Top 12 Reliability Engineer Skills to Put on Your Resume
In today's competitive job market, standing out as a reliability engineer involves showcasing a distinctive set of technical and soft skills on your resume. Highlighting the top skills that demonstrate your expertise in ensuring the dependability of engineering systems can significantly enhance your appeal to potential employers.
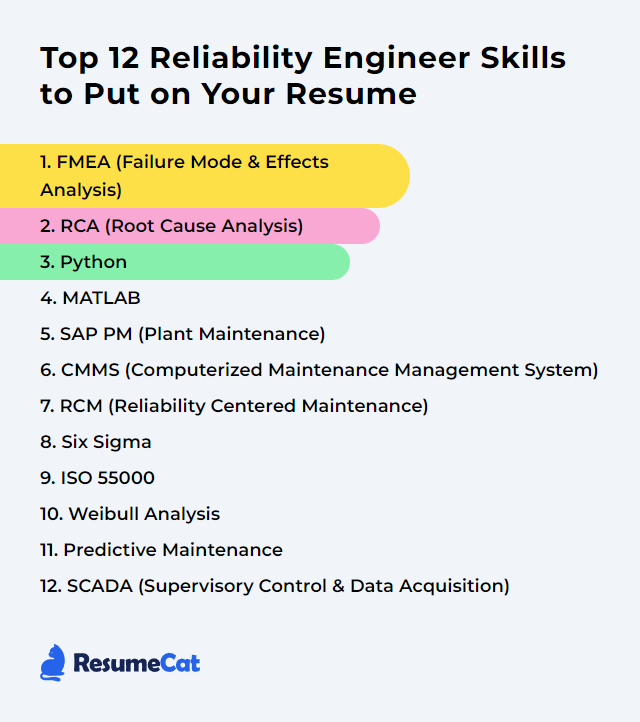
Reliability Engineer Skills
- FMEA (Failure Mode and Effects Analysis)
- RCA (Root Cause Analysis)
- Python
- MATLAB
- SAP PM (Plant Maintenance)
- CMMS (Computerized Maintenance Management System)
- RCM (Reliability Centered Maintenance)
- Six Sigma
- ISO 55000
- Weibull Analysis
- Predictive Maintenance
- SCADA (Supervisory Control and Data Acquisition)
1. FMEA (Failure Mode and Effects Analysis)
FMEA (Failure Mode and Effects Analysis) is a systematic method used by reliability engineers to identify and evaluate potential failure modes of a product or process, assess their effects on performance, and prioritize actions to mitigate or eliminate the risks associated with these failures.
Why It's Important
FMEA is crucial for a Reliability Engineer as it systematically identifies and assesses potential failure modes in a system, product, or process, allowing for proactive risk mitigation and enhancing reliability, safety, and customer satisfaction.
How to Improve FMEA (Failure Mode and Effects Analysis) Skills
Improving FMEA involves enhancing its accuracy, relevance, and usefulness in identifying and mitigating risks. For a Reliability Engineer, consider the following concise strategies:
Cross-Functional Teamwork: Engage a diverse team from different departments (design, manufacturing, quality, etc.) to gather comprehensive insights. ASQ provides guidelines on team composition and roles.
Prioritize Failure Modes: Use the Risk Priority Number (RPN) effectively to prioritize issues for corrective actions. Focus on high RPN values but also consider addressing lower-scored items with easy fixes. AIAG & VDA FMEA Handbook offers a refined approach to prioritization.
Dynamic Documentation: Keep FMEA documents live and dynamic. Update them with new findings, design changes, and process improvements. SAE International provides standards for maintaining FMEA documentation.
Training and Competence: Ensure team members are well-trained in FMEA methodology and tools. Regular training updates as methodologies evolve are crucial. Reliabilityweb offers resources and training opportunities.
Leverage Software Tools: Utilize FMEA software tools for efficient data management, analysis, and reporting. These tools facilitate collaboration and ensure consistency. PFMEA software comparison provides a starting point for selecting tools.
Integration with Other Processes: Integrate FMEA with other quality and reliability processes, such as Design for Reliability (DfR) and Root Cause Analysis (RCA), to enhance overall system reliability. NREL's Integration Guide offers insights into integrating FMEA into broader reliability engineering practices.
Implementing these strategies can significantly improve the effectiveness of FMEA in any organization.
How to Display FMEA (Failure Mode and Effects Analysis) Skills on Your Resume
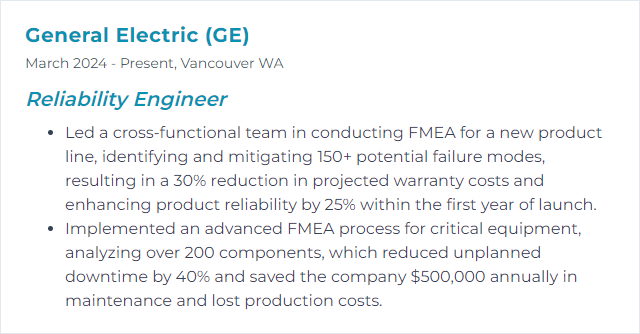
2. RCA (Root Cause Analysis)
Root Cause Analysis (RCA) is a systematic process used by Reliability Engineers to identify the underlying reasons for failures or problems in order to develop effective solutions that prevent recurrence.
Why It's Important
RCA (Root Cause Analysis) is crucial for a Reliability Engineer as it systematically identifies the underlying reasons for failures or problems, enabling the implementation of effective solutions to prevent recurrence, thus enhancing system reliability and performance.
How to Improve RCA (Root Cause Analysis) Skills
Improving Root Cause Analysis (RCA) involves systematic approaches and continuous learning. Here's a concise guide for a Reliability Engineer:
Define the Problem Clearly: Start with a specific, clear definition of the problem. Use 5 Whys to drill down to the root cause.
Gather Data Thoroughly: Collect comprehensive data around the failure. Use tools like Failure Mode and Effects Analysis (FMEA) to understand potential failures.
Analyze Data Systematically: Apply Cause and Effect Diagrams (Fishbone Diagrams) to identify all possible causes.
Identify Solutions: Focus on corrective actions that prevent recurrence. Consider Fault Tree Analysis (FTA) for complex problems.
Implement and Monitor: Implement solutions and monitor for effectiveness. Adapt and adjust as necessary.
Document and Share Learnings: Maintain records of RCAs and share lessons learned within the organization. Consider using a knowledge management system for this purpose.
Continuous Improvement: Employ Continuous Improvement Processes (CIP) to refine RCA techniques over time.
For a comprehensive understanding, regularly update your knowledge and skills through resources like the Reliabilityweb and The Association for the Advancement of Medical Instrumentation (AAMI), which offer insights and best practices in reliability engineering and RCA.
How to Display RCA (Root Cause Analysis) Skills on Your Resume
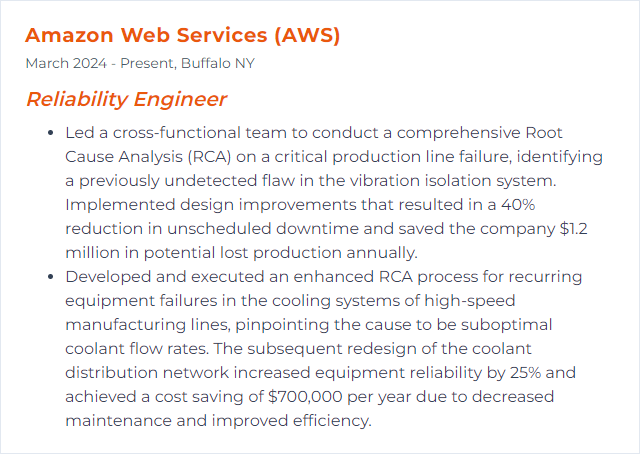
3. Python
Python is a high-level, interpreted programming language known for its simplicity and versatility, widely used in automation, data analysis, and software development, making it a valuable tool for Reliability Engineers in automating repetitive tasks, analyzing system performance data, and developing reliable software solutions.
Why It's Important
Python is important for Reliability Engineers due to its simplicity and versatility, enabling them to easily automate repetitive tasks, analyze system performance data, and develop reliable, scalable, and maintainable software solutions to ensure system uptime and efficiency.
How to Improve Python Skills
To improve your Python skills as a Reliability Engineer, focus on mastering the following areas:
Understand Python Basics: Ensure a solid grasp of Python syntax and fundamental concepts. Python Official Tutorial is a great starting point.
Learn System Automation: Automate routine system maintenance and configuration tasks. Automate the Boring Stuff with Python offers practical examples.
Master Error Handling: Develop robust applications by effectively managing exceptions. Python Documentation on Errors and Exceptions provides comprehensive guidance.
Dive into DevOps Tools: Familiarize yourself with tools like Ansible, Docker, and Kubernetes. Real Python’s DevOps Resources can be particularly useful.
Understand Infrastructure as Code (IaC): Learn tools like Terraform and practice writing infrastructure as code. Terraform Getting Started Guide will help.
Version Control with Git: Version control is crucial for collaboration and code management. Pro Git Book is a comprehensive resource.
Continuous Integration/Continuous Deployment (CI/CD): Implement CI/CD pipelines using Jenkins or GitHub Actions. GitHub Actions Documentation offers insights.
Monitoring and Logging: Leverage tools like Prometheus and ELK Stack for system monitoring and logging. Prometheus Documentation and Elastic ELK Stack Guide are good resources.
Improve Python Performance: Learn to optimize Python code for better performance. High Performance Python is a valuable read.
Participate in Open Source Projects: Contribute to open-source projects to gain real-world experience. GitHub is the platform to discover projects in need of help.
By focusing on these areas, you'll enhance your Python skills relevant to reliability engineering, making you a more effective and efficient professional.
How to Display Python Skills on Your Resume
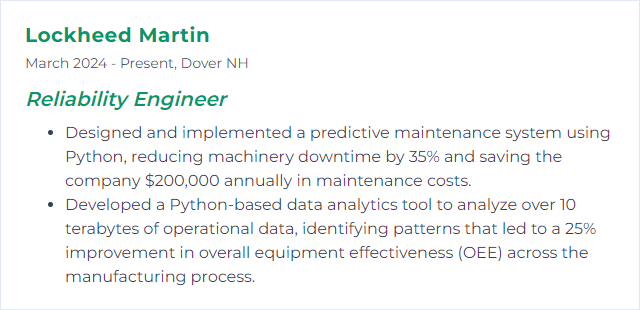
4. MATLAB
MATLAB is a high-level programming and numerical computing environment used for algorithm development, data analysis, visualization, and numerical computation, enabling Reliability Engineers to model, simulate, and evaluate the reliability and performance of systems and components.
Why It's Important
MATLAB is important for a Reliability Engineer because it provides powerful tools for data analysis, modeling, and simulation, enabling the efficient assessment and improvement of system reliability and performance.
How to Improve MATLAB Skills
To improve MATLAB skills, especially for a Reliability Engineer, consider the following concise strategies:
Online Courses: Engage in structured learning through platforms like Coursera or Udemy, focusing on courses tailored to engineering applications.
Official MATLAB Tutorials: Utilize MATLAB's official documentation and tutorials, which include examples specific to different engineering fields, including reliability engineering.
Practice Projects: Apply your skills to real-world problems or Kaggle competitions relevant to reliability engineering, enhancing both your MATLAB proficiency and domain-specific knowledge.
Join Forums and Communities: Participate in forums such as MATLAB Central to exchange knowledge, solve problems, and network with other professionals.
Read Books: Incorporate books into your learning routine. Titles like "MATLAB for Engineers" by Holly Moore offer practical insights and applications relevant to your field.
Use MATLAB Add-Ons: Explore and integrate MATLAB Add-Ons, including toolboxes relevant to reliability engineering, to extend MATLAB’s capabilities.
By combining these strategies, you'll not only improve your MATLAB skills but also tailor your learning to the specific needs of reliability engineering.
How to Display MATLAB Skills on Your Resume
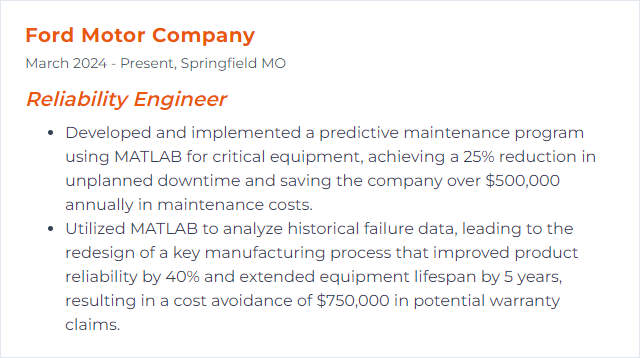
5. SAP PM (Plant Maintenance)
SAP PM (Plant Maintenance) is a module within the SAP ERP system designed to support the maintenance activities of an organization. For a Reliability Engineer, it offers tools for planning, executing, and recording maintenance tasks, tracking equipment history, and analyzing maintenance data to enhance asset reliability and performance.
Why It's Important
SAP PM (Plant Maintenance) is crucial for a Reliability Engineer as it enables efficient planning, execution, and tracking of maintenance activities, ensuring equipment reliability and minimizing downtime, ultimately optimizing plant performance and reducing operational costs.
How to Improve SAP PM (Plant Maintenance) Skills
Improving SAP Plant Maintenance (PM) involves enhancing the system's effectiveness in managing and executing maintenance activities within an organization. For a Reliability Engineer, focusing on these key areas can lead to significant improvements:
Data Quality and Structure: Ensure that all equipment and functional locations are accurately represented in SAP. This includes having a structured and standardized way of naming and categorizing assets. Regularly review and cleanse data to maintain its accuracy and relevance. SAP PM Data Management.
Maintenance Strategies: Develop and implement preventive maintenance strategies based on reliability-centered maintenance (RCM) principles. Utilize SAP's capabilities to schedule, track, and analyze preventive and predictive maintenance activities. Preventive Maintenance with SAP PM.
Training and User Adoption: Enhance the skills of maintenance teams and end-users by providing targeted training on the effective use of SAP PM. Focus on the benefits and how-to aspects of key transactions and reports. SAP PM Training.
Integration with Other Modules: Leverage the integration capabilities of SAP to connect PM with other modules such as Material Management (MM), Production Planning (PP), and Quality Management (QM) for a seamless flow of information and processes. This enhances decision-making and operational efficiency. SAP Module Integration.
Leverage Analytics and Reporting: Utilize SAP's analytics and reporting tools to gain insights into maintenance performance, equipment reliability, and failure patterns. This will help in making data-driven decisions to improve maintenance strategies and operations. SAP Analytics Cloud.
Continuous Improvement: Adopt a continuous improvement mindset by regularly reviewing the maintenance processes, system utilization, and performance metrics. Use SAP PM's feedback and analysis features to identify areas for improvement. Continuous Improvement Process.
By focusing on these areas, a Reliability Engineer can significantly enhance the effectiveness and efficiency of SAP PM within their organization.
How to Display SAP PM (Plant Maintenance) Skills on Your Resume
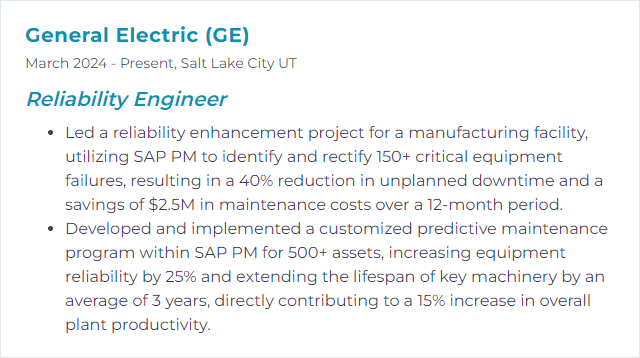
6. CMMS (Computerized Maintenance Management System)
A Computerized Maintenance Management System (CMMS) is a digital tool that helps reliability engineers plan, track, and optimize maintenance activities for equipment and assets, ensuring their efficient operation and minimizing downtime.
Why It's Important
A CMMS is crucial for a Reliability Engineer as it enables efficient scheduling of maintenance tasks, tracks equipment history, optimizes asset performance and reliability, and reduces downtime and operational costs.
How to Improve CMMS (Computerized Maintenance Management System) Skills
Improving a Computerized Maintenance Management System (CMMS) as a Reliability Engineer involves several focused steps to enhance efficiency, data accuracy, and decision-making processes. Here's a concise guide:
Data Quality: Start with ensuring the data entered into the CMMS is accurate, complete, and standardized. Implement regular audits and clean-ups. Data Quality Improvement
Training: Provide comprehensive training for all users on how to effectively use the CMMS. Training should be ongoing to cover updates and refreshers. CMMS Training Best Practices
Integration: Integrate your CMMS with other systems (e.g., ERP, SCADA) to streamline data flow and improve visibility across operations. System Integration Strategies
Mobility: Leverage mobile capabilities to allow real-time data entry and access, enhancing the responsiveness of maintenance activities. Mobile CMMS Benefits
KPIs and Reporting: Define and track key performance indicators (KPIs) relevant to maintenance reliability. Use the CMMS’s reporting tools to monitor trends and make data-driven decisions. Maintenance KPIs
Preventive and Predictive Maintenance: Shift from reactive to preventive and predictive maintenance strategies using the CMMS's scheduling and analysis tools. Predictive Maintenance
Feedback System: Implement a feedback loop with users to continuously identify and implement improvements to the CMMS and maintenance processes. Continuous Improvement in Maintenance
Vendor Support: Work closely with your CMMS vendor for support, updates, and to leverage their expertise in optimizing the system for your specific needs. Choosing the Right CMMS Vendor
By focusing on these areas, a Reliability Engineer can significantly enhance the effectiveness of a CMMS, leading to improved maintenance operations and equipment reliability.
How to Display CMMS (Computerized Maintenance Management System) Skills on Your Resume
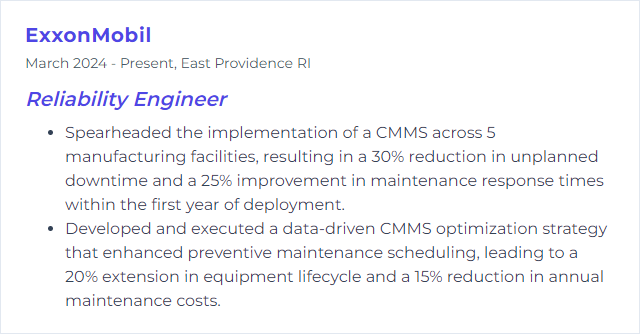
7. RCM (Reliability Centered Maintenance)
Reliability Centered Maintenance (RCM) is a systematic approach aimed at determining the most effective maintenance strategies to ensure equipment reliability and performance, focusing on identifying and preventing potential failures before they occur.
Why It's Important
RCM (Reliability Centered Maintenance) is important because it ensures that assets receive the appropriate level of maintenance to prevent failures, enhance safety, and optimize operational costs, thereby maximizing reliability and performance efficiency.
How to Improve RCM (Reliability Centered Maintenance) Skills
Improving Reliability Centered Maintenance (RCM) involves a systematic approach to ensure maintenance strategies are efficient, effective, and directly contribute to the long-term performance and reliability of equipment. Here are concise strategies for a Reliability Engineer:
Understand and Implement Core RCM Principles: Start by thoroughly understanding the fundamental principles of RCM. This includes identifying critical systems/components, understanding their failure modes, and prioritizing maintenance tasks based on risk and operational impact. The Reliabilityweb provides a wealth of resources and case studies on RCM principles.
Leverage Data Analytics: Utilize data analytics to predict equipment failures and optimize maintenance schedules. Predictive maintenance technologies can significantly improve the efficiency of RCM programs. Tools like IBM's Maximo offer advanced analytics for predictive maintenance.
Continuous Training and Education: Ensure that maintenance teams are continuously trained in the latest RCM methodologies and tools. This includes understanding the use of software tools, data analysis techniques, and staying updated with industry best practices. SMRP (Society for Maintenance & Reliability Professionals) provides certification and training resources.
Implement a Continuous Improvement Process: RCM should not be static. Adopt a culture of continuous improvement by regularly reviewing and updating maintenance strategies based on new data, technologies, and feedback from the maintenance team. ASQ (American Society for Quality) offers resources on continuous improvement methodologies like Six Sigma, which can be applied to RCM.
Integrate RCM with EAM/CMMS Systems: Ensure your RCM process is fully integrated with your Enterprise Asset Management (EAM) or Computerized Maintenance Management System (CMMS) for streamlined operations. This integration allows for better tracking, scheduling, and reporting of maintenance activities. Fiix Software is an example of a CMMS that supports RCM strategies.
Focus on Proactive Maintenance: Shift the maintenance strategy from reactive to proactive by focusing on preventive and predictive maintenance. This approach reduces downtime and extends the lifespan of equipment. Mobius Institute offers training and certification in vibration analysis and other predictive maintenance techniques.
Stakeholder Engagement: Engage all stakeholders, including operators, maintenance personnel, and management, in the RCM process. Their involvement ensures buy-in, enhances the understanding of maintenance implications on operations, and fosters a culture of reliability.
By focusing on these strategies, a Reliability Engineer can significantly enhance the efficiency and effectiveness of an RCM program, leading to improved equipment reliability, reduced maintenance costs, and increased operational efficiency.
How to Display RCM (Reliability Centered Maintenance) Skills on Your Resume
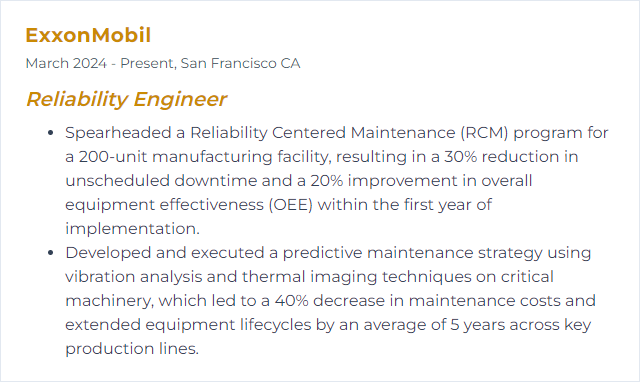
8. Six Sigma
Six Sigma is a data-driven methodology aimed at improving quality by identifying and eliminating defects in processes and products, focusing on variability reduction and process performance enhancement, highly relevant for Reliability Engineers in ensuring consistent and reliable outcomes.
Why It's Important
Six Sigma is important for a Reliability Engineer because it provides a structured, data-driven methodology to identify, analyze, and reduce defects and variability in processes, leading to improved product quality, reliability, and customer satisfaction.
How to Improve Six Sigma Skills
Improving Six Sigma, particularly from a Reliability Engineer's perspective, involves enhancing process efficiency and product reliability through data-driven approaches and continual process optimization. Here are concise steps to achieve this:
Understand the Basics: Gain a solid foundation in Six Sigma methodologies. ASQ provides comprehensive resources on Six Sigma principles.
Master Statistical Tools: Utilize statistical tools like Minitab for data analysis. Training resources are available on the Minitab website.
Implement DMAIC: Focus on the Define, Measure, Analyze, Improve, Control (DMAIC) methodology to systematically improve processes. The iSixSigma website offers detailed insights on DMAIC.
Focus on Reliability: Apply Six Sigma techniques to enhance product reliability. The Reliability Engineering website by ReliaSoft offers tools and software for reliability engineers.
Continuous Learning: Stay updated with the latest trends and techniques in Six Sigma and reliability engineering through professional development courses on platforms like Coursera and LinkedIn Learning.
Engage with Community: Join forums and communities such as the Lean Six Sigma LinkedIn Group to share knowledge and learn from peers.
By focusing on these areas, a Reliability Engineer can significantly contribute to enhancing Six Sigma processes, leading to improved efficiency and product reliability.
How to Display Six Sigma Skills on Your Resume
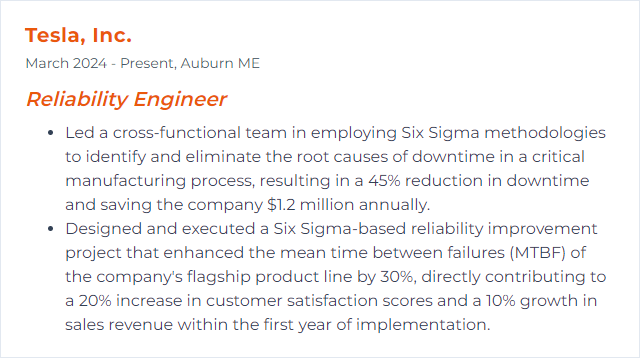
9. ISO 55000
ISO 55000 is an international standard for asset management. It provides a framework for establishing, implementing, maintaining, and improving an asset management system. For a Reliability Engineer, it offers guidelines to ensure assets consistently perform their desired functions, optimizing reliability and availability while minimizing risks and costs throughout the asset's lifecycle.
Why It's Important
ISO 55000 provides a framework for implementing an effective asset management system, focusing on optimizing asset reliability and performance. For a Reliability Engineer, it is crucial as it guides the systematic approach to developing, coordinating, and controlling activities related to assets, thus ensuring their reliability and availability meet the strategic objectives of the organization.
How to Improve ISO 55000 Skills
Improving ISO 55000, especially from a Reliability Engineer's perspective, involves a focused approach toward enhancing asset management systems to meet or exceed the standard's requirements. Here are concise steps to achieve this:
Understand the Standard: Begin with a thorough understanding of ISO 55000 requirements and principles. The ISO website and resources like the Institute of Asset Management offer comprehensive insights.
Gap Analysis: Conduct a gap analysis against ISO 55000 to identify areas of improvement in your current asset management system. Tools and guidelines for gap analysis can be found through professional organizations like SMRP (Society for Maintenance & Reliability Professionals).
Develop an Improvement Plan: Based on the gap analysis, develop a concise improvement plan focusing on areas such as risk management, lifecycle cost analysis, and continuous improvement processes. Resources for planning may be found via Project Management Institute.
Implement Technology Solutions: Leverage technology solutions for asset management, predictive maintenance, and data analytics to enhance decision-making and operational efficiency. Explore solutions from industry leaders and case studies for insights, available through platforms like Reliabilityweb.
Training and Competence Development: Invest in training and competence development for the asset management team on ISO 55000 and best practices in reliability engineering. Check out courses and certifications from The Reliability and Maintainability Center (RMC) at the University of Tennessee, Knoxville.
Monitor, Measure, and Review: Establish KPIs for asset management and reliability. Regularly monitor, measure, and review performance against these KPIs to ensure continuous improvement. Guidance on KPIs and performance measurement can be found through ISO 55000 guidance documents and industry forums.
Engage Stakeholders: Ensure effective communication and engagement with all stakeholders, including maintenance teams, management, and external partners, to align efforts and share best practices.
Continuous Improvement: Adopt a culture of continuous improvement, utilizing feedback loops and innovation to refine asset management processes. Engage with communities and forums, such as Reliabilityweb and SMRP, for the latest trends and insights.
Each step involves leveraging resources, technology, and community knowledge to align with ISO 55000 standards, ultimately enhancing the organization's asset management capabilities.
How to Display ISO 55000 Skills on Your Resume
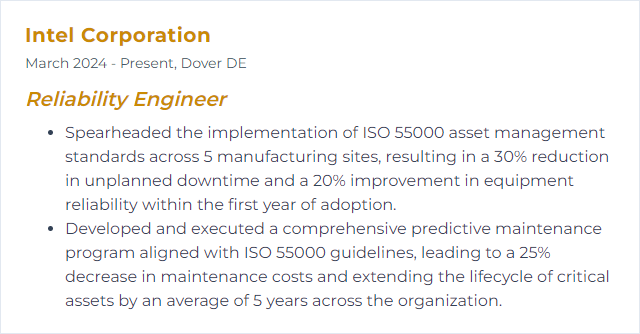
10. Weibull Analysis
Weibull Analysis is a statistical method used by Reliability Engineers for modeling the life data of products to predict failure rates and assess product reliability over time. It helps in understanding how and when a product will fail by fitting the data to a Weibull distribution, enabling the identification of failure patterns and guiding reliability improvement efforts.
Why It's Important
Weibull Analysis is crucial for a Reliability Engineer because it provides a statistical method to analyze life data, identify failure patterns, predict future failures, and guide the improvement of product reliability and maintenance strategies.
How to Improve Weibull Analysis Skills
Improving Weibull Analysis involves enhancing data quality, model selection, and interpretation techniques. Here's a concise guide for a Reliability Engineer:
Data Collection: Ensure comprehensive and accurate failure data collection. Utilize robust data logging and tracking systems to capture all relevant failure instances and conditions. Data Collection Best Practices
Right-Censoring Handling: Properly account for right-censored data, which occurs when an item does not fail within the study period. Use statistical software that can effectively incorporate censored data into the analysis. Handling Censored Data
Model Selection: Choose the right Weibull model (1-parameter, 2-parameter, or 3-parameter) based on the data characteristics. Conduct goodness-of-fit tests to determine the model that best fits your data. Weibull Model Selection
Software Tools: Utilize specialized reliability analysis software like ReliaSoft Weibull++ for more sophisticated analysis, better visualization, and easier interpretation of results. ReliaSoft Weibull++
Continuous Learning: Stay updated with the latest methodologies and software updates in Weibull analysis. Join forums, attend workshops, and read recent publications on reliability engineering. Reliability Engineering Community
Collaboration and Cross-Validation: Work with cross-functional teams to validate assumptions and interpretations. Collaborate with other reliability engineers and statisticians to cross-verify findings and improve analysis robustness.
By focusing on these areas, a Reliability Engineer can significantly enhance the accuracy and usefulness of Weibull Analysis in predicting product life and identifying reliability improvements.
How to Display Weibull Analysis Skills on Your Resume
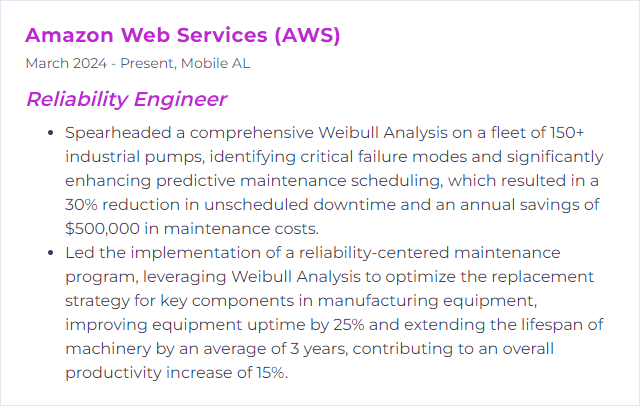
11. Predictive Maintenance
Predictive maintenance is a proactive maintenance strategy that uses data analysis tools and techniques to detect anomalies and predict equipment failures before they occur, allowing for maintenance to be scheduled at a convenient time to prevent unexpected equipment downtime and extend the lifespan of assets.
Why It's Important
Predictive maintenance is crucial for a Reliability Engineer as it helps in forecasting equipment failures and scheduling maintenance activities proactively. This approach minimizes unexpected downtime, reduces maintenance costs, and extends the lifespan of equipment, thereby enhancing overall operational reliability and efficiency.
How to Improve Predictive Maintenance Skills
To improve Predictive Maintenance, a Reliability Engineer should focus on the following steps:
Data Collection and Quality: Ensure the collection of high-quality, relevant data from machinery through sensors and IoT devices. IBM's guide on Predictive Maintenance highlights the importance of data quality and variety.
Real-time Monitoring: Implement real-time monitoring systems to track the performance and health of equipment continuously. National Instruments provides insights into how real-time data can be used effectively.
Advanced Analytics: Use advanced analytics and machine learning algorithms to analyze the collected data. This can help identify patterns and predict potential failures before they occur. Microsoft Azure offers tools that can be used for building predictive models.
Routine Testing and Inspection: Regularly test and inspect equipment to validate the predictions and refine the predictive maintenance models. ASME provides a comprehensive guide on different maintenance types, including predictive maintenance.
Training and Skills Development: Invest in training for the maintenance team to understand and use predictive maintenance tools and technologies effectively. SMRP (Society for Maintenance & Reliability Professionals) offers resources and certifications for professionals.
Review and Optimization: Continuously review and optimize the predictive maintenance program based on feedback and new data to improve accuracy and efficiency. Plant Engineering has articles on strategies for enhancing predictive maintenance.
By focusing on these areas, a Reliability Engineer can significantly improve the effectiveness of a Predictive Maintenance program.
How to Display Predictive Maintenance Skills on Your Resume
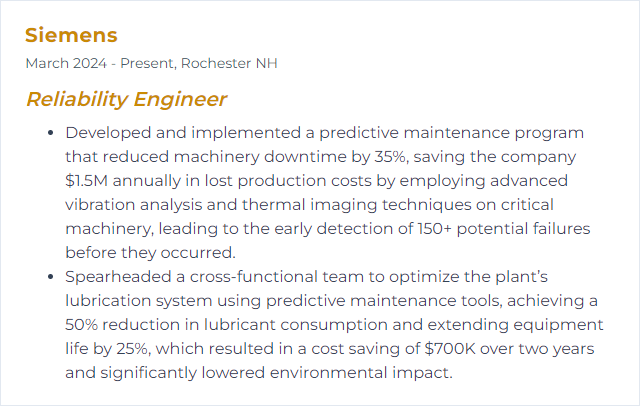
12. SCADA (Supervisory Control and Data Acquisition)
SCADA (Supervisory Control and Data Acquisition) is a system used for monitoring and controlling industrial processes and infrastructure in real time. It collects data from sensors and equipment, allowing a Reliability Engineer to analyze performance, anticipate failures, and ensure efficient, safe operation of facilities and systems.
Why It's Important
SCADA is crucial for a Reliability Engineer as it enables real-time monitoring and control of equipment and processes, enhancing operational reliability, reducing downtime, and facilitating predictive maintenance through data analysis and trend identification.
How to Improve SCADA (Supervisory Control and Data Acquisition) Skills
Improving SCADA systems, especially from a Reliability Engineer's perspective, involves enhancing reliability, security, and efficiency. Here are concise strategies:
Regular Maintenance and Updates: Schedule regular maintenance and ensure software and firmware are up-to-date to prevent malfunctions and security vulnerabilities. National Institute of Standards and Technology
Enhance Security Measures: Implement robust cybersecurity practices including firewalls, intrusion detection systems, and regular security audits to protect against cyber threats. Cybersecurity & Infrastructure Security Agency (CISA) Guidelines
Implement Redundancy: Design systems with redundancy in critical components (e.g., servers, network paths) to ensure continuous operation during failures. ISA-18.2 - Management of Alarm Systems for the Process Industries
Data Analysis and Predictive Maintenance: Use data analytics tools for predictive maintenance, identifying potential issues before they cause system failure. IEEE Xplore
Training and Awareness: Regular training for staff on the latest SCADA technologies, security practices, and response strategies for system anomalies. SANS Institute
Upgrade Legacy Systems: Replace or upgrade outdated components and software to improve efficiency, compatibility, and security. International Society of Automation (ISA)
Network Segmentation: Segment SCADA networks from business networks to minimize the risk of cyber-attacks spreading across networks. NIST Special Publication 800-82
By focusing on these areas, a Reliability Engineer can significantly improve the performance and reliability of SCADA systems.
How to Display SCADA (Supervisory Control and Data Acquisition) Skills on Your Resume
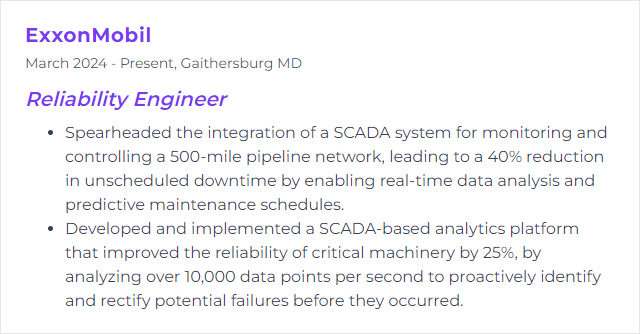