Top 12 Industrial Hygienist Skills to Put on Your Resume
In the field of occupational health and safety, industrial hygienists play a crucial role in identifying and mitigating workplace hazards. A strong resume showcasing a comprehensive set of industrial hygienist skills is essential for candidates aiming to excel in this vital profession and make a significant impact on workplace safety.
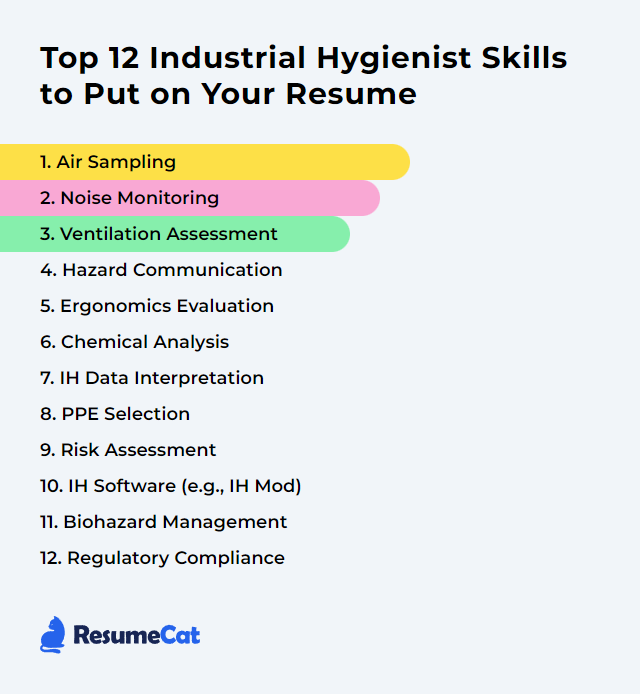
Industrial Hygienist Skills
- Air Sampling
- Noise Monitoring
- Ventilation Assessment
- Hazard Communication
- Ergonomics Evaluation
- Chemical Analysis
- IH Data Interpretation
- PPE Selection
- Risk Assessment
- IH Software (e.g., IH Mod)
- Biohazard Management
- Regulatory Compliance
1. Air Sampling
Air sampling is a method used by industrial hygienists to collect and analyze airborne contaminants to assess occupational exposure levels and ensure workplace air quality meets safety and health standards.
Why It's Important
Air sampling is crucial for an Industrial Hygienist to identify, quantify, and control airborne contaminants, ensuring workplace health and safety by preventing occupational diseases and meeting regulatory compliance.
How to Improve Air Sampling Skills
Improving air sampling for an Industrial Hygienist involves a few key steps aimed at ensuring accuracy, representativeness, and compliance with relevant standards. Here's a concise guide:
Select Appropriate Sampling Methods: Choose methods approved by agencies like NIOSH or OSHA, ensuring they match the specific contaminants and conditions of your workplace. NIOSH Manual of Analytical Methods (NMAM) is a valuable resource.
Use Correct Equipment: Ensure sampling equipment such as pumps, tubes, and filters is suitable for the target analytes and environmental conditions. Calibrate equipment regularly. SKC Inc. provides a variety of sampling equipment and guidance.
Optimize Sampling Location and Duration: Place samplers in the breathing zone for personal sampling or strategically in the area for area sampling. Follow guidelines for sampling duration to capture representative exposure levels. OSHA’s Technical Manual, Section II: Chapter 1 outlines personal sampling principles.
Ensure Quality Control: Implement a quality control program that includes field blanks, duplicate samples, and chain-of-custody documentation to ensure the integrity of samples and data. AIHA offers resources on quality control practices.
Stay Updated and Train Continuously: Regularly update your knowledge on new sampling technologies, regulations, and standards. Provide ongoing training for those involved in sampling to ensure best practices are followed.
Analyze Data Accurately and Report: Use accredited laboratories for sample analysis and report data in the context of relevant exposure limits and guidelines. Interpret results with a deep understanding of workplace processes and controls.
By focusing on these areas, an Industrial Hygienist can significantly improve the effectiveness of air sampling efforts in the workplace.
How to Display Air Sampling Skills on Your Resume
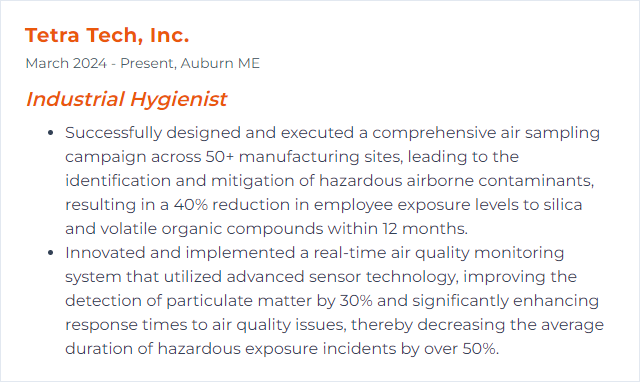
2. Noise Monitoring
Noise monitoring, in the context of an Industrial Hygienist, refers to the process of measuring and analyzing sound levels in the workplace to assess exposure risks to employees and ensure compliance with occupational noise standards, aiming to prevent hearing loss and protect worker health.
Why It's Important
Noise monitoring is crucial for an Industrial Hygienist to assess and manage occupational noise exposure risks, prevent hearing loss, and ensure compliance with legal safety standards, thereby safeguarding workers' health and productivity.
How to Improve Noise Monitoring Skills
Improving noise monitoring, especially for an Industrial Hygienist, involves adopting a strategic approach to accurately assess and manage noise exposure risks in the workplace. Here's a concise guide:
Utilize Advanced Monitoring Instruments: Employ the latest noise dosimeters and sound level meters that meet international standards (e.g., ANSI or IEC) for accuracy and reliability. 3M Science Applied to Life offers a range of advanced noise monitoring equipment.
Implement a Comprehensive Noise Assessment Strategy: Conduct regular and thorough noise assessments to identify sources of noise and employees at risk. The Centers for Disease Control and Prevention (CDC) provides guidelines on evaluating workplace noise.
Adopt Noise Mapping: Use noise mapping for a visual representation of noise levels across different areas, helping in identifying hotspots and planning control measures efficiently. The European Environment Agency (EEA) offers insights into noise mapping.
Engage in Continuous Education and Training: Educate employees about the risks of noise exposure and the importance of hearing conservation programs. Training should include the proper use of personal protective equipment (PPE) and adherence to noise control measures. Occupational Safety and Health Administration (OSHA) provides resources on hearing conservation programs.
Implement Engineering Controls: Whenever feasible, modify or replace noisy machinery with quieter alternatives, install sound barriers, or implement changes in the workflow to minimize noise exposure. National Institute for Occupational Safety and Health (NIOSH) offers guidance on engineering controls for noise.
Regularly Review and Update Noise Control Measures: Noise monitoring and control is an ongoing process. Regularly review the effectiveness of implemented measures and update them as necessary to ensure continuous improvement in noise management.
By combining advanced technology with a strategic approach to noise assessment and control, Industrial Hygienists can significantly improve workplace noise monitoring and protect workers from harmful noise exposure.
How to Display Noise Monitoring Skills on Your Resume
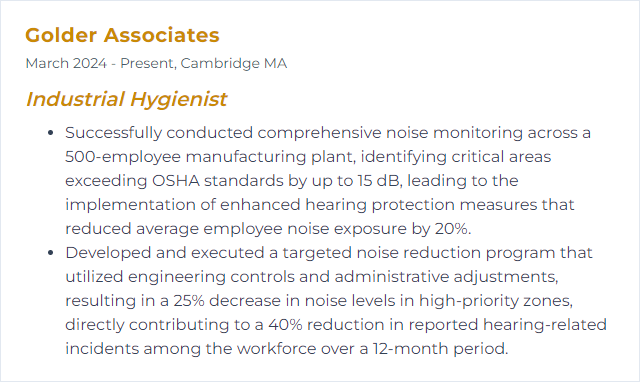
3. Ventilation Assessment
A Ventilation Assessment is an evaluation process conducted by an Industrial Hygienist to examine the efficiency and effectiveness of a workplace's ventilation system in controlling airborne contaminants and ensuring a healthy environment for employees. This involves measuring airflow, analyzing air quality, and identifying improvements to protect workers' health.
Why It's Important
Ventilation assessment is crucial for an Industrial Hygienist because it ensures the effective removal of hazardous substances and contaminants from the workplace, thereby protecting workers' health and safety by maintaining air quality within prescribed standards.
How to Improve Ventilation Assessment Skills
Improving ventilation assessment, especially for an Industrial Hygienist, involves a systematic approach that ensures the effective capture, control, and removal of airborne contaminants. Here’s a concise guide:
Understand and Map the Ventilation System: Begin with comprehensive documentation of the existing ventilation system layout, including all air inlets, exhausts, and air handling units. CDC Ventilation Guidance provides insights on assessing and improving ventilation.
Identify Contaminant Sources: Clearly identify all sources of air contaminants within the facility. This step is crucial for targeted ventilation improvements. The NIOSH Manual of Analytical Methods is a valuable resource for identifying and assessing workplace contaminants.
Measure Airflow and Pressure Relationships: Use anemometers and manometers to measure airflow rates and pressure differences across different areas. Understanding these dynamics is essential for effective ventilation. Guidelines on these measurements can be found in the ASHRAE Handbook.
Conduct Air Quality Assessments: Regularly monitor the air quality to identify particulate levels and gas concentrations. Tools and methodologies for these assessments are detailed in the EPA’s Indoor Air Quality Tools for Schools.
Evaluate Ventilation Effectiveness: Use tracer gas techniques or smoke tests to evaluate the effectiveness of the ventilation in capturing and removing contaminants. The AIHA’s Ventilation Manual provides practical guidance on these evaluation methods.
Implement Engineering Controls: Based on the assessment, implement engineering controls to improve air capture and removal. This could involve modifications to existing ventilation systems or the installation of local exhaust ventilation at contaminant sources.
Ensure Regular Maintenance and Review: Establish a routine maintenance schedule for all ventilation equipment and review the system's performance periodically. Changes in production processes or facility layout may necessitate adjustments to the ventilation system.
Educate and Train Staff: Ensure that all employees are aware of the importance of ventilation and how to maintain optimal air quality. Training resources are available through OSHA’s Training Services.
By following these steps and utilizing the resources provided, an Industrial Hygienist can significantly improve ventilation assessment and control airborne contaminants effectively.
How to Display Ventilation Assessment Skills on Your Resume
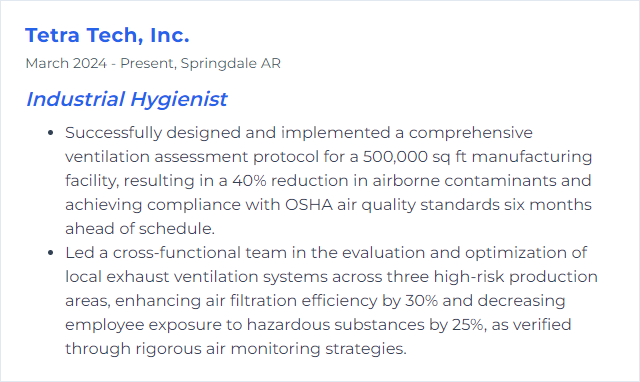
4. Hazard Communication
Hazard Communication (HazCom) is a regulatory requirement mandating the evaluation and communication of chemical hazards in the workplace to ensure the safety and health of workers, primarily through Safety Data Sheets (SDS), labeling, and training, which are critical components for an Industrial Hygienist in managing occupational health risks.
Why It's Important
Hazard Communication is crucial for Industrial Hygienists as it ensures the proper identification, evaluation, and communication of chemical hazards in the workplace, enabling the implementation of appropriate safety precautions to protect workers' health and prevent occupational diseases and injuries.
How to Improve Hazard Communication Skills
Improving Hazard Communication in an industrial setting, especially from the perspective of an Industrial Hygienist, involves several key strategies for ensuring workplace safety and compliance with regulations like the OSHA Hazard Communication Standard (HCS). Here's a concise guide:
Conduct Comprehensive Assessments: Regularly perform and update hazard assessments to identify and understand the types of hazardous chemicals in the workplace. Use resources like the NIOSH Pocket Guide to Chemical Hazards for detailed information.
Update Safety Data Sheets (SDS): Ensure that Safety Data Sheets for all hazardous chemicals are accessible, up-to-date, and comply with the OSHA HCS requirements. Regular training on how to read and understand SDS is crucial.
Labeling: Implement a consistent labeling system for all chemicals, following the Globally Harmonized System (GHS) of Classification and Labeling of Chemicals, ensuring labels are always legible and intact.
Employee Training and Education: Provide comprehensive, ongoing training for employees on hazard communication, including understanding labels, SDS, and the appropriate response to chemical exposures. OSHA provides guidelines and resources for effective training.
Emergency Preparedness: Develop and regularly update an emergency response plan for hazardous chemical exposures, including first aid measures, spill cleanup procedures, and emergency contact information.
Communication and Feedback Channels: Establish open channels for employees to report hazards, provide feedback, and ask questions regarding chemical safety. Encourage a culture of safety and open communication.
Review and Audit: Regularly review and audit the hazard communication program to ensure compliance and effectiveness. This includes checking for any changes in regulations and updating procedures accordingly.
Implementing these strategies can significantly enhance hazard communication in the workplace, reduce the risk of chemical exposures, and ensure compliance with relevant health and safety regulations.
How to Display Hazard Communication Skills on Your Resume
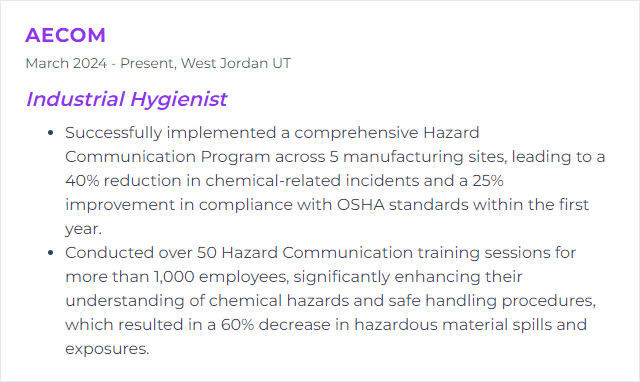
5. Ergonomics Evaluation
Ergonomics evaluation, in the context of an Industrial Hygienist, is the assessment of work environments and job tasks to identify and mitigate factors that might cause musculoskeletal injuries or discomfort, thereby improving worker safety, health, and productivity through the design of ergonomic workspaces.
Why It's Important
Ergonomics evaluation is crucial for an Industrial Hygienist because it helps identify and mitigate workplace risk factors that can lead to musculoskeletal disorders (MSDs), enhancing employee well-being, productivity, and reducing the likelihood of work-related injuries and associated costs.
How to Improve Ergonomics Evaluation Skills
Improving ergonomics evaluation, especially from the perspective of an Industrial Hygienist, involves a blend of direct observation, employee engagement, and the application of ergonomic assessment tools. Here's a concise guide:
Conduct Workplace Assessments: Start by observing the physical layout of the workspace and the tasks being performed. Use tools like the Rapid Entire Body Assessment (REBA) to evaluate the risk of musculoskeletal disorders.
Engage with Employees: Gather feedback directly from employees about any discomfort or issues they're experiencing. This can help identify less obvious ergonomic risks.
Implement Participatory Ergonomics: Involve employees in the process of identifying, assessing, and controlling ergonomic risks. This approach has been shown to improve workplace ergonomics effectively.
Use Ergonomic Assessment Tools: Leverage specific tools for evaluating ergonomic risks associated with tasks. The NIOSH Lifting Equation is an excellent resource for manual lifting tasks.
Continuous Education and Training: Provide ongoing education and training on ergonomics to all employees. The OSHA eTool for Ergonomics offers valuable insights and guidelines.
Adopt Technological Solutions: Utilize ergonomic evaluation software and apps that can streamline the assessment process. Tools like ErgoPlus can be particularly helpful.
Regular Review and Update of Ergonomic Practices: Ergonomics is an ongoing process. Regularly review and update your practices to accommodate new technologies, changes in workflows, and feedback from employees.
By following these steps, an Industrial Hygienist can significantly improve the ergonomics evaluation process, leading to a healthier, more productive workplace environment.
How to Display Ergonomics Evaluation Skills on Your Resume
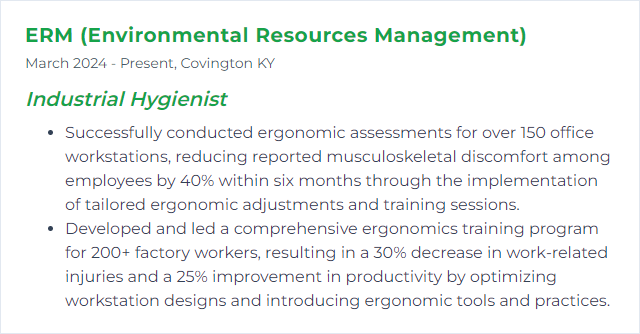
6. Chemical Analysis
Chemical analysis, in the context of an Industrial Hygienist, involves the systematic examination of materials and substances to identify their chemical components and concentrations, ensuring workplace safety and compliance with health regulations by detecting hazardous chemicals and assessing exposure risks.
Why It's Important
Chemical analysis is crucial for an Industrial Hygienist as it identifies and quantifies hazardous substances in the workplace, ensuring the health and safety of workers by enabling the implementation of appropriate exposure controls and compliance with regulatory standards.
How to Improve Chemical Analysis Skills
Improving chemical analysis for an Industrial Hygienist involves enhancing accuracy, sensitivity, and specificity of detection methods for workplace hazards. Here are concise strategies:
Upgrade Instrumentation: Invest in high-quality analytical instruments like GC-MS (Gas Chromatography-Mass Spectrometry) and HPLC (High-Performance Liquid Chromatography) for more precise chemical identification and quantification.
Regular Calibration and Maintenance: Ensure analytical equipment is regularly calibrated and maintained for accurate results (NIOSH).
Use Standardized Methods: Adopt standardized analysis methods from recognized bodies like OSHA or NIOSH for consistency and reliability.
Quality Control Samples: Regularly use quality control samples alongside real samples to monitor analysis accuracy and precision.
Training and Education: Continuously educate and train laboratory personnel on new analytical techniques and safety protocols. AIHA offers resources and courses for ongoing education.
Incorporate Software Tools: Use data management and analysis software to efficiently handle data and improve error detection (LIMS).
External Proficiency Testing: Participate in external proficiency testing programs to benchmark your laboratory’s performance against others and improve accuracy.
By implementing these strategies, an Industrial Hygienist can significantly enhance the effectiveness of chemical analysis in the workplace.
How to Display Chemical Analysis Skills on Your Resume
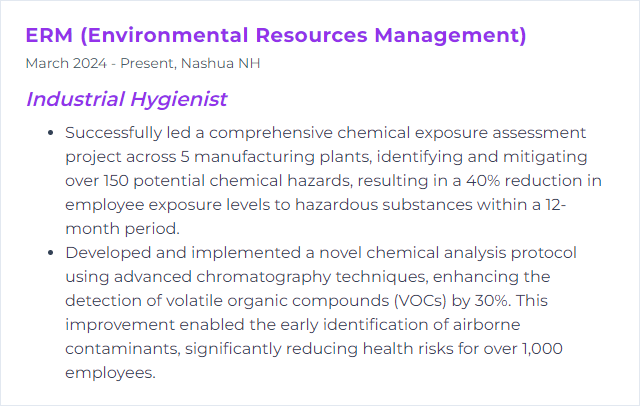
7. IH Data Interpretation
IH Data Interpretation refers to the process by which an Industrial Hygienist analyzes and evaluates data collected from workplace environments to identify hazards, assess exposure levels to chemicals, noise, and other potential risks, and determine compliance with occupational health standards. This involves the use of scientific methods and principles to make informed decisions for protecting worker health.
Why It's Important
Data interpretation in Industrial Hygiene (IH) is crucial because it enables the identification, evaluation, and control of workplace hazards, ensuring the health and safety of workers. By accurately analyzing data, Industrial Hygienists can develop effective strategies to mitigate exposure to harmful agents, thereby preventing occupational diseases and injuries.
How to Improve IH Data Interpretation Skills
Improving data interpretation skills as an Industrial Hygienist (IH) involves enhancing your ability to analyze, understand, and apply information derived from workplace assessments to protect worker health. Here’s a concise guide:
Strengthen Statistical Knowledge: A solid grasp of statistics is crucial for interpreting data accurately. Consider online courses or resources to brush up on statistical analysis techniques relevant to IH. Khan Academy’s Statistics and Probability offers free, high-quality tutorials.
Utilize IH Software Tools: Familiarize yourself with software tools designed for exposure assessment and data management. Tools like IH Data Analyst can help in interpreting and managing occupational exposure data more effectively.
Engage in Continuous Learning: Stay updated with the latest research and methodologies in industrial hygiene. Journals such as the Journal of Occupational and Environmental Hygiene provide valuable insights into current trends and case studies.
Practice Critical Thinking: Apply critical thinking to interpret data within the context of your specific work environment. This involves questioning assumptions, evaluating sources, and considering alternative interpretations.
Attend Workshops and Seminars: Participate in workshops and seminars focused on data interpretation and industrial hygiene. Professional bodies like the American Industrial Hygiene Association (AIHA) often host relevant educational events.
Network with Peers: Exchange knowledge and experiences with peers through forums and professional networks. The AIHA’s Catalyst community is a good place to start discussions and seek advice on data interpretation challenges.
By focusing on these areas, you can significantly improve your ability to interpret data in the context of industrial hygiene, leading to better decision-making and enhanced worker protection.
How to Display IH Data Interpretation Skills on Your Resume
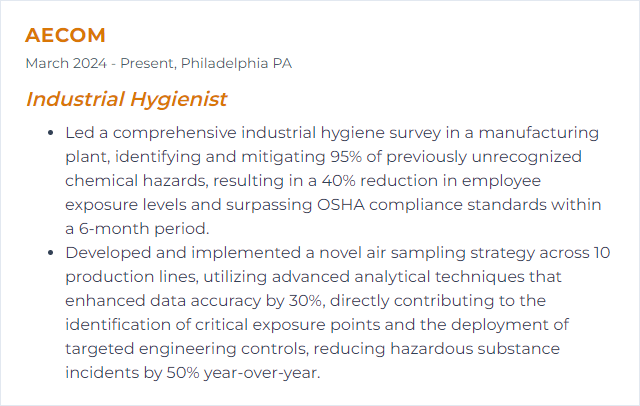
8. PPE Selection
PPE Selection refers to the process an Industrial Hygienist undertakes to choose appropriate Personal Protective Equipment (PPE) based on a thorough assessment of workplace hazards, to ensure the safety and health of employees from exposure to harmful substances or environments.
Why It's Important
PPE selection is crucial for ensuring worker safety by providing effective protection against specific hazards encountered in the workplace, thereby preventing occupational illnesses and injuries.
How to Improve PPE Selection Skills
Improving PPE (Personal Protective Equipment) selection, especially from the perspective of an Industrial Hygienist, involves a systematic and informed approach to ensure worker safety and compliance with regulatory standards. Here's a concise guide:
Hazard Identification: Begin by conducting a comprehensive risk assessment to identify potential hazards in the workplace. This involves understanding the types of chemicals, physical hazards, or biological agents workers might be exposed to. OSHA's Hazard Identification Training Tool can assist in this step.
PPE Standards and Guidelines: Familiarize yourself with relevant PPE standards and guidelines. The ANSI/ISEA Z87.1 standard for eye and face protection and NIOSH’s Respirator Selection Logic are critical references.
PPE Performance: Select PPE based on performance requirements against identified hazards. Ensure the PPE meets or exceeds the necessary protection levels, as outlined in standards like ASTM International for foot protection or the previously mentioned ANSI/ISEA for eye protection.
Fit Testing and Comfort: Ensure that PPE fits correctly and is comfortable for the user, which is crucial for compliance. Conduct regular fit-testing sessions, especially for respirators, as per OSHA’s Respiratory Protection standard.
Training and Education: Provide comprehensive training for workers on the correct use, maintenance, and limitations of their PPE. OSHA’s PPE Fact Sheet offers guidance on implementing an effective training program.
Continuous Review and Feedback: Establish a feedback loop with workers to continuously review and improve PPE selection and use. This ensures that PPE remains effective and user-friendly, encouraging compliance.
Consultation and Resources: Utilize resources from reputable organizations like NIOSH or the AIHA for the latest research and guidance on PPE and occupational health.
By following these steps, an Industrial Hygienist can ensure the selection of appropriate PPE that not only meets regulatory requirements but also enhances worker safety and health.
How to Display PPE Selection Skills on Your Resume
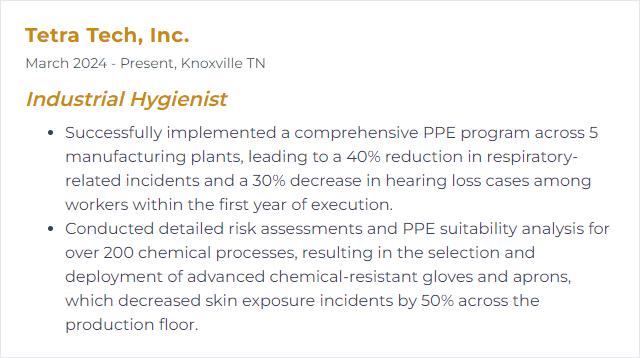
9. Risk Assessment
Risk assessment, in the context of an Industrial Hygienist, is the process of identifying, analyzing, and evaluating the potential hazards and risks in the workplace to determine their impact on workers' health and safety, and to devise appropriate control measures to minimize or eliminate those risks.
Why It's Important
Risk assessment is crucial for an Industrial Hygienist as it enables the identification, evaluation, and mitigation of workplace hazards, thereby protecting workers' health, ensuring compliance with safety regulations, and reducing the potential for occupational illnesses and injuries.
How to Improve Risk Assessment Skills
Improving risk assessment, particularly for an Industrial Hygienist, involves a systematic approach to identifying, evaluating, and controlling workplace hazards. Here's a concise guide:
Stay Updated with Standards: Regularly consult updated guidelines and standards from authoritative bodies like NIOSH and OSHA.
Comprehensive Hazard Identification: Employ a variety of methods such as workplace inspections, employee interviews, and review of safety data sheets (SDSs) to identify potential hazards.
Risk Analysis and Evaluation: Use tools like quantitative risk assessment methodologies to evaluate the severity and likelihood of hazards.
Implement Controls: Based on the hierarchy of controls, from elimination to PPE, implement the most effective control measures. Continuous monitoring and adjustment of these controls are crucial.
Training and Communication: Ensure all employees are trained on the risks and the precautions they need to take. Clear communication is key to compliance and safety.
Continuous Improvement: Adopt a culture of continuous improvement by regularly reviewing and updating risk assessments to reflect any changes in processes, technologies, or regulations.
These steps, rooted in the principles of industrial hygiene, ensure a proactive approach to workplace safety and health.
For further reading and resources, visiting professional bodies like the American Industrial Hygiene Association (AIHA) can provide valuable insights and tools for effective risk assessment and management.
How to Display Risk Assessment Skills on Your Resume
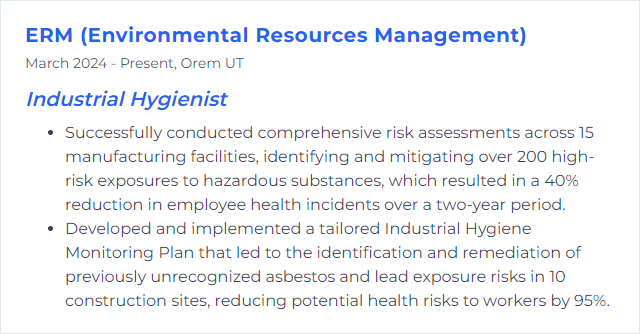
10. IH Software (e.g., IH Mod)
IH Software, such as IH Mod, refers to software tools designed for Industrial Hygienists to assess, analyze, and manage workplace environmental health and safety risks. These tools can help in calculating exposures, modeling hazardous conditions, and ensuring regulatory compliance.
Why It's Important
IH Software, such as IH Mod, is important for Industrial Hygienists as it provides essential tools for assessing and managing workplace environmental health and safety risks. It facilitates the accurate evaluation of chemical exposures, noise levels, and other hazards, allowing for the implementation of effective control measures to protect worker health.
How to Improve IH Software (e.g., IH Mod) Skills
To improve IH software such as IH Mod, consider the following concise strategies:
User Feedback Integration: Regularly collect and analyze user feedback to identify areas for enhancement and incorporate suggestions into updates. SurveyMonkey or Google Forms can facilitate this process.
Mobile Optimization: Ensure the software is fully optimized for mobile devices, enhancing accessibility for fieldwork. Resources on mobile optimization can be found on MDN Web Docs.
Data Security: Implement the latest security protocols to protect user data, referring to OWASP for best practices in web application security.
Interoperability: Enhance the software’s ability to work seamlessly with other tools and databases used by industrial hygienists, utilizing standards from Health Level Seven International (HL7).
Analytical Tools: Incorporate advanced analytical tools for data analysis, benchmarking against industry standards found on AIHA.
Customization: Allow users to customize dashboards and reports to meet their specific needs, drawing inspiration from customizable software design principles on Nielsen Norman Group.
Training and Support: Offer comprehensive online training and robust support to enhance user competency and software utilization, using platforms like Teachable for creating online courses.
Regular Updates: Keep the software up-to-date with the latest industry regulations and standards, referencing OSHA for regulatory updates.
AI and Machine Learning: Integrate AI for predictive analytics and machine learning for data insights, with foundational knowledge available from Coursera.
User Interface (UI) Improvement: Focus on making the UI more intuitive and user-friendly, utilizing UI design principles from Usability.gov.
Implementing these strategies requires a balance between technical innovation and practical application, always with the end-user’s needs in focus.
How to Display IH Software (e.g., IH Mod) Skills on Your Resume
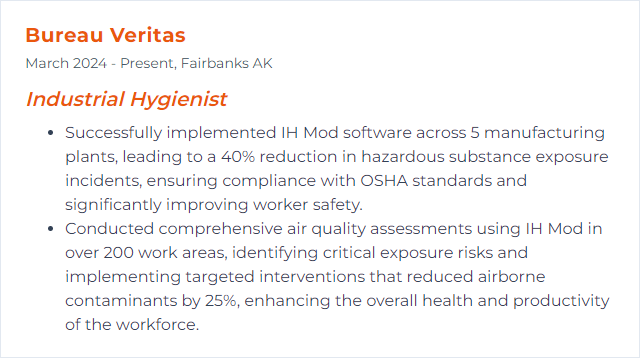
11. Biohazard Management
Biohazard management involves identifying, evaluating, and controlling biological hazards to prevent occupational exposure and ensure safety in the workplace. It includes procedures for handling, storage, disposal of biohazardous materials, and emergency response, tailored to protect workers and the environment from harmful biological agents.
Why It's Important
Biohazard management is crucial for an Industrial Hygienist to prevent exposure to harmful biological substances that can cause infections, illnesses, and environmental contamination, ensuring workplace safety and public health.
How to Improve Biohazard Management Skills
Improving biohazard management requires a comprehensive approach that involves assessment, control, and continuous education. Here are key strategies tailored for an Industrial Hygienist:
Risk Assessment: Conduct thorough risk assessments to identify potential biohazards. Utilize resources from CDC's Biosafety Home for guidelines on assessing laboratory biosafety levels.
Implement Control Measures: Apply the hierarchy of controls starting with elimination, substitution, engineering controls, administrative controls, and finally, personal protective equipment (PPE). The OSHA’s Control and Prevention page offers detailed guidance.
Proper Use of PPE: Ensure proper selection, use, and disposal of PPE. Training resources are available at NIOSH’s Personal Protective Equipment page.
Emergency Preparedness and Response: Develop and regularly update an emergency response plan for biohazard incidents. WHO’s Laboratory Biosafety Manual provides a framework for emergency planning.
Training and Education: Continuously educate and train staff on biohazard management, emphasizing new protocols and technologies. The APIC offers resources for infection prevention and control.
Waste Management: Implement a safe and compliant biohazard waste management system. Refer to EPA’s Medical and Infectious Waste for regulations and guidelines.
Regular Audits and Monitoring: Conduct regular biohazard management system audits and air monitoring to ensure ongoing compliance and effectiveness. Tools and guidelines can be found on AIHA’s website.
Communication and Reporting: Maintain open lines of communication for reporting hazards and incidents. Familiarize yourself with OSHA’s Reporting requirements for workplace illnesses and injuries.
By implementing these strategies, an Industrial Hygienist can significantly improve biohazard management in their workplace, ensuring the safety and health of all employees.
How to Display Biohazard Management Skills on Your Resume
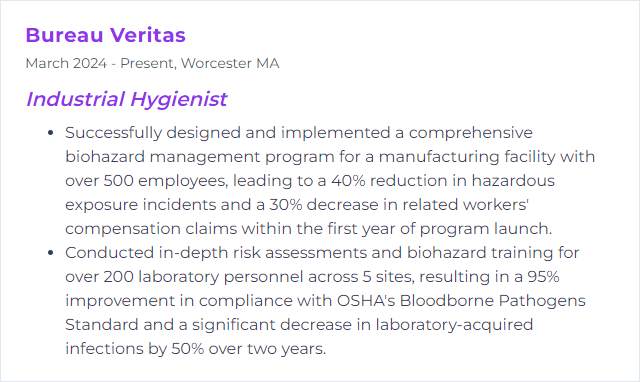
12. Regulatory Compliance
Regulatory compliance, in the context of an Industrial Hygienist, refers to adhering to laws, regulations, and standards that govern workplace health and safety, ensuring the well-being of workers by managing and mitigating exposure to hazardous substances and conditions.
Why It's Important
Regulatory compliance is important for an Industrial Hygienist because it ensures the safety and health of workers by adhering to standards that minimize exposure to hazardous substances and conditions, thereby reducing the risk of occupational illnesses and injuries.
How to Improve Regulatory Compliance Skills
Improving regulatory compliance for an Industrial Hygienist involves staying updated on regulations, conducting regular risk assessments, employee training, and maintaining accurate records. Here are key steps:
Stay Updated: Regularly review updates from regulatory bodies like OSHA and NIOSH to ensure compliance with current standards.
Risk Assessments: Conduct thorough risk assessments to identify potential hazards and implement control measures to mitigate risks.
Employee Training: Provide comprehensive training to employees on safety protocols and the importance of compliance as outlined by OSHA’s Training Requirements.
Record Keeping: Maintain accurate records of risk assessments, training, incidents, and corrective actions taken to ensure compliance and facilitate audits.
Compliance Audits: Regularly conduct internal or external compliance audits to identify areas of improvement and ensure adherence to regulatory requirements.
Engage with Professionals: Join professional organizations like the American Industrial Hygiene Association (AIHA) for resources, updates, and networking with peers.
By following these steps, an Industrial Hygienist can strengthen regulatory compliance within their organization.
How to Display Regulatory Compliance Skills on Your Resume
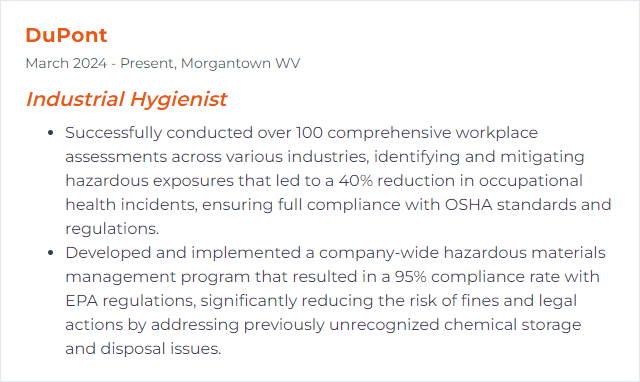