Top 12 Physical Design Engineer Skills to Put on Your Resume
In the competitive field of physical design engineering, showcasing a robust set of skills on your resume can significantly elevate your chances of landing your desired job. This article highlights the top 12 skills that are essential for a physical design engineer to possess, ensuring you stand out to potential employers in this specialized area of expertise.

Physical Design Engineer Skills
- Cadence Virtuoso
- Synopsys Design Compiler
- Floorplanning
- Clock Tree Synthesis
- Place & Route
- Static Timing Analysis
- Power Integrity Analysis
- Signal Integrity Analysis
- Tcl Scripting
- Verilog/VHDL
- Physical Verification
- DRC/LVS
1. Cadence Virtuoso
Cadence Virtuoso is a highly advanced and comprehensive suite of tools used by Physical Design Engineers for the design, simulation, and layout verification of complex integrated circuits (ICs), focusing on custom, analog, and mixed-signal designs.
Why It's Important
Cadence Virtuoso is important for a Physical Design Engineer because it provides a comprehensive IC design, simulation, and verification platform, enabling precise and efficient creation, analysis, and optimization of complex silicon chip designs, crucial for achieving high performance and reliability in semiconductor manufacturing.
How to Improve Cadence Virtuoso Skills
Improving your proficiency with Cadence Virtuoso, especially from a Physical Design Engineer's perspective, involves honing specific skills and utilizing resources efficiently. Here's a concise guide:
Master the Basics: Ensure a solid understanding of Virtuoso's fundamental concepts and tools. Official Cadence documentation is a great starting point.
Skill Enhancement: Enhance your skills through online courses or tutorials. Websites like Udemy and Coursera often have relevant courses.
Automation Scripts: Learn to write and use SKILL programming language for automation to speed up the design process. The Cadence Community forums can be a good place to exchange scripts and tips.
Practice Layout Techniques: Focus on mastering layout techniques such as floorplanning, routing, and DRC/LVS clean-up. Practice is key to efficiency.
Stay Updated: The field is always evolving. Stay updated with the latest features and tools released by Cadence. Subscribe to the Cadence Blog for updates and insights.
Networking and Community Engagement: Engage with the Virtuoso community through forums, social media groups, or attending Cadence-related events. Sharing knowledge and learning from peers can provide practical insights not found in manuals.
Remember, consistent practice and staying engaged with the Cadence community are crucial for continuous improvement.
How to Display Cadence Virtuoso Skills on Your Resume
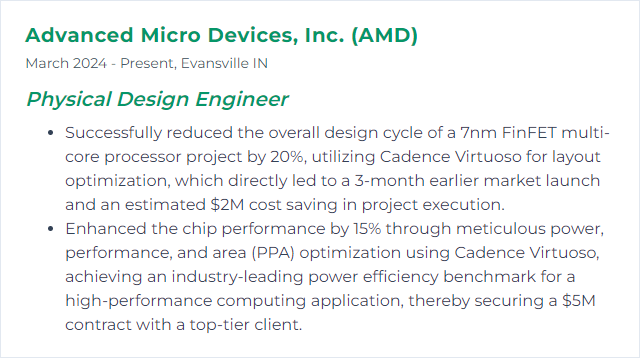
2. Synopsys Design Compiler
Synopsys Design Compiler is a comprehensive RTL synthesis tool used by Physical Design Engineers to translate Verilog or VHDL code into optimized gate-level representations, facilitating the physical layout and design of digital circuits and systems on a chip.
Why It's Important
Synopsys Design Compiler is crucial for a Physical Design Engineer as it provides advanced synthesis capabilities to optimize digital designs for power, performance, and area, significantly impacting the efficiency and success of the physical design process.
How to Improve Synopsys Design Compiler Skills
Improving Synopsys Design Compiler performance from a Physical Design Engineer's perspective involves a focused approach on optimizing scripts, design constraints, and understanding the tool's capabilities. Here are concise steps with resources:
Understand Constraints: Deeply understand the synthesis constraints (timing, area, power). Use the Synopsys Design Constraints (SDC) effectively. Synopsys SDC Guide
Optimize Scripts: Streamline and optimize your scripts for synthesis. Ensure they are clean and efficient, focusing on the critical path and minimizing unnecessary computations. Design Compiler User Guide
Hierarchy Management: Properly manage the design hierarchy to improve compile times and memory usage. Flatten or partition the design appropriately. Best Practices for Design Compiler
Utilize Advanced Features: Use advanced features like physical guidance to Design Compiler Graphical for better correlation with place and route. Design Compiler Graphical
Timing and Area Recovery: Implement strategies for timing and area recovery post-synthesis. This includes re-synthesis with different strategies or constraints. Synopsys Community
Tool Updates and Training: Stay updated with the latest tool versions and features. Regular training can uncover new optimizations techniques. Synopsys Training
Collaborate and Share Knowledge: Engage with the Synopsys community and internal team to share knowledge and learn from others' experiences. Synopsys Community Forum
By focusing on these areas, you can significantly improve the performance of the Synopsys Design Compiler in your physical design projects.
How to Display Synopsys Design Compiler Skills on Your Resume
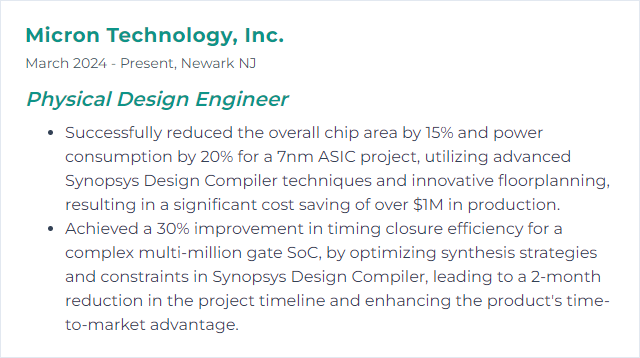
3. Floorplanning
Floorplanning in the context of physical design engineering is the process of defining the placement and arrangement of various functional blocks or modules within a semiconductor chip, ensuring optimal space utilization, electrical performance, and meeting design constraints such as timing, power, and connectivity.
Why It's Important
Floorplanning is crucial for a Physical Design Engineer as it lays out the blueprint for chip design, optimizing the spatial allocation of various components within an integrated circuit. This ensures efficient use of space, minimizes signal delay by optimizing the placement of interconnected components, and enhances overall performance and power efficiency of the chip.
How to Improve Floorplanning Skills
Improving floorplanning involves optimizing the layout of cells and blocks within an integrated circuit to enhance performance, minimize area, and ensure routability. Here are concise steps tailored for a Physical Design Engineer:
Define Floorplan Constraints: Start by setting clear boundaries and requirements, including aspect ratio, core utilization, and pre-placement of critical blocks. Synopsys offers insights on early-stage floorplanning.
Analyze Power, Clock, and Thermal Requirements: Consider power distribution, clock tree synthesis, and thermal dissipation early to avoid redesigns. Cadence provides advanced tools for power, clock, and thermal analysis.
Optimize Block Placement: Arrange blocks to minimize wire length and congestion while considering timing and signal integrity. The IEEE Xplore Digital Library discusses strategies for optimal block placement.
Utilize EDA Tools: Employ Electronic Design Automation (EDA) tools for simulation and analysis to iteratively refine the floorplan. Mentor, a Siemens Business, offers comprehensive EDA solutions.
Incorporate IP and Macro Blocks Thoughtfully: Place IP and macro blocks considering their connectivity and performance impact. ARM provides guidelines for integrating IP blocks.
Conduct Regular Reviews: Regularly review the floorplan against design specifications and constraints to ensure alignment with project goals.
Iterate Based on Analysis: Use the results from timing, power, and signal integrity analyses to iteratively refine the floorplan.
By following these steps and leveraging the resources provided, a Physical Design Engineer can significantly improve the floorplanning process, leading to more efficient and effective chip designs.
How to Display Floorplanning Skills on Your Resume
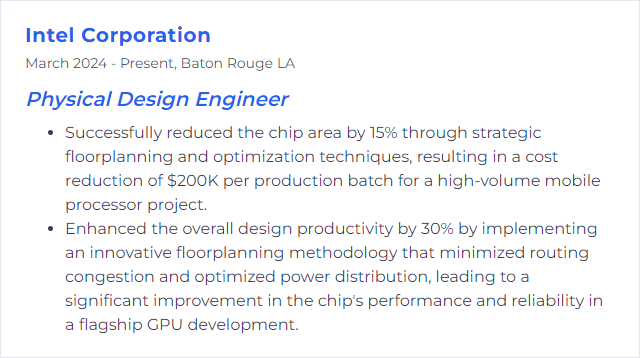
4. Clock Tree Synthesis
Clock Tree Synthesis (CTS) is a process in the physical design of integrated circuits where a clock distribution network is created. This network ensures that the clock signal reaches all elements of the chip simultaneously or within a specified skew time, optimizing timing performance and minimizing power consumption.
Why It's Important
Clock Tree Synthesis (CTS) is crucial for ensuring that the clock signal reaches all elements of an integrated circuit simultaneously, minimizing clock skew and meeting timing requirements, which is essential for the reliable performance and power efficiency of the chip.
How to Improve Clock Tree Synthesis Skills
Improving Clock Tree Synthesis (CTS) involves enhancing performance, power, and area efficiency during the chip design process. Here's a concise guide for a Physical Design Engineer:
Optimize Skew and Jitter: Aim for minimal skew and jitter by adjusting buffer sizes and placement. Techniques include balancing clock paths and using advanced algorithms for skew reduction.
Hierarchy Planning: Design a hierarchical clock tree that efficiently distributes the clock signal while minimizing power and delay. Divide the clock network into manageable sub-trees.
Use Advanced CTS Tools: Leverage the latest CTS tools that offer better algorithms for clock distribution, skew control, and power optimization.
Buffer Insertion and Sizing: Optimize buffer insertion and sizing for effective load balancing and reduced power consumption. Tools like Synopsys Design Compiler can automate this task.
Analyze and Optimize Power: Use power analysis tools to identify and minimize power-hungry sections of your clock tree. Implement techniques like clock gating to reduce dynamic power.
Floorplanning Considerations: During floorplanning, allocate space for clock buffers and consider clock routing paths to minimize delays and congestion.
Post-CTS Simulation: Perform post-CTS simulation to validate timing, power, and signal integrity. Use tools like Mentor Graphics’ Questa for accurate simulation results.
Iterative Refinement: Clock tree synthesis is an iterative process. Use feedback from post-CTS analysis to refine your clock tree design continuously.
For further reading and detailed methodologies, refer to specialized resources and documentation provided by tool vendors and industry standards.
How to Display Clock Tree Synthesis Skills on Your Resume
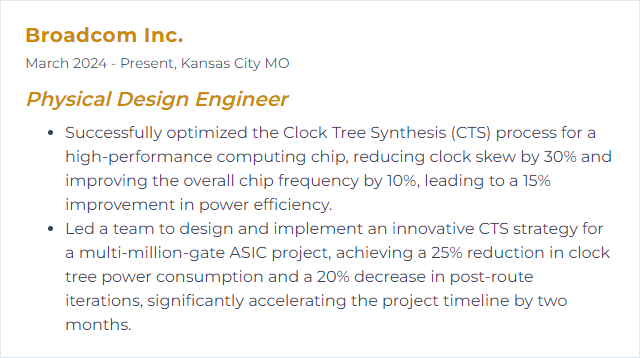
5. Place & Route
Place & Route (P&R) is a process in the field of VLSI design where, after logical synthesis, the physical instantiation of a circuit is determined. This involves placing blocks or cells onto a chip's layout and then routing the interconnections between them. The goal is to meet design specifications such as performance, area, power consumption, and reliability, while also ensuring manufacturability. This critical stage in physical design influences the final performance and yield of semiconductor devices.
Why It's Important
Place & Route (P&R) is crucial in physical design engineering as it determines the optimal placement of components and the routing of interconnections on a chip, directly impacting its performance, power consumption, and area efficiency. This process ensures the design meets specific constraints and requirements, enabling the successful fabrication of high-quality, reliable semiconductor devices.
How to Improve Place & Route Skills
Improving Place & Route (P&R) in the context of physical design involves optimizing the layout of cells and interconnects on a chip to meet design specifications such as performance, area, power, and timing. Here’s a concise guide for a Physical Design Engineer:
Floorplanning: Start with efficient floorplanning to allocate space for cells and macros while considering power distribution and signal routing. Utilize hierarchical floorplanning for complex designs.
Power Planning: Implement robust power planning to ensure uniform power distribution and minimize IR drop. Cadence's Power Planning Guide offers insights.
Placement Optimization: Use tools for optimal cell placement considering timing, congestion, and power. Techniques like timing-driven placement are crucial. Synopsys IC Compiler provides advanced placement strategies.
Clock Tree Synthesis (CTS): Efficiently design your clock distribution network to minimize skew and jitter. Siemens' Clock Tree Synthesis offers methodologies.
Routing: Leverage advanced routing tools and techniques to address signal integrity, crosstalk, and routing congestion. Tools like Mentor's Calibre can help in achieving clean routing.
Post-Route Optimization: Perform post-route optimization for timing, crosstalk, and power. Utilize ECO (Engineering Change Order) techniques for targeted fixes.
Timing Closure: Achieve timing closure through iterative analysis and refinement. Tools like PrimeTime from Synopsys are essential for timing analysis and closure.
Physical Verification: Ensure design meets all foundry rules for manufacturability using DRC (Design Rule Checking) and LVS (Layout vs. Schematic) checks. Cadence's Physical Verification System is a key tool for this step.
Improving P&R is an iterative process requiring a combination of strategic planning, tool expertise, and design refinement. Keeping abreast with the latest tools and methodologies through forums, webinars, and documentation from tool vendors is essential for continuous improvement.
How to Display Place & Route Skills on Your Resume
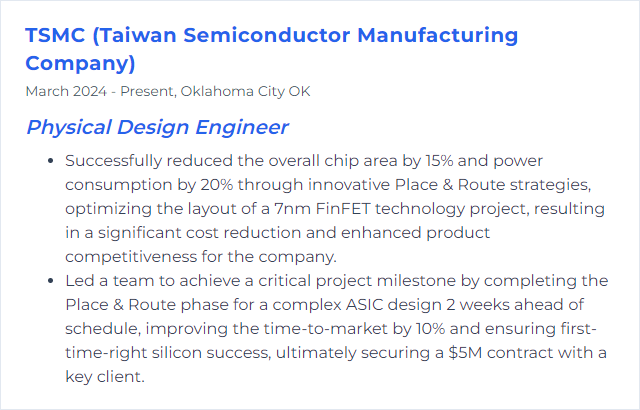
6. Static Timing Analysis
Static Timing Analysis (STA) is a method used by Physical Design Engineers to evaluate the timing performance of a digital circuit without simulating its actual operation. It involves checking that all data paths in a circuit meet timing requirements, ensuring signals propagate within defined time constraints, and identifying potential setup and hold time violations. This analysis is crucial for verifying the circuit's reliability and performance before fabrication.
Why It's Important
Static Timing Analysis (STA) is crucial for Physical Design Engineers because it enables them to verify that the digital circuit meets all timing requirements without needing to run the circuit at its operational speed. This ensures reliability, optimizes performance, and avoids timing-related errors in chip design before fabrication.
How to Improve Static Timing Analysis Skills
Improving Static Timing Analysis (STA) involves optimizing the design and analysis process to ensure accurate timing closure. Here's a concise guide tailored for a Physical Design Engineer:
Understand Timing Constraints: Ensure that all timing constraints are correctly defined and applied. This includes setup and hold times, clock definitions, and false paths. Synopsys Timing Constraints User Guide offers insights into setting accurate constraints.
Optimize Design for Timing: Use synthesis and place & route (P&R) tools effectively to optimize the design. Techniques include logic restructuring, gate sizing, and buffer insertion. Cadence's Genus Synthesis Solution can help in logic optimization.
Clock Tree Synthesis (CTS) Tuning: Optimize the clock tree for skew and insertion delay, crucial for STA accuracy. Siemens offers a comprehensive guide on CTS.
Analyze and Fix Timing Violations: Use STA tools to identify and address setup and hold violations. Incremental STA can be useful in iterating quickly. Mentor Graphics provides resources on timing analysis.
Leverage Advanced Analysis Features: Utilize on-chip variation (OCV), aging, and crosstalk analysis features of STA tools to account for real-world conditions. Cadence's Tempus Timing Signoff Solution supports these analyses.
Collaborate with the Design Team: Ensure tight integration and communication with the design team to implement timing fixes and understand the impact on power, area, and other design metrics.
By focusing on these areas, a Physical Design Engineer can significantly improve the accuracy and efficiency of Static Timing Analysis, leading to a more robust and high-performance design.
How to Display Static Timing Analysis Skills on Your Resume
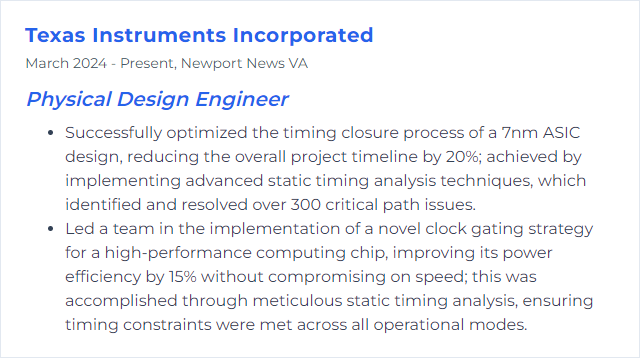
7. Power Integrity Analysis
Power Integrity Analysis is a process used by Physical Design Engineers to ensure that a chip's design can reliably deliver the necessary power to all components without suffering from issues such as voltage drops, noise, or fluctuations that could affect performance or cause failures. This involves simulating and validating the power distribution network to meet the design's power requirements under various conditions.
Why It's Important
Power Integrity Analysis is crucial for a Physical Design Engineer as it ensures reliable performance and stability of electronic circuits by identifying and mitigating issues related to voltage drops, power distribution imbalances, and noise in the power supply, preventing component failures and system malfunctions.
How to Improve Power Integrity Analysis Skills
Improving Power Integrity Analysis involves optimizing the delivery of power across an IC (Integrated Circuit) to ensure stable operation and performance. For a Physical Design Engineer, this entails:
Accurate Modeling: Start with accurate models of your components and interconnects. Use vendor-supplied or measured data for the most precise representation.
Decoupling Capacitors: Effectively place decoupling capacitors to minimize power supply noise. Keysight offers guidelines for decoupling capacitor placement.
Power Grid Design: Optimize your power grid design for uniform distribution and minimize voltage drops. Cadence provides insights into Power Grid Design.
Simulation and Analysis: Use simulation tools like ANSYS SIwave (ANSYS) to analyze power integrity issues early in the design phase.
Mitigate IR Drop: Address IR drop issues by optimizing the width of power and ground nets. Mentor Graphics discusses strategies in their white paper on power integrity.
Thermal Considerations: Consider the thermal impact on power integrity and manage hotspots through thermal analysis and management strategies.
Frequent Review and Iteration: Continuously review and iterate your design based on analysis results to meet power integrity requirements.
By following these steps and utilizing the resources provided, a Physical Design Engineer can significantly improve Power Integrity Analysis in their projects.
How to Display Power Integrity Analysis Skills on Your Resume
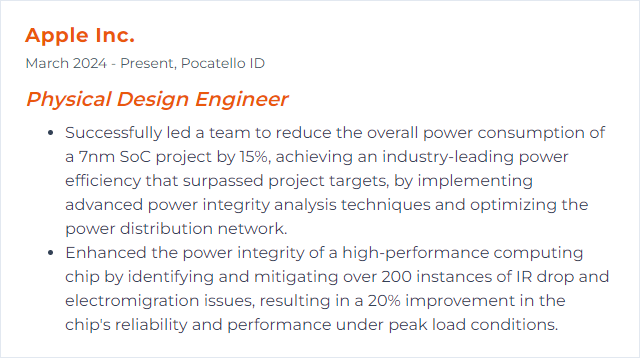
8. Signal Integrity Analysis
Signal Integrity Analysis is the evaluation of the quality and reliability of electrical signals on a chip or within an electronic system. For a Physical Design Engineer, it involves ensuring that signals transmitted across the circuit meet timing, noise, and power integrity requirements to avoid data corruption or system failure.
Why It's Important
Signal Integrity Analysis is crucial for a Physical Design Engineer to ensure that electronic signals maintain their integrity throughout a circuit, avoiding issues like signal loss, timing errors, and cross-talk. This ensures reliable performance and functionality of the final product, especially at high frequencies and in complex designs.
How to Improve Signal Integrity Analysis Skills
Improving Signal Integrity Analysis involves several strategies focused on minimizing noise and distortion in signal paths to ensure reliable communication between components in electronic systems. As a Physical Design Engineer, consider the following concise steps:
Model Accurately: Use precise models for components and materials that reflect real-world behavior. Tools like Cadence Sigrity offer detailed modeling capabilities.
Minimize Crosstalk: Route critical signals away from each other and use shielding or differential signaling when possible. Techniques can be found in resources like Altium’s guide on reducing crosstalk.
Optimize Power Integrity: Ensure stable power distribution with decoupling capacitors and proper power plane design. The Intel Power Integrity Guide provides insights into effective strategies.
Use Termination Strategies: Implement appropriate termination techniques to reduce reflections. A concise overview is available in Texas Instruments’ Termination Techniques.
Perform Simulation and Analysis Early and Often: Leverage simulation tools like ANSYS SIwave for early detection and fixing of potential issues.
Follow Best Practices in Layout Design: Adhere to guidelines for trace routing, layer stacking, and via placements to minimize signal degradation. Mentor Graphics offers a comprehensive layout guide in their PCB Design Best Practices.
Stay Informed on Latest Technologies: Continuous learning about new materials, components, and design techniques is crucial. Websites like EE Times provide updates on the latest trends.
By integrating these strategies into your design process, you can significantly improve signal integrity analysis outcomes, leading to more reliable and high-performing electronic systems.
How to Display Signal Integrity Analysis Skills on Your Resume
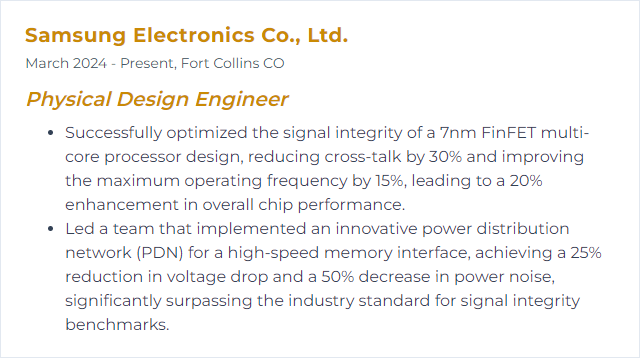
9. Tcl Scripting
Tcl (Tool Command Language) scripting is a dynamic programming language often used by Physical Design Engineers for automating tasks in Electronic Design Automation (EDA) tools, enabling efficient manipulation and analysis of chip designs.
Why It's Important
Tcl scripting is important for a Physical Design Engineer because it enables automation of repetitive tasks in the design process, customization of EDA tools, and efficient manipulation of design data, thus enhancing productivity and accuracy in the physical design flow.
How to Improve Tcl Scripting Skills
To improve Tcl (Tool Command Language) scripting skills, especially for a Physical Design Engineer, focus on mastering specific areas relevant to automation and tool interaction in the VLSI design process. Here's a concise guide:
Understand Tcl Basics: Start with the core syntax, control structures, and data types. Tcl Developer Site offers comprehensive resources.
Learn Tcl Extensions for EDA Tools: Many EDA tools use Tcl for scripting. Explore tool-specific extensions or commands. Documentation from tool vendors like Cadence or Synopsys is invaluable.
Practice Scripting for Automation: Automate repetitive tasks in your design flow. Start with simple scripts and gradually tackle more complex automation tasks.
Use Tcl Libraries: Leverage existing Tcl libraries for file I/O, regular expressions, and data processing. Tcllib is a good resource.
Debugging and Optimization: Learn to debug and optimize your scripts for better performance. Tcler's Wiki has tips and tricks for debugging and improving script efficiency.
Join Tcl Community: Engage with the Tcl community for support, tips, and sharing knowledge. The Tcl Mailing List and Stack Overflow are great platforms.
Continuous Learning and Experimentation: Stay updated with the latest in Tcl and EDA tool enhancements. Experiment with new features and techniques in your scripts.
By focusing on these areas, Physical Design Engineers can significantly enhance their Tcl scripting capabilities, leading to more efficient and automated design processes.
How to Display Tcl Scripting Skills on Your Resume
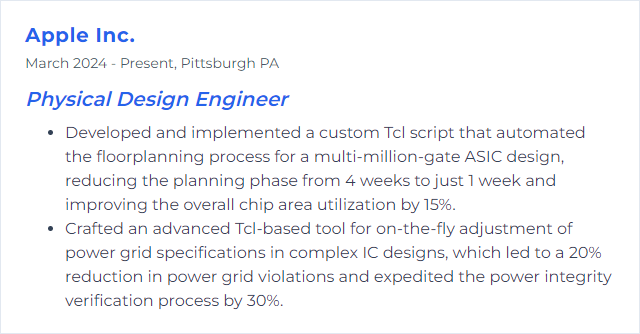
10. Verilog/VHDL
Verilog and VHDL are hardware description languages used to model and design electronic systems. For a Physical Design Engineer, they serve as tools to describe, simulate, and synthesize the logic and structure of integrated circuits (ICs) and printed circuit boards (PCBs) at a high level before physical implementation.
Why It's Important
Verilog/VHDL is crucial for Physical Design Engineers because it allows them to describe, simulate, and verify the hardware functionality of digital circuits before the physical layout, ensuring design correctness and efficiency.
How to Improve Verilog/VHDL Skills
Improving your skills in Verilog/VHDL as a Physical Design Engineer involves a focused approach towards understanding both languages' syntax, semantics, and best practices for hardware description. Here’s a very short and concise guide to get you started:
Understand the Basics:
- Master the fundamental concepts of both Verilog and VHDL. This includes understanding data types, operators, conditional statements, loops, and modular design.
- Verilog: Verilog Tutorial
- VHDL: VHDL Tutorial
Practice Coding:
- Regular practice is key. Implement various digital designs starting from simple to complex ones.
- Example Projects: FPGA4Student
Learn Best Practices:
- Familiarize yourself with coding guidelines for synthesis and simulation to write efficient, synthesizable, and reliable code.
- Verilog Best Practices: Verilog Guidelines
- VHDL Best Practices: VHDL Guidelines
Understand Simulation and Synthesis:
- Grasp how your Verilog/VHDL code translates into actual hardware and the implications of various coding styles on the synthesis outcome.
- Synthesis and Simulation: Guide
Stay Updated and Involved:
- Technology and methodologies evolve, so stay informed through forums, publications, and continuous learning.
- Forums: EDAboard for VHDL and Verilog
Use Development Tools:
- Gain proficiency in using simulation and synthesis tools like ModelSim, Vivado, Quartus, etc. Understanding tool-specific features can significantly enhance your productivity.
- ModelSim: Tutorial
- Vivado: Getting Started
- Quartus: Introduction
Improving in Verilog/VHDL requires a balance of theoretical knowledge, practical implementation skills, and staying updated with the latest industry practices. Engage with the community through forums and projects to exchange knowledge and solve challenges.
How to Display Verilog/VHDL Skills on Your Resume
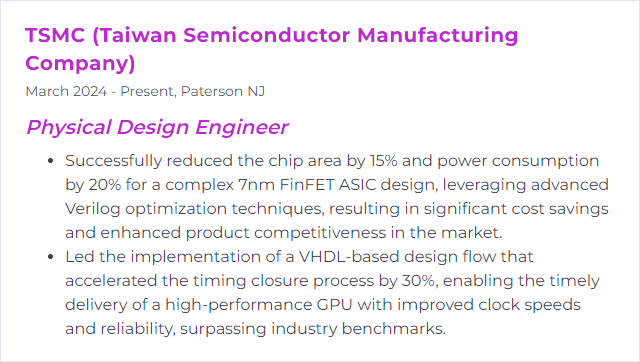
11. Physical Verification
Physical Verification in the context of a Physical Design Engineer involves checking the correctness and completeness of integrated circuit designs against design rules (Design Rule Checking - DRC), verifying the electrical connectivity accuracy (Layout Versus Schematic - LVS), and ensuring the design is free of manufacturing defects (e.g., via antenna checks). This process is crucial for ensuring the manufacturability and functionality of the chip design before fabrication.
Why It's Important
Physical Verification is crucial for a Physical Design Engineer because it ensures the design meets specific manufacturing, performance, and reliability standards before fabrication, preventing costly errors and ensuring the final product functions as intended.
How to Improve Physical Verification Skills
Improving Physical Verification involves enhancing the accuracy and efficiency of checking a chip's design against its physical layout to ensure manufacturability and functionality. Here are concise strategies for a Physical Design Engineer:
Automation: Utilize automation tools for layout vs. schematic (LVS) and design rule checking (DRC) to speed up the process.
Up-to-date Design Rules: Ensure you're using the latest design rules from the foundry to reduce iterations.
Incremental Verification: Apply incremental verification techniques to check only the modified sections of the design, saving time.
Cross-verification: Use multiple verification tools when possible to cross-verify, ensuring that no single tool's limitations impact the final design's quality.
Layout Cleanliness: Maintain a clean layout with clear labeling and organization to ease the identification of issues and improve verification.
Collaboration and Knowledge Sharing: Regularly communicate with the fabrication team and other engineers. Sharing knowledge and insights can uncover new strategies and common pitfalls to avoid.
Continuous Learning: Stay updated with the latest technologies and methodologies in physical verification through professional development resources and training.
By implementing these strategies, Physical Design Engineers can enhance the physical verification process, ensuring designs are manufacturable, function as intended, and are delivered on schedule.
How to Display Physical Verification Skills on Your Resume
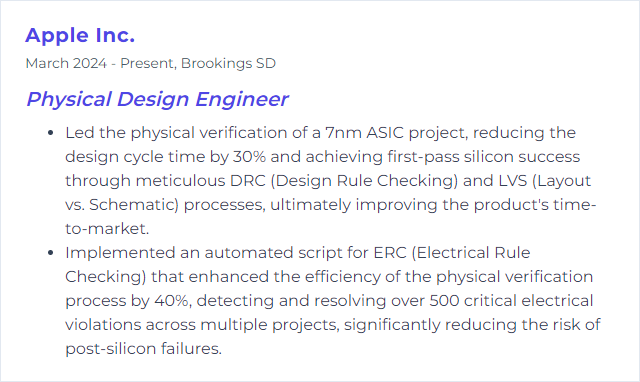
12. DRC/LVS
DRC (Design Rule Check) and LVS (Layout Versus Schematic) are essential verification steps in the physical design process of integrated circuits (ICs). DRC ensures that the IC layout adheres to specific manufacturing rules, while LVS confirms that the layout matches the original schematic design accurately. These checks are crucial for ensuring the manufacturability and functionality of the final IC product.
Why It's Important
DRC (Design Rule Check) and LVS (Layout vs. Schematic) are crucial for a Physical Design Engineer because they ensure that the IC (integrated circuit) layout adheres to specific fabrication rules (DRC) and matches the original schematic design accurately (LVS), thereby minimizing errors, ensuring manufacturability, and optimizing performance of the final product.
How to Improve DRC/LVS Skills
Improving Design Rule Checking (DRC) and Layout Versus Schematic (LVS) processes is crucial for ensuring the integrity and functionality of integrated circuits. Here's a concise guide for a Physical Design Engineer:
Understand Design Rules: Deeply understand the foundry's design rules to avoid common pitfalls. Reference the design rule manual thoroughly.
Use High-Quality Libraries: Ensure the cell libraries used are of high quality and are compatible with the technology node. This reduces errors during DRC/LVS.
Incremental DRC/LVS: Run DRC/LVS checks incrementally during the design phase rather than waiting for the final layout. This helps in identifying and fixing errors early.
Employ DRC/LVS Clean IP: Utilize IPs that are already DRC/LVS clean to reduce the overall number of errors in the design.
Automate Repetitive Fixes: Use scripts for common error fixes to save time. Many EDA tools support scripting for automation.
Cross-Verification: Use multiple DRC/LVS tools for cross-verification if possible. This can help catch errors that one tool might miss.
Continuous Learning: Stay updated with the latest DRC/LVS techniques and tools. Participate in forums and workshops.
Collaborate: Work closely with the design, layout, and verification teams to ensure everyone understands the impact of their work on DRC/LVS.
For more detailed information and resources, consider visiting:
- Cadence Design Systems for tools and methodologies.
- Synopsys offers advanced verification solutions.
- Mentor Graphics (now part of Siemens) for comprehensive DRC/LVS tools and guides.
Remember, improving DRC/LVS is an ongoing process that benefits from experience, continuous learning, and leveraging the latest tools and methodologies in the industry.
How to Display DRC/LVS Skills on Your Resume
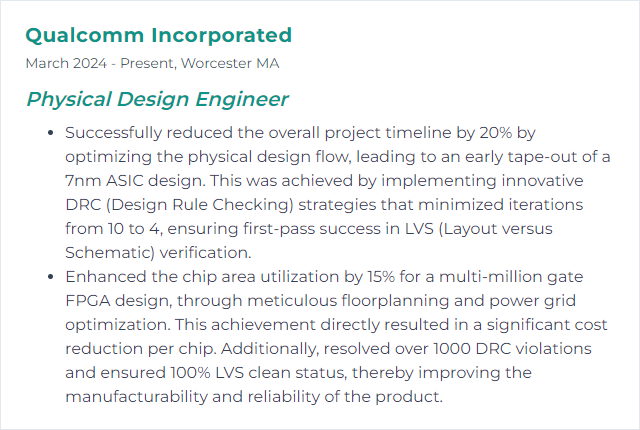