Top 12 Validation Manager Skills to Put on Your Resume
In today's competitive job market, standing out as a Validation Manager requires showcasing a robust set of skills on your resume. Mastering and highlighting the top skills in this role not only demonstrates your expertise but also significantly enhances your employability and potential for career advancement.
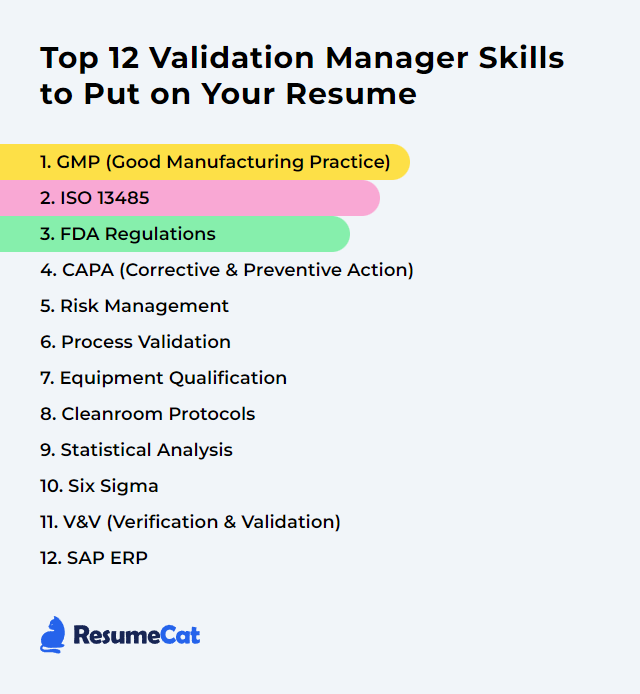
Validation Manager Skills
- GMP (Good Manufacturing Practice)
- ISO 13485
- FDA Regulations
- CAPA (Corrective and Preventive Action)
- Risk Management
- Process Validation
- Equipment Qualification
- Cleanroom Protocols
- Statistical Analysis
- Six Sigma
- V&V (Verification and Validation)
- SAP ERP
1. GMP (Good Manufacturing Practice)
GMP (Good Manufacturing Practice) refers to a system of guidelines ensuring that products are consistently produced and controlled according to quality standards. For a Validation Manager, GMP emphasizes the importance of validating processes, systems, and equipment to ensure they are capable of consistently delivering products that meet predetermined quality criteria.
Why It's Important
GMP ensures products are consistently produced and controlled according to quality standards, minimizing risks involved in production that cannot be eliminated through final product testing. It's crucial for a Validation Manager to ensure compliance, as it directly impacts product safety, efficacy, and regulatory adherence, safeguarding both public health and the company's reputation.
How to Improve GMP (Good Manufacturing Practice) Skills
Improving Good Manufacturing Practice (GMP) involves a continuous effort to enhance the processes, procedures, and overall compliance within a manufacturing environment. As a Validation Manager, focusing on the following key areas can lead to significant improvements:
Training and Competency: Ensure all personnel are adequately trained and competent in GMP requirements. Regular training sessions and assessments can keep the team updated and compliant. FDA Training
Documentation: Strengthen documentation practices. Ensure all procedures, changes, and data are accurately recorded and easily retrievable. This includes developing clear, concise SOPs and maintaining robust records of validation activities. ICH Guidelines
Validation and Qualification: Continually review and update validation protocols to ensure they meet current industry standards. Implement a systematic review process for equipment qualification and process validation to ensure ongoing compliance. ISPE Guidelines
Risk Management: Adopt a proactive approach to risk management by identifying potential GMP risks and implementing mitigation strategies. Utilize tools such as FMEA (Failure Mode and Effects Analysis) to systematically evaluate processes. ICH Q9
Continuous Improvement: Foster a culture of continuous improvement through regular audits, feedback mechanisms, and embracing a quality management system (QMS) that aligns with GMP principles. Engage in benchmarking and adopt best practices from industry leaders. ISO 9001:2015
Supplier Management: Ensure suppliers and contractors comply with GMP standards. Conduct regular audits and assessments of suppliers to maintain a high-quality supply chain. EudraLex Volume 4
Technology and Innovation: Leverage new technologies and automation to enhance GMP compliance. This includes adopting electronic batch records (EBR) and implementing advanced monitoring and control systems. FDA Technology Transfer
By focusing on these areas, a Validation Manager can significantly improve GMP compliance, leading to higher quality products, reduced risk of non-compliance, and enhanced operational efficiency.
How to Display GMP (Good Manufacturing Practice) Skills on Your Resume
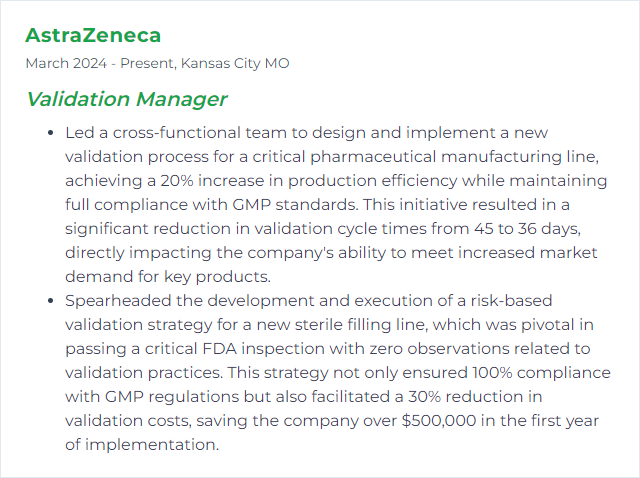
2. ISO 13485
ISO 13485 is an international standard that specifies requirements for a quality management system specific to the medical device industry, focusing on the design, development, production, and delivery of medical devices, ensuring their safety and efficacy. For a Validation Manager, it guides the processes for validating the design and manufacture of medical devices to meet regulatory and customer requirements.
Why It's Important
ISO 13485 is crucial for a Validation Manager because it provides a comprehensive framework for meeting regulatory requirements, ensures quality management systems are effectively implemented for medical devices, and facilitates consistent design, development, and production processes to enhance product safety and efficacy.
How to Improve ISO 13485 Skills
Improving ISO 13485, particularly from a Validation Manager's perspective, involves enhancing the quality management system (QMS) for medical devices. Here's a concise guide:
Risk Management: Integrate risk management throughout your QMS processes. Focus on identifying, evaluating, and controlling risks associated with product quality and compliance. ISO 14971 provides guidance on applying risk management to medical devices.
Documentation and Records: Ensure comprehensive, clear, and accessible documentation and record-keeping. Documentation should cover all processes, changes, and validations, adhering to ISO 13485 requirements. ISO 13485:2016 outlines specific requirements for documentation.
Validation and Verification: Strengthen your validation and verification processes. This includes software validation, process validation, and product validation to ensure they meet specified requirements. FDA’s General Principles of Software Validation provides additional insights.
Supplier Management: Enhance your supplier management process to ensure all external providers meet the required quality standards. This includes conducting audits, evaluating performance, and maintaining strong communication. ISO 13485:2016, Clause 7.4 details requirements on supplier management.
Continuous Improvement: Implement a culture of continuous improvement within your organization. Utilize tools like audits, Corrective and Preventive Actions (CAPA), and management reviews to identify areas for improvement and implement changes effectively. ISO 9001:2015 on quality management systems emphasizes the importance of continuous improvement and can offer useful methodologies applicable to ISO 13485.
Training and Awareness: Regularly train and update your team on ISO 13485 requirements, changes in regulations, and best practices in validation. Ensuring your team's competence is critical for maintaining compliance and product quality.
Regulatory Compliance: Stay updated with regulatory requirements in every market you operate. Compliance with ISO 13485 is often part of broader regulatory compliance, including EU MDR or FDA requirements.
Engage with Auditors: Use external and internal audits as opportunities to gain insights and feedback on your QMS. Engaging constructively with auditors can help identify potential improvements.
For further detailed guidance, refer directly to the ISO 13485:2016 standard and consider consulting specific guidance documents from regulatory bodies relevant to your market.
How to Display ISO 13485 Skills on Your Resume
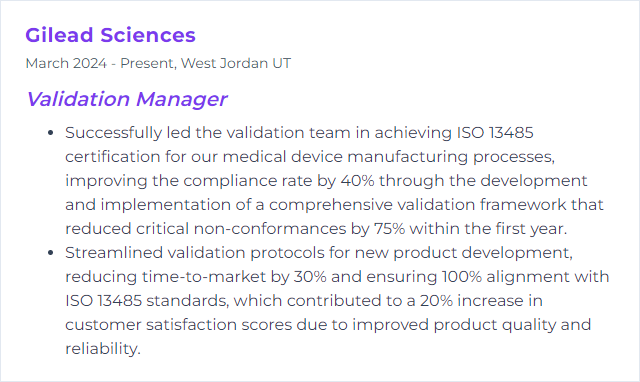
3. FDA Regulations
FDA regulations are a set of federal rules and guidelines enforced by the U.S. Food and Drug Administration (FDA) to ensure the safety, efficacy, and security of drugs, biological products, medical devices, food supply, cosmetics, and radiation-emitting products. For a Validation Manager, these regulations require the establishment of documented evidence that a process, procedure, or method operates effectively and consistently to produce a product meeting its predetermined specifications and quality attributes.
Why It's Important
FDA regulations ensure that pharmaceuticals, medical devices, and food products are safe and effective, protecting public health. For a Validation Manager, they provide a framework for guaranteeing that production processes, equipment, and systems are properly qualified and validated to meet these stringent standards, ensuring product consistency, safety, and efficacy.
How to Improve FDA Regulations Skills
Improving FDA regulations, particularly from a Validation Manager's perspective, involves enhancing clarity, efficiency, and adaptability. Here's a concise guide:
Enhance Clarity: Clarify guidelines and requirements to reduce ambiguities, thereby speeding up validation processes. This involves detailed guidance on new technologies and methodologies. FDA's Guidance Documents serve as a primary resource.
Increase Efficiency: Streamline review and approval processes by adopting more digital submissions and leveraging advanced analytics to predict outcomes. The FDA's Digital Health Innovation Action Plan outlines steps towards modernization.
Promote Adaptability: Update regulations to keep pace with technological advancements in pharmaceuticals and medical devices. Engage with industry stakeholders for insights and proactive regulation adjustments. FDA Voices provides perspectives on current focuses and future directions.
Strengthen Collaboration: Foster partnerships between the FDA, industry, and academia to facilitate knowledge exchange and innovation. This collaborative approach is highlighted in the FDA's Public Private Partnership Program.
Emphasize Training: Improve training for both FDA staff and industry professionals on the latest regulatory standards and technologies. The FDA's Training and Continuing Education offers resources for various stakeholders.
By focusing on these areas, a Validation Manager can contribute to the enhancement of FDA regulations, ensuring they efficiently and effectively safeguard public health while fostering innovation.
How to Display FDA Regulations Skills on Your Resume
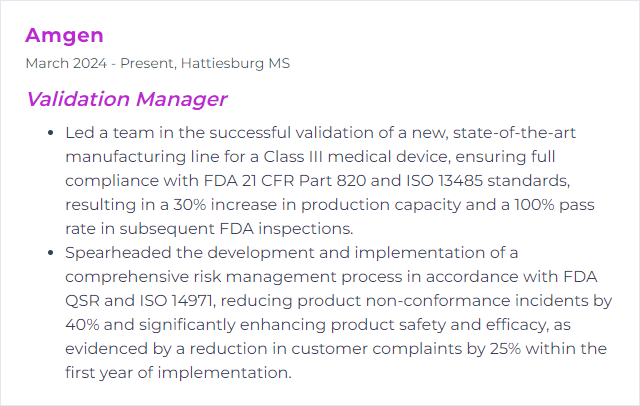
4. CAPA (Corrective and Preventive Action)
CAPA (Corrective and Preventive Action) is a systematic approach used to identify, address, and eliminate the root causes of identified problems or discrepancies to prevent their recurrence (corrective actions) and to prevent the occurrence of similar problems (preventive actions). For a Validation Manager, it involves implementing measures to ensure product quality and compliance by addressing and rectifying validation process issues or failures.
Why It's Important
CAPA is crucial for a Validation Manager because it ensures product quality and compliance by systematically identifying, addressing, and preventing issues in the validation processes, ultimately safeguarding patient safety and meeting regulatory requirements.
How to Improve CAPA (Corrective and Preventive Action) Skills
Improving CAPA (Corrective and Preventive Action) involves systematic analysis, identification of root causes, and implementation of effective solutions. For a Validation Manager, focusing on these key strategies can enhance CAPA processes:
Root Cause Analysis (RCA): Implement robust root cause analysis methods such as the 5 Whys or Fishbone Diagram to accurately identify underlying issues. This ensures that the corrective actions address the actual problems rather than symptoms.
Risk Assessment: Incorporate risk management principles from standards like ISO 14971 to prioritize actions based on the severity and likelihood of potential failures. This helps in focusing efforts where they are most needed.
Action Plan Development: Develop clear, actionable plans with specific timelines, responsibilities, and milestones. Ensure actions are SMART (Specific, Measurable, Achievable, Relevant, Time-bound).
Effectiveness Verification: Implement a process for verifying the effectiveness of CAPA actions, ensuring they have resolved the issues without causing unintended consequences. This may involve revisiting initial risk assessments.
Documentation and Communication: Maintain thorough documentation for all stages of the CAPA process, from identification through to resolution and verification. Clear communication with all stakeholders ensures transparency and facilitates continuous improvement.
Training and Awareness: Provide continuous training and awareness programs for staff to enhance their understanding of the CAPA process, including problem identification, RCA techniques, and the importance of compliance.
Continuous Improvement: Adopt a culture of continuous improvement by regularly reviewing and updating CAPA processes. Utilize quality management systems like ISO 9001 to embed CAPA in the organization's operational fabric.
By focusing on these areas, a Validation Manager can significantly improve the effectiveness of CAPA processes, leading to enhanced product quality, regulatory compliance, and customer satisfaction.
How to Display CAPA (Corrective and Preventive Action) Skills on Your Resume
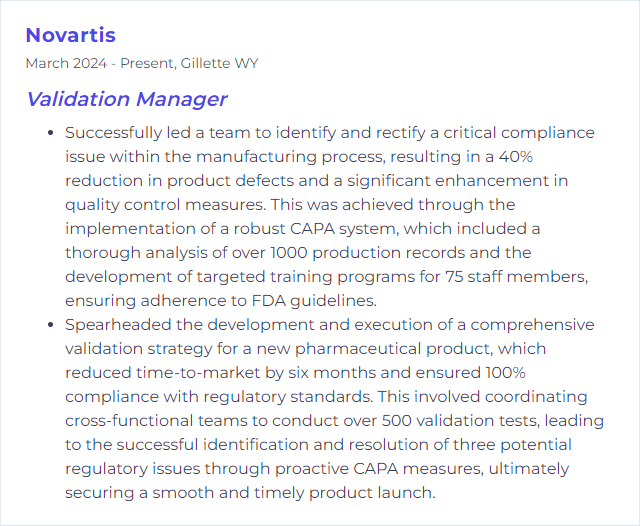
5. Risk Management
Risk Management, in the context of a Validation Manager, involves identifying, assessing, and prioritizing potential risks to ensure the safety, compliance, and effectiveness of products or processes, and implementing strategies to mitigate or eliminate these risks.
Why It's Important
Risk Management is essential for a Validation Manager as it ensures the identification, analysis, and mitigation of potential risks, safeguarding the integrity and compliance of validation processes. This proactive approach helps in preventing costly errors, ensuring product quality, and maintaining regulatory compliance.
How to Improve Risk Management Skills
Improving Risk Management, particularly for a Validation Manager, involves a multi-faceted approach focusing on identifying, assessing, and mitigating risks throughout the validation process. Here's a concise guide:
Understand and Define Risks: Clearly understand the types of risks (e.g., technical, compliance) associated with the validation process. Use guidelines like ICH Q9 for a structured approach to quality risk management.
Risk Assessment Tools: Implement risk assessment tools such as Failure Mode and Effects Analysis (FMEA) or Fault Tree Analysis (FTA) to systematically evaluate potential risks. The ASQ offers resources and tools for risk assessment.
Prioritize Risks: Not all risks are equal. Use a risk matrix to prioritize risks based on their severity and likelihood. This helps focus efforts on the most critical risks.
Mitigation Strategies: Develop and implement strategies to mitigate high-priority risks. This could involve changes in processes, training, or introducing new controls. The Project Management Institute provides insights into effective risk mitigation strategies.
Continuous Monitoring: Risk management is an ongoing process. Regularly review and update your risk assessments, especially when there are changes in processes, regulations, or the external environment.
Documentation and Reporting: Maintain comprehensive documentation of all risk management activities. This ensures transparency and facilitates communication among stakeholders. The FDA’s Guidance on Risk Management offers a framework for documenting risk management processes in a regulatory context.
Training and Culture: Foster a risk-aware culture within the organization by providing regular training and encouraging open communication about risks.
By systematically implementing these steps, Validation Managers can significantly improve risk management processes, ensuring that validation activities are conducted efficiently and in compliance with regulatory requirements.
How to Display Risk Management Skills on Your Resume
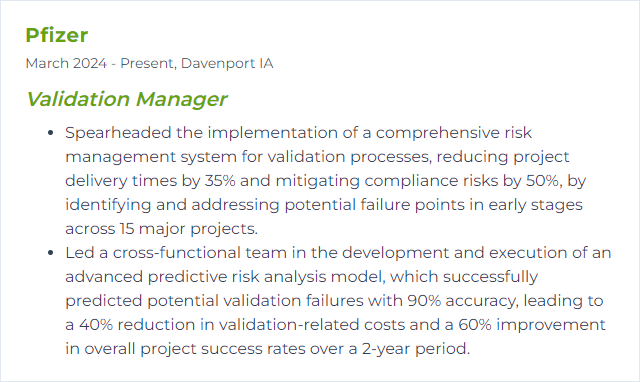
6. Process Validation
Process Validation is a documented procedure for obtaining, recording, and interpreting the results needed to establish that a process consistently produces a product meeting its predetermined specifications and quality attributes.
Why It's Important
Process validation ensures that manufacturing processes consistently produce products meeting predetermined quality criteria, minimizing risks and ensuring regulatory compliance, essential for product safety and efficacy.
How to Improve Process Validation Skills
Improving Process Validation involves a strategic approach focusing on compliance, efficiency, and continuous improvement. Here's a concise guide for a Validation Manager:
Understand Guidelines: Familiarize yourself with current regulatory guidelines (e.g., FDA Process Validation Guidance) to ensure compliance.
Risk Management: Implement a risk-based approach as per ICH Q9 to identify and mitigate potential failures early in the validation process.
Design of Experiments (DoE): Use DoE techniques to understand process variability and establish robust process controls. DoE resources can be found through ASQ.
Involve Cross-functional Teams: Collaboration between departments ensures diverse expertise in the validation process, enhancing outcome quality and efficiency.
Continuous Monitoring: Utilize continuous monitoring and data analysis tools to ensure ongoing control and improvement of the process. Tools like SPC can be instrumental.
Training and Development: Invest in regular training for the validation team on the latest validation principles, technologies, and regulatory changes.
Leverage Technology: Implement advanced software solutions for validation management to improve data integrity, traceability, and efficiency. Explore options like MasterControl for software support.
Review and Improve: Regularly review validation processes and outcomes to identify areas for improvement. Implement a feedback loop for continuous process enhancement.
Documentation Excellence: Ensure meticulous documentation at every stage of the validation process for regulatory compliance and knowledge transfer. Guidance on documentation best practices can be found through regulatory bodies' websites.
Stakeholder Communication: Maintain clear and consistent communication with all stakeholders, including regulatory bodies, to ensure alignment and compliance.
By focusing on these areas, a Validation Manager can significantly improve the efficiency, compliance, and effectiveness of the process validation activities.
How to Display Process Validation Skills on Your Resume
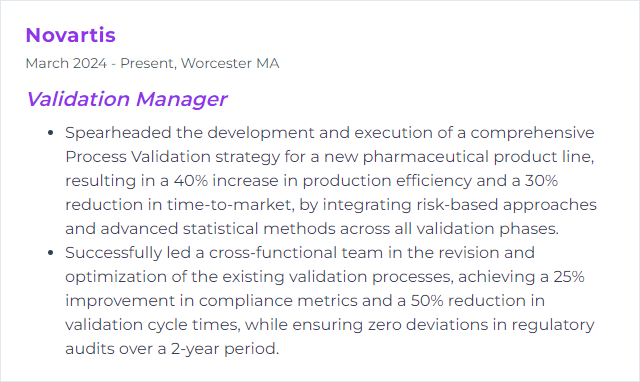
7. Equipment Qualification
Equipment Qualification is the process of demonstrating that an equipment or system is properly installed, works correctly, and consistently produces the expected results within specified parameters. It's essential for ensuring reliability, consistency, and compliance with industry standards and regulatory requirements. This process typically involves stages such as Design Qualification (DQ), Installation Qualification (IQ), Operational Qualification (OQ), and Performance Qualification (PQ).
Why It's Important
Equipment Qualification is crucial as it ensures that equipment is properly installed, operates correctly, and consistently produces the intended results, guaranteeing product quality, safety, and regulatory compliance.
How to Improve Equipment Qualification Skills
Improving Equipment Qualification involves a strategic approach to ensure that equipment performs safely and consistently within specified limits. As a Validation Manager, focusing on the following points can streamline the process:
Define Clear Requirements: Start by comprehensively documenting equipment specifications, intended use, and regulatory requirements. This clarity ensures all stakeholders are aligned. ISPE’s Baseline® Guide: Commissioning and Qualification offers industry-standard practices.
Risk Assessment: Implement a risk-based approach to prioritize efforts and resources. This involves identifying potential risks to product quality and focusing on critical aspects of the equipment. The ICH Q9 Quality Risk Management provides guidelines for a structured process.
Develop a Qualification Plan: Outline a comprehensive plan that includes Design Qualification (DQ), Installation Qualification (IQ), Operational Qualification (OQ), and Performance Qualification (PQ). The plan should detail the methodology, acceptance criteria, and responsibilities. FDA’s Guidance for Industry on Process Validation includes principles that can be applied to equipment qualification.
Effective Training: Ensure that all personnel involved in qualification activities are adequately trained on the equipment, procedures, and regulatory standards. Continuous training helps in maintaining compliance and efficiency.
Documentation and Review: Maintain thorough documentation for each qualification phase, including test results, deviations, and corrective actions. Regular reviews of the qualification documentation ensure ongoing compliance and facilitate audits. GAMP® 5 Guide: A Risk-Based Approach to Compliant GxP Computerized Systems provides a framework for good automated manufacturing practice, relevant for documentation practices.
Continuous Improvement: Utilize feedback and data from the qualification process to drive continuous improvement. Implement a systematic approach for periodic review and requalification to adapt to changes in regulations, equipment, or process.
By focusing on these key areas, a Validation Manager can enhance the robustness, efficiency, and compliance of Equipment Qualification processes.
How to Display Equipment Qualification Skills on Your Resume
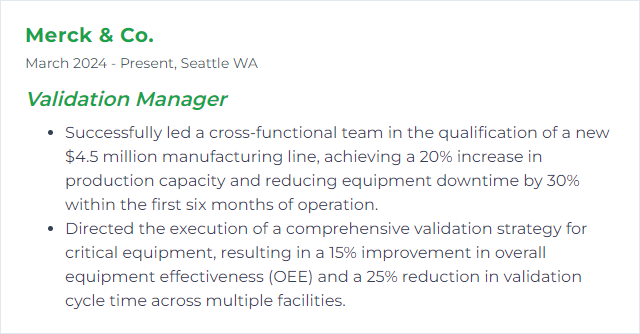
8. Cleanroom Protocols
Cleanroom protocols are a set of stringent procedures designed to maintain a controlled environment free from pollutants such as dust, airborne microbes, and aerosol particles. For a Validation Manager, these protocols ensure that the cleanroom meets specific cleanliness standards and regulatory requirements through regular monitoring, testing, and validation of the environment and processes to prevent contamination of products, especially in industries like pharmaceuticals, biotech, and electronics manufacturing.
Why It's Important
Cleanroom protocols are crucial for ensuring the integrity of controlled environments, preventing contamination, and maintaining product quality and safety. This is essential for meeting regulatory requirements and customer expectations, ultimately protecting both the company's reputation and consumer health.
How to Improve Cleanroom Protocols Skills
Improving cleanroom protocols, especially from a Validation Manager's perspective, involves a multifaceted approach to ensure compliance, efficiency, and safety. Here’s a concise guide:
Update SOPs Regularly: Ensure standard operating procedures (SOPs) are up-to-date with the latest industry standards and regulations. This includes reviewing and updating protocols for cleaning, gowning, and equipment operation. ISO Standards provide a benchmark for cleanroom conditions.
Employee Training: Conduct regular training sessions for employees on cleanroom behavior, contamination control, and proper use of equipment. Keeping staff informed about the importance of protocols boosts compliance. The Institute of Environmental Sciences and Technology (IEST) offers resources and training programs.
Monitor and Validate: Use real-time monitoring systems to track environmental conditions like temperature, humidity, and particulate levels. Regular validation of cleanroom performance against ISO 14644-1 standards ensures adherence to cleanliness levels.
Equipment Maintenance: Implement a stringent maintenance schedule for all cleanroom equipment. Ensuring machinery is in optimal condition reduces the risk of contamination. ISPE Guidelines provide insights into best practices for equipment maintenance in clean environments.
Audit and Feedback: Conduct periodic internal audits to assess protocol adherence and identify areas for improvement. Encourage feedback from employees as they may provide practical insights for enhancing cleanroom operations.
Quality Control Checks: Implement rigorous quality control checks for materials entering the cleanroom. This minimizes the introduction of contaminants. Guidelines by FDA’s Aseptic Processing Guide offer comprehensive practices for material handling.
Incident Management: Develop a clear protocol for managing and documenting incidents of contamination. This helps in tracing sources of contamination and preventing future occurrences.
Improving cleanroom protocols is an ongoing process that requires diligence, continuous learning, and adaptation to technological advancements and regulatory changes.
How to Display Cleanroom Protocols Skills on Your Resume
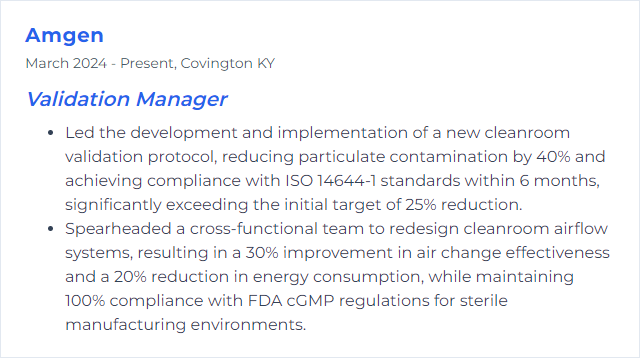
9. Statistical Analysis
Statistical analysis is the process of collecting, examining, interpreting, and presenting data to uncover patterns, trends, and relationships, enabling informed decision-making. For a Validation Manager, it is crucial for validating processes, ensuring reliability, and demonstrating compliance with industry standards.
Why It's Important
Statistical analysis is crucial for a Validation Manager as it provides a rigorous, quantifiable basis for evaluating the reliability and performance of systems or processes, ensuring they meet specified requirements and standards. This facilitates informed decision-making, risk management, and compliance with regulatory guidelines.
How to Improve Statistical Analysis Skills
Improving statistical analysis, especially for a Validation Manager, involves enhancing the accuracy, reliability, and interpretability of data analysis. Here are concise strategies:
Understand the Data: Deeply understand the data you're working with, including its sources, limitations, and the appropriate statistical methods for analysis. Data Understanding.
Use Appropriate Statistical Methods: Match your statistical methods to the data type and analysis objectives. This may involve regression analysis for predicting outcomes or ANOVA for comparing groups. Choosing the Right Statistical Test.
Validate Models and Methods: Ensure the reliability of your statistical models through validation techniques such as cross-validation or bootstrapping. This helps in confirming that your models perform well on unseen data. Model Validation Techniques.
Enhance Data Quality: Work on improving the quality of data through proper collection, handling, and preprocessing methods. Address issues like missing values and outliers. Data Preprocessing.
Stay Updated with Statistical Advances: Continuously update your knowledge and skills in statistical analysis by following new research, attending workshops, and using advanced software tools. Statistical Learning.
Collaborate and Communicate: Engage with other professionals through forums, seminars, and professional networks to share knowledge and challenges. Effective communication with stakeholders about your analysis process and findings is crucial. Effective Communication in Statistics.
Leverage Software Tools: Utilize statistical software tools and platforms that offer advanced features for data analysis, visualization, and reporting. R Project and Python for Data Analysis.
Implement Rigorous Quality Control: Adopt stringent quality control measures in your statistical analysis process to ensure accuracy and reliability of results. Quality Control in Statistics.
By focusing on these areas, a Validation Manager can significantly improve the statistical analysis process, leading to more accurate and reliable outcomes.
How to Display Statistical Analysis Skills on Your Resume
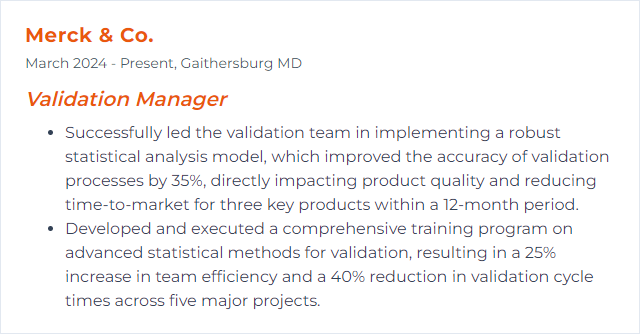
10. Six Sigma
Six Sigma is a data-driven methodology and set of tools designed to improve processes by minimizing defects and variability, aiming to achieve near-perfect quality. For a Validation Manager, it provides a structured approach to validate and enhance process performance, ensuring products or services meet stringent quality standards.
Why It's Important
Six Sigma is important for a Validation Manager because it provides a systematic methodology to reduce variability and errors in processes, ensuring product quality and regulatory compliance, thereby enhancing customer satisfaction and operational efficiency.
How to Improve Six Sigma Skills
Improving Six Sigma, particularly for a Validation Manager, involves enhancing the quality and efficiency of processes through continuous improvement and defect reduction. Here are concise steps and resources for improvement:
Enhance Team Skills: Train your team in Six Sigma methodologies. This includes DMAIC (Define, Measure, Analyze, Improve, Control) for existing processes and DMADV (Define, Measure, Analyze, Design, Verify) for new processes. ASQ's Six Sigma Training offers comprehensive courses.
Implement Lean Principles: Combine Six Sigma with Lean manufacturing. Lean focuses on waste reduction, complementing Six Sigma’s focus on variation and defect reduction. Lean Enterprise Institute provides insights into integrating these practices.
Utilize Statistical Tools: Make extensive use of statistical tools for analyzing data, such as Minitab or SigmaXL. This helps in identifying root causes of defects. Resources for learning these tools can be found on their respective websites: Minitab and SigmaXL.
Focus on Customer Feedback: Align improvement projects with customer needs and feedback to ensure that quality enhancements meet market demands. Tools like Net Promoter Score (NPS) can be useful. Qualtrics offers a guide on NPS.
Optimize Validation Processes: As a Validation Manager, focus on optimizing validation processes by integrating Six Sigma techniques to improve the reliability and efficiency of testing and validation. The FDA’s Process Validation: General Principles and Practices guide provides a regulatory framework that can be enhanced with Six Sigma methodologies.
Regular Audits and Reviews: Conduct regular Six Sigma project audits and process reviews to ensure continuous improvement. Applying Six Sigma’s DMAIC cycle to the audit process itself can lead to improvements in efficiency and effectiveness.
Encourage a Culture of Continuous Improvement: Foster an organizational culture that values continuous improvement. Leadership commitment and employee involvement are crucial for sustaining Six Sigma initiatives. The American Society for Quality (ASQ) offers resources on building such a culture.
By following these steps and utilizing the provided resources, a Validation Manager can significantly improve Six Sigma processes, leading to higher quality, greater efficiency, and increased customer satisfaction.
How to Display Six Sigma Skills on Your Resume
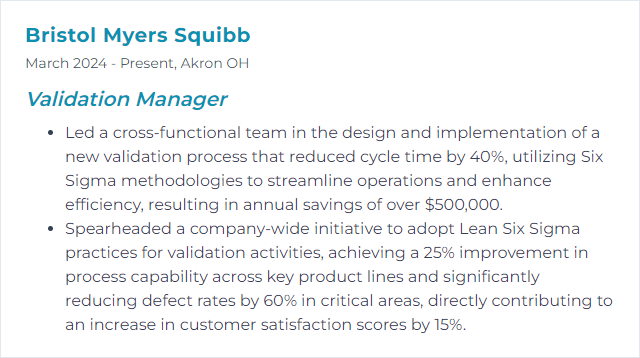
11. V&V (Verification and Validation)
V&V (Verification and Validation) in the context of a Validation Manager involves the process of ensuring that a product, service, or system meets requirements and specifications (Verification) and fulfills its intended purpose effectively and efficiently (Validation). Verification checks that the product was built correctly according to specifications, while Validation ensures the right product was built for the customer's needs.
Why It's Important
V&V (Verification and Validation) is crucial as it ensures that a product or system meets its design specifications (verification) and fulfills its intended purpose effectively and safely (validation). This process minimizes the risk of failures or non-compliance, ensuring high quality, reliability, and regulatory adherence, which is paramount for customer satisfaction and legal compliance. For a Validation Manager, it is essential for managing risks, optimizing performance, and maintaining the product's integrity throughout its lifecycle.
How to Improve V&V (Verification and Validation) Skills
Improving Verification and Validation (V&V) processes involves a strategic approach focused on enhancing efficiency, accuracy, and compliance. For a Validation Manager, here are key steps to take:
Define Clear Objectives: Establish clear, measurable objectives for both verification and validation activities. SMART goals can guide you in setting specific, measurable, achievable, relevant, and time-bound objectives.
Standardize Processes: Adopt and enforce industry standards and best practices for V&V activities. ISO 9001 provides guidelines for quality management systems and can be a valuable reference.
Implement Automated Tools: Utilize automated testing tools to increase efficiency and reduce human error. Tools like Selenium for software testing can significantly improve your V&V processes.
Continuous Training: Ensure your team is up to date with the latest V&V methodologies and tools through ongoing training. Coursera and LinkedIn Learning offer courses relevant to V&V practices.
Engage Stakeholders Early: Involve stakeholders, including customers and end-users, early in the V&V process to ensure the output meets their needs and expectations. Stakeholder engagement strategies by PMI can provide valuable insights.
Regular Reviews and Audits: Conduct regular reviews and audits of V&V activities to ensure compliance with quality standards and to identify areas for improvement. ASQ’s auditing handbook is a comprehensive resource.
Feedback Loops: Establish mechanisms for collecting and integrating feedback from all V&V phases to continuously improve processes. Feedback loops in V&V can enhance product quality and team performance.
Risk Management: Incorporate risk management into your V&V strategy to identify potential issues early in the process. The ISO 31000 standard provides guidelines on risk management principles and practices.
By focusing on these key areas, a Validation Manager can significantly improve the effectiveness and efficiency of their V&V processes.
How to Display V&V (Verification and Validation) Skills on Your Resume
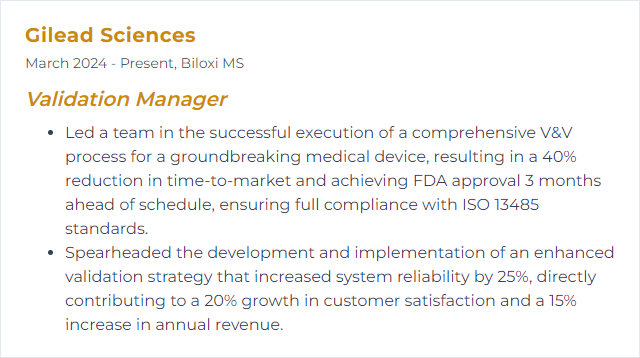
12. SAP ERP
SAP ERP is an enterprise resource planning software that integrates key business functions such as finance, HR, manufacturing, and supply chain management, enabling efficient and standardized processes across an organization. For a Validation Manager, it provides a centralized platform to ensure compliance, quality control, and process validation within these integrated systems.
Why It's Important
For a Validation Manager, SAP ERP is crucial as it ensures the integrity, compliance, and efficiency of business processes through a centralized and standardized system, facilitating effective management and validation of critical data across the organization.
How to Improve SAP ERP Skills
Improving SAP ERP, especially from a Validation Manager's perspective, involves enhancing system reliability, compliance, and efficiency. Here are succinct strategies:
Enhance Data Quality: Implement strict data validation rules and regular audits to ensure data integrity. SAP Master Data Governance can aid in maintaining high-quality data across the enterprise.
Automate Processes: Utilize SAP Intelligent Robotic Process Automation to automate repetitive and manual tasks, reducing errors and freeing up resources for more critical tasks.
Optimize System Performance: Regularly monitor system performance and utilize tools like SAP Solution Manager to identify and resolve bottlenecks, ensuring smooth and efficient operations.
Regular Training and Support: Provide continuous training and support to users to ensure they are proficient in using the system effectively. SAP offers various training and certification courses for users at different levels.
Compliance and Security: Regularly update the system to comply with the latest regulations and security standards. Use SAP GRC solutions to manage compliance and risks efficiently.
Customization and Integration: Customize and integrate SAP ERP with other systems and tools specific to your business needs for seamless operations. Explore SAP API Business Hub for integration options.
By focusing on these areas, a Validation Manager can significantly improve the performance and reliability of SAP ERP within their organization.
How to Display SAP ERP Skills on Your Resume
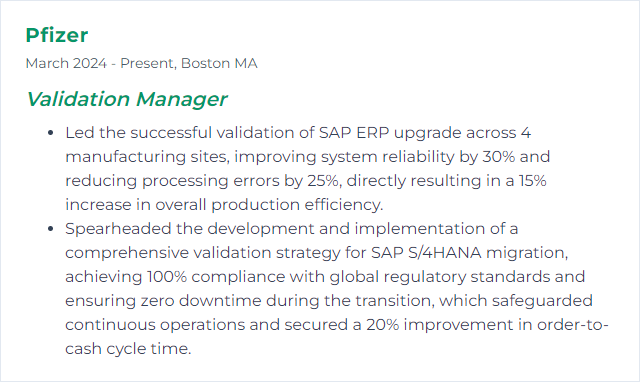