Top 12 Refinery Operator Skills to Put on Your Resume
In the highly specialized and competitive field of refinery operations, showcasing a robust set of skills on your resume can significantly increase your marketability to potential employers. This article outlines the top 12 skills refinery operators should highlight to stand out, ensuring they present a compelling case for their expertise and readiness to excel in this demanding industry.
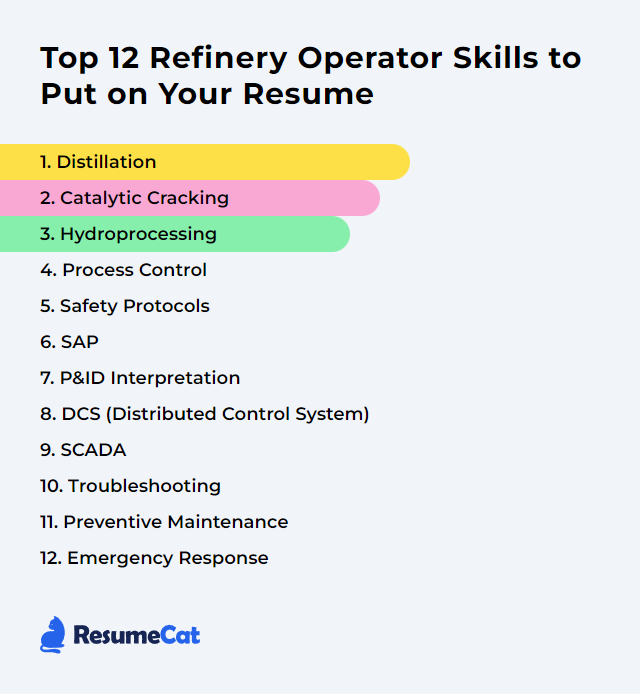
Refinery Operator Skills
- Distillation
- Catalytic Cracking
- Hydroprocessing
- Process Control
- Safety Protocols
- SAP
- P&ID Interpretation
- DCS (Distributed Control System)
- SCADA
- Troubleshooting
- Preventive Maintenance
- Emergency Response
1. Distillation
Distillation is a process used in refineries to separate components of a liquid mixture based on their different boiling points, typically involving heating the mixture and collecting the vapors to condense them back into liquid form.
Why It's Important
Distillation is crucial in a refinery as it separates crude oil into its component fractions based on their boiling points, enabling the production of various petroleum products (like gasoline, diesel, and jet fuel) efficiently and safely, optimizing resource use and meeting market demands.
How to Improve Distillation Skills
To improve distillation in a refinery setting, consider the following concise strategies:
Optimize Feed Quality: Pre-treat feedstock to remove contaminants and ensure consistent quality. Understanding Feed Quality.
Control Heat Management: Precisely control heating and cooling to maintain optimal column operation. Heat Management in Distillation.
Enhance Column Internals: Upgrade trays and packing to increase separation efficiency and capacity. Column Internals Optimization.
Implement Advanced Controls: Use process control systems for real-time adjustments to improve yield and quality. Advanced Process Control.
Regular Maintenance: Schedule and conduct regular inspections and maintenance to avoid unplanned downtimes. Maintenance Best Practices.
Energy Efficiency Measures: Adopt energy-saving technologies and practices to reduce operational costs. Energy Efficiency in Refineries.
Employee Training: Invest in continuous operator training to improve operational efficiency and safety. Operator Training Programs.
Implementing these strategies involves a combination of technical adjustments, process optimization, and personnel development to achieve more efficient, cost-effective, and safe distillation operations.
How to Display Distillation Skills on Your Resume
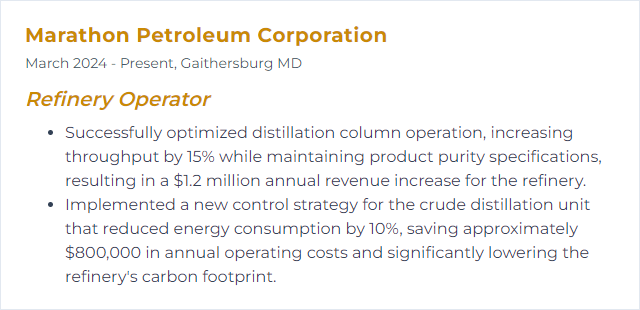
2. Catalytic Cracking
Catalytic cracking is a refinery process where heavy petroleum fractions are broken down into lighter, more valuable products such as gasoline and diesel, using heat and a catalyst to speed up the chemical reactions.
Why It's Important
Catalytic cracking is important in a refinery because it converts heavy, less valuable hydrocarbons into lighter, more valuable products such as gasoline, diesel, and jet fuel, enhancing the overall efficiency and profitability of the refinery operations.
How to Improve Catalytic Cracking Skills
Improving Catalytic Cracking in a refinery setting involves optimizing operational parameters, maintaining catalyst health, and employing advanced technologies. Here are concise recommendations:
Optimize Feed Quality: Ensure the feedstock is within the optimal range for your catalytic cracker. Pre-treat feed to remove contaminants that poison the catalyst. Feed Quality Impact.
Catalyst Management: Regularly regenerate catalysts to maintain activity and selectivity. Consider modern, more efficient catalysts that can better handle impurities and offer higher conversion rates. Catalyst Selection and Management.
Operational Parameters: Fine-tune temperature, pressure, and recycle ratios to maximize yield and product quality. Utilize real-time monitoring and control systems for precise adjustments. Optimizing FCC Operations.
Equipment Upkeep: Regular maintenance and timely upgrades of the FCC unit and related equipment minimize downtime and improve efficiency. Equipment Maintenance.
Incorporate Advanced Technologies: Implement state-of-the-art technologies like real-time analytics, machine learning for predictive maintenance, and advanced control systems for better operational control and decision-making. Advanced Technologies in Refining.
By focusing on these areas, a refinery operator can significantly enhance the performance and efficiency of Catalytic Cracking operations.
How to Display Catalytic Cracking Skills on Your Resume
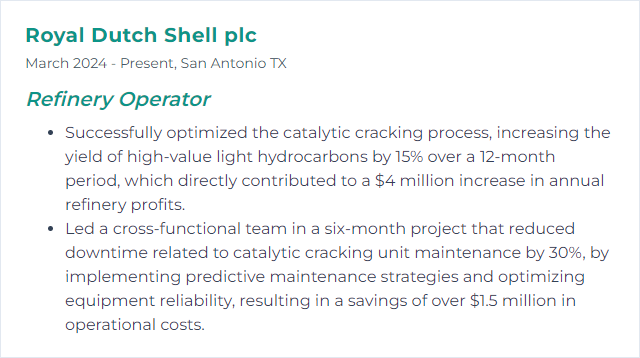
3. Hydroprocessing
Hydroprocessing is a refinery process where hydrogen is used to remove impurities such as sulfur, nitrogen, and metals from crude oil fractions, improving fuel quality and producing cleaner products.
Why It's Important
Hydroprocessing is crucial in refineries to remove impurities (like sulfur, nitrogen, and metals) and to saturate unsaturated hydrocarbons, improving fuel quality, meeting environmental regulations, and enhancing refinery product value and performance.
How to Improve Hydroprocessing Skills
Hydroprocessing, crucial for enhancing fuel quality and compliance with environmental standards, can be improved through focused strategies aimed at optimizing operation and maintaining system integrity. Here's a concise guide for a refinery operator:
Optimize Operating Conditions: Adjust temperature, pressure, and hydrogen flow rate to maximize reaction efficiency and catalyst life. Understanding Hydroprocessing outlines key parameters.
Catalyst Management: Regularly monitor and replace catalysts to ensure high activity and selectivity. Efficient catalyst handling can significantly boost process outcomes. Catalyst Handling in Refineries provides insights into best practices.
Equipment Integrity: Implement routine maintenance and inspections to prevent leaks, fouling, and corrosion, ensuring operational safety and efficiency. Maintenance Strategies offers guidance on maintaining processing equipment.
Process Optimization Software: Utilize advanced software tools for real-time process monitoring and optimization, aiding in decision-making and operational improvements. Process Optimization in Refining highlights technology applications.
Training and Safety: Continuously educate staff on best practices and safety protocols to prevent accidents and enhance operational efficiency. API Training provides industry-specific courses.
By focusing on these areas, refinery operators can enhance hydroprocessing efficiency, extending catalyst life, improving product yield and quality, and ensuring environmental compliance.
How to Display Hydroprocessing Skills on Your Resume
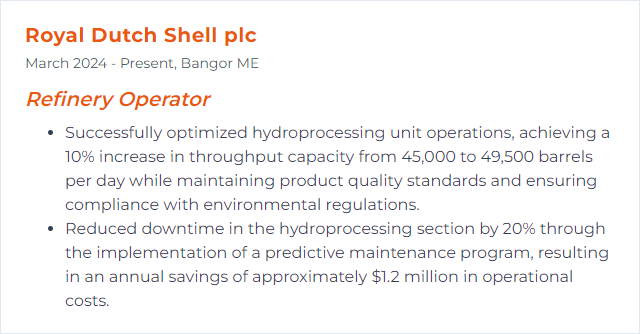
4. Process Control
Process control in the context of a refinery operator refers to the monitoring and adjusting of refinery processes and equipment to ensure efficient and safe production of fuels and other products. It involves managing variables such as temperature, pressure, and flow rates to maintain optimal operating conditions.
Why It's Important
Process control is crucial for a refinery operator as it ensures the efficient, safe, and consistent operation of the refinery processes, optimizing production, reducing waste, and preventing accidents.
How to Improve Process Control Skills
Improving process control in a refinery setting involves optimizing operational efficiency, ensuring product quality, and maintaining safety standards. Here's a concise guide for a refinery operator:
Understand the Basics: Gain a thorough understanding of the principles of process control systems, including PID (Proportional, Integral, Derivative) control. Free resources like Control Guru offer foundational knowledge.
Leverage Technology: Utilize advanced process control (APC) technologies. Tools like Honeywell's Advanced Solutions can optimize refinery operations.
Regular Training: Stay updated with the latest control strategies and tools through regular training. Organizations like ISA (International Society of Automation) offer specialized courses.
Data Analysis: Use data analytics to identify trends and inefficiencies. Platforms like Seeq help analyze and visualize process data for better decision-making.
Preventive Maintenance: Ensure the regular maintenance of control systems to prevent unexpected failures. Guidelines from API (American Petroleum Institute) can help establish maintenance best practices.
Safety Protocols: Adhere strictly to safety protocols and standards. Resources from OSHA (Occupational Safety and Health Administration) provide guidelines for safe refinery operations.
Collaboration and Communication: Foster a culture of open communication and collaboration among operators, engineers, and management to promptly address any process control issues.
By focusing on these areas, refinery operators can significantly improve process control, enhancing both efficiency and safety in operations.
How to Display Process Control Skills on Your Resume
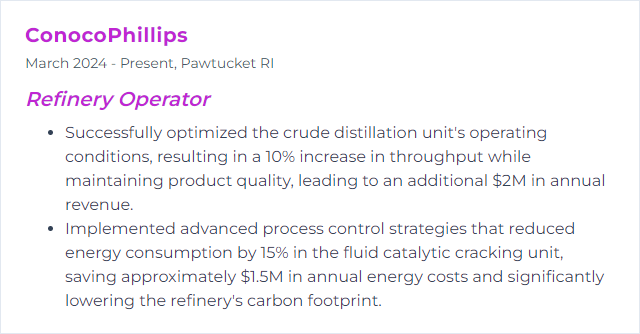
5. Safety Protocols
Safety protocols for a refinery operator are guidelines and procedures designed to prevent accidents, ensure safe operation of equipment, and protect worker health within a refinery environment. These protocols cover personal protective equipment (PPE) usage, emergency response, handling of hazardous materials, and adherence to operational and maintenance safety standards.
Why It's Important
Safety protocols are crucial for refinery operators to prevent accidents, protect health, ensure efficient operations, and comply with regulatory requirements, thereby safeguarding both personnel and the environment.
How to Improve Safety Protocols Skills
To improve safety protocols for a refinery operator, follow these concise steps:
Risk Assessment: Conduct regular and thorough risk assessments to identify potential hazards. Use guidelines from the Occupational Safety and Health Administration (OSHA).
Training and Education: Implement ongoing safety training programs. Resources from the American Petroleum Institute (API) can be beneficial.
Emergency Preparedness: Develop and regularly update emergency response plans. Refer to the National Response Center (NRC) for best practices.
Equipment Maintenance: Ensure regular maintenance and safety checks of all equipment. The American Society of Mechanical Engineers (ASME) provides relevant standards.
Safety Culture: Foster a safety-first culture by encouraging open communication and reporting of hazards without fear of reprisal. OSHA's Safety and Health Program Management Guidelines offer strategies for building such a culture.
Personal Protective Equipment (PPE): Ensure the use of appropriate PPE for all tasks. Guidelines on PPE can be found through OSHA's Personal Protective Equipment.
Regulatory Compliance: Stay updated with local, state, and federal regulations. The Environmental Protection Agency (EPA) provides resources on environmental regulations affecting refineries.
By systematically addressing these areas, refinery operators can significantly improve their safety protocols and minimize risks.
How to Display Safety Protocols Skills on Your Resume
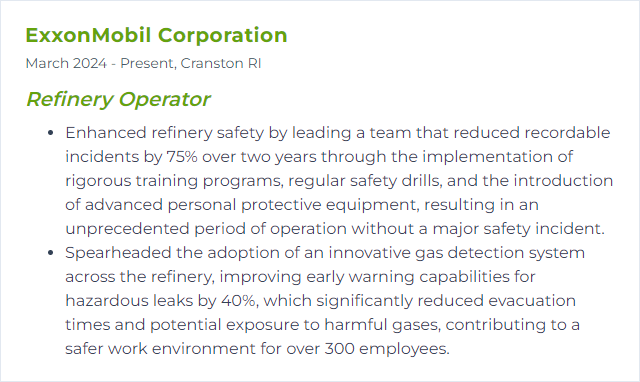
6. SAP
SAP (Systems, Applications, and Products) is a software system designed to manage business operations and customer relations, including inventory, procurement, and maintenance activities, which can help a Refinery Operator streamline and automate the management of refinery processes and resources.
Why It's Important
SAP is important for a Refinery Operator because it facilitates efficient process management, maintenance scheduling, inventory control, and compliance tracking, ensuring safe, reliable, and optimized refinery operations.
How to Improve SAP Skills
Improving SAP (Systems, Applications, and Products in Data Processing) efficiency, especially for roles such as a Refinery Operator, involves optimizing data management, enhancing user skills, and leveraging SAP's features to streamline operations. Here’s a concise guide:
Enhance User Training: Provide tailored training sessions focusing on modules relevant to refinery operations. SAP offers various training resources, which can be found on their official training site.
Customize SAP Interface: Tailor the SAP interface to meet the specific needs of refinery operations. This includes creating custom dashboards that display relevant data for quick decision-making. SAP’s user interface customization options are detailed in their UI customization guide.
Integrate Real-Time Data: Implement IoT (Internet of Things) solutions to feed real-time data from refinery operations into SAP, enabling timely decisions. SAP’s IoT solutions and their integration into SAP systems are covered on their IoT solution page.
Leverage SAP Analytics: Utilize SAP Analytics Cloud to analyze operational data for insights that can lead to efficiency improvements. The tool can help identify bottlenecks and areas for improvement. Explore features on the SAP Analytics Cloud page.
Implement Best Practices: Adopt industry best practices for refinery operations within SAP. SAP’s Best Practices for Chemicals, which can be adapted for refinery operations, offer a starting point and can be found on their industry solution page.
Regular System Audits: Conduct regular audits of your SAP system to ensure it is being used effectively and to identify areas for improvement. SAP offers guidelines for conducting system audits.
Improving SAP for a Refinery Operator revolves around optimizing the system to enhance data visibility, decision-making, and operational efficiency, leveraging SAP’s vast resources, and customizing solutions to meet the specific needs of refinery operations.
How to Display SAP Skills on Your Resume
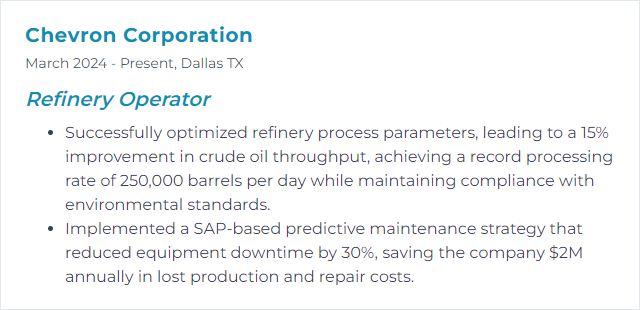
7. P&ID Interpretation
P&ID Interpretation for a refinery operator involves understanding and reading Piping and Instrumentation Diagrams to identify the layout of pipes, instruments, and equipment within the refinery, ensuring safe and efficient operation and troubleshooting of the plant's processes.
Why It's Important
P&ID interpretation is crucial for a Refinery Operator because it ensures the safe and efficient operation of the refinery by enabling the operator to understand the process flow, equipment layout, and safety systems, thus facilitating effective monitoring, control, and troubleshooting of the refining processes.
How to Improve P&ID Interpretation Skills
Improving P&ID (Piping & Instrumentation Diagram) interpretation, especially for a refinery operator, involves several key steps aimed at enhancing understanding and application of these critical documents. Here are concise recommendations:
Familiarize with Symbols: Start by learning the standard symbols used in P&IDs. Resources like ISA-5.1 provide comprehensive guides on instrumentation symbols and identification.
Understand System Layout: Focus on understanding how different components are interconnected within the system. Practice tracing lines and identifying equipment on actual P&IDs of your facility.
Utilize Training Resources: Take advantage of online courses and tutorials. Websites like Coursera and Udemy offer specific courses on P&ID interpretation and related topics.
Hands-On Practice: Apply your knowledge by practicing with real P&IDs in your refinery. Cross-reference the diagrams with physical components in the plant to solidify your understanding.
Engage with Experienced Operators: Learn from seasoned operators and engineers. Their practical insights can provide nuances not covered in manuals or guides.
Continuous Learning: Stay updated with industry standards and new technologies. Resources like Engineering360 and Chemical Engineering Magazine can be valuable.
By focusing on these areas, refinery operators can significantly improve their P&ID interpretation skills, leading to better performance and safety in their roles.
How to Display P&ID Interpretation Skills on Your Resume
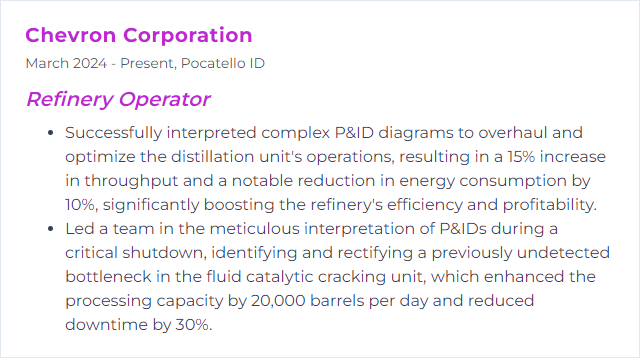
8. DCS (Distributed Control System)
A Distributed Control System (DCS) is a computerized control system used in manufacturing plants and refineries that manages and automates industrial processes. It distributes control functions across multiple interconnected subsystems, ensuring efficient operation, monitoring, and safety of the plant's machinery and processes.
Why It's Important
A Distributed Control System (DCS) is crucial for a refinery operator because it enables centralized monitoring and control of the entire refinery process, ensuring efficient operation, safety, and productivity by providing real-time data and automation capabilities.
How to Improve DCS (Distributed Control System) Skills
Improving a Distributed Control System (DCS) in a refinery setting involves enhancing process control, operational efficiency, and system reliability. Here are concise strategies:
Upgrade Hardware and Software: Periodically update DCS hardware and software to leverage advancements in technology for better performance and features. Yokogawa and Honeywell offer updates and support for their systems.
Optimize Process Control Strategies: Review and fine-tune control loops and algorithms to improve process stability and efficiency. Emerson provides resources for optimizing control strategies.
Enhance Operator Training: Invest in ongoing training and simulation tools to ensure operators can efficiently manage the DCS and respond to scenarios promptly. Siemens offers training solutions for operators.
Implement Advanced Process Control (APC): Utilize APC modules to automate complex control strategies, improving product quality and reducing energy consumption. Schneider Electric provides APC solutions.
Improve Cybersecurity Measures: Secure the DCS from cyber threats with regular software updates, secure network architectures, and employee awareness training. The ISA/IEC 62443 standards provide guidelines for industrial cybersecurity.
Regular System Maintenance: Perform regular maintenance checks and diagnostics to prevent unexpected failures and downtimes. ABB offers maintenance and service options for control systems.
Data Analysis and Optimization: Utilize data analytics tools to analyze operational data for insights into process improvements and efficiency gains. Rockwell Automation offers analytics solutions tailored for industrial operations.
Integrate with Enterprise Systems: Ensure the DCS integrates seamlessly with ERP, MES, and other enterprise systems for better decision-making and operational visibility. SAP provides solutions for integrating business processes.
By focusing on these areas, refinery operators can enhance the functionality, reliability, and efficiency of their DCS, leading to improved process control, reduced operational costs, and higher product quality.
How to Display DCS (Distributed Control System) Skills on Your Resume
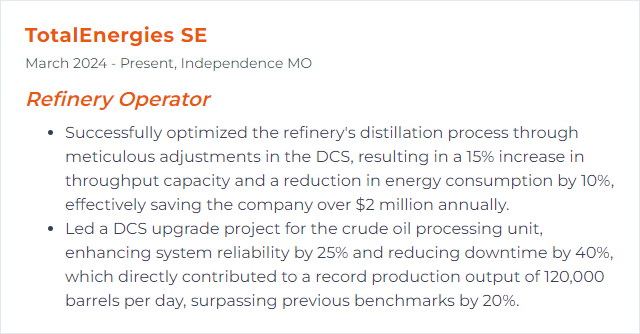
9. SCADA
SCADA (Supervisory Control and Data Acquisition) is a system used in industrial settings like refineries to monitor and control equipment and processes remotely, ensuring efficient and safe operations.
Why It's Important
SCADA (Supervisory Control and Data Acquisition) is crucial for Refinery Operators as it enables real-time monitoring and control of refinery processes, ensuring efficient operation, safety, and quick response to any issues, thus optimizing production and minimizing downtime.
How to Improve SCADA Skills
Improving SCADA systems in a refinery setting involves enhancing data accuracy, system reliability, and operational efficiency. Here are concise strategies:
Upgrade Hardware: Invest in modern, high-performance PLCs and RTUs for faster, more reliable data processing and control. Rockwell Automation offers robust solutions.
Software Updates: Keep SCADA software up-to-date to leverage new features and security patches. Check Wonderware for industry-standard updates.
Enhance Cybersecurity: Implement strong network security practices, including firewalls, intrusion detection systems, and regular security audits. ISA/IEC 62443 standards guide industrial cybersecurity.
Data Analytics Integration: Use advanced data analytics tools to predict equipment failures and optimize operations. Splunk offers powerful analytics for industrial data.
User Training: Regularly train operators on the latest SCADA features and best practices to improve system efficiency and response times. ISA Training provides comprehensive courses for operators and engineers.
Redundancy and Failover: Implement redundant systems and automatic failover to ensure continuous operation during hardware or software failures. Schneider Electric systems support high availability configurations.
By focusing on these areas, refinery operators can significantly improve SCADA performance, leading to enhanced operational efficiency and safety.
How to Display SCADA Skills on Your Resume
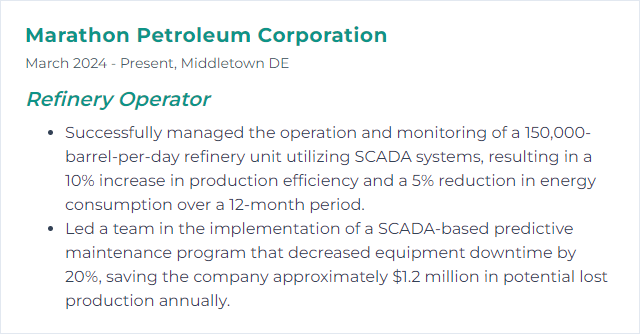
10. Troubleshooting
Troubleshooting, in the context of a refinery operator, is the systematic process of identifying, diagnosing, and resolving problems or malfunctions within refinery operations and equipment to ensure optimal performance and safety.
Why It's Important
Troubleshooting is crucial for a refinery operator as it ensures the efficient and safe operation of the refinery processes, minimizes downtime, prevents accidents, and protects both personnel and the environment from hazards associated with malfunctions or process deviations.
How to Improve Troubleshooting Skills
Improving troubleshooting skills, especially for a Refinery Operator, involves a blend of technical knowledge, experience, and a systematic approach. Here are concise steps to enhance your troubleshooting abilities:
Understand Systems: Gain a deep understanding of refinery processes and systems. Study materials and online courses can help broaden your knowledge base.
Learn from Experience: Document and review past troubleshooting scenarios. Websites like Chemical Processing offer real-world case studies.
Systematic Approach: Adopt a methodical approach to troubleshooting, such as the Kepner-Tregoe method, which helps in identifying the root cause efficiently.
Use Technology: Leverage technology like simulation software to understand complex scenarios and predict outcomes.
Continuous Learning: Stay updated with the latest trends and technologies in refinery operations through industry publications and workshops.
By integrating these strategies, you can enhance your problem-solving skills and become more effective in troubleshooting refinery operations.
How to Display Troubleshooting Skills on Your Resume
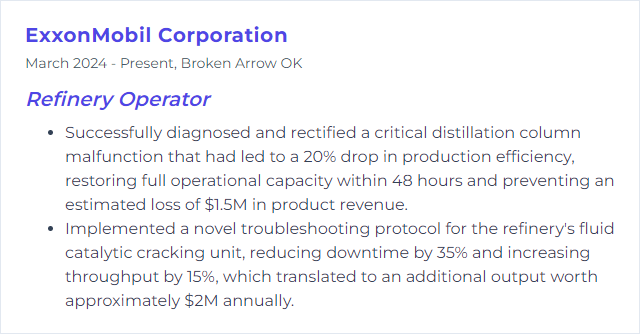
11. Preventive Maintenance
Preventive Maintenance in the context of a Refinery Operator involves routine inspection, servicing, and upkeep of equipment and facilities to prevent breakdowns, ensure safety, and maintain efficient operations.
Why It's Important
Preventive maintenance is crucial for a refinery operator as it ensures the continuous, safe, and efficient operation of the refinery by minimizing unexpected equipment failures, reducing downtime, and extending the lifespan of machinery, thereby safeguarding production output and reducing operational costs.
How to Improve Preventive Maintenance Skills
Improving preventive maintenance in a refinery setting involves several key steps aimed at enhancing operational efficiency, safety, and equipment longevity. Here's a concise guide:
Schedule Optimization: Use maintenance scheduling software to ensure maintenance activities are planned during least disruptive times, improving overall productivity.
Condition Monitoring: Implement condition-based monitoring tools to track equipment performance in real-time, allowing for timely maintenance before failures occur.
Training and Skills Development: Invest in continuous training for maintenance staff to keep them updated on the latest techniques and technologies in refinery operation and maintenance.
Inventory Management: Use inventory management systems to ensure essential spare parts are always available, reducing downtime during maintenance activities.
Root Cause Analysis: After any equipment failure, perform a root cause analysis to understand the underlying issues, preventing future occurrences by addressing the core problem.
Safety and Compliance: Stay updated with industry safety standards and ensure all maintenance activities comply with these guidelines to prevent accidents and regulatory issues.
By focusing on these areas, refinery operators can significantly improve the effectiveness of their preventive maintenance programs, leading to safer, more reliable, and cost-effective operations.
How to Display Preventive Maintenance Skills on Your Resume
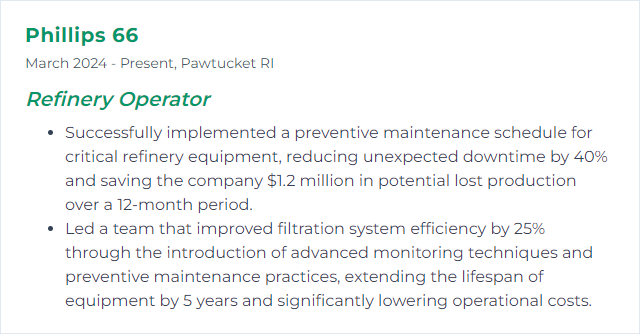
12. Emergency Response
Emergency Response in the context of a Refinery Operator involves the immediate and coordinated actions taken to address unexpected events or situations that pose a threat to the facility, employees, or the environment, ensuring safety and minimizing impact through rapid containment, control, and remediation of hazards.
Why It's Important
Emergency response is crucial for a refinery operator to ensure immediate and effective action against incidents such as fires, chemical spills, or explosions, minimizing harm to people, property, and the environment.
How to Improve Emergency Response Skills
To improve Emergency Response for a Refinery Operator, consider the following steps:
Training and Exercises: Regularly conduct emergency response training and simulation exercises for all staff to enhance preparedness and response skills.
Communication Systems: Implement and maintain robust communication systems that ensure clear, concise, and quick information flow during emergencies.
Incident Command System (ICS): Adopt the Incident Command System to provide a standardized approach to the command, control, and coordination of emergency response.
Emergency Response Plan (ERP): Develop and regularly update a comprehensive Emergency Response Plan that includes specific procedures for various types of incidents, including coordination with local emergency services.
Technology and Equipment: Invest in the latest emergency response technologies and equipment to enhance effectiveness in dealing with incidents.
Review and Improve: Conduct thorough debriefings and reviews after exercises or actual incidents to identify lessons learned and areas for improvement.
By focusing on these key areas, a Refinery Operator can significantly improve their emergency response capabilities, ensuring safety and minimizing the impact of any emergency situation.
How to Display Emergency Response Skills on Your Resume
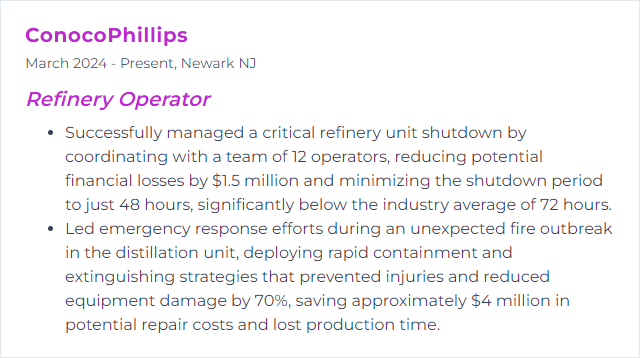