Top 12 Plastics Engineer Skills to Put on Your Resume
In the competitive field of plastics engineering, having a standout resume is crucial for securing your dream job. Highlighting a set of specific technical and soft skills can significantly elevate your application, demonstrating to potential employers your comprehensive expertise and adaptability in this dynamic industry.
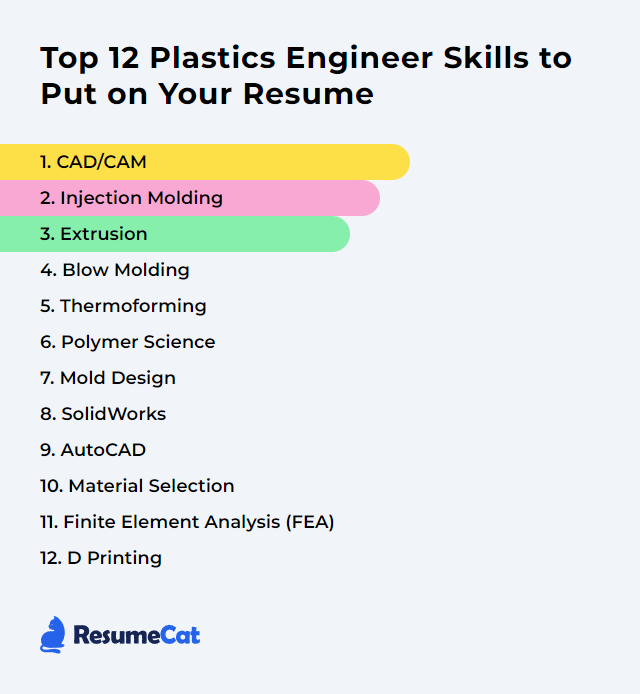
Plastics Engineer Skills
- CAD/CAM
- Injection Molding
- Extrusion
- Blow Molding
- Thermoforming
- Polymer Science
- Mold Design
- SolidWorks
- AutoCAD
- Material Selection
- Finite Element Analysis (FEA)
- D Printing
1. CAD/CAM
CAD/CAM stands for Computer-Aided Design/Computer-Aided Manufacturing. For a Plastics Engineer, it involves using software to design plastic parts and tools and then programming manufacturing processes, like injection molding or CNC machining, to produce those designs efficiently and accurately.
Why It's Important
CAD/CAM is crucial for a Plastics Engineer as it enables precise design and manufacturing of complex plastic components with high accuracy, efficiency, and speed, facilitating innovation and cost reduction in product development.
How to Improve CAD/CAM Skills
To improve CAD/CAM as a Plastics Engineer, focus on these key areas:
Stay Updated: Regularly update your software to access the latest features and improvements. Autodesk provides a variety of CAD/CAM tools suitable for plastics engineering, including AutoCAD and Fusion 360.
Training: Enhance your skills through online courses and certifications. Websites like Coursera and Udemy offer specialized courses in CAD/CAM technologies.
Integration: Leverage CAD/CAM software that integrates well with other systems (ERP, MES) to streamline workflows. Siemens offers advanced Digital Enterprise Software Suite for comprehensive integration.
Simulation: Use simulation tools to predict and solve manufacturing challenges before they occur. ANSYS offers plastics engineering-specific simulations that can predict material behavior and manufacturability.
Customization: Customize your CAD/CAM software using scripts or plugins to tailor the tools to your specific needs. The SolidWorks API allows for automation and customization, enhancing productivity.
Feedback Loop: Implement a feedback loop from the manufacturing floor back to the design phase to continually improve designs based on real-world data. Technologies like PLM (Product Lifecycle Management) help in managing this feedback efficiently.
Networking: Join online forums and communities such as the Eng-Tips Forums or Reddit’s r/cad to share insights, ask questions, and stay informed about the latest industry trends and solutions.
By focusing on these areas, you can significantly improve your CAD/CAM capabilities, leading to more efficient and innovative plastics engineering solutions.
How to Display CAD/CAM Skills on Your Resume
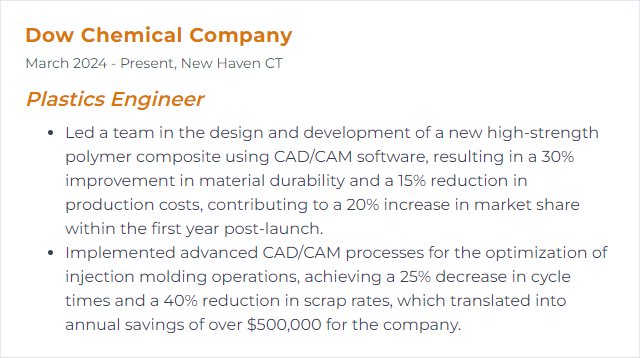
2. Injection Molding
Injection molding is a manufacturing process for producing parts by injecting molten material into a mold, primarily used for mass-producing plastic components with complex shapes, ensuring high repeatability and scalability.
Why It's Important
Injection molding is essential for a Plastics Engineer as it enables the high-volume production of complex, precision parts with excellent finish, consistent quality, and cost efficiency, facilitating innovation and speed in product development across various industries.
How to Improve Injection Molding Skills
Improving injection molding involves optimizing various aspects of the process to enhance efficiency, part quality, and production consistency. As a Plastics Engineer, consider the following concise strategies:
Material Selection: Choose the appropriate material based on part design, application, and performance requirements. Understanding the material's flow properties can help in selecting the right conditions for molding. Material Selection Guide.
Mold Design: Invest in high-quality mold design with proper cooling channels and gating system to ensure uniform cooling and minimal stress. Mold Design Best Practices.
Process Optimization: Utilize scientific molding principles to find the optimal processing parameters (temperature, pressure, injection speed) through Design of Experiments (DoE). Scientific Molding Guide.
Maintenance: Regular maintenance of the injection molding machine and molds to prevent defects and downtime. This includes cleaning, lubrication, and checking for wear. Maintenance Best Practices.
Training: Ensure operators and engineers are well-trained in both the theoretical and practical aspects of injection molding. Continuous learning helps in adapting to new technologies and materials. Society of Plastics Engineers Training.
Quality Control: Implement strict quality control measures, utilizing both visual inspection and advanced measurement tools to detect and mitigate defects early in the production process. Quality Control in Injection Molding.
By addressing these key areas, a Plastics Engineer can significantly improve the efficiency, quality, and profitability of injection molding operations.
How to Display Injection Molding Skills on Your Resume
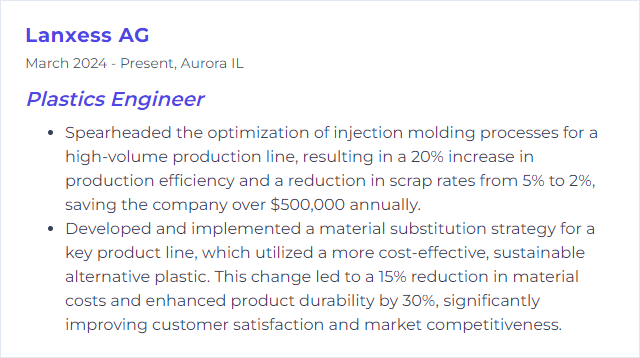
3. Extrusion
Extrusion is a manufacturing process where plastic material is melted and forced through a die to produce continuous shapes with a uniform cross-section, such as tubing, profiles, or films.
Why It's Important
Extrusion is crucial for a Plastics Engineer because it enables the continuous shaping of plastic materials into a variety of complex profiles with precise dimensions, expanding the range of possible applications and improving manufacturing efficiency and material properties.
How to Improve Extrusion Skills
Improving extrusion in the context of plastics engineering involves several key strategies aimed at enhancing efficiency, product quality, and process stability. Here's a concise guide:
Material Preparation: Ensure consistent material properties by pre-drying polymers (when necessary) and using consistent blends. Homogeneous material feeding improves the extrusion process. More on Material Preparation.
Equipment Maintenance: Regular maintenance of the extruder and downstream equipment prevents unexpected downtime and defects. Ensure screws, barrels, and dies are in optimal condition. Maintenance Tips.
Process Optimization: Optimize screw design and process parameters (temperature profiles, screw speed, and feed rate) for the material and product requirements. This enhances throughput and product quality. Screw Design Basics.
Die Design: Use properly designed dies to minimize pressure drops and ensure uniform flow distribution. This reduces defects and improves dimensional stability. Die Design Considerations.
Cooling and Sizing: Properly configure the cooling and sizing equipment to ensure rapid and uniform cooling, which is crucial for achieving the desired product dimensions and properties. Cooling Systems in Extrusion.
Quality Control: Implement real-time monitoring and quality control measures (such as dimensional checks and material property assessments) to detect and correct issues promptly. Quality Control in Extrusion.
Training and Education: Continuously educate and train the operational staff on the latest extrusion technologies and best practices to ensure the process runs at its optimum. Training Resources.
By focusing on these areas, plastics engineers can significantly improve the efficiency and quality of their extrusion processes.
How to Display Extrusion Skills on Your Resume
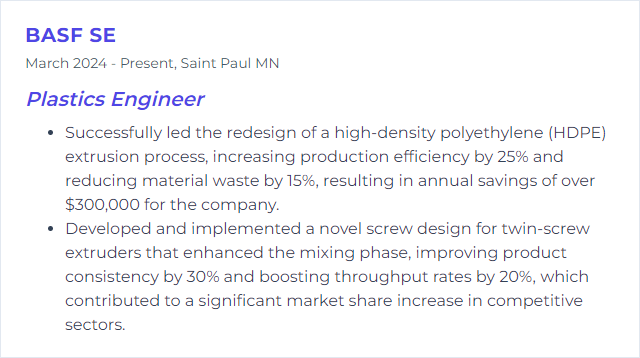
4. Blow Molding
Blow molding is a manufacturing process used to create hollow plastic parts by inflating a heated plastic tube (parison) inside a mold cavity until it conforms to the shape of the mold. This process is commonly used for producing bottles, containers, and other hollow shapes.
Why It's Important
Blow molding is crucial for a Plastics Engineer because it enables the cost-effective mass production of complex, hollow plastic parts with uniform wall thicknesses, such as bottles and containers, using a relatively simple and efficient process.
How to Improve Blow Molding Skills
To enhance blow molding efficiency and quality, a Plastics Engineer can focus on the following strategies:
Material Selection: Optimize materials for better flow and stability. Use predictive simulation tools like Autodesk Moldflow to analyze and select the best material.
Mold Design Optimization: Utilize advanced CAD software, e.g., SolidWorks, to design molds that ensure uniform wall thickness and reduce defects.
Process Control Improvement: Implement precise control systems for temperature, pressure, and cooling time to enhance repeatability. Siemens offers solutions tailored for plastics machinery automation.
Quality Monitoring: Adopt real-time quality monitoring systems, such as ZEISS IMT solutions, for immediate feedback and adjustment, ensuring consistent product quality.
Training and Skill Development: Engage in continuous learning through platforms like SPE (Society of Plastics Engineers) to stay updated on the latest technologies and methodologies in blow molding.
Focusing on these areas can significantly improve the blow molding process, leading to enhanced product quality, reduced waste, and increased efficiency.
How to Display Blow Molding Skills on Your Resume
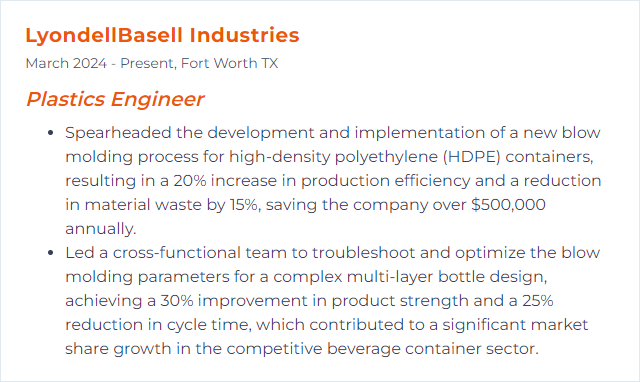
5. Thermoforming
Thermoforming is a manufacturing process where a plastic sheet is heated to a pliable forming temperature, formed to a specific shape in a mold, and trimmed to create a usable product.
Why It's Important
Thermoforming is crucial for a Plastics Engineer as it offers a cost-effective, versatile method for producing lightweight, complex plastic parts with precise dimensions, enabling rapid prototyping and efficient mass production.
How to Improve Thermoforming Skills
To improve thermoforming processes, a Plastics Engineer can focus on optimization in several key areas:
Material Selection: Choose the right material for your application considering its formability, strength, and end-use. Material Selection Guide.
Mold Design: Innovative mold designs can enhance product quality. Utilize simulations to predict outcomes. Mold Design Tips.
Heating System Efficiency: Optimize heating systems for uniform material heating. This includes zoning controls and precise temperature management. Heating Systems in Thermoforming.
Process Control: Implementing advanced process control systems can lead to more consistent quality and reduce waste. Advanced Process Control.
Cooling and Trimming Technologies: Invest in efficient cooling systems and precise trimming technologies to reduce cycle times and improve product quality. Cooling Systems Efficiency.
Sustainability Practices: Incorporate sustainability by using recyclable materials and optimizing processes to reduce waste. Sustainability in Thermoforming.
By focusing on these areas, a Plastics Engineer can significantly improve the efficiency and quality of thermoforming processes.
How to Display Thermoforming Skills on Your Resume
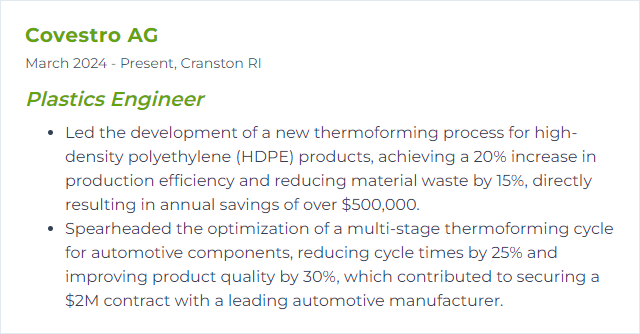
6. Polymer Science
Polymer Science is the study of polymers, large molecules composed of repeating structural units, focusing on their synthesis, structure, properties, and applications. For a Plastics Engineer, it serves as the foundational knowledge for designing, developing, manufacturing, and testing plastic materials and products.
Why It's Important
Polymer science is crucial for plastics engineers as it provides the foundational knowledge for designing, developing, and optimizing plastic materials. Understanding polymer structure-property relationships enables engineers to tailor plastics for specific applications, improving performance, sustainability, and manufacturing efficiency.
How to Improve Polymer Science Skills
To improve in Polymer Science as a Plastics Engineer, focus on understanding polymer materials from synthesis to applications, incorporating modern technologies and sustainability practices. Key steps include:
Continuous Learning: Stay updated with the latest advancements in polymer science by reading journals and attending seminars. Resources like Polymer Journal and Journal of Polymer Science offer cutting-edge research insights.
Hands-On Experience: Engage in research projects or internships that allow practical application of polymer science concepts. Laboratories and industries offer real-world problem-solving experiences.
Advanced Education: Consider furthering your education with specialized courses or degrees in polymer science. Online platforms like Coursera and edX offer relevant courses from top universities.
Networking: Join professional organizations such as the Society of Plastics Engineers (SPE) to connect with peers, attend conferences, and access resources.
Sustainability Practices: Emphasize developing eco-friendly polymers and recycling methods. Resources like ScienceDirect provide numerous articles on sustainable polymers and environmental impacts.
Innovation and Technology: Stay abreast of technological advancements in polymer processing and synthesis. Familiarize yourself with new materials and processing techniques that can enhance material properties and applications.
By integrating these strategies, you can significantly advance your expertise and career in Polymer Science.
How to Display Polymer Science Skills on Your Resume
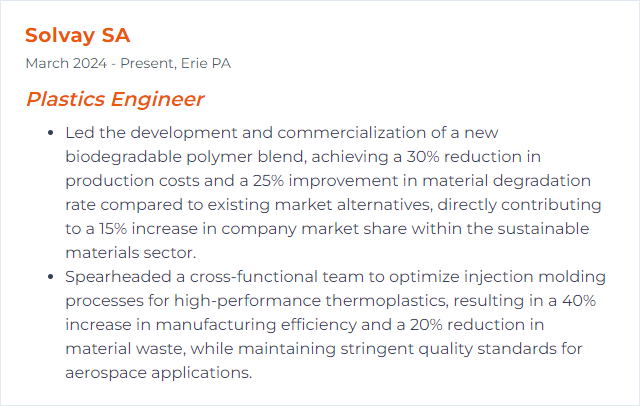
7. Mold Design
Mold design in plastics engineering is the process of creating detailed plans and specifications for molds that will be used to shape plastic materials into desired forms through processes like injection molding. This involves determining the mold's geometry, material, gating system, cooling channels, and ejection mechanism to ensure optimal manufacturing efficiency and product quality.
Why It's Important
Mold design is crucial for a Plastics Engineer because it directly influences the quality, efficiency, and cost-effectiveness of the plastic parts production process. Proper mold design ensures optimal material flow, cooling, and ejection, leading to high-quality products with minimal defects, reduced cycle times, and lower production costs.
How to Improve Mold Design Skills
Improving mold design in plastics engineering involves focusing on precision, efficiency, and the quality of the final product. Here are key strategies:
Optimize Mold Flow Analysis: Utilize mold flow simulation software to predict and improve material flow and cooling efficiency, reducing warpage and potential defects.
Enhance Cooling System Design: Design a balanced and efficient cooling system to minimize cycle times and ensure uniform cooling. Consider conformal cooling for complex shapes.
Apply Surface Treatments: Use appropriate surface treatments on the mold to improve ejection, reduce wear, and enhance the appearance of the final part.
Incorporate Modular Design: Design molds to be modular where possible to allow for easy maintenance, repair, and adjustment. This approach saves time and reduces costs in the long run.
Utilize High-Quality Materials: Select high-grade steel for the mold to withstand wear, corrosion, and the high pressures of injection molding, extending the mold's lifespan.
Implement Proper Venting: Ensure the mold has adequate venting to prevent trapped air, which can cause burn marks and incomplete filling. Accurate vent placement is crucial.
Adopt Latest Technologies: Stay updated with the latest in mold manufacturing technologies such as 3D printing for rapid prototyping and direct metal laser sintering (DMLS) for complex components. Stratasys and 3D Systems offer advanced solutions.
Focus on Gate Placement: Optimal gate placement ensures good flow, aesthetic quality, and reduces stress marks. Tools like SolidWorks Plastics can assist in determining the best locations.
By implementing these strategies and leveraging cutting-edge tools and materials, plastics engineers can significantly improve mold design, leading to more efficient production processes and higher-quality products.
How to Display Mold Design Skills on Your Resume
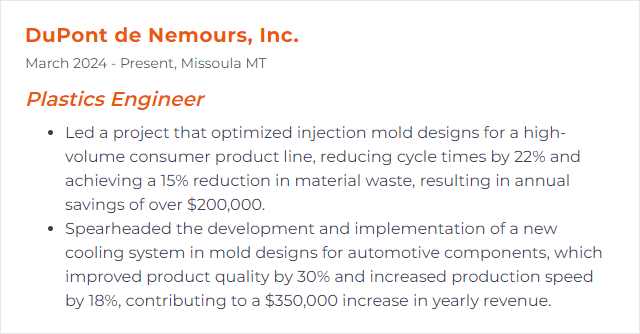
8. SolidWorks
SolidWorks is a computer-aided design (CAD) software used by plastics engineers for designing, simulating, and analyzing plastic parts and molds, facilitating the development of detailed 3D models and technical drawings for manufacturing.
Why It's Important
SolidWorks is crucial for a Plastics Engineer as it provides powerful 3D design capabilities for creating precise plastic component models, simulating mold flow and cooling to optimize manufacturability, and ensuring product quality and performance through rigorous testing and analysis tools.
How to Improve SolidWorks Skills
To enhance your SolidWorks skills as a Plastics Engineer, focus on mastering specific features relevant to plastics design and manufacturing. Here's a concise guide:
Learn Mold Design Tools: SolidWorks offers specialized tools for mold design. Master these to efficiently create and analyze molds. Explore the Mold Design Tutorial.
Utilize SolidWorks Plastics: This simulation tool helps predict how melted plastic flows during the injection molding process. It's crucial for identifying potential manufacturing issues. Dive into SolidWorks Plastics.
Explore Advanced Surface Modeling: Complex plastic parts often require advanced surface modeling techniques. Enhance your skills in this area to design intricate and aesthetically pleasing parts. Start with Surface Modeling.
Get Certified: SolidWorks offers certification programs. Consider obtaining a Certified SolidWorks Professional (CSWP) certification, focusing on areas relevant to plastics engineering.
Join the SolidWorks Community: Engage with other professionals and enthusiasts. The SolidWorks Community is a great resource for tips, advice, and advanced techniques.
By focusing on these areas, you'll significantly improve your proficiency in SolidWorks, making you more effective in plastics engineering projects.
How to Display SolidWorks Skills on Your Resume
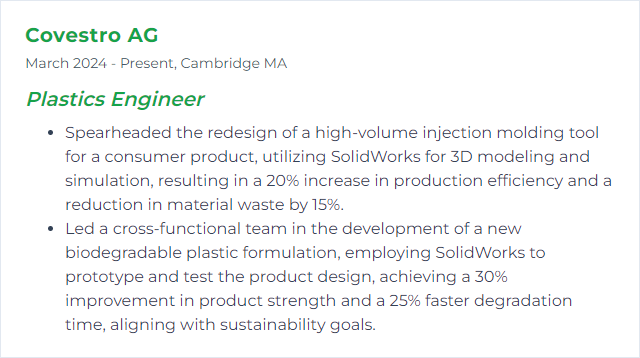
9. AutoCAD
AutoCAD is a computer-aided design (CAD) software used by plastics engineers for creating precise 2D and 3D drawings and models of plastic components and molds, facilitating design, visualization, and modification of engineering projects.
Why It's Important
AutoCAD is crucial for a Plastics Engineer as it enables precise design and modification of plastic components, streamlining the development process from conceptualization to manufacturing, ensuring accuracy, efficiency, and product quality.
How to Improve AutoCAD Skills
To improve AutoCAD skills for a Plastics Engineer, focusing on specific areas relevant to the industry and leveraging Autodesk's resources is crucial. Here's a concise guide:
Master 3D Modeling: Plastics engineers frequently work with complex shapes. Enhance your 3D modeling skills in AutoCAD by exploring tutorials focused on creating and manipulating 3D objects. Autodesk's 3D modeling resources are a great place to start.
Learn about Materials and Manufacturing Processes: Understanding the materials you'll be working with and their manufacturing processes can greatly enhance your CAD designs. Autodesk offers specific materials libraries and tools that can be integrated into AutoCAD.
Customize AutoCAD for Efficiency: Tailor your AutoCAD interface and create custom commands relevant to plastics engineering. Autodesk provides guidance on customization to streamline your workflow.
Stay Updated with AutoCAD Versions: New AutoCAD features can offer improved tools for design and analysis. Keep your software up to date and explore what's new with each release on the Autodesk official website.
Engage with the AutoCAD Community: Join forums and discussion groups for plastics engineers using AutoCAD. Sharing experiences and solutions with peers can provide industry-specific tips and tricks. The Autodesk Community is a good place to start networking and learning from fellow professionals.
By focusing on these areas, a Plastics Engineer can significantly enhance their proficiency and efficiency in AutoCAD, leading to better design outcomes and project success.
How to Display AutoCAD Skills on Your Resume
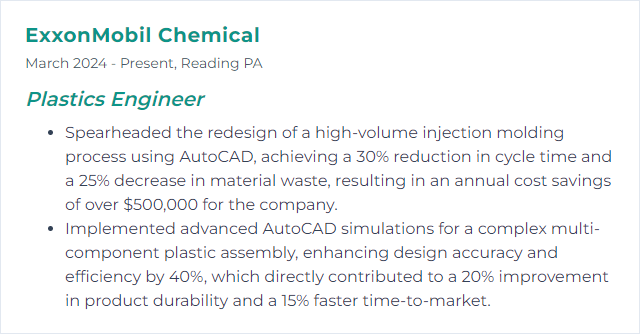
10. Material Selection
Material selection in the context of a Plastics Engineer involves choosing the most suitable plastic or polymer material for a specific application based on criteria such as mechanical properties, thermal behavior, chemical resistance, manufacturability, cost, and environmental impact.
Why It's Important
Material selection is crucial for a Plastics Engineer because it directly influences the product's performance, durability, manufacturing efficiency, cost-effectiveness, and environmental impact, ensuring the final product meets specific application requirements and standards.
How to Improve Material Selection Skills
Improving material selection, especially in the context of a Plastics Engineer, involves understanding the application requirements, comparing material properties, considering environmental factors, and evaluating cost-effectiveness. Here’s a concise guide:
Define Application Requirements: Clearly understand the mechanical, thermal, and chemical requirements of the application. MatWeb is a resourceful database for material properties.
Compare Material Properties: Use resources like UL Prospector to compare the properties of different plastics, ensuring they meet the application's needs.
Environmental Considerations: Consider the environmental impact of materials, focusing on recyclability and sustainability. The Ellen MacArthur Foundation offers insights into circular economy principles.
Cost-Effectiveness: Evaluate the cost relative to performance benefits. Tools like Plastics News can provide market pricing for various polymers.
Consult Standards and Regulations: Ensure material selection complies with relevant industry standards and regulations. The ASTM International website is a good starting point for standards.
Simulation and Testing: Utilize CAD and CAE software for predictive modeling and prototyping. Autodesk Material Library can be useful for simulations.
Seek Expert Advice: When in doubt, consult with material suppliers or industry experts. Networks like SPE (Society of Plastics Engineers) can connect you with professionals and further resources.
By systematically analyzing these aspects, a Plastics Engineer can make informed decisions on material selection, balancing performance, cost, and environmental impact.
How to Display Material Selection Skills on Your Resume
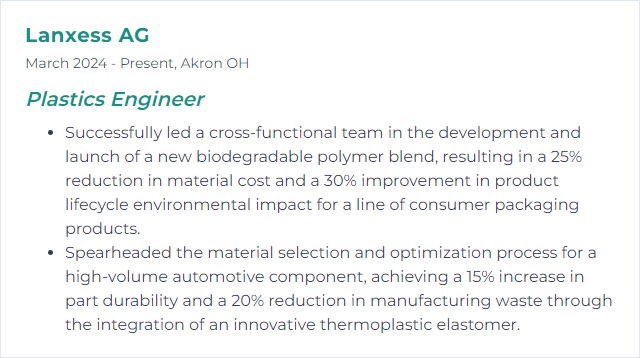
11. Finite Element Analysis (FEA)
Finite Element Analysis (FEA) is a computational technique used by plastics engineers to predict how plastic components will react to forces, vibrations, heat, and other physical effects by dividing the component into smaller, simpler parts (finite elements) and simulating their behavior under various conditions. This allows for optimization of designs for strength, durability, and performance before physical prototyping.
Why It's Important
Finite Element Analysis (FEA) is crucial for Plastics Engineers as it enables the prediction and optimization of plastic part and mold design, material selection, and processing conditions, significantly reducing development time, cost, and the need for physical prototypes while ensuring product durability, performance, and safety.
How to Improve Finite Element Analysis (FEA) Skills
Improving Finite Element Analysis (FEA) for a Plastics Engineer involves enhancing model accuracy, simulation speed, and result interpretation. Here's a concise guide:
Mesh Quality: Use adaptive meshing to ensure critical areas in the plastic component have finer meshes for higher accuracy. ANSYS Meshing Guide
Material Data: Accurately input material properties specific to the plastic, considering temperature and strain rate dependencies. Explore MatWeb for comprehensive material databases.
Boundary Conditions: Apply realistic boundary conditions that closely mimic the actual service conditions of the plastic part. SolidWorks Simulation offers practical examples.
Solver Settings: Optimize solver settings for the specific problem type (e.g., static, dynamic, thermal) to speed up analysis without compromising accuracy. COMSOL Multiphysics provides solver selection guidance.
Post-Processing: Focus on relevant results (e.g., stress concentrations, deformation) and use advanced visualization tools to better understand the behavior of the plastic component. Autodesk Fusion 360 integrates FEA with design for iterative analysis.
Validation: Always validate FEA results with experimental data or trusted benchmarks to ensure model reliability. NIST offers reference data for validation.
By focusing on these areas, a Plastics Engineer can significantly improve the effectiveness of FEA in predicting and optimizing the behavior of plastic components under various conditions.
How to Display Finite Element Analysis (FEA) Skills on Your Resume
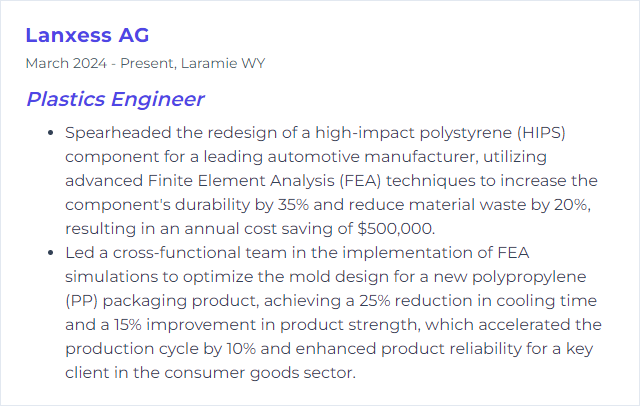
12. D Printing
3D printing is an additive manufacturing process that creates three-dimensional objects from a digital file, layer by layer, using various materials, including plastics, by a Plastics Engineer.
Why It's Important
3D printing is important for a Plastics Engineer as it enables rapid prototyping, customization, and complex geometry fabrication with reduced waste and lower costs, revolutionizing product development and manufacturing processes in the plastics industry.
How to Improve D Printing Skills
Improving 3D printing, especially from a plastics engineer's perspective, involves enhancing material properties, printing processes, and design optimization. Here are concise strategies:
Material Development: Focus on creating or selecting high-performance polymers tailored for specific applications. Consider factors like strength, flexibility, and temperature resistance. More about 3D printing materials.
Process Optimization: Refine printing parameters (temperature, speed, layer height) to achieve better surface finish and mechanical properties. Utilize software for simulation-based predictions. Optimization techniques.
Post-Processing Techniques: Implement methods such as chemical vapor smoothing or UV curing to enhance part strength and aesthetics. Explore post-processing methods.
Hybrid Printing Technologies: Combine traditional manufacturing with additive manufacturing for complex parts, improving functionality and material properties. Hybrid approaches.
Sustainability Practices: Select biodegradable polymers or develop recycling processes for 3D printing waste to minimize environmental impact. Sustainable 3D printing.
By focusing on these areas, plastics engineers can significantly contribute to the advancement of 3D printing technologies.
How to Display D Printing Skills on Your Resume
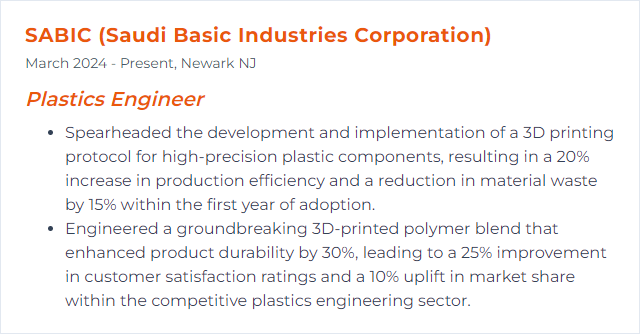