Top 12 Yield Engineer Skills to Put on Your Resume
In today's competitive job market, standing out as a Yield Engineer requires showcasing a unique set of skills on your resume that highlights your expertise and value to potential employers. This article delves into the top 12 skills you should emphasize to demonstrate your proficiency in optimizing production processes and improving yield, making you an indispensable asset to any team.
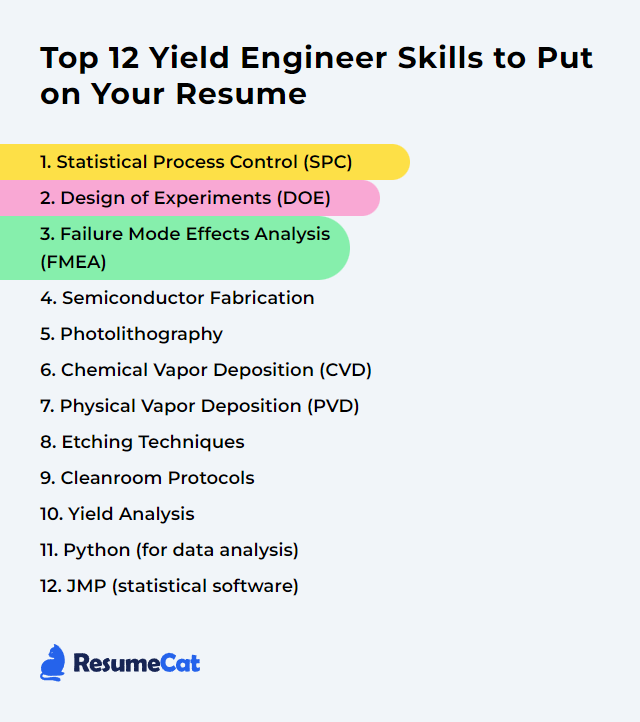
Yield Engineer Skills
- Statistical Process Control (SPC)
- Design of Experiments (DOE)
- Failure Mode Effects Analysis (FMEA)
- Semiconductor Fabrication
- Photolithography
- Chemical Vapor Deposition (CVD)
- Physical Vapor Deposition (PVD)
- Etching Techniques
- Cleanroom Protocols
- Yield Analysis
- Python (for data analysis)
- JMP (statistical software)
1. Statistical Process Control (SPC)
Statistical Process Control (SPC) is a method used by yield engineers to monitor and control a manufacturing process through statistical analysis, ensuring that the process operates at its fullest potential to produce consistent, high-quality output with minimal waste.
Why It's Important
Statistical Process Control (SPC) is crucial for a Yield Engineer because it enables the monitoring and control of manufacturing processes to detect and prevent defects, ensuring product quality and consistency, which directly impacts yield optimization and cost reduction.
How to Improve Statistical Process Control (SPC) Skills
Improving Statistical Process Control (SPC) for a Yield Engineer involves several key steps focused on enhancing the precision and reliability of process monitoring to maximize yield efficiency. Here's a concise guide:
Enhance Data Quality: Ensure the data collected is accurate, reliable, and timely. Use advanced sensors and automate data collection where possible. This improves the foundation upon which SPC analyses are performed. ASQ’s guide on data quality.
Implement Real-time Monitoring: Utilize real-time SPC software solutions to monitor processes closely. This allows for immediate adjustments and reduces the lag between data collection and analysis. Consider options like InfinityQS.
Advanced Statistical Methods: Beyond basic control charts, incorporate advanced statistical methods such as multivariate analysis to detect and understand complex process variations. Resources like NIST’s Engineering Statistics Handbook can provide in-depth techniques.
SPC Training: Regularly train staff on SPC principles and new methodologies. A well-informed team can significantly improve SPC implementation through better data handling and analysis. MIT OpenCourseWare on Statistical Process Control offers free, comprehensive resources.
Continuous Improvement: Adopt a Kaizen or continuous improvement philosophy, where SPC is not just a tool but part of the culture. This involves regularly reviewing processes, data, and control limits to identify improvement opportunities. Lean Enterprise Institute on Continuous Improvement.
Cross-functional Teams: Collaborate with other departments (R&D, Operations, Quality) to gain insights and perspectives that can improve SPC strategies. This holistic approach can uncover hidden opportunities for yield improvement.
Leverage Technology: Explore the latest in AI and machine learning for predictive analytics, which can anticipate process deviations before they occur, thereby proactively controlling quality. McKinsey on Digital and Analytics.
Implementing these strategies requires a balanced approach of technology, people, and processes to significantly enhance SPC in your role as a Yield Engineer.
How to Display Statistical Process Control (SPC) Skills on Your Resume
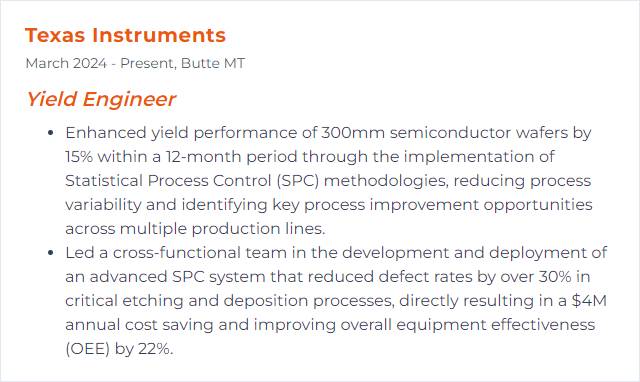
2. Design of Experiments (DOE)
Design of Experiments (DOE) is a statistical approach used by yield engineers to systematically plan, conduct, and analyze experiments. It aims to identify the factors influencing product yields, optimize processes, and improve product quality by efficiently exploring the effects of multiple variables on outcomes.
Why It's Important
Design of Experiments (DOE) is crucial for a Yield Engineer because it systematically enables the identification and analysis of factors that influence the yield of a process or product, thereby facilitating targeted improvements, efficient troubleshooting, and optimized processes for higher quality and cost-effectiveness.
How to Improve Design of Experiments (DOE) Skills
Improving Design of Experiments (DOE) for a Yield Engineer involves leveraging statistical tools and methodologies to optimize processes and improve manufacturing yields. Here's a concise guide:
Define Clear Objectives: Clearly outline the goals of your experiment, focusing on critical yield factors. This helps in designing an experiment that directly addresses the problems at hand.
Select Appropriate Design: Choose the right DOE design (e.g., Full Factorial, Fractional Factorial, Response Surface Methodology) based on the number of factors and levels to efficiently explore the process space. NIST's Engineering Statistics Handbook offers a good primer on selecting DOE designs.
Use Software Tools: Utilize DOE software (e.g., JMP, Minitab) for design creation, analysis, and visualization. These tools can help in identifying significant factors and interactions more effectively.
Pilot Experiments: Conduct small-scale pilot experiments to validate the assumptions about the process and the feasibility of the experimental design. This step can save resources and guide adjustments before full-scale experimentation.
Analyze and Optimize: Analyze the data using statistical methods to identify significant factors and their interactions. Optimization techniques like Design Space Exploration can then be applied to find the optimal process settings for yield improvement.
Iterate: DOE is an iterative process. Based on initial findings, refine the experiment by adjusting factors or exploring new areas. Continual learning and adaptation are key to uncovering deeper insights.
Knowledge Sharing: Document and share findings within your organization. This not only aids in collective learning but also helps in standardizing best practices for future experiments.
For a deeper dive into DOE concepts and best practices, refer to the American Society for Quality (ASQ) for resources and case studies relevant to yield engineering and process improvement.
How to Display Design of Experiments (DOE) Skills on Your Resume
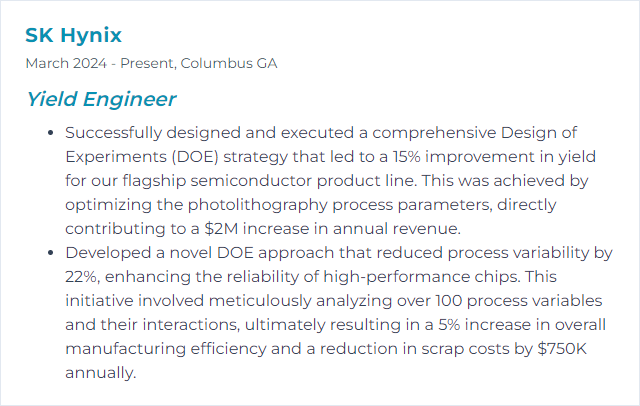
3. Failure Mode Effects Analysis (FMEA)
Failure Mode Effects Analysis (FMEA) is a systematic method used to identify and evaluate potential failures in products or processes, assess their impact on performance and yield, and prioritize actions to mitigate or eliminate the risks of these failures. For a Yield Engineer, FMEA helps in identifying potential points of failure in manufacturing processes that can affect product yield, enabling proactive improvements to enhance yield and reliability.
Why It's Important
FMEA is crucial for a Yield Engineer as it systematically identifies potential failures in manufacturing processes, assesses their impact on product quality and yield, and prioritizes corrective actions, thereby minimizing defects, improving reliability, and optimizing production yield.
How to Improve Failure Mode Effects Analysis (FMEA) Skills
Improving Failure Mode Effects Analysis (FMEA) for a Yield Engineer involves these concise steps:
Identify All Failure Modes: Begin with a thorough identification of potential failure modes for each process step. Utilizing tools like Process Flow Diagrams can help visualize and track these modes.
Prioritize Risks: Use the Risk Priority Number (RPN) calculation to prioritize risks. Focus on reducing the RPN for the highest-risk failures first. Learn more about RPN from ASQ’s explanation.
Root Cause Analysis: Implement root cause analysis techniques such as 5 Whys and Ishikawa Diagrams to understand the underlying causes of identified failures.
Develop Action Plans: For each high-priority failure mode, develop specific action plans targeting the root cause. Incorporate best practices from resources like IEEE Xplore for technology and engineering-related solutions.
Review and Update Regularly: FMEA is a living document. Regularly review and update your analysis to reflect process changes, new failure modes, and the effectiveness of implemented actions. Continuous improvement frameworks such as Kaizen can guide this iterative process.
Cross-Functional Teamwork: Collaborate with cross-functional teams for comprehensive perspectives on failure modes and their impacts. Tools like Scrum can facilitate effective teamwork and communication.
Training and Education: Ensure all team members are trained in FMEA methodology and tools. Online platforms like Coursera and edX offer courses on FMEA and related quality improvement techniques.
Utilize Software Tools: Leverage FMEA software tools for efficient analysis and documentation. Comparison of various FMEA software can be found on Capterra.
By focusing on these steps, a Yield Engineer can effectively improve the FMEA process, leading to enhanced product quality and reliability.
How to Display Failure Mode Effects Analysis (FMEA) Skills on Your Resume
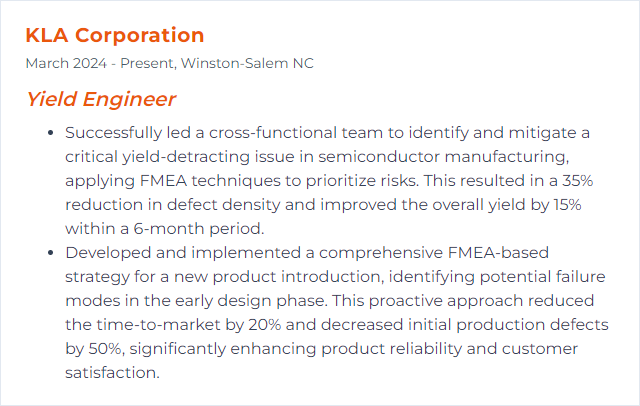
4. Semiconductor Fabrication
Semiconductor fabrication is the process of creating integrated circuits (ICs) by depositing and patterning layers of materials on silicon wafers through various techniques. A Yield Engineer focuses on optimizing this process to maximize the number of functional chips produced per wafer, thereby increasing the yield.
Why It's Important
Semiconductor fabrication is crucial for producing the intricate and tiny circuits found in electronic devices. For a Yield Engineer, it's essential because it directly impacts the efficiency, quality, and cost-effectiveness of producing these devices by maximizing the number of functional chips from each wafer, thereby increasing profitability and product reliability.
How to Improve Semiconductor Fabrication Skills
Improving semiconductor fabrication involves optimizing processes, materials, and equipment to enhance yield and quality. As a Yield Engineer, focusing on the following areas can drive improvements:
Process Optimization: Fine-tune manufacturing processes such as lithography, etching, and deposition to reduce defects. Utilizing advanced process control (APC) techniques can lead to significant enhancements in process stability and yield.
Defect Reduction: Implement defect reduction strategies, including root cause analysis and defect monitoring systems. Tools like SEM/EDX for material analysis can help identify and eliminate sources of contamination or process variation.
Equipment Maintenance: Adopt predictive and preventive maintenance strategies for fabrication equipment to minimize downtime and ensure consistent process conditions. Equipment Health Monitoring systems can predict failures before they occur.
Data Analytics: Leverage big data analytics and machine learning to analyze manufacturing data, predict yield outcomes, and identify areas for improvement. Platforms like Applied Materials' SmartFactory offer insights for yield enhancement.
Collaboration and Training: Foster a culture of continuous improvement and knowledge sharing among engineers and technicians. Ongoing training in best practices and new technologies is key.
By focusing on these areas, Yield Engineers can significantly improve semiconductor fabrication processes, leading to higher yields and better product quality.
How to Display Semiconductor Fabrication Skills on Your Resume
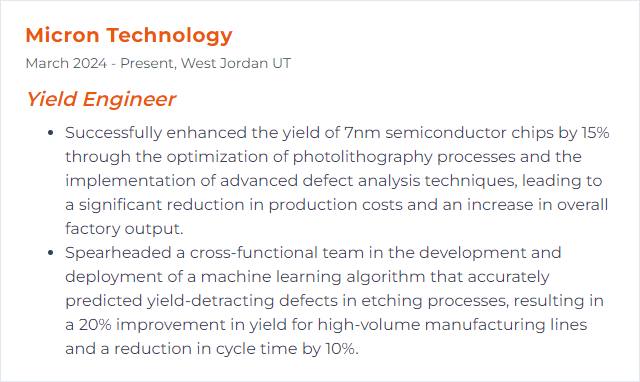
5. Photolithography
Photolithography is a process used in semiconductor manufacturing to transfer geometric shapes on a mask to the surface of a silicon wafer. It involves coating the wafer with a light-sensitive material (photoresist), exposing it to ultraviolet light through the mask to imprint the circuit design, and then developing and etching away the exposed regions. For a Yield Engineer, this process is critical for creating precise and intricate patterns on semiconductor devices, directly impacting the yield, quality, and functionality of the final products.
Why It's Important
Photolithography is crucial for Yield Engineers as it precisely transfers circuit patterns onto semiconductor wafers, directly influencing chip quality, performance, and production efficiency, thereby maximizing yield and reducing defects.
How to Improve Photolithography Skills
Improving photolithography, particularly from a Yield Engineer's perspective, involves optimizing process parameters, enhancing equipment stability, and minimizing defects to increase yield. Key strategies include:
Process Optimization: Fine-tune exposure and development times, resist thickness, and post-exposure bake conditions to improve resolution and pattern fidelity. SPIE.
Equipment Maintenance: Regular calibration and maintenance of photolithography tools to ensure consistent performance. This includes the alignment systems, exposure units, and wafer stages. SEMI.
Defect Reduction: Implement advanced defect detection and reduction techniques, such as improving cleanroom environments, using high-quality photoresists, and optimizing rinse and spin cycles. IOPscience.
Resolution Enhancement Techniques (RET): Employ techniques like phase-shifting masks, optical proximity correction, and multi-patterning to enhance feature resolution beyond the tool's native capabilities. Nature.
Process Control and Monitoring: Utilize advanced metrology and inspection tools to monitor critical dimensions and overlay errors, facilitating real-time adjustments. IEEE Xplore.
Collaboration with Design Teams: Work closely with design teams to ensure design for manufacturability (DFM), allowing for a smoother translation of designs into physical patterns. ACM Digital Library.
By focusing on these areas, Yield Engineers can significantly improve photolithography processes, leading to higher yields and reduced manufacturing costs.
How to Display Photolithography Skills on Your Resume
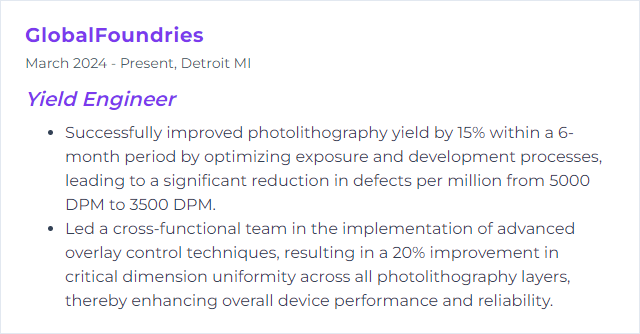
6. Chemical Vapor Deposition (CVD)
Chemical Vapor Deposition (CVD) is a chemical process used in manufacturing to produce high-quality, high-performance, solid materials, typically on a substrate. For a Yield Engineer, it is crucial for creating thin films and coatings with precise control over thickness and composition, directly impacting product yield and performance in semiconductor fabrication and other industries.
Why It's Important
Chemical Vapor Deposition (CVD) is crucial for a Yield Engineer as it enables the precise deposition of materials at the atomic or molecular level, directly influencing the quality, uniformity, and electrical properties of semiconductor devices, thereby significantly impacting the yield and performance of manufactured components.
How to Improve Chemical Vapor Deposition (CVD) Skills
Improving Chemical Vapor Deposition (CVD) processes, especially from a Yield Engineer's perspective, involves optimizing various parameters to enhance efficiency, uniformity, and product quality. Here are concise strategies:
Optimization of Precursor Flow: Adjust the flow rates of precursor gases to ensure optimal deposition rates and film qualities. Uniform flow distribution can be achieved by designing appropriate gas delivery systems. Flow Control.
Temperature Uniformity: Ensure uniform temperature distribution across the substrate by optimizing reactor design and heating mechanisms. Temperature directly affects film properties and deposition rates. Temperature Effects.
Pressure Control: Fine-tuning the chamber pressure can lead to improvements in film uniformity and deposition rates. Lower pressures can aid in the production of high-quality films. Pressure Considerations.
Substrate Preparation: Proper substrate cleaning and preparation can significantly enhance adhesion and quality of the deposited layers. Substrate Surface Preparation.
System Maintenance: Regular checks and maintenance of the CVD system, including leak detection and precursor purity checks, ensure consistent operation and yield. Maintenance Best Practices.
Real-time Monitoring and Control: Implementing sensors and feedback systems for real-time control of deposition parameters can lead to immediate adjustments for optimal deposition conditions. Monitoring Techniques.
Process Simulation: Utilize computational fluid dynamics (CFD) and other simulation tools to predict and optimize process conditions before experimental implementation. CFD in CVD Processes.
By focusing on these areas, a Yield Engineer can significantly improve the efficiency and output of CVD processes.
How to Display Chemical Vapor Deposition (CVD) Skills on Your Resume
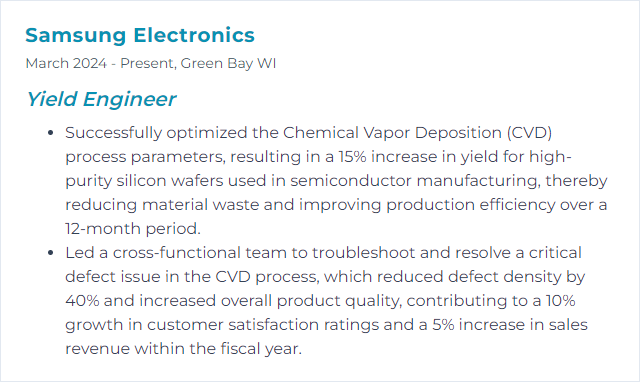
7. Physical Vapor Deposition (PVD)
Physical Vapor Deposition (PVD) is a vacuum coating process where materials are vaporized and then deposited on substrates to form thin films, crucial for enhancing yield by improving wear resistance, reducing friction, and increasing durability of components.
Why It's Important
Physical Vapor Deposition (PVD) is crucial for a Yield Engineer because it allows for the precise deposition of thin films with excellent uniformity and purity, directly impacting the yield, performance, and reliability of semiconductor devices.
How to Improve Physical Vapor Deposition (PVD) Skills
Improving Physical Vapor Deposition (PVD) as a Yield Engineer involves optimizing various parameters and processes to enhance the coating quality, reduce defects, and increase the overall yield. Here are concise strategies:
Optimize Pre-treatment: Ensure thorough cleaning and surface preparation of substrates to improve adhesion and reduce defects. Surface Preparation.
Control Deposition Parameters: Precisely control parameters such as deposition rate, temperature, and chamber pressure to ensure uniform film thickness and composition. PVD Parameter Control.
Implement Real-time Monitoring: Use in-situ monitoring tools for real-time adjustments to deposition conditions to ensure consistent quality. In-Situ Monitoring.
Material Purity: Use high-purity target materials to reduce contamination and improve film quality. Material Purity in PVD.
Equipment Maintenance: Regularly maintain and calibrate PVD equipment to prevent faults and ensure stable deposition conditions. Equipment Maintenance.
Process Simulation: Utilize computational modeling and simulation to predict outcomes and optimize process parameters before actual deposition. Process Simulation.
By focusing on these areas, Yield Engineers can significantly enhance the efficiency and effectiveness of PVD processes.
How to Display Physical Vapor Deposition (PVD) Skills on Your Resume
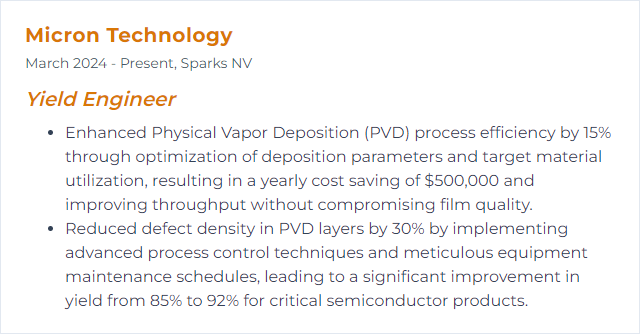
8. Etching Techniques
Etching techniques in the context of a Yield Engineer involve precise material removal processes used in semiconductor manufacturing to create patterns or structures on a substrate. These techniques, such as wet etching (chemical solution-based) and dry etching (plasma-based), are crucial for shaping semiconductor devices with high precision and accuracy, directly impacting the yield, performance, and reliability of the final product. Yield Engineers focus on optimizing these etching processes to maximize manufacturing efficiency and minimize defects.
Why It's Important
Etching techniques are crucial for Yield Engineers as they enable precise material removal, critical for manufacturing high-quality, defect-free semiconductor devices, directly impacting yield improvement and cost reduction in the production process.
How to Improve Etching Techniques Skills
Improving etching techniques for a Yield Engineer involves optimizing process parameters, materials selection, and equipment maintenance. Here's a concise guide:
Process Optimization: Fine-tune etching parameters (pressure, temperature, gas flow rates) for uniformity and selectivity. Use Design of Experiments (DoE) methodologies to identify optimal settings.
Material Selection: Choose high-quality masking materials with excellent resistance to the etching process. Advanced Materials provides insights into materials that enhance etching precision.
Equipment Calibration and Maintenance: Regularly calibrate and maintain etching equipment to ensure consistent performance. SEMI Standards for equipment maintenance can guide best practices.
Real-time Monitoring: Implement in-situ monitoring techniques for real-time process control. Spectroscopic Ellipsometry and laser interferometry are effective for end-point detection.
Cleanroom Environment: Maintain a strict cleanroom environment to reduce contamination. ISO Standards for Cleanrooms outline the requirements for particle control.
Advanced Etching Techniques: Explore advanced etching techniques such as Atomic Layer Etching (ALE) for atomic-level precision.
By focusing on these areas, a Yield Engineer can significantly improve etching techniques, leading to better yield and device performance.
How to Display Etching Techniques Skills on Your Resume
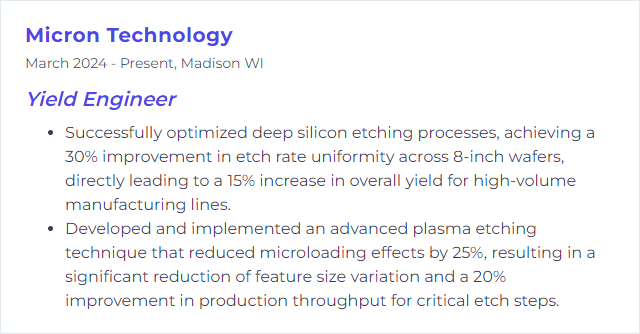
9. Cleanroom Protocols
Cleanroom protocols for a Yield Engineer involve stringent procedures to minimize contamination in the manufacturing environment, ensuring high-quality production and maximizing yield. These protocols include wearing specialized garments, controlling environmental conditions (like temperature and humidity), and adhering to strict cleanliness and process guidelines to prevent defects in semiconductor or pharmaceutical manufacturing.
Why It's Important
Cleanroom protocols are crucial for a Yield Engineer because they minimize particulate contamination, ensuring the high quality and reliability of semiconductor devices, which directly impacts manufacturing yield and product performance.
How to Improve Cleanroom Protocols Skills
Improving cleanroom protocols, particularly from a Yield Engineer's perspective, involves a focus on minimizing contamination and optimizing processes to enhance product yield. Here are concise strategies:
Enhance Training: Ensure all personnel are regularly trained on cleanroom behavior, contamination control, and protocol updates. CDC Guidelines for Cleanrooms provide a comprehensive overview.
Regular Auditing: Implement frequent audits of cleanroom practices and protocols to identify and rectify non-compliance issues. ISO 14644-1:2015 standards can guide the establishment of a contamination control plan.
Upgrade Equipment and Materials: Invest in state-of-the-art equipment and high-quality consumables that reduce contamination risk. Information on advanced cleanroom technology can be found through Semi.
Optimize Cleanroom Layout: Design the cleanroom layout to minimize traffic and airflow disruptions, which can carry particles. The Institute of Environmental Sciences and Technology (IEST) provides resources on optimal cleanroom configurations.
Implement Strict Access Control: Limit cleanroom access to essential personnel and enforce strict gowning and de-gowning procedures. Guidelines for Gowning by the CDC outline best practices.
Regular Maintenance and Cleaning: Schedule regular maintenance of HEPA filters, HVAC systems, and rigorous cleaning of all surfaces to maintain an ultra-clean environment. The EPA’s Indoor Air Quality tools can offer insights into maintaining clean air standards.
Continuous Monitoring: Utilize real-time monitoring systems for particulate matter, humidity, and temperature to ensure parameters remain within strict thresholds. Particle Measuring Systems offers advanced solutions.
Feedback Loop: Establish a robust feedback mechanism for continuous improvement, encouraging staff to report issues and suggest improvements actively.
By focusing on these areas, Yield Engineers can significantly enhance cleanroom protocols, leading to improved product yield and reduced contamination risks.
How to Display Cleanroom Protocols Skills on Your Resume
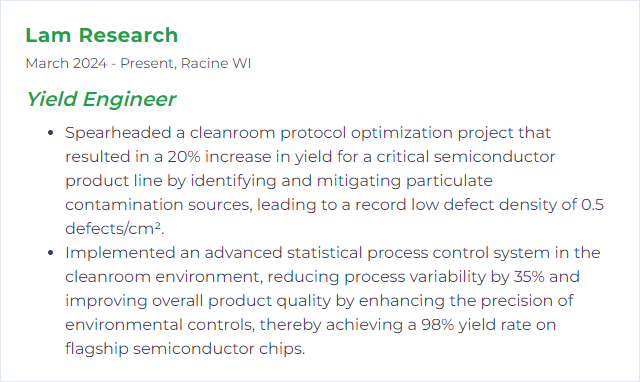
10. Yield Analysis
Yield Analysis refers to the process of examining and optimizing the percentage of functional products or devices produced in a manufacturing line, aiming to identify, analyze, and rectify the causes of defects or inefficiencies to maximize output and quality. For a Yield Engineer, it involves data collection and analysis, process monitoring, and implementing strategies for yield improvement.
Why It's Important
Yield Analysis is crucial for Yield Engineers as it helps identify, analyze, and rectify process deviations and defects in manufacturing, optimizing production efficiency, reducing costs, and increasing the overall yield of high-quality products.
How to Improve Yield Analysis Skills
Improving yield analysis involves a combination of data-driven strategies, process optimization, and technological advancements. Here's a concise guide:
Enhance Data Collection: Utilize advanced sensors and IoT devices to gather real-time, comprehensive data across all stages of production. Semiconductor Engineering offers insights into the latest technologies in data collection.
Implement Advanced Analytics: Apply machine learning and AI to analyze data, predict yield-related issues, and identify root causes. Analytics Vidhya provides tutorials and case studies on implementing these techniques.
Optimize Processes: Use statistical process control (SPC) and design of experiments (DOE) to fine-tune manufacturing processes, reducing variability and defects. The American Society for Quality (ASQ) offers resources on SPC methodologies.
Continuous Training: Keep the team updated on the latest yield enhancement techniques and technologies through continuous education. SEMI has educational programs tailored for semiconductor professionals.
Collaborate with Suppliers: Work closely with material and equipment suppliers to ensure quality and consistency, using shared data to troubleshoot issues. Supply Chain Quarterly provides strategies for effective supplier collaboration.
Regular Reviews and Feedback Loops: Establish regular review meetings to discuss yield trends, share insights across departments, and implement feedback loops for continuous improvement.
By focusing on these areas, a Yield Engineer can significantly improve yield analysis, leading to higher productivity and cost efficiency.
How to Display Yield Analysis Skills on Your Resume
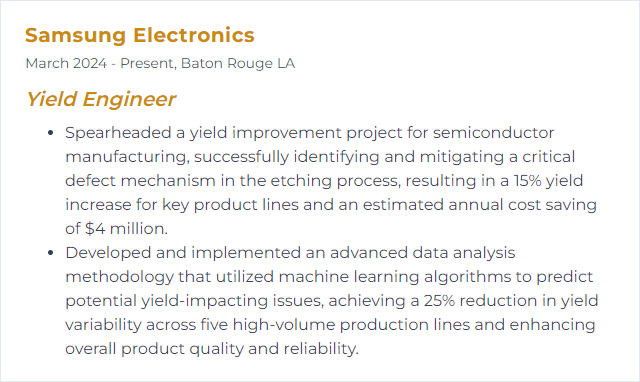
11. Python (for data analysis)
Python is a powerful, versatile programming language widely used by Yield Engineers for data analysis, offering libraries like Pandas and NumPy for efficient data manipulation, analysis, and visualization, facilitating the optimization of manufacturing yields.
Why It's Important
Python is crucial for data analysis in the context of a Yield Engineer because it provides powerful libraries (like pandas, NumPy, and Matplotlib) for data manipulation, statistical analysis, and visualization, enabling efficient identification and troubleshooting of yield-impacting issues in manufacturing processes.
How to Improve Python (for data analysis) Skills
Improving your Python skills for data analysis, particularly as a Yield Engineer, involves a focus on specific libraries and practices that streamline data processing, analysis, and visualization. Here's a concise guide:
Master Core Libraries: Proficiency in Pandas for data manipulation, NumPy for numerical computations, and Matplotlib or Seaborn for data visualization is crucial.
Learn Advanced Data Analysis Techniques: Dive deeper into statistical analysis and machine learning with SciPy for scientific computing and scikit-learn for machine learning tasks.
Efficient Data Engineering: Understanding how to efficiently process large datasets can be crucial. Learn about Dask for parallel computing and Apache Arrow for in-memory data processing.
Automation and Scripting: Automate repetitive tasks using Python scripts. This not only saves time but also reduces the chance of error in repetitive data analysis tasks.
Version Control: Use Git and platforms like GitHub to manage, track, and share your code changes. This is beneficial for collaboration and maintaining a history of your work.
Continuous Learning: Python and its libraries are constantly evolving. Stay updated by following PyData and Towards Data Science for the latest trends, techniques, and case studies.
Practical Projects: Apply what you learn in real-world projects. This could involve analyzing yield-related datasets to find patterns, anomalies, or to predict future trends.
Contribute to Open Source: Engaging with open-source projects on platforms like GitHub can provide practical experience and feedback from the community.
Online Courses and Tutorials: Platforms like Coursera, Udacity, and DataCamp offer specialized courses that can boost your data analysis skills with Python.
By focusing on these areas, you can significantly improve your Python skills for data analysis, making you a more effective and efficient Yield Engineer.
How to Display Python (for data analysis) Skills on Your Resume
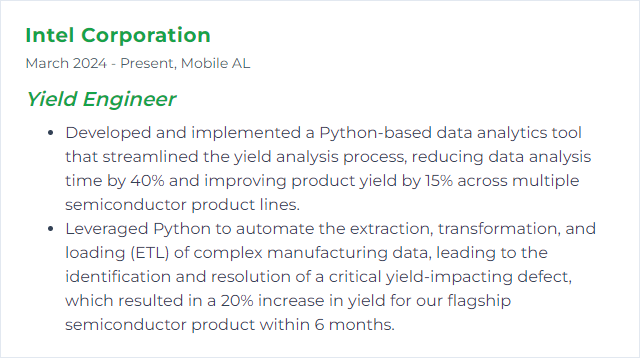
12. JMP (statistical software)
JMP is an interactive statistical analysis software developed by SAS Institute, designed for dynamic data visualization and in-depth statistical modeling. For a Yield Engineer, JMP facilitates the analysis of manufacturing data to optimize processes, improve yield, and reduce defects through insightful statistical analysis and predictive modeling.
Why It's Important
JMP is important for a Yield Engineer because it provides powerful statistical analysis tools to identify trends, diagnose problems, and optimize processes, directly impacting the efficiency and productivity of manufacturing operations.
How to Improve JMP (statistical software) Skills
Improving your efficiency and effectiveness with JMP as a Yield Engineer involves leveraging the software's capabilities to analyze and enhance manufacturing processes. Here are concise steps to achieve this:
Master the Basics: Start with JMP's official tutorials to ensure a solid understanding of the fundamentals.
Utilize Design of Experiments (DOE): Take advantage of JMP's DOE capabilities to systematically improve and optimize your processes.
Leverage Statistical Process Control (SPC): Implement SPC techniques to monitor and control manufacturing processes, ensuring they operate at their full potential.
Deep Dive into Data Visualization: Effectively use JMP’s data visualization tools for in-depth analysis and to communicate complex data insights easily.
Automate Routine Analyses: Learn to script in JSL (JMP Scripting Language) to automate repetitive tasks, saving time and reducing errors.
Stay Updated and Network: Regularly update your software and connect with other professionals through the JMP User Community for tips, tricks, and best practices.
By focusing on these areas, you can significantly improve your proficiency and productivity with JMP, driving better yield analysis and optimization in your role as a Yield Engineer.
How to Display JMP (statistical software) Skills on Your Resume
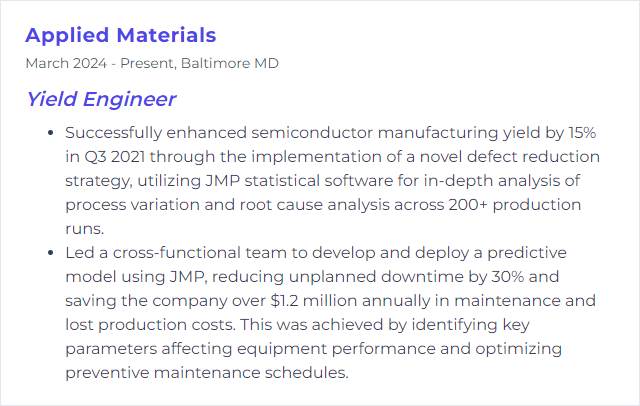