Top 12 Quality Technician Skills to Put on Your Resume
In today's highly competitive job market, standing out as a quality technician requires showcasing a unique set of skills that demonstrate your expertise and commitment to excellence. This article delves into the top 12 skills you should highlight on your resume to grab the attention of employers and secure your position as a top candidate in the field of quality control.
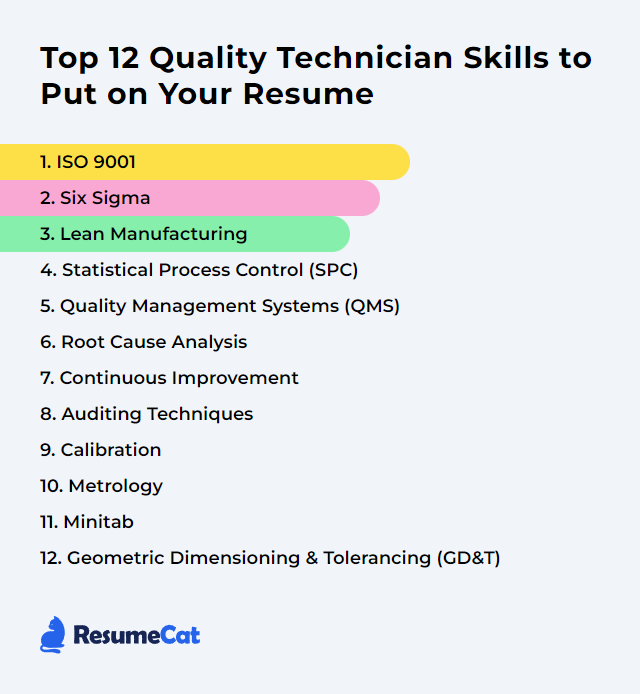
Quality Technician Skills
- ISO 9001
- Six Sigma
- Lean Manufacturing
- Statistical Process Control (SPC)
- Quality Management Systems (QMS)
- Root Cause Analysis
- Continuous Improvement
- Auditing Techniques
- Calibration
- Metrology
- Minitab
- Geometric Dimensioning and Tolerancing (GD&T)
1. ISO 9001
ISO 9001 is an international standard that specifies requirements for a quality management system (QMS). It helps organizations ensure they consistently provide products and services that meet customer and regulatory requirements, focusing on continuous improvement and customer satisfaction. For a Quality Technician, it guides the implementation, maintenance, and improvement of quality-related processes and controls.
Why It's Important
ISO 9001 is important for a Quality Technician as it provides a framework for consistent quality management practices, ensuring products and services meet customer and regulatory requirements, and facilitates continuous improvement in processes.
How to Improve ISO 9001 Skills
Improving ISO 9001 within your role as a Quality Technician involves several focused actions aimed at enhancing the quality management system (QMS) effectiveness. Here’s a concise guide:
Conduct Regular Audits: Regularly audit your QMS to identify areas for improvement. Use these insights to make necessary adjustments.
Engage in Continuous Training: Stay updated with the latest ISO 9001 training and trends. This ensures you're equipped with current knowledge to implement best practices.
Implement Corrective Actions: When non-conformities arise, promptly implement corrective actions to address root causes and prevent recurrence.
Foster a Quality Culture: Advocate for a quality culture where continuous improvement is a shared responsibility across the organization.
Utilize Quality Tools: Make use of quality tools such as Pareto charts and root cause analysis for problem-solving and process improvement.
Monitor and Measure Performance: Regularly monitor and measure the performance of processes to ensure they meet quality objectives and implement improvements as needed.
Customer Feedback: Actively seek and incorporate customer feedback into quality improvement initiatives.
Review and Update Documentation: Ensure that all QMS documentation is current, accurate, and accessible, reflecting the latest processes and procedures.
By focusing on these areas, you can contribute significantly to the improvement of your organization's ISO 9001 QMS.
How to Display ISO 9001 Skills on Your Resume
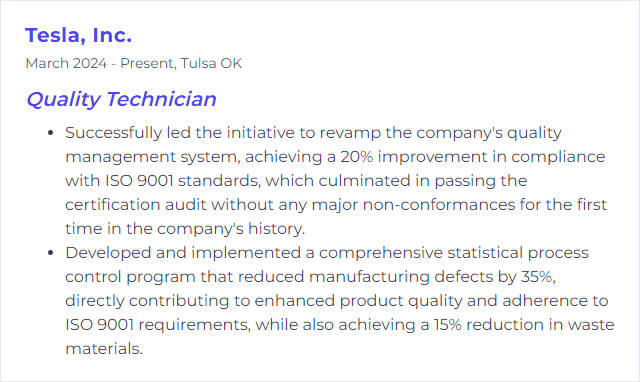
2. Six Sigma
Six Sigma is a data-driven methodology and set of tools aimed at process improvement by identifying and removing the causes of defects and minimizing variability in manufacturing and business processes, thereby ensuring quality and efficiency.
Why It's Important
Six Sigma is crucial for a Quality Technician because it provides a systematic and data-driven approach to reducing defects and improving quality, ensuring products meet customer satisfaction and regulatory standards efficiently.
How to Improve Six Sigma Skills
To improve Six Sigma as a Quality Technician, focus on the following strategies:
Enhance Statistical Knowledge: Deepen your understanding of statistical tools used in Six Sigma projects. ASQ's Statistical Methods is an excellent resource.
Lean Principles Integration: Incorporate Lean methodologies to streamline processes and reduce waste. Learn more through Lean Enterprise Institute.
Continuous Learning: Stay updated with the latest trends and techniques in Six Sigma through iSixSigma.
Certification Advancement: Aim for higher Six Sigma belts (Green, Black, Master Black Belt) through recognized organizations such as ASQ.
Practical Application: Apply what you learn in real-world projects and use Six Sigma Tools effectively.
Software Proficiency: Enhance your skills in Six Sigma software tools like Minitab. Familiarize yourself through Minitab's Learning Center.
Networking and Community Engagement: Join forums and groups, such as LinkedIn's Six Sigma Group, to share knowledge and learn from peers.
By focusing on these areas, you can significantly contribute to your organization's quality improvement initiatives and advance your career as a Quality Technician.
How to Display Six Sigma Skills on Your Resume
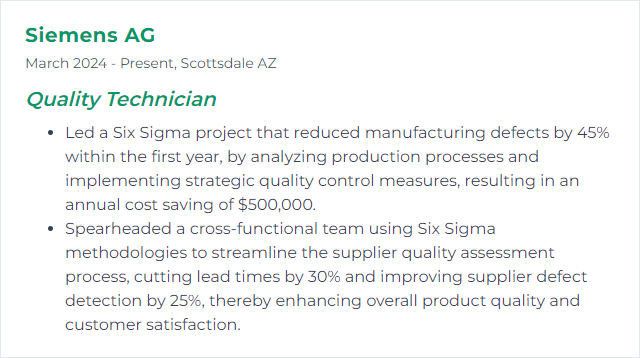
3. Lean Manufacturing
Lean Manufacturing is a systematic approach to minimizing waste within manufacturing systems while maximizing productivity, aimed at enhancing quality and efficiency, directly relevant to a Quality Technician's role in improving processes and ensuring high-quality outputs.
Why It's Important
Lean Manufacturing is important because it helps in reducing waste and improving efficiency, thereby ensuring higher quality products and processes, which is directly aligned with the responsibilities of a Quality Technician in monitoring and enhancing product quality and operational efficiency.
How to Improve Lean Manufacturing Skills
Improving Lean Manufacturing, especially from a Quality Technician's perspective, involves continuous process optimization and waste minimization. Here are concise strategies:
Implement Continuous Improvement: Regularly apply the Plan-Do-Check-Act (PDCA) cycle to identify inefficiencies and implement process improvements.
Embrace 5S Methodology: Organize and maintain the workplace for efficiency and effectiveness by using the 5S system - Sort, Set in Order, Shine, Standardize, and Sustain.
Adopt Kaizen: Encourage Kaizen, or continuous improvement, involving everyone from managers to workers, to seek small, incremental changes in processes to enhance efficiency.
Utilize Value Stream Mapping: Identify and eliminate waste in processes through Value Stream Mapping, visualizing each step of a process to pinpoint inefficiencies.
Focus on Quality Control: Implement Total Quality Management (TQM) techniques to improve the quality of products and services and minimize defects.
Standardize Work: Create and follow standardized work procedures to ensure consistency, which can be found at the Lean Enterprise Institute.
Engage in Training and Development: Continually educate and train employees on lean principles and techniques, fostering a culture of continuous improvement.
By focusing on these strategies, a Quality Technician can significantly contribute to enhancing Lean Manufacturing practices within their organization.
How to Display Lean Manufacturing Skills on Your Resume
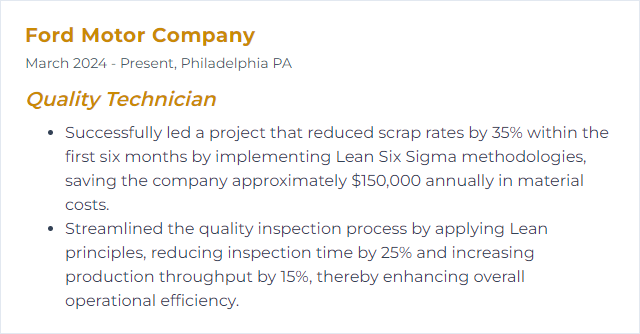
4. Statistical Process Control (SPC)
Statistical Process Control (SPC) is a method used by quality technicians to monitor and control a process using statistical techniques to ensure it operates at its full potential, producing consistent, high-quality products with minimal waste.
Why It's Important
Statistical Process Control (SPC) is crucial for a Quality Technician as it provides a data-driven method for monitoring, controlling, and improving the manufacturing process quality by identifying variations, ensuring product consistency, and reducing defects.
How to Improve Statistical Process Control (SPC) Skills
Improving Statistical Process Control (SPC) involves several key steps tailored for Quality Technicians:
Education and Training: Enhance understanding of SPC principles, tools, and applications. Invest in ASQ’s SPC training courses.
Data Accuracy: Ensure the accuracy and reliability of the data collected. Use precise measurement tools and validate data regularly.
Software Tools: Utilize advanced SPC software for real-time data analysis and trend detection.
Process Understanding: Deepen your understanding of the processes through process mapping to identify variables affecting quality.
Continuous Improvement: Adopt a Kaizen or continuous improvement approach to SPC, integrating feedback loops for ongoing refinement (Kaizen Institute).
Employee Engagement: Engage operators and employees in SPC practices through regular training sessions and encourage their feedback for process improvements.
Customized SPC Charts: Develop and use customized SPC charts that are relevant to your specific processes and quality objectives.
Regular Audits: Conduct regular SPC system audits to ensure the effectiveness of the SPC processes and to identify areas for improvement.
Cross-Functional Teams: Work with cross-functional teams to ensure that SPC is integrated across all departments and processes.
Benchmarking: Compare your SPC practices with industry standards or leaders to identify improvement areas (Benchmarking).
By focusing on these key areas, you can significantly improve the effectiveness of SPC within your organization, leading to better quality control and continuous improvement.
How to Display Statistical Process Control (SPC) Skills on Your Resume
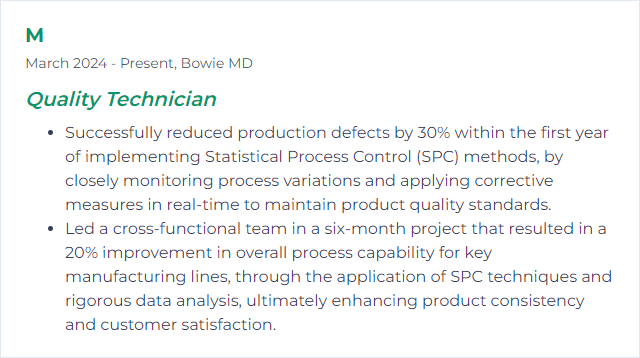
5. Quality Management Systems (QMS)
A Quality Management System (QMS) is a structured framework of procedures and processes used by an organization to ensure that its products or services meet and maintain the desired levels of quality. For a Quality Technician, it involves the application of quality control and quality assurance practices, focusing on continuous improvement and customer satisfaction through adherence to international quality standards and regulations.
Why It's Important
Quality Management Systems (QMS) are crucial as they provide a structured framework for ensuring product and service quality, consistency, and customer satisfaction. For a Quality Technician, a QMS helps in identifying and implementing best practices, reducing errors, and facilitating continuous improvement in processes, directly contributing to the organization's efficiency and competitive advantage.
How to Improve Quality Management Systems (QMS) Skills
Improving Quality Management Systems (QMS) involves a continuous process of evaluation, feedback, and enhancement to ensure that quality standards are not only met but exceeded. Here are concise steps a Quality Technician can take, supported by relevant resources:
Conduct Regular Audits: Perform regular audits to identify gaps and areas for improvement within your QMS. ISO 19011 provides guidelines for auditing management systems.
Implement Continuous Improvement Processes: Adopt methodologies like Kaizen for continuous, incremental improvement. This involves everyone in the organization from the top down.
Training and Development: Ensure all team members are properly trained on the latest quality standards and practices. The American Society for Quality (ASQ) offers various training resources.
Leverage Technology: Utilize QMS software to streamline processes, maintain documentation, and track quality metrics effectively. Tools like Qualio can help manage your QMS more efficiently.
Customer Feedback Integration: Regularly collect and analyze customer feedback to align your QMS improvements with customer expectations. Tools like SurveyMonkey can facilitate this process.
Management Engagement: Ensure top management is actively involved in the QMS to foster a quality-centric culture. ISO 9001:2015 emphasizes the importance of leadership in quality management.
Risk Management: Incorporate risk management processes into your QMS to identify, assess, and mitigate risks proactively. ISO 31000 provides guidelines on risk management.
Benchmarking: Compare your QMS processes and performance against industry leaders to identify areas for improvement. The Benchmarking Network offers resources and studies.
By integrating these steps, a Quality Technician can significantly contribute to the enhancement of their organization's Quality Management System, driving efficiency, customer satisfaction, and compliance with international standards.
How to Display Quality Management Systems (QMS) Skills on Your Resume
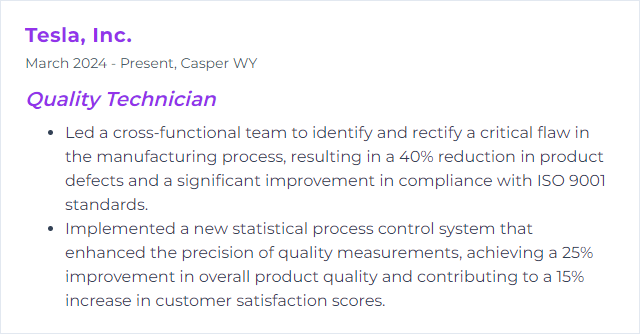
6. Root Cause Analysis
Root Cause Analysis (RCA) is a systematic process used by Quality Technicians to identify the underlying reasons for defects or problems in order to implement solutions that prevent recurrence.
Why It's Important
Root Cause Analysis (RCA) is important for a Quality Technician because it systematically identifies the underlying reasons for defects or problems, ensuring effective solutions can be implemented to prevent recurrence, thereby maintaining product quality and operational efficiency.
How to Improve Root Cause Analysis Skills
Improving Root Cause Analysis (RCA) involves a focused approach to identify, understand, and address the underlying reasons for problems in processes or quality issues. For a Quality Technician, enhancing RCA skills is crucial for effective problem-solving and continuous improvement. Here's a concise guide:
Understand Various RCA Tools: Familiarize yourself with RCA tools like the 5 Whys, Fishbone Diagram, and Pareto Analysis. Each tool has its strengths in different scenarios. ASQ's overview of problem-solving tools offers a good starting point.
Gather Complete and Accurate Data: Ensure the data you collect is comprehensive and reliable. Accurate data is the foundation of an effective RCA. The Data Quality Management by DAMA International provides guidelines on ensuring data quality.
Engage the Right Team: RCA should be collaborative. Involve individuals with diverse expertise related to the issue at hand. TeamSTEPPS by AHRQ offers strategies for improving team collaboration and communication.
Focus on Systemic Causes: Look beyond immediate causes and identify systemic issues contributing to the problem. This approach prevents recurrence. The Systems Thinking Approach by The Systems Thinker introduces the concept of systemic thinking.
Implement Corrective Actions Effectively: After identifying root causes, develop and implement corrective actions that are sustainable. ISO 9001 standards on quality management emphasize the importance of effective implementation and monitoring of corrective actions.
Monitor and Adjust: Post-implementation, continuously monitor the effectiveness of corrective actions and make necessary adjustments. Continuous Improvement principles from Lean Manufacturing provide guidance on maintaining momentum in improvement efforts.
Educate and Train: Continuous learning and training in RCA techniques keep skills sharp. ASQ's training courses on RCA and quality management are valuable resources for ongoing education.
By adopting these strategies, Quality Technicians can significantly enhance their RCA skills, leading to more effective problem-solving and quality improvements within their organizations.
How to Display Root Cause Analysis Skills on Your Resume
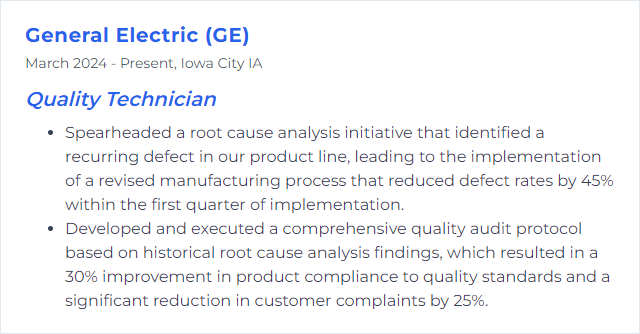
7. Continuous Improvement
Continuous Improvement, in the context of a Quality Technician, refers to the ongoing effort to enhance products, services, or processes through incremental and breakthrough improvements, aiming to increase efficiency, effectiveness, and quality.
Why It's Important
Continuous improvement is essential for a Quality Technician as it enables the ongoing enhancement of products, processes, and systems, ensuring higher quality standards, increased efficiency, and customer satisfaction, while also reducing costs and waste.
How to Improve Continuous Improvement Skills
Improving Continuous Improvement (CI) as a Quality Technician involves a focused approach on enhancing processes, fostering a culture of quality, and leveraging data effectively. Here’s a concise guide:
Embrace Lean Principles: Adopt Lean methodologies to eliminate waste, streamline processes, and increase efficiency.
Implement Six Sigma: Utilize Six Sigma techniques for reducing defects and improving quality.
Engage in Root Cause Analysis: Conduct thorough Root Cause Analysis (RCA) to identify and address the underlying issues in processes.
Foster a Culture of Continuous Learning: Encourage ongoing education and training. Platforms like Coursera offer courses on quality management and improvement methodologies.
Utilize Quality Management Systems (QMS): Implement and maintain a QMS like ISO 9001 to standardize and improve processes.
Leverage Technology and Data Analytics: Use data analytics tools to collect, analyze, and act on quality data. Tools like Minitab can help in decision-making.
Promote Team Collaboration: Foster a collaborative environment where feedback is valued and acted upon. Use collaborative tools like Slack for communication.
Set SMART Goals: Define Specific, Measurable, Achievable, Relevant, and Time-bound goals for quality improvement projects.
Benchmark and Learn from Best Practices: Look into industry benchmarks and case studies from leaders in quality like the Baldrige Performance Excellence Program.
Regular Reviews and Audits: Conduct regular process audits and reviews to ensure compliance and identify areas for improvement.
By focusing on these areas, a Quality Technician can effectively contribute to and enhance Continuous Improvement efforts within their organization.
How to Display Continuous Improvement Skills on Your Resume
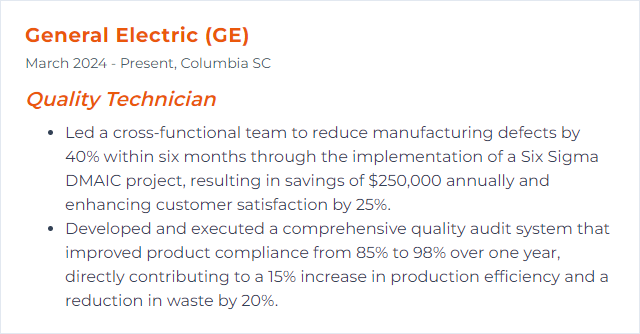
8. Auditing Techniques
Auditing techniques for a Quality Technician involve systematic methods used to examine and evaluate the quality processes and systems of an organization. These techniques include reviewing documents, observing operations, interviewing personnel, and analyzing data to ensure compliance with quality standards and identify areas for improvement.
Why It's Important
Auditing techniques are important for a Quality Technician because they provide systematic methods to assess and ensure the effectiveness of quality control processes, identify areas for improvement, and ensure compliance with industry standards and regulations. This helps maintain high-quality products and services, enhancing customer satisfaction and competitive advantage.
How to Improve Auditing Techniques Skills
Improving auditing techniques, especially for a Quality Technician, involves continuous learning, adopting best practices, and leveraging technology. Here are concise strategies:
Stay Updated: Regularly update your knowledge on the latest standards and regulations relevant to your field. Websites like ASQ (American Society for Quality) and ISO (International Organization for Standardization) are valuable resources.
Enhance Your Skills: Take advantage of online courses and certifications. Platforms like Coursera and Udemy offer courses on auditing and quality management.
Use Technology: Implement audit management software to streamline processes. Tools like iAuditor and Qualtrax can improve efficiency and accuracy.
Practice Risk-based Thinking: Focus on areas with the highest risk. This approach maximizes resource efficiency and effectiveness. The ISO 31000 standard on risk management provides a good framework.
Engage in Peer Review: Share and review audit techniques with peers. Forums on LinkedIn groups related to quality management and auditing are great for this.
Feedback and Continuous Improvement: Incorporate feedback from auditees and audit team members to refine your auditing process. Applying principles from Kaizen can foster a culture of continuous improvement.
Adopting these strategies can significantly enhance the effectiveness and efficiency of your auditing processes.
How to Display Auditing Techniques Skills on Your Resume
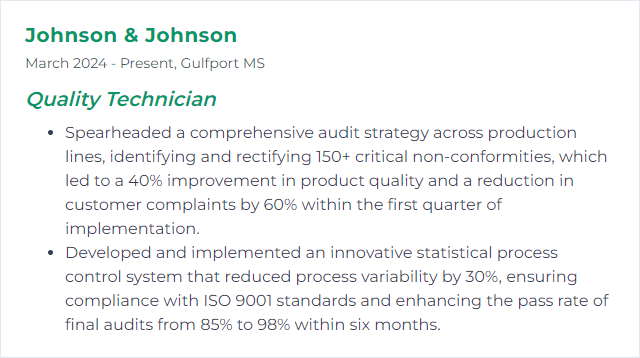
9. Calibration
Calibration is the process of configuring an instrument to provide accurate measurements by comparing its output to a known standard or reference. For a Quality Technician, it ensures that measurement tools and equipment are producing reliable, precise, and accurate results consistent with established standards.
Why It's Important
Calibration ensures the accuracy and reliability of measuring equipment, enabling Quality Technicians to make precise measurements for consistent product quality and compliance with standards.
How to Improve Calibration Skills
To improve calibration as a Quality Technician, follow these concise steps:
Understand Standards: Familiarize yourself with relevant international standards such as ISO/IEC 17025 for calibration and testing laboratories.
Regular Training: Ensure continuous training on calibration techniques and equipment. Online platforms like Coursera offer relevant courses.
Routine Calibration: Adhere to a strict schedule for calibrating instruments. Use manufacturers' guidelines and industry standards to determine frequency.
Use Certified Equipment: Only use calibration equipment that has been certified by a competent body. Reference standards should be traceable to national or international standards.
Documentation: Maintain meticulous records of calibration procedures, results, and corrective actions taken. Software like GAGEpack can help manage this.
Audit and Review: Regularly audit calibration processes and review procedures to identify areas for improvement. Feedback loops are crucial.
Preventive Maintenance: Implement a preventive maintenance program for calibration equipment to avoid inaccuracies due to wear and tear.
Cross-Checks: Conduct cross-checks using alternate certified equipment to verify calibration results.
Temperature & Humidity Control: Ensure the calibration environment is controlled and consistent, as changes can affect measurements.
Participate in Proficiency Testing: Engage in proficiency testing programs like those offered by NAPT to compare your results with those of other laboratories.
For further reading and resources on calibration, visit the National Institute of Standards and Technology (NIST) and explore their guidelines and tools related to calibration and measurement standards.
How to Display Calibration Skills on Your Resume
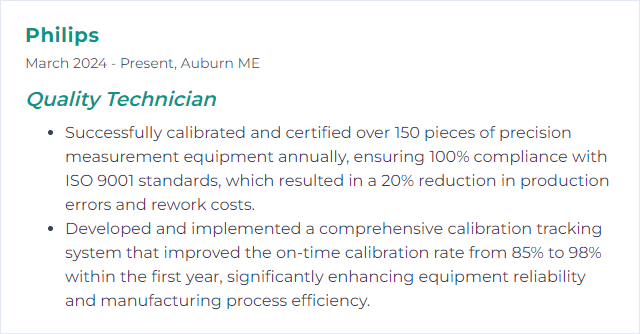
10. Metrology
Metrology is the science of measurement and its application, encompassing both theoretical and practical aspects. For a Quality Technician, it involves ensuring the accuracy, precision, and reliability of measurements used in quality control and assurance processes to meet specified standards.
Why It's Important
Metrology is crucial for a Quality Technician as it ensures the accuracy, consistency, and reliability of measurements, enabling precise product specifications, quality control, and compliance with standards, thereby guaranteeing customer satisfaction and regulatory adherence.
How to Improve Metrology Skills
Improving metrology, especially from the perspective of a Quality Technician, involves enhancing measurement accuracy, repeatability, and the overall reliability of measurement processes. Here are concise steps to achieve this:
Regular Calibration: Ensure all measuring instruments are regularly calibrated according to manufacturer guidelines and industry standards. This NIST guide provides insights into calibration practices.
Training: Invest in continuous training for personnel on the latest measurement techniques and metrology tools. The ASQ (American Society for Quality) offers relevant courses.
Implement SPC: Utilize Statistical Process Control (SPC) to monitor and control measurement processes, improving precision over time. More about SPC.
Adopt New Technologies: Stay updated with advancements in metrology, such as laser scanning and 3D imaging, to enhance measurement capabilities. MIT Technology Review is a good source for the latest tech news.
Ensure Proper Maintenance: Regularly maintain measurement tools and environments to prevent inaccuracies due to wear and tear or environmental factors. The Maintenance Management Guide can be a helpful resource.
Quality Control Circles: Participate in or establish quality control circles within the organization to foster a culture of continuous improvement in metrology practices. Learn more about Quality Circles.
By focusing on these areas, a Quality Technician can significantly improve the metrology practices within their organization, leading to higher quality outputs and better compliance with relevant standards.
How to Display Metrology Skills on Your Resume
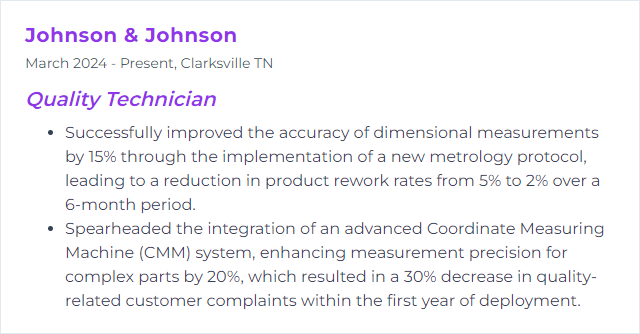
11. Minitab
Minitab is a statistical software tool used by Quality Technicians for data analysis, quality control, and process improvement, facilitating tasks like statistical analysis, visualization, and prediction to ensure and enhance product quality.
Why It's Important
Minitab is important for a Quality Technician because it provides powerful statistical tools to analyze quality data, identify trends, and uncover problems in processes, facilitating data-driven decision-making and continuous improvement efforts.
How to Improve Minitab Skills
To enhance your proficiency in Minitab as a Quality Technician, focus on the following concise strategies:
Training Courses: Enroll in Minitab's official training programs, which cover basic to advanced statistical techniques tailored for quality improvement.
Online Tutorials: Utilize free online tutorials and webinars, such as those found on YouTube and Minitab's Resource Center, to gain practical insights and tips.
Practice Data Analysis: Regularly apply your skills on real-world datasets or simulated data to reinforce learning. Websites like Kaggle offer a variety of datasets for practice.
Join Forums: Engage in Minitab User Groups or forums such as Stack Overflow to share experiences, ask questions, and get advice from experienced users.
Read Books: Supplement your learning with comprehensive guides like "Minitab Demystified" or the "Minitab Cookbook", which you can find on platforms like Amazon.
Use Minitab Help: Leverage the built-in help feature and Minitab Support for specific queries or troubleshooting.
By systematically following these steps and regularly applying your skills, you'll significantly improve your Minitab proficiency in a Quality Technician role.
How to Display Minitab Skills on Your Resume
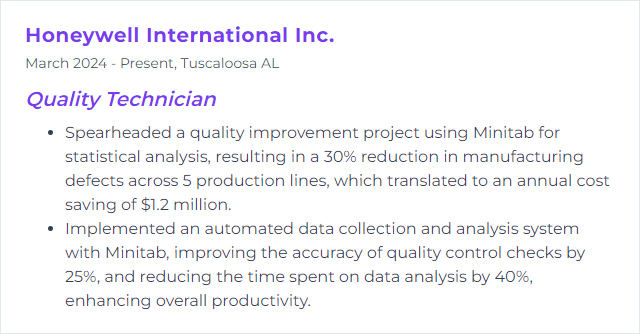
12. Geometric Dimensioning and Tolerancing (GD&T)
Geometric Dimensioning and Tolerancing (GD&T) is a system for defining and communicating engineering tolerances. It uses a symbolic language on engineering drawings and computer-generated three-dimensional solid models that explicitly describes nominal geometry and its allowable variation. For a Quality Technician, it's crucial for ensuring that parts fit and function together as intended, by precisely specifying dimensions, forms, and tolerances.
Why It's Important
Geometric Dimensioning and Tolerancing (GD&T) is crucial for a Quality Technician as it provides a precise and standardized method for defining and communicating engineering tolerances. It ensures parts fit and function together as intended, reduces manufacturing errors, and enhances product quality and reliability.
How to Improve Geometric Dimensioning and Tolerancing (GD&T) Skills
Improving your skills in Geometric Dimensioning and Tolerancing (GD&T) as a Quality Technician involves a focus on understanding standards, practical application, and continuous learning. Here’s a concise guide:
Familiarize with ASME Standards: Begin by thoroughly understanding the ASME Y14.5 standard, which is fundamental for GD&T practices. This foundation is crucial for accurate interpretation and application of GD&T principles.
Hands-On Practice: Apply your knowledge through practical exercises. Websites like I Get It Training offer interactive courses and exercises that simulate real-world scenarios.
Use Software Tools: Familiarize yourself with CAD software that supports GD&T, such as SolidWorks or AutoCAD. Many offer specific GD&T modules or training resources.
Take Professional Courses: Enroll in accredited GD&T courses that offer in-depth knowledge and certification. The American Society for Quality (ASQ) provides courses tailored for quality professionals.
Join Forums and Groups: Engage with communities on platforms like LinkedIn or specialized forums. Sharing experiences and solutions with peers can provide practical insights and tips.
Continuous Learning: Standards and technologies evolve, so it’s important to stay updated. Subscribe to relevant publications and attend webinars or workshops. The National Institute for Metalworking Skills (NIMS) often updates its resources and training programs.
By focusing on these areas, you can significantly improve your GD&T skills and understanding, making you a more effective Quality Technician in the manufacturing and engineering fields.
How to Display Geometric Dimensioning and Tolerancing (GD&T) Skills on Your Resume
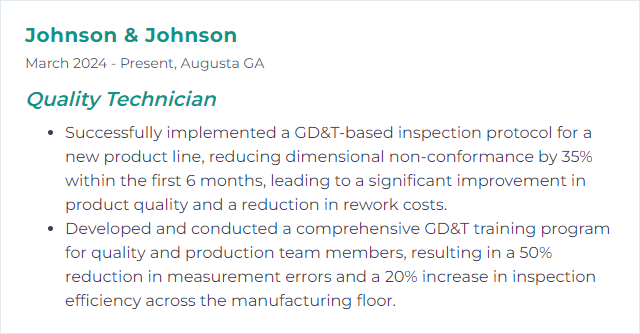