Top 12 Stress Engineer Skills to Put on Your Resume
In the dynamic field of stress engineering, showcasing the right blend of technical expertise and soft skills on your resume can significantly elevate your job prospects. This article delves into the top 12 skills that stress engineers should highlight to stand out in the competitive job market and thrive in their careers.
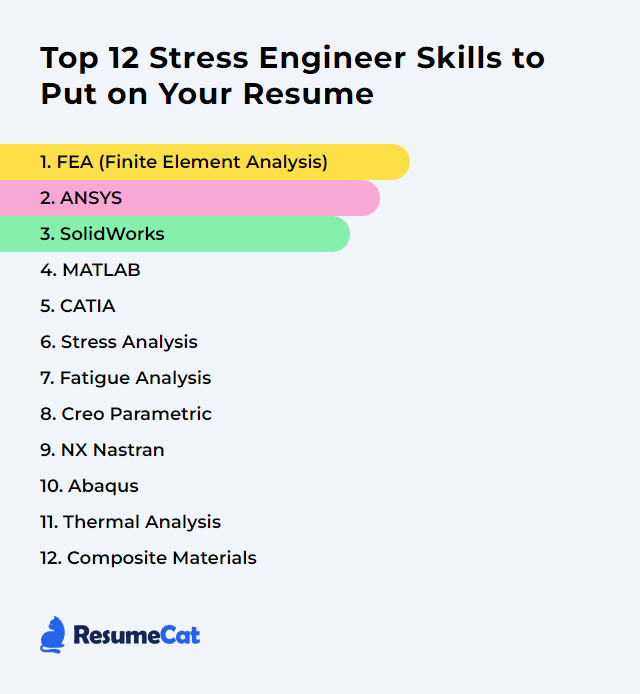
Stress Engineer Skills
- FEA (Finite Element Analysis)
- ANSYS
- SolidWorks
- MATLAB
- CATIA
- Stress Analysis
- Fatigue Analysis
- Creo Parametric
- NX Nastran
- Abaqus
- Thermal Analysis
- Composite Materials
1. FEA (Finite Element Analysis)
Finite Element Analysis (FEA) is a computational technique used by stress engineers to predict how structures respond to forces, by dividing a structure into smaller, manageable elements and analyzing their behavior under given conditions.
Why It's Important
FEA (Finite Element Analysis) is crucial for a Stress Engineer as it enables the precise prediction and analysis of structural behavior under various loads, ensuring safety, reliability, and optimization of design while reducing the need for costly physical prototypes.
How to Improve FEA (Finite Element Analysis) Skills
Improving Finite Element Analysis (FEA) as a Stress Engineer involves enhancing model accuracy, efficiency, and reliability. Here are concise strategies:
Mesh Refinement: Optimize mesh size and quality for critical areas without overly increasing computational costs. Use convergence studies to determine the appropriate mesh density. ANSYS Meshing Guide.
Material Properties: Ensure accurate material models that closely represent the physical behavior under operating conditions. Consult material databases and manufacturer data sheets for precise properties. MatWeb Material Database.
Boundary Conditions: Apply realistic boundary and loading conditions that accurately mimic the real-world scenario. Review engineering drawings and consult with design teams for accuracy. SolidWorks Simulation Setup.
Solver Selection: Choose the appropriate solver and analysis type (linear vs. nonlinear, static vs. dynamic) based on the problem specifics. NASTRAN Solver Options.
Validation and Verification: Correlate FEA results with experimental data or hand calculations to validate the model. Regularly perform verification checks against known solutions or benchmarks. Nafems Verification and Validation.
Continuous Learning: Stay updated with the latest FEA software developments, methodologies, and training to improve analysis skills. COMSOL Multiphysics Learning Resources.
Peer Review: Engage with colleagues or online communities for model reviews and feedback. Participate in forums like Eng-Tips Forums for community advice and support.
Incorporating these strategies will lead to enhanced FEA outcomes, contributing to the development of more reliable and efficient designs.
How to Display FEA (Finite Element Analysis) Skills on Your Resume
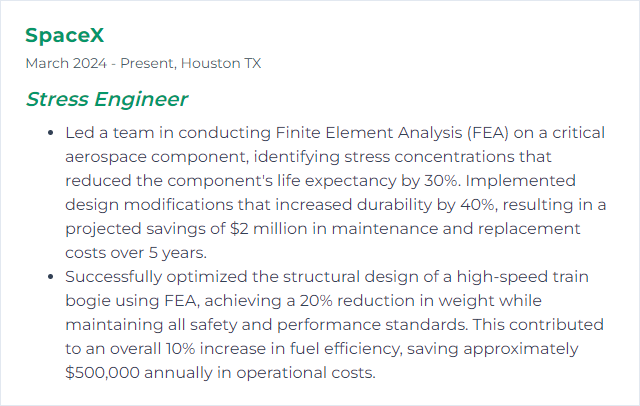
2. ANSYS
ANSYS is a comprehensive simulation software tool used by stress engineers for performing finite element analysis (FEA) to predict how product designs react to physical forces, including structural, thermal, and dynamic stress analyses, helping in optimizing design performance and reliability.
Why It's Important
ANSYS is crucial for a Stress Engineer because it provides sophisticated simulation tools for predicting and analyzing structural stresses, enabling the design and optimization of components and systems for safety, performance, and reliability.
How to Improve ANSYS Skills
Improving your skills in ANSYS as a Stress Engineer involves a combination of enhancing your foundational knowledge, practicing complex simulations, and staying updated with the latest features and techniques. Here are concise steps and resources:
Master the Basics: Ensure you have a strong grasp of ANSYS fundamentals. ANSYS provides official tutorials that cover everything from introductory lessons to advanced applications.
Specialized Learning: Focus on modules and features in ANSYS that are specific to stress analysis, such as Mechanical APDL (ANSYS Parametric Design Language) and ANSYS Workbench. Courses and webinars tailored for stress analysis can be found on platforms like Coursera or edX.
Practice Real-World Problems: Apply your skills to solve real-world engineering problems. This could mean participating in forums like the ANSYS Learning Forum or working on projects that challenge your understanding and skill.
Stay Updated: ANSYS continuously evolves, introducing new features and improvements. Regularly visit the ANSYS Blog to stay informed about the latest developments and how they can be applied to stress analysis.
Networking and Collaborations: Engage with other professionals through social platforms like LinkedIn or specialized engineering communities. Sharing insights and solutions can offer new perspectives and techniques.
By following these steps and utilizing the provided resources, you can significantly improve your proficiency in ANSYS, leading to more accurate and efficient stress analysis in your engineering projects.
How to Display ANSYS Skills on Your Resume
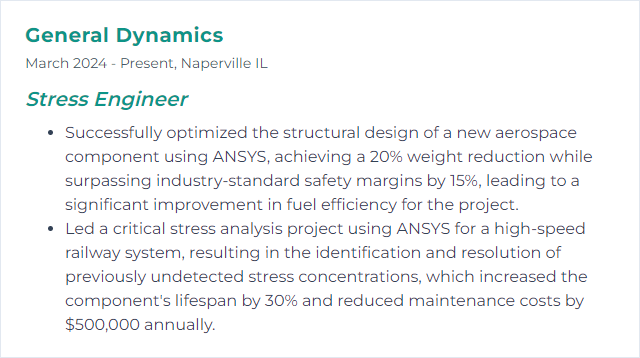
3. SolidWorks
SolidWorks is a computer-aided design (CAD) and engineering software used for creating 3D models and simulations, particularly useful for stress engineers in analyzing structural integrity, durability, and predicting performance under various load conditions.
Why It's Important
SolidWorks is important for a Stress Engineer because it provides powerful simulation tools to analyze stress, strain, and displacement in designs, enabling the optimization of materials and geometry for safety, durability, and performance efficiency.
How to Improve SolidWorks Skills
Improving your SolidWorks skills, particularly for a Stress Engineer, involves a few targeted strategies. Here are concise recommendations with relevant resources:
Master the Basics: Ensure you have a strong foundation in SolidWorks basics. SolidWorks tutorials can guide you through fundamental concepts and operations.
Specialize in Simulation: Focus on SolidWorks Simulation to understand stress analysis. Utilize Simulation tutorials to learn about setting up and interpreting stress analysis projects.
Certification: Consider obtaining a SolidWorks certification, like the Certified SolidWorks Professional (CSWP) in Simulation, to validate your skills and knowledge.
Join the Community: Engage with the SolidWorks Community, where you can ask questions, share experiences, and get advice from other stress engineers.
Stay Updated: Keep up with new features and techniques by attending SolidWorks World or webinars, which provide insights into advanced functionalities and industry trends.
Practice: Regularly challenging yourself with new projects can significantly improve your proficiency. Try to incorporate complex simulations or volunteer for diverse projects that require innovative stress analysis solutions.
By focusing on these areas, you'll be able to enhance your SolidWorks skills effectively as a Stress Engineer.
How to Display SolidWorks Skills on Your Resume
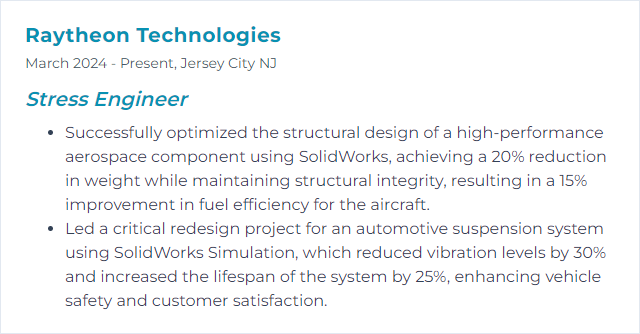
4. MATLAB
MATLAB is a high-level programming and numerical computing environment used by stress engineers for modeling, simulation, and analysis of mechanical structures under various stress conditions.
Why It's Important
MATLAB is important for a Stress Engineer because it provides powerful tools for numerical analysis, simulation, and visualization of complex engineering problems, enabling efficient design optimization and validation of structural integrity under various loading conditions.
How to Improve MATLAB Skills
To enhance MATLAB for a Stress Engineer, focus on these areas:
Master Vectorization: Replace loops with vectorized operations for faster computations. MATLAB's documentation on vectorization provides a good starting point.
Utilize Parallel Computing: For large-scale simulations, use MATLAB's Parallel Computing Toolbox to distribute tasks across multiple processors.
Optimize Code with Profiler: Use MATLAB's Profiler to identify bottlenecks and optimize your code's performance.
Implement Efficient Data Structures: Use appropriate data structures (e.g., tables, structures, cell arrays) for efficient data manipulation. The MATLAB Data Types documentation offers insights into selecting the right structure.
Stay Updated with MATLAB and Add-Ons: Regularly updating MATLAB and exploring relevant Add-Ons can introduce new functionalities beneficial for stress analysis.
Learn from the Community: Engage with MATLAB's user community for shared codes, advice, and innovative solutions to complex problems.
Customize MATLAB for Stress Analysis: Develop or incorporate custom functions and toolboxes specifically designed for stress analysis, such as those available through academic or professional societies in your field.
By focusing on these areas, you can significantly enhance MATLAB's performance and utility for stress engineering tasks.
How to Display MATLAB Skills on Your Resume
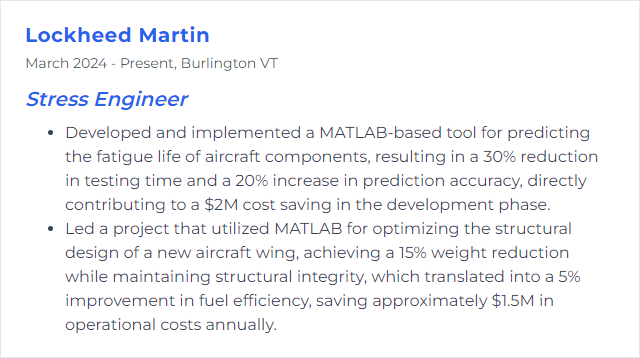
5. CATIA
CATIA (Computer-Aided Three-dimensional Interactive Application) is a powerful multi-platform CAD software suite developed by Dassault Systèmes, used for product design and innovation across various industries. For a Stress Engineer, CATIA provides advanced tools for modeling complex 3D structures and conducting finite element analysis (FEA) to simulate and evaluate structural stress, deformation, and other critical mechanical properties, supporting the optimization of product design for safety and performance.
Why It's Important
CATIA is crucial for a Stress Engineer because it offers advanced tools for 3D modeling and simulation, enabling the accurate analysis of materials, structures, and stress points to ensure product safety and integrity.
How to Improve CATIA Skills
Improving your skills in CATIA as a Stress Engineer involves focusing on key areas that enhance modeling accuracy, analysis proficiency, and design optimization. Here’s a short guide:
Master the Basics: Solidify your understanding of fundamental CATIA modules relevant to stress analysis, such as Part Design and Assembly Design.
Learn Generative Structural Analysis: Dive into the Generative Structural Analysis workbench to perform simulations and interpret results accurately. DS Learning Center offers specific courses.
Advanced Tutorials: Practice with advanced tutorials focusing on aerospace or automotive components to apply stress analysis in real-world scenarios. Websites like COE provide resources and community support.
Customize CATIA for Efficiency: Learn to customize your CATIA environment using macros and scripting to automate repetitive tasks. The CATIA User Community is a good place to exchange scripts and tips.
Stay Updated: Keep abreast of the latest features and updates in CATIA that can aid in stress analysis. Dassault Systèmes’ official website and forums are valuable resources.
Networking and Continuous Learning: Join online forums and LinkedIn groups related to CATIA and stress engineering to share insights and learn from peers.
By focusing on these areas and leveraging online resources, you can significantly enhance your CATIA proficiency as a Stress Engineer.
How to Display CATIA Skills on Your Resume
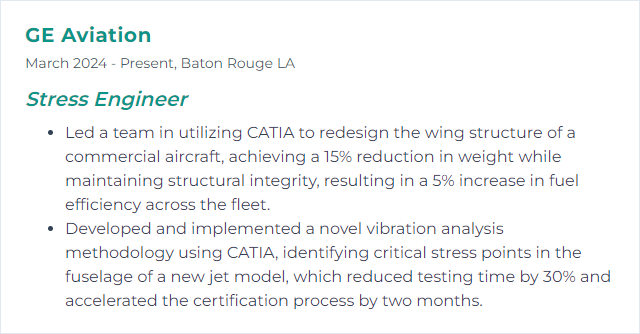
6. Stress Analysis
Stress analysis is the process of determining the internal forces, stresses, and deformations within materials or structures under applied loads, to ensure they meet safety, reliability, and performance criteria.
Why It's Important
Stress analysis is crucial for a Stress Engineer as it ensures the structural integrity and reliability of materials and components under various loads, preventing failure and enhancing safety and performance.
How to Improve Stress Analysis Skills
To improve stress analysis, a stress engineer should:
Enhance Computational Skills: Master the use of FEA (Finite Element Analysis) tools like ANSYS, Abaqus, or SolidWorks Simulation for accurate modeling and analysis.
Understand Material Behavior: Deepen knowledge on material science to predict how materials respond under stress accurately. Resources like MatWeb provide valuable material property information.
Stay Updated with Standards: Keep abreast of latest industry standards and protocols from ASTM International or ISO to ensure compliance and reliability in your analyses.
Continuous Learning: Engage in continuous education through courses and certifications from platforms like Coursera and edX, focusing on mechanical engineering and material science.
Leverage Peer Review: Actively seek peer reviews for your analyses to uncover overlooked issues and gain new perspectives. Participate in forums like Eng-Tips to exchange knowledge.
Practical Experience: Supplement theoretical knowledge with hands-on experience through internships, project work, or collaboration with experienced engineers.
By focusing on these areas, a stress engineer can significantly enhance the accuracy and reliability of their stress analyses.
How to Display Stress Analysis Skills on Your Resume
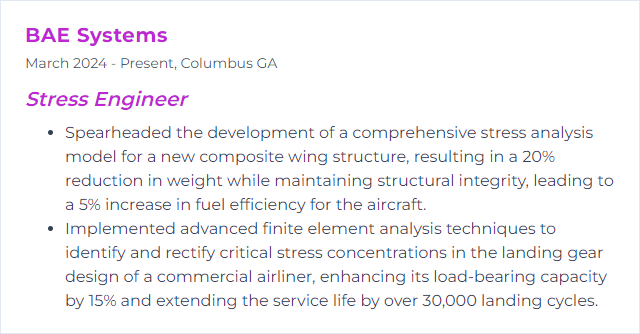
7. Fatigue Analysis
Fatigue analysis is the process used by stress engineers to evaluate and predict the life of materials or structures under cyclic loading, identifying when and where fatigue damage or failure might occur due to repeated stress variations over time.
Why It's Important
Fatigue analysis is crucial for a Stress Engineer as it helps predict and prevent failure in materials and structures due to repeated loading, ensuring safety and reliability over their service life.
How to Improve Fatigue Analysis Skills
Improving fatigue analysis involves enhancing the accuracy and reliability of predicting how long a material or structural component can withstand cyclic loading before failure. As a Stress Engineer, consider the following concise steps:
Material Characterization: Understand the material properties thoroughly. Use accurate S-N curves (Fatigue Life) for different materials to model fatigue life more precisely.
Load Analysis: Accurately quantify the loading conditions (Loading Analysis) the component will experience, including magnitude, direction, and frequency of cyclic loads.
Finite Element Analysis (FEA): Use advanced FEA software to simulate the stress distribution and identify critical stress locations. Tools like ANSYS (ANSYS Fatigue Analysis) offer robust modules for fatigue analysis.
Fatigue Life Prediction Models: Apply appropriate fatigue life prediction models (e.g., Palmgren-Miner rule) that match your scenario. Stay updated with the latest models and methodologies by consulting resources like the International Journal of Fatigue.
Factor of Safety (FoS): Implement a conservative FoS based on industry standards and the criticality of the component. This accounts for uncertainties in material properties, load estimations, and model assumptions.
Testing and Validation: Validate your analysis with physical fatigue testing (ASTM Fatigue Testing Standards). This step is crucial for correlating your predictions with real-world behavior.
Incorporate Manufacturing Effects: Consider the effects of manufacturing processes (e.g., welding, casting) on fatigue life. Surface finish, residual stresses, and heat treatment can significantly influence fatigue resistance.
Continuous Learning and Improvement: Stay informed about advances in fatigue analysis methods and technologies. Participating in forums like Eng-Tips can provide insights into practical challenges and solutions.
By focusing on these areas, you can refine your approach to fatigue analysis, leading to more reliable and accurate predictions of component life under cyclic loading conditions.
How to Display Fatigue Analysis Skills on Your Resume
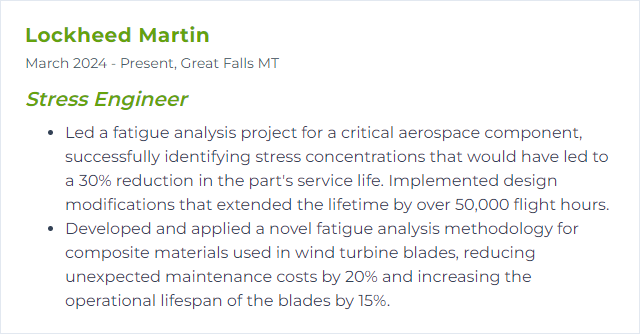
8. Creo Parametric
Creo Parametric is a powerful 3D CAD software tool that allows stress engineers to create, analyze, and optimize complex geometries and assemblies for structural integrity, durability, and performance under various loading conditions.
Why It's Important
Creo Parametric is crucial for a Stress Engineer as it provides advanced tools for creating precise 3D models, enabling detailed stress analysis, simulation, and optimization of designs for structural integrity and performance under various load conditions.
How to Improve Creo Parametric Skills
Improving your skills in Creo Parametric as a Stress Engineer involves focusing on aspects that enhance your ability to model, analyze, and optimize designs for structural integrity. Follow these concise steps:
Master the Basics: Ensure you are comfortable with the fundamental tools and features of Creo Parametric. PTC's Creo Parametric Help Center is an excellent starting point.
Understand Simulation Features: Dive into the simulation capabilities of Creo Parametric to perform stress analysis. The Simulation section on the official PTC website provides insights into available tools for structural, thermal, and modal analysis.
Learn Advanced Modeling Techniques: Advanced modeling techniques can help create more accurate and complex geometry for analysis. Utilize the Advanced Modeling tutorials provided by PTC to improve your modeling skills.
Optimize Designs: Familiarize yourself with the optimization tools within Creo Parametric to iteratively improve designs based on stress analysis results. Refer to the Design Optimization section for guidance.
Stay Updated: Creo Parametric is constantly evolving, so staying updated with the latest versions and features is crucial. The What’s New page helps keep you informed about the latest developments.
Join the Community: Engage with the Creo community through forums and discussions. The PTC Community is a valuable resource for tips, tricks, and advice from fellow engineers.
Seek Professional Training: Consider enrolling in official Creo Parametric training courses tailored for stress engineers. PTC’s Training Courses offer comprehensive learning paths from basic to advanced levels.
Focusing on these steps will help you leverage Creo Parametric's full potential in your role as a Stress Engineer, leading to more efficient and effective design and analysis processes.
How to Display Creo Parametric Skills on Your Resume
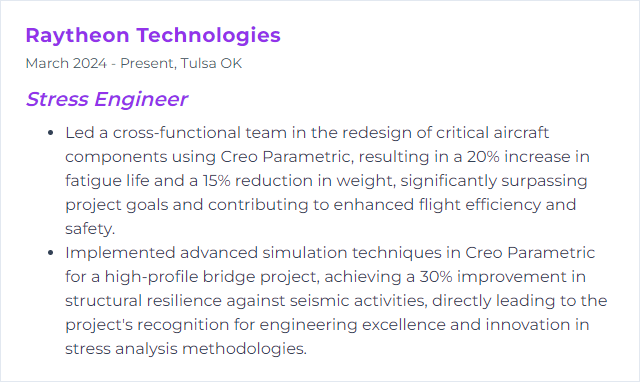
9. NX Nastran
NX Nastran is a finite element analysis (FEA) software used by stress engineers to simulate and analyze mechanical stress, vibration, structural failure, and heat transfer within components and assemblies to ensure product performance and reliability.
Why It's Important
NX Nastran is important for a Stress Engineer because it provides advanced simulation capabilities for structural analysis, enabling accurate prediction of component behavior under various loading conditions, thus aiding in the design of safer and more efficient structures.
How to Improve NX Nastran Skills
To improve your use of NX Nastran as a Stress Engineer, focus on the following concise strategies:
Enhance Modeling Skills: Enhance your understanding of finite element modeling practices. Siemens provides NX Nastran documentation that can help refine your approach.
Master the Software Tools: Utilize NX Nastran's advanced features such as solution sequences (SOLs). Siemens NX Nastran resources can guide you through advanced functionalities.
Optimization Techniques: Learn optimization techniques within NX Nastran to improve design efficiency. Refer to Siemens optimization solutions for strategies and tips.
Stay Updated: Regularly update your software to leverage improvements and new features. Keep an eye on Siemens' official updates page for the latest releases.
Participate in Forums: Engage with the NX Nastran community through forums like Siemens Community to exchange knowledge and tips.
Continuous Learning: Enroll in specialized courses or webinars offered by Siemens or third-party providers to stay abreast of the latest techniques and software capabilities. Check out Siemens Learning for available courses.
By focusing on these areas, you can significantly enhance your proficiency and effectiveness in using NX Nastran for stress analysis tasks.
How to Display NX Nastran Skills on Your Resume
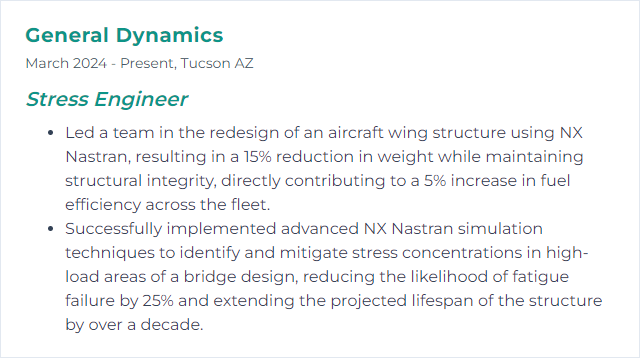
10. Abaqus
Abaqus is a comprehensive finite element analysis (FEA) software used by stress engineers for simulating the behavior of structures under various physical loads, predicting how they will react to stress, strain, and deformation.
Why It's Important
Abaqus is crucial for a Stress Engineer because it enables highly accurate simulations of complex material behaviors and structural responses under various loading conditions, facilitating the design and optimization of products for durability, safety, and performance.
How to Improve Abaqus Skills
Improving your skills in Abaqus as a Stress Engineer involves a combination of enhancing your understanding of the software's capabilities, applying best practices in simulation, and staying updated with the latest features and techniques. Here’s a concise guide:
Understand the Fundamentals: Start with mastering the basics of Abaqus. Grasp the theoretical concepts behind finite element analysis (FEA) to effectively apply them in Abaqus. SIMULIA Learning Community offers resources and courses to build a strong foundation.
Specialize in Advanced Features: Dive deep into advanced modules relevant to stress engineering, such as nonlinear analysis, dynamic simulations, and composite materials. The Abaqus Documentation is an excellent resource for understanding specific functionalities.
Utilize Python Scripting: Automate tasks and customize analyses with Python scripting within Abaqus. Enhance efficiency and accuracy of your simulations. Abaqus Scripting User's Guide provides insights into scripting capabilities.
Engage with the Community: Join forums and discussion groups like the Abaqus Users Group on LinkedIn to exchange knowledge, solve problems, and stay informed about the latest trends and solutions.
Practice and Experiment: Apply your skills on various projects to gain practical experience. Experiment with different approaches to understand their impact on results.
Stay Updated: Abaqus regularly updates its features and capabilities. Stay informed about updates and new techniques by subscribing to SIMULIA's Blog and attending webinars or conferences.
By focusing on these areas, you can significantly improve your proficiency in Abaqus and enhance your capabilities as a Stress Engineer.
How to Display Abaqus Skills on Your Resume
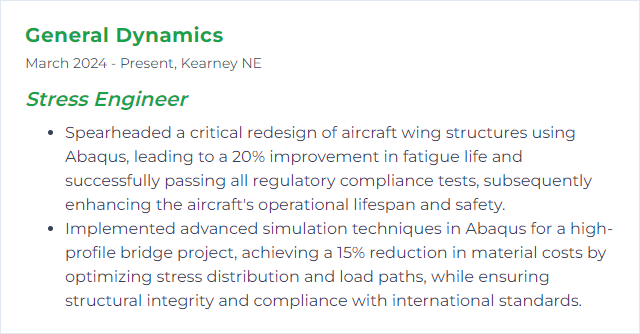
11. Thermal Analysis
Thermal analysis, in the context of a Stress Engineer, is the study of a material's response to changes in temperature, focusing on the thermal-induced stresses and deformations that occur due to thermal expansion or contraction. This analysis helps in predicting and mitigating potential failures in structures or components exposed to varying thermal conditions.
Why It's Important
Thermal analysis is crucial for a Stress Engineer as it helps predict and assess how temperature variations affect materials and structures, ensuring their integrity, reliability, and performance under varying thermal conditions.
How to Improve Thermal Analysis Skills
To improve thermal analysis as a Stress Engineer, focus on the following concise strategies:
Enhance Material Data Accuracy: Ensure the thermal properties of materials (conductivity, specific heat, etc.) used in simulations are precise. Consult MatWeb for comprehensive material properties.
Use High-Quality Mesh: A finer mesh in areas of high thermal gradients improves accuracy. Tools like ANSYS Meshing offer advanced meshing capabilities.
Implement Advanced Software: Utilize advanced CAE tools that offer robust thermal analysis capabilities, such as ABAQUS or ANSYS Mechanical, for more accurate simulations.
Apply Realistic Boundary Conditions: Ensure that the thermal loads and boundary conditions closely mimic actual operating conditions. Engineering Toolbox can be a resource for real-world engineering parameters.
Conduct Sensitivity Analysis: Determine which parameters most affect your model by varying material properties, boundary conditions, and environmental conditions. This can highlight areas needing more accurate data or refined modeling.
Validate with Experimental Data: Whenever possible, validate your thermal models against experimental or real-world data to ensure accuracy. This can also help in refining the assumptions made during the modeling process.
Continuous Learning: Stay updated with the latest techniques and tools in thermal analysis through courses and certifications from platforms like Coursera and edX.
By focusing on these areas, you can significantly improve the accuracy and reliability of your thermal analyses.
How to Display Thermal Analysis Skills on Your Resume
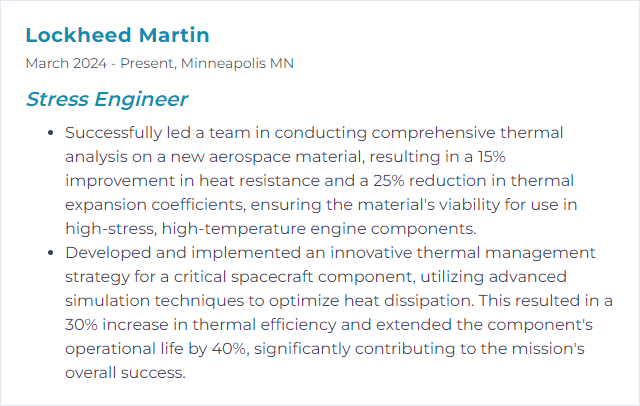
12. Composite Materials
Composite materials are engineered materials made from two or more constituent materials with significantly different physical or chemical properties that, when combined, produce a material with characteristics different from the individual components. For a Stress Engineer, these materials are crucial for designing structures that require a high strength-to-weight ratio, enhanced durability, and resistance to environmental factors, allowing for innovative solutions in load-bearing applications.
Why It's Important
Composite materials are crucial for a Stress Engineer because they offer superior strength-to-weight ratios and customizable properties, enabling the design of structures that are lighter, stronger, and more resistant to environmental and operational stresses.
How to Improve Composite Materials Skills
Improving composite materials, especially from a stress engineer's perspective, involves enhancing their mechanical properties and durability under various loading conditions. Here are concise strategies:
Fiber Reinforcement Optimization: Selecting the right type of fibers (e.g., carbon, glass, aramid) and their orientations can significantly increase strength and stiffness. Learn more.
Matrix Material Enhancement: Developing or choosing advanced resin systems that have improved mechanical properties and environmental resistance can enhance the composite's overall performance. Explore advancements.
Hybridization: Combining different types of fibers within a single matrix can offer a balance of properties, such as high strength and impact resistance. Read about hybrid composites.
Nano-Engineering: Incorporating nanoparticles into the composite matrix can improve properties like fracture toughness and thermal stability. Nano-enhancements in composites.
Manufacturing Process Optimization: Techniques such as vacuum bagging, resin transfer molding, and autoclave curing can reduce voids and defects, increasing the composite's strength and reliability. Manufacturing processes overview.
Damage Tolerance Design: Designing composites to tolerate certain amounts of damage without catastrophic failure enhances safety and longevity. This involves understanding failure mechanisms and stress concentrations. Damage tolerance in composites.
Environmental Conditioning and Testing: Simulating real-world environmental conditions (moisture, UV, temperature cycles) during testing ensures that the composite materials can withstand operational stresses and environmental degradation. Environmental effects on composites.
By focusing on these areas, stress engineers can significantly contribute to the development of composite materials that meet the demanding requirements of various applications.
How to Display Composite Materials Skills on Your Resume
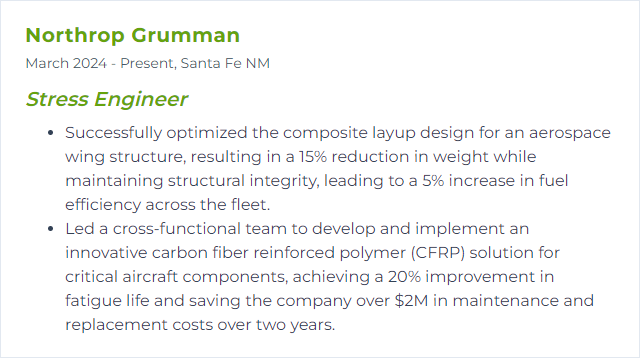