Top 12 Lathe Operator Skills to Put on Your Resume
Crafting an impressive resume as a lathe operator means highlighting the unique blend of technical proficiency and precision craftsmanship that you bring to the table. Showcasing your top skills not only demonstrates your expertise in operating lathes with finesse but also your dedication to maintaining high-quality standards in every project you undertake.
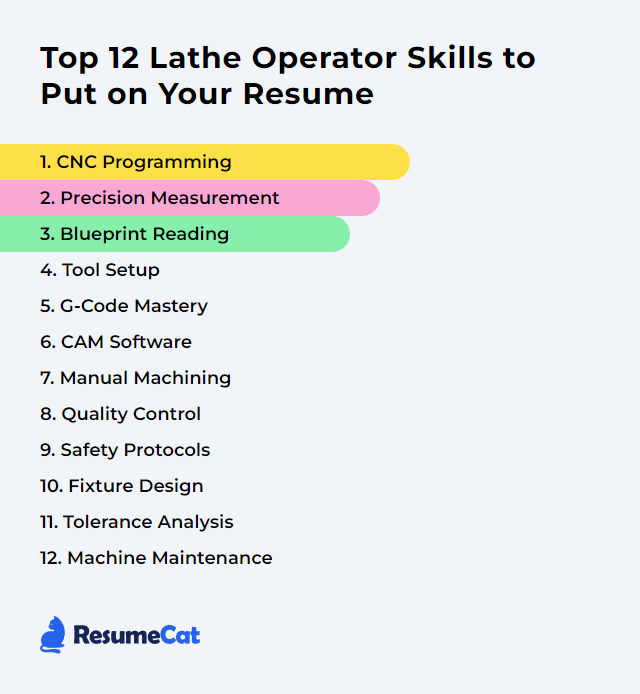
Lathe Operator Skills
- CNC Programming
- Precision Measurement
- Blueprint Reading
- Tool Setup
- G-Code Mastery
- CAM Software
- Manual Machining
- Quality Control
- Safety Protocols
- Fixture Design
- Tolerance Analysis
- Machine Maintenance
1. CNC Programming
CNC programming for a lathe operator involves creating and inputting instructions into a CNC (Computer Numerical Control) machine to automatically control the cutting, shaping, and finishing of materials such as metal or wood, using a lathe. This process requires setting parameters such as speed, feed rate, and tool path to produce precise cylindrical or spherical parts.
Why It's Important
CNC programming is crucial for a Lathe Operator as it enables precise control over the machining processes, ensuring high accuracy, repeatability, and efficiency in producing complex parts.
How to Improve CNC Programming Skills
Improving CNC programming, especially for a Lathe operator, involves enhancing efficiency, accuracy, and safety. Here are concise strategies:
Understand the Basics: Ensure a strong grasp of CNC fundamentals, machining processes, and lathe operation. MIT's Introduction to CNC offers valuable insights.
Master CAD/CAM Software: Proficiency in CAD/CAM software enables efficient programming and simulation. Explore resources like Fusion 360 Tutorials for learning.
Optimize Tool Paths: Efficient tool paths reduce machining time and wear. Study strategies through Mastercam's Dynamic Motion Technology.
Implement Standardization: Develop and use standard programming templates and libraries. CNCCookbook’s G-Code Tutorial is a great resource for learning and standardization.
Continuous Learning: Stay updated with the latest techniques and technologies in CNC machining through platforms like Modern Machine Shop.
Safety First: Always prioritize safety by following best practices and guidelines, as outlined in OSHA’s Machine Guarding eTool.
Practice and Experiment: Hands-on practice and experimentation with different materials and settings can lead to better understanding and improvements.
By focusing on these areas, a Lathe operator can significantly enhance their CNC programming skills and efficiency.
How to Display CNC Programming Skills on Your Resume
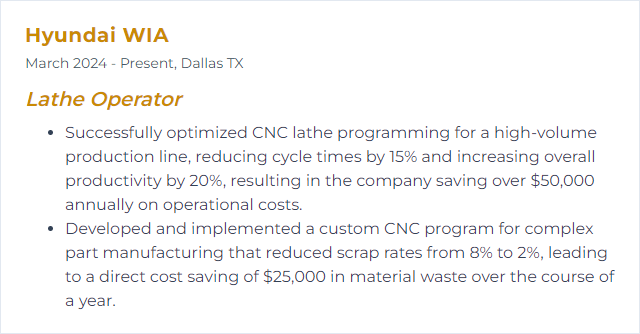
2. Precision Measurement
Precision measurement for a lathe operator refers to the use of precise measuring tools (such as micrometers, calipers, and gauges) to accurately determine the dimensions of workpieces being machined, ensuring they meet specified tolerances and quality standards.
Why It's Important
Precision measurement is crucial for a lathe operator to ensure the machined parts meet exact specifications, achieving high-quality, consistent, and interchangeable components, minimizing waste and ensuring safety and efficiency.
How to Improve Precision Measurement Skills
To improve precision measurement as a Lathe Operator, follow these concise strategies:
Regular Calibration: Ensure all measuring tools and the lathe itself are regularly calibrated to maintain accuracy. NIST Guidelines
Use of High-Quality Tools: Invest in high-quality, reliable measuring instruments like micrometers and calipers. Mitutoyo
Proper Setup: Ensure the workpiece is properly secured and aligned in the lathe to avoid inaccuracies due to movement or vibration. Haas Tip of the Day
Temperature Control: Maintain a stable temperature in the workspace to prevent material expansion or contraction, affecting measurements. Fluke Calibration
Skill Development: Continuously improve your skills through training and practice. Understanding the nuances of the lathe and the materials can significantly improve precision. Tooling U-SME
Use of Digital Tools: Where possible, use digital measurement tools for more accurate readings. Starrett Precision Tools
Implementing these strategies can significantly enhance measurement precision in lathe operations.
How to Display Precision Measurement Skills on Your Resume
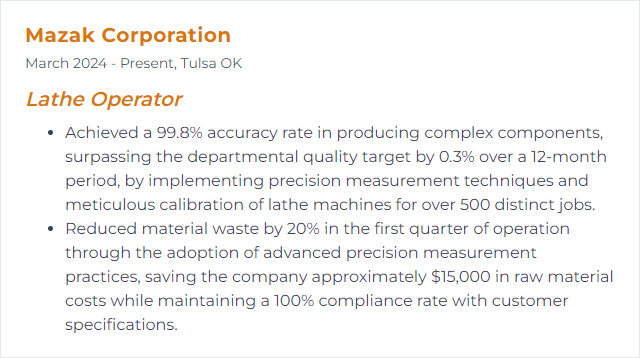
3. Blueprint Reading
Blueprint reading for a lathe operator involves understanding and interpreting detailed technical drawings that specify the dimensions, geometry, and finishing requirements for parts to be machined. This skill enables the operator to accurately set up and operate the lathe in order to produce components as specified by the blueprint.
Why It's Important
For a Lathe Operator, blueprint reading is crucial to accurately interpret and follow the design specifications and dimensions required for machining parts, ensuring precision and quality in the final product.
How to Improve Blueprint Reading Skills
Improving blueprint reading as a Lathe Operator involves enhancing your ability to interpret and visualize 2D drawings and understand the specifications required for machining. Here’s a concise guide:
Familiarize with Symbols and Abbreviations: Start by learning the common symbols and abbreviations used in machining blueprints. This guide is an excellent place to begin.
Understand Views and Dimensions: Practice recognizing different views (front, top, side) and how dimensions are depicted. Engineering.com provides a good overview of orthographic projection and dimensioning.
Study Geometric Dimensioning and Tolerancing (GD&T): GD&T is crucial for precision machining. This basic guide will help you understand the concepts.
Apply Knowledge Practically: Practice by interpreting blueprints and visualizing or sketching the 3D part. Try to predict potential machining challenges.
Take Online Courses or Workshops: Consider enrolling in online courses or workshops specifically designed for machinists. Websites like Udemy and Coursera offer relevant courses that can deepen your understanding.
Use Simulation Software: Engage with CAD/CAM software that allows you to view and manipulate 3D models based on 2D blueprints. This can bridge the gap between theory and practice.
By systematically enhancing your knowledge and applying it through practice and continuing education, you can significantly improve your blueprint reading skills as a Lathe Operator.
How to Display Blueprint Reading Skills on Your Resume
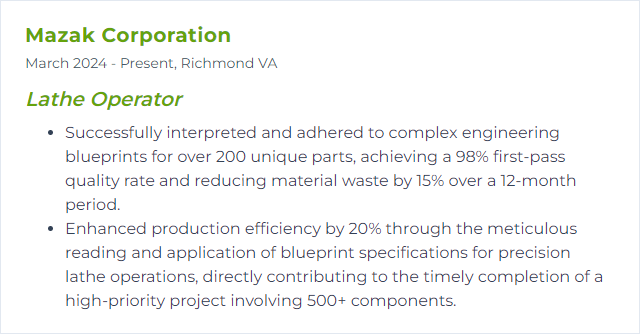
4. Tool Setup
Tool setup for a lathe operator involves selecting, mounting, and adjusting the cutting tools on a lathe machine to perform specific machining tasks on a workpiece accurately and efficiently.
Why It's Important
Proper tool setup in lathe operations is crucial for ensuring accuracy, achieving desired surface finishes, maintaining tool life, and ensuring the safety of the operator. It impacts the quality of the workpiece and the efficiency of the machining process.
How to Improve Tool Setup Skills
Improving tool setup for a lathe operator involves several key steps aimed at increasing precision, efficiency, and safety. Here's a concise guide:
Understand Your Machine: Familiarize yourself with your lathe's specifications and capabilities. Manufacturer manuals or online tutorials can be invaluable resources.
Select the Right Tools: Choose the appropriate cutting tools based on the material and the type of operation. MSC Industrial Supply Co. offers a wide variety of tools suitable for different lathe operations.
Maintain Tools: Keep tools sharp and in good condition. Regular maintenance reduces setup time and improves quality. Consider consulting Machinery's Handbook for maintenance tips.
Use a Quick Change Tool Post: Investing in a quick change tool post can significantly reduce setup time between operations. Learn more about them at LittleMachineShop.com.
Optimize Tool Height: Ensure the cutting tool's tip is at the center height of the workpiece for optimal performance. Incorrect tool height can lead to poor finish and tool breakage.
Employ Presetters: Use tool presetters to measure tools off-machine, saving setup time and increasing accuracy. BIG KAISER offers advanced tool measuring and presetting technology.
Implement Tool Crib Management Software: Use software to manage tools and track inventory. This can reduce search time and streamline tool setup. CribMaster provides solutions tailored for tool management.
Continuous Learning: Stay updated with the latest techniques and technologies. Websites like Modern Machine Shop offer articles, webinars, and other resources for continuous improvement.
By systematically addressing each of these areas, a lathe operator can significantly improve tool setup efficiency, accuracy, and ultimately, the quality of the machining operations.
How to Display Tool Setup Skills on Your Resume
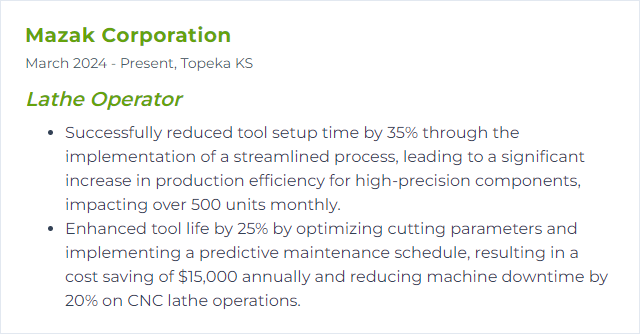
5. G-Code Mastery
G-Code Mastery for a Lathe Operator refers to the comprehensive understanding and skillful application of G-Code, the programming language used to control CNC lathes, enabling precise machining operations and part production.
Why It's Important
G-Code mastery is crucial for a Lathe Operator as it enables precise control over the machining processes, ensuring accuracy, efficiency, and the ability to execute complex part designs with minimal errors.
How to Improve G-Code Mastery Skills
Improving your G-Code mastery, particularly as a lathe operator, involves a combination of structured learning, practice, and resource utilization. Here's a concise guide:
Understand the Basics: Start with a solid understanding of G-Code fundamentals. MIT's Introduction to G-Code video can provide a clear overview.
Practice Regularly: Apply what you've learned by writing and editing G-Code. Use simulation software like NC Viewer to test your codes without risking machinery.
Learn from Mistakes: Analyze and learn from the errors in your G-Code. Tools like G-Wizard G-Code Editor can help you debug and improve your codes.
Stay Updated: G-Code standards and practices evolve. Follow forums like CNCZone and subscribe to relevant YouTube channels for the latest trends and tips.
Use Reference Materials: Keep handy G-Code reference materials and charts specific to your lathe. Websites like CNC Cookbook offer comprehensive guides and cheat sheets.
Take Online Courses: Enroll in online courses that focus on G-Code for lathe operations. Platforms like Udemy and LinkedIn Learning offer courses tailored to different levels of expertise.
Join Workshops and Webinars: Participate in workshops and webinars for hands-on experience and expert advice. Check out community colleges or local maker spaces for scheduled events.
Remember, mastery comes with time and persistent practice. Keep experimenting, learning from mistakes, and seeking feedback from more experienced operators or online communities.
How to Display G-Code Mastery Skills on Your Resume
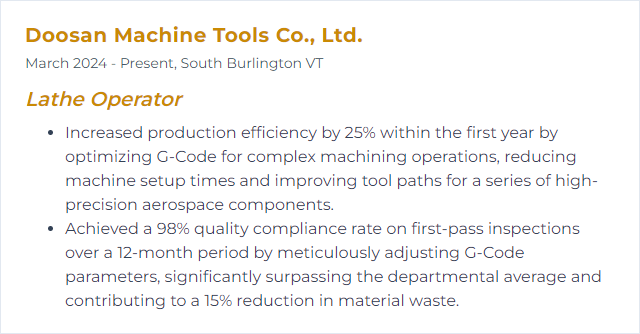
6. CAM Software
CAM software (Computer-Aided Manufacturing) is a digital tool that Lathe Operators use to create detailed instructions (G-code) for CNC lathes, enabling the precise cutting, shaping, and machining of materials based on designed models.
Why It's Important
CAM (Computer-Aided Manufacturing) software is important for a Lathe Operator because it streamlines the process of converting CAD drawings into G-code, the programming language that controls the lathe machine. This automation reduces manual programming errors, enhances precision in creating parts, and increases overall productivity.
How to Improve CAM Software Skills
Improving CAM (Computer-Aided Manufacturing) software for a lathe operator involves focusing on ease of use, integration capabilities, and advanced toolpath strategies. Here's a concise guide:
Enhance User Interface: Streamline the interface for intuitive navigation and operation. Fusion 360 is an example of software with an accessible UI.
Improve Simulation Features: Offer precise and detailed simulations to preemptively address potential machining issues. Mastercam Lathe provides advanced simulation capabilities.
Expand Tool Libraries: Include comprehensive, customizable tool libraries for faster setup and accurate tool selection. SolidCAM supports extensive libraries.
Integrate with CAD Software: Seamless integration with CAD software for smoother workflow from design to production. GibbsCAM offers strong CAD integration.
Offer Advanced Toolpath Strategies: Introduce efficient and sophisticated toolpath options to optimize machining time and tool life. CAMWorks features advanced toolpath strategies.
Facilitate Easy Post-Processor Customization: Ensure easy customization of post-processors to match specific machine requirements. BobCAD-CAM provides flexible post-processor options.
By focusing on these areas, CAM software can better meet the needs of lathe operators, leading to increased productivity and reduced machining time.
How to Display CAM Software Skills on Your Resume
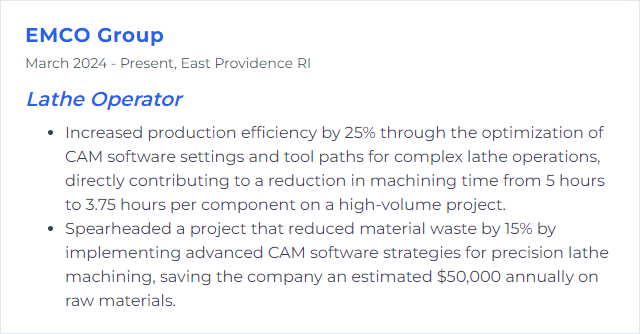
7. Manual Machining
Manual machining, in the context of a lathe operator, involves the hands-on operation of lathe machines to cut, shape, and finish materials into precise dimensions, relying on manual adjustments and controls, without computer automation.
Why It's Important
Manual machining is crucial for a Lathe Operator as it provides fundamental understanding of machining processes, enables precise custom work on unique or small-scale projects, and enhances problem-solving skills through hands-on experience with tools and materials.
How to Improve Manual Machining Skills
Improving manual machining skills, especially as a lathe operator, involves a combination of practice, knowledge enhancement, and proper tool management. Here are concise steps to follow:
Understand the Basics: Ensure a strong grasp of fundamental lathe operations and terminology. MIT's introduction to lathe offers a solid start.
Learn from Experts: Watch tutorial videos from experienced machinists. Channels like NYC CNC provide valuable insights and practical tips.
Practice Regularly: Consistent practice helps refine your skills. Start with simple projects and gradually increase complexity.
Tool Maintenance: Keep your tools sharp and well-maintained. This guide covers essential maintenance tips.
Measure Twice, Cut Once: Precision is key in machining. Use calipers and micrometers accurately to ensure your work meets specifications. MIT's Measuring Guide is a useful resource.
Safety First: Always adhere to safety protocols to prevent accidents. OSHA's Machine Guarding details crucial safety measures.
Join a Community: Engage with forums like Practical Machinist where you can ask questions, share experiences, and get advice from fellow machinists.
Improvement comes from a blend of continuous learning, diligent practice, and community engagement.
How to Display Manual Machining Skills on Your Resume
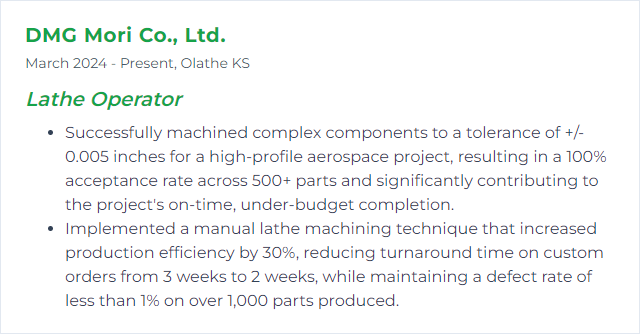
8. Quality Control
Quality Control for a Lathe Operator involves the process of ensuring that machined parts meet specified tolerance levels and quality standards through measurements and inspections during and after the machining process.
Why It's Important
Quality control is essential for a Lathe Operator to ensure the precision and accuracy of machined parts, reduce waste, minimize rework, and maintain customer satisfaction by delivering products that meet or exceed specifications and standards.
How to Improve Quality Control Skills
Improving Quality Control for a Lathe Operator can be achieved through the following concise steps:
Training & Education: Ensure ongoing training for operators on the latest lathe operation techniques and quality standards. Tooling U-SME offers a wide range of courses.
Regular Maintenance: Keep the lathe and tools in optimal condition through a routine maintenance schedule. Machinery Lubrication provides insights on proper machine maintenance.
Use of Quality Tools: Invest in high-quality cutting tools and measuring instruments. MSC Industrial Supply offers a variety of quality tools suitable for lathe operations.
Implement Standard Operating Procedures (SOPs): Develop and adhere to SOPs for consistent operations. ISO provides guidelines for establishing quality management systems.
Continuous Monitoring and Feedback: Utilize real-time monitoring tools for immediate quality control and provide regular feedback to operators. Fluke offers tools for precision measurement and quality control.
By focusing on these areas, a Lathe Operator can significantly improve the quality of their work and contribute to the overall success of their manufacturing processes.
How to Display Quality Control Skills on Your Resume
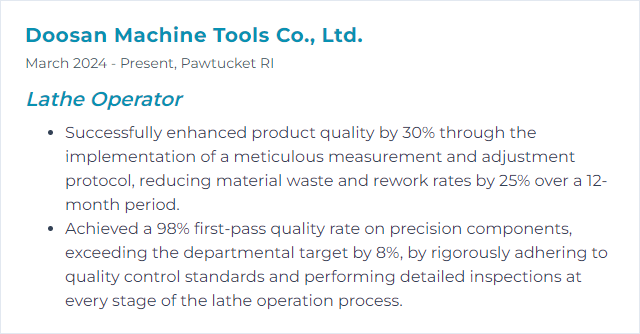
9. Safety Protocols
Safety protocols for a lathe operator include wearing personal protective equipment, ensuring machine guards are in place, maintaining a clean workspace, checking the lathe before use, using correct tooling and techniques, keeping hands clear of moving parts, and following all manufacturer and workplace safety guidelines to prevent accidents and injuries.
Why It's Important
Safety protocols for a lathe operator are critical to prevent accidents, injuries, and fatalities by minimizing exposure to hazards associated with the operation of lathes, such as entanglement, cuts, and flying debris. They ensure a safe working environment and protect the operator's well-being.
How to Improve Safety Protocols Skills
Improving safety protocols for a lathe operator involves a multi-faceted approach focusing on training, equipment maintenance, and personal protective equipment (PPE). Here's a concise guide:
Enhanced Training: Ensure that operators receive comprehensive safety training including machine operation, hazard recognition, and emergency procedures. Refresher courses should be mandatory.
Regular Maintenance: Implement a strict schedule for lathe maintenance to ensure all safety features are functional and the machine operates smoothly, reducing the risk of accidents.
Use of PPE: Require operators to use appropriate personal protective equipment, such as safety glasses, gloves (where safe and applicable), and ear protection, to mitigate risks from flying debris and noise.
Safety Signage: Place clear, visible safety signs around the lathe area, reminding operators of the dangers and the necessary precautions to take.
Emergency Protocols: Develop and regularly update emergency response procedures in case of an accident, ensuring all employees know how to act swiftly and efficiently.
By focusing on these key areas, safety protocols around lathe operations can be significantly improved, leading to a safer working environment.
How to Display Safety Protocols Skills on Your Resume
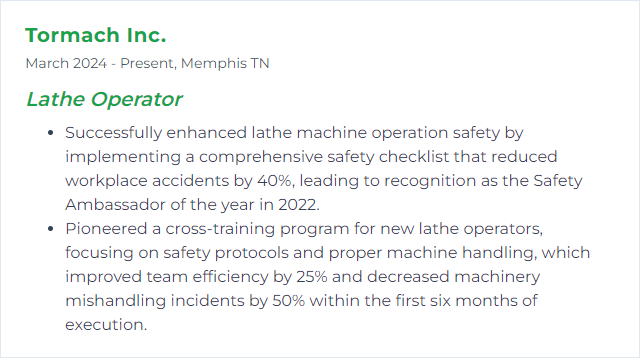
10. Fixture Design
Fixture design refers to the process of creating a specialized workholding device to securely position and support a workpiece during machining operations on a lathe, ensuring precision, repeatability, and safety.
Why It's Important
Fixture design is crucial for a lathe operator because it ensures accuracy, repeatability, and safety during machining operations by securely holding and positioning the workpiece.
How to Improve Fixture Design Skills
Improving fixture design, especially for a lathe operator, involves enhancing efficiency, accuracy, and safety. Here's a concise guide:
Analyze Requirements: Understand the workpiece's geometry, tolerances, and machining operations. This ensures the fixture design meets all machining needs.
Modularity and Flexibility: Design fixtures that are modular and adaptable for various workpieces to reduce setup time and cost. SMW Modular Fixtures offer insights into modular design principles.
Material Selection: Use durable materials for fixtures to withstand the machining environment and prolong their life. Carr Lane's Material Consideration Guide provides valuable material selection insights.
Incorporate Clamping Efficiency: Design clamps to secure the workpiece without deformation and allow for quick loading/unloading. DESTACO Clamping Technology showcases efficient clamping solutions.
Ergonomics and Safety: Ensure the fixture design is ergonomic for the operator, reducing fatigue and the risk of injury. OSHA's Ergonomics Guidelines can guide ergonomic considerations.
Precision and Stability: Design fixtures to maintain positional accuracy and stability during machining operations. Mitee-Bite's Fixture Clamps demonstrate how innovative clamping can enhance precision.
Simplify for Efficiency: Aim for simplicity to facilitate easy setup, operation, and maintenance. Haas Tip of the Day videos offer practical tips on efficient fixture setup.
Feedback and Continuous Improvement: Regularly gather feedback from lathe operators and incorporate improvements in future designs.
By focusing on these aspects, you can significantly improve fixture design for lathe operations, enhancing overall productivity and work quality.
How to Display Fixture Design Skills on Your Resume
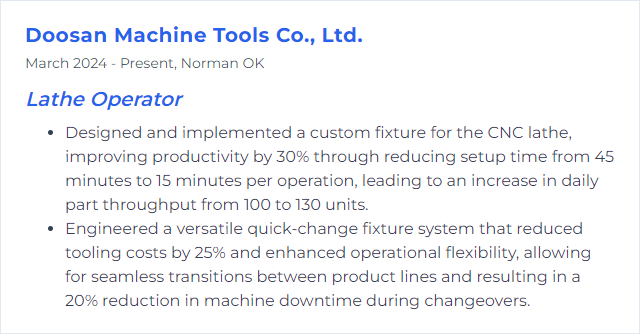
11. Tolerance Analysis
Tolerance analysis is the evaluation of the permissible limits of variation in the dimensions and geometry of manufactured parts, ensuring that they fit and function together as intended. For a lathe operator, it involves determining how much a part's size or position can vary from the specified dimensions without compromising the final product's quality or performance.
Why It's Important
Tolerance analysis is crucial for a Lathe Operator to ensure that machined parts meet precise specifications and fit together correctly in assemblies, minimizing waste and ensuring product quality and functionality.
How to Improve Tolerance Analysis Skills
To improve Tolerance Analysis as a Lathe Operator, focus on precision and consistency.
Understand Specifications: Carefully review and understand the tolerance specifications for each project. Engineering drawing standards provide a good starting point.
Regular Calibration: Ensure your lathe and measuring instruments are regularly calibrated. This calibration guide from NIST outlines best practices.
Use of Precision Tools: Invest in high-quality cutting tools and measuring instruments. Machining tutorials offer insights into selecting and using the right tools.
Skill Enhancement: Continuously improve your machining skills through online courses and training. Websites like Tooling U-SME offer specialized courses for lathe operators.
Implement Statistical Process Control (SPC): Use SPC to monitor and control your machining process. The ASQ resource provides a comprehensive overview.
Maintain Environmental Conditions: Ensure a stable working environment as temperature and humidity can affect material properties and machining accuracy. Refer to material handling guidelines for more details.
Review and Adjust: Regularly review your work against specifications and adjust your process based on feedback. Continuous improvement methodologies like Kaizen can guide these efforts.
By focusing on these areas, you can significantly improve tolerance analysis and overall machining accuracy.
How to Display Tolerance Analysis Skills on Your Resume
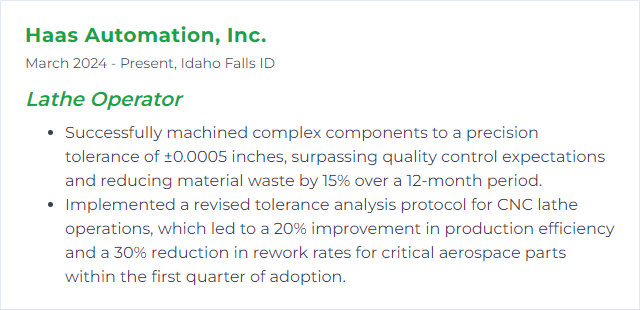
12. Machine Maintenance
Machine maintenance, in the context of a Lathe Operator, involves regular checking, cleaning, lubricating, and adjusting the lathe to ensure it operates efficiently and safely, preventing breakdowns and extending its service life.
Why It's Important
Machine maintenance is crucial for a Lathe Operator as it ensures the equipment operates efficiently and accurately, reduces the risk of breakdowns, prolongs the machine's lifespan, and ensures operator safety by preventing accidents caused by malfunctioning equipment.
How to Improve Machine Maintenance Skills
Improving machine maintenance, especially for a Lathe Operator, involves regular and systematic checks to ensure optimal functioning and longevity of the machinery. Here are concise steps:
Daily Inspections: Check for any abnormalities in noise, vibration, and temperature. Daily checks should include lubrication levels and the condition of cutting tools. Lathe Maintenance Schedule provides a basic checklist.
Scheduled Maintenance: Adhere to the manufacturer's maintenance schedule for tasks such as replacing filters, checking alignments, and recalibrating the machine. Machinery Lubrication offers insights into proper lubrication practices.
Cleanliness: Keep the machine and surrounding area clean to prevent the build-up of debris that can affect the machine's operation. OSHA Guidelines detail the importance of a clean work environment for safety and efficiency.
Training: Ensure operators are trained not only in operation but also in basic troubleshooting and maintenance tasks. Tooling U-SME provides industry-standard training modules for lathe operators.
Record Keeping: Maintain a log of all maintenance activities to help predict future failures and plan preventive maintenance. Maintenance Management Software can streamline this process.
By implementing these steps, a Lathe Operator can significantly improve the maintenance and reliability of their machinery.
How to Display Machine Maintenance Skills on Your Resume
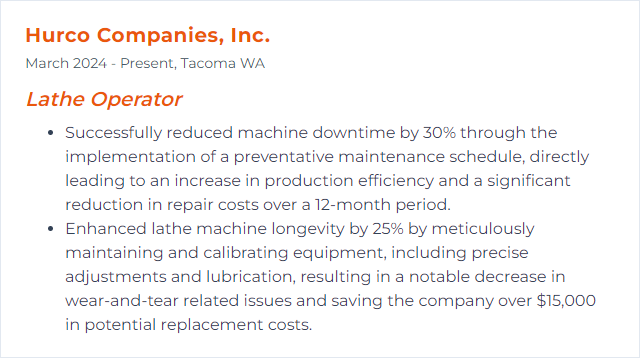