment layouts for optimal workflow, and facilitates clear communication of maintenance plans and requirements through detailed drawings and schematics.
How to Improve AutoCAD Skills
To improve AutoCAD for a Maintenance Planner:
Customize Tool Palettes: Streamline your workflow by customizing tool palettes with frequently used blocks, commands, and tools specific to maintenance planning. Autodesk Help
Use Data Extraction: Automate the extraction of data from your drawings for maintenance schedules or inventory management. Autodesk Tutorial
Implement Layer Management: Organize your drawings by using a consistent layering system to easily isolate and manage different elements of your maintenance plans. Autodesk Guide
Leverage Dynamic Blocks: Create dynamic blocks for common maintenance items to save time and enhance the accuracy of your maintenance drawings. Autodesk Support
Automate Repetitive Tasks with Scripts: Use scripts to automate repetitive tasks such as updating drawing standards or batch processing drawings. Autodesk Knowledge
Stay Updated with Training and Resources: Continuously improve your AutoCAD skills through Autodesk’s official training and resources. Autodesk Learning
By implementing these strategies, a Maintenance Planner can significantly enhance efficiency and productivity in AutoCAD.
How to Display AutoCAD Skills on Your Resume
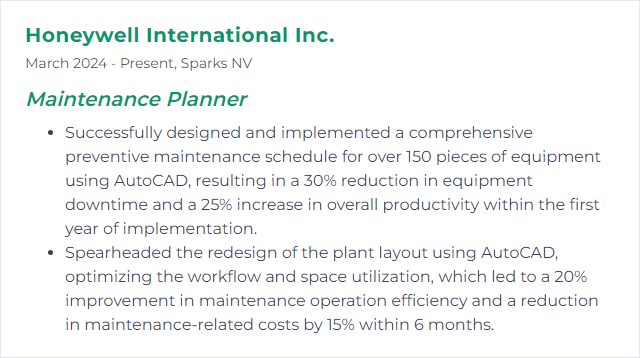
8. Inventory Management
Inventory Management, in the context of a Maintenance Planner, refers to the process of overseeing and controlling the ordering, storage, and use of parts and materials needed for maintenance activities, ensuring the right quantities are available when needed to minimize downtime and maintain operational efficiency.
Why It's Important
Inventory management is crucial for a Maintenance Planner because it ensures the timely availability of parts and materials needed for repairs and maintenance, optimizing downtime and increasing operational efficiency.
How to Improve Inventory Management Skills
Improving inventory management, especially for a Maintenance Planner, involves streamlining processes and ensuring efficient use of resources. Here are concise steps with relevant resources:
Implement an Inventory Management System: Adopt a comprehensive inventory management software that can track stock levels, orders, sales, and deliveries in real-time.
Regular Inventory Audits: Conduct regular audits (physical counts, spot checking, or cycle counting) to ensure accuracy between what's in the database and what's physically in stock.
Adopt Just-In-Time (JIT) Inventory: Implement JIT to minimize stock levels and reduce waste, ordering parts only as they are needed. Here's how JIT works.
Improve Forecasting: Enhance demand forecasting by using historical data and predictive analytics. Tools like Forecast Pro can help in improving the accuracy of your forecasts.
Streamline Supplier Relationships: Maintain good relationships with multiple suppliers and use supplier management software to manage contacts, performance, and negotiations.
Use ABC Analysis: Categorize inventory into A, B, and C groups based on importance and usage rate. This ABC Analysis guide can help in prioritizing management efforts.
Implement Lean Inventory Management: Adopt lean principles to eliminate waste, improve processes, and increase efficiency. This Lean Management Guide provides an overview.
Automate Reordering Process: Set up automatic reordering points for your most critical items to prevent stockouts. Many inventory systems offer automated reordering features.
Enhance Training and Communication: Ensure your team is well-trained on inventory management best practices and tools. Platforms like LinkedIn Learning offer courses on inventory management.
Review and Optimize Regularly: Continuously review and adjust your inventory management practices to adapt to changes in demand, market conditions, and business goals.
Implementing these strategies requires a proactive approach and willingness to adapt to new technologies and processes for optimal inventory management.
How to Display Inventory Management Skills on Your Resume
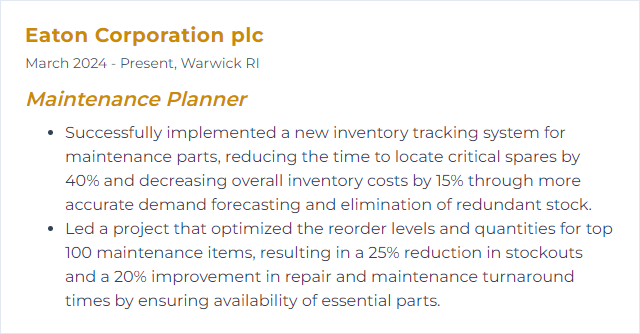
9. Work Order Management
Work Order Management, in the context of a Maintenance Planner, involves the process of initiating, planning, executing, and closing maintenance tasks. It includes creating work orders for maintenance activities, scheduling, assigning tasks to technicians, tracking progress, and ensuring completion within set timelines and standards.
Why It's Important
Work Order Management is crucial for a Maintenance Planner as it ensures efficient organization and tracking of maintenance tasks, optimizes resource allocation, minimizes downtime, and enhances asset longevity, ultimately leading to improved operational reliability and cost savings.
How to Improve Work Order Management Skills
Improving Work Order Management, particularly for a Maintenance Planner, involves optimizing the process of creating, executing, and tracking maintenance tasks. Here's a concise guide:
Define Clear Objectives: Clearly outline the goals for each work order, ensuring alignment with overall maintenance objectives. This aids in prioritizing tasks effectively.
Implement a CMMS: Use a Computerized Maintenance Management System (CMMS) to automate and streamline work order management, from creation to closure. This technology helps in scheduling, assigning, and tracking maintenance tasks efficiently.
Standardize Processes: Develop and enforce standardized procedures for creating, executing, and closing work orders. This includes templates for common tasks to ensure consistency and efficiency.
Train Staff: Ensure all team members are adequately trained on the CMMS and understand the standard operating procedures. Continuous training helps in adapting to system updates and process improvements.
Monitor and Adjust: Regularly review work order performance metrics through the CMMS dashboard to identify areas for improvement. Adjust strategies and processes based on data-driven insights.
Communicate Effectively: Maintain open lines of communication between maintenance teams and other departments. Effective communication ensures that everyone is aligned and informed about maintenance schedules and disruptions.
Leverage Mobile Technology: Utilize mobile solutions for real-time updates and access to work orders on the go. This increases flexibility and responsiveness of the maintenance team.
Prioritize Preventive Maintenance: Shift focus towards preventive maintenance to reduce the frequency and severity of breakdowns. Schedule regular inspections and servicing to catch issues early.
For more insights, the Plant Engineering's guide on Improving Work Order Management provides practical tips and strategies tailored to maintenance planners.
How to Display Work Order Management Skills on Your Resume
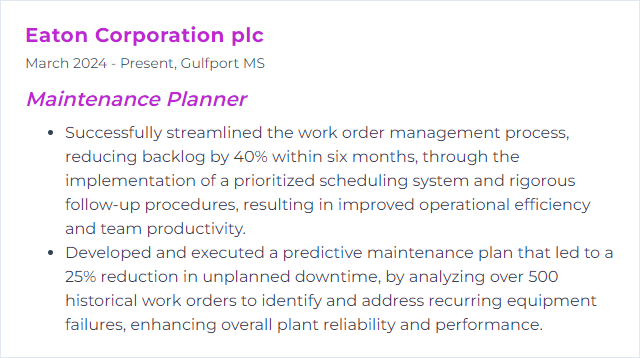
10. Scheduling Optimization
Scheduling optimization in the context of a Maintenance Planner involves using algorithms or software tools to efficiently allocate resources (such as personnel, equipment, and time) to perform maintenance tasks. The goal is to minimize downtime, costs, and resource utilization while ensuring maintenance activities are completed effectively and on schedule.
Why It's Important
Scheduling optimization is crucial for a Maintenance Planner as it ensures the most efficient use of resources, minimizes downtime, and maximizes equipment availability and reliability, leading to increased operational efficiency and cost savings.
How to Improve Scheduling Optimization Skills
To improve Scheduling Optimization for a Maintenance Planner, focus on the following concise strategies:
Data Analysis and Forecasting: Utilize historical maintenance data to predict future needs and optimize scheduling. Tools like IBM Maximo provide advanced predictive analytics.
Prioritization of Tasks: Determine criticality of equipment and prioritize maintenance tasks accordingly. Techniques such as Pareto Analysis can be effective.
Resource Allocation: Efficiently allocate human and material resources. Software like Maintenance Connection helps in resource planning and tracking.
Adopting CMMS/EAM Systems: Utilize Computerized Maintenance Management Systems (CMMS) or Enterprise Asset Management (EAM) software for automating scheduling. Fiix Software is a popular choice.
Continuous Improvement: Implement a feedback loop for continuous improvement in the scheduling process, using methodologies like Kaizen.
Integration of IoT: Use Internet of Things (IoT) devices for real-time monitoring and predictive maintenance scheduling. Check out PTC’s ThingWorx for IoT integration.
Employee Training and Involvement: Ensure that staff are well-trained and involved in the scheduling process. Engaging staff can lead to more efficient scheduling and execution of maintenance tasks.
By focusing on these strategies and leveraging the right tools, Maintenance Planners can significantly improve scheduling optimization.
How to Display Scheduling Optimization Skills on Your Resume
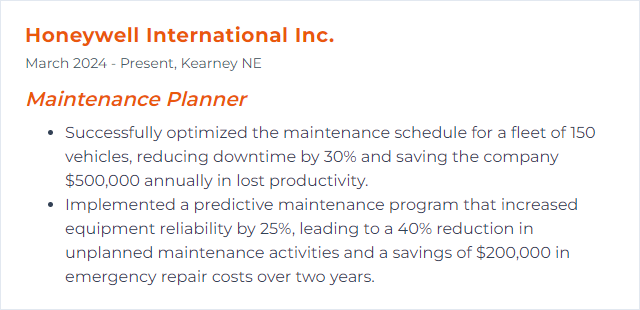
11. Asset Management
Asset Management, in the context of a Maintenance Planner, involves the systematic and coordinated activities and practices through which an organization optimally and sustainably manages its assets, and their associated performance, risks, and expenditures over their lifecycle for the purpose of achieving its organizational strategic plan. This includes planning, acquiring, operating, maintaining, and disposing of assets to maximize their value and ensure the assets' reliability, availability, and capability to perform their intended functions efficiently and effectively.
Why It's Important
Asset management is crucial for a Maintenance Planner as it ensures optimal utilization and performance of assets, reduces operational costs through preventive maintenance, and extends the lifespan of equipment, leading to improved efficiency and reliability in operations.
How to Improve Asset Management Skills
Improving Asset Management involves adopting a strategic approach to maintain, upgrade, and operate physical assets efficiently. For a Maintenance Planner, this means:
Implementing a Computerized Maintenance Management System (CMMS): Use software to streamline maintenance operations, track asset performance, and schedule preventive maintenance. Fiix offers insights on how a CMMS can enhance maintenance management.
Adopting Predictive Maintenance: Utilize sensors and data analytics to predict equipment failures before they occur. This approach reduces downtime and extends asset life. IBM’s guide on Predictive Maintenance explains its benefits and implementation strategies.
Improving Inventory Management: Optimize spare parts inventory to ensure availability while minimizing excess stock. Reliabilityweb offers best practices in inventory management for maintenance.
Enhancing Training and Skills Development: Ensure maintenance staff are trained in the latest techniques and technologies. Continuous learning enhances the team's ability to manage assets effectively. SMRP (Society for Maintenance & Reliability Professionals) provides resources and certification programs for maintenance professionals.
Adopting Reliability-Centered Maintenance (RCM): Focus on preventive maintenance strategies based on the reliability and criticality of assets. This approach prioritizes tasks to improve overall asset performance. Reliabilityweb offers a primer on RCM principles.
By integrating these strategies, Maintenance Planners can enhance asset management, leading to increased reliability, reduced costs, and improved operational efficiency.
How to Display Asset Management Skills on Your Resume
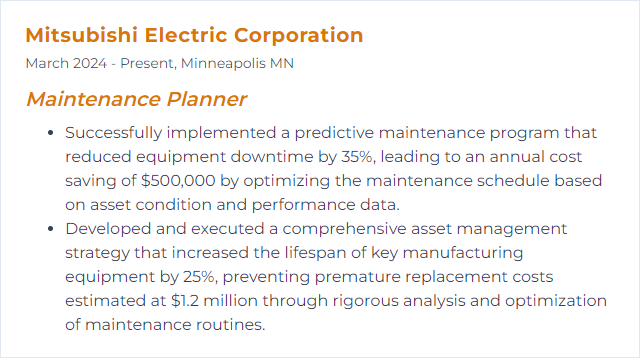
12. Safety Compliance
Safety compliance, in the context of a Maintenance Planner, involves ensuring all maintenance activities adhere to established safety regulations and standards to prevent accidents, injuries, and ensure a safe working environment.
Why It's Important
Safety compliance is crucial for a Maintenance Planner as it ensures adherence to legal and regulatory standards, minimizes risks of accidents and injuries, and protects the well-being of employees and the integrity of equipment and facilities.
How to Improve Safety Compliance Skills
Improving safety compliance, especially for a Maintenance Planner, involves several key steps. Here's a concise guide:
Stay Informed: Regularly update your knowledge of industry standards and safety regulations. Websites like OSHA (Occupational Safety and Health Administration) or HSE (Health and Safety Executive) provide valuable resources.
Risk Assessment: Conduct thorough risk assessments for maintenance activities. Identify hazards and implement measures to mitigate them. The CDC's NIOSH offers guidelines on assessing workplace hazards.
Training and Awareness: Ensure all team members are trained on safety protocols and aware of the risks. Online platforms like Coursera and OSHA Education Center offer relevant courses.
Safety Equipment: Invest in and maintain proper safety equipment. Regular checks are crucial to ensure they are in good working condition.
Safety Procedures: Develop and implement clear safety procedures for maintenance tasks. Documentation and regular updates are key.
Feedback Loop: Create a system for receiving and acting on safety feedback from employees. This promotes a culture of safety and continuous improvement.
Emergency Preparedness: Have a solid emergency plan in place, and ensure all employees are familiar with it. Practice drills regularly.
Compliance Software: Utilize compliance management software to track and manage safety tasks, documentation, and compliance. Platforms like SafetyCulture offer tools for audits, inspections, and reports.
By systematically addressing these areas, a Maintenance Planner can significantly improve safety compliance in their operations, ensuring a safer workplace for all employees.
How to Display Safety Compliance Skills on Your Resume
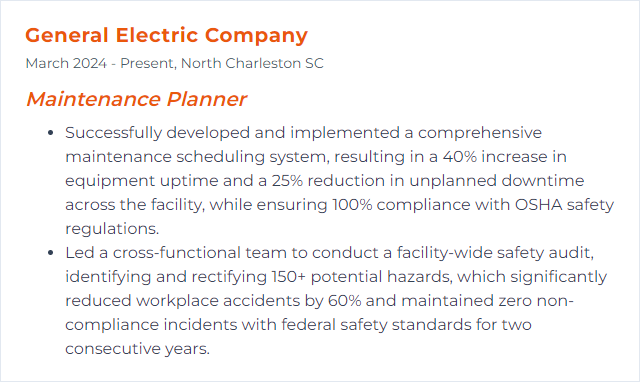