Top 12 Receiving Manager Skills to Put on Your Resume
In today's competitive job market, distinguishing yourself as a top candidate for a receiving manager position is crucial, and one effective way to do so is by showcasing a robust set of skills on your resume. Highlighting key receiving manager skills can demonstrate your ability to efficiently manage warehouse operations, optimize inventory control, and lead teams, making you stand out to potential employers.
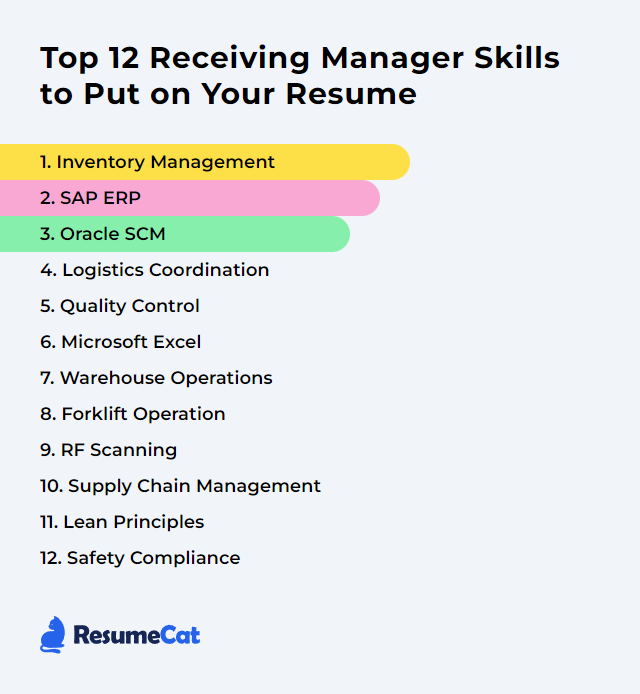
Receiving Manager Skills
- Inventory Management
- SAP ERP
- Oracle SCM
- Logistics Coordination
- Quality Control
- Microsoft Excel
- Warehouse Operations
- Forklift Operation
- RF Scanning
- Supply Chain Management
- Lean Principles
- Safety Compliance
1. Inventory Management
Inventory management, in the context of a Receiving Manager, involves overseeing the reception, storage, and distribution of stock or materials to ensure accurate quantity, location, and availability for ongoing operations or sales.
Why It's Important
Inventory management is crucial for a Receiving Manager as it ensures the accurate tracking and storage of incoming goods, optimizes space utilization, minimizes overstocking or stockouts, and improves the efficiency of receiving operations, ultimately supporting timely order fulfillment and customer satisfaction.
How to Improve Inventory Management Skills
Improving inventory management, especially for a Receiving Manager, involves a few key strategies. Implementing these effectively can streamline operations, reduce costs, and enhance efficiency:
Leverage Technology: Use inventory management software to track stock levels, orders, and deliveries in real-time. QuickBooks and NetSuite are popular options.
Regular Audits: Conduct regular inventory audits to ensure the accuracy of your records. This can be done through physical counts, spot checking, or using a cycle count approach.
Supplier Communication: Maintain clear and open communication with suppliers. This helps in managing lead times, resolving discrepancies quickly, and adjusting to demand changes. Harvard Business Review discusses the importance of this in depth.
Just-In-Time (JIT) Inventory: Adopt a JIT inventory system to minimize holding costs and reduce waste by receiving goods only as they are needed. This requires precise planning and forecasting. Investopedia offers a clear explanation of JIT.
Employee Training: Ensure all staff, especially those handling inventory, are properly trained on best practices, software use, and the importance of accuracy in inventory management.
KPI Monitoring: Set Key Performance Indicators (KPIs) such as stock turnover rates, order accuracy, and backorder rates to monitor performance and identify areas for improvement. The Balance SMB provides a list of common inventory management KPIs.
Implementing these strategies requires commitment and may involve overhauling existing procedures, but the payoff in improved efficiency, reduced costs, and better customer satisfaction can be significant.
How to Display Inventory Management Skills on Your Resume
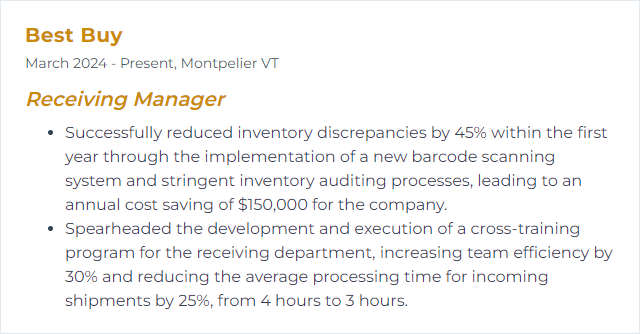
2. SAP ERP
SAP ERP is an enterprise resource planning software that integrates key business functions, streamlining processes like inventory management, order processing, and financials, aiding Receiving Managers in efficiently managing and tracking incoming goods and supplier relationships.
Why It's Important
SAP ERP is important for a Receiving Manager as it streamlines and automates the receiving process, enhances inventory management, improves data accuracy, and facilitates real-time tracking of shipments and stock levels, leading to more efficient operations and decision-making.
How to Improve SAP ERP Skills
Improving SAP ERP for a Receiving Manager involves optimizing system features to streamline receiving processes, enhance data accuracy, and improve decision-making. Here's a concise guide:
Automate Data Entry: Implement barcode scanning and RFID technologies to automate the capture of goods received. This reduces manual input errors and speeds up the process. SAP Extended Warehouse Management integrates seamlessly for this purpose.
Customize Workflows: Tailor SAP workflows to match your specific receiving processes. This ensures that the system supports your operational needs efficiently. Utilize the SAP Business Workflow to customize workflows.
Enhance Reporting: Use SAP's reporting tools to create real-time dashboards or reports that provide insights into receiving operations, inventory levels, and supplier performance. The SAP Analytics Cloud offers advanced analytics capabilities.
Integrate Quality Management (QM): Link the SAP QM module to the receiving process to automatically trigger quality checks for incoming goods, ensuring compliance with standards. Learn more about SAP QM.
Implement Advanced Shipping Notification (ASN): Encourage suppliers to send ASNs through SAP. This prepares the receiving department in advance for what to expect, streamlining the receiving process. SAP Supplier Relationship Management supports ASN functionalities.
Train and Support Staff: Regularly train staff on SAP ERP features and updates to ensure they can leverage the system effectively. SAP offers various training and certification programs.
Leverage Mobile Solutions: Utilize SAP's mobile solutions to enable staff to process receipts and access information on the go. SAP Fiori provides a user-friendly mobile interface for SAP applications.
By focusing on these areas, Receiving Managers can significantly improve the efficiency and accuracy of their SAP ERP systems, leading to better inventory management and operational effectiveness.
How to Display SAP ERP Skills on Your Resume
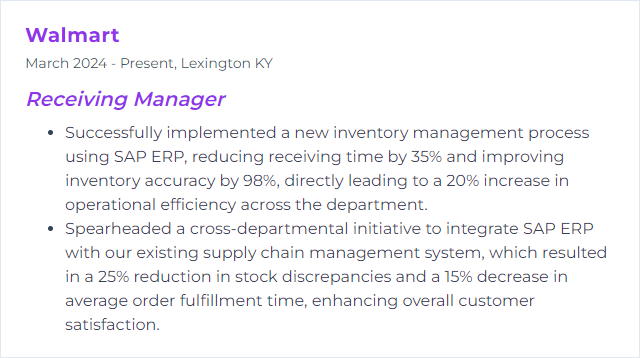
3. Oracle SCM
Oracle SCM (Supply Chain Management) is a comprehensive suite of applications designed to manage and optimize supply chain processes, including procurement, inventory, and order management. For a Receiving Manager, it facilitates the efficient handling of received goods, ensuring accurate tracking, quality control, and timely availability of inventory for production or sales.
Why It's Important
Oracle SCM (Supply Chain Management) is important for a Receiving Manager because it streamlines and automates the receiving process, enhances inventory accuracy, improves supplier collaboration, and accelerates decision-making through real-time data, ensuring efficient and effective management of the supply chain.
How to Improve Oracle SCM Skills
Improving Oracle SCM, specifically for a Receiving Manager, involves optimizing processes, leveraging technology, and enhancing data accuracy. Here’s a concise guide:
Streamline Receiving Processes: Simplify receiving operations by automating data entry and leveraging mobile solutions for real-time updates. Oracle Mobile SCM Solutions can enhance efficiency.
Implement Advanced Shipment Notices (ASN): Use ASNs to prepare for incoming goods, improving dock scheduling and reducing receiving times. Oracle's ASN capabilities facilitate better planning.
Enhance Data Accuracy: Utilize Oracle SCM’s barcode and RFID scanning capabilities to improve data accuracy, reducing manual errors. Oracle Inventory Management supports these technologies.
Optimize Inventory Management: Leverage Oracle SCM Cloud’s inventory optimization tools to maintain optimal inventory levels, reducing carrying costs and improving space utilization. Oracle Inventory Optimization offers advanced features.
Upgrade Training and Support: Ensure your team is well-trained on Oracle SCM updates and best practices. Oracle’s Learning Subscriptions provide ongoing training opportunities.
Leverage Analytics for Continuous Improvement: Utilize Oracle SCM Cloud analytics to monitor performance, identify bottlenecks, and drive continuous improvement. Oracle SCM Analytics can provide actionable insights.
By focusing on these areas, a Receiving Manager can significantly improve Oracle SCM effectiveness, leading to streamlined operations, cost savings, and enhanced productivity.
How to Display Oracle SCM Skills on Your Resume
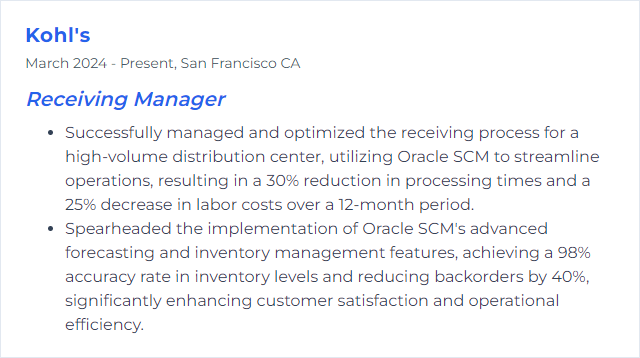
4. Logistics Coordination
Logistics Coordination involves managing and overseeing the supply chain operations to ensure the efficient and timely delivery and reception of goods. For a Receiving Manager, it specifically entails organizing the receipt of products, coordinating with suppliers and transportation services, and ensuring the smooth unloading, inspection, and storage of goods in accordance with company policies and schedules.
Why It's Important
Logistics coordination is crucial for a Receiving Manager as it ensures the timely and efficient arrival of goods, optimizes inventory management, minimizes delays, and enhances customer satisfaction by maintaining product availability.
How to Improve Logistics Coordination Skills
To improve Logistics Coordination as a Receiving Manager, follow these concise steps:
Streamline Communication: Establish clear, direct communication channels with suppliers and transporters. Utilize tools like Slack for real-time messaging.
Implement Technology: Adopt logistics management software, such as ShipBob or Logi-Sys, to automate and optimize operations.
Enhance Visibility: Use tracking systems like Track-POD to monitor shipments in real-time, ensuring timely updates and adjustments.
Optimize Inventory Management: Apply principles of lean inventory and use systems like Fishbowl Inventory to reduce excess and improve order accuracy.
Develop Strong Relationships: Foster positive relationships with all stakeholders through regular feedback and collaboration.
Continuous Improvement: Regularly review and adapt processes based on performance data. Tools like Tableau can help analyze logistics data for insights.
Training and Development: Ensure your team is well-trained on latest logistics trends and technologies through platforms like LinkedIn Learning.
By focusing on these areas, a Receiving Manager can significantly enhance logistics coordination, leading to more efficient and effective operations.
How to Display Logistics Coordination Skills on Your Resume
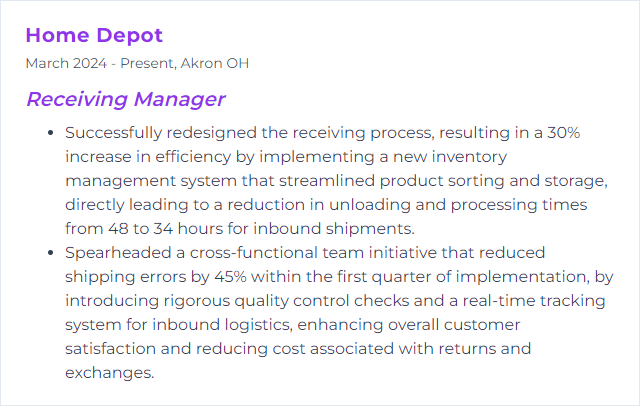
5. Quality Control
Quality Control (QC) is a process used by a Receiving Manager to ensure that all received goods meet the company's standards for quality, specifications, and functionality, aiming to identify and address defects or discrepancies before these goods are accepted and used in operations.
Why It's Important
Quality Control is crucial for a Receiving Manager as it ensures that incoming goods meet the required standards and specifications, preventing defective or substandard materials from entering the production process, reducing waste, and safeguarding customer satisfaction.
How to Improve Quality Control Skills
Improving Quality Control (QC) for a Receiving Manager involves several key steps focused on enhancing the accuracy and efficiency of inspecting, accepting, or rejecting incoming goods. Here’s a concise guide:
Develop Clear Standards: Establish specific quality standards for all incoming materials. These should be based on industry benchmarks and tailored to your specific needs.
Supplier Collaboration: Work closely with suppliers to ensure they understand your quality requirements. Regular communication can help mitigate issues before they arise.
Implement Inspection Protocols: Develop a rigorous inspection protocol that includes checklists and quality control measures for all received goods. This could involve sampling, full inspections, or a combination of both depending on the item and supplier history.
Leverage Technology: Utilize quality management software that can help streamline the inspection process, maintain records, and analyze supplier performance over time.
Train Your Team: Ensure all team members are trained on QC standards, inspection techniques, and how to handle non-conforming goods. Continuous education is key to adapting to new quality challenges.
Continuous Improvement: Adopt a continuous improvement mindset, regularly reviewing and adjusting QC processes based on performance data, feedback, and evolving standards.
Feedback Loop: Establish a robust feedback loop with suppliers, providing them with detailed reports on issues and working collaboratively on corrective actions to prevent recurrence.
By following these steps, a Receiving Manager can significantly improve the quality control process, ensuring that only products that meet or exceed the set standards are accepted, thereby reducing waste and improving customer satisfaction.
How to Display Quality Control Skills on Your Resume
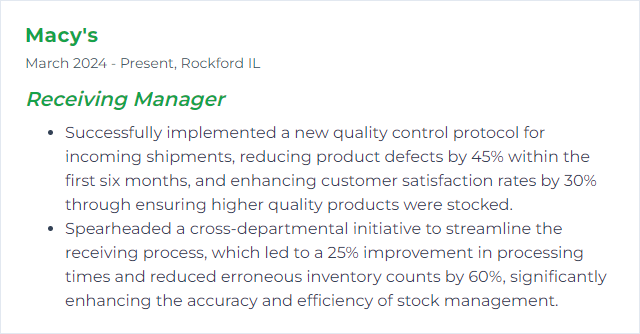
6. Microsoft Excel
Microsoft Excel is a spreadsheet program used for data organization, analysis, and reporting, facilitating inventory tracking, order management, and financial planning for a Receiving Manager.
Why It's Important
Microsoft Excel is crucial for a Receiving Manager as it enables efficient tracking of inventory, analysis of supply chain data, and the creation of detailed reports, thereby optimizing stock management and enhancing operational decisions.
How to Improve Microsoft Excel Skills
To improve Microsoft Excel for a Receiving Manager, focus on mastering specific functionalities relevant to inventory management, data analysis, and report generation:
Learn Advanced Formulas: Deepen your understanding of formulas critical for inventory tracking, such as
VLOOKUP
,INDEX+MATCH
, andSUMIFS
. ExcelJet offers concise explanations and examples.Utilize PivotTables: PivotTables can efficiently summarize, analyze, explore, and present your inventory data. Explore Excel's PivotTable guide for a comprehensive tutorial.
Implement Data Validation: Use data validation to maintain data integrity in your inventory records. Learn how to set it up from Microsoft’s guide.
Automate with Macros: Automate repetitive tasks, like daily reports or inventory updates, by creating macros. Start with Microsoft’s introduction to macros.
Explore Power Query: Use Power Query to connect, combine, and refine data sources to meet your inventory management needs. Excel’s Power Query overview provides a solid starting point.
Master Conditional Formatting: Highlight critical inventory levels, due dates, or anomalies using conditional formatting. Excel’s guide helps you get started.
Integrate with External Data Sources: Connect Excel to external databases or systems (e.g., ERP software) for real-time data updates. Explore Microsoft’s external data connections feature.
Keep Learning: Continuously update your Excel skills and stay informed about new features. Websites like Excel Easy offer free tutorials for all levels.
By focusing on these areas, a Receiving Manager can significantly enhance their efficiency and accuracy in managing inventory and reporting through Microsoft Excel.
How to Display Microsoft Excel Skills on Your Resume
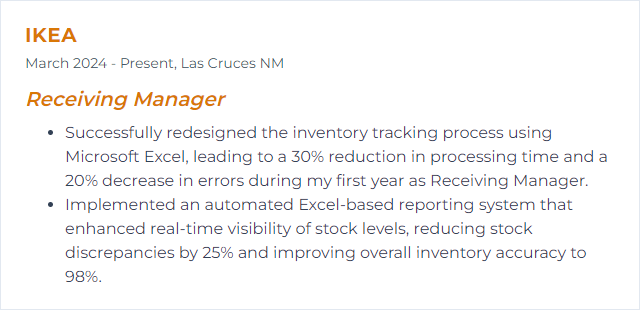
7. Warehouse Operations
Warehouse operations encompass the activities involved in the receipt, storage, and movement of goods in a warehouse to ensure efficient and effective inventory management and product distribution. For a Receiving Manager, this specifically includes overseeing the receipt of goods, verifying shipments, coordinating unloading and storage, and ensuring accurate documentation and inventory control upon goods' arrival.
Why It's Important
Warehouse operations are crucial for ensuring the efficient and accurate receipt, storage, and dispatch of goods, directly impacting inventory management, order fulfillment speed, and customer satisfaction. For a Receiving Manager, this means maintaining streamlined operations is vital for minimizing errors, reducing costs, and enhancing the overall productivity of the supply chain.
How to Improve Warehouse Operations Skills
Improving warehouse operations, especially from the perspective of a Receiving Manager, involves focusing on efficiency, accuracy, and safety. Here are concise strategies:
Implement an Efficient Receiving Process: Streamline the receiving process by using technology such as a Warehouse Management System (WMS) that can help track inventory in real-time and reduce errors.
Optimize Layout and Organization: Ensure the warehouse layout allows for smooth flow of goods. Use racking systems that maximize space and keep frequently accessed items easily accessible.
Standardize Operations: Develop and enforce standard operating procedures (SOPs) for receiving goods, including inspection, documentation, and storage processes.
Invest in Training: Regularly train staff on best practices, safety, and use of technology. Websites like LinkedIn Learning offer courses on warehouse management and operations.
Focus on Safety: Implement strict safety guidelines and conduct regular safety audits. Resources like OSHA’s guidelines can help in maintaining a safe work environment.
Adopt Lean Principles: Reduce waste and improve efficiency by adopting lean warehouse operations principles, focusing on processes that add value and eliminating those that don’t.
Leverage Technology for Inventory Management: Use RFID tags and barcode scanners to improve accuracy and speed in inventory management. Solutions like Zebra Technologies can provide the necessary tools.
Continuous Improvement: Regularly review processes and solicit feedback from staff for continuous improvement. Tools like Six Sigma can offer methodologies for process improvement.
By focusing on these areas, a Receiving Manager can significantly improve warehouse operations, leading to increased productivity, reduced costs, and enhanced employee satisfaction.
How to Display Warehouse Operations Skills on Your Resume
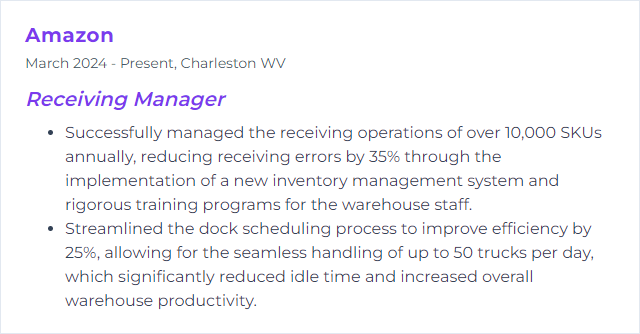
8. Forklift Operation
Forklift operation involves the use of a powered industrial truck to lift, move, and stack materials. For a Receiving Manager, it is crucial for efficiently handling incoming goods, organizing stock, and ensuring a safe and orderly warehouse environment.
Why It's Important
Forklift operation is crucial for a Receiving Manager as it ensures efficient, safe handling and storage of goods, significantly enhancing productivity and minimizing the risk of damage to inventory and injury to staff.
How to Improve Forklift Operation Skills
Improving forklift operation, especially from the perspective of a Receiving Manager, involves enhancing safety, efficiency, and operator competency. Here’s a concise guide:
Safety First: Implement and enforce strict safety protocols based on OSHA’s guidelines. Regular safety training and meetings can significantly reduce accidents.
Regular Maintenance: Ensure forklifts are in optimal working condition through routine checks and maintenance. A well-maintained forklift is more efficient and safer to operate. Refer to the manufacturer’s maintenance schedule for specifics.
Operator Training: Invest in comprehensive training programs for operators, focusing on both practical and theoretical knowledge. CertifyMe.net offers resources for certification and training.
Efficiency in Operations: Utilize technology such as Warehouse Management Systems (WMS) to streamline operations, optimize forklift routes, and manage inventory effectively. Oracle's WMS is an example of such technology.
Ergonomics and Comfort: Enhance operator comfort by selecting forklifts with ergonomic features. Comfortable operators are more productive and less prone to errors. Crown Equipment provides ergonomically designed forklifts.
Regular Feedback and Communication: Encourage open communication between operators and management to identify areas for improvement. Regular feedback sessions can help in addressing concerns promptly.
Performance Metrics: Establish clear performance metrics to monitor efficiency, safety, and productivity. Tools like Telematics systems can provide valuable data for analysis and improvement.
Implementing these strategies can significantly improve forklift operations within the receiving department, ensuring safety, efficiency, and productivity.
How to Display Forklift Operation Skills on Your Resume
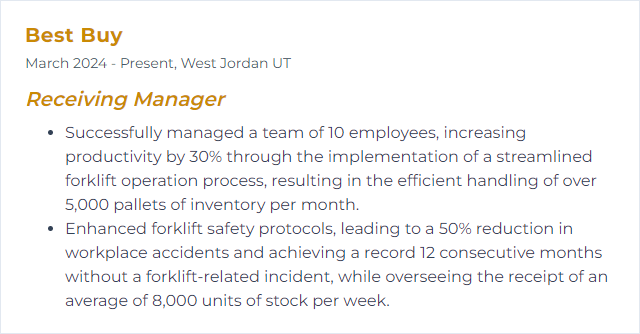
9. RF Scanning
RF Scanning, in the context of a Receiving Manager, refers to the use of Radio Frequency scanners to electronically capture and track data on incoming goods. This process streamlines inventory management, improves accuracy, and speeds up the receiving process by instantly updating the warehouse management system with information about the received items.
Why It's Important
RF scanning is crucial for a Receiving Manager as it enables accurate, efficient tracking and management of inventory, ensuring timely updates and reducing errors in stock levels, which is essential for maintaining operational efficiency and customer satisfaction.
How to Improve RF Scanning Skills
To improve RF (Radio Frequency) scanning, a Receiving Manager can implement the following strategies:
- Training: Ensure all staff are properly trained on RF scanner use, focusing on scanning techniques and device care.
- Equipment Maintenance: Regularly maintain and update RF equipment to ensure optimal performance.
- Process Optimization: Review and optimize scanning processes for efficiency, possibly incorporating task interleaving or zone picking.
- Technology Upgrade: Consider upgrading to more advanced RF scanners with better ergonomics and battery life.
- Quality Control: Implement a quality control step to validate scanning accuracy, reducing errors and rework.
- Feedback System: Establish a feedback mechanism for employees to report issues or suggest improvements related to RF scanning.
By focusing on these areas, a Receiving Manager can enhance the efficiency and accuracy of RF scanning operations in the warehouse.
How to Display RF Scanning Skills on Your Resume
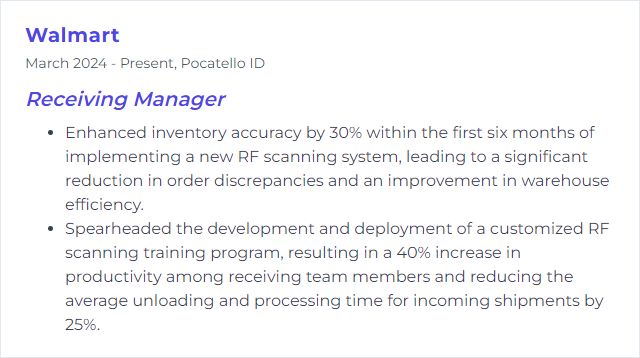
10. Supply Chain Management
Supply Chain Management (SCM) is the coordination and management of all activities involved in sourcing, procuring, producing, and delivering goods and services. For a Receiving Manager, SCM focuses on efficiently receiving, verifying, and storing incoming goods and materials to ensure timely availability for production or sales.
Why It's Important
Supply Chain Management is crucial for a Receiving Manager as it ensures the efficient and timely delivery of goods, reduces costs by optimizing inventory levels, and enhances customer satisfaction through the consistent availability of products. This management facilitates better planning, forecasting, and coordination with suppliers, vital for maintaining operational flow and meeting business objectives.
How to Improve Supply Chain Management Skills
Improving Supply Chain Management, especially from the perspective of a Receiving Manager, involves a strategic approach to optimize operations, enhance communication, and leverage technology. Here are concise strategies:
Streamline Processes: Simplify receiving procedures to minimize errors and delays. Implement standardized protocols for handling shipments and returns. Council of Supply Chain Management Professionals (CSCMP) provides resources and case studies on best practices.
Enhance Supplier Relationships: Build strong, collaborative relationships with suppliers to improve reliability and quality of deliveries. Regular communication and feedback can lead to improvements and more favorable terms. Institute for Supply Management (ISM) offers insights on supplier relationship management.
Leverage Technology: Adopt advanced technologies like Warehouse Management Systems (WMS) and Supply Chain Management (SCM) software to automate processes, improve accuracy, and gain real-time visibility into inventory and shipments. Gartner provides market-leading research on SCM technologies.
Implement Key Performance Indicators (KPIs): Track performance through KPIs to identify areas for improvement. Metrics such as receiving efficiency, accuracy, and supplier performance can guide optimization efforts. APICS (now part of ASCM) is a great resource for learning about supply chain metrics and benchmarking.
Continuous Improvement: Encourage a culture of continuous improvement through regular training, review processes, and adopting industry best practices. Engage teams in problem-solving and process optimization initiatives. Lean Enterprise Institute offers resources on lean principles and continuous improvement strategies.
By focusing on these areas, a Receiving Manager can significantly improve supply chain operations, enhancing efficiency, reducing costs, and improving supplier and customer relationships.
How to Display Supply Chain Management Skills on Your Resume
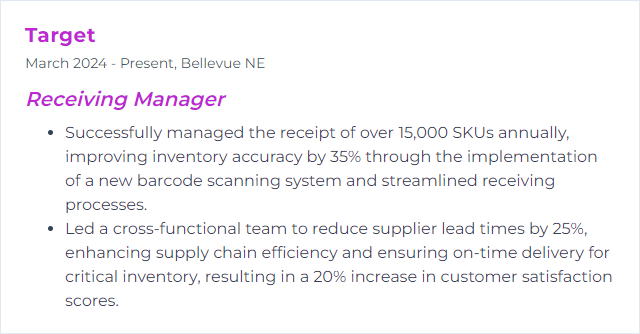
11. Lean Principles
Lean Principles focus on maximizing customer value while minimizing waste. For a Receiving Manager, this means ensuring that goods are received, processed, and moved through the system as efficiently as possible, reducing delays, excess inventory, and unnecessary steps to improve overall effectiveness and reduce costs.
Why It's Important
Lean principles are important for a Receiving Manager because they streamline processes, reduce waste, improve efficiency, and enhance quality, leading to faster turnaround times, cost savings, and higher customer satisfaction.
How to Improve Lean Principles Skills
To improve Lean Principles as a Receiving Manager, follow these concise steps:
Value Stream Mapping: Identify and map out all steps in the receiving process to visualize waste and areas for improvement. (Lean Enterprise Institute)
Continuous Improvement (Kaizen): Implement a culture of continuous small improvements, encouraging feedback and suggestions from all team members. (ASQ - Kaizen)
Standardize Work: Create standard operating procedures for receiving tasks to ensure consistency, efficiency, and quality. (Lean Manufacturing Tools)
Pull Systems (Kanban): Use Kanban or pull systems to manage inventory and signal when new stock is needed, reducing excess inventory. (Planview)
Root Cause Analysis: When problems occur, use tools like the 5 Whys to identify and address the root cause, preventing recurrence. (MindTools)
Empower Teams: Empower your team to make decisions and improvements in their work area. This increases engagement and innovation. (Lean Leadership Way Institute)
Visual Management: Implement visual tools and displays to make the flow of materials and information transparent and accessible to all team members. (Lean Smarts)
Lean Training and Education: Invest in continuous lean training and education for yourself and your team to deepen understanding and skills. (Gemba Academy)
By focusing on these steps, a Receiving Manager can significantly improve efficiency, reduce waste, and contribute to a leaner organization.
How to Display Lean Principles Skills on Your Resume

12. Safety Compliance
Safety compliance, for a Receiving Manager, involves ensuring all operations, equipment, and procedures in the receiving area meet established health and safety regulations and standards to prevent accidents and injuries.
Why It's Important
Safety compliance is crucial for a Receiving Manager because it ensures a safe working environment, minimizes the risk of accidents and injuries, and protects the company from legal issues and financial losses.
How to Improve Safety Compliance Skills
Improving safety compliance, especially for a Receiving Manager, involves a multi-faceted approach focusing on education, environment, and enforcement. Here's a concise guide:
Educate and Train: Ensure all team members, including temporary staff, are regularly trained on the latest safety protocols and equipment handling. Tailor training sessions to address common safety risks encountered in the receiving area. OSHA’s Training Services offers resources and guidelines for workplace safety training.
Implement Safety Protocols: Develop and enforce clear safety procedures for receiving operations. This includes safe lifting techniques, proper use of equipment, and handling hazardous materials. The National Safety Council provides guidelines on various workplace safety topics.
Regular Safety Audits: Conduct frequent safety inspections to identify and mitigate risks. Use checklists to ensure compliance with safety standards and protocols. SafetyCulture offers digital checklists to streamline this process.
Foster a Safety Culture: Encourage an environment where safety is a shared responsibility. Promote open communication, allowing team members to report unsafe conditions without fear of reprisal. NIOSH’s Safety and Health Management Systems can guide creating a positive safety culture.
Stay Updated: Keep abreast of new safety regulations and industry best practices. Regulatory bodies like OSHA provide updates and resources to help maintain compliance.
Leverage Technology: Utilize safety management software to track incidents, manage documentation, and analyze data to prevent future accidents. Tools like iAuditor by SafetyCulture can help streamline these processes.
By focusing on these areas, a Receiving Manager can significantly improve safety compliance, creating a safer and more efficient work environment.
How to Display Safety Compliance Skills on Your Resume
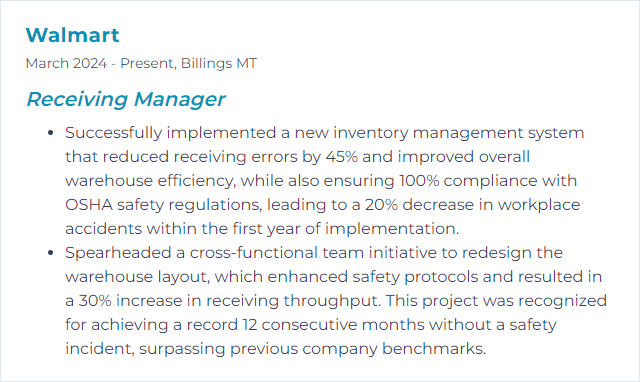