Top 12 Screen Printer Skills to Put on Your Resume
In today’s competitive job market, showcasing the right set of skills on your resume can significantly enhance your prospects as a screen printer. This article outlines the top 12 skills you need to highlight, ensuring you stand out to potential employers by demonstrating both technical prowess and creative acumen in the screen printing industry.

Screen Printer Skills
- Photoshop
- Illustrator
- Color Matching
- Prepress Operations
- Screen Making
- Ink Mixing
- Squeegee Technique
- Registration Accuracy
- Quality Control
- DTG Printing
- Sublimation Printing
- Plastisol Inks
1. Photoshop
Photoshop is a digital imaging software used for editing and manipulating images, creating detailed graphics, and preparing photos for high-quality screen printing output.
Why It's Important
Photoshop is crucial for a screen printer because it allows for precise editing and manipulation of images and graphics, ensuring high-quality, accurate color separations, and detailed control over the final print output.
How to Improve Photoshop Skills
To enhance Photoshop for screen printing, focus on mastering color separation, using high-resolution images, and employing custom brushes and textures for more precise and creative designs. Here are concise strategies:
Color Separation Mastery: Learn advanced color separation techniques for screen printing to ensure accurate and vibrant prints. Adobe's guide on color separations is a valuable resource.
High-Resolution Images: Always work with high-resolution images to prevent quality loss during the screen printing process. This tutorial from Adobe can help improve your understanding of image resolution.
Custom Brushes and Textures: Utilize or create custom brushes and textures tailored to screen printing needs for unique effects. Brushes can be managed effectively with this guide.
Regular Updates and Learning: Stay updated with the latest Photoshop features and continuously learn new techniques specific to screen printing. Adobe's Photoshop tutorials section is a great place to start.
Utilize Actions and Automation for Repetitive Tasks: Learn to create actions for repetitive tasks to save time and ensure consistency. Here's how to use actions in Photoshop.
By focusing on these areas, you can significantly improve your Photoshop workflow and output quality for screen printing projects.
How to Display Photoshop Skills on Your Resume
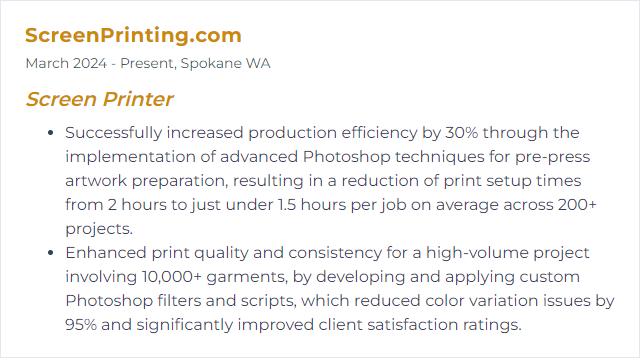
2. Illustrator
Illustrator, in the context of a Screen Printer, is a vector graphics software used for designing and preparing detailed, scalable artwork for screen printing processes.
Why It's Important
Illustrator is crucial for screen printers because it enables the creation of high-quality, vector-based designs that are scalable without loss of detail, ensuring precise and clean prints on various materials.
How to Improve Illustrator Skills
To improve your Illustrator skills for screen printing, focus on mastering the following areas concisely:
Vector Artwork Creation: Learn to create clean, high-resolution vector artwork. Vector designs are scalable without losing quality, crucial for screen printing. Adobe's own tutorials on vector graphics are a great starting point.
Color Separation: Understand how to separate colors in your designs since each color in screen printing is applied using a different screen. This guide on color separations in Illustrator can be useful.
Halftones and Gradients: For creating gradients or shading, learn to use halftones effectively, as they allow for the illusion of gradient in screen printing. Check out this halftone tutorial for practical tips.
Using the Pathfinder Tool: Master the Pathfinder tool for creating complex shapes and designs by combining or subtracting simple shapes. Adobe offers a concise overview of the Pathfinder tool.
Layer Management: Efficient layer management can streamline your workflow, making it easier to separate colors and organize your design elements. Here’s a brief guide to layers in Illustrator.
Keyboard Shortcuts: Familiarize yourself with Illustrator’s keyboard shortcuts to speed up your design process. Adobe’s keyboard shortcuts guide can help.
By concentrating on these areas and incorporating the resources provided, you can significantly improve your Illustrator skills for screen printing applications.
How to Display Illustrator Skills on Your Resume
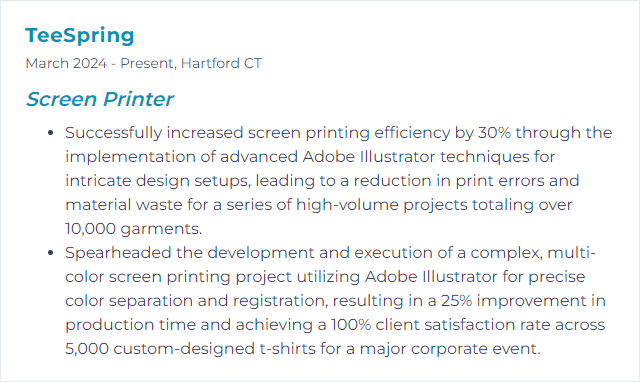
3. Color Matching
Color matching in screen printing is the process of ensuring that the colors printed on a substrate accurately match the desired or specified colors, often referencing a color system like Pantone, to ensure consistency and accuracy in reproductions.
Why It's Important
Color matching is crucial for a screen printer to ensure consistency and accuracy in reproducing the desired colors on printed materials, meeting client expectations, and maintaining quality across multiple prints or products.
How to Improve Color Matching Skills
Improving color matching in screen printing involves several key steps, focusing on calibration, ink management, and environmental factors. Here’s a concise guide:
Calibrate Your Equipment: Regularly calibrate your screen printing equipment and color matching tools to ensure consistency. Use colorimeters or spectrophotometers for precise calibration. X-Rite offers reliable tools for color measurement.
Use Pantone Matching System (PMS): Utilize the Pantone Matching System for a standardized color reproduction guide. It helps in accurately matching and communicating colors.
Ink Management: Properly mix and manage your inks. Use high-quality inks and follow the manufacturer's guidelines for mixing. Nazdar provides comprehensive ink solutions tailored for screen printing.
Test Prints: Always run test prints on the actual substrate you’ll be using. This helps in adjusting the colors before final production.
Control Environmental Variables: Maintain consistent environmental conditions (temperature and humidity) in your printing area, as variations can affect ink behavior and color consistency.
Educate Yourself: Continuously educate yourself and your team on color theory and screen printing techniques. ScreenPrinting.com offers resources and tutorials that can be invaluable.
Software Tools: Utilize software for color matching and management, such as Adobe Photoshop or Illustrator, which have built-in tools to help match and adjust colors. Adobe Color is a useful tool for creating color palettes.
By implementing these strategies, you can significantly improve color matching in your screen printing projects.
How to Display Color Matching Skills on Your Resume
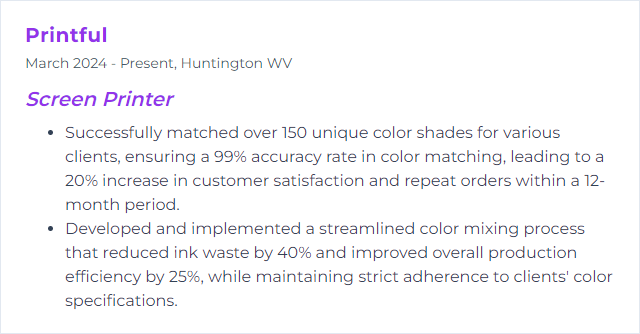
4. Prepress Operations
Prepress operations for a screen printer involve the preparation and adjustment of images and text before the actual printing process. This includes creating and editing designs, selecting and mixing inks, preparing screens with the design to be printed, and setting up the printing equipment to ensure accurate and high-quality prints on the desired substrate.
Why It's Important
Prepress operations are crucial for a screen printer as they ensure the accuracy and quality of the final print. This process involves preparing and finalizing the design files, selecting appropriate color separations, and creating screens. It sets the foundation for a successful print run by minimizing errors and material waste, ultimately saving time and money.
How to Improve Prepress Operations Skills
Improving prepress operations in screen printing involves optimizing artwork preparation, screen making, and setup processes to enhance efficiency, quality, and turnaround times. Here are concise strategies:
Digital Artwork Preparation: Use advanced graphic design software like Adobe Photoshop or Illustrator to create high-quality designs. Ensure artworks are in the correct format, resolution, and color mode (CMYK or Pantone) for screen printing.
Color Separation Software: Invest in specialized software like Separation Studio for accurate color separation, which is crucial for multicolor jobs. This software simplifies creating screens for each color in the design.
Screen Making Improvements: Use high-quality screens and emulsion to ensure detailed image transfer. Ryonet offers a range of supplies and equipment for creating durable screens. Proper exposure and post-exposure processes also enhance screen lifespan and print quality.
Workflow Management Tools: Implement workflow management software like Trello or Asana to streamline prepress operations, from artwork approval to final screen setup. These tools aid in tracking project progress and improving team collaboration.
Continuous Training: Regularly train staff on the latest prepress techniques and technologies. Online platforms like Udemy offer courses on screen printing and graphic design software.
Regular Maintenance: Maintain prepress equipment according to manufacturer recommendations to ensure consistent performance. This includes cleaning and degreasing screens, checking exposure units, and software updates.
By implementing these strategies, screen printers can significantly improve their prepress operations, leading to higher quality prints, reduced waste, and improved customer satisfaction.
How to Display Prepress Operations Skills on Your Resume
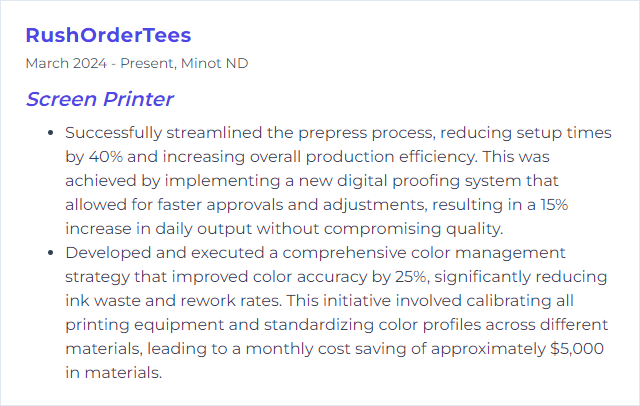
5. Screen Making
Screen making in screen printing involves creating a stencil (the screen) on a mesh screen, where parts of the screen are blocked off to form a design. This stencil will then be used to apply ink through the open areas of the mesh onto the printing surface, creating the desired image or pattern.
Why It's Important
Screen making is crucial in screen printing as it determines the accuracy, detail, and quality of the final print by ensuring the correct transfer of the design onto the substrate. It involves creating a precise stencil on a screen mesh that allows ink to pass through only in specific areas, directly affecting the print's resolution and fidelity.
How to Improve Screen Making Skills
Improving screen making for screen printing involves several key steps aimed at enhancing the quality and efficiency of your prints. Below are concise strategies along with external resources:
Proper Screen Tension: Ensure your screen is evenly and adequately tensioned to prevent issues with image detail and ink application. A tension meter can be helpful. Learn more about screen tension.
Correct Mesh Selection: Choose the right mesh count for your project based on the ink type and artwork detail. Mesh selection guide.
Use High-Quality Emulsion: Invest in a high-quality emulsion suitable for your ink type and printing conditions for better durability and resolution. Guide to choosing emulsions.
Optimal Exposure Time: Properly calculate exposure time to avoid under or over-exposure, which affects the stencil quality. Tools like an exposure calculator can be indispensable. Exposure tips.
Maintain a Clean Environment: Keep the screen making area clean to prevent dust and debris from affecting the emulsion and final print quality. Importance of cleanliness.
Invest in a Good Scoop Coater: A quality scoop coater ensures an even and smooth emulsion layer, crucial for screen longevity and consistency. Scoop coater basics.
Regularly Check and Refine Your Process: Continuously evaluate your screen making process for any potential improvements, including experimenting with new materials and techniques.
By focusing on these areas and seeking continuous improvement, you'll achieve higher quality prints and more efficient screen printing operations.
How to Display Screen Making Skills on Your Resume
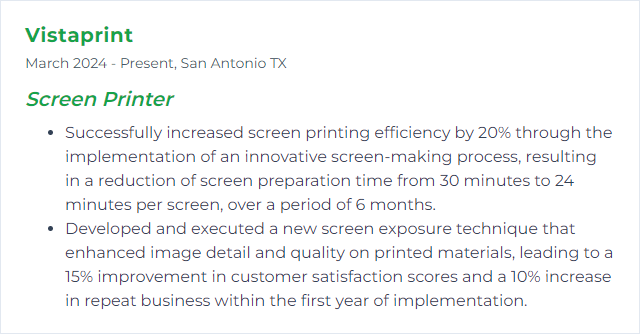
6. Ink Mixing
Ink mixing in screen printing involves combining different colors and types of ink to achieve a specific shade or consistency required for printing designs onto materials. This process is crucial for matching color specifications and ensuring uniformity across prints.
Why It's Important
Ink mixing is crucial for screen printers to achieve precise, consistent color matches across prints, ensuring high-quality, visually appealing results that meet client specifications.
How to Improve Ink Mixing Skills
To improve ink mixing for screen printing, follow these concise steps:
- Precise Measurement: Use a digital scale to measure ink components accurately. Consistency is key.
- Color Matching System: Utilize a Pantone matching system (PMS) for precise color replication. Pantone guides are essential.
- Stir Thoroughly: Mix inks thoroughly to ensure an even color and consistency. Avoid quick or uneven stirring to prevent air bubbles.
- Additives: Understand and use the correct additives for your ink type and application. This could include thinners or thickeners as needed. SGIA provides guidelines on additives.
- Test Prints: Always do a test print on the same substrate as your project to check for color accuracy and consistency.
- Record Keeping: Keep detailed records of ink formulations and adjustments for future reference and consistency.
By following these steps and continually educating yourself on the nuances of ink mixing, you can significantly improve your screen printing results.
How to Display Ink Mixing Skills on Your Resume
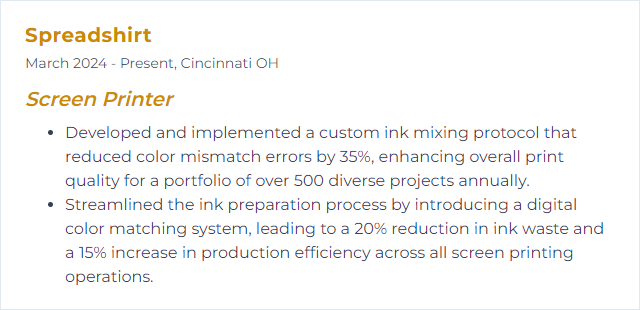
7. Squeegee Technique
The Squeegee Technique in screen printing involves dragging a rubber blade (squeegee) across a screen stencil to push ink through the mesh onto the printing surface, ensuring even ink distribution and clear design transfer.
Why It's Important
The Squeegee Technique is crucial for screen printers as it directly affects the quality and consistency of the ink transfer onto the substrate, ensuring a sharp, even, and vibrant print.
How to Improve Squeegee Technique Skills
Improving your squeegee technique as a screen printer is crucial for achieving high-quality prints. Here are concise tips with inline links for further reading:
Hold and Angle: Hold the squeegee at a 45-65 degree angle relative to the screen. This ensures an even spread of ink across the stencil. Speedball Art provides insights into proper handling.
Pressure: Apply consistent pressure throughout the stroke; too little won't transfer ink well, and too much can cause bleeding. Anthem Screen Printing Supplies discusses the balance of pressure.
Speed: Maintain a steady speed; too fast can result in incomplete coverage, too slow can cause ink bleeding. Ryonet Blog offers tips on finding the right speed.
Practice Different Techniques: Experiment with push and pull strokes to see which yields better results for you. Printavo explains the differences and benefits of each.
Maintain Your Squeegee: Ensure the edge is always smooth and free of nicks. Regularly rotating and replacing blades can improve print quality. Lawson Screen & Digital highlights maintenance tips.
Improving your squeegee technique requires practice and attention to these fundamental aspects. Regularly revisiting these principles and integrating feedback from your printing results will lead to noticeable improvements in your screen printing quality.
How to Display Squeegee Technique Skills on Your Resume
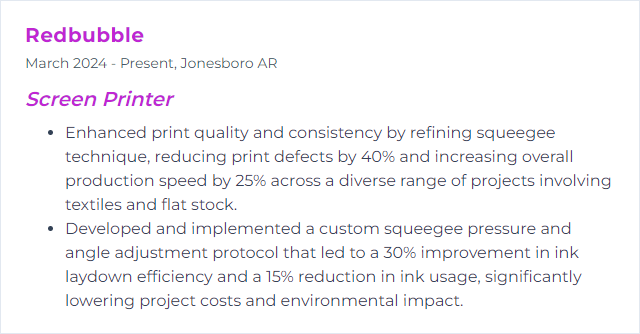
8. Registration Accuracy
Registration accuracy in screen printing refers to the precision with which each color layer aligns or registers with others on the print substrate, ensuring that the final image is sharp, and colors are correctly positioned without misalignment.
Why It's Important
Registration accuracy in screen printing is crucial because it ensures that multiple layers of ink align precisely on the substrate, resulting in a sharp, professional, and visually appealing final product. Poor registration can lead to misaligned colors or designs, reducing the quality and value of the print.
How to Improve Registration Accuracy Skills
To improve registration accuracy in a screen printer, follow these concise steps:
Ensure Proper Alignment: Regularly check and adjust the alignment of your screen frame to the base of the printer. Misalignment can lead to inaccuracies in registration.
Maintain Screen Tension: Consistently monitor and maintain the tension of your screen. A well-tensioned screen helps in achieving better registration. Screen Tension Tips
Use High-Quality Screens: Invest in high-quality screens with fine mesh counts for detailed designs, as they hold registration better. Choosing the Right Screen
Adjust Off-Contact Distance: Properly set the off-contact distance between the screen and the substrate to allow the screen to snap off the substrate cleanly, improving print accuracy. Setting Off-Contact
Utilize Registration Marks: Print clear registration marks on your substrates and use them to align the screens before printing. Using Registration Marks
Regular Calibration: Regularly calibrate your screen printer's mechanical and optical systems to ensure consistent registration accuracy. Calibration Methods
Software Alignment Tools: If available, use your printer’s software alignment tools for micro-adjustments, ensuring precision in registration. Software Tools Guide
Remember, practice and patience are key. Each step contributes to the overall improvement of registration accuracy in screen printing.
How to Display Registration Accuracy Skills on Your Resume
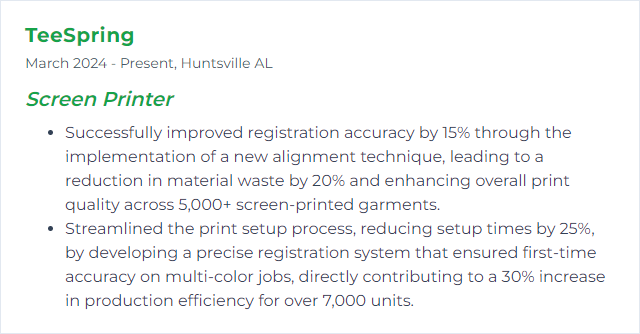
9. Quality Control
Quality control in screen printing involves systematically monitoring the printing process and final outputs to ensure that all products meet the predetermined standards of quality, including correct colors, sharpness, alignment, and absence of defects.
Why It's Important
Quality Control is crucial for a Screen Printer to ensure the consistency, durability, and accuracy of prints, thereby satisfying customer expectations and maintaining a strong reputation in a competitive market.
How to Improve Quality Control Skills
Improving Quality Control for a Screen Printer involves several focused steps. Here’s a concise guide:
Standardize Processes: Establish clear, documented procedures for each step of the screen printing process. This ensures consistency and repeatability. Screen Printing Magazine offers insights on standardizing processes.
Training: Invest in thorough training for your team. Proper handling and understanding of the equipment and processes reduce errors. SGIA provides various educational resources.
Regular Maintenance: Keep all equipment in optimal condition through regular maintenance. This prevents defects related to machinery performance. Impressions often shares tips on equipment upkeep.
Material Quality: Use high-quality inks and substrates. Quality materials lead to quality outputs. Suppliers like Nazdar provide premium screen printing materials.
Pre-Production Samples: Always run a pre-production sample to check for potential issues before the full run. This early detection saves resources. Printwear Magazine discusses the importance of pre-production protocols.
Inspection and Testing: Implement a robust inspection and testing phase for each batch to catch and correct errors early. ASTM Standards for printing technologies can be a guideline for setting up quality tests.
Feedback Loop: Create a system for collecting feedback from the end-users and the production team. This information is crucial for continuous improvement. Quality Magazine offers strategies for effective feedback systems.
By focusing on these areas, a screen printer can significantly enhance their quality control efforts.
How to Display Quality Control Skills on Your Resume
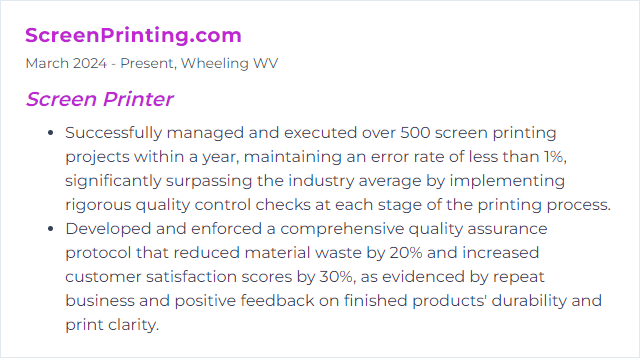
10. DTG Printing
DTG (Direct to Garment) Printing is a digital printing method that sprays ink directly onto the fabric, allowing for high-quality, detailed designs on garments, ideal for small runs and complex color graphics, contrasting with the stencil-based, ink-blocking technique of traditional screen printing.
Why It's Important
DTG (Direct to Garment) printing is important for a screen printer because it offers a versatile, low-cost solution for short runs and complex, multi-color designs, enabling high-quality, detailed printing directly onto garments without the need for screens or setup costs.
How to Improve DTG Printing Skills
Improving DTG (Direct to Garment) Printing, especially for a screen printer transitioning or expanding into DTG, involves several focused strategies. Here’s a concise guide:
Pre-Treatment Mastery: Properly pre-treat garments to ensure vibrant colors and sharp prints. Pre-treatment also affects washability. Experiment with different pre-treat formulas and application amounts based on fabric type. Epson offers detailed guides and products for pre-treatment.
Maintenance Routine: Regularly maintain your DTG printer to prevent clogs and ensure consistent print quality. This includes daily printhead cleaning and system checks. Brother’s maintenance tips provide a good starting point.
High-Quality Artwork: Use high-resolution and properly adjusted artwork to get sharp and detailed prints. Vector graphics are preferred for their scalability without loss of quality. Adobe’s tips for preparing graphics for printing can be very helpful.
Optimize Workflow: Streamline the process from design to finished product to increase efficiency and reduce errors. This includes software for order management, color matching, and scheduling. RIP software solutions by Wasatch can significantly enhance workflow efficiency.
Experiment with Fabrics: DTG prints differently on various fabrics. Natural fibers like cotton yield the best results. Test different fabric blends to find the optimal balance for your product range.
Education and Training: Continuously educate yourself and your team on the latest DTG technologies and techniques. Online forums, webinars, and trade shows are great resources. SGIA (Specialty Graphic Imaging Association) offers in-depth resources and events for industry professionals.
Utilize Software Tools: Employ DTG-specific software for color matching and print fidelity. This ensures colors are vibrant and accurate. Kornit’s software solutions can enhance print quality and efficiency.
Quality Control: Implement a strict quality control process to catch and correct issues before products reach customers. This should cover every step, from pre-treatment to the final product.
By focusing on these areas, screen printers can significantly improve their DTG printing capabilities, leading to higher quality prints, greater efficiency, and better customer satisfaction.
How to Display DTG Printing Skills on Your Resume
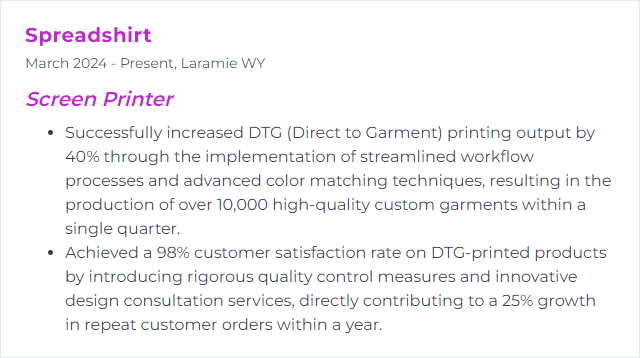
11. Sublimation Printing
Sublimation printing is a digital printing technique that transfers designs onto materials using heat-sensitive inks. It's distinct from traditional screen printing, as it enables full-color, high-resolution images to be printed directly onto polyester or polymer-coated items, making it ideal for complex or photographic designs. The ink transitions from solid to gas without becoming liquid, embedding the design seamlessly into the material for a durable and vibrant finish.
Why It's Important
Sublimation printing is important for a screen printer because it allows for the transfer of high-resolution, full-color images directly onto synthetic materials and surfaces, offering a durable and vibrant print quality that screen printing cannot achieve on certain substrates. It expands the range of printable products, enhancing the versatility and service offerings of a screen printing business.
How to Improve Sublimation Printing Skills
Improving sublimation printing, especially for a screen printer, involves focusing on key areas such as materials, equipment, process control, and design optimization. Here’s a concise guide:
Use High-Quality Substrates: Always select high-grade, poly-coated substrates optimized for sublimation. This ensures better ink absorption and vibrant colors. Coastal Business Supplies offers a wide range of suitable materials.
Ink and Printer Quality: Invest in premium sublimation inks and a reliable printer designed specifically for sublimation. This enhances the print's durability and color fidelity. Epson and Sawgrass are notable brands in this space.
Optimize Color Management: Utilize ICC profiles for your printer and software to ensure accurate color reproduction. Calibration tools and software like those from X-Rite can help maintain color accuracy.
Heat Press Quality and Settings: A consistent and even heat press is crucial. Ensure the temperature, pressure, and timing are precisely controlled for each type of substrate. Stahls’ offers high-quality heat press equipment.
Master the Technique: Perfect the pre-press, pressing, and post-press processes. This includes pre-treating fabrics if necessary, using proper protective sheets, and understanding the specific requirements of different materials. HeatPressNation provides resources and tutorials.
Design Optimization: Use high-resolution images and software like Adobe Illustrator or Photoshop to create or adjust designs. Ensure designs are tailored for sublimation printing to maximize detail and color quality. Adobe Creative Cloud is a comprehensive tool for design creation.
Continuous Learning and Testing: Stay updated with the latest techniques and products. Experiment with different settings and materials to find what works best for specific projects.
By focusing on these areas, a screen printer can significantly improve the quality and efficiency of their sublimation printing projects.
How to Display Sublimation Printing Skills on Your Resume
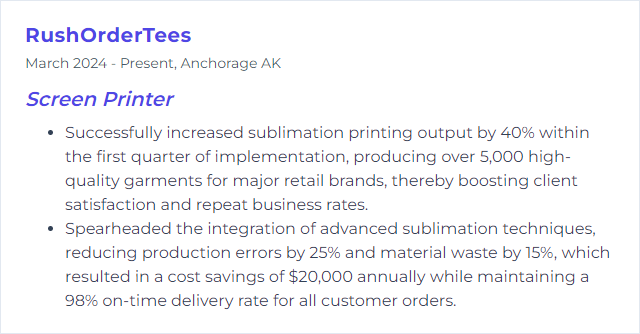
12. Plastisol Inks
Plastisol inks are a type of screen printing ink made from PVC particles suspended in a plasticizer. They are widely used by screen printers because they are easy to use, durable, and versatile, allowing for vibrant prints on a variety of fabrics. Unlike water-based inks, plastisol inks do not dry in the screen, making them ideal for longer print runs. They require heat to cure, typically around 320°F (160°C), after which they become solid and permanently adhere to the fabric.
Why It's Important
Plastisol inks are crucial for screen printers because they provide vibrant, opaque colors that adhere well to fabric, are highly durable, and easy to work with, enabling high-quality, long-lasting prints on a wide range of textiles.
How to Improve Plastisol Inks Skills
Improving Plastisol Inks for screen printing involves several strategies aimed at enhancing print quality, durability, and process efficiency. Below are concise recommendations:
Proper Mixing: Thoroughly mix your ink before use to ensure consistency and smoothness. This prevents issues like pigment separation or thickening. Ink Mixing Techniques.
Use Additives: Incorporate additives to adjust viscosity, drying time, or opacity as needed for specific jobs. Be mindful of manufacturer recommendations to avoid over-alteration. Guide to Plastisol Additives.
Proper Mesh Selection: Choose the correct mesh count for your design's detail level and ink type to achieve the best print quality. Mesh Selection Guide.
Cure Correctly: Ensure proper curing of prints to prevent cracking or fading. Use a precise temperature and time based on ink specifications. Curing Plastisol Inks.
Maintain Equipment: Regularly clean and maintain your screen printing equipment to ensure consistent ink application and prevent defects. Equipment Maintenance Tips.
Test Prints: Always perform test prints on scrap material before starting the actual print run to adjust pressure, squeegee angle, and stroke speed for optimal results. Screen Printing Test Print Guide.
Incorporating these practices into your screen printing workflow can significantly improve the quality and durability of prints made with Plastisol inks.
How to Display Plastisol Inks Skills on Your Resume
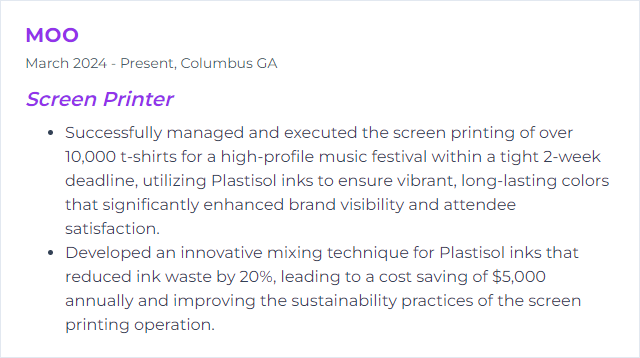