Top 12 Safety Specialist Skills to Put on Your Resume
In today's competitive job market, safety specialists stand out by showcasing a unique set of skills that highlight their expertise in creating and maintaining a secure work environment. This article delves into the top 12 skills that are essential for safety specialists to include on their resumes, ensuring they catch the eye of prospective employers and demonstrate their capability to effectively manage workplace safety.
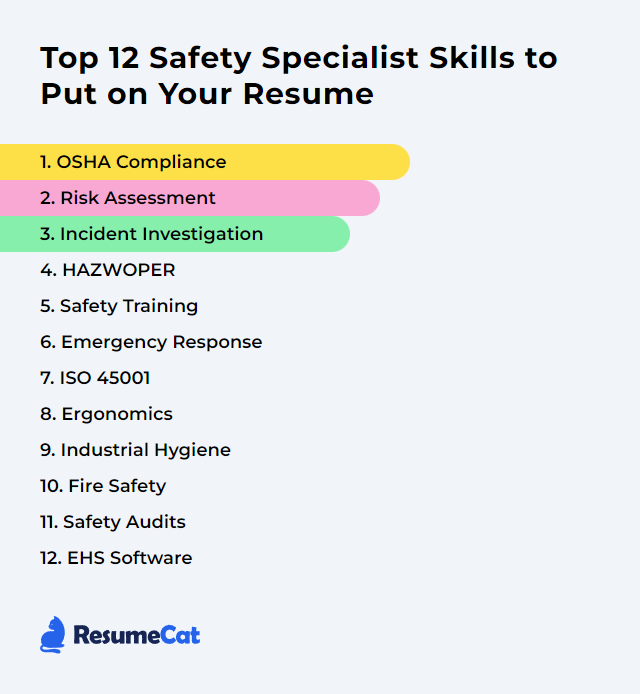
Safety Specialist Skills
- OSHA Compliance
- Risk Assessment
- Incident Investigation
- HAZWOPER
- Safety Training
- Emergency Response
- ISO 45001
- Ergonomics
- Industrial Hygiene
- Fire Safety
- Safety Audits
- EHS Software
1. OSHA Compliance
OSHA compliance refers to adhering to the standards and regulations set by the Occupational Safety and Health Administration to ensure a safe and healthy working environment. For a Safety Specialist, this involves implementing, monitoring, and enforcing these standards within an organization to prevent workplace injuries and illnesses.
Why It's Important
OSHA compliance is crucial for a Safety Specialist as it ensures the implementation of standardized health and safety protocols, minimizes workplace hazards, and protects both employees and the organization from potential legal and financial consequences.
How to Improve OSHA Compliance Skills
Improving OSHA compliance involves a multifaceted approach focusing on awareness, training, and continuous improvement. Here's a concise guide for a Safety Specialist:
Stay Informed: Regularly visit the OSHA website to stay updated on new regulations, guidelines, and resources.
Conduct Regular Audits: Perform comprehensive safety audits to identify and mitigate workplace hazards.
Employee Training: Ensure all employees receive training on relevant safety standards and emergency procedures.
Implement Safety Programs: Develop and enforce safety programs tailored to your workplace's specific needs. Resources on program development are available on the OSHA Recommended Practices page.
Engage Employees: Encourage employee participation in safety discussions and safety committees to foster a culture of safety.
Report and Investigate: Promptly report and investigate accidents and near misses to understand their root causes. OSHA's Incident Investigation guide provides a useful framework.
Maintain Records: Accurately maintain and review records of work-related injuries and illnesses as per OSHA requirements, detailed in their Recordkeeping section.
Use OSHA Resources: Leverage the variety of resources OSHA offers, including consultation services for small and medium-sized businesses, available through the OSHA Consultation Program.
Stay Proactive: Always look for ways to improve safety measures before issues arise. Engage with professional safety organizations and networks for new ideas and best practices.
Legal Compliance: Ensure all practices comply not just with federal OSHA standards, but also with any applicable state-specific safety regulations, available through State Plans.
Following these steps will not only help in maintaining compliance with OSHA standards but will also contribute to creating a safer and more productive workplace.
How to Display OSHA Compliance Skills on Your Resume
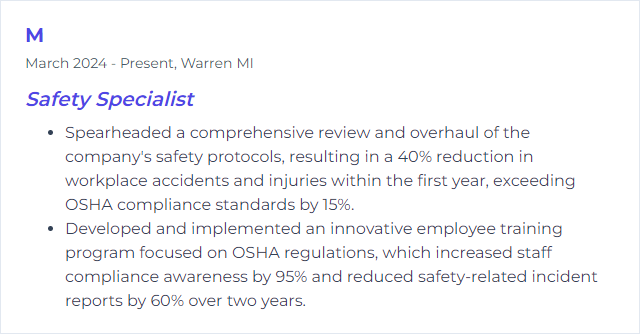
2. Risk Assessment
Risk assessment is the process of identifying, analyzing, and evaluating potential hazards to prevent accidents, injuries, and occupational illnesses in the workplace, thereby ensuring the safety and well-being of employees.
Why It's Important
Risk assessment is crucial for a Safety Specialist as it identifies potential hazards, evaluates the risk of harm, and enables the implementation of measures to prevent accidents, ensuring the health and safety of workers and compliance with legal requirements.
How to Improve Risk Assessment Skills
Improving risk assessment involves a systematic approach to identify, evaluate, and control hazards in the workplace. Here’s a concise guide to enhance your risk assessment process:
Stay Informed: Keep abreast of the latest safety standards and regulations relevant to your industry. Websites like OSHA (Occupational Safety and Health Administration) provide valuable resources and guidelines.
Comprehensive Hazard Identification: Conduct thorough inspections and consult with employees to identify potential risks. Tools such as Hazard Identification Training Tool from NIOSH can help.
Risk Evaluation: Prioritize risks based on their likelihood and impact. The Risk Matrix Tool from CCOHS (Canadian Centre for Occupational Health and Safety) offers a framework for evaluating risks.
Implement Controls: Develop and implement control measures to mitigate identified risks. Refer to the hierarchy of controls outlined by NIOSH for effective strategies.
Continuous Monitoring and Review: Regularly review and update the risk assessment to reflect any changes in the workplace or following an incident. Continuous improvement practices are detailed in resources like ISO 31000, an international standard for risk management.
Training and Communication: Ensure that all employees are trained on the risks and the measures in place to mitigate them. Engage with platforms like SafetySkills for online safety training courses.
Leverage Technology: Utilize software tools for risk assessment and management. Platforms like SafetyCulture (iAuditor) offer digital checklists and inspection tools to streamline the process.
By systematically implementing these steps and leveraging the resources provided, you can significantly enhance the effectiveness of your risk assessments and contribute to creating a safer workplace environment.
How to Display Risk Assessment Skills on Your Resume
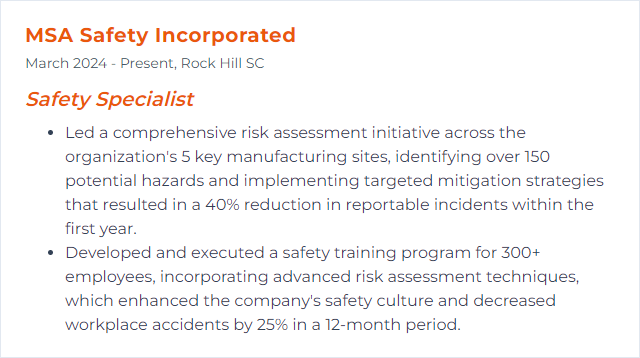
3. Incident Investigation
Incident Investigation is a systematic process conducted by Safety Specialists to identify the root causes of an incident, accident, or near miss in the workplace, with the goal of implementing measures to prevent recurrence and improve safety.
Why It's Important
Incident investigation is crucial for a Safety Specialist as it helps identify the root causes of accidents or near-misses, allowing for the implementation of corrective actions to prevent future occurrences, thereby ensuring the safety and well-being of employees and the integrity of workplace operations.
How to Improve Incident Investigation Skills
Improving incident investigation involves a systematic approach to identify root causes and implement corrective actions effectively. Here's a concise guide for a Safety Specialist:
Preparation: Ensure you have the right tools and training. Familiarize yourself with the site and processes. OSHA's Incident Investigation Guide is a valuable resource.
Immediate Response: Secure the scene to preserve evidence. Provide first aid and medical care as needed. CDC's Emergency Preparedness and Response offers guidelines.
Gather Data: Collect evidence, including photographs, measurements, and witness statements. Use structured interviews. The TapRooT® System is a comprehensive tool for root cause analysis.
Analysis: Identify root causes using techniques like the 5 Whys or Fishbone Diagram. ASSE's Root Cause Analysis provides detailed methodologies.
Report Writing: Document findings, root causes, and recommended corrective actions clearly and concisely. The Safety Report Writing Guide by NSC offers valuable tips.
Follow-Up: Ensure implementation of corrective actions and evaluate their effectiveness over time. Continuous improvement should be a goal. ISO 45001 outlines an effective safety management system that includes incident investigation.
By following these steps and utilizing these resources, a Safety Specialist can enhance their incident investigation process, leading to safer work environments.
How to Display Incident Investigation Skills on Your Resume
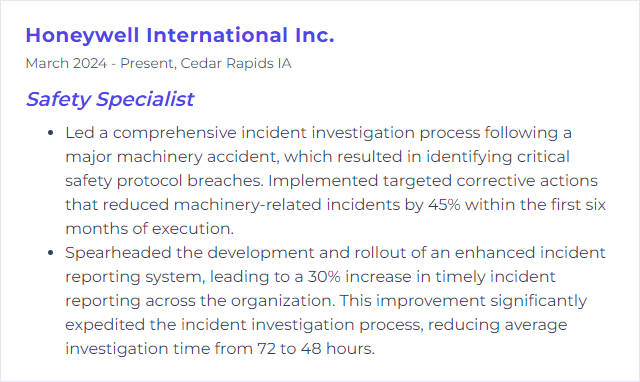
4. HAZWOPER
HAZWOPER (Hazardous Waste Operations and Emergency Response) is a set of guidelines and training requirements designed to protect workers who handle hazardous substances, ensuring they can safely manage and respond to emergencies involving hazardous waste. For a Safety Specialist, it involves overseeing compliance, training, and safety protocols related to hazardous material handling and emergency response.
Why It's Important
HAZWOPER is crucial for Safety Specialists as it provides comprehensive training on hazardous waste operations and emergency response, ensuring the safety and health of workers handling dangerous substances, and protecting the environment from contamination.
How to Improve HAZWOPER Skills
Improving HAZWOPER (Hazardous Waste Operations and Emergency Response) as a Safety Specialist involves continuous education, practical training, and the implementation of updated safety protocols. Here are concise steps to enhance HAZWOPER effectiveness:
Stay Informed: Regularly update your knowledge on HAZWOPER standards by visiting OSHA’s HAZWOPER page.
Continuing Education: Enroll in advanced HAZWOPER training courses to stay ahead of new regulations and technologies.
Practical Training: Implement hands-on training scenarios that mimic real-life hazardous situations for better preparedness. Practice makes perfect.
Safety Protocols: Regularly review and update emergency response plans and safety protocols to align with current best practices. Ensure all team members are familiar with these protocols.
Equipment Checks: Conduct routine inspections and maintenance of safety equipment to ensure they are in good working order.
Health Surveillance: Implement a comprehensive health surveillance program to monitor the health of workers involved in hazardous waste operations.
Community Engagement: Engage with local emergency services and other organizations to foster a collaborative approach to hazardous waste emergencies.
Feedback Loops: Create a feedback system where workers can report safety concerns or suggest improvements without fear of reprisal.
By focusing on these areas, a Safety Specialist can significantly improve the effectiveness of HAZWOPER activities, enhancing both safety and compliance.
How to Display HAZWOPER Skills on Your Resume
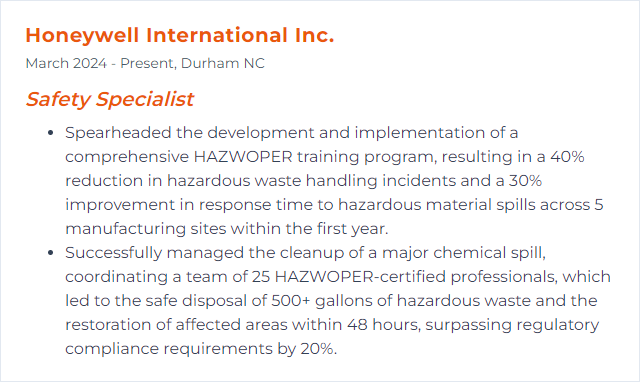
5. Safety Training
Safety training involves educating employees on the necessary procedures, practices, and behaviors to prevent accidents and injuries in the workplace, ensuring a safe and healthy environment.
Why It's Important
Safety training is crucial as it equips a Safety Specialist with the necessary knowledge and skills to identify, assess, and mitigate workplace hazards, ensuring the health and safety of all employees and preventing accidents, injuries, and fatalities.
How to Improve Safety Training Skills
Improving safety training involves a multifaceted approach focusing on engagement, relevance, and continuous improvement. Here are concise strategies:
Engagement: Enhance learner engagement by incorporating interactive elements such as quizzes, simulations, and group discussions. Tools like Kahoot! can make learning fun and interactive.
Relevance: Customize training content to be job-specific, addressing real-life scenarios that employees might face. Utilize resources from OSHA for industry-specific guidelines and training materials.
Blended Learning: Combine in-person training with e-learning platforms for a flexible and comprehensive learning experience. Platforms like LinkedIn Learning offer courses on a wide range of safety topics.
Feedback Loop: Establish a feedback mechanism using tools like SurveyMonkey to gather insights from participants on training effectiveness and areas for improvement.
Continuous Improvement: Stay updated with the latest safety trends, regulations, and technologies. Join professional networks such as the American Society of Safety Professionals for resources and community support.
By focusing on these strategies, safety training can be made more effective, engaging, and relevant to the workforce.
How to Display Safety Training Skills on Your Resume
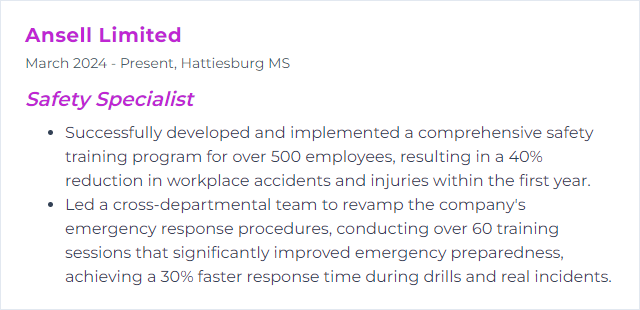
6. Emergency Response
Emergency Response refers to the organized and immediate actions taken to address and manage the aftermath of an emergency situation, aiming to minimize its impact on health, safety, and the environment. For a Safety Specialist, it involves coordinating and implementing safety protocols, providing first aid, conducting evacuations, and liaising with emergency services to protect personnel and property.
Why It's Important
Emergency response is crucial as it ensures immediate, efficient action to prevent further harm, save lives, and minimize damage during unexpected incidents, aligning with a Safety Specialist's goal of safeguarding people and property.
How to Improve Emergency Response Skills
Improving emergency response involves strategic planning, training, and technological integration. Here are concise strategies for a Safety Specialist:
Risk Assessment: Regularly conduct risk assessments to identify potential hazards and vulnerabilities within your organization or community.
Training and Drills: Implement comprehensive training programs for all staff, emphasizing realistic drills and simulations to enhance readiness.
Communication Plans: Develop clear communication plans that include both internal protocols and coordination with external emergency services.
Technology Integration: Utilize modern emergency management software and apps to streamline response efforts, ensuring quick and efficient coordination.
Community Engagement: Engage with the community through educational programs and partnerships with local emergency services to foster a collaborative response network.
Continuous Improvement: Regularly review and update emergency plans based on lessons learned from drills and actual events, incorporating feedback from all stakeholders.
By focusing on these areas, Safety Specialists can significantly enhance emergency response capabilities.
How to Display Emergency Response Skills on Your Resume
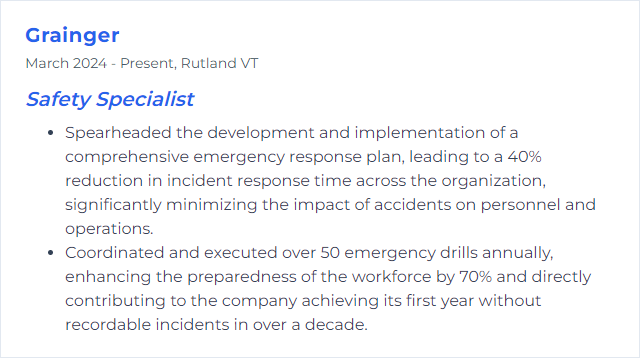
7. ISO 45001
ISO 45001 is an international standard for occupational health and safety management systems, designed to help organizations improve employee safety, reduce workplace risks, and create better, safer working conditions.
Why It's Important
ISO 45001 is important for a Safety Specialist because it provides a global standard for occupational health and safety management systems, helping to proactively prevent work-related injury and ill health, as well as improve employee safety, reduce workplace risks, and create better, safer working conditions.
How to Improve ISO 45001 Skills
Improving ISO 45001, the international standard for occupational health and safety management systems, involves continuous evaluation and enhancement of the workplace safety processes. For a Safety Specialist, the following concise steps can significantly contribute to the improvement of ISO 45001 implementation:
Gap Analysis: Perform a comprehensive gap analysis to identify discrepancies between your current OHS management system and the requirements of ISO 45001.
Employee Engagement: Enhance employee involvement in safety matters by providing training and awareness programs. This ensures that safety becomes everyone's responsibility.
Risk Management: Continuously identify, assess, and control workplace hazards to minimize risks to employees' health and safety.
Leadership Commitment: Strengthen management's commitment to safety by ensuring they lead by example and allocate appropriate resources for safety initiatives. Leadership roles in ISO 45001 play a crucial role in its success.
Performance Monitoring: Implement a robust system for monitoring and measuring safety performance against predefined objectives and targets.
Continuous Improvement: Adopt a culture of continual improvement through regular audits, management reviews, and corrective actions. Utilize tools like the Plan-Do-Check-Act (PDCA) cycle for systematic improvements.
Legal Compliance: Ensure ongoing compliance with applicable legal and other requirements related to occupational health and safety.
Incident Management: Develop and maintain a proactive approach to incident management, including investigation and learning from non-conformities.
By focusing on these areas, a Safety Specialist can drive significant improvements in their organization's implementation of ISO 45001, leading to a safer and healthier workplace for all employees.
How to Display ISO 45001 Skills on Your Resume
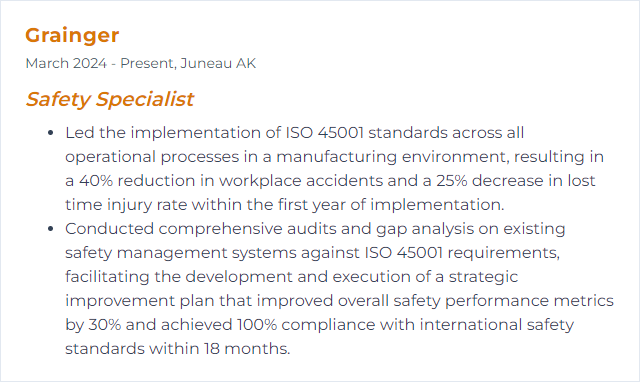
8. Ergonomics
Ergonomics is the science of designing work environments to fit the physical and cognitive abilities of workers, aiming to enhance safety, comfort, and productivity.
Why It's Important
Ergonomics is crucial for enhancing comfort, reducing injury risk, and improving productivity and job satisfaction, thereby promoting a safer and more efficient work environment.
How to Improve Ergonomics Skills
Improving ergonomics involves the design and arrangement of workplaces to fit the worker, thereby enhancing comfort, efficiency, and safety. As a Safety Specialist, focus on:
Assess Workstations: Conduct ergonomic assessments to identify potential risks and areas for improvement. Tools like the Rapid Upper Limb Assessment (RULA) can help.
Adjustable Furniture: Encourage the use of adjustable chairs, desks, and monitors to suit individual needs. OSHA's Computer Workstations eTool provides guidelines for proper adjustments.
Proper Equipment: Promote the use of ergonomic tools and equipment, like vertical mice or padded keyboard rests. The CDC's Ergonomics and Musculoskeletal Disorders page offers resources on selecting ergonomic tools.
Training: Provide ergonomic training sessions to educate employees on correct posture, workstation setup, and usage of ergonomic tools. ErgoPlus has resources for workplace ergonomics training.
Frequent Breaks: Encourage short, frequent breaks to reduce muscle fatigue and strain. The Pomodoro Technique is one method to structure breaks effectively.
Exercise and Stretch: Promote regular exercise and stretching routines to strengthen muscles and increase flexibility. Mayo Clinic's Desk Exercises guide provides simple exercises that can be done at the desk.
Implementing these strategies can significantly improve workplace ergonomics, leading to increased worker comfort, reduced injury risks, and enhanced productivity.
How to Display Ergonomics Skills on Your Resume
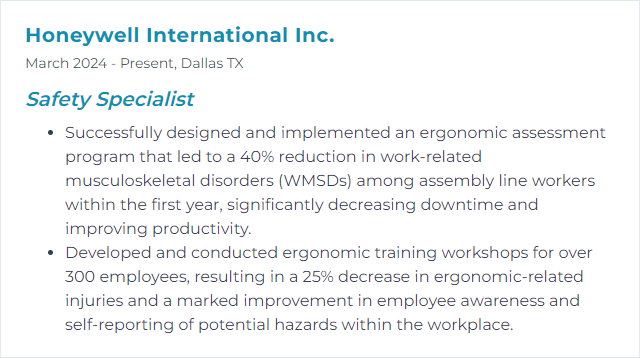
9. Industrial Hygiene
Industrial Hygiene is the science of anticipating, recognizing, evaluating, and controlling workplace conditions that may cause workers' injury or illness. For a Safety Specialist, it involves implementing measures to protect the health and safety of workers by identifying hazards and setting up controls to manage them.
Why It's Important
Industrial hygiene is crucial for a Safety Specialist as it focuses on identifying, evaluating, and controlling environmental hazards in the workplace, thereby safeguarding the health and well-being of employees, preventing occupational diseases, and ensuring compliance with health and safety regulations.
How to Improve Industrial Hygiene Skills
Improving Industrial Hygiene involves several key steps that Safety Specialists can undertake to ensure a safer work environment:
Assess Risks: Conduct thorough workplace assessments to identify potential hazards related to chemical, physical, biological, and ergonomic risks. OSHA's Hazard Identification provides guidelines on how to identify hazards.
Implement Control Measures: Based on the risk assessment, implement appropriate control measures following the hierarchy of controls - elimination, substitution, engineering controls, administrative controls, and personal protective equipment (PPE). The NIOSH Hierarchy of Controls offers insights into effectively implementing these measures.
Training and Education: Provide comprehensive training and education to employees about the hazards they might encounter and the safety practices to mitigate these risks. OSHA's Training and Education resources can be beneficial.
Monitor and Maintain: Regularly monitor the work environment and the health of employees to ensure control measures are effective. Maintain safety equipment and ensure that PPE is in good condition. The AIHA's Framework for IH Program Effectiveness provides resources on monitoring.
Continuous Improvement: Continuously review and update safety policies, procedures, and programs based on new scientific findings, technology advancements, and feedback from employees. Engaging with professional bodies such as the American Industrial Hygiene Association (AIHA) can keep you updated on the latest in the field.
Emergency Preparedness: Develop and regularly update an emergency response plan. Training employees on this plan is crucial. Check OSHA's Emergency Preparedness and Response for guidelines.
By following these steps and utilizing resources from reliable organizations, Safety Specialists can significantly improve Industrial Hygiene in the workplace.
How to Display Industrial Hygiene Skills on Your Resume
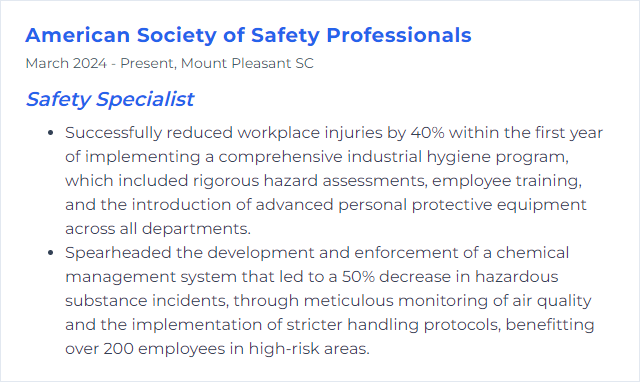
10. Fire Safety
Fire Safety refers to the set of practices aimed at preventing the outbreak of fire, minimizing potential harm, and ensuring safe evacuation and response in the event of a fire. It involves compliance with fire codes, installation of fire detection and suppression systems, conducting risk assessments, and providing fire safety training.
Why It's Important
Fire safety is essential to prevent loss of life, property damage, and workplace disruptions, ensuring the well-being of employees and the continuity of business operations.
How to Improve Fire Safety Skills
Improving fire safety involves a multifaceted approach focusing on prevention, detection, and response. As a Safety Specialist, consider the following steps:
Risk Assessment: Regularly conduct fire risk assessments to identify potential hazards and implement measures to mitigate them. National Fire Protection Association (NFPA) provides guidelines on conducting thorough assessments.
Safety Training: Provide comprehensive fire safety training for all employees, including the use of fire extinguishers, evacuation procedures, and emergency response. The Occupational Safety and Health Administration (OSHA) offers resources on training and emergency preparedness.
Fire Detection Systems: Ensure the installation and maintenance of reliable fire detection systems like smoke alarms and fire alarms. Regular testing and maintenance are crucial. The National Fire Protection Association (NFPA) sets standards for these systems.
Fire Suppression Equipment: Equip the facility with appropriate fire suppression tools, including fire extinguishers, sprinkler systems, and fire hoses. It's vital to choose the right type of extinguisher for different kinds of fires. Refer to OSHA guidelines for selection and placement.
Clear Evacuation Routes: Maintain clear and marked evacuation routes and exits. Conduct regular drills to ensure everyone knows how to evacuate safely and quickly. Ready.gov provides insights on planning and executing evacuation plans.
Electrical Safety: Regularly inspect wiring and electrical equipment to prevent electrical fires. Guidance on electrical safety can be found through OSHA’s Electrical Safety workspace.
Hazardous Material Management: Properly store and handle flammable materials following regulatory standards. The Environmental Protection Agency (EPA) offers guidelines on managing hazardous air pollutants that could elevate fire risks.
Fire Safety Policies: Develop and enforce strict fire safety policies, including smoking regulations and control measures for open flames or heating elements.
By focusing on these key areas, a Safety Specialist can significantly enhance fire safety within any organization or facility. Continuous education, regular updates to safety protocols, and adherence to local and national fire safety regulations are essential components of an effective fire safety strategy.
How to Display Fire Safety Skills on Your Resume
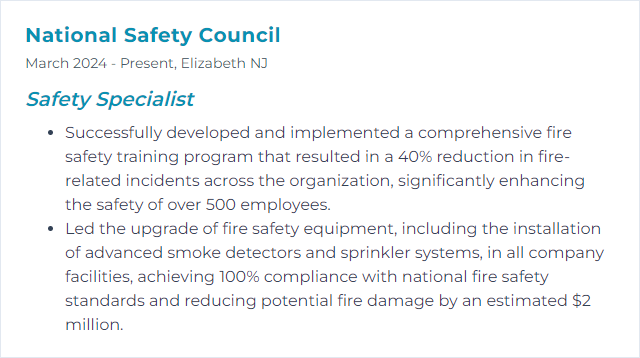
11. Safety Audits
Safety audits are systematic evaluations conducted by safety specialists to assess the effectiveness of an organization's health and safety programs, identify potential hazards, ensure compliance with relevant safety regulations, and recommend improvements to enhance workplace safety.
Why It's Important
Safety audits are crucial as they systematically evaluate the effectiveness of an organization's health and safety programs, ensuring compliance with regulations, identifying potential hazards, and preventing accidents or incidents, ultimately safeguarding employees and the workplace.
How to Improve Safety Audits Skills
Improving safety audits involves a structured approach focusing on thorough preparation, execution, and follow-up. Here are concise steps for a Safety Specialist to enhance the process:
Stay Updated: Keep abreast with the latest safety regulations and standards. Organizations such as OSHA provide a plethora of resources.
Engage Employees: Foster a culture of safety by involving employees in the audit process. This can be through safety meetings or training sessions.
Use Technology: Adopt audit management software to streamline the process. Tools like SafetyCulture (iAuditor) can help manage checklists and reports efficiently.
Comprehensive Planning: Define the scope of the audit clearly. Pre-audit checklists can be a useful tool.
Detail-Oriented Inspection: During the audit, pay attention to both major and minor safety concerns. Document findings meticulously.
Actionable Reporting: Post-audit, provide clear, actionable recommendations. Ensure findings are communicated effectively to all stakeholders.
Follow-Up: Implement a follow-up schedule to ensure corrective actions are taken. Continuous improvement should be the goal.
Training and Education: Regularly update training programs based on audit findings to educate employees about safety practices. Resources for training can be found at National Safety Council.
Benchmarking: Compare your audit results with industry standards or similar organizations to gauge your performance. This can help identify areas of improvement.
Seek Feedback: After the audit, get feedback from the audited teams on the process and use it to make future audits more effective.
By focusing on these areas, Safety Specialists can significantly improve the effectiveness of safety audits, ultimately fostering a safer workplace environment.
How to Display Safety Audits Skills on Your Resume
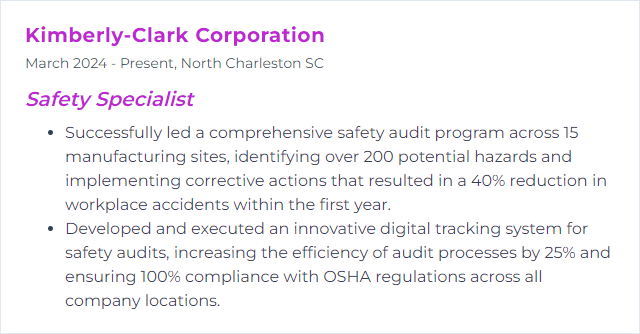
12. EHS Software
EHS Software, designed for Safety Specialists, is a digital tool that streamlines and manages the processes related to Environmental, Health, and Safety compliance, risk assessment, incident management, and sustainability initiatives, enhancing workplace safety and regulatory adherence.
Why It's Important
EHS (Environmental, Health, and Safety) Software is crucial for Safety Specialists as it streamlines compliance, risk management, and incident reporting processes, ensuring a safer, more efficient, and legally compliant workplace.
How to Improve EHS Software Skills
Improving Environmental, Health, and Safety (EHS) Software involves several key steps tailored to enhance user experience, compliance, and data management for Safety Specialists. Here's a concise guide:
User-Friendly Interface: Optimize the user interface for intuitiveness and ease of use. A straightforward design encourages user engagement and reduces training time.
Mobile Accessibility: Ensure the software is fully functional on mobile devices, allowing Safety Specialists to access and input data on the go.
Customization and Scalability: Adapt the software to meet specific organizational needs and scale as the company grows. Customization options can improve user satisfaction and data relevance.
Integration Capabilities: Facilitate integration with other systems (HR, Operations, etc.) for seamless data flow and comprehensive analytics. This enhances decision-making through holistic insights.
Robust Reporting Tools: Include advanced reporting features for generating insightful, actionable reports. Effective reporting tools help in identifying trends and areas needing improvement.
Compliance Management: Update the software regularly to reflect the latest regulations and standards, ensuring compliance. Keeping up with compliance reduces legal risks and promotes safety culture.
Data Security and Privacy: Prioritize strong data protection measures to safeguard sensitive information. Data security builds user trust and complies with regulations.
Continuous Improvement and Support: Offer ongoing support and regularly update the software based on user feedback and technological advancements. This approach ensures the software evolves to meet changing needs.
By focusing on these areas, Safety Specialists can significantly enhance the functionality and effectiveness of EHS software, leading to better safety outcomes and compliance.
How to Display EHS Software Skills on Your Resume
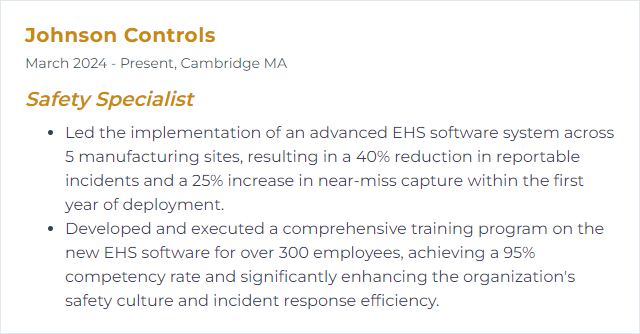