Top 12 Supply Chain Specialist Skills to Put on Your Resume
In today's fast-paced and interconnected global economy, a skilled supply chain specialist is invaluable, making the demand for professionals with the right set of skills more critical than ever. Crafting a resume that highlights a comprehensive set of supply chain management skills can significantly elevate your marketability, ensuring you stand out in a competitive job market.
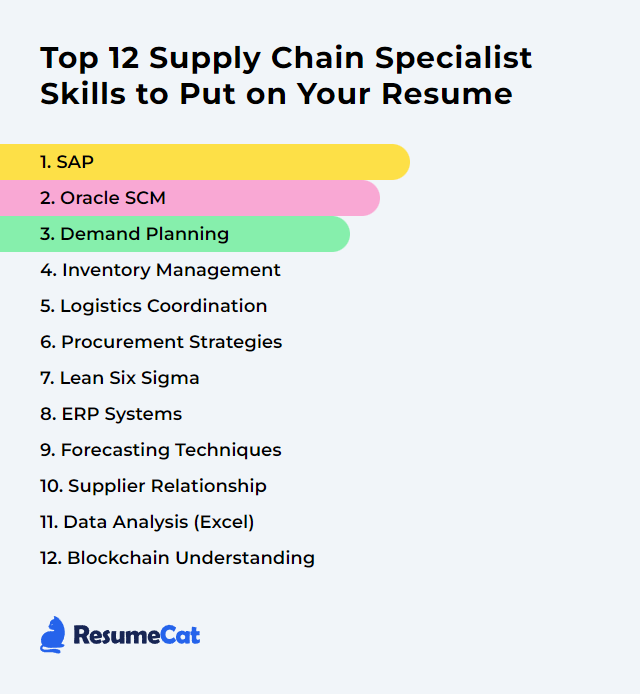
Supply Chain Specialist Skills
- SAP
- Oracle SCM
- Demand Planning
- Inventory Management
- Logistics Coordination
- Procurement Strategies
- Lean Six Sigma
- ERP Systems
- Forecasting Techniques
- Supplier Relationship
- Data Analysis (Excel)
- Blockchain Understanding
1. SAP
SAP is a comprehensive enterprise resource planning (ERP) software that integrates all aspects of business operations, including supply chain management, to enhance process efficiency, data accuracy, and decision-making for organizations.
Why It's Important
SAP is crucial for a Supply Chain Specialist because it streamlines and integrates procurement, production, and distribution processes, enhancing efficiency, visibility, and collaboration across the entire supply chain.
How to Improve SAP Skills
Improving SAP for a Supply Chain Specialist involves enhancing system efficiency, data accuracy, and user experience. Here’s a concise guide:
Customization and Optimization: Tailor SAP to fit your specific supply chain needs. Utilize SAP's Customizing Guide to adjust settings for procurement, inventory management, and order processing.
Integration: Ensure seamless integration with other systems (CRM, external databases) for real-time data exchange. SAP offers integration solutions to connect different systems efficiently.
Data Management: Implement strict data management protocols. Cleanse and standardize data using tools like SAP Master Data Governance to ensure accuracy and reliability.
Training and Support: Invest in ongoing training for users. SAP provides various training and certification programs to enhance user competence and system utilization.
Leverage Advanced Technologies: Utilize SAP’s advanced technologies like AI and IoT within the SAP Leonardo digital innovation system to automate processes and gain insights.
Performance Monitoring: Regularly review system performance using SAP Solution Manager. Adjust configurations as needed to improve response times and efficiency.
User Experience: Enhance the user interface with SAP Fiori for a more intuitive, user-friendly experience.
Feedback Loop: Establish a feedback mechanism for users to report issues and suggest improvements, fostering continuous optimization.
By focusing on these areas, a Supply Chain Specialist can significantly enhance the functionality and efficiency of their SAP system, leading to optimized operations and strategic advantage.
How to Display SAP Skills on Your Resume
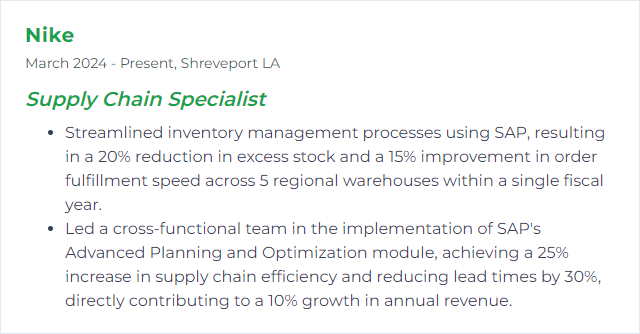
2. Oracle SCM
Oracle SCM (Supply Chain Management) is a comprehensive suite of cloud-based applications designed to streamline and optimize all aspects of supply chain operations, including planning, procurement, manufacturing, and logistics, enabling Supply Chain Specialists to improve efficiency, reduce costs, and enhance supply chain visibility and agility.
Why It's Important
Oracle SCM (Supply Chain Management) is crucial for a Supply Chain Specialist as it integrates and automates all aspects of the supply chain, optimizing logistics, improving demand forecasting, enhancing inventory management, and facilitating seamless collaboration across suppliers and customers. This leads to increased efficiency, reduced costs, and improved customer satisfaction.
How to Improve Oracle SCM Skills
Improving Oracle SCM involves optimizing processes, leveraging the latest features, and enhancing user skill sets. Here's a concise guide tailored for a Supply Chain Specialist:
Stay Updated: Regularly update your Oracle SCM Cloud to leverage new functionalities and improvements. Oracle's What's New page provides the latest updates.
Train and Certify: Enhance your team's capabilities through Oracle University's training and certification programs. Oracle SCM Training offers courses for various roles.
Optimize Integration: Ensure seamless integration with other systems (ERP, CRM) for real-time data exchange. Oracle's Integration Cloud Service (ICS) can streamline this process.
Leverage Analytics: Utilize Oracle SCM Cloud's built-in analytics for data-driven decisions. The Oracle SCM Analytics page offers insights into its capabilities.
Customize Smartly: Customize only when necessary and in a way that doesn't hinder upgrades. Oracle's Customization Best Practices guide provides strategies for effective customization.
Engage with the Community: Join Oracle Cloud Customer Connect forums for insights, tips, and networking with peers. Oracle Cloud Customer Connect is a valuable resource for collaboration.
Implement Best Practices: Follow Oracle SCM best practices for your industry. Oracle provides a Best Practice Guide that outlines strategies for success.
Seek Professional Guidance: Consider consulting with Oracle partners for tailored advice and implementation support. The Oracle PartnerNetwork directory can help you find the right expertise.
By focusing on continuous learning, leveraging technological advancements, and engaging with the Oracle SCM community, a Supply Chain Specialist can significantly enhance the efficiency and effectiveness of their supply chain operations.
How to Display Oracle SCM Skills on Your Resume
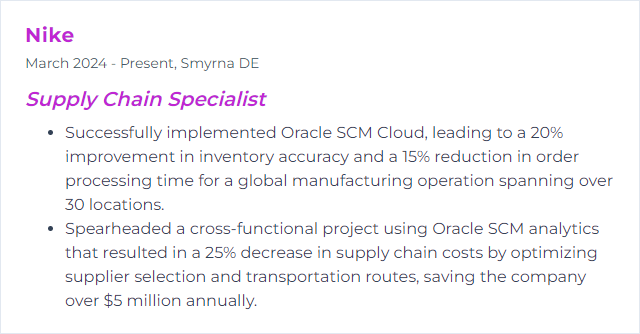
3. Demand Planning
Demand Planning is the process of forecasting customer demand to optimize supply chain processes, ensuring the right balance between inventory levels and customer satisfaction.
Why It's Important
Demand Planning is crucial for a Supply Chain Specialist as it enables accurate forecasting of customer demand, ensuring optimal inventory levels, reducing costs, and improving customer satisfaction through timely product availability.
How to Improve Demand Planning Skills
Improving Demand Planning involves refining the processes used to forecast customer demand and aligning those forecasts with supply chain operations. Here are concise steps aimed at enhancing Demand Planning for a Supply Chain Specialist:
Implement Advanced Forecasting Tools: Utilize advanced forecasting software that incorporates AI and machine learning to analyze historical data and predict future demand more accurately.
Enhance Data Quality: Ensure the accuracy and consistency of data used in demand planning by regular audits and integrating data from all relevant sources.
Collaborative Planning: Foster collaboration between departments (sales, marketing, finance) and external partners (suppliers, customers) to share insights and adjust forecasts in real time.
Market Analysis: Continuously monitor market trends and consumer behavior to anticipate changes in demand. This includes staying informed about economic indicators, seasonal fluctuations, and competitive actions.
Inventory Optimization: Use demand planning data to optimize inventory levels, ensuring the right balance between meeting demand and minimizing holding costs. Inventory optimization tools can help in setting reorder points and quantities.
Scenario Planning: Prepare for uncertainty by developing multiple demand scenarios based on different assumptions. This allows for quicker adjustments in strategy as actual demand patterns emerge.
Continuous Improvement: Regularly review and adjust demand planning processes based on performance metrics and feedback. This should involve iterative learning and refinement to improve accuracy over time.
By focusing on these key areas, a Supply Chain Specialist can significantly enhance the effectiveness of Demand Planning, leading to improved supply chain efficiency and customer satisfaction.
How to Display Demand Planning Skills on Your Resume
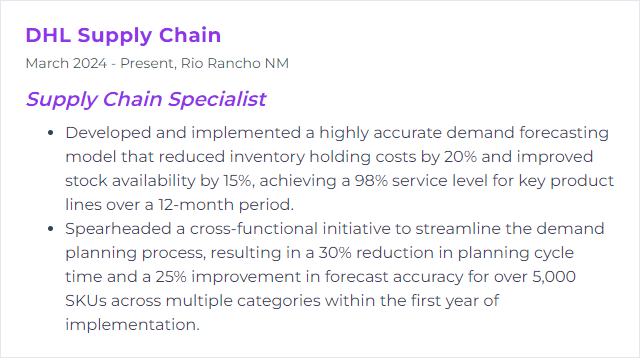
4. Inventory Management
Inventory management is the process of overseeing and controlling the flow of goods from manufacturers to warehouses and ultimately to the point of sale, ensuring the right quantity of products is available at the right time and place without excessive surplus or shortage, to optimize supply chain efficiency and cost-effectiveness.
Why It's Important
Inventory management is crucial for ensuring optimal stock levels, minimizing costs, and meeting customer demand efficiently, thereby enhancing the supply chain's overall performance and profitability.
How to Improve Inventory Management Skills
Improving inventory management, especially for a Supply Chain Specialist, involves several key strategies:
Implement an Inventory Management System: Use software that integrates with your existing supply chain management tools to automate stock tracking and reorder processes. Shopify's guide provides insight into choosing the right system.
Adopt Just-In-Time (JIT) Inventory: Reduce waste and storage costs by receiving goods only as they are needed in the production process. The Lean Enterprise Institute explains JIT principles in detail.
Improve Forecasting: Use historical data, market trends, and predictive analytics to better anticipate demand and adjust inventory levels accordingly. Harvard Business Review offers strategies for enhancing forecasting accuracy.
Regularly Audit Inventory: Conduct physical counts periodically to verify stock levels and identify discrepancies early. Vend's Retail Blog outlines steps for conducting an effective inventory audit.
Optimize Supplier Relationships: Collaborate closely with suppliers to improve lead times, reduce costs, and ensure quality. The Institute for Supply Management provides resources for enhancing supplier relationships.
Implement ABC Analysis: Classify inventory into three categories (A, B, and C) based on importance to prioritize management efforts. Investopedia describes ABC analysis in more detail.
Enhance Returns Management: Develop an efficient process for handling returns to minimize losses and restock items quickly. Reverse Logistics Association offers insights into optimizing returns management.
By focusing on these strategies, a Supply Chain Specialist can significantly improve inventory management, contributing to the overall efficiency and profitability of the supply chain.
How to Display Inventory Management Skills on Your Resume
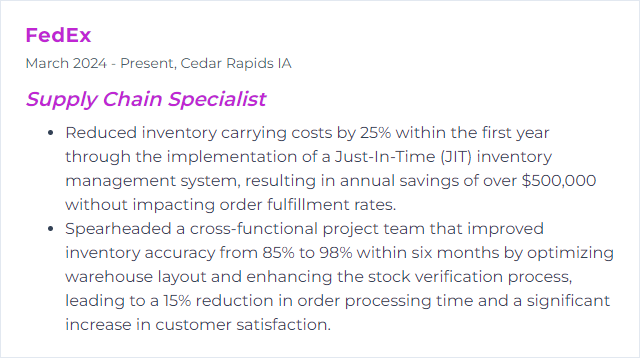
5. Logistics Coordination
Logistics coordination involves managing and overseeing the movement, storage, and supply of goods throughout the supply chain, ensuring timely delivery and optimal use of resources. It includes planning, executing, and monitoring transportation, warehousing, and distribution activities.
Why It's Important
Logistics coordination is crucial for ensuring efficient and timely movement of goods, optimizing supply chain operations, minimizing costs, and meeting customer demands effectively.
How to Improve Logistics Coordination Skills
Improving logistics coordination involves optimizing the flow of goods, information, and resources throughout the supply chain to enhance efficiency and reduce costs. For a Supply Chain Specialist, here are concise strategies:
Implement Technology Solutions: Use Transportation Management Systems (TMS) and Warehouse Management Systems (WMS) to automate processes, improve tracking, and enhance communication between stakeholders.
Enhance Communication: Foster better communication within and between organizations to ensure everyone is aligned with goals and expectations.
Optimize Inventory Management: Implement just-in-time (JIT) inventory strategies to reduce holding costs and minimize stockouts or excess inventory.
Strengthen Supplier Relationships: Develop strong, collaborative relationships with suppliers to ensure reliability and efficiency. Tools like Supplier Relationship Management (SRM) software can aid in managing these relationships effectively.
Analyze and Optimize Routes: Use logistics software to analyze and optimize shipping routes and modes of transportation, reducing costs and transit times.
Continuous Improvement: Adopt a culture of continuous improvement by regularly reviewing logistics processes and performance, using methodologies like Lean and Six Sigma to identify and eliminate inefficiencies.
By integrating these strategies, a Supply Chain Specialist can significantly enhance logistics coordination, leading to improved operational efficiency, cost savings, and better customer satisfaction.
How to Display Logistics Coordination Skills on Your Resume
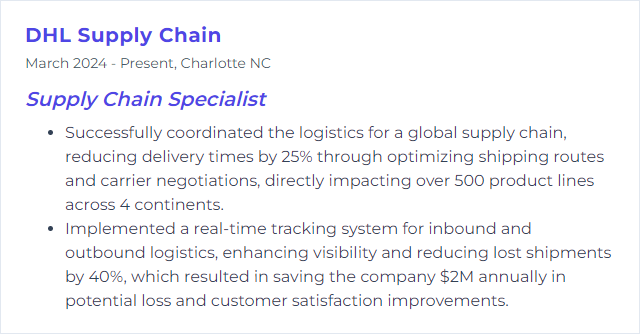
6. Procurement Strategies
Procurement strategies in the context of a Supply Chain Specialist involve the deliberate planning and execution of methods aimed at optimizing the acquisition of goods and services. This includes selecting appropriate suppliers, negotiating contracts, managing relationships, and aligning purchases with company goals to ensure efficiency, cost-effectiveness, and supply chain resilience.
Why It's Important
Procurement strategies are crucial for a Supply Chain Specialist as they ensure the efficient and cost-effective acquisition of goods and services, maintaining quality and reliability, minimizing risks, and optimizing supplier relationships to achieve competitive advantage and meet organizational goals.
How to Improve Procurement Strategies Skills
Improving procurement strategies involves several key steps aimed at optimizing the efficiency and effectiveness of purchasing processes within the supply chain. Below are concise strategies with relevant resources for further exploration:
Leverage Technology: Implement advanced procurement software for better supplier management and process automation. Tools like SAP Ariba facilitate streamlined procurement operations.
Supplier Relationship Management (SRM): Foster strong, collaborative relationships with suppliers for mutual benefit, improving reliability and innovation. The Institute for Supply Management offers resources on SRM best practices.
Spend Analysis: Regularly review and analyze procurement spend to identify cost-saving opportunities and areas for efficiency improvements. CIPS provides insights on conducting spend analyses.
Risk Management: Develop strategies to mitigate risks such as supplier failures, geopolitical factors, or market fluctuations. The Global Supply Chain Institute offers resources on supply chain risk management.
Sustainable Procurement: Integrate sustainability into procurement decisions to meet regulatory requirements and consumer expectations. The Sustainable Procurement Guide by UNGM offers guidance on sustainable procurement practices.
Negotiation Strategies: Enhance negotiation skills to secure favorable terms and build beneficial supplier partnerships. Harvard Law School provides resources on negotiation tactics and strategies.
Continuous Improvement: Implement a continuous improvement culture to regularly review and enhance procurement processes. ASQ has resources on continuous improvement methodologies.
By focusing on these strategies, Supply Chain Specialists can significantly improve procurement operations, leading to cost savings, enhanced supplier relationships, and a more resilient supply chain.
How to Display Procurement Strategies Skills on Your Resume
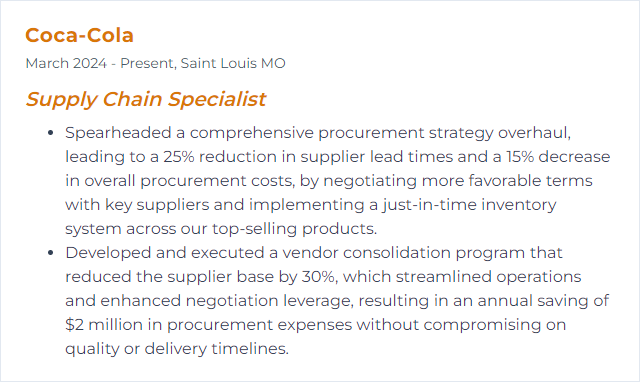
7. Lean Six Sigma
Lean Six Sigma is a methodology that combines the waste reduction principles of Lean with the process improvement and defect reduction focus of Six Sigma, aiming to enhance efficiency, reduce variability, and improve quality in supply chain operations.
Why It's Important
Lean Six Sigma is important for a Supply Chain Specialist because it systematically eliminates waste and reduces variability in supply chain processes, leading to enhanced efficiency, improved quality, and increased customer satisfaction.
How to Improve Lean Six Sigma Skills
To improve Lean Six Sigma as a Supply Chain Specialist:
Understand the Basics: Familiarize yourself with the fundamentals of Lean Six Sigma. Focus on the DMAIC (Define, Measure, Analyze, Improve, Control) methodology for process improvement. ASQ’s Lean Six Sigma Overview is a great starting point.
Identify Key Processes: Identify critical supply chain processes that directly impact customer satisfaction and operational efficiency. Prioritize these for Lean Six Sigma projects.
Utilize Data Analytics: Leverage data analytics to identify inefficiencies and bottlenecks within the supply chain. Tools like Minitab can help in analyzing data for informed decision-making.
Engage Stakeholders: Involve all stakeholders, including suppliers and customers, in the improvement process. Their insights can provide valuable perspectives on areas for improvement. The Institute for Supply Management offers resources on supplier relationships.
Implement Technology Solutions: Adopt technology solutions like ERP systems or supply chain management software to enhance visibility and control over the supply chain. Research platforms through Gartner’s Market Research for industry-leading solutions.
Continuous Training: Invest in continuous training and certification for the team in Lean Six Sigma methodologies. Organizations like IASSC offer certification programs.
Measure and Adjust: Regularly measure the impact of implemented changes using KPIs and adjust strategies as necessary. This iterative approach ensures continuous improvement.
By focusing on these steps, a Supply Chain Specialist can significantly improve processes within their supply chain, leveraging Lean Six Sigma methodologies for enhanced efficiency and customer satisfaction.
How to Display Lean Six Sigma Skills on Your Resume
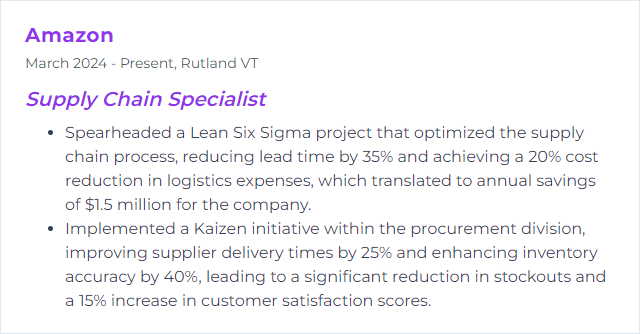
8. ERP Systems
ERP (Enterprise Resource Planning) systems are integrated software platforms used by organizations to manage and automate core business processes, including supply chain operations, inventory management, procurement, and logistics, ensuring real-time visibility, efficiency, and coordination across various departments.
Why It's Important
ERP systems centralize and streamline data across an organization, offering real-time visibility and coordination of all supply chain operations. This ensures efficient inventory management, procurement, order fulfillment, and demand forecasting, significantly improving decision-making and operational efficiency for Supply Chain Specialists.
How to Improve ERP Systems Skills
Improving ERP (Enterprise Resource Planning) systems, especially from a Supply Chain Specialist perspective, involves focusing on integration, automation, real-time data access, and adaptability. Here are concise strategies:
Integration Enhancement: Strengthen the ERP's ability to seamlessly integrate with other tools and platforms, including CRM, SCM, and BI tools, to ensure smooth data flow and comprehensive visibility across all departments. SAP and Oracle offer robust integration capabilities.
Automation of Processes: Automate repetitive and time-consuming tasks within the supply chain to reduce errors, save time, and increase efficiency. Tools like Blue Yonder can significantly improve automation within supply chains.
Real-time Data Access: Upgrade the ERP system to provide real-time data analytics and reporting capabilities. This ensures timely decision-making based on current data. Infor ERP solutions offer strong real-time data analytics features.
Cloud-based Solutions: Transition to cloud-based ERP solutions for better scalability, flexibility, and remote access. Providers like Microsoft Dynamics 365 offer comprehensive cloud-based ERP solutions.
Customization and User Training: Tailor the ERP system to meet the specific needs of the supply chain and conduct regular training sessions for users to maximize the system’s potential.
Enhance Security Measures: Implement robust cybersecurity measures to protect sensitive supply chain data. Regular updates and security audits are crucial.
Sustainability Focus: Incorporate tools and modules within the ERP that aid in measuring and improving the sustainability aspects of the supply chain.
By focusing on these areas, Supply Chain Specialists can significantly improve their ERP systems, leading to enhanced efficiency, accuracy, and decision-making capabilities within the supply chain.
How to Display ERP Systems Skills on Your Resume
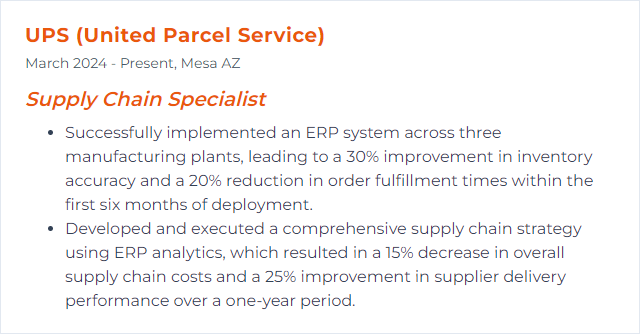
9. Forecasting Techniques
Forecasting techniques in supply chain management involve using historical data, market trends, and statistical methods to predict future demand, inventory needs, and resource requirements. These techniques help supply chain specialists make informed decisions on production planning, inventory management, and procurement to optimize efficiency and meet customer demand.
Why It's Important
Forecasting techniques are crucial for a Supply Chain Specialist because they enable accurate predictions of demand, inventory needs, and production planning. This ensures optimal stock levels, reduces costs, improves customer satisfaction, and enhances overall supply chain efficiency.
How to Improve Forecasting Techniques Skills
Improving forecasting techniques in the context of supply chain requires a multifaceted approach focusing on data quality, technology adoption, and methodology refinement. Here are some concise steps:
Enhance Data Quality: Ensure the accuracy and completeness of historical data, as it forms the foundation of forecasting. Data Quality Management is crucial for reliable predictions.
Implement Advanced Technologies: Adopt AI and machine learning for dynamic forecasting models. These technologies can uncover complex patterns in data. Explore Machine Learning for Supply Chain Forecasting.
Collaborative Planning: Engage in Collaborative Planning, Forecasting, and Replenishment (CPFR) with partners to integrate external insights. The VICS CPFR Model provides a standard framework.
Demand Sensing: Use demand sensing tools to react to real-time market changes for short-term accuracy. This involves leveraging current data points to predict immediate demand. Read more about Demand Sensing.
Continuous Improvement: Regularly review and adjust forecasting methods based on performance feedback. This iterative process is essential for adapting to changes in the market and supply chain. Familiarize yourself with the principles of Continuous Improvement.
Training and Skills Development: Enhance the skills of the team responsible for forecasting through continuous training on new tools and techniques. Investing in Supply Chain Education can pay dividends in improved forecasting accuracy.
By focusing on these areas, a supply chain specialist can significantly improve forecasting techniques, leading to more efficient operations and better alignment with market demand.
How to Display Forecasting Techniques Skills on Your Resume
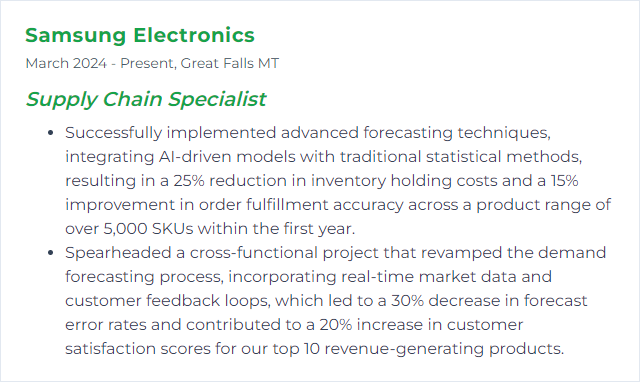
10. Supplier Relationship
Supplier Relationship in the context of a Supply Chain Specialist refers to the strategic management and interaction with suppliers to optimize the value and performance within the supply chain, focusing on collaboration, trust, and mutually beneficial outcomes.
Why It's Important
Supplier relationships are crucial for ensuring a reliable, cost-effective, and quality supply chain, enabling proactive management of risks and fostering innovation and collaboration for continuous improvement and competitive advantage.
How to Improve Supplier Relationship Skills
Improving supplier relationships involves strategic management and communication efforts to build trust, ensure mutual benefits, and enhance performance. Here’s a concise guide for a Supply Chain Specialist:
Communication: Establish open, transparent, and continuous communication channels. Discuss goals, expectations, and feedback regularly. Institute for Supply Management
Performance Metrics: Set clear, measurable performance indicators. Use these metrics for regular reviews and to identify improvement areas. APICS (now part of ASCM)
Collaboration: Engage in joint activities like product development or process improvement. This approach fosters innovation and shared success. Council of Supply Chain Management Professionals (CSCMP)
Long-term Partnerships: Focus on building long-term relationships rather than short-term gains. This commitment encourages investment in mutual growth. Supply Chain Management Review
Risk Management: Collaboratively identify potential risks and develop mitigation strategies. This proactive approach helps in maintaining a resilient supply chain. Risk Management Society (RIMS)
Technology Integration: Utilize technology for better data sharing, process integration, and efficiency. This enhances transparency and coordination. Digital Supply Chain Institute
Training and Development: Offer opportunities for supplier development through training and sharing best practices. This elevates the overall supply chain performance. The Chartered Institute of Procurement & Supply (CIPS)
Recognize and Reward: Acknowledge and reward superior performance. Recognition programs motivate suppliers to maintain high standards. Supply Chain Dive
By focusing on these key areas, a Supply Chain Specialist can significantly improve supplier relationships, leading to a more efficient, resilient, and competitive supply chain.
How to Display Supplier Relationship Skills on Your Resume
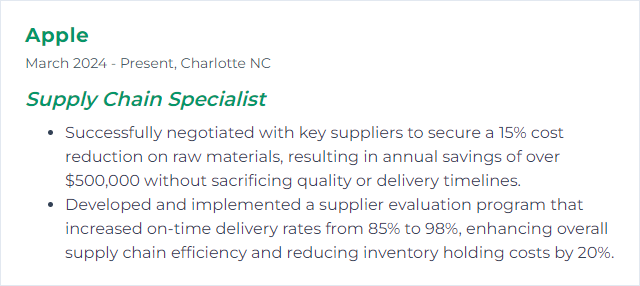
11. Data Analysis (Excel)
Data Analysis in Excel for a Supply Chain Specialist involves using Excel tools and functions to collect, process, and analyze supply chain data such as inventory levels, supplier performance, logistics costs, and demand forecasts, to optimize supply chain operations and decision-making.
Why It's Important
Data analysis using Excel is crucial for a Supply Chain Specialist as it enables efficient management of inventory levels, optimization of supply chain processes, forecasting demand accurately, and identifying cost-saving opportunities, leading to improved decision-making and operational efficiency.
How to Improve Data Analysis (Excel) Skills
Improving data analysis skills in Excel as a Supply Chain Specialist involves mastering specific functions and tools for effective data management, analysis, and visualization. Focus on:
Advanced Excel Functions: Master functions relevant to supply chain data such as
VLOOKUP
,INDEX
,MATCH
, andSUMIFS
for efficient data lookup and conditional analysis. Excel Functions Guide.PivotTables: Learn to create PivotTables for summarizing, analyzing, and presenting large data sets. This is crucial for inventory management, sales analysis, and forecasting. PivotTables Tutorial.
Data Visualization: Enhance your skills in creating charts and graphs in Excel. Visual representation of data like supply chain metrics and KPIs makes it easier to interpret and communicate insights. Data Visualization in Excel.
Power Query & Power Pivot: Use Power Query for data preprocessing and cleaning, and Power Pivot for advanced data modeling and analysis. These tools are powerful for handling and analyzing large datasets from diverse sources. Power Query and Power Pivot.
Macros and VBA: Automate repetitive tasks and customize Excel functionality to suit your specific supply chain needs using Macros and VBA. This can save time and increase efficiency. Getting Started with VBA.
Online Courses and Certifications: Invest time in Excel training courses and certifications. Platforms like LinkedIn Learning, Coursera, and Udemy offer specialized courses tailored to improving Excel skills for business analysis.
By focusing on these areas, a Supply Chain Specialist can significantly enhance their data analysis capabilities in Excel, leading to more informed decision-making and improved supply chain efficiency.
How to Display Data Analysis (Excel) Skills on Your Resume
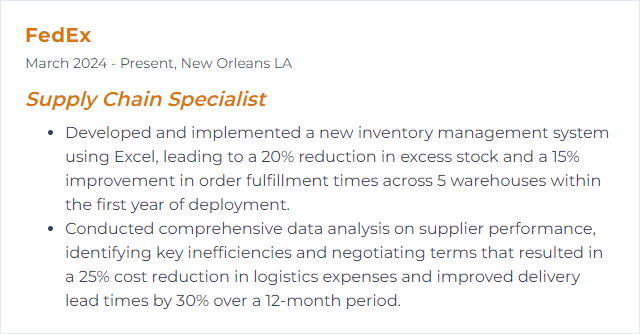
12. Blockchain Understanding
Blockchain is a secure, decentralized, and transparent digital ledger technology that records transactions across multiple computers. For a Supply Chain Specialist, it enables real-time tracking of products and transactions, enhancing transparency, security, and efficiency throughout the supply chain.
Why It's Important
Understanding blockchain is crucial for a Supply Chain Specialist as it offers a secure, transparent, and immutable ledger, enhancing traceability, reducing fraud, and improving efficiency and trust across the entire supply chain.
How to Improve Blockchain Understanding Skills
Improving your understanding of blockchain, especially as a Supply Chain Specialist, involves grasping the technology's fundamentals and its applications in supply chain management. Here's a concise guide to get started:
Start with the Basics: Understand what blockchain is - a decentralized, distributed ledger technology that records transactions across multiple computers so that the record cannot be altered retroactively.
Learn About Blockchain in Supply Chain: Dive into how blockchain can enhance transparency, traceability, and efficiency in supply chains by reading industry-specific articles and case studies. The World Economic Forum provides an insightful overview here.
Online Courses and Webinars: Enroll in online courses that specifically focus on blockchain in supply chain management. Platforms like Coursera and edX offer courses designed for professionals. For instance, the "Blockchain: Foundations and Use Cases" course on Coursera can be a good starting point.
Attend Workshops and Conferences: These can provide valuable networking opportunities and insights from industry leaders. Websites like Eventbrite and Meetup list relevant events.
Join Online Forums and Communities: Engage with blockchain and supply chain professionals through forums such as the Supply Chain subreddit or specialized LinkedIn groups. This fosters knowledge sharing and keeps you updated on the latest trends and challenges.
Practice by Doing: Experiment with blockchain technology through demo projects or simulations. Platforms like IBM Blockchain Platform allow you to create your own blockchain network and understand its workings.
Read Books and Research Papers: For a deeper dive, look for books and academic papers on the subject. "Blockchain Enabled Applications: Understand the Blockchain Ecosystem and How to Make it Work for You" by Vikram Dhillon, David Metcalf, and Max Hooper is a practical read for beginners.
Follow Thought Leaders and Influencers: On platforms like LinkedIn and Twitter, follow blockchain experts and supply chain leaders who share valuable insights and updates.
By following these steps and continuously engaging with the community, you'll enhance your understanding of how blockchain technology can revolutionize the supply chain industry.
How to Display Blockchain Understanding Skills on Your Resume
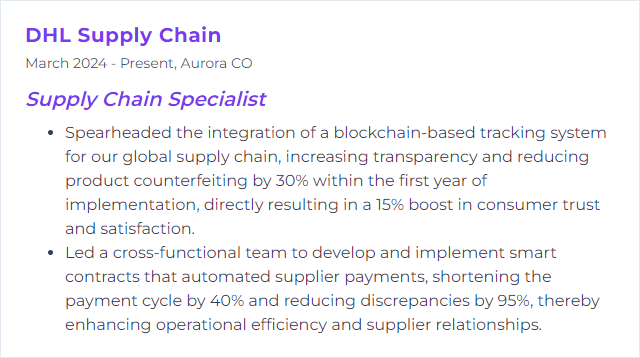