Top 12 Bindery Operator Skills to Put on Your Resume
In the competitive field of print production, a bindery operator's resume must highlight a unique set of technical and soft skills that demonstrate their proficiency and efficiency in bookbinding and finishing processes. Showcasing these top skills not only reflects an applicant's expertise and attention to detail but also sets them apart in the eyes of potential employers in the dynamic printing industry.
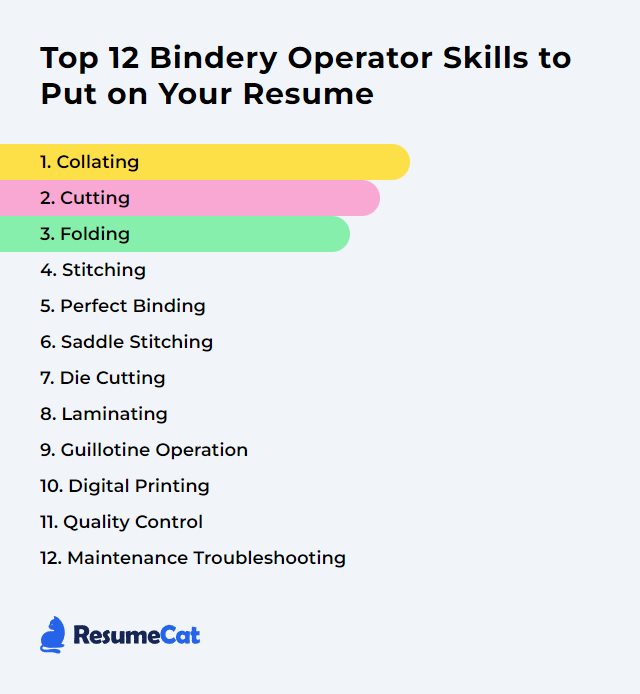
Bindery Operator Skills
- Collating
- Cutting
- Folding
- Stitching
- Perfect Binding
- Saddle Stitching
- Die Cutting
- Laminating
- Guillotine Operation
- Digital Printing
- Quality Control
- Maintenance Troubleshooting
1. Collating
Collating in the context of a Bindery Operator refers to the process of gathering and arranging individual sheets or sections of a publication in the correct order before binding.
Why It's Important
Collating is crucial for a Bindery Operator because it ensures that pages or sheets are arranged in the correct sequence before they are bound together, guaranteeing the final product is organized and accurate for the end-user.
How to Improve Collating Skills
To enhance collating efficiency as a Bindery Operator, focus on these key strategies:
Routine Maintenance: Regularly clean and maintain your collating machines to ensure optimal performance and minimize downtime.
Proper Setup: Invest time in proper setup and adjustments based on the project requirements to reduce errors and rework.
Quality Checks: Implement frequent quality checks throughout the collating process to catch and correct issues early.
Training: Continuously upgrade your skills and knowledge of the latest collating techniques and machinery.
Efficiency Practices: Adopt lean manufacturing principles to streamline your workflow and reduce waste.
By focusing on these areas, you can significantly improve the collating process in your bindery operations.
How to Display Collating Skills on Your Resume

2. Cutting
Cutting, in the context of a Bindery Operator, refers to the process of trimming printed materials to their desired size or shape using precise cutting equipment.
Why It's Important
Cutting is essential for a Bindery Operator as it ensures precision in trimming materials to the correct size and shape, achieving high-quality finishes, and facilitating the accurate assembly of printed products.
How to Improve Cutting Skills
Improving cutting in a bindery environment focuses on precision, efficiency, and safety. Here’s a concise guide to enhancing your cutting skills:
Maintain Equipment: Regularly sharpen blades and ensure cutting machines are properly calibrated. (Printing Impressions)
Measure Twice, Cut Once: Always double-check measurements before cutting to minimize errors. (Bindery Success Blog)
Use the Right Tools: Utilize the correct cutting tools and accessories tailored for the specific job. (Graphics Arts Magazine)
Follow Safety Protocols: Adhere to all safety guidelines to prevent accidents. (Printing Industries of America)
Continuous Learning: Stay updated with new cutting techniques and technologies. (PrintWeek)
Quality Control: Implement a quality check system to catch and correct errors early. (WhatTheyThink)
Improving cutting skills is an ongoing process that combines the mastery of technology, the precision of techniques, and the rigor of safety and quality standards.
How to Display Cutting Skills on Your Resume
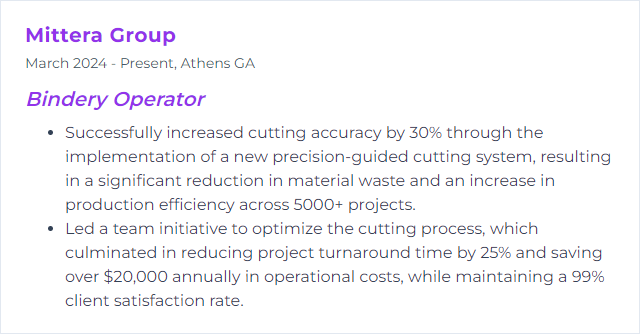
3. Folding
Folding in the context of a Bindery Operator involves precisely creasing paper or other materials along designated lines to form specific shapes or to prepare them for binding, mailing, or packaging, ensuring the final product meets quality standards and specifications.
Why It's Important
Folding is crucial for a Bindery Operator because it ensures that printed materials are accurately and precisely folded according to specifications, contributing to the final presentation and functionality of the product, such as books, brochures, and pamphlets.
How to Improve Folding Skills
Improving folding in a bindery operation involves enhancing both the accuracy and efficiency of the folding process. Here are concise steps with inline links for a Bindery Operator:
Maintain Equipment: Regularly clean and maintain your folding machines. Follow the manufacturer's guidelines for maintenance and adjustments. Heidelberg's maintenance tips offer valuable insights.
Proper Setup: Ensure the folding machine is correctly set up for the specific job. Accurate alignment and fold plate settings are crucial. Technifold USA provides setup tips and accessories that can help.
Quality Control: Implement a quality control process to catch errors early. Use samples to test settings before running the entire batch. The Printing Industries of America offers resources on quality standards.
Operator Training: Invest in continuous training for operators. Knowledge of machine intricacies and troubleshooting can drastically reduce downtime and errors. APTech's education programs are a great place to start.
Use Correct Paper: Match the paper type with the job requirements and machine capabilities. Paper quality can affect the fold outcome significantly. Mohawk Connects offers a guide on choosing the right paper.
Monitor Humidity and Temperature: Keep the working environment at optimal conditions for paper handling, as this can affect the folding process. Trotec Laser provides insights into managing these environmental factors.
By focusing on these areas, a Bindery Operator can significantly improve the folding process, leading to higher quality products and increased productivity.
How to Display Folding Skills on Your Resume
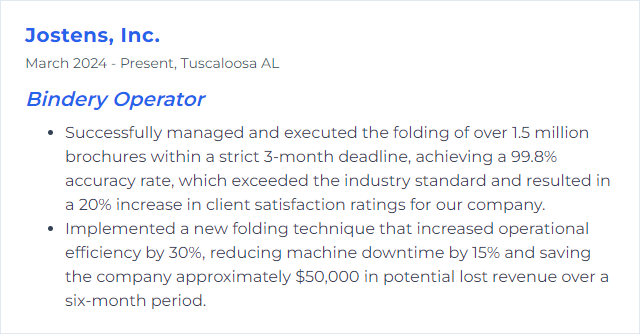
4. Stitching
Stitching, in the context of a Bindery Operator, refers to the process of using wire staples to fasten together pages of a booklet, brochure, or document to create a bound finish.
Why It's Important
Stitching is crucial for a Bindery Operator as it ensures the pages of a book, brochure, or pamphlet are securely fastened together, enhancing the durability and professional appearance of the final product.
How to Improve Stitching Skills
Improving stitching in a bindery operation focuses on ensuring quality control, maintaining equipment, and refining techniques. Here are concise steps:
Regular Maintenance: Keep your stitching machines well-maintained. Regular cleaning and servicing prevent malfunctions and ensure smooth operation. Machine Maintenance Guide.
Quality Control Checks: Implement rigorous quality control checks at every stage of the stitching process. This helps in identifying and correcting issues early. Quality Control in Print Production.
Operator Training: Continually train operators on the latest stitching techniques and machinery updates. Well-trained operators can significantly improve stitching quality. Bindery Training Resources.
Proper Setup and Calibration: Ensure machines are correctly set up and calibrated for the specific job at hand. Incorrect settings can lead to poor stitching quality. Calibration Techniques.
Use Quality Materials: The quality of thread, needles, and other consumables directly impacts the final stitch quality. Invest in high-quality materials. Choosing the Right Supplies.
Monitor Speed: Sometimes decreasing the machine speed can improve stitch quality, especially for complex or thick materials. Speed Adjustment Tips.
By focusing on these areas, a Bindery Operator can significantly improve the stitching quality in their projects.
How to Display Stitching Skills on Your Resume
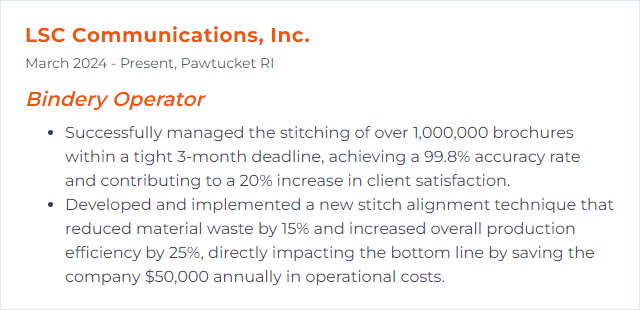
5. Perfect Binding
Perfect binding is a method where the pages of a document are glued together at the spine with a strong, flexible adhesive, and the cover is then attached, creating a flat spine. As a bindery operator, you would prepare the pages, apply the adhesive, attach the cover, and ensure a clean, professional finish.
Why It's Important
Perfect binding is important for a Bindery Operator because it offers a professional and durable finish, allowing for the production of high-quality, attractive books and documents with a flat spine that can be printed on, enhancing their marketability and shelf appeal.
How to Improve Perfect Binding Skills
To improve perfect binding, a Bindery Operator can follow these concise steps:
Ensure Proper Spine Preparation: Use a milling or notching machine for consistent spine roughening, enhancing adhesive penetration.
Select the Right Adhesive: Choose EVA or PUR glue based on book usage and durability requirements.
Control Spine Thickness: Accurately measure and adjust the book block and cover to avoid spine crush or weak binds, with guidelines available here.
Maintain Optimal Temperature and Humidity: Adhesive performance can vary; ensure your working environment is stable. This study outlines the importance of environmental conditions.
Regular Machine Maintenance: Keep equipment clean and well-maintained for consistent quality. Follow the manufacturer’s maintenance schedule.
Use Quality Materials: Invest in high-quality paper and covers that are compatible with your binding method, as advised by paper manufacturers.
Test Regularly: Conduct regular binding tests to ensure strength and durability, adjusting techniques and materials as necessary.
By focusing on these key areas, Bindery Operators can achieve superior perfect binding results.
How to Display Perfect Binding Skills on Your Resume
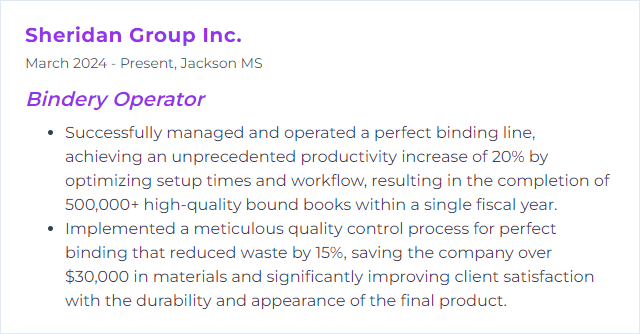
6. Saddle Stitching
Saddle stitching is a binding process where folded sheets are gathered together one inside the other and then stapled through the fold line with wire staples. This method is commonly used for binding booklets, magazines, and catalogs.
Why It's Important
Saddle stitching is crucial for a Bindery Operator as it offers a quick, cost-effective method for assembling booklets, brochures, and catalogs, ensuring a neat, professional finish suitable for various printing projects.
How to Improve Saddle Stitching Skills
To improve saddle stitching as a Bindery Operator, focus on these concise strategies:
Preparation: Ensure all materials are properly sorted and aligned before stitching. Heidelberg offers insights on machine setup.
Machine Calibration: Regularly check and adjust the stitching machine for consistent stitch length and alignment. Spiel Associates provides guidelines on machine maintenance.
Quality Control: Implement a system for periodic checks during the run to catch and correct issues early. Print Finishing Partners offers resources on maintaining quality standards.
Operator Training: Continuous learning and training on new techniques and machinery can enhance efficiency. Printing Industries of America provides training resources.
Optimize Workflow: Streamline the process from printing to stitching to ensure smooth transitions and reduce downtime. Xerox discusses workflow optimization.
By focusing on these areas, a Bindery Operator can significantly improve the quality and efficiency of saddle stitching operations.
How to Display Saddle Stitching Skills on Your Resume
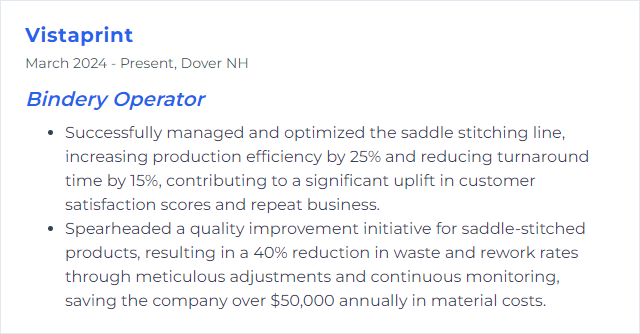
7. Die Cutting
Die cutting is a precision cutting process used in bindery operations to shape and cut materials into specific designs or outlines using a customized, sharp steel blade formed into a specific pattern, known as a die. This process is widely used for creating detailed cuts and shapes in paper, cardboard, and other materials for packaging, labels, and various print products.
Why It's Important
Die cutting is crucial for a Bindery Operator as it enables precise and consistent cutting of materials into specific shapes or sizes, enhancing the quality and efficiency of creating various printed materials or packaging.
How to Improve Die Cutting Skills
Improving die cutting as a Bindery Operator involves several key strategies to ensure precision, efficiency, and quality in the cutting process:
Regular Maintenance: Keep the die-cutting machine well-maintained. Regularly check and replace dull blades or dies to ensure clean cuts. Maintenance Guide.
Material Preparation: Properly prepare materials before die cutting. Ensure paper stock is acclimated to the environment to prevent misfeeds or jams. Material Handling Tips.
Die Test Runs: Perform test runs with new dies or materials to adjust for pressure and alignment. This helps in minimizing waste. Die Testing Best Practices.
Training and Skills Development: Continually upgrade your skills and knowledge on die-cutting techniques and advancements. Participate in workshops or online courses. Operator Training.
Use High-Quality Dies: Invest in high-quality dies that match your specific cutting requirements. This can significantly improve the precision and lifespan of your cuts. Choosing the Right Die.
Optimize Workflow: Streamline the workflow by organizing workstations, scheduling regular maintenance, and ensuring materials are readily available. Efficiency in workflow can reduce downtime and increase productivity. Workflow Optimization Tips.
By focusing on these areas, a Bindery Operator can significantly improve the quality and efficiency of the die-cutting process.
How to Display Die Cutting Skills on Your Resume
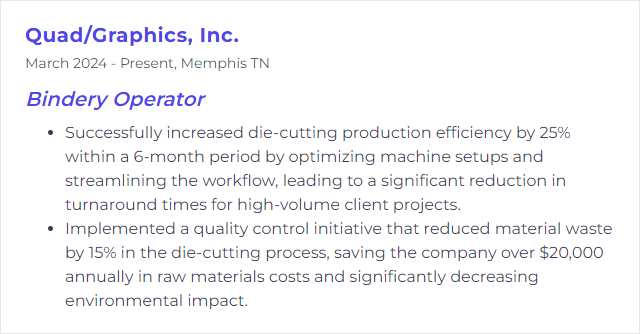
8. Laminating
Laminating, in the context of a Bindery Operator, is the process of applying a thin layer of plastic film to printed materials to protect and enhance their durability and appearance.
Why It's Important
Laminating is important for a Bindery Operator because it protects printed materials from damage, enhances durability, and improves aesthetic appeal, ensuring longevity and quality of the finished product.
How to Improve Laminating Skills
Improving laminating as a Bindery Operator involves optimizing both the technique and equipment for better efficiency and quality. Here are concise steps to enhance your laminating process:
Machine Calibration: Regularly check and calibrate your laminator for consistent temperature and pressure, ensuring optimal adhesion and finish. Laminator Calibration Guide.
Material Quality: Use high-quality laminating film and substrates suitable for your specific project, affecting the durability and appearance of the final product. Choosing Laminating Films.
Proper Cleaning: Keep the laminator rollers clean to prevent defects. Regular cleaning maintains quality and extends the machine's lifespan. Cleaning Laminator Rollers.
Speed and Temperature Adjustment: Adjust the laminator's speed and temperature according to the material and type of laminate being used. Optimal settings reduce imperfections. Adjusting Speed and Temperature.
Preventive Maintenance: Schedule regular maintenance to prevent breakdowns and ensure the laminator operates efficiently. Laminator Maintenance Tips.
Training and Practice: Continuously learn and practice. Staying updated with new techniques and materials can significantly enhance your laminating skills. Laminating Techniques.
By focusing on these key areas, a Bindery Operator can significantly improve the quality and efficiency of their laminating process.
How to Display Laminating Skills on Your Resume
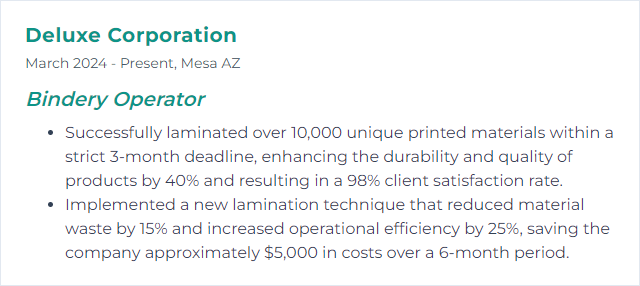
9. Guillotine Operation
In the context of a Bindery Operator, a Guillotine Operation refers to the process of using a guillotine cutter to trim or cut large stacks of paper or other materials to precise sizes with a straight edge, typically as part of the finishing process in print production.
Why It's Important
The guillotine operation is important for a Bindery Operator because it ensures precise and efficient cutting of paper materials to the exact specifications required for high-quality bookbinding and finishing tasks.
How to Improve Guillotine Operation Skills
Improving guillotine operation in a bindery environment involves enhancing safety, accuracy, and efficiency. Here are concise recommendations:
Safety: Always follow the manufacturer's safety guidelines. Regularly check and maintain safety guards and features. Occupational Safety and Health Administration (OSHA) provides resources on machine operation safety.
Maintenance: Keep the guillotine well-maintained. Sharpen and replace blades as needed to ensure clean cuts. Printing Industries of America offers maintenance tips specific to printing equipment.
Accuracy: Use programming features for repeat jobs and ensure material is properly aligned. Graphic Arts Magazine periodically shares tips and tricks for improving accuracy in print operations.
Efficiency: Organize workflow to minimize turnaround time. Implementing a lean manufacturing approach can streamline processes. The Lean Enterprise Institute provides resources on lean principles in manufacturing.
Training: Ensure operators are properly trained. Continual training on new techniques and safety practices is crucial. PrintSkills offers specialized training for the printing industry.
By focusing on these aspects, a Bindery Operator can significantly improve the operation of a guillotine, enhancing productivity and safety.
How to Display Guillotine Operation Skills on Your Resume
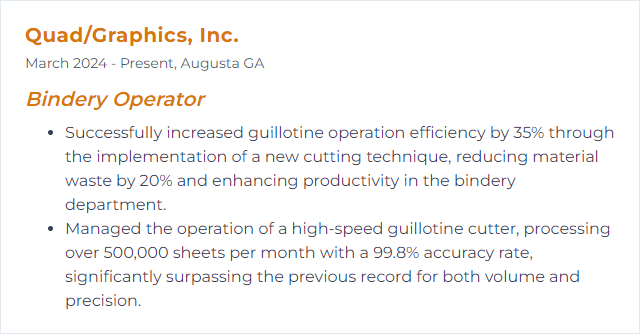
10. Digital Printing
Digital printing is a method of printing from a digital-based image directly to a variety of media. For a Bindery Operator, it means handling materials that are printed using non-impact printers, requiring finishing processes like cutting, folding, or binding without the need for plates or setup time associated with traditional printing methods.
Why It's Important
Digital printing is important for a Bindery Operator because it allows for quick turnaround times, cost-effective short runs, and the ability to easily customize and personalize printed materials, enhancing the value and flexibility of the finishing services they provide.
How to Improve Digital Printing Skills
Improving digital printing, especially from the perspective of a Bindery Operator, involves focusing on both machinery optimization and workflow efficiency. Here are concise strategies:
Regular Maintenance: Ensure regular maintenance of digital printers to prevent breakdowns and ensure high-quality prints. Digital Printing Maintenance Guide.
Software Updates: Keep the printing software up-to-date to leverage the latest features and improvements. This can enhance print quality and speed. Latest Printing Software Updates.
Material Quality: Use high-quality printing materials to avoid issues such as paper jams and ensure superior print quality. Choosing the Right Printing Paper.
Training and Skill Development: Continuously improve skills through training, focusing on both digital printing and binding techniques. Digital Print Training Courses.
Optimize Workflow: Streamline the workflow from digital printing to binding for efficiency and reduced turnaround time. Implement Lean manufacturing principles. Lean Manufacturing in Printing.
Quality Control: Implement strict quality control measures at every stage of the printing and binding process to ensure the final product meets or exceeds expectations. Quality Control in Print Production.
By focusing on these areas, a Bindery Operator can contribute to significant improvements in digital printing quality and efficiency.
How to Display Digital Printing Skills on Your Resume
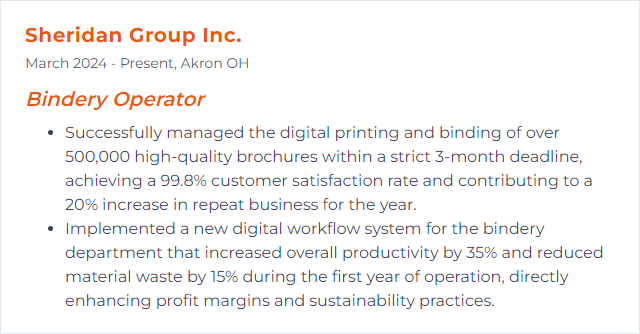
11. Quality Control
Quality Control, in the context of a Bindery Operator, involves systematically inspecting and verifying the accuracy and quality of printed materials and bound products to ensure they meet specified standards and customer requirements.
Why It's Important
Quality control is crucial for a Bindery Operator to ensure the final printed materials meet the specified standards, avoiding waste, reducing rework, and ensuring customer satisfaction with the finished product.
How to Improve Quality Control Skills
Improving Quality Control as a Bindery Operator involves a few key steps focused on precision, consistency, and continuous improvement. Here’s a concise guide:
Understand Specifications: Fully grasp job requirements and specifications before beginning any project. Printing Industries of America offers resources on standards and best practices.
Regular Equipment Maintenance: Ensure all bindery equipment is regularly maintained and calibrated. This reduces errors and improves output quality. The Bindery Equipment Manufacturers Association may provide guidance on maintenance standards.
Quality Checks: Implement regular quality checks at various stages of the binding process. Use checklists based on common defects related to binding, such as misalignments or adhesive issues.
Training and Education: Continuously update your skills and knowledge. Online courses on platforms like LinkedIn Learning can be very beneficial.
Feedback Loop: Create a system for receiving and acting on feedback from both clients and peers to continuously improve the quality of work.
Lean Manufacturing Principles: Apply lean manufacturing principles to reduce waste and increase efficiency, which indirectly improves quality. The Lean Enterprise Institute offers insights into lean principles.
By focusing on these areas, a Bindery Operator can significantly enhance the quality control of their work, ensuring that the final products meet or exceed expectations.
How to Display Quality Control Skills on Your Resume
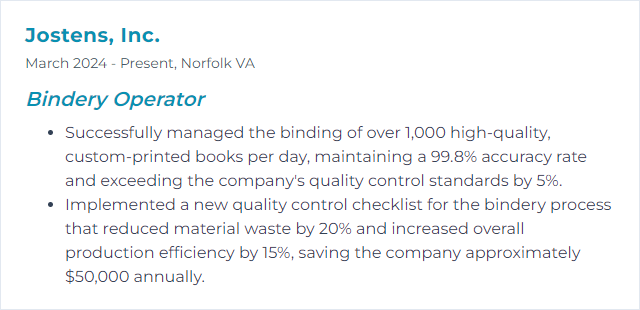
12. Maintenance Troubleshooting
Maintenance troubleshooting, in the context of a Bindery Operator, involves systematically diagnosing and resolving issues with binding machinery and equipment to ensure optimal operation, minimize downtime, and maintain production quality.
Why It's Important
Maintenance troubleshooting is crucial for a Bindery Operator because it ensures the efficient operation of binding machinery, minimizes downtime caused by mechanical failures, and maintains consistent quality in the final product. This proactive approach helps in identifying and resolving issues promptly, reducing operational costs and enhancing productivity.
How to Improve Maintenance Troubleshooting Skills
Improving maintenance troubleshooting for a Bindery Operator involves enhancing diagnostic skills, understanding machinery, and implementing systematic approaches. Here are concise tips:
Understand Equipment: Gain a deep understanding of the bindery equipment you operate. Manuals and manufacturer websites often provide crucial insights.
Systematic Approach: Adopt a systematic approach to troubleshooting. Use methods like the Six Step Troubleshooting Procedure to identify issues efficiently.
Training and Education: Continually improve your skills through online courses and training. Platforms like LinkedIn Learning offer courses on machinery maintenance.
Use of Diagnostic Tools: Learn to use diagnostic tools effectively. Information on tools can be found through suppliers such as Grainger.
Preventive Maintenance: Implement a preventive maintenance schedule to mitigate issues before they occur. Guides on setting this up can be found on Maintenance Management.
Leverage Technology: Utilize maintenance management software for efficient tracking and management of maintenance tasks. UpKeep is an example of such technology.
Peer Forums and Networks: Engage in forums and networks for bindery operators to exchange knowledge and solutions. PrintPlanet can be a valuable resource.
By focusing on these areas, a Bindery Operator can significantly improve their maintenance troubleshooting capabilities.
How to Display Maintenance Troubleshooting Skills on Your Resume
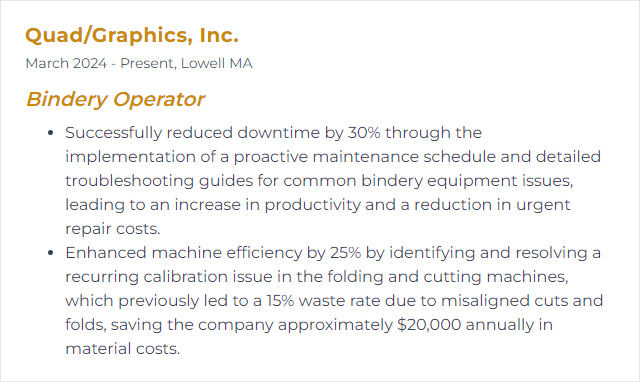