Top 12 Bindery Worker Skills to Put on Your Resume
In the competitive field of bindery work, showcasing a robust set of skills on your resume can significantly elevate your chances of securing your desired position. This article outlines the top 12 skills that bindery workers should highlight to demonstrate their expertise and adaptability in the ever-evolving print finishing industry.

Bindery Worker Skills
- Collating
- Folding
- Cutting
- Saddle stitching
- Perfect binding
- Die-cutting
- Laminating
- Guillotine operation
- PUR binding
- Foil stamping
- Book sewing
- Heidelberg equipment
1. Collating
Collating in a bindery context refers to the process of gathering and arranging individual sheets or sections of a publication in their correct sequence before binding.
Why It's Important
Collating is important for a Bindery Worker because it ensures that pages or sheets are arranged in the correct order before binding, guaranteeing the final product is organized and functional for the end-user.
How to Improve Collating Skills
Improving collating in a bindery setting focuses on optimizing efficiency, accuracy, and productivity. Here are concise strategies:
Upgrade Equipment: Invest in automated collating machines that offer higher speeds and precision. Review options.
Regular Maintenance: Ensure machines are regularly serviced to prevent malfunctions and downtime. Maintenance tips.
Employee Training: Provide comprehensive training for workers on equipment use and troubleshooting. Training resources.
Quality Control Processes: Implement rigorous quality checks at multiple stages of the collating process. Quality control basics.
Workflow Optimization: Analyze and streamline workflow for maximum efficiency, reducing bottlenecks. Workflow optimization tips.
Use of Software: Leverage software for pre-collation setup and error minimization. Software options.
By focusing on these areas, bindery workers can significantly improve the collating process, enhancing overall productivity and product quality.
How to Display Collating Skills on Your Resume
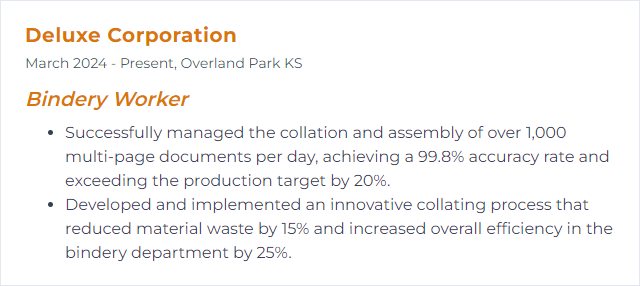
2. Folding
Folding, in the context of a bindery worker, refers to the process of bending and creasing paper or other materials into specific shapes or sizes, often as part of the bookbinding or packaging process.
Why It's Important
Folding is crucial for a Bindery Worker as it ensures precision in aligning pages, contributes to the professional appearance and durability of the final product, and facilitates the efficient assembly of books, brochures, and other printed materials.
How to Improve Folding Skills
Improving folding as a Bindery Worker involves honing skills, understanding machinery, and implementing best practices. Here’s how:
Understand Your Machinery: Get to know the specific folding machines you work with. Each machine may have unique settings, maintenance needs, and capabilities.
Regular Maintenance: Perform regular maintenance and cleaning of your folding machines to ensure they operate efficiently and accurately.
Material Knowledge: Understand the properties of different materials you're working with. Paper thickness, grain direction, and humidity can all affect folding quality.
Precision in Setup: Be meticulous in setting up folding jobs. Accurate alignment and proper adjustment of folding plates are crucial for consistent folds.
Continuous Learning: Stay updated with the latest folding techniques and machinery. Online forums and tutorials can be excellent resources. Websites like Printing Impressions offer insights into new technologies and methods.
Practice: Like any skill, proficiency in folding comes with practice. Experiment with different materials and folds to expand your expertise.
Quality Control: Develop a keen eye for detail. Regularly check your output for consistency and quality, making adjustments as necessary.
For more in-depth understanding and updates on folding techniques and bindery work, consider joining professional communities or exploring resources such as PrintWeek or Bindery Success™ Strategies for practical advice and innovation in the field.
How to Display Folding Skills on Your Resume
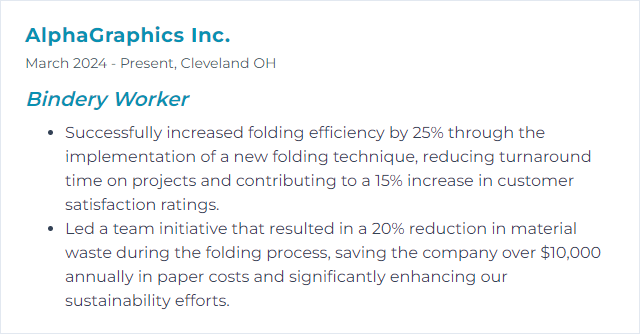
3. Cutting
Cutting, in the context of a Bindery Worker, refers to the process of using machines or hand tools to trim pages and materials to specific dimensions as part of the bookbinding or finishing process.
Why It's Important
Cutting is crucial for a Bindery Worker because it ensures precision in trimming materials to exact specifications, essential for high-quality and uniform finished products.
How to Improve Cutting Skills
To enhance cutting accuracy and efficiency as a Bindery Worker, follow these concise steps:
Sharpen Blades Regularly: Dull blades result in poor cuts. Regular sharpening ensures clean, precise edges. Friedheim offers equipment and maintenance tips.
Maintain Equipment: Regular maintenance of cutting machines prevents malfunctions and ensures consistent quality. Heidelberg provides maintenance guides for their cutting machines.
Use the Right Tools: Employ cutting tools that are specifically designed for the type of material you are working with. C&T Matrix offers a variety of cutting solutions.
Follow Safety Procedures: Always prioritize safety to prevent accidents, which can cause delays and affect the quality of work. OSHA provides safety guidelines for bindery workers.
Measure Twice, Cut Once: Double-check measurements before making cuts to ensure accuracy. This old adage is crucial for minimizing waste and ensuring precision.
Practice Good Housekeeping: Keep the workspace clean and organized to improve efficiency and reduce errors.
Invest in Training: Continuous learning and training on new techniques and technologies can improve skill levels. Consider resources such as Printing Industries of America for courses and certifications.
By implementing these strategies, bindery workers can significantly improve their cutting accuracy and efficiency.
How to Display Cutting Skills on Your Resume
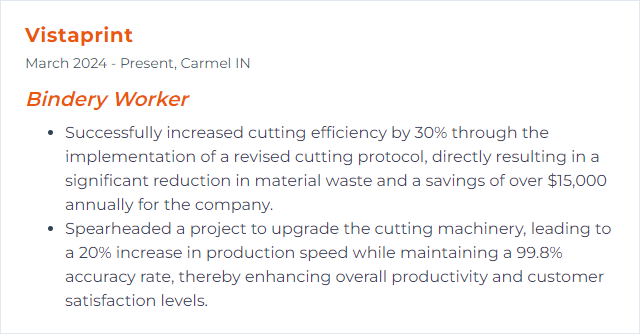
4. Saddle stitching
Saddle stitching is a binding process where folded sheets are gathered together one inside the other and then stapled through the fold line with wire staples.
Why It's Important
Saddle stitching is important for a Bindery Worker because it provides a quick, cost-effective method for assembling smaller booklets, magazines, and catalogs, ensuring a neat, professional finish.
How to Improve Saddle stitching Skills
To improve saddle stitching, follow these concise steps:
Machine Calibration: Regularly calibrate your stitching machine for consistent stitch placement. Heidelberg offers guidance on machine maintenance.
Material Preparation: Ensure all sheets are precisely jogged and aligned. Misalignment can cause stitching issues. Printing United Alliance provides tips on material preparation.
Stitch Quality: Use high-quality wire and adjust stitching heads for optimal penetration and clinching. Check resources from Deluxe Stitcher for stitch quality improvement.
Regular Maintenance: Clean and lubricate your machine regularly to prevent malfunction and wear. Graphic Arts Magazine has articles on equipment maintenance.
Operator Training: Ensure operators are well-trained in machine use and troubleshooting. PIA offers training resources for bindery workers.
By focusing on these areas, you can significantly improve the quality and efficiency of your saddle stitching process.
How to Display Saddle stitching Skills on Your Resume
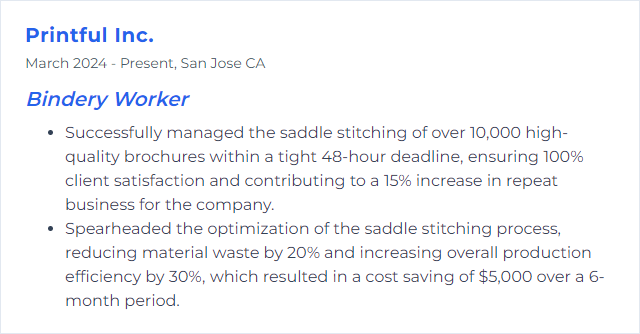
5. Perfect binding
Perfect binding is a method where pages and cover are glued together at the spine with a strong yet flexible thermal adhesive for a smooth and sleek finish.
Why It's Important
Perfect binding is important because it provides a clean, professional finish to books and documents, offering durability and allowing for printing on the spine, enhancing aesthetic appeal and marketability.
How to Improve Perfect binding Skills
To enhance perfect binding, focus on these concise steps:
- Preparation: Ensure the spine and paper edges are properly milled and notched to enhance adhesive penetration. Binding Industry
- Adhesive Application: Use the right adhesive (EVA, PUR, or PVA) based on the book's requirements. Apply evenly without overdoing it. For details, see Adhesive & Sealant Council.
- Nipping and Pressing: Correctly adjust the nipping and pressing stages for a tight, square bind. Printing Industries of America provides guidelines.
- Curing Time: Allow adequate curing time for the adhesive. PUR adhesives, for example, require longer curing times but offer superior strength.
- Quality Control: Implement a stringent QC process to check for issues like spine glue strength and page pull strength. TAPPI offers resources on testing standards.
Improving perfect binding involves meticulous preparation, choosing the right adhesive, and ensuring proper curing and quality control.
How to Display Perfect binding Skills on Your Resume
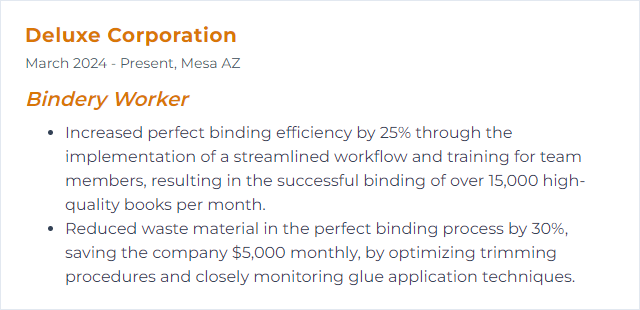
6. Die-cutting
Die-cutting is a precision cutting process used in bindery and printing work to shape and cut materials into specific, intricate designs with a custom-shaped blade, known as a die, often used for creating unique packaging, labels, and business cards.
Why It's Important
Die-cutting is essential for a Bindery Worker as it allows for precise cutting of materials into specific shapes or designs, enabling the creation of custom packaging, unique business cards, decorative elements, and more, thus enhancing the quality and variety of finished products offered to clients.
How to Improve Die-cutting Skills
To improve die-cutting as a Bindery Worker, focus on the following concise steps:
Maintenance: Regularly maintain and clean your die-cutting machines to ensure precision and efficiency. Cleaning and Maintenance Guide.
Material Preparation: Properly prepare materials before die-cutting to avoid issues like tearing or incomplete cuts. Material Handling.
Die Quality: Invest in high-quality dies and regularly inspect them for wear and tear to ensure clean cuts. Die Quality Importance.
Machine Calibration: Calibrate your die-cutting machines accurately for different materials to achieve precise cuts and minimize waste. Calibration Guide.
Training: Continuously update your skills and knowledge about new die-cutting techniques and materials through workshops and online courses. Online Training Resources.
By focusing on these areas, you can significantly improve the die-cutting process in your role as a Bindery Worker.
How to Display Die-cutting Skills on Your Resume
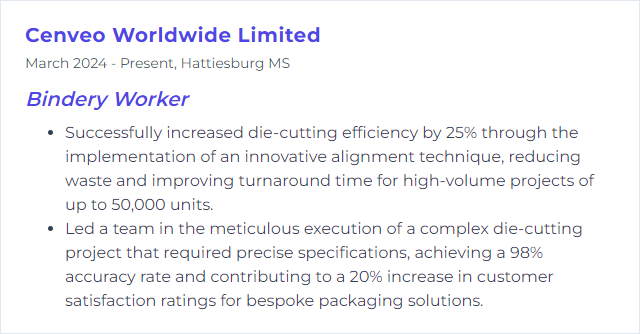
7. Laminating
Laminating, in the context of bindery work, refers to the process of applying a thin plastic film over paper or card products to protect and enhance their durability, appearance, and longevity.
Why It's Important
Laminating is important for a Bindery Worker because it provides a protective layer that enhances durability, preserves the quality, and improves the appearance of printed materials, ensuring they withstand handling and last longer.
How to Improve Laminating Skills
To improve laminating as a Bindery Worker, focus on the following concise steps:
- Material Preparation: Ensure materials are clean and dry. Remove any dust or debris for a smoother finish.
- Machine Calibration: Adjust the laminator settings such as temperature, speed, and pressure according to the material and type of laminate being used.
- Test Runs: Conduct a test run with a similar material to check for quality and make necessary adjustments.
- Proper Feeding: Feed the material straight and centered into the laminator to avoid wrinkles or misalignment.
- Regular Maintenance: Clean rollers and routinely check the machine for any wear or damage to maintain optimal performance.
For further reading and detailed guides, consider referencing:
- Laminating Tips and Tricks for specific techniques and common pitfalls.
- Understanding Laminating Machines and How to Use Them for a deeper dive into machine specifics and operation.
How to Display Laminating Skills on Your Resume
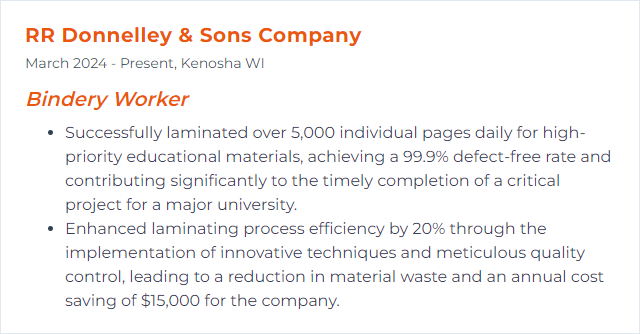
8. Guillotine operation
In bindery, a Guillotine operation refers to the cutting or trimming of paper or book materials using a Guillotine cutter, a machine equipped with a large blade that makes straight cuts through stacks of paper with precision and efficiency.
Why It's Important
The guillotine operation is important for a Bindery Worker because it ensures precise and efficient cutting of paper or other materials to exact specifications, essential for high-quality bookbinding and finishing processes.
How to Improve Guillotine operation Skills
Improving guillotine operation in a bindery involves ensuring safety, maintaining the equipment, and optimizing workflows. Here are concise steps:
- Safety Training: Ensure all operators undergo comprehensive safety training specific to guillotine usage, focusing on proper handling and emergency procedures.
- Regular Maintenance: Implement a regular maintenance schedule for the guillotine, including blade sharpening and mechanism lubrication, to keep it in optimal condition.
- Quality Blades: Use high-quality blades and replace them regularly to ensure clean cuts and reduce wear on the machine.
- Material Handling: Streamline material handling processes to reduce idle time and increase efficiency in guillotine operation.
- Workflow Optimization: Utilize software or workflow optimization techniques to plan cutting sequences, minimizing adjustments and downtime.
- Ergonomics: Adjust the work area to promote ergonomic operation, reducing operator fatigue and increasing productivity.
Focusing on these areas can significantly improve the efficiency and safety of guillotine operations in a bindery setting.
How to Display Guillotine operation Skills on Your Resume
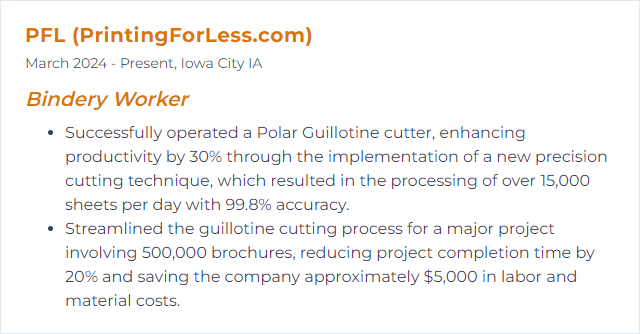
9. PUR binding
PUR binding, short for Polyurethane Reactive binding, is a method of bookbinding that uses a durable, flexible adhesive to securely bind pages together, creating a strong, long-lasting bond suitable for a wide range of print materials.
Why It's Important
PUR binding, using polyurethane reactive adhesive, offers superior durability, flexibility, and lay-flat properties for books. It's crucial for bindery workers as it ensures high-quality, long-lasting products, suitable for a wide range of materials and applications.
How to Improve PUR binding Skills
Improving PUR (Polyurethane Reactive) binding involves focusing on preparation, application, and curing processes. Ensure the spine is milled to the correct depth and notches are clean for optimal adhesive penetration. Use a high-quality PUR adhesive and apply it at the manufacturer's recommended temperature and thickness. Make sure the book block is properly jogged and aligned before entering the binder. After binding, books should cure for 24 hours under optimal conditions (room temperature, low humidity) to achieve full strength. Regular maintenance of the binding equipment and adherence to the adhesive manufacturer's guidelines are crucial for consistent quality.
For further detailed guidance:
- Preparation and Application: Binding and Finishing
- Adhesive Selection and Usage: Adhesive and Sealant Council
- Equipment Maintenance: Plockmatic Group
These resources will help a Bindery Worker improve their PUR binding process through better understanding and practices.
How to Display PUR binding Skills on Your Resume
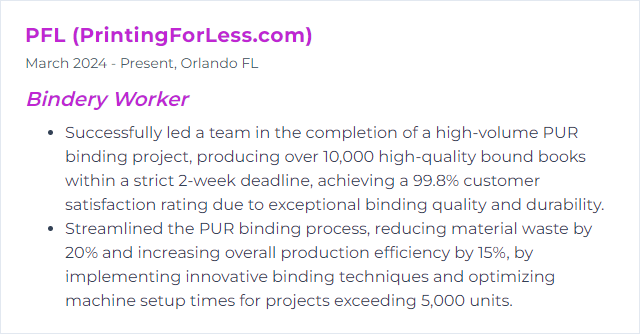
10. Foil stamping
Foil stamping is a printing process where metallic or pigmented foil is applied to a surface using heat and pressure, creating decorative finishes or lettering on books, invitations, or business cards.
Why It's Important
Foil stamping is important for a Bindery Worker as it adds value and appeal to printed materials by applying metallic or pigmented foil onto the surface, enhancing the product's aesthetic, attracting attention, and differentiating it in the market.
How to Improve Foil stamping Skills
To improve foil stamping, a bindery worker should:
Ensure proper machine setup: Adjust temperature, pressure, and dwell time according to the substrate and foil type. Foil Stamping Basics
Use high-quality materials: Select premium foils and compatible substrates for consistent results. Choosing the Right Foil
Regular maintenance: Keep the stamping machine clean and well-maintained to prevent defects. Maintenance Tips
Test Runs: Conduct test runs to fine-tune adjustments before the final print run. Foil Stamping Process
Continuous Learning: Stay updated with new techniques and materials in the industry. FSEA for resources and trends.
By focusing on these areas, a bindery worker can significantly improve the quality and consistency of foil stamping projects.
How to Display Foil stamping Skills on Your Resume
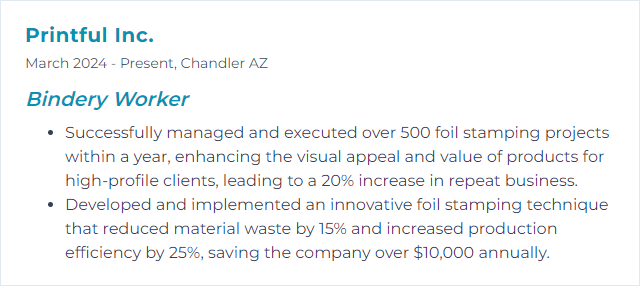
11. Book sewing
Book sewing is a binding technique where folded sheets are stitched together along the spine before being attached to the book cover, ensuring durability and a professional finish.
Why It's Important
Book sewing is crucial for a Bindery Worker as it enhances the durability and longevity of books, ensuring they can withstand frequent handling and usage. This traditional binding method also allows books to lay flat when open, improving readability and user experience.
How to Improve Book sewing Skills
Improving book sewing involves enhancing both the quality and efficiency of the binding process. As a bindery worker, focus on these concise steps:
Material Preparation: Ensure all materials (thread, signatures, cover) are of high quality and compatible. Learn more about materials.
Machine Setup: Properly set up and maintain your sewing machine. Regular maintenance can prevent many issues. See machine setup tips.
Sewing Technique: Master various sewing techniques (e.g., saddle stitching, perfect binding) and use the most appropriate one based on the book type and size. Explore sewing techniques.
Quality Control: Implement a quality control process to check for loose threads or misaligned signatures before the final binding stage. Understand quality control in binding.
Continuous Learning: Stay updated with the latest trends and technologies in bookbinding by attending workshops or online courses. Explore educational resources.
Improvement is a continuous process. Regularly revisiting and refining these steps will lead to enhanced skill and productivity in book sewing.
How to Display Book sewing Skills on Your Resume
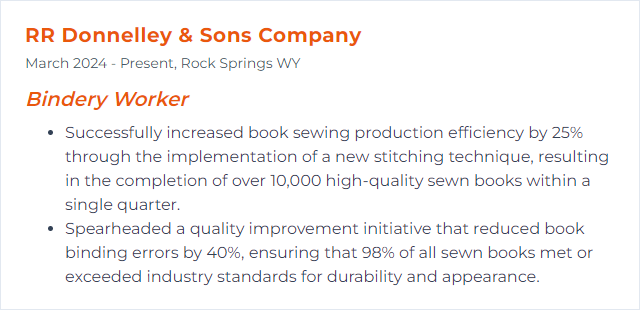
12. Heidelberg equipment
Heidelberg equipment refers to high-quality printing and finishing machinery produced by Heidelberg, a leading manufacturer in the printing industry. For a Bindery Worker, this would involve machines for cutting, folding, gluing, and binding printed materials to create finished products like books, brochures, and magazines.
Why It's Important
Heidelberg equipment is crucial for a Bindery Worker because it represents high-quality, efficient, and versatile printing and finishing solutions, enabling precise cutting, folding, and binding tasks essential for producing professional-grade printed materials.
How to Improve Heidelberg equipment Skills
Improving Heidelberg equipment in a bindery environment involves several key strategies focused on maintenance, training, and process optimization. Here are concise tips for a Bindery Worker:
Regular Maintenance: Schedule and perform regular maintenance checks to prevent breakdowns and ensure the equipment operates at peak efficiency. Heidelberg's maintenance solutions provide guidelines and services.
Operator Training: Ensure all operators undergo comprehensive training to understand the equipment thoroughly. This improves efficiency and reduces errors. Heidelberg offers specific training courses for their equipment.
Optimize Workflow: Analyze and streamline the workflow to minimize idle time for the Heidelberg equipment. Implementing lean manufacturing principles can be beneficial.
Use Genuine Parts and Supplies: Always use genuine Heidelberg parts and supplies to ensure compatibility and reliability. You can find parts and supplies on the Heidelberg Online Shop.
Implement Preventive Measures: Regularly clean and inspect the equipment to prevent small issues from becoming major problems. Heidelberg provides cleaning and care products designed specifically for their machines.
Stay Up-to-Date: Keep up with the latest software updates and technology upgrades from Heidelberg to enhance performance and add new features to the equipment. Heidelberg's news and updates can be a useful resource.
By focusing on these areas, a Bindery Worker can significantly improve the performance and longevity of Heidelberg equipment.
How to Display Heidelberg equipment Skills on Your Resume
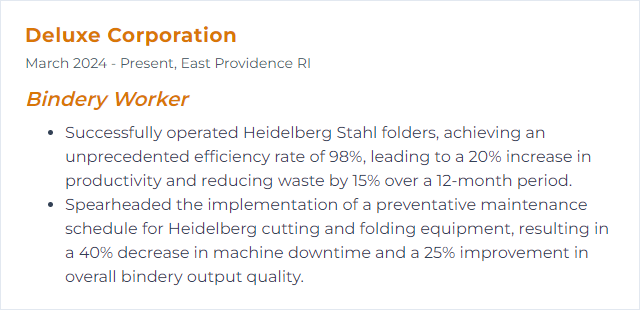