Top 12 Stocker Skills to Put on Your Resume
In today’s competitive job market, having a well-crafted resume is crucial for stockers aiming to stand out among numerous applicants. Highlighting the top skills on your resume not only showcases your proficiency and experience but also demonstrates to potential employers your ability to efficiently manage and contribute to their inventory needs.
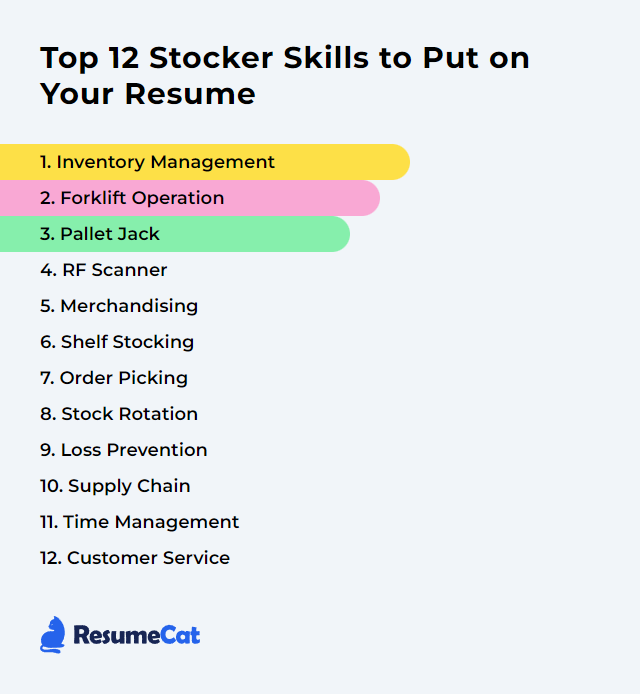
Stocker Skills
- Inventory Management
- Forklift Operation
- Pallet Jack
- RF Scanner
- Merchandising
- Shelf Stocking
- Order Picking
- Stock Rotation
- Loss Prevention
- Supply Chain
- Time Management
- Customer Service
1. Inventory Management
Inventory management is the process of ordering, storing, using, and selling a company's inventory, including the management of raw materials, components, and finished products. For a stocker, it involves tasks like stocking shelves, organizing products, ensuring the accurate tracking of inventory levels, and maintaining the right amount of stock to meet customer demand without overstocking.
Why It's Important
Inventory management is crucial for a stocker as it ensures the right products are available at the right time, reduces the risk of overstocking or stockouts, maximizes storage space efficiency, and helps maintain accurate stock levels for optimal business operations.
How to Improve Inventory Management Skills
Improving inventory management involves streamlining processes, enhancing accuracy, and optimizing stock levels to meet demand without overstocking. For a stocker, focus on:
Implementing Inventory Management Software: Adopt tools (Shopify) that offer real-time tracking, forecasting, and analytics for better decision-making.
Regular Stock Audits: Conduct frequent physical counts to ensure system data matches actual stock (Square).
FIFO Method: Use the First-In, First-Out approach, particularly for perishable goods, to minimize waste and obsolescence (TradeGecko).
Just-In-Time (JIT) Inventory: Minimize holding costs by receiving goods only as they are needed (Kanbanize).
Supplier Management: Build strong relationships with suppliers for reliable lead times and flexible order quantities (Supply Chain Dive).
Streamline Receiving and Sorting Processes: Ensure efficient systems are in place for when new inventory arrives to avoid backlogs and errors (Camcode).
Continuous Improvement: Regularly review and adjust inventory practices based on analytics and performance metrics (Deloitte).
By focusing on these areas, a stocker can significantly contribute to the efficiency and effectiveness of inventory management.
How to Display Inventory Management Skills on Your Resume
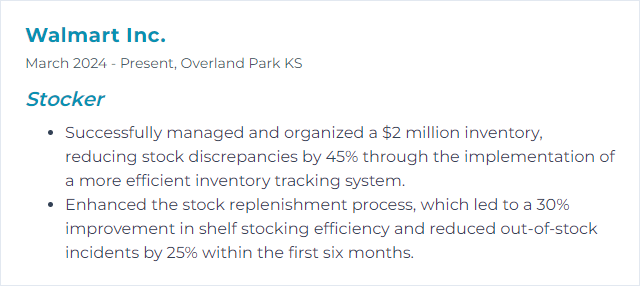
2. Forklift Operation
Forklift operation involves maneuvering a powered industrial truck to lift, transport, and stack materials, aiding in the efficient handling and storage of goods within warehouses or storage facilities. For a Stocker, it facilitates the stocking and retrieval of products at various heights and locations, ensuring organized and safe storage of inventory.
Why It's Important
Forklift operation is important for a stocker because it enables efficient handling and transportation of heavy or bulky goods within warehouses, minimizing physical strain and enhancing productivity and safety in stock management.
How to Improve Forklift Operation Skills
Improving forklift operation, particularly for a stocker, involves focusing on safety, efficiency, and continuous learning. Here's a concise guide:
Safety First: Prioritize safety by adhering to OSHA's Forklift Safety Guidelines. This includes wearing proper safety gear, performing pre-operation checks, and understanding the forklift's load capacity.
Efficiency: Optimize storage layout and forklift paths to minimize travel time and increase productivity. Implementing a lean inventory system can also enhance efficiency. The Toyota Production System offers insights into lean practices.
Continuous Learning: Engage in ongoing training and certification to stay updated on best practices and new technologies. Resources like Material Handling Education Foundation Inc. provide valuable learning opportunities.
Maintenance: Regular maintenance ensures forklifts operate smoothly and safely. Follow the manufacturer’s guidelines and schedule routine checks.
Use Technology: Adopt warehouse management systems (WMS) and forklift-mounted devices to streamline operations. Information on WMS can be found through SelectHub's guide.
By focusing on these areas, a stocker can significantly improve forklift operation, contributing to a safer and more efficient workplace.
How to Display Forklift Operation Skills on Your Resume
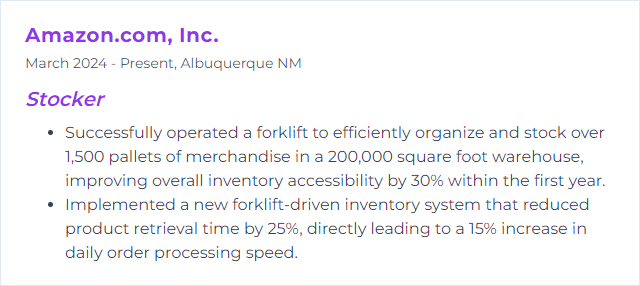
3. Pallet Jack
A pallet jack, in the context of a stocker's work, is a manual or powered tool used to lift and move pallets of goods within a warehouse or retail environment, facilitating the handling of stock.
Why It's Important
A pallet jack is crucial for a stocker because it allows for the efficient and safe moving of heavy or bulky merchandise, enhancing productivity and reducing the risk of injury during the stocking process.
How to Improve Pallet Jack Skills
To improve a pallet jack for stockers, focus on:
- Ergonomics: Enhance handle design for better grip and less strain. Ergonomic Guidelines
- Wheels: Upgrade to high-quality, non-marking wheels for smoother movement and durability. Wheel Types
- Load Capacity: Ensure it meets or exceeds your typical load requirements. Understanding Load Capacity
- Width Adjustment: Implement adjustable fork width for versatility with different pallet sizes. Pallet Jack Selection
- Maintenance: Regular maintenance schedule to keep it in optimal condition. Maintenance Tips
These enhancements aim for improved usability, safety, and efficiency in a stocking environment.
How to Display Pallet Jack Skills on Your Resume
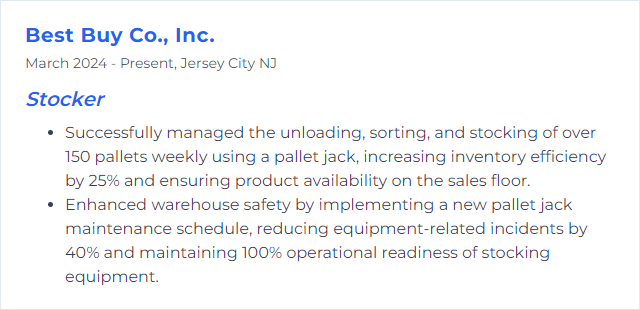
4. RF Scanner
An RF (Radio Frequency) Scanner is a handheld device used by stockers in warehouses and retail environments to track inventory by scanning barcodes, ensuring accurate stock levels and locations.
Why It's Important
RF scanners are essential for stockers because they enable quick and accurate tracking, management, and replenishment of inventory, ensuring that products are correctly stocked and available for customers.
How to Improve RF Scanner Skills
Improving an RF (Radio Frequency) Scanner for a stocker involves enhancing both the hardware and software capabilities to streamline inventory management and increase efficiency. Here are concise steps to achieve that:
Software Update: Ensure the RF scanner's software is updated to the latest version for improved functionality and bug fixes. Manufacturers often release updates that can be downloaded from their official website.
Ergonomic Design: Use RF scanners with an ergonomic design to reduce fatigue and increase productivity. Consider options with comfortable grips and lightweight materials. Ergonomic scanners are available from various manufacturers.
Battery Life: Opt for scanners with extended battery life or have a set of fully charged spare batteries to minimize downtime. Information on battery life can be found in the product specifications.
Training: Ensure stockers receive comprehensive training on the optimal use of RF scanners, including shortcuts and scanning techniques. Many manufacturers provide training resources or manuals on their websites.
Wi-Fi Connectivity: Improve the Wi-Fi infrastructure in the warehouse to ensure a stable and strong connection for RF scanners, enhancing real-time inventory tracking. Cisco offers solutions for industrial wireless networking.
Barcode Quality: Use high-quality, easily scannable barcodes to reduce scanning errors. Tips on creating better barcodes can be found in guidelines provided by GS1.
Improving RF scanners involves a combination of choosing the right equipment, ensuring up-to-date software, providing staff training, and maintaining a supportive infrastructure.
How to Display RF Scanner Skills on Your Resume
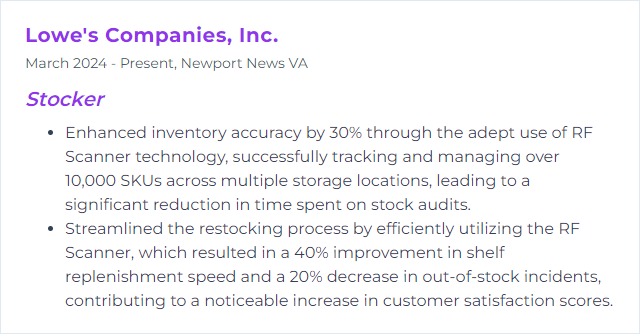
5. Merchandising
Merchandising, in the context of a stocker, involves the stocking, organizing, and displaying of products in a retail environment to attract customers and encourage sales.
Why It's Important
Merchandising is crucial for a Stocker as it directly impacts sales through the effective display of products, ensuring visibility, accessibility, and attractiveness to customers, thus influencing their buying decisions and enhancing the overall shopping experience.
How to Improve Merchandising Skills
Improving merchandising, especially from the perspective of a stocker, involves enhancing product visibility, accessibility, and appeal to boost sales and customer satisfaction. Here’s a concise guide:
Product Placement: Position high-demand and impulse items at eye level or along the main aisles. This strategy makes products more noticeable and accessible. Visual Merchandising Techniques.
Restock Regularly: Ensure shelves are consistently stocked to meet customer expectations and drive sales. This also involves rotating stock to keep the display fresh and appealing. Effective Stock Rotation.
Cleanliness and Organization: Maintain a clean, organized, and clutter-free environment. This improves the shopping experience and makes products more attractive. Importance of Store Cleanliness.
Signage and Pricing: Clearly marked prices and informational signage help customers make informed decisions quickly, enhancing their shopping experience. Effective Retail Signage.
Seasonal and Thematic Displays: Create displays that align with seasons, holidays, or events to capture customer interest and encourage purchases. Creating Effective Displays.
Feedback and Adaptation: Listen to customer feedback and monitor sales data to understand what works and what doesn’t, allowing for quick adaptation and improvement. Adapting to Customer Feedback.
Each of these strategies, when implemented thoughtfully, can significantly enhance the effectiveness of merchandising efforts from a stocker's perspective.
How to Display Merchandising Skills on Your Resume
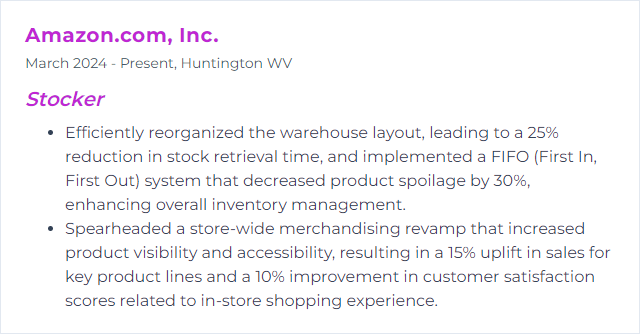
6. Shelf Stocking
Shelf stocking involves the process of organizing and replenishing merchandise on the shelves in a retail environment to ensure products are available and presented appealingly for customers. It typically involves unloading deliveries, sorting items, and placing products in their designated location according to store layout and display standards.
Why It's Important
Shelf stocking is crucial for ensuring products are available, visible, and accessible to customers, directly influencing sales and customer satisfaction. It also helps maintain store organization and appearance.
How to Improve Shelf Stocking Skills
Improving shelf stocking efficiency involves several straightforward strategies:
Organize Products Beforehand: Pre-sort items in the stockroom to match the shelf layout. This minimizes the time spent looking for products on the floor.
Use a Planogram: Follow a planogram, a visual diagram that details where every product goes on the shelf. This ensures consistent and organized product placement.
Implement FIFO Method: Practice the First-In, First-Out (FIFO) method to keep inventory fresh, especially for perishable goods.
Equip Properly: Use the right tools and equipment, like stock carts and handheld scanners, to speed up the stocking process. Ensure everything is in good working order.
Train Staff: Provide training on efficient stocking techniques and the use of equipment. Regularly update them on any layout or process changes.
Maintain Cleanliness: Keep aisles and shelves clean to make stocking easier and prevent damage to products and equipment.
Monitor Stock Levels: Use an inventory management system to keep track of stock levels in real-time, helping to prioritize restocking efforts.
Gather Feedback: Regularly ask for feedback from both staff and customers to identify areas for improvement.
By integrating these strategies, stockers can significantly improve shelf stocking efficiency, leading to better inventory management and customer satisfaction.
How to Display Shelf Stocking Skills on Your Resume
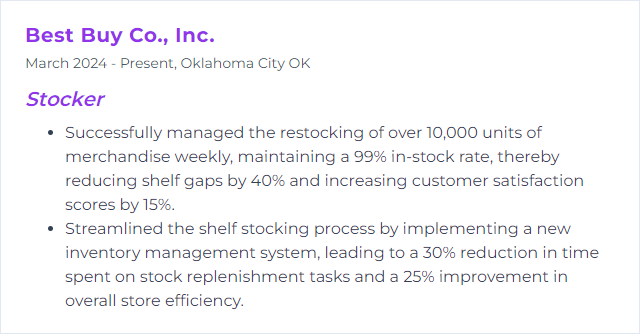
7. Order Picking
Order picking is the process of retrieving and assembling items from a warehouse or storage location to fulfill customer orders, as performed by a stocker.
Why It's Important
Order picking is crucial because it directly impacts customer satisfaction by ensuring the accurate and timely delivery of products, thereby enhancing efficiency and reducing errors in the distribution process. For a stocker, it is essential for maintaining inventory accuracy and optimizing stock levels.
How to Improve Order Picking Skills
To improve order picking, a stocker can focus on:
Optimization of Layout: Arrange the warehouse layout to minimize travel time between picks. Place high-demand items closer to packing areas. Warehouse Layout Optimization
Batch Picking: Group similar orders to reduce the number of trips. Batch Picking Benefits
Use of Technology: Implement barcode scanners or RFID tags for faster item identification and reduced errors. RFID in Warehouse Management
Employee Training: Continuously train employees on the best practices and use of technology in order picking. Impact of Training on Employee Performance
Pick-to-Light Systems: Utilize pick-to-light technology for faster picking and reducing errors. Pick-to-Light Systems
Regular Audits and Feedback: Conduct regular performance audits and provide feedback for improvement. Performance Feedback for Warehouse Operations
By strategically combining these approaches, a stocker can significantly enhance the efficiency and accuracy of order picking processes.
How to Display Order Picking Skills on Your Resume
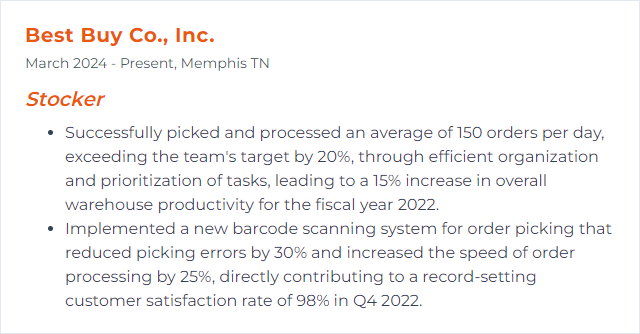
8. Stock Rotation
Stock rotation is the process of organizing inventory so that older items are sold or used before newer ones, minimizing waste and ensuring products are sold within their shelf life.
Why It's Important
Stock rotation is important to ensure that older inventory is sold before it expires or becomes outdated, minimizing losses and ensuring customers receive fresh or up-to-date products, thus maintaining inventory quality and customer satisfaction.
How to Improve Stock Rotation Skills
To improve stock rotation, follow these concise steps:
First In, First Out (FIFO): Always move the oldest stock to the front, ensuring it gets used or sold first. Learn more about FIFO.
Regularly Review Inventory: Schedule regular checks to identify and prioritize items nearing their expiry or end-of-season. Effective Inventory Reviews.
Use a Stock Rotation System: Implement or utilize an existing stock rotation system or software to automate and keep track of stock movement. Stock Management Systems.
Train Your Team: Ensure all team members understand the importance of stock rotation and how to do it correctly. Training for Retail Employees.
Label Clearly: Make sure all items are labeled with dates or batch numbers for easy identification. Labeling Best Practices.
Implement Quality Control: Regularly inspect stock for damage or spoilage to maintain quality. Quality Control Tips.
By following these steps, you can ensure a more efficient and effective stock rotation process.
How to Display Stock Rotation Skills on Your Resume
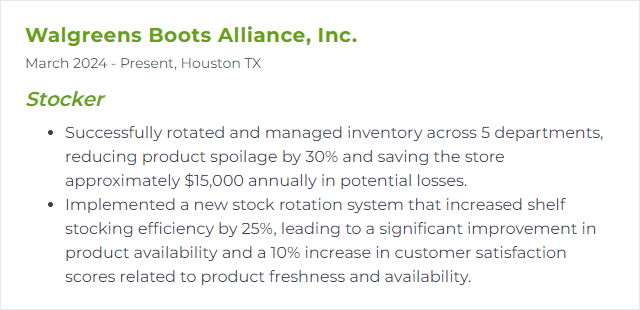
9. Loss Prevention
Loss Prevention, in the context of a Stocker, involves measures and practices aimed at reducing theft, damage, or waste of merchandise in a retail environment to protect the store's profits and inventory integrity.
Why It's Important
Loss Prevention is crucial for a Stocker as it ensures the safeguarding of inventory from theft, damage, or any form of loss, directly impacting store profitability and job security.
How to Improve Loss Prevention Skills
To improve Loss Prevention as a Stocker, focus on the following strategies:
Stay Aware: Always be vigilant and aware of your surroundings. Spotting unusual behavior early can prevent theft. National Retail Federation
Follow Procedures: Adhere strictly to your company's loss prevention policies and procedures. Properly executing these can deter theft. Loss Prevention Foundation
Secure Merchandise: Ensure high-theft items are secured or locked up, making them less accessible to potential thieves. Retail Council of Canada
Report Suspicious Activity: Immediately report any suspicious behavior or activity to your supervisor or loss prevention team. ASIS International
Keep Areas Organized: A well-organized stockroom and sales floor make it harder for theft to occur unnoticed. Professional Retail Store Maintenance Association
Regular Training: Participate in regular loss prevention training sessions to stay updated on the latest strategies and technologies. Loss Prevention Magazine
By implementing these strategies consistently, you can significantly contribute to minimizing loss within your retail environment.
How to Display Loss Prevention Skills on Your Resume
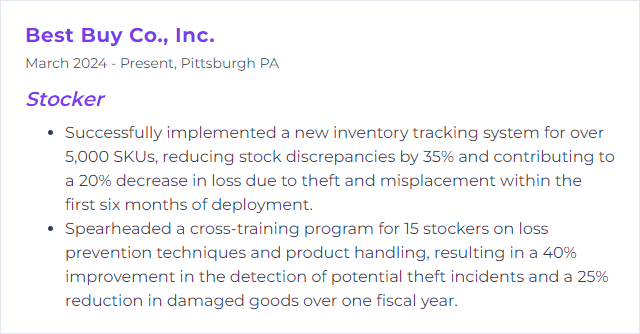
10. Supply Chain
A supply chain is the network of all the individuals, organizations, resources, activities, and technology involved in the creation and sale of a product, from the delivery of source materials from the supplier to the manufacturer, and eventually to the end user. For a stocker, it encompasses the processes that ensure products are delivered from suppliers to the store, then organized and made available for purchase by customers.
Why It's Important
Supply chain is crucial for a Stocker because it ensures the timely and efficient delivery of products to the store, enabling the stocker to maintain inventory levels, meet customer demand, and contribute to the store’s profitability.
How to Improve Supply Chain Skills
Improving a supply chain, especially from the perspective of a stocker, involves strategies aimed at enhancing efficiency, reducing costs, and ensuring timely product availability. Here are key steps:
Optimize Inventory Management: Implement just-in-time (JIT) inventory systems to reduce overstocking costs and minimize shortages. Inventory Optimization Techniques.
Enhance Supplier Relationships: Build strong relationships with suppliers for better negotiation on prices and improved reliability. Supplier Relationship Management.
Leverage Technology: Use advanced supply chain management software for real-time tracking and efficient stock management. Supply Chain Management Software.
Implement Lean Principles: Focus on eliminating waste within the supply chain, improving processes, and reducing costs. Lean Supply Chain Basics.
Continuous Training: Regularly train staff on new technologies and best practices to improve efficiency and adaptability. Importance of Training.
By focusing on these areas, a stocker can contribute significantly to the improvement of the supply chain, promoting a more efficient, cost-effective, and responsive operation.
How to Display Supply Chain Skills on Your Resume
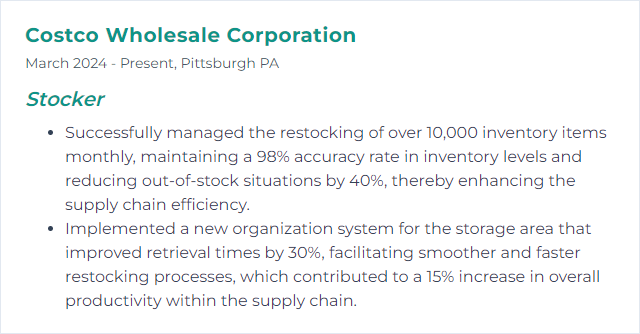
11. Time Management
Time management for a stocker involves efficiently organizing and prioritizing tasks to ensure that inventory is replenished, organized, and maintained within the set deadlines, optimizing productivity and ensuring smooth operations on the sales floor.
Why It's Important
Time management is crucial for a Stocker because it ensures efficient organization and replenishment of inventory, maximizes productivity, minimizes downtime, and improves the ability to meet deadlines and customer demands.
How to Improve Time Management Skills
Improving time management, especially for a stocker, involves prioritizing tasks, setting realistic goals, and minimizing distractions. Here's a concise guide:
Prioritize Tasks: Identify high-priority tasks and tackle them first. Use the Eisenhower Box technique to categorize tasks based on their urgency and importance.
Set Realistic Goals: Break down your workday into achievable goals. Use the SMART criteria to set specific, measurable, achievable, relevant, and time-bound goals.
Minimize Distractions: Keep your workspace organized and limit interruptions. The Pomodoro Technique can help manage breaks and maintain focus.
Use Tools and Apps: Leverage technology to stay organized and track your time effectively. Tools like Trello for task management and RescueTime for tracking how you spend your time can be very helpful.
Review and Adjust: Regularly review your performance and adjust your strategies as needed. Continuous improvement is key.
Implementing these strategies can help you manage your time more efficiently, leading to higher productivity and reduced stress.
How to Display Time Management Skills on Your Resume
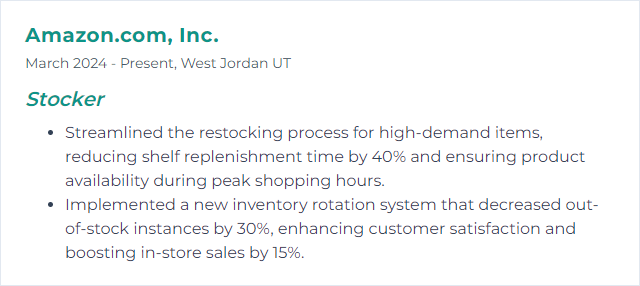
12. Customer Service
Customer service, in the context of a Stocker, involves assisting shoppers by answering questions, helping locate items, and ensuring a pleasant and efficient shopping experience.
Why It's Important
Customer service is important for a stocker because it enhances the shopping experience, ensuring customers can easily find and access products, leading to increased satisfaction and loyalty.
How to Improve Customer Service Skills
Improving customer service, especially for a Stocker, involves a few key strategies aimed at enhancing the overall shopping experience. Here are concise tips:
Product Knowledge: Ensure you're well-versed in the products you stock. This enables you to provide accurate and helpful information to customers. Learn more about product knowledge.
Proactivity: Anticipate customer needs by paying attention to their behavior and the store's busy times. Offer help before they have to ask. Read about proactive customer service.
Efficiency and Organization: Keep shelves well-stocked and organized. An orderly store makes for a better shopping experience. Discover tips on efficient stocking.
Friendliness: A smile and a greeting can go a long way in making customers feel welcome. Understand the impact of friendliness.
Feedback: Be open to customer feedback and willing to act on it to improve the shopping experience. Learn about utilizing customer feedback.
By focusing on these areas, a Stocker can significantly contribute to a positive customer service experience.
How to Display Customer Service Skills on Your Resume
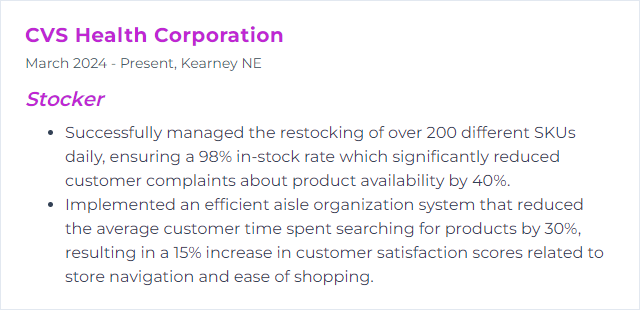