Top 12 Quality Consultant Skills to Put on Your Resume
In today's competitive job market, having a standout resume is crucial for quality consultants aiming to secure top positions. Highlighting a unique blend of skills on your resume can significantly enhance your appeal to potential employers, setting you apart as a highly qualified candidate in the field of quality assurance and management.
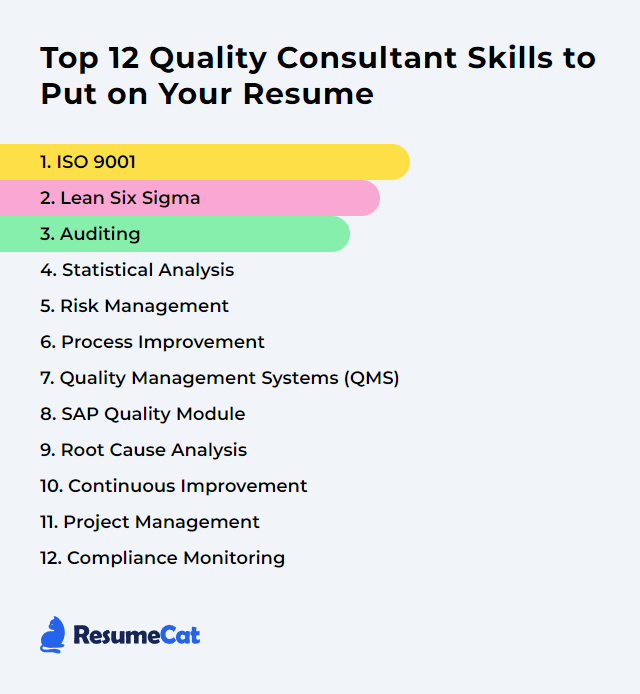
Quality Consultant Skills
- ISO 9001
- Lean Six Sigma
- Auditing
- Statistical Analysis
- Risk Management
- Process Improvement
- Quality Management Systems (QMS)
- SAP Quality Module
- Root Cause Analysis
- Continuous Improvement
- Project Management
- Compliance Monitoring
1. ISO 9001
ISO 9001 is an international standard that specifies requirements for a quality management system (QMS). Organizations use the standard to demonstrate their ability to consistently provide products and services that meet customer and regulatory requirements. For a Quality Consultant, it provides a framework to ensure quality consistency and improvement, facilitating client satisfaction and regulatory compliance.
Why It's Important
ISO 9001 is important because it provides a universally recognized framework for quality management, ensuring that organizations consistently meet customer and regulatory requirements, enhance customer satisfaction, and continually improve their processes. For a Quality Consultant, it serves as a critical tool for advising organizations on establishing, implementing, and maintaining quality standards effectively.
How to Improve ISO 9001 Skills
Improving your ISO 9001 Quality Management System (QMS) involves a continuous process of evaluation and enhancement to meet the evolving needs of your organization and ensure compliance with the standard's requirements. Here's a concise guide for a Quality Consultant:
Conduct Gap Analysis: Start by comparing your current QMS against the ISO 9001 requirements. Identify areas of non-conformance or opportunities for improvement. This ISO 9001 Checklist from the International Organization for Standardization (ISO) can guide your analysis.
Engage Leadership: Ensure top management's commitment to quality improvement by involving them in the review process and ensuring they understand the importance of their role in the QMS. The ISO 9001 Leadership clause provides insights.
Employee Training and Awareness: Enhance the competency of your workforce through targeted training and awareness programs. Focus on the relevance and importance of their activities and how they contribute to the achievement of quality objectives. ASQ’s Training Resources offer a good starting point.
Improve Documentation: Streamline your QMS documentation to ensure it's clear, concise, and useful. Implement a document control system if not already in place. Guidance on Document Control can be found within the ISO 9001 standards.
Enhance Customer Focus: Regularly gather, analyze, and act on customer feedback. Implement strategies to boost customer satisfaction. ISO 9001 emphasizes Customer Satisfaction as a key measure of QMS performance.
Implement Continuous Improvement: Adopt a culture of continuous improvement through methodologies like Plan-Do-Check-Act (PDCA) and tools like Six Sigma or Lean. ISO 9001's Continuous Improvement clause provides a framework.
Conduct Internal Audits: Regularly perform internal audits to assess the effectiveness of the QMS and identify areas for improvement. The ISO 19011 guidelines for auditing management systems can assist.
Management Review: Organize periodic management review meetings to assess the QMS's performance and suitability and make necessary adjustments. The Management Review section in ISO 9001 outlines this process.
Benchmarking: Compare your QMS practices against those of industry leaders or competitors. This can highlight areas for improvement or innovation. Resources like Benchmarking Guidelines can be helpful.
Technology Utilization: Leverage technology to enhance your QMS processes. Software solutions for document control, audit management, and corrective action can streamline compliance and improve efficiency.
By focusing on these areas, you can systematically enhance your organization's QMS, driving improvements in quality, customer satisfaction, and operational efficiency.
How to Display ISO 9001 Skills on Your Resume
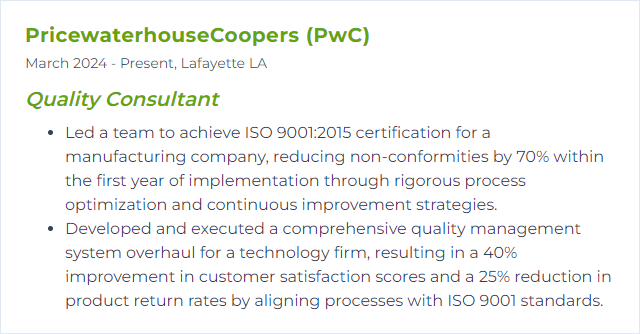
2. Lean Six Sigma
Lean Six Sigma is a methodology that combines the waste reduction principles of Lean manufacturing with the process improvement tools of Six Sigma to enhance quality, efficiency, and speed in an organization. As a Quality Consultant, it provides a structured framework and a set of tools for identifying and eliminating waste and variability in processes, aiming for near-perfect quality.
Why It's Important
Lean Six Sigma is important for a Quality Consultant because it provides a proven methodology for improving efficiency, reducing waste, and enhancing product quality, thereby enabling organizations to achieve operational excellence and deliver greater value to customers.
How to Improve Lean Six Sigma Skills
Improving Lean Six Sigma involves a continuous effort to enhance process efficiency and quality. As a Quality Consultant, focus on the following steps:
Stay Updated: Continually educate yourself on the latest methodologies and tools in Lean Six Sigma. Websites like ASQ (American Society for Quality) and iSixSigma offer resources and updates.
Engage in Continuous Learning: Participate in workshops, webinars, and certification courses from recognized institutions. Lean Six Sigma Institute provides various learning opportunities.
Implement Technology: Leverage modern software tools for process mapping and statistical analysis. Tools like Minitab or SigmaXL can be instrumental.
Collaborate and Network: Engage with professionals through forums and LinkedIn groups. Join networks like Lean Six Sigma Group on LinkedIn to exchange insights.
Practice Hands-on Application: Apply your knowledge practically through projects. Offer pro bono or discounted services to gain more experience and showcase your expertise.
Feedback and Reflect: Actively seek feedback from peers and clients on your strategies and projects. Use it to refine your approach.
Customize Strategies: Understand that each organization has unique needs. Tailor your Lean Six Sigma solutions to fit the specific context of the business.
By focusing on these areas, you can significantly improve your Lean Six Sigma practices, thereby enhancing your value as a Quality Consultant.
How to Display Lean Six Sigma Skills on Your Resume
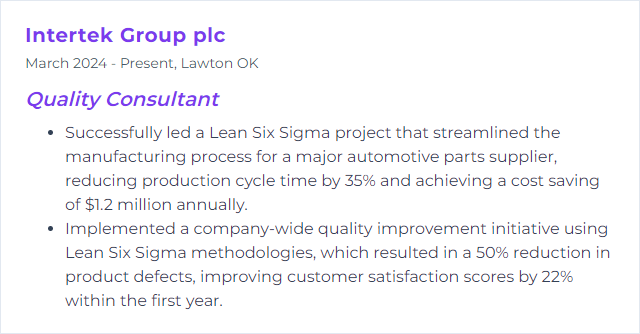
3. Auditing
Auditing, in the context of a Quality Consultant, is the systematic examination and evaluation of an organization's quality management systems and processes to ensure compliance with established standards, identify areas for improvement, and enhance overall quality performance.
Why It's Important
Auditing is crucial for a Quality Consultant as it ensures compliance with established standards, identifies areas for improvement, and enhances the credibility and reliability of processes and products.
How to Improve Auditing Skills
Improving auditing, particularly from a Quality Consultant perspective, involves a strategic approach focused on enhancing efficiency, accuracy, and value. Here are concise steps to achieve this:
Continuous Education: Stay updated with the latest auditing standards, methodologies, and technologies. Engaging in continuous professional development ensures auditors can apply the most current practices. ASQ offers resources and courses for auditors at all levels.
Leverage Technology: Utilize auditing software and tools for data collection and analysis to improve accuracy and efficiency. Technologies like AI and data analytics can significantly enhance audit quality. TechTarget discusses technological impacts on audit quality.
Risk-Based Auditing: Focus more on areas with higher risks. This approach ensures resources are allocated efficiently, improving the effectiveness of the audit. The Institute of Internal Auditors offers insights into risk-based auditing.
Stakeholder Engagement: Engage regularly with stakeholders to understand their concerns and expectations. This helps in aligning audit objectives with organizational goals. KPMG provides strategies for stakeholder engagement.
Quality Control and Assurance: Implement strict quality control and assurance procedures within the auditing process to ensure compliance and reliability of results. The ISO framework for quality management systems can be a valuable resource.
Feedback and Improvement: Solicit feedback from auditees and stakeholders to identify areas for improvement. Continuous improvement practices like Kaizen can be applied to the auditing process. ASQ has resources on continuous improvement strategies.
By focusing on these areas, a Quality Consultant can significantly improve the auditing process, adding value to the organization and its stakeholders.
How to Display Auditing Skills on Your Resume
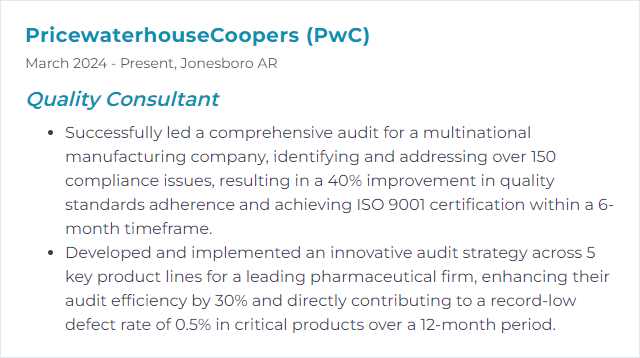
4. Statistical Analysis
Statistical analysis is the process of collecting, examining, interpreting, and presenting data to identify patterns, trends, and relationships, enabling informed decision-making and quality improvement strategies.
Why It's Important
Statistical analysis is crucial for a Quality Consultant as it enables data-driven decision-making, identifies trends and patterns in quality metrics, and ensures the reliability and consistency of products or services through quantitative evidence.
How to Improve Statistical Analysis Skills
Improving statistical analysis, especially for a Quality Consultant, involves a focused approach on enhancing data quality, statistical knowledge, and the application of appropriate analytical methods. Here are concise steps to achieve this:
Enhance Statistical Knowledge: Continuous learning through courses and resources on platforms like Coursera or edX can update you on the latest statistical methods and best practices.
Utilize Advanced Software Tools: Master advanced statistical software like R or SAS to perform more sophisticated analyses efficiently.
Data Quality Management: Implement data quality management practices to ensure that the data used for analysis is accurate and reliable. Guidelines from ASQ (American Society for Quality) can be beneficial.
Apply Appropriate Statistical Methods: Tailor your statistical methods to the specific problem at hand. Resources like NIST/SEMATECH e-Handbook of Statistical Methods provide a comprehensive guide to choosing and applying the right statistical techniques.
Peer Review and Validation: Engage in peer review processes and validate your findings with external data sets or through replication studies to ensure reliability and validity of your analysis.
Stay Informed on Industry Trends: Subscribe to relevant journals and websites like Quality Magazine to stay updated on the latest trends and case studies in quality and statistical analysis.
By focusing on these areas, a Quality Consultant can significantly improve their statistical analysis skills and contribute more effectively to quality improvement initiatives.
How to Display Statistical Analysis Skills on Your Resume
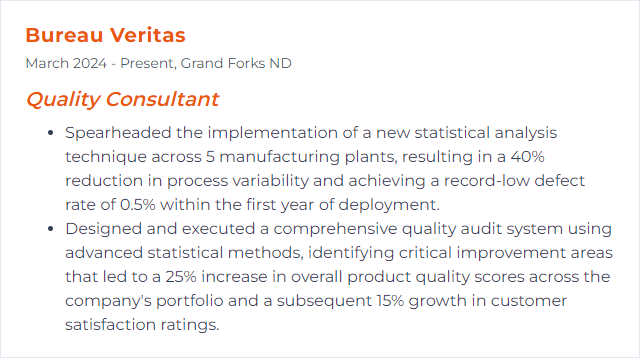
5. Risk Management
Risk Management, in the context of a Quality Consultant, involves identifying, assessing, and prioritizing risks to quality, followed by coordinated efforts to minimize, monitor, and control the probability or impact of unfortunate events or to maximize the realization of opportunities.
Why It's Important
Risk management is crucial for a Quality Consultant as it helps to identify, assess, and mitigate potential threats to the quality of projects or processes, ensuring they meet client expectations, regulatory requirements, and industry standards, while also minimizing errors, enhancing safety, and protecting the organization's reputation and financial stability.
How to Improve Risk Management Skills
Improving Risk Management involves a systematic approach to identifying, analyzing, and addressing potential risks to ensure project success and organizational objectives. Here's a very short and concise strategy tailored for a Quality Consultant:
Identify Risks: Start by thoroughly identifying potential risks that could impact the project or organization. Tools like SWOT Analysis can be helpful.
Analyze Risks: Evaluate the identified risks in terms of their potential impact and likelihood. Techniques like Risk Matrix can facilitate this analysis.
Prioritize Risks: Prioritize the risks based on their potential impact and likelihood of occurrence. This step ensures that you focus on the most critical risks first.
Develop Mitigation Strategies: For each high-priority risk, develop strategies to mitigate, transfer, accept, or avoid the risk. Risk Response Strategies can guide this process.
Implement Solutions: Implement the chosen strategies to manage the identified risks effectively.
Monitor and Review: Continuously monitor the risks and the effectiveness of the mitigation strategies, adjusting as necessary. Regular Risk Reviews are essential.
Communicate: Keep all stakeholders informed about the risk status and mitigation steps being taken. Effective communication is key to successful risk management.
By following these steps, a Quality Consultant can enhance their risk management process, ensuring better preparedness and response to potential risks.
How to Display Risk Management Skills on Your Resume
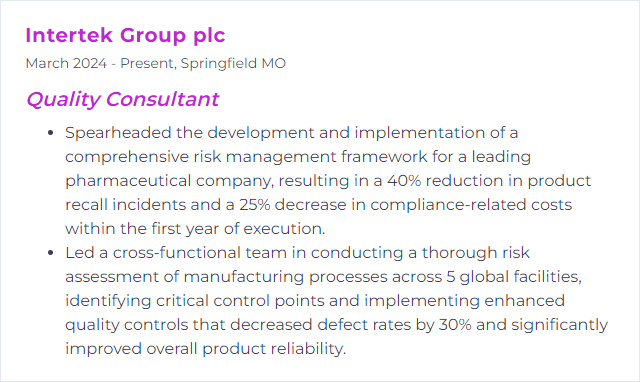
6. Process Improvement
Process Improvement is a systematic approach aimed at enhancing the efficiency and effectiveness of organizational processes, to increase quality and reduce waste, thereby meeting or surpassing customer expectations.
Why It's Important
Process improvement is crucial for enhancing efficiency, reducing waste, increasing customer satisfaction, and ensuring consistent quality of products or services, thereby offering a competitive advantage.
How to Improve Process Improvement Skills
Improving Process Improvement involves a focused approach to enhance the efficiency and effectiveness of organizational processes. As a Quality Consultant, consider the following concise steps:
Assess Current Processes: Begin by thoroughly understanding existing processes through tools like Process Mapping and SWOT Analysis. This helps in identifying areas for improvement.
Set Clear Objectives: Define specific, measurable, achievable, relevant, and time-bound (SMART) objectives based on the assessment. Clear objectives guide the improvement efforts and facilitate tracking progress. SMART Goals can provide a framework.
Employ Process Improvement Methodologies: Utilize proven methodologies like Lean, Six Sigma, and Total Quality Management (TQM) to streamline processes, eliminate waste, and enhance quality.
Engage Stakeholders: Involve employees, management, and other stakeholders in the improvement process. Tools like Stakeholder Analysis can help in understanding their perspectives and gaining their support.
Implement Changes and Monitor Progress: Roll out improvements in a controlled manner, using Project Management principles. Monitor progress using Key Performance Indicators (KPIs) and adjust strategies as necessary.
Foster a Culture of Continuous Improvement: Encourage a mindset of ongoing improvement through training, recognition, and communication. Resources like Kotter’s 8-Step Change Model can guide cultural transformation.
Leverage Technology: Adopt relevant technology solutions for process automation and data analysis. Tools like Process Mining can uncover inefficiencies and suggest improvements.
Review and Refine Regularly: Continuously review processes against objectives and industry benchmarks. This iterative approach ensures that processes remain efficient and aligned with organizational goals.
By following these steps and leveraging appropriate resources and methodologies, Quality Consultants can significantly improve process improvement initiatives within organizations.
How to Display Process Improvement Skills on Your Resume
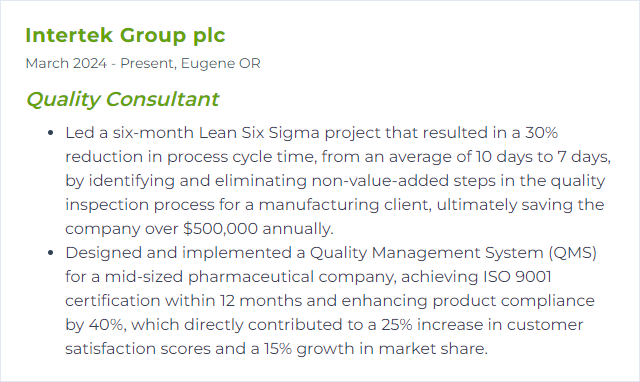
7. Quality Management Systems (QMS)
A Quality Management System (QMS) is a structured framework of policies, processes, and procedures required to plan and execute core business areas with the aim of improving customer satisfaction and ensuring compliance with regulations and standards. It helps organizations consistently meet customer requirements and enhance their effectiveness and efficiency on a continuous basis.
Why It's Important
A Quality Management System (QMS) is crucial because it ensures consistent delivery of high-quality products or services, enhances customer satisfaction, and improves operational efficiency, thereby reducing waste and increasing profitability. It enables an organization to meet regulatory requirements and improve continuously through systematic processes and performance metrics.
How to Improve Quality Management Systems (QMS) Skills
Improving a Quality Management System (QMS) involves several key steps that focus on continuous improvement, employee engagement, process optimization, and the effective use of technology. Here’s a concise guide tailored for a Quality Consultant:
Conduct a Gap Analysis: Identify areas for improvement by comparing current practices against QMS standards (e.g., ISO 9001). ASQ offers resources on understanding these standards.
Engage Stakeholders: Involve employees at all levels to foster a quality-centric culture. Tools like MindTools can help in stakeholder analysis.
Streamline Processes: Use process mapping to identify inefficiencies or redundancies. Lean and Six Sigma methodologies can be instrumental; resources on iSixSigma provide valuable insights.
Implement Technology Solutions: Adopt QMS software for better documentation, audit management, and corrective action processes. Capterra offers comparisons of various QMS tools.
Training and Development: Ensure ongoing training programs for staff to stay updated on QMS practices. Coursera and edX offer relevant courses.
Continuous Improvement: Adopt the Plan-Do-Check-Act (PDCA) cycle for continuous QMS improvement. ASQ’s PDCA Cycle guide provides a comprehensive overview.
Regular Audits and Reviews: Conduct internal and external audits to ensure compliance and identify areas for improvement. ISO’s auditing standards provide guidelines for effective quality audits.
Customer Feedback: Use customer feedback to drive improvements in product and service quality. Tools like SurveyMonkey can facilitate this process.
Benchmarking: Compare your QMS practices against those of leading organizations in your industry. BMGI offers insights on benchmarking for excellence.
Management Review and Support: Ensure top management is actively involved in reviewing and supporting QMS initiatives for alignment with business objectives.
By focusing on these areas, a Quality Consultant can significantly contribute to enhancing the effectiveness of a Quality Management System, driving better business outcomes and customer satisfaction.
How to Display Quality Management Systems (QMS) Skills on Your Resume
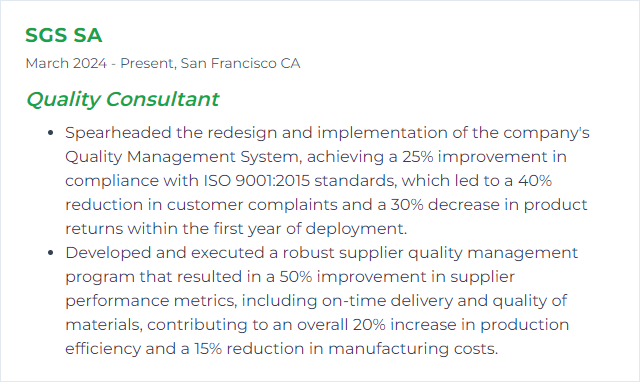
8. SAP Quality Module
The SAP Quality Module, formally known as SAP Quality Management (QM), is a component of the SAP ERP system that focuses on quality assurance and control in manufacturing and production processes. It helps in managing quality in materials, production, and procurement processes by facilitating tasks such as quality planning, quality inspection, and quality certificates. As a Quality Consultant, you would leverage this module to ensure products meet regulatory and customer requirements, optimize quality costs, and enhance product reliability and safety.
Why It's Important
The SAP Quality Management (QM) module is crucial for a Quality Consultant as it facilitates comprehensive quality planning, execution, and control processes, ensuring product compliance and enhancing customer satisfaction by integrating quality tasks directly with manufacturing and procurement operations.
How to Improve SAP Quality Module Skills
Improving the SAP Quality Management (QM) module involves several key strategies focused on optimizing processes, enhancing system functionality, and ensuring that the module fully supports your quality management requirements. Here's a concise guide for a Quality Consultant:
Assess Current Setup: Begin with a thorough assessment of your current SAP QM configuration. Identify gaps in processes and functionalities that do not meet your organizational quality standards.
Standardize Processes: Standardize quality management processes across the organization to ensure consistency. This simplifies training and compliance. SAP Best Practices can provide a benchmark.
Integrate with Other Modules: Enhance integration with other SAP modules like Material Management (MM), Production Planning (PP), and Sales and Distribution (SD) for a seamless flow of quality-related information across the enterprise. SAP QM Integration offers insights into how QM can be integrated effectively.
Automate Quality Processes: Leverage SAP's automation capabilities to reduce manual errors and improve efficiency. Focus on automating routine tasks, alerts, and workflows within the QM module.
Implement Advanced Quality Planning: Utilize the Quality Planning function to manage master data for quality planning and inspection. This includes inspection plans, material specifications, and engineering drawings. SAP QM Planning provides a detailed guide.
Continuous Training and Support: Ensure that your team is well-trained on the latest functionalities and best practices within SAP QM. SAP offers training and certification for various modules and aspects of the system.
Leverage Analytics for Continuous Improvement: Utilize SAP QM reporting and analytics tools to track quality performance and identify areas for improvement. SAP Analytics Cloud can enhance your data analysis capabilities.
Stay Updated with SAP Releases: Regularly update your SAP QM module to leverage new features and improvements. Keep track of SAP's release notes for information on the latest enhancements.
Engage with SAP Community: Participate in the SAP Community to share insights, ask questions, and learn from the experiences of other SAP QM users.
Feedback Loop: Establish a feedback loop with end-users to continuously gather insights on the usability and effectiveness of the QM module, allowing for ongoing refinement and optimization.
By implementing these strategies, a Quality Consultant can significantly improve the efficiency and effectiveness of the SAP Quality Management module, ensuring it fully supports the organization's quality goals.
How to Display SAP Quality Module Skills on Your Resume
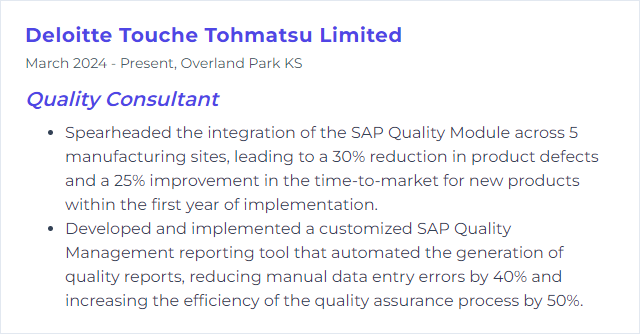
9. Root Cause Analysis
Root Cause Analysis (RCA) is a systematic process used by Quality Consultants to identify the fundamental underlying issues that lead to a problem or non-conformance, aiming to implement solutions that prevent recurrence.
Why It's Important
Root Cause Analysis (RCA) is crucial for a Quality Consultant as it systematically identifies the underlying reasons for problems or defects, allowing for the implementation of long-term solutions that enhance quality, efficiency, and customer satisfaction, while reducing costs and preventing recurrence of issues.
How to Improve Root Cause Analysis Skills
To improve Root Cause Analysis (RCA) as a Quality Consultant, follow these concise steps:
Define the Problem Clearly: Start with a clear, concise statement of the issue. ASQ's problem statement guide can help in formulating this.
Gather Data and Evidence: Collect data related to the problem's symptoms. Use tools like Fishbone Diagrams and 5 Whys for thorough analysis.
Identify Potential Causes: Utilize brainstorming and tools like the Pareto Chart to prioritize potential causes.
Analyze Root Causes: Apply techniques like the 5 Whys method or Failure Mode and Effects Analysis (FMEA) for deeper analysis.
Implement Corrective Actions: Develop a plan to address the root causes, referencing ASQ’s Corrective Action guide for best practices.
Monitor and Adjust: Regularly review the effectiveness of corrective actions, adjusting as necessary. Project Management Institute offers resources on managing these changes effectively.
Document and Share Learnings: Document the process and share insights with your team. Platforms like Lucidchart can be used for creating and sharing diagrams and flowcharts that illustrate the RCA process.
By following these steps, you'll enhance your RCA process, leading to more effective problem-solving and quality improvement initiatives.
How to Display Root Cause Analysis Skills on Your Resume
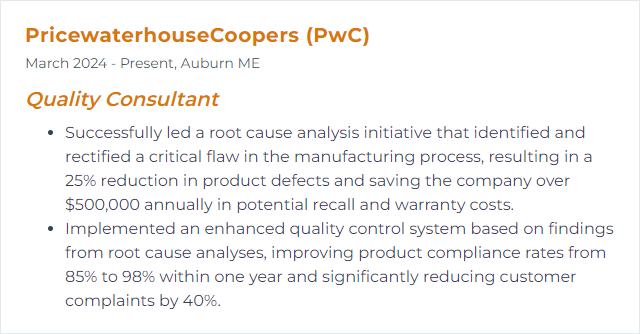
10. Continuous Improvement
Continuous Improvement is an ongoing effort to enhance products, services, or processes by implementing incremental improvements or breakthrough innovations, aiming to increase quality and efficiency. For a Quality Consultant, it involves systematically identifying opportunities for improvement and applying methodologies like PDCA (Plan-Do-Check-Act) or Lean Six Sigma to achieve sustainable excellence in quality performance.
Why It's Important
Continuous improvement is vital as it systematically enhances processes, products, and services, ensuring they meet or exceed quality standards, thereby increasing customer satisfaction, reducing costs, and maintaining a competitive edge.
How to Improve Continuous Improvement Skills
Improving Continuous Improvement (CI) involves a strategic approach focusing on enhancing processes and fostering a culture of ongoing quality enhancement. Here are concise steps tailored for a Quality Consultant:
Assess Current State: Begin with a thorough assessment of existing processes and performance. Tools like SWOT analysis can help identify strengths, weaknesses, opportunities, and threats.
Set Clear Objectives: Establish SMART goals (Specific, Measurable, Achievable, Relevant, Time-bound) that align with the organization's overall objectives.
Engage Stakeholders: Foster a culture of improvement by engaging employees at all levels. Techniques like Kaizen emphasize small, continuous changes involving all employees.
Implement PDCA Cycle: Utilize the Plan-Do-Check-Act (PDCA) cycle for structured implementation and evaluation of improvements.
Leverage Technology: Adopt Lean Six Sigma tools and methodologies to streamline processes, reduce waste, and enhance quality.
Train and Develop: Invest in training and development for all employees to build a skilled workforce committed to continuous improvement.
Monitor and Adjust: Regularly review performance data and feedback to monitor effectiveness of the changes. Be prepared to adjust strategies as needed.
Celebrate Achievements: Recognize and reward improvements, no matter how small, to motivate ongoing participation and commitment to quality.
By following these steps, a Quality Consultant can enhance Continuous Improvement efforts, leading to sustained organizational growth and performance.
How to Display Continuous Improvement Skills on Your Resume
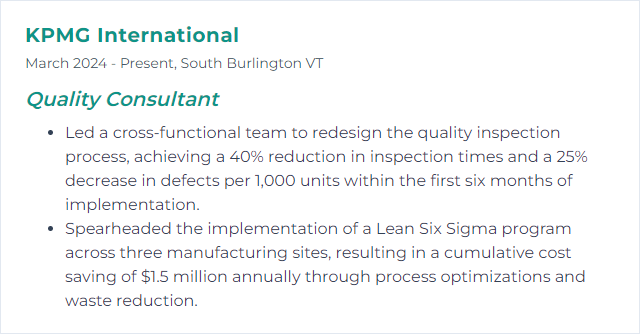
11. Project Management
Project management is the process of leading the work of a team to achieve all project goals within the given constraints, such as time, quality, and budget. For a Quality Consultant, it focuses on ensuring that project deliverables meet the required standards and specifications.
Why It's Important
Project management is crucial for a Quality Consultant as it ensures the efficient organization and execution of tasks to achieve high-quality outcomes within budget and time constraints, enabling the delivery of value and satisfaction to clients.
How to Improve Project Management Skills
Improving project management, especially from a Quality Consultant perspective, involves honing skills, methodologies, and tools to ensure projects meet or exceed stakeholders' quality expectations. Here’s a concise guide:
Adopt a Quality Management System (QMS): Implement a QMS like ISO 9001 to standardize project processes and ensure quality consistency across projects.
Utilize Project Management Software: Leverage software tools like Asana or Trello to streamline task allocation, tracking, and collaboration.
Enhance Communication: Foster open lines of communication using platforms like Slack to ensure team alignment and timely resolution of quality issues.
Continuous Improvement: Apply the Plan-Do-Check-Act (PDCA) cycle to continuously refine project processes and outcomes.
Professional Development: Encourage ongoing learning and certification through reputable organizations like PMI to stay updated with the latest project management trends and best practices.
Risk Management: Implement effective risk management strategies to anticipate and mitigate potential quality risks. Tools like Risk Register can help in organizing and addressing risks systematically.
Stakeholder Engagement: Ensure continuous engagement with stakeholders through tools like StakeholderMap to align project objectives with quality expectations.
By focusing on these areas, Quality Consultants can significantly enhance project management effectiveness, leading to improved project outcomes and stakeholder satisfaction.
How to Display Project Management Skills on Your Resume
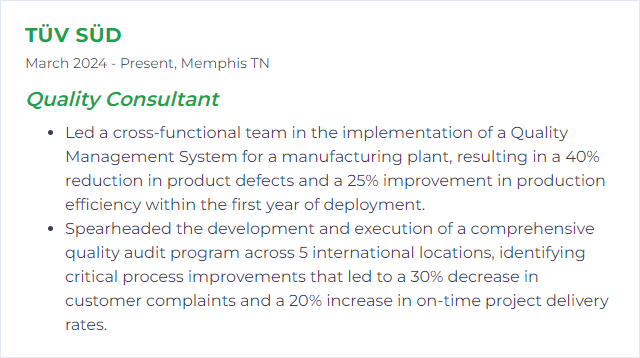
12. Compliance Monitoring
Compliance Monitoring, in the context of a Quality Consultant, refers to the continuous process of assessing, reviewing, and ensuring that an organization's operations and procedures align with established quality standards, regulatory requirements, and industry best practices.
Why It's Important
Compliance Monitoring is crucial for a Quality Consultant as it ensures that an organization's operations adhere to established standards, regulations, and quality requirements, minimizing legal risks, enhancing operational efficiency, and maintaining the organization's reputation for quality and reliability.
How to Improve Compliance Monitoring Skills
Improving compliance monitoring involves a multi-faceted approach tailored to ensure that an organization adheres to relevant laws, regulations, standards, and internal policies. As a Quality Consultant, focus on the following steps for a more effective compliance monitoring process:
Risk Assessment: Regularly identify and assess the compliance risks associated with your organization's operations. Tools like the Compliance Risk Assessment Template from Smartsheet can guide this process.
Develop Policies and Procedures: Establish clear, accessible policies and procedures that comply with legal and regulatory requirements. The ISO 19600:2014 provides guidelines on compliance management systems.
Training and Education: Implement ongoing training programs for employees on compliance matters relevant to their roles. Resources like Compliance Online offer various training modules.
Monitoring and Auditing: Use technology to automate monitoring where possible. Tools like ComplianceManager can help in tracking compliance across different areas.
Reporting Mechanisms: Establish secure and anonymous channels for reporting non-compliance or misconduct. The Ethics & Compliance Initiative (ECI) provides resources on developing effective reporting mechanisms.
Regular Reviews: Continuously review and update compliance programs to reflect changes in laws, regulations, and organizational operations. The Compliance Reviews section on Compliance Cosmos offers insights into conducting effective compliance reviews.
Corrective Actions: Develop a protocol for immediate corrective action when non-compliance is detected. Implementing a corrective action software like CAPA Software can streamline this process.
By following these steps and leveraging the recommended resources, you can enhance your organization's compliance monitoring efforts effectively.
How to Display Compliance Monitoring Skills on Your Resume
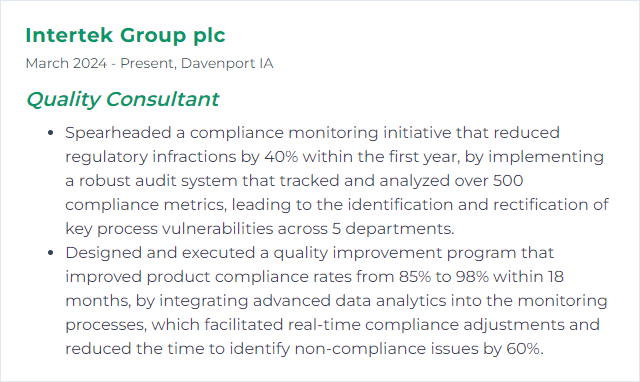