Top 12 Health and Safety Manager Skills to Put on Your Resume
In today's competitive job market, being an effective Health and Safety Manager requires a distinct set of skills that not only ensure compliance with regulations but also foster a culture of safety and well-being in the workplace. Highlighting these top skills on your resume can significantly enhance your appeal to prospective employers, demonstrating your capability to manage complex safety programs and mitigate risks efficiently.
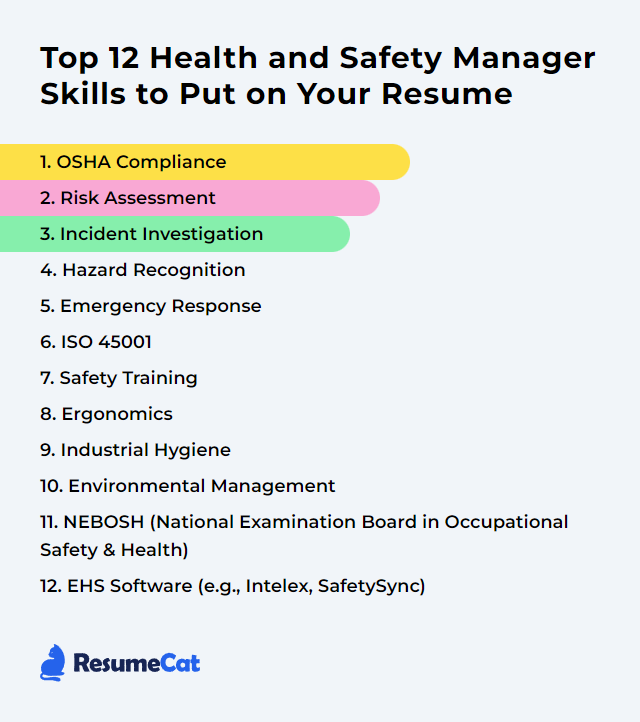
Health and Safety Manager Skills
- OSHA Compliance
- Risk Assessment
- Incident Investigation
- Hazard Recognition
- Emergency Response
- ISO 45001
- Safety Training
- Ergonomics
- Industrial Hygiene
- Environmental Management
- NEBOSH (National Examination Board in Occupational Safety and Health)
- EHS Software (e.g., Intelex, SafetySync)
1. OSHA Compliance
OSHA compliance refers to adhering to the standards and regulations set forth by the Occupational Safety and Health Administration (OSHA) to ensure workplace safety and health. For a Health and Safety Manager, it involves implementing, managing, and monitoring safety programs and practices to prevent workplace injuries and illnesses, and ensuring that the organization complies with all applicable OSHA regulations.
Why It's Important
OSHA compliance is crucial for a Health and Safety Manager as it ensures a safe and healthy work environment, minimizes the risk of accidents and occupational illnesses, and protects the organization from legal issues and potential fines.
How to Improve OSHA Compliance Skills
Improving OSHA compliance involves a proactive approach to workplace safety and health management. Here are concise steps for a Health and Safety Manager:
Conduct Regular Training: Ensure employees receive ongoing safety training relevant to their roles, emphasizing hazard recognition and prevention.
Perform Risk Assessments: Regularly carry out risk assessments to identify workplace hazards and implement control measures.
Stay Informed on Regulations: Keep up-to-date with the latest OSHA standards and regulations by visiting the OSHA Law and Regulations page.
Implement a Safety Management System: Develop and maintain a comprehensive safety management system that includes employee participation, hazard identification, and continuous improvement. Guidelines can be found in OSHA's Recommended Practices for Safety and Health Programs.
Ensure Proper Recordkeeping: Maintain accurate records of work-related injuries and illnesses as required by OSHA's Recordkeeping Rule.
Conduct Internal Audits: Regularly perform internal audits to evaluate compliance with OSHA standards and identify areas for improvement.
Engage with Employees: Encourage employee participation in safety programs and establish a system for them to report hazards or safety concerns anonymously.
Prepare for OSHA Inspections: Understand the OSHA inspection process and have a plan in place for handling inspections. The OSHA Inspection Fact Sheet provides useful information.
By following these steps, Health and Safety Managers can effectively improve OSHA compliance, thereby reducing the risk of violations and enhancing the overall safety of the workplace.
How to Display OSHA Compliance Skills on Your Resume
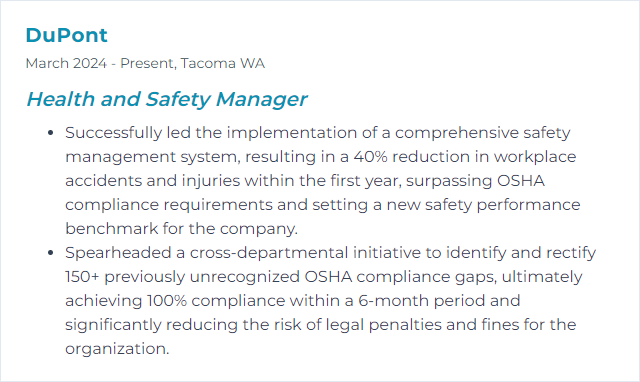
2. Risk Assessment
Risk assessment is the process of identifying, analyzing, and evaluating potential hazards to prevent workplace accidents, injuries, and illnesses, ensuring the safety and well-being of employees.
Why It's Important
Risk assessment is crucial for a Health and Safety Manager as it identifies potential hazards, evaluates the likelihood of accidents or health issues, and aids in implementing preventive measures to protect employees and comply with legal safety standards.
How to Improve Risk Assessment Skills
Improving risk assessment involves a strategic approach to identifying, analyzing, and controlling hazards in the workplace. Here's a concise guide for a Health and Safety Manager:
Identify Hazards: Begin by observing the workplace, reviewing incident reports, and consulting with employees. Tools like the CDC’s Workplace Health Model can provide a comprehensive framework for identifying potential hazards.
Risk Analysis: Evaluate how likely it is for each hazard to cause harm and the severity of the potential harm. The Risk Assessment Matrix from OSHA (pg. 20) can be a useful tool in this step.
Control Measures: Implement the hierarchy of controls, starting with elimination and substitution, followed by engineering controls, administrative controls, and PPE. The NIOSH Hierarchy of Controls offers guidance on prioritizing risk control measures.
Training and Communication: Ensure that all employees are aware of the risks and the measures in place to mitigate them. Engage them in safety training tailored to their roles.
Review and Update: Continually monitor the workplace for new hazards and review the effectiveness of control measures. The ISO 45001 standard emphasizes the importance of an ongoing, proactive process.
Documentation and Compliance: Keep detailed records of your risk assessments and control measures. Follow local regulations and standards, like those provided by OSHA.
By systematically identifying hazards, analyzing risks, implementing controls, and engaging in continuous improvement, Health and Safety Managers can significantly enhance workplace safety.
How to Display Risk Assessment Skills on Your Resume
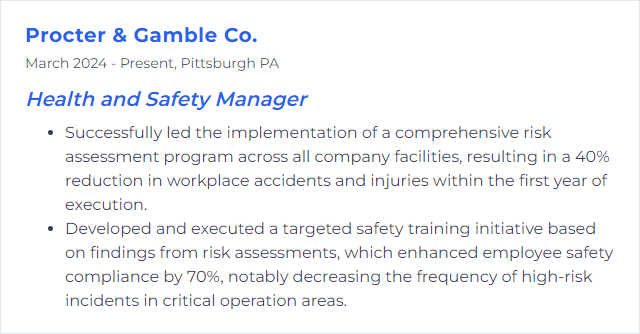
3. Incident Investigation
Incident investigation, from the perspective of a Health and Safety Manager, is the systematic process of identifying the root causes of workplace incidents, accidents, or near misses, with the aim of implementing measures to prevent future occurrences and improve safety protocols.
Why It's Important
Incident investigation is crucial for a Health and Safety Manager because it identifies root causes of accidents or near-misses, preventing future occurrences, ensuring compliance with regulations, and maintaining a safe working environment for all employees.
How to Improve Incident Investigation Skills
Improving incident investigation involves a structured approach focused on identifying root causes and implementing effective measures to prevent recurrence. For a Health and Safety Manager, here are concise steps:
Preparation: Ensure you have the necessary tools, forms, and training. Familiarize yourself with the Incident Investigation Guidelines from OSHA.
Immediate Response: Secure the scene, provide medical care, and notify relevant authorities. Refer to Emergency Response Planning for guidelines.
Data Collection: Gather evidence, interview witnesses, and document findings. The CDC's Workplace Safety & Health Topics offer tools for data collection and analysis.
Analysis: Identify root causes using methods such as the "Five Whys" or Fishbone Diagram. Resources on root cause analysis can be found at the ASSE (now ASSP).
Report and Action Plan: Develop a clear report and action plan to address root causes. The NIOSH provides templates and examples.
Follow-Up: Monitor the effectiveness of implemented actions and make adjustments as necessary. Continuous improvement strategies can be reinforced through resources like the ISO 45001 standards on occupational health and safety management.
Remember, the goal is not only to investigate but to prevent future incidents through proactive measures and a culture of safety.
How to Display Incident Investigation Skills on Your Resume
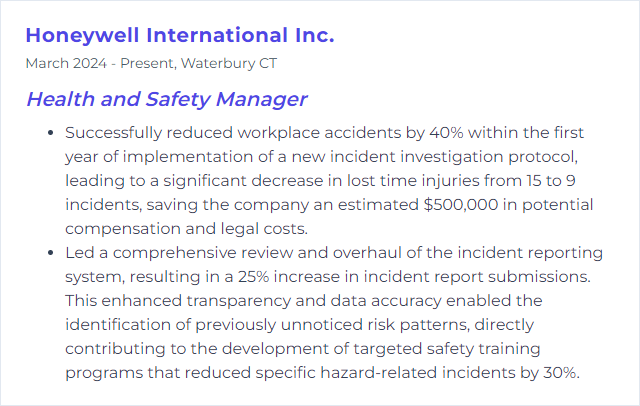
4. Hazard Recognition
Hazard recognition is the process of identifying potential sources of harm or danger in the workplace, aiming to prevent accidents, injuries, and illnesses. It involves assessing work environments, processes, and practices to pinpoint risks that could affect the health and safety of employees.
Why It's Important
Hazard recognition is crucial for a Health and Safety Manager as it enables the proactive identification and mitigation of potential risks, ensuring a safe working environment and preventing accidents, injuries, and occupational illnesses.
How to Improve Hazard Recognition Skills
Improving hazard recognition involves a combination of training, observation, and continuous improvement. Here's a concise guide:
Training: Invest in comprehensive safety training programs for all employees, focusing on hazard identification, risk assessment, and the importance of reporting. Regularly update these programs to reflect current best practices.
Risk Assessments: Conduct regular risk assessments to identify potential hazards in the workplace. Encourage employee participation to gain diverse perspectives on potential risks.
Safety Audits: Perform frequent safety audits to evaluate the effectiveness of current hazard control measures and identify areas for improvement.
Incident Reporting System: Establish an easy-to-use incident reporting system that encourages employees to report hazards without fear of retribution. Analyze reports to identify trends and areas requiring attention.
Continuous Learning: Stay informed about new hazards and safety innovations by engaging with professional safety organizations and health and safety forums. Share relevant findings with your team.
Safety Culture: Foster a positive safety culture where everyone feels responsible for hazard recognition and prevention. Recognize and reward proactive safety behaviors.
By integrating these strategies, Health and Safety Managers can significantly improve hazard recognition in the workplace.
How to Display Hazard Recognition Skills on Your Resume
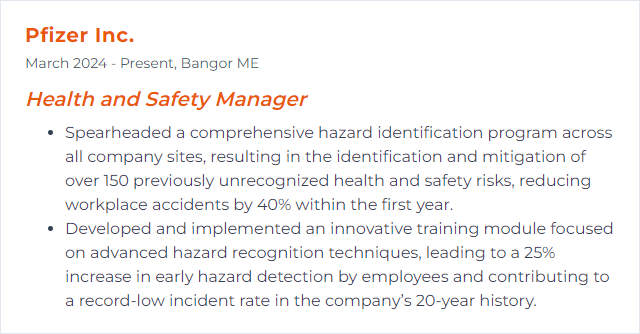
5. Emergency Response
Emergency Response in the context of a Health and Safety Manager refers to the organized and immediate actions taken to address unforeseen incidents or accidents at the workplace, aiming to minimize harm to individuals, property, and the environment. This includes planning, coordination, and execution of safety measures and procedures to effectively manage and mitigate the impacts of emergencies.
Why It's Important
Emergency response is crucial for promptly addressing incidents, minimizing harm, ensuring employee safety, and maintaining regulatory compliance, thus safeguarding both personnel and organizational integrity.
How to Improve Emergency Response Skills
Improving emergency response involves a multi-faceted approach focusing on preparedness, training, communication, and continuous improvement. Here's a concise guide for a Health and Safety Manager:
Assess and Plan: Conduct a comprehensive risk assessment to identify potential emergencies. Develop clear, actionable emergency response plans tailored to these risks. FEMA's guide offers a solid starting point.
Training and Drills: Regularly train employees on emergency procedures, including evacuation routes, assembly points, and the use of emergency equipment. Conduct drills periodically to ensure readiness. The Occupational Safety and Health Administration (OSHA) provides resources for training and exercises.
Communication Systems: Implement efficient communication systems to alert and instruct employees during an emergency. Consider options like mass notification systems. Ready.gov has guidelines on crisis communications planning.
Emergency Equipment: Ensure easy access to emergency equipment like fire extinguishers, first aid kits, and AEDs. Regularly inspect and maintain these tools. The National Fire Protection Association (NFPA) offers standards and codes for fire safety and emergency equipment.
Review and Improve: After drills or actual emergencies, debrief and identify areas for improvement. Adjust plans and training as necessary to address any shortcomings. The Centers for Disease Control and Prevention (CDC) provides a guide for reviewing and updating plans.
By focusing on these key areas, Health and Safety Managers can significantly enhance their organization's emergency response capabilities.
How to Display Emergency Response Skills on Your Resume
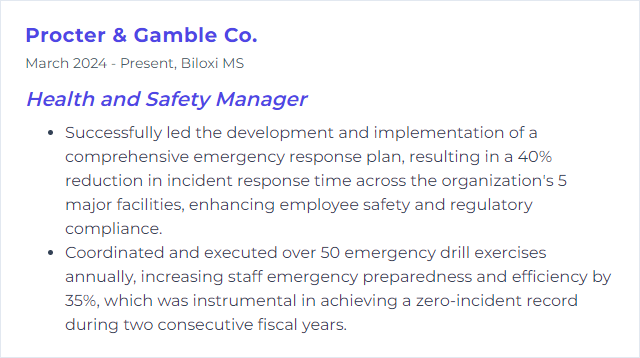
6. ISO 45001
ISO 45001 is an international standard for occupational health and safety management systems, designed to help organizations improve employee safety, reduce workplace risks, and create better, safer working conditions.
Why It's Important
ISO 45001 is important for a Health and Safety Manager because it provides a globally recognized framework for managing occupational health and safety risks, ensuring compliance, and promoting a safe and healthy workplace environment. It helps in systematically reducing workplace hazards and enhancing employee well-being.
How to Improve ISO 45001 Skills
Improving ISO 45001, the international standard for occupational health and safety management systems, involves continuous evaluation and enhancement of your organization's health and safety practices. Here are concise steps for a Health and Safety Manager:
Gap Analysis: Conduct a thorough gap analysis against ISO 45001 requirements to identify areas of improvement. ISO 45001 Gap Analysis Guide
Employee Engagement: Increase employee participation and consultation in the safety management process. Empower workers to identify hazards and suggest improvements. Effective Worker Engagement
Training and Competence: Enhance employee competence through regular, relevant health and safety training. OSH Training Guidelines
Risk Management: Improve the identification, assessment, and control of workplace risks using a proactive approach. Implement and regularly update risk assessment methodologies. Risk Management Guide
Performance Monitoring: Implement key performance indicators (KPIs) to measure and monitor health and safety performance. Regularly review and analyze these metrics for continuous improvement. KPI Examples
Management Review: Conduct regular management reviews of the OH&S management system to ensure its continuing suitability, adequacy, and effectiveness. Adjust policies and objectives as necessary. Management Review Guidance
Internal Audits: Perform regular internal audits to ensure compliance with ISO 45001 and to identify opportunities for improvement. ISO 19011 Guidelines for Auditing
Incident Investigation: Enhance incident investigation processes to identify root causes and implement corrective actions, preventing recurrence. Incident Investigation Guide
Legal Compliance: Regularly review and ensure compliance with applicable legal and other requirements. Use compliance tracking tools and regularly update your legal register. Compliance Management Guide
Continuous Improvement: Foster a culture of continuous improvement within the organization, using tools like Plan-Do-Check-Act (PDCA) cycle and Six Sigma. Continuous Improvement Guide
By taking these steps, Health and Safety Managers can enhance their organization's occupational health and safety performance, aligning with ISO 45001's requirements and beyond.
How to Display ISO 45001 Skills on Your Resume
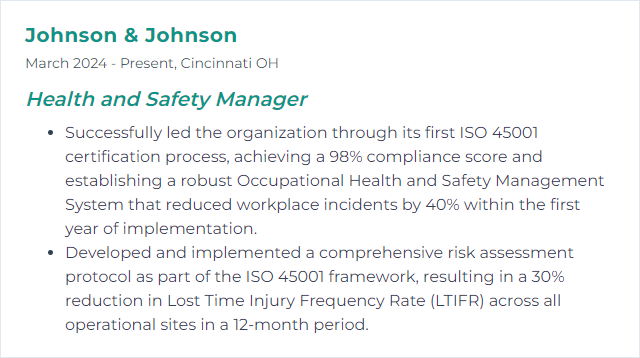
7. Safety Training
Safety training is a program designed to educate employees on the necessary procedures, practices, and behaviors to prevent accidents and injuries in the workplace, ensuring a safe and healthy environment.
Why It's Important
Safety training is essential as it equips employees with knowledge and skills to perform their tasks safely, reducing the risk of accidents and injuries in the workplace. This not only promotes a healthy work environment but also ensures compliance with safety regulations, minimizing legal liabilities and enhancing overall productivity.
How to Improve Safety Training Skills
Improving safety training involves a strategic approach that ensures the information is engaging, accessible, and relevant. Here are concise strategies for a Health and Safety Manager to enhance safety training:
Identify Specific Needs: Conduct a hazard assessment to tailor the training to address the specific risks your workers face. OSHA’s Hazard Identification Training Tool can help in identifying workplace hazards.
Adopt Blended Learning: Combine traditional classroom training with online modules to cater to different learning styles and schedules. The National Safety Council offers a variety of courses that can supplement in-person training.
Interactive Training Methods: Use simulations, virtual reality (VR), and interactive quizzes to increase engagement and retention. Tools like SafetySkills provide interactive online safety training options.
Regular Updates and Refreshers: Keep training materials up-to-date with the latest regulations and best practices. EHS Insight offers tips on keeping safety training effective and current.
Measure and Adapt: Use surveys, quizzes, and practical assessments to measure the effectiveness of your training programs. Tools like SurveyMonkey can help gather feedback.
Foster a Safety Culture: Encourage open communication about safety and make training an ongoing conversation. SafeStart provides resources on creating a culture of safety.
Utilize Peer-to-Peer Learning: Encourage experienced employees to share their knowledge and experiences with newer team members. This approach can foster a more engaged learning environment.
Leverage Industry Resources: Stay informed about industry trends and resources. The Center for Construction Research and Training (CPWR) offers a wealth of information for the construction industry, for example.
By implementing these strategies, Health and Safety Managers can enhance the effectiveness of their safety training programs, ensuring that employees are well-prepared to identify and mitigate risks in the workplace.
How to Display Safety Training Skills on Your Resume
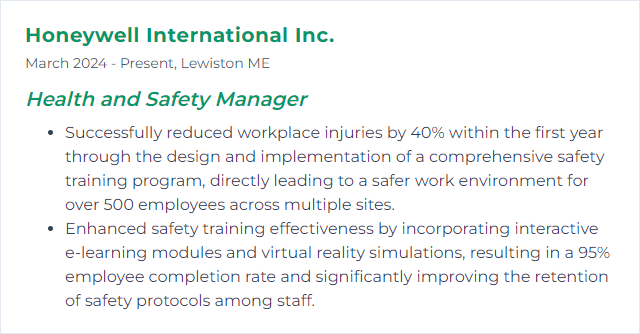
8. Ergonomics
Ergonomics is the science of designing work environments to fit the physical capabilities of workers, aiming to enhance efficiency and reduce the risk of injuries.
Why It's Important
Ergonomics is crucial for preventing work-related injuries, enhancing productivity, and promoting employees' overall well-being and comfort, thereby reducing healthcare costs and absenteeism.
How to Improve Ergonomics Skills
Improving ergonomics involves analyzing and designing workspaces, tools, and tasks to fit employees, enhancing both their safety and productivity. Here are concise steps for a Health and Safety Manager:
Conduct Ergonomic Assessments: Regularly evaluate workstations and tasks to identify ergonomics issues. Use tools like the Rapid Upper Limb Assessment (RULA) for quick analysis.
Provide Ergonomic Training: Educate employees on the importance of ergonomics and proper posture. The Occupational Safety and Health Administration (OSHA) offers resources and guidelines.
Implement Ergonomic Solutions: Adjust furniture, equipment, and work processes. Consider adjustable desks or chairs and ergonomic tools. The Human Factors and Ergonomics Society provides insights on effective solutions.
Encourage Regular Breaks: Implement short, frequent breaks to reduce muscle fatigue and strain. Tools like the Pomodoro Technique can help manage this.
Promote Physical Activity: Encourage stretching or light exercises during breaks to keep muscles active. Simple guides, like the Mayo Clinic’s Desk Exercises, can be shared with employees.
Monitor and Iterate: Continuously monitor the effectiveness of implemented ergonomic solutions and make adjustments as needed. Feedback forms and regular check-ins can help gauge progress.
By focusing on these areas, a Health and Safety Manager can significantly improve workplace ergonomics, leading to a healthier, safer, and more productive environment.
How to Display Ergonomics Skills on Your Resume
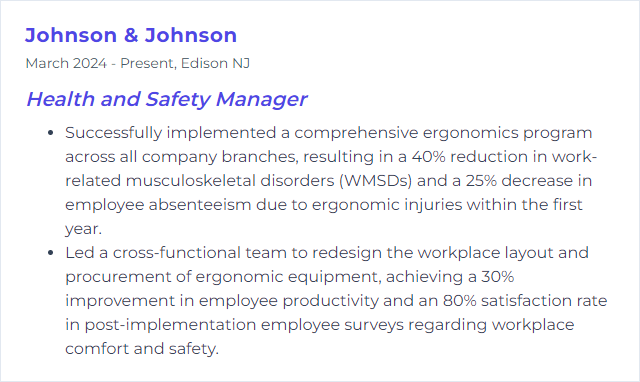
9. Industrial Hygiene
Industrial Hygiene is the science of anticipating, recognizing, evaluating, and controlling workplace conditions that may cause workers' injury or illness. It involves implementing measures to mitigate environmental hazards, ensuring the health and safety of employees.
Why It's Important
Industrial Hygiene is crucial as it protects workers from health hazards, ensuring a safe and productive workplace, thereby reducing the risk of occupational diseases and accidents, and ensuring compliance with health and safety regulations.
How to Improve Industrial Hygiene Skills
Improving industrial hygiene involves several key steps aimed at minimizing occupational health risks within the workplace. As a Health and Safety Manager, focus on these core strategies:
Assessment: Conduct comprehensive hazard assessments to identify potential health risks, including chemical, physical, and biological hazards.
Control Measures: Implement appropriate control measures following the hierarchy of controls, prioritizing elimination and substitution, followed by engineering controls, administrative controls, and personal protective equipment (PPE).
Training and Education: Provide ongoing training and education for employees on the correct use of PPE, safe work practices, and emergency procedures.
Monitoring: Regularly monitor the workplace environment for hazardous agents and conditions, ensuring that controls are effective and exposures are below permissible exposure limits (PELs).
Medical Surveillance: Implement a medical surveillance program to monitor workers’ health, focusing on those exposed to significant health risks.
Recordkeeping and Analysis: Maintain accurate records of exposure data, medical examinations, and training activities. Regularly analyze this data to identify trends and areas for improvement.
Continuous Improvement: Foster a culture of continuous improvement by regularly reviewing and updating health and safety policies, procedures, and programs based on the latest regulations, standards, and best practices.
By prioritizing these actions, Health and Safety Managers can significantly improve industrial hygiene, thereby reducing health risks and enhancing employee well-being in the workplace.
How to Display Industrial Hygiene Skills on Your Resume
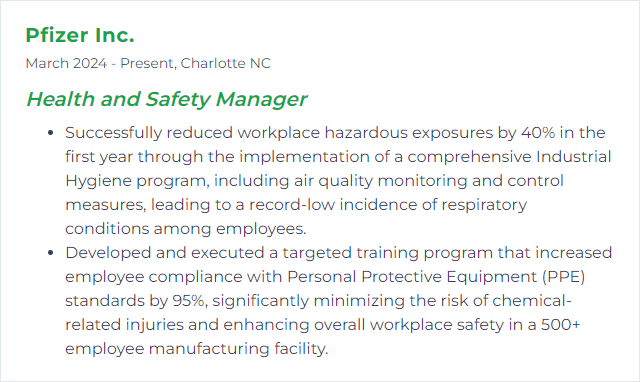
10. Environmental Management
Environmental Management involves the systematic approach to minimizing the environmental impact of an organization's operations, ensuring compliance with environmental laws, and promoting sustainable practices, all of which are critical for a Health and Safety Manager to protect worker health, safety, and the surrounding environment.
Why It's Important
Environmental Management is crucial for a Health and Safety Manager as it ensures the workplace operates within legal and ethical frameworks, minimizing environmental hazards and health risks to employees, and promoting a sustainable and safe working environment.
How to Improve Environmental Management Skills
Improving environmental management, especially from a Health and Safety Manager's perspective, involves a strategic approach focused on compliance, sustainability, and continuous improvement. Here are concise steps with relevant resources:
Stay Informed: Keep abreast of environmental laws and regulations to ensure compliance. This includes understanding local, national, and international standards.
Conduct Regular Environmental Audits: Assess your organization's environmental impact regularly. Tools like ISO 14001 can guide the establishment of an effective Environmental Management System (EMS).
Implement Sustainable Practices: Reduce waste, conserve resources, and minimize environmental footprints. Initiatives can include recycling programs, energy efficiency projects, and sustainable sourcing. The Environmental Protection Agency (EPA) offers resources on sustainability.
Employee Training & Engagement: Educate employees on environmental policies and practices. Engage them in sustainability goals. Resources like OSHA’s Training Services can be invaluable for developing appropriate training programs.
Monitor and Improve: Use environmental performance indicators to track progress. Regularly review and adjust policies, procedures, and objectives to enhance environmental performance.
Stakeholder Engagement: Collaborate with stakeholders, including local communities, suppliers, and customers, to promote broader environmental goals. The Global Reporting Initiative (GRI) provides standards for transparent and accountable reporting.
Emergency Preparedness: Develop and maintain an emergency response plan for environmental incidents, ensuring quick and effective action to minimize impacts.
By integrating these strategies into daily operations, Health and Safety Managers can significantly improve their organization's environmental management practices.
How to Display Environmental Management Skills on Your Resume
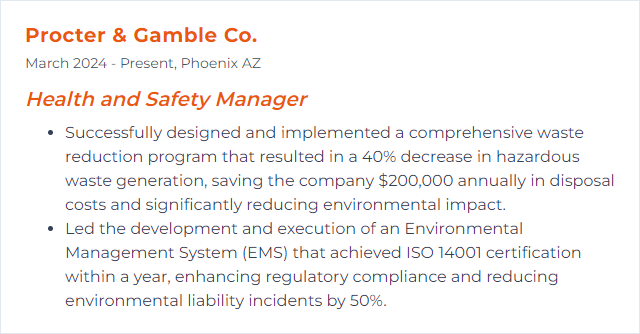
11. NEBOSH (National Examination Board in Occupational Safety and Health)
NEBOSH (National Examination Board in Occupational Safety and Health) is a globally recognized body that provides qualifications and courses in health, safety, and environmental management, designed to raise the competence of safety and environmental professionals as well as individuals at all working levels. For a Health and Safety Manager, achieving NEBOSH certification can signify a strong foundation in managing workplace safety and health risks effectively.
Why It's Important
NEBOSH is important for a Health and Safety Manager because it provides internationally recognized qualifications that demonstrate a comprehensive understanding of occupational health and safety principles and practices, enabling them to manage risks effectively and ensure a safe working environment.
How to Improve NEBOSH (National Examination Board in Occupational Safety and Health) Skills
Improving your NEBOSH qualifications as a Health and Safety Manager involves continuous learning, practical experience, and leveraging resources effectively. Here’s a concise guide:
Engage in Continuous Professional Development (CPD): Enhance your knowledge and skills through CPD activities like webinars, seminars, and workshops relevant to health and safety.
Utilize NEBOSH Study Materials: Access official NEBOSH study materials and resources for up-to-date information and exam preparation.
Gain Practical Experience: Apply your knowledge in real-world situations to understand complex safety issues, developing practical solutions.
Join Professional Networks: Connect with other professionals through platforms like LinkedIn and IOSH to exchange knowledge and experiences.
Seek Mentorship: Find a mentor experienced in health and safety to provide guidance, feedback, and insights into industry best practices.
Practice Exam Questions: Regularly practice with past exam questions to improve your exam technique and time management.
Stay Updated with Legislation: Keep abreast of the latest health and safety legislation and guidelines through official websites like HSE (Health and Safety Executive) for UK regulations.
By focusing on these areas, you can enhance your NEBOSH qualifications and effectiveness as a Health and Safety Manager.
How to Display NEBOSH (National Examination Board in Occupational Safety and Health) Skills on Your Resume
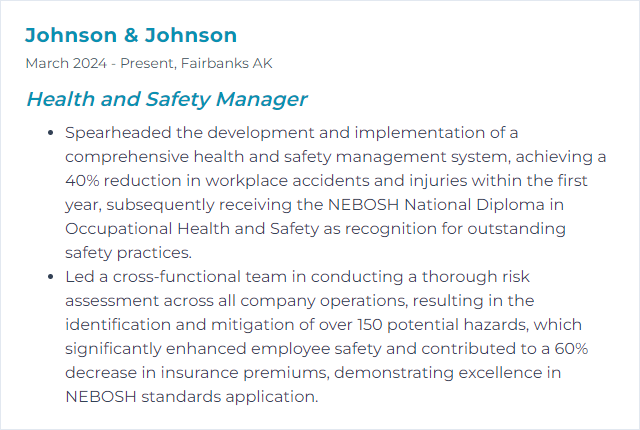
12. EHS Software (e.g., Intelex, SafetySync)
EHS Software, such as Intelex and SafetySync, is a digital tool designed to help organizations manage and improve their Environmental, Health, and Safety programs. It streamlines compliance, risk assessment, incident management, and reporting processes, aiding Health and Safety Managers in maintaining safer work environments.
Why It's Important
EHS Software, such as Intelex and SafetySync, is crucial for Health and Safety Managers as it streamlines compliance, risk management, and incident reporting processes, enhancing workplace safety and operational efficiency.
How to Improve EHS Software (e.g., Intelex, SafetySync) Skills
Improving EHS (Environmental, Health, and Safety) software, such as Intelex or SafetySync, involves enhancing usability, integration, customization, and analytics capabilities. Here's a concise guide for Health and Safety Managers to elevate their EHS software solutions:
User Experience (UX) Upgrade: Prioritize intuitive navigation and mobile-friendly design to ensure that employees at all levels can efficiently use the software. Intelex’s UX approach offers insights into designing for end-users.
Enhanced Integration: Ensure the software can seamlessly integrate with existing systems (HR, Operations, etc.) for a unified management approach. SafetySync’s features page highlights integration capabilities.
Customization: Opt for software that allows customization to fit your organization's unique EHS needs, including custom forms, workflows, and reports. Explore Intelex’s Platform Capabilities for customization options.
Advanced Analytics: Implement software with robust analytics and reporting tools for real-time data analysis and decision-making. SafetySync’s analytics demonstrate how data can drive safety improvements.
Continuous Training: Invest in ongoing training for users to maximize the software’s potential. Utilize resources like Intelex’s Training to keep your team updated.
Feedback Mechanism: Establish a feedback loop with users to continually refine and improve the software’s functionality and user experience.
By focusing on these areas, Health and Safety Managers can significantly enhance the effectiveness of their EHS software, leading to better compliance, improved safety outcomes, and a more engaged workforce.
How to Display EHS Software (e.g., Intelex, SafetySync) Skills on Your Resume
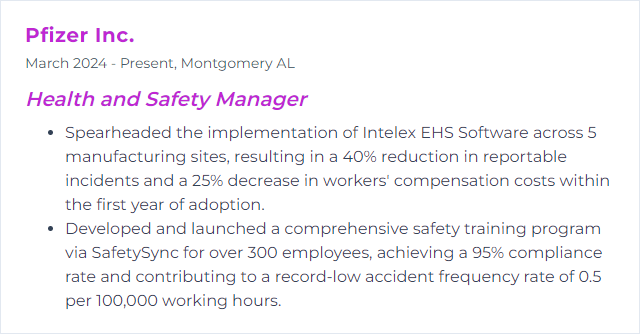